Key Takeaways
- Idle equipment runs up additional costs and decreases productivity on the construction site.
- Due to often being neglected when it comes to maintenance, idle equipment can malfunction and lead to injuries.
- Inefficiencies caused by idle equipment can reduce the competitiveness of the construction company in the market.
Compared to other pressing issues troubling construction companies, having idle equipment is often considered a minor hiccup.
After all, you can’t eliminate idle time, so it’s best not to waste too much time and effort on it, right?
Wrong: if left unchecked, idle time creates a devastating ripple effect that your business is bound to feel sooner, rather than later.
So, it’s crucial to recognize and tackle these problems before they hurt your business.
And in this article, we’ll provide you with the insights you need to do just that.
In this article...
Increase In Avoidable Costs
For starters, having construction equipment that you’re not actually using leads to costs that could have easily been avoided.
Here’s one scenario to consider.
The project crew occasionally uses a large excavator that makes quick work of any trenching operations.
However, since the space on the site is generally tight, they rely on mini excavators and backhoes a lot more.
This begs the question: what are the costs of having an underutilized excavator brought in for that specific project?
First, there’s the maintenance.
General maintenance, repairs, and operations (MRO) costs typically include:
- Labor Costs
- Spare Parts and Materials
- Maintenance Vendors
- Energy Costs
- Overhead Expenses
On top of these standard ones, idle equipment runs up additional costs which typically take time to notice.
Why?
Because the truth is, assets that are not used regularly are rarely a maintenance priority—whether on-site or outside of it.
And if maintenance is skipped in favor of other equipment and machinery, there’s a higher chance that the underutilized assets will deteriorate over time.
Lack of maintenance also means a higher chance of malfunctions that invite costly repairs.
Some assets carry significant operational costs from the get-go.
Combined with the expenses of idleness, this creates a heavy drain on resources and profits, without giving enough in return.
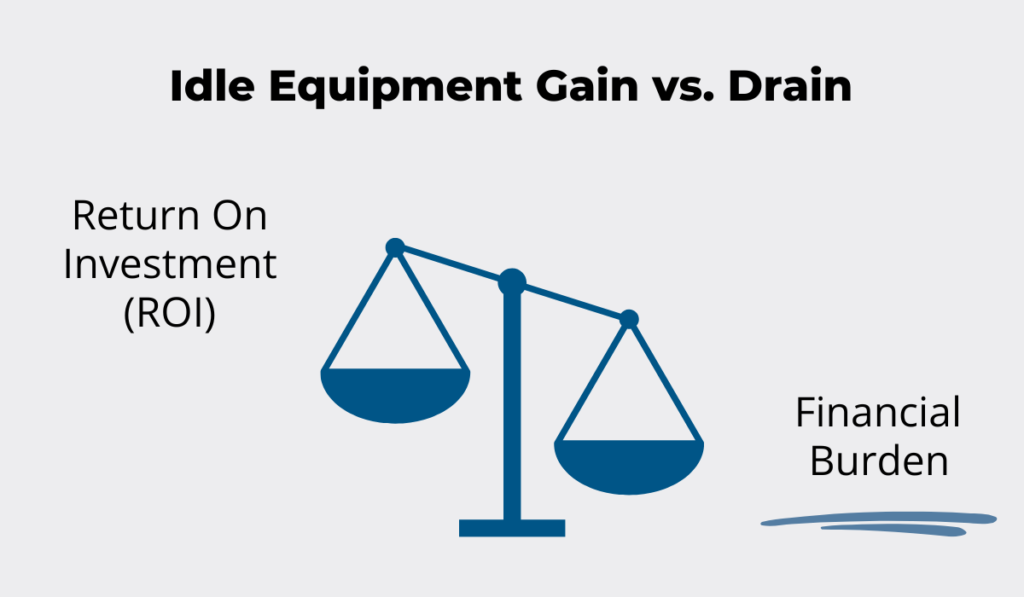
The imbalance is made more evident once we factor in the costs of insurance premiums and storage for the underutilized equipment, but more on that later.
