Key Takeaways:
- Delays caused by weather, supply chain disruptions, and labor shortages lead to increased costs.
- Inadequate equipment maintenance results in project delays.
- Poor communication is the main cause of construction rework.
- Manual processes and fragmented data management cause inefficiencies and errors.
Building a house, a skyscraper, or a bridge is costly.
However, with the right budget and a clear picture of your expenses at every step, it’s manageable.
But what about hidden costs that creep up unexpectedly?
Consider the expense of when it rains for days, halting work because workers can’t pour concrete.
Or when the crucial equipment breaks down unexpectedly, leading to costly repairs and even more delays, or additional expenses of renting new equipment.
These hidden costs can quickly add up, making your head and wallet spin.
But that’s why we are here.
Today, we will reveal five hidden costs you may be experiencing in your construction company, and provide solutions to prevent these costs from affecting your profits.
Let’s get into it.
In this article...
Unforeseen Delays
Delays are a significant source of extra costs in construction.
Unfortunately, they are a reality for many construction companies, and you have likely experienced this firsthand.
Delays can be caused by various factors, such as:
- weather,
- supply chain disruptions,
- labor shortages,
- crucial equipment breaking down unexpectedly, or
- simply by poor project planning.
Let’s go through some of these in more detail.
Bad weather can significantly extend construction timelines.
To be precise, one UK study from 2017 revealed that it extends the duration by an average of 21%.
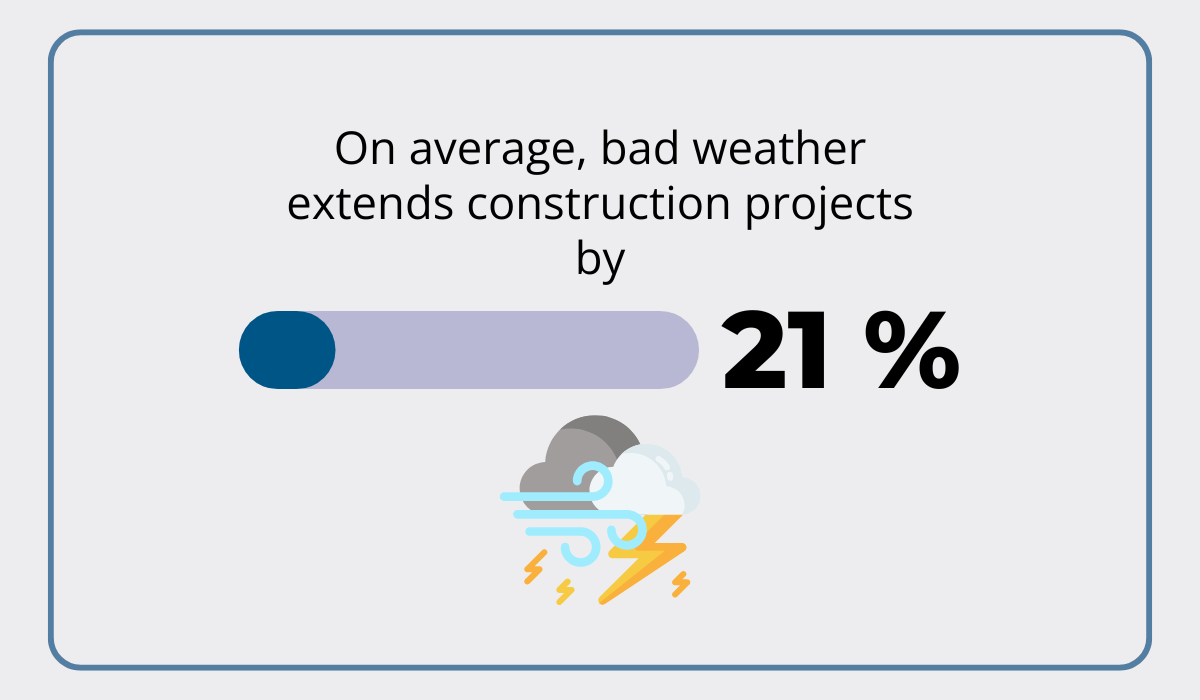
This means your project might take twelve months instead of ten, adding substantial costs and frustration.
Labor shortages also contribute to delays, and this is a pressing challenge today.
According to the AGC & Autodesk Workforce Survey, 88% of US construction firms struggled to find workers in 2023.
A significant reason for this shortage is the lack of qualified candidates, with 68% of firms reporting that applicants lack the necessary skills.
And when you don’t have enough skilled workers, projects slow down, while costs and rework rise.
Supply chain disruptions further exacerbate the problem.
The same survey reports that companies in the US are dealing with extreme lead times for electrical equipment such as transformers and switchgear, as well as for heating, ventilating, and air conditioning equipment.
Given all these challenges, it’s no surprise that 65% of firms report project delays due to supply chain issues, and 61% cite labor shortages as a cause.
These factors combined significantly increase costs, which then leads to project cancellations, postponements, or scaling back.
