Key Takeaways
- Clearly defining what constitutes equipment idle time and keeping track of it is the first step toward reducing it.
- Construction companies that want to reduce the idle time of their equipment should focus on making their project scheduling more efficient.
- Better communication on the construction site can help ensure that equipment doesn’t sit idle.
In construction, managing equipment efficiently is crucial for maximizing productivity and controlling costs.
However, when machinery is functional but not performing work, this leads to equipment idle time—a common yet often overlooked issue that lowers productivity and increases costs.
In this article, we’ll explore four practical tips that can help you reduce equipment idle time and optimize construction operations.
In this article...
Address Workflow Inefficiencies
Among many factors that can lead to longer equipment idle times, construction workflow inefficiencies are significant culprits.
More precisely, construction equipment can be forced to wait due to issues like:
- poor project scheduling and coordination,
- material delivery delays,
- inefficient task sequencing, and
- operator unavailability.
Before delving into how these and other internal inefficiencies can be addressed, it’s important to note that, while equipment idle time can be reduced, it can’t be entirely eliminated.
In other words, some idle time is always to be expected on any job, let alone construction.
For instance, when an operator takes a lunch break, the equipment is typically not used during that period, even though it technically could be working on the assigned task.

That’s why it’s essential to distinguish between normal, to-be-expected idle time and those instances where idle time is caused by preventable inefficiencies.
So, how can you address the internal workflow issues we mentioned above?
Typically, most of them stem from inefficient project scheduling and coordination.
These processes can be significantly improved with the help of project scheduling tools.
Such tools allow you to visualize all planned construction tasks, identify their interdependencies and optimal sequence, add project milestones, and insert subtasks.
You can see an example of such a tool below.
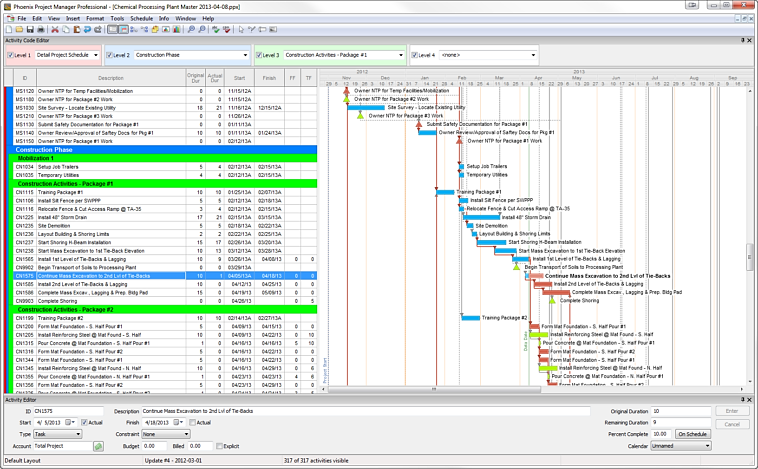
Furthermore, scheduling tools enable you to include buffer times and contingencies in the project schedule.
This makes it more flexible to accommodate unforeseen changes and reassign your equipment and workers to minimize idle time.
As part of scheduling, proper resource allocation planning can also streamline other issues that might prevent scheduled tasks from starting on time, such as material delivery delays and operator unavailability.
Additionally, material-waiting times can be reduced by coordinating with suppliers for just-in-time (JIT) deliveries or maintaining a buffer stock of critical materials.
As for operator shortage (e.g., sick leave), cross-training operators to handle multiple types of equipment can increase flexibility and reduce the related equipment idle time.
Lastly, consider that one survey revealed that 68% of construction professionals see poor schedule management as the main contributor to lower productivity, including idle time.
This only further underscores a close connection between addressing internal workflow inefficiencies and reducing equipment idle time.
Develop a Preventive Maintenance Program
A sudden breakdown of one piece of construction equipment can cause a cascade of delays, forcing other equipment on-site to sit idle while the task that the failed equipment was performing is completed.
To prevent—or at least minimize—such idle times, it’s best to develop and adhere to a comprehensive preventive maintenance program.