One way to tip the scales back to ROI would be to review and optimize equipment usage regularly.
Otherwise, you’re risking a set of productivity problems, too.
Decrease In Productivity
Insufficiently used equipment quickly becomes neglected, making it more likely to be subjected to reactive maintenance interventions.
Naturally, this is bound to incur higher costs down the road.
But besides the costs, idle time leaves a large dent in the equipment’s efficiency.
Without regular use, equipment loses some of its operational efficiency, and that’s all the more true after it’s gone through a round of repairs.
Avoiding a catastrophic failure is a positive outcome, but getting the asset back on the field won’t automatically result in the expected output.
And if processes are lagging due to inefficiency, this impacts overall productivity levels and results in delays.
To help you visualize this domino effect, the image below breaks it down.
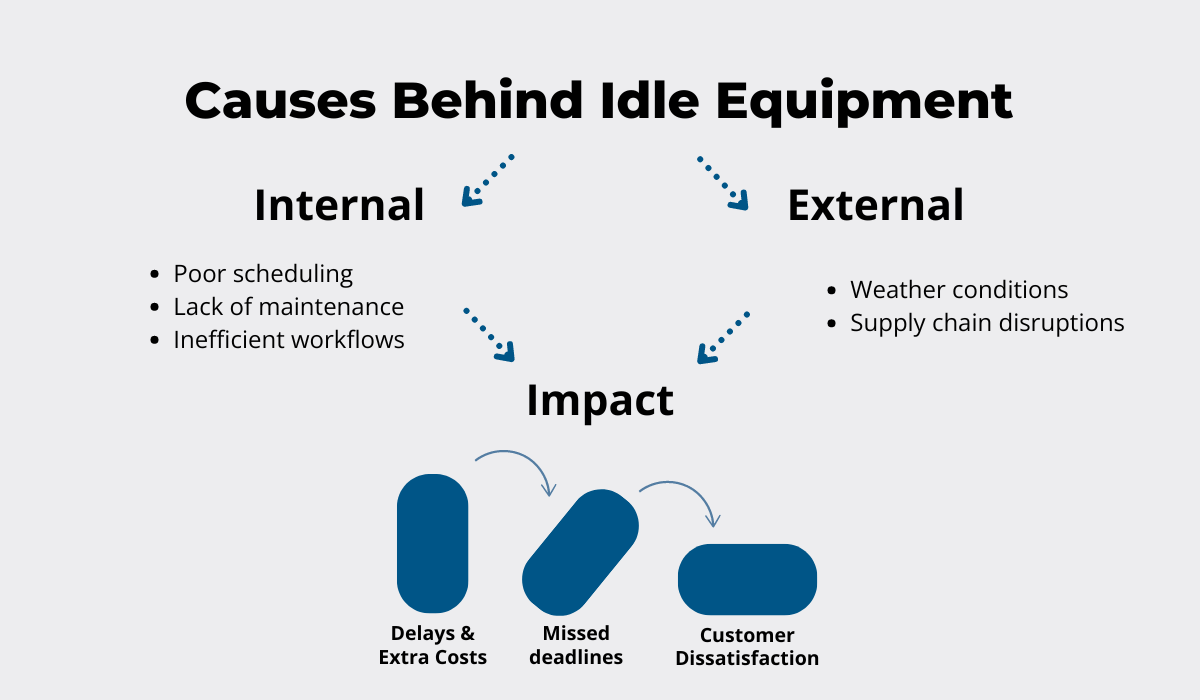
Major consequences—such as missed deadlines and dissatisfied customers—can easily pile up on top of delays, and threaten the reputation and profitability of your business.
Yes, some idle time is unavoidable.
But the avoidable bit is linked to internal processes, which is why businesses need to look into their equipment utilization and identify bottlenecks that hinder it.
Neglecting to do that and sticking to inefficient workflows can cause frustration among workers.