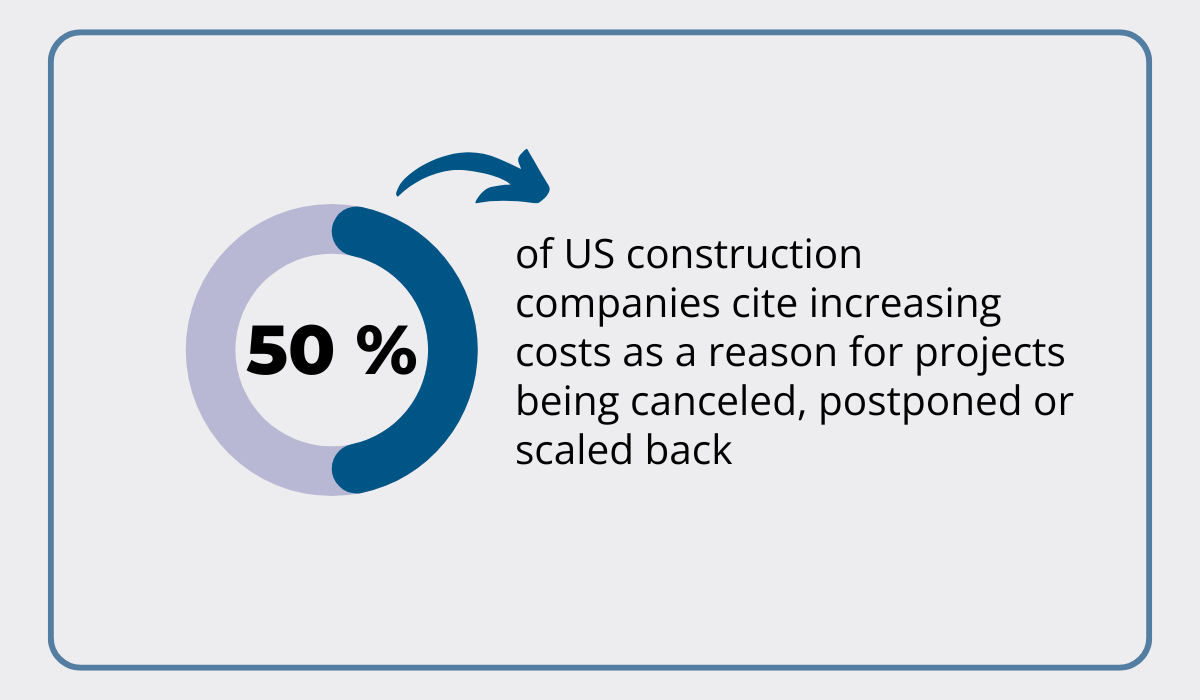
So, to combat construction delays and associated costs, you need effective solutions.
One key strategy is to implement project management software to better plan and manage your construction projects.
This kind of software allows you to monitor project progress in detail, identify potential delays early, and reschedule tasks to prevent disruptions.
By keeping a close eye on every aspect of your project, you can anticipate problems before they occur and take corrective action.
Additionally, it’s crucial to develop contingency plans.
The fact of the matter is that some delays are simply unavoidable.
So, having backup suppliers, flexible schedules, and alternative resources ready can help mitigate their impact.
A well-prepared contingency plan will help you quickly adapt to unexpected issues without significant delays—or costs.
Finally, addressing labor and skill shortages can only be achieved by investing in the training and professional development of your workers.
All in all, proactively managing your projects, preparing for the unexpected, and investing in your workforce can minimize the impact of delays on your construction operations and protect your bottom line.
Equipment Maintenance
Imagine you’re in the middle of a major construction project.
Everything is running smoothly until a crucial piece of equipment breaks down unexpectedly.
Suddenly, your project grinds to a halt, and you’re facing hefty repair costs, the costs of idle workers, and delayed timelines.
This scenario is all too common in the construction industry.
But why does it happen?
According to a research paper from the International Journal of Engineering and Science Invention (IJESI), for around 40% of total construction project cost overruns, the culprit is nothing less than poor equipment maintenance.
Repair costs alone for such unexpected breakages can average $1,560 to $3,120 per year just to replace defective components.
But the true cost goes beyond just the price of repairs.
Jeff Krupp, former Director of Applications at Cat Digital, explains that this downtime is a significant drain on productivity, too.