This program involves regularly scheduled inspections and servicing of equipment to ensure that it remains in optimal working condition, thus minimizing breakdowns and the resulting idle time for other equipment.
Moreover, this is a financially sound move because run-to-fail and then repair strategy is significantly more expensive.
David Auton, senior director at Cushman and Wakefield, confirms this.
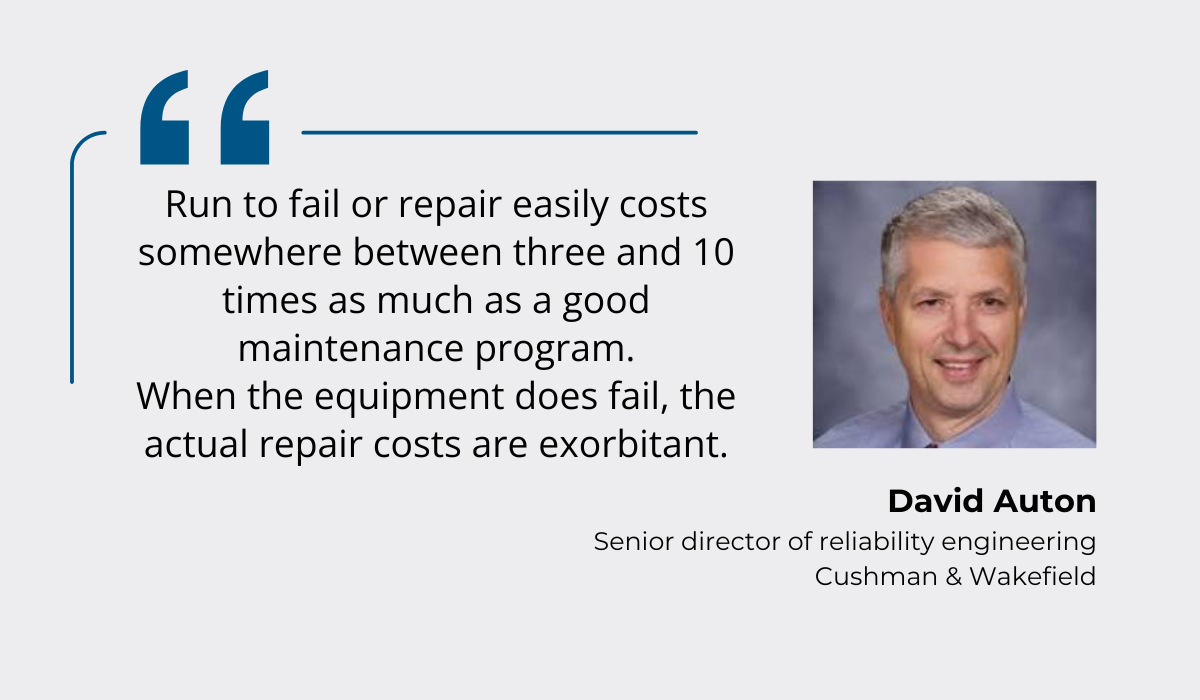
In addition to its cost-effectiveness, a preventive maintenance program improves scheduling accuracy.
In other words, it allows managers to integrate scheduled maintenance activities into the overall project schedule.
This means that preventive maintenance can be performed while equipment is not scheduled to perform any tasks.
So, what is required to develop a preventive maintenance program?
For starters, you’ll need to integrate manufacturers’ maintenance recommendations (especially during the warranty period) and your technicians’ operational experience into your program.
Once the program is set up, you’ll need a system that keeps track of all planned and completed service tasks or, more precisely, maintenance management software.
Such software can automatically alert equipment managers and assigned technicians of upcoming maintenance, track completed tasks, and maintain detailed maintenance records.
Here’s an example of a scheduled service notification that designated staff would receive by email.