In such a setting, they would likely look for workarounds themselves or go back to less efficient and more time-consuming manual processes.
To counter this, construction companies can turn to scheduling and resource planning tools that help optimize equipment deployment.
Procore, for example, offers a comprehensive construction management solution that includes scheduling tools and provides total, real-time visibility.
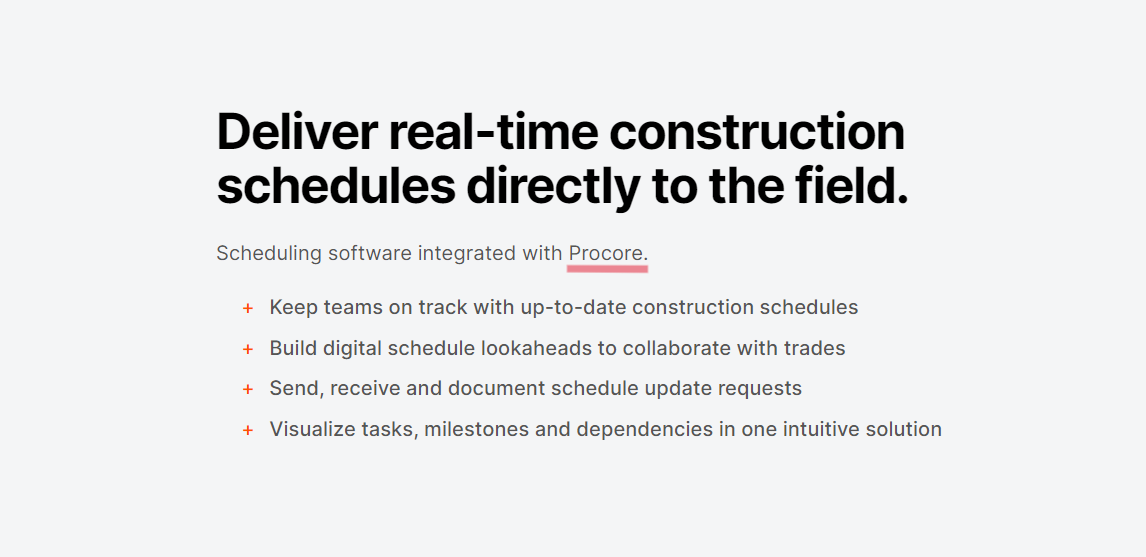
Having an intuitive, visual overview of different tasks and dependencies enhances your resource management abilities, thereby boosting job site productivity.
However, some inefficiencies regarding equipment allocation tie in with other issues, such as storage space utilization, which we will discuss next.
Inefficient Utilization of Storage Space
To put it simply, idle equipment takes up space, and the extra clutter comes with a price.
Underutilized assets vary in size and function, but there is one thing they have in common:
They need to be stored regardless of how much they contribute.
Let’s go back to our earlier excavator example for a moment.
An asset with power and capacity like that can be tricky to accommodate due to its size and value, but well worth the effort if it makes a difference on the job site.
If it doesn’t, navigating the storage challenges becomes all the more vexing.
After all, idle equipment occupies the same space as the equipment which is actively used.