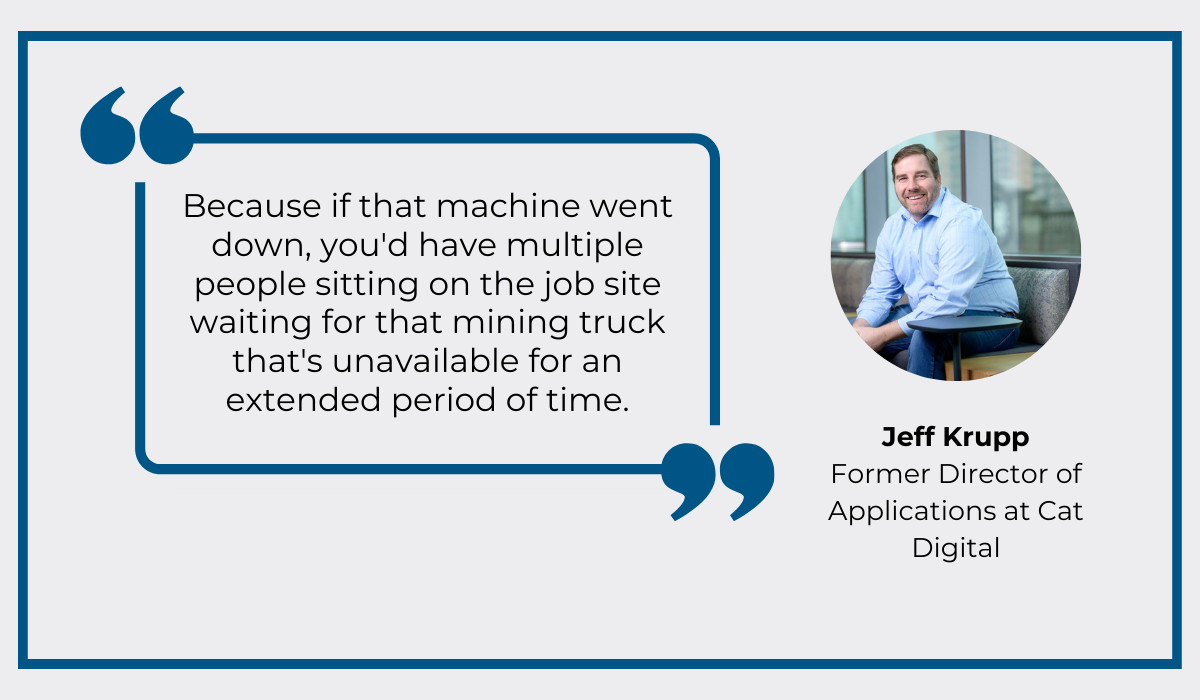
What’s more, a study by Caterpillar found that unplanned downtime can cost project managers around 400 to 800 non-productive hours per year, per machine.
Given these staggering numbers, it’s clear that regular equipment maintenance should be a top priority for any construction company.
But how can you manage maintenance effectively when you have hundreds or even thousands of tools, machines, and vehicles?
The solution lies in a comprehensive asset management system.
With such a system, you can keep all asset information—including maintenance data—in one central database.
Our very own GoCodes Asset Tracking offers exactly this kind of solution.
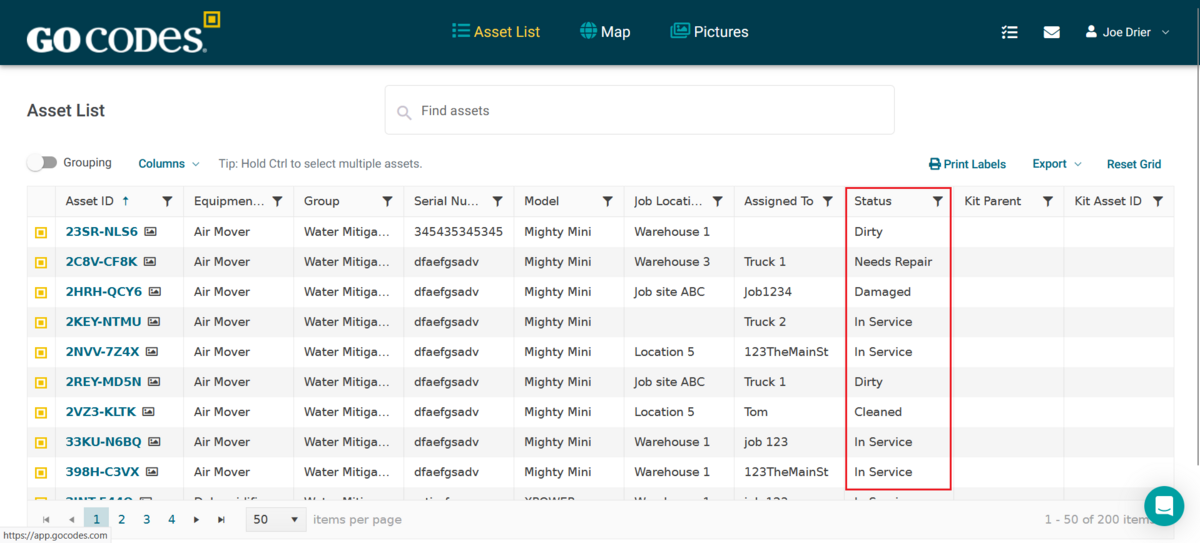
But instead of just helping you monitor the condition of your equipment, GoCodes Asset Tracking also allows you to schedule and assign maintenance tasks for each asset to the right personnel.