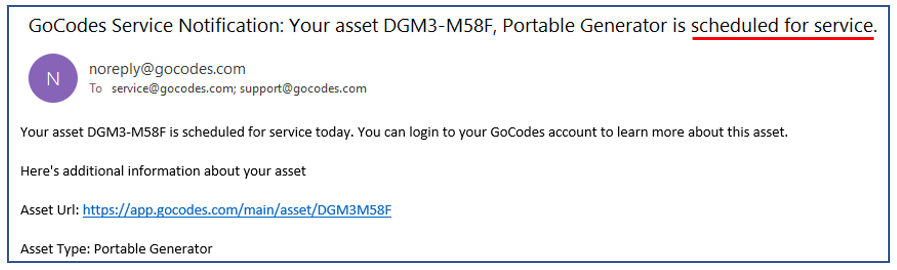
This means that preventive maintenance tasks, such as oil and filter changes, hydraulic system checks, and critical part replacements, will be done according to the schedule and manufacturer recommendations.
To recap, a preventive maintenance program ensures that planned equipment downtime overlaps with equipment standby time and that unexpected breakdowns and idle time are minimized.
Enhance Communication on the Construction Site
Effective communication on the construction site is pivotal for reducing equipment idle time.
Why?
Because many of the idle periods experienced by construction equipment scheduled to perform a specific task are caused by poor communication.
For instance, if a late delivery of steel beams is not properly communicated to the site manager, both the crane and its operator scheduled to unload them will experience idle time.
Conversely, if the site manager is timely notified of, say, a 4-hour delay in delivery, they can reschedule the crane and operator to perform other tasks in the meantime.
This minimizes idle time and ensures more efficient use of resources.
Of course, this is but one of countless examples highlighting the importance of effective jobsite communication.
When extended to all project stakeholders, efficient communication stands as a key factor for successful project completion.
Research by Pro Crew Schedule clearly demonstrates this.
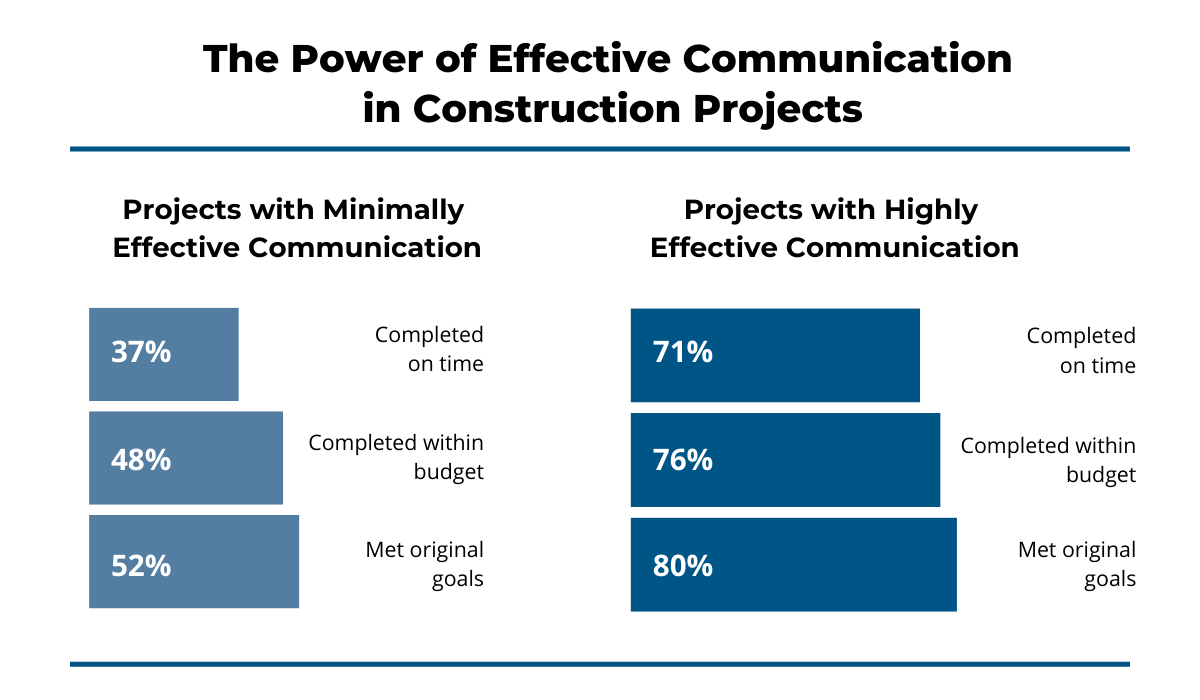
These numbers show the significant positive impacts that effective communication between on-site and off-site project teams has on project outcomes, i.e., its schedule, budget, and goals.