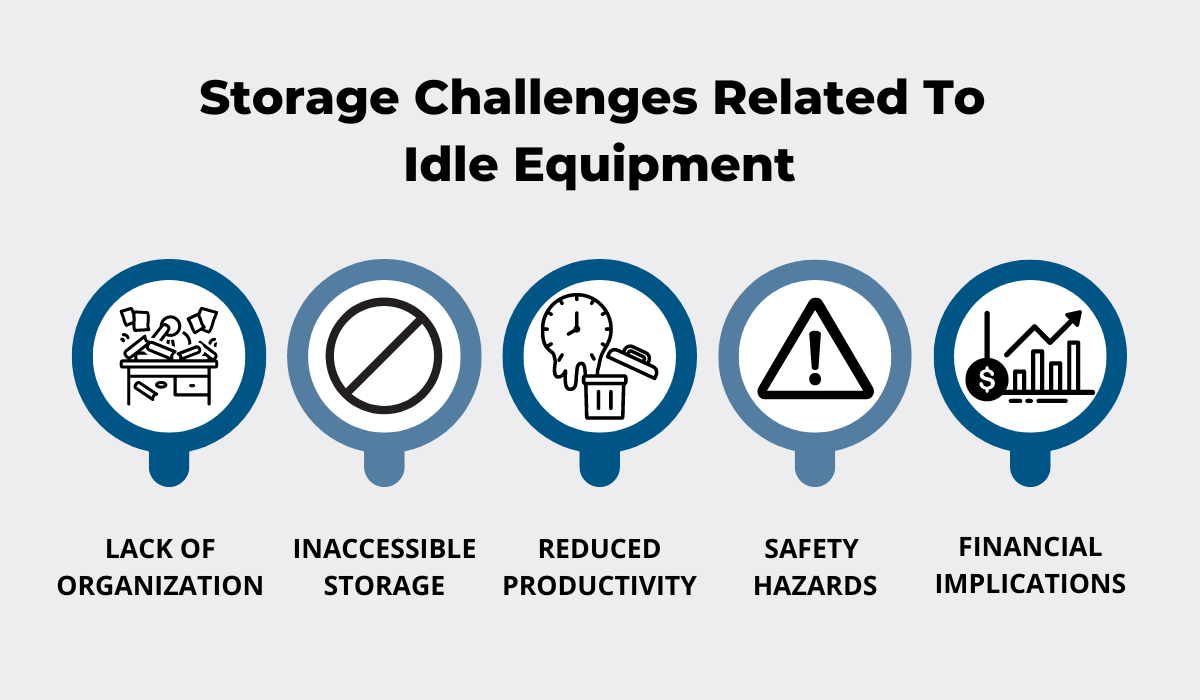
Even if it doesn’t necessarily make the other equipment and materials inaccessible, it creates disorder and makes organizing the space more difficult.
Moreover, retrieving different equipment based on ongoing operational needs can also turn less intuitive and more complicated if unused assets are in the way.
If workers can’t grab what they need as quickly as they should, your overall efficiency and productivity are taking a serious hit.
But, it’s also important to highlight the immediate financial implications.
Construction businesses handling complex jobs need to secure major storage capacity.
Leasing a warehouse close to the job site is a common scenario, but rarely an affordable one, especially judging by the estimates made by Warehousing and Fulfillment operating in the US and Canada.
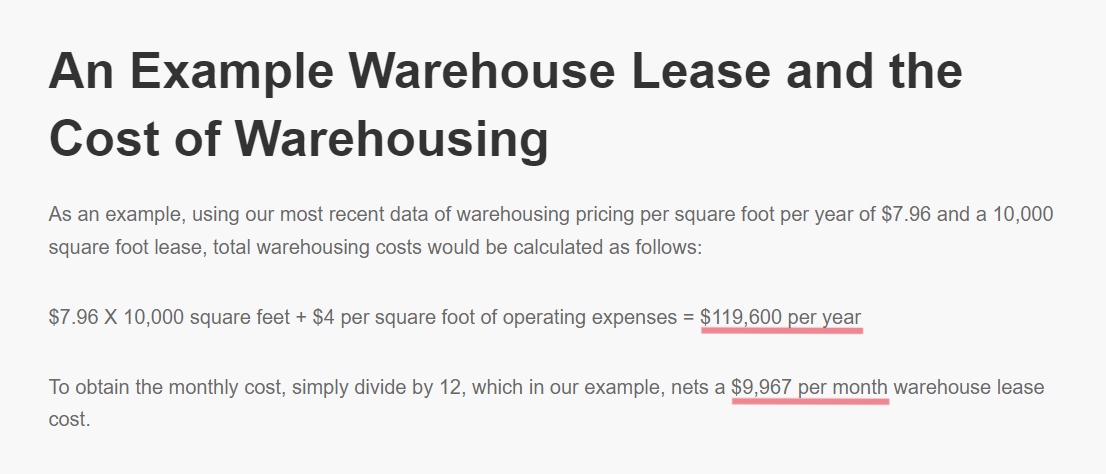
With the skyrocketing prices of warehouse and distribution center rentals, construction companies need to carefully estimate the kind of storage size their operations require.