GoCodes Asset Tracking combines a software platform, a mobile app, and QR-code labels that you attach to your equipment, both big and small.
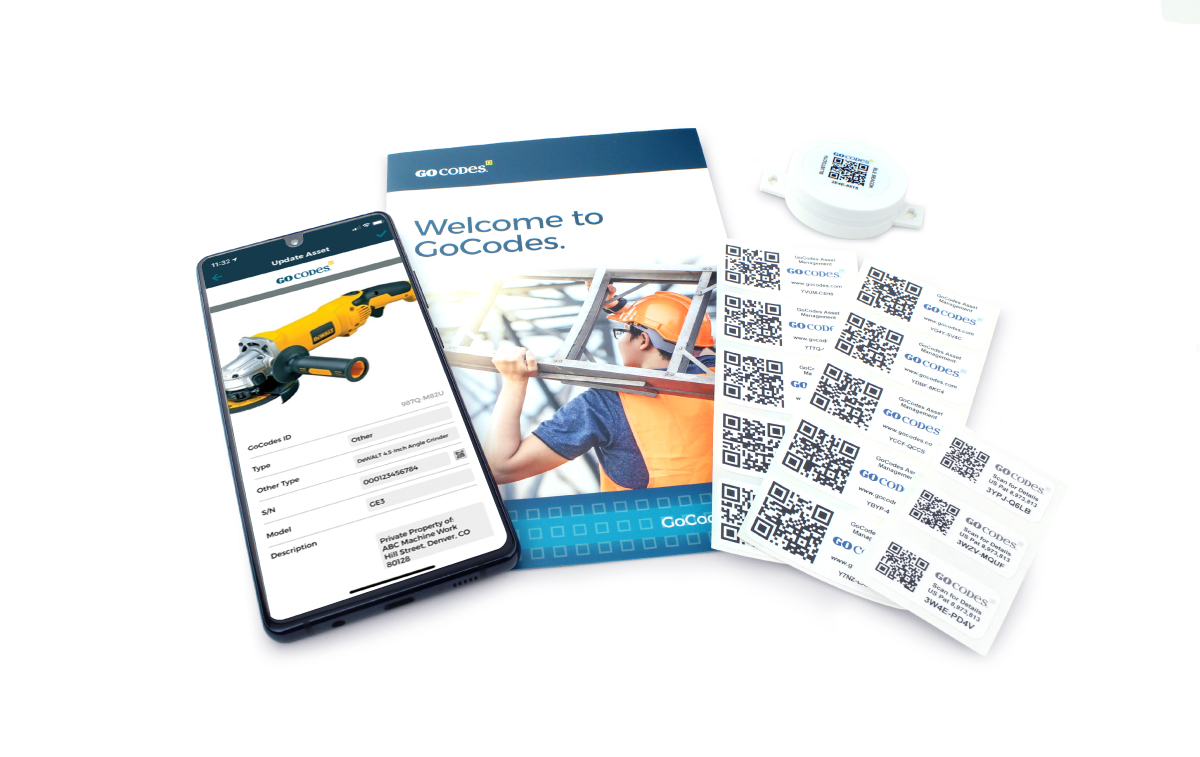
For heavy machinery and vehicles, we even provide real-time GPS tracking devices.
With GoCodes Asset Tracking, you always know where your assets are, who is using them, and what their maintenance status is.
The best part?
You can schedule future service tasks for all your equipment from one place and be reminded by email when the date is approaching.
Check out how easy it is to set up this feature in our short video below:
Source: GoCodes Asset Tracking on YouTube
Simply put, implementing such a tool in your construction company means that you’re making sure your equipment is always in top condition.
This not only reduces unexpected repair costs but also minimizes project delays, keeping your projects on track, and your business profitable.
Rework
Have you ever had to remove and replace concrete because you didn’t test the mix for the correct strength?
Or have you ever worked with incomplete and unclear designs that led to errors and confusion, and you had to redo all the work?
These are classic examples of rework due to poor quality control and planning.
Rework happens for various other reasons.
PlanRadar, a construction management software, conducted a survey of more than 2,500 active users to understand why.
They found that poor communication was the top cause, followed by a lack of organization and poor document control, as well as quality control mistakes.