So, what can you do to enhance job site communication among all relevant project stakeholders?
If you already don’t have it, cloud-based all-in-one construction software or another centralized communication platform is the best way to keep everyone informed in real time.
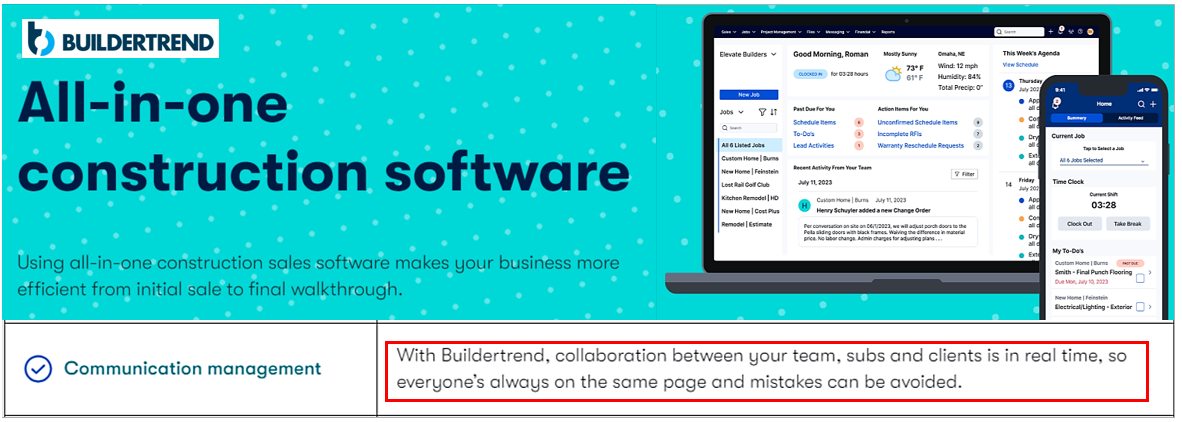
Using such tools, all construction team members can be updated about any scheduling, task assignment, or delivery changes, thereby preventing idle time due to outdated or incomplete information.
Another key component refers to establishing a clear communication chain of command.
That way, everyone knows who to contact for specific issues, which prevents confusion and minimizes idle time during problem-solving and decision-making.
Lastly, one more effective way to reduce equipment idle time is to hold daily briefings.
More specifically, when reviewing the day’s schedule, you can highlight critical tasks and their sequence, so all team members are aware of their responsibilities and timelines.
All in all, streamlined construction site communication is the best remedy for many causes of equipment idle time.
Keep Track of Idle Time
To keep track of equipment idle time, you first need a clear understanding of what constitutes idle time for your company.
This will help you determine which equipment parameters should be monitored to identify idle time patterns and uncover their underlying causes.
From there, you can consider what kind of equipment-tracking technology you should leverage to collect equipment data relevant to devising and implementing appropriate strategies for reducing idle time.
For starters, consider the possibility that you might already have what you need.
More specifically, your equipment—especially newer models—might already have built-in telematics.
This onboard telematics typically consists of a GPS tracker integrated with various internal equipment sensors that track, among other things:
- when equipment is operating,
- when its engine is idling, and
- when it’s shut down.
In such cases, all you need is to integrate this built-in telematics with equipment tracking software to access the data relevant to idle time.
This would include, for instance, engine idling events and shut-down time during scheduled operating hours.
Even if your equipment lacks internal telematics, modern GPS trackers equipped with their own sensors can serve the same purpose.
For instance, our equipment tracking solution, GoCodes Asset Tracking, offers real-time GPS trackers that continuously monitor the location of your equipment, engine hours, and much more.