This makes tracking and reducing the number of idle equipment an even bigger cost-saving priority.
Safety Hazards
Plenty of things can happen when the storage area is disorganized and cluttered with idle equipment and machinery—especially if they don’t get regular maintenance.
Inefficient storing is annoying and hinders operations, but the lack of space can easily lead to bigger issues, such as breaching safety regulations.
Picture a warehouse with rows upon rows of stacked boxes.
These boxes contain spare parts and some raw materials that would usually be organized quite differently, but since some assets take up quite a lot of space, there weren’t too many options.
Some boxes are difficult to reach since they’re high up, and there is some worry about them toppling over.
The really worrying part?
The aisles and walkways are cluttered, and although workers can still reach emergency exits fairly easily in case of an accident, it would probably take some extra time.
In a nutshell, it’s a safety hazard waiting to happen.
There’s a multitude of reasons why companies look to prevent and avoid any injuries and accidents.
The estimates on lost work days shared by the National Safety Council point in one clear direction.
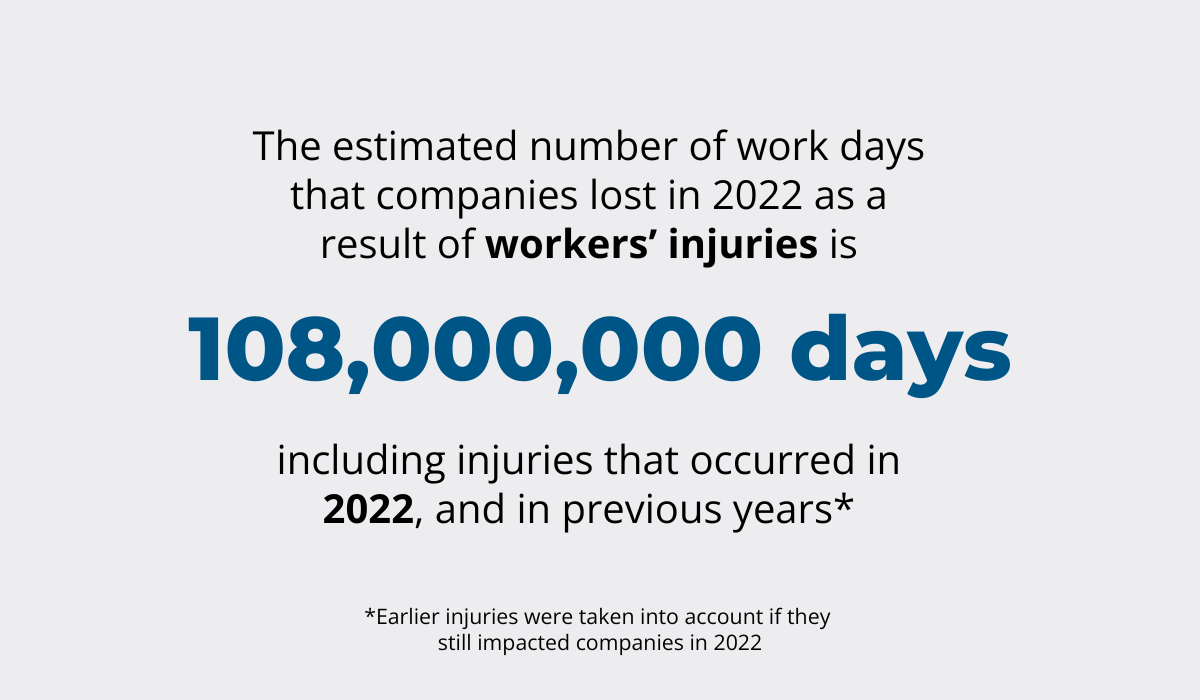
The findings include different sectors and highlight the staggering costs of injuries and accidents, no matter how small.