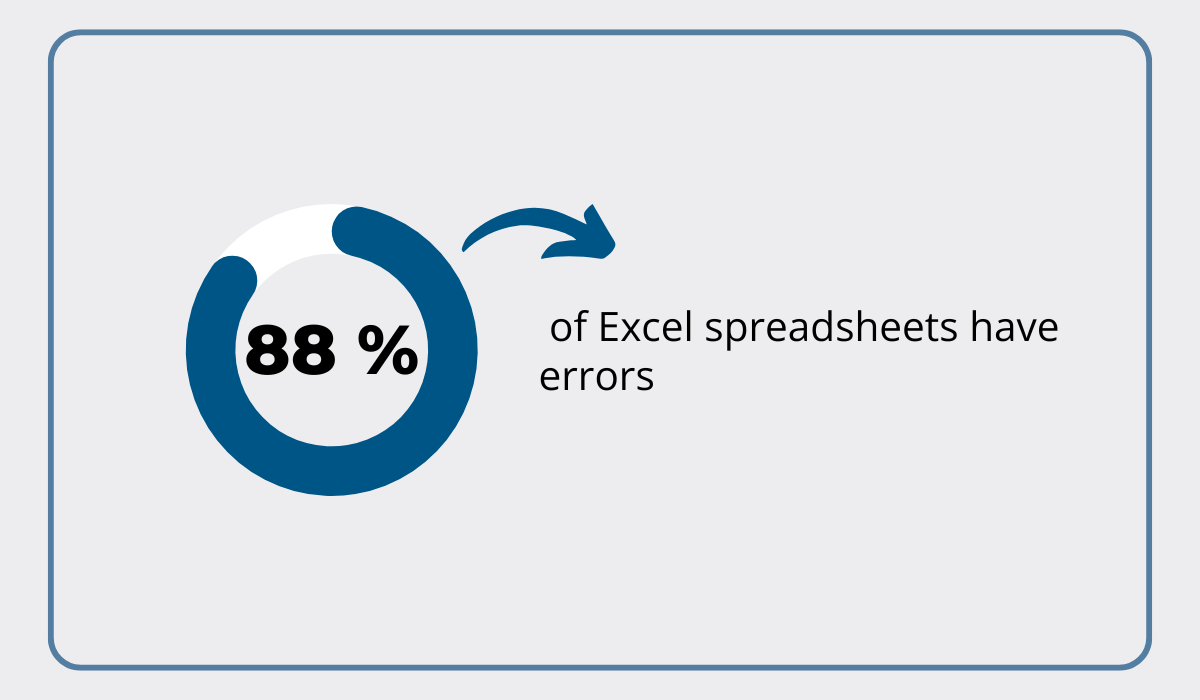
Other significant causes include:
- improper planning,
- lack of skilled labor, and
- poor-quality materials.
Sometimes, rework happens when clients change their minds because the project’s scope wasn’t well defined.
Regardless of the cause, rework can severely eat into your profits, as it increases costs and extends project timelines.
It can also lead to customer dissatisfaction and damage your company’s reputation—both of which have long-term financial impacts.
So, how can you avoid rework in your construction projects?
The number one solution is better communication between all stakeholders.
According to the Project Management Institute (PMI), projects with highly effective communication are 71% more likely to finish on time, 76% more likely to stay within budget, and 80% more likely to meet their original goals.
Investing in communication platforms or project management software where everyone can track progress and access necessary documents is, therefore, crucial.
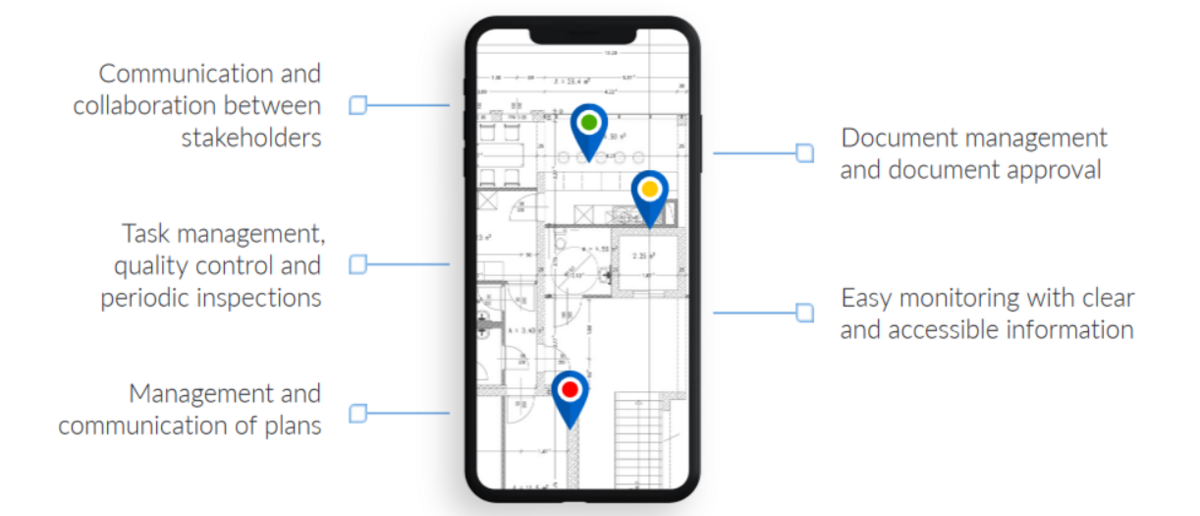
For instance, PlanRadar’s clients report a 52% reduction in required rework after implementing their tool.
In summary, rework is a hidden cost that can drastically affect your bottom line.
However, when you focus on better communication, thorough planning, and using project management tools, you can minimize it and keep your projects on track in every way.