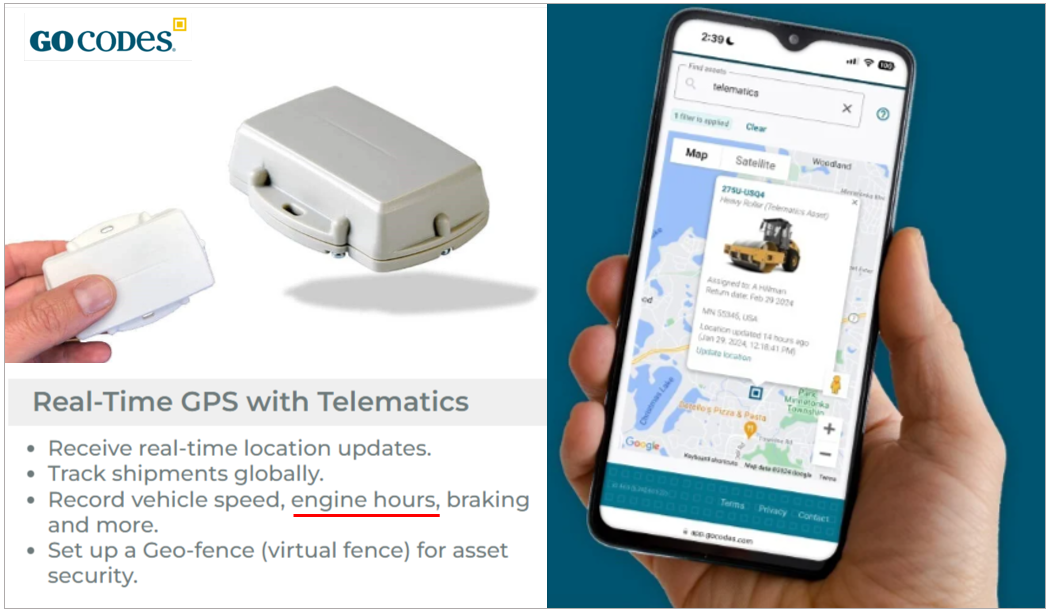
In addition, you can use GoCodes Asset Tracking to schedule and track maintenance tasks and set up automated alerts for upcoming maintenance.
These functionalities allow you to operationalize your preventive maintenance program, which is an essential part of your idle time-lowering efforts, as we discussed.
Another useful feature that can help reduce both equipment and staff idle time is the GoCodes Asset Tracking’ automated equipment check-in/check-out feature.
More precisely, rugged QR codes attached to equipment and tools and our smartphone app with a digital scanner enable workers to simply scan the asset they’re taking from the storage yard or toolroom, and the system will record that fact.
It will even send automated reminders when an asset is to be returned.
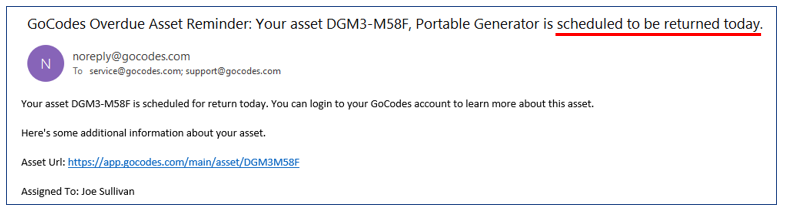
Again, this contributes to less idle time resulting from specific equipment or tools not being available when scheduled to perform a task.
Given all the above, it’s clear that telematics is the best way to track equipment data relevant to reducing idle time.
From there, such data can be integrated with other project data to provide a comprehensive view of equipment usage and efficiency.
When analyzed, all this information can reveal valuable insights on how to minimize equipment idle time, allowing you to implement targeted measures.
Conclusion
So, what conclusions can be drawn from these idle time-reducing tips?
Firstly, you should be clear about what equipment idle time is, and how prevalent it is in your operations.
Then, you should address those workflow inefficiencies that cause most idle time, such as poor project planning and scheduling.
Other important actions include preventing idle time through a preventive maintenance program and enhanced jobsite communication.
Lastly, you should leverage relevant software tools and tracking technologies to keep track of idle time, extract insights, and devise appropriate measures to minimize it.
When put together, these activities will allow you to meet your goal and get that idle time down.