Workplace injuries have far-reaching effects outside of bodily harm, which is why a safety-first approach is so important for construction companies.
Adopting this approach rests on properly securing idle equipment and regularly inspecting it to prevent accidents, but also upholding safety standards.
Idle assets have a higher chance of malfunctioning, thus endangering your crew members, from operators to the maintenance team.
What’s more, the OSHA listed unsafe machinery among the top 10 workplace safety violations for the 2023.
This further confirms the prevalence of the issue, giving you yet another reason to work on minimizing the amount of equipment you have sitting idly.
Shorter Equipment Lifespan
It’s true: equipment that remains idle for prolonged periods doesn’t suffer typical wear and tear.
However, the consequences are very much there, just in a different shape and form.
The wear from inactivity, such as accumulated rust or general degradation, has a considerable impact on the equipment’s lifespan—and that’s if we disregard more serious damage.
Let’s take a look at some common types of damage that your idle equipment can suffer.
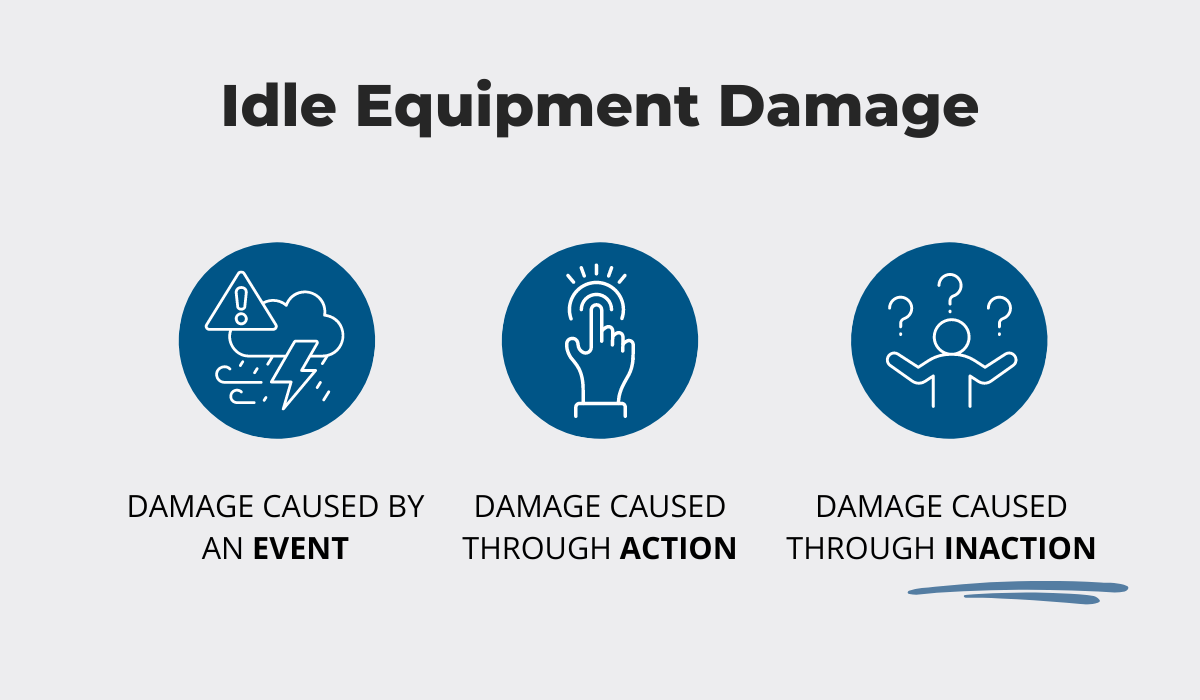
In cases of extreme weather conditions, sheltering less used equipment would come second to protecting key assets, increasing the likelihood of damage.