Lack of Digitalization
Manual processes, or lack of digitalization, are a significant source of hidden costs in construction.
While manual methods might seem manageable, they often introduce inefficiencies, human errors, and delays that hurt your bottom line.
Think about how you log your workers’ daily hours, for instance.
Do they report manually, and you jot it down in Excel?
How do you plan your projects, and do you use spreadsheets for cost management?
If you said yes, it is time to rethink your approach.
Namely, statistics show that almost 90% of Excel spreadsheets contain mistakes.
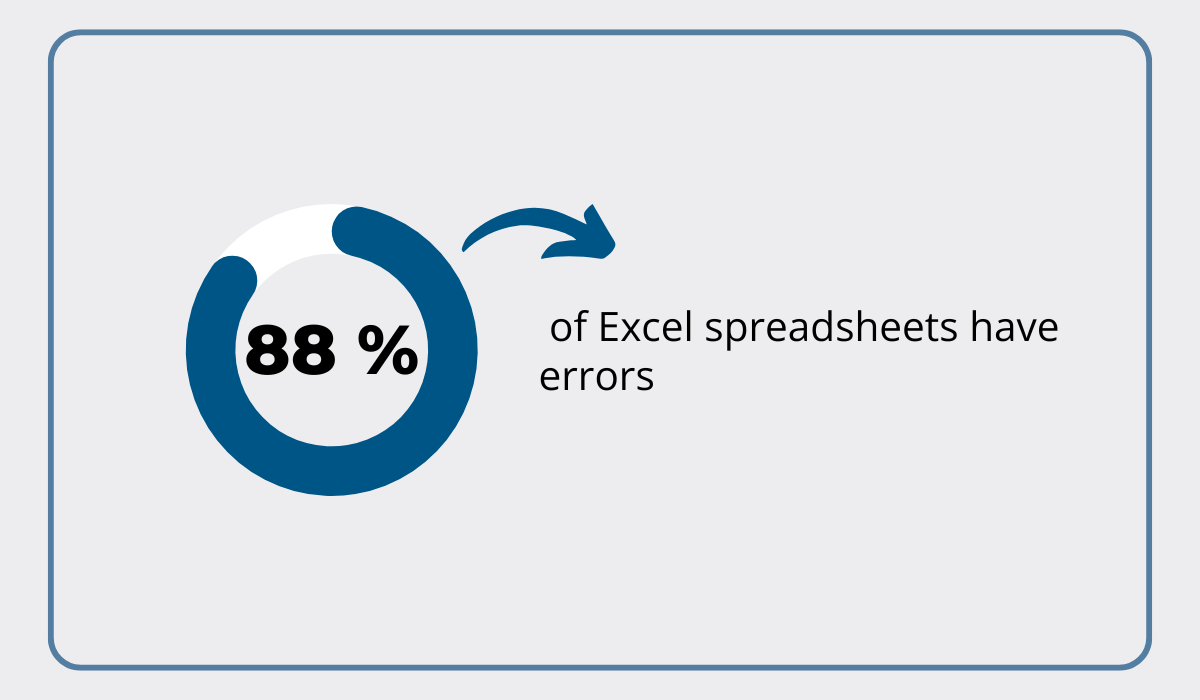
Every manual entry is a potential error point, and these errors cost time and money to fix.
Now, consider how you manage project information.
Is it scattered across paper files, different software systems, and Excel sheets?
When data is stored in multiple places, it becomes nearly impossible to maintain a single, accurate source of truth.
As Petter Merok, an Industry Executive at Microsoft, points out:
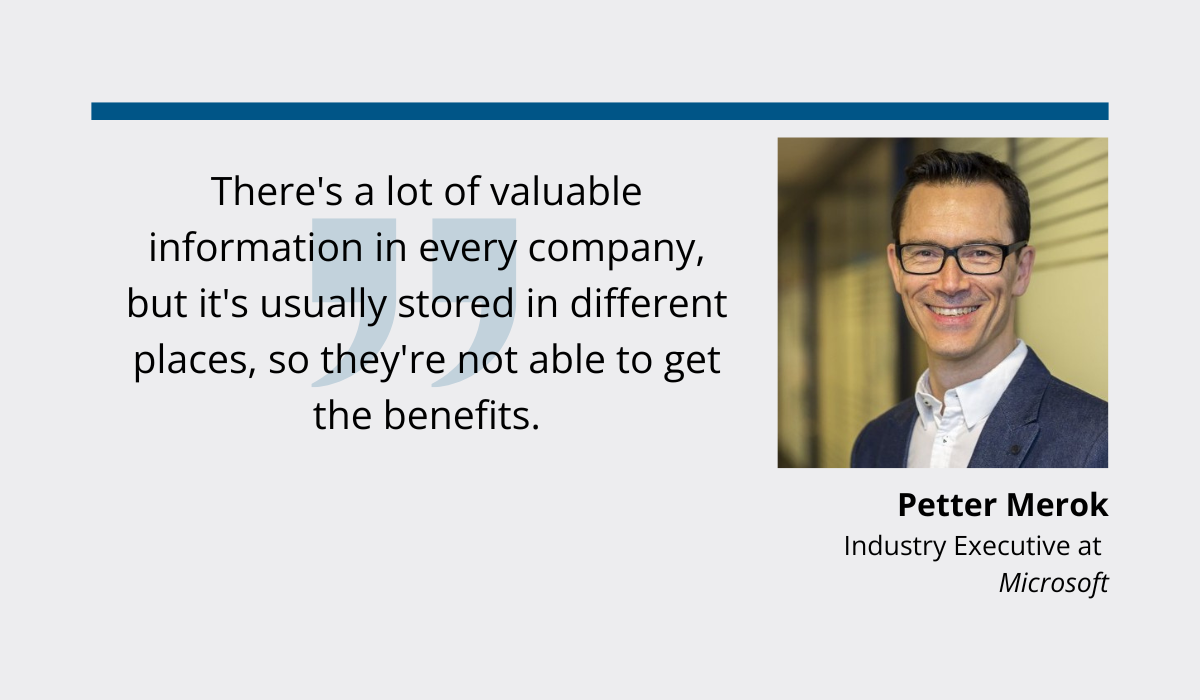
This fragmented data leads to inconsistencies, miscommunications, and delays.