Likewise, operating a piece of equipment that’s idle a lot of the time, doesn’t mean just higher chances of malfunction.
It simply doesn’t come as naturally or easily as handling regularly used equipment, which increases the chances of the operator making a mistake.
Finally, damage incurred through inaction happens when faulty components are left unattended, and gradual wear and tear become more pronounced.
Altogether, these kinds of damage impact your equipment’s overall lifespan and shorten its useful life.
The easiest way for companies to keep this window of cost-effectiveness and productivity open is through regular maintenance and prompt repair.
Preventive maintenance ensures equipment longevity through routine checks, and implementing a maintenance program is made easier with different software solutions.
One of them is our own asset tracking solution, GoCodes Asset Tracking.
It combines cloud-based software, an in-app scanner, and custom QR code labels to give you total visibility and control over your assets.
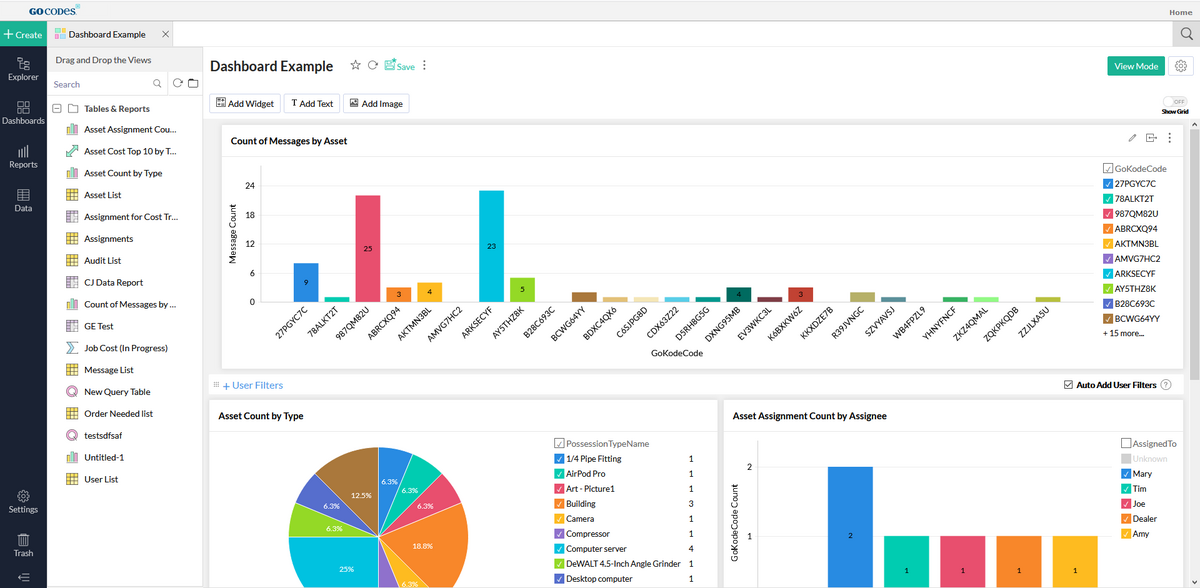
The system incorporates numerous tracking and reporting features and makes asset life cycle management a breeze.
Outside of regular maintenance, different service tasks can easily be scheduled via any device, based on the data and insights from the field.
Plus, thanks to helpful email reminders, they won’t be forgotten.
Investing in technology like that can help you ensure that you’re making the most of your equipment—both in terms of day-to-day operations and its overall lifespan.
Loss of Competitive Edge
Remaining flexible and agile is key to standing out among competitors.
But with idle assets, the growth opportunities are limited.
How do these small inefficiencies, brought upon by idle equipment, reduce the competitiveness of construction companies?
Well, having idle equipment means carrying dead weight.
Idle equipment doesn’t contribute to revenue, yet it ties up the capital and prevents you from allocating your resources elsewhere.
Let’s say your company is looking to invest in digital transformation and reap its benefits.
But, you soon realize that you have to postpone this strategic move, in part because of the mounting costs of one idle excavator and several other underutilized assets.
The fact of the matter is, construction is a rapidly changing and very competitive industry.
This means that companies need agility and flexibility to make smart business decisions and stay ahead.
Lorna Barrow, an entrepreneur and trainer who specializes in transforming small businesses, also notes the importance of adaptable business models.
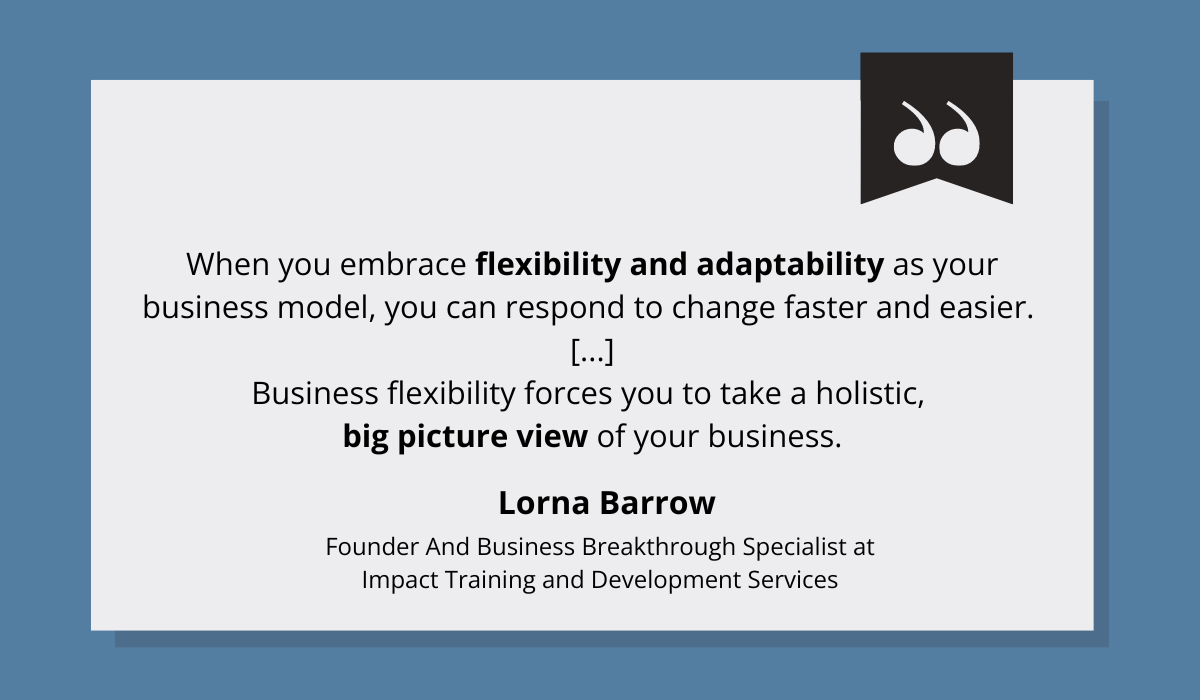
Nurturing flexibility also brings clarity about the strategic direction of your business, and in the case of idle equipment, it can take two main directions.
Some businesses may hold onto their equipment for a while longer and focus on enhancing their asset management and workflows.
Others might explore renting and selling options.
Regardless of which direction you decide to take, the final destination is the same:
You want to make the most of your construction equipment, put yourself in a better position to adapt to shifting market demands, and seize new opportunities.
Conclusion
Holding on to idle equipment slows down construction businesses in more ways than one, impeding processes and jeopardizing growth.
Even with costly maintenance and repairs, idle equipment maintains a shortened lifespan and can still lead to safety hazards.
What’s worse, it causes a drop in productivity and efficiency, tying up resources that could be used more strategically.
There’s a way out of it, however, and it begins with you tracking your equipment utilization.
So, what are you waiting for? It’s time to move forward!