Moreover, without digital tools, tracking project progress and coordinating teams can be a nightmare.
Miscommunications due to outdated information can delay projects, increase costs, and frustrate clients.
And delays not only inflate costs but also affect your reputation and future business prospects.
The solution is clear: digitalize your operations.
Invest in construction management software that integrates scheduling, cost management, and resource allocation.
This ensures all data is centralized and accessible in real time, thereby reducing errors and boosting efficiency.
Consider this: 69% of organizations that complete projects on time or ahead of schedule use project management software.
And time is money!

In other words, digital tools do it both: improve project timelines and cut costs.
But there are other tools you can start with.
For example, you can adopt digital communication tools like Slack to streamline coordination between teams, ensuring everyone has the latest updates, even when on the construction site.
Then, asset management software, for example, can help you track equipment and materials, optimize usage, and plan maintenance to avoid unexpected breakdowns.
When you digitalize these processes, you can reduce mistakes and make sure you have all data in one place.
As you can see, the hidden costs of manual processes and fragmented data are significant.
However, by embracing various digital tools, you can streamline operations, reduce errors, and enhance project outcomes.
But digitalization isn’t just an upgrade—it’s essential for staying competitive and profitable in today’s construction industry.
Material Price Fluctuations
Imagine you’re in the middle of a huge construction project, and suddenly, the cost of essential materials, like lumber for example, skyrockets.
In fact, you might have experienced this during the COVID-19 pandemic when lumber prices surged drastically.
Sawmills shut down while the housing market boomed, driving lumber prices from $200 to over $1,500 per 1,000 board feet.
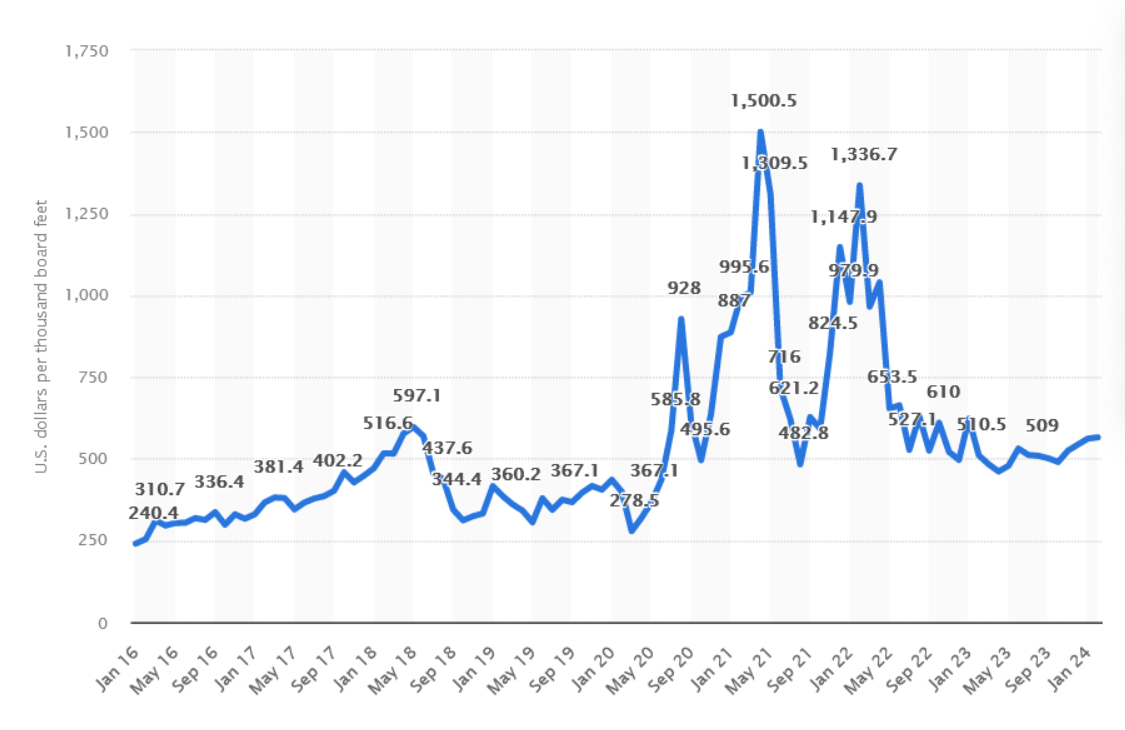
This price hike added about $35,000 to the cost of a typical family home.
Supply chain disruptions and labor shortages only made things worse, delaying shipments and increasing costs.
Steel is another example of how market volatility can wreak havoc on construction budgets.
In 2018, the U.S. imposed tariffs on steel imports, causing domestic prices to rise sharply.
At some point, the tariffs led to a 40% increase in steel prices, affecting industries that rely heavily on this material, including construction.
These price hikes translated into increased project costs, delays, and reduced profit margins for construction companies.
As a construction company owner, you know how devastating material price fluctuations can be on your bottom line.
But how can you prepare for and minimize these unpredictable costs?
Here are some practical strategies to help you stay ahead:
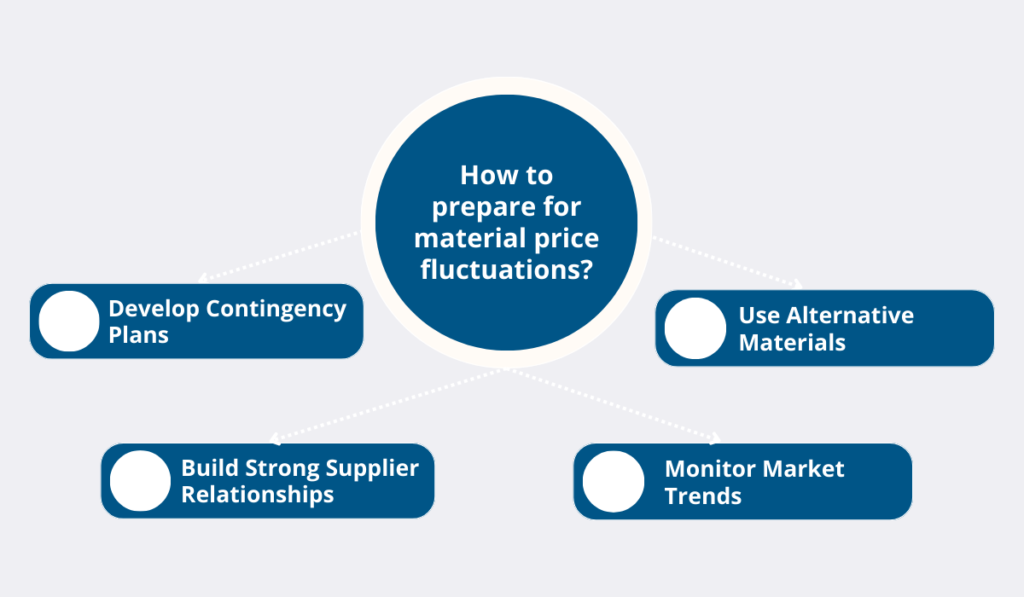
First and foremost, always have a financial cushion—a contingency plan.
Allocate a portion of your budget to accommodate sudden price increases and delays.
This safety net can absorb unexpected costs without derailing your project.
Second, cultivate good relationships with multiple suppliers, as this can secure better deals and a more reliable supply of materials.
When you have strong connections, you gain leverage to negotiate prices and delivery schedules, reducing your vulnerability to market fluctuations.
On top of that, keep your options open.
If the price of one material skyrockets, explore alternative materials where applicable.
Having flexible material options can help you manage costs more effectively.
Finally, stay informed.
Regularly check market trends and forecasts to anticipate potential price changes.
If you time your purchases strategically, you can lock in prices before they rise, saving you money in the long run.
By putting yourself in a proactive mindset and implementing these strategies, you can better handle material price fluctuations.
This will help you manage costs and ensure that your projects stay on track and within budget.
Conclusion
Have you found yourself nodding along as we uncovered the hidden costs lurking in construction?
Perhaps rainy days have halted your concrete pours, or equipment breakdowns have sent your project timelines spiraling.
If so, it’s time to take a proactive approach and prevent these hidden costs from shaking your profits.
The solution is clear: embrace technology.
Tools like project management software, communication platforms, and asset management systems can significantly reduce hidden costs by streamlining operations, improving coordination, and minimizing errors.
By digitalizing your construction processes, you can stay ahead of the curve, protect your bottom line, and ensure the success of your projects.
So, don’t let hidden costs erode your profits any longer—take action and digitalize your construction operations today.