Struggling with misplaced, lost, or poorly managed assets in your construction business?
Of course, having the right tools at your disposal at any time can help your construction business function properly and grow further.
On the other hand, a lack of efficient equipment management can quickly sabotage its productivity and profitability.
That’s why, in this article, we guide you to identify the signs that signal the necessity for a systematic equipment management upgrade.
You’ll uncover when it’s time to invest in the equipment tracking software to transform your equipment management, streamline operations, and ultimately boost your bottom line.
Read on to learn about this game-changing solution.
In this article...
You Don’t Know How Much Equipment You Have
Without equipment tracking software, your construction company must track all of your equipment using inefficient methods, such as paper records or digital spreadsheets.
This might sound like a straightforward, low-cost option, but attempting to conduct business this way will cost you money in the end due to its inefficiencies.
For example, there’s a better-than-average chance that your equipment records are inaccurate because equipment records might house hidden errors as a result of human mistakes in transferring data.
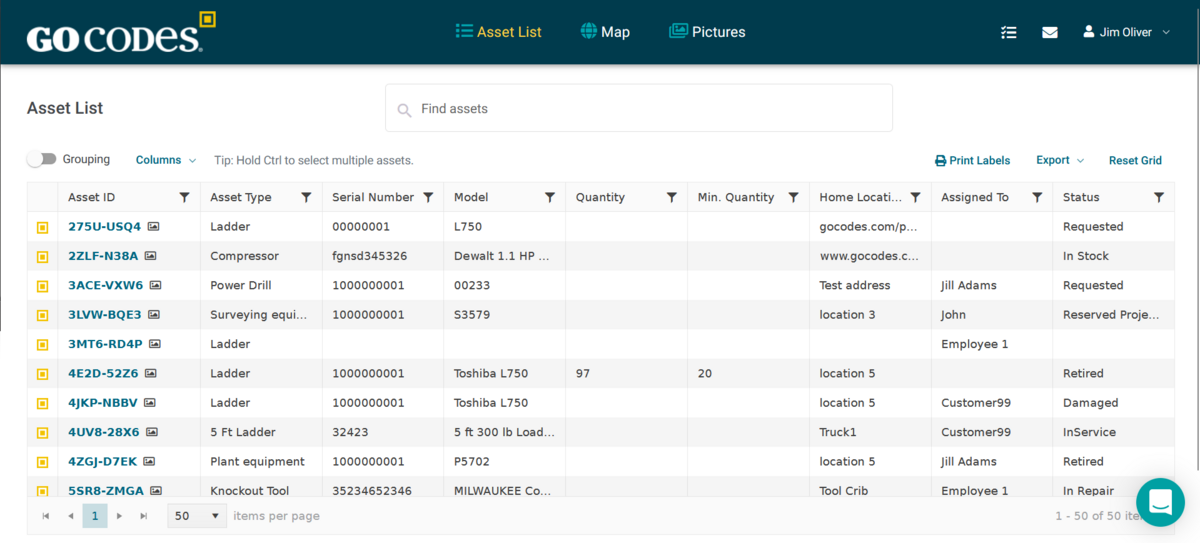
As time passes and data is transferred quarter to quarter and year to year, these errors can compound quickly.
While the mistake seems small at first, this can eventually lead to wrong decisions, such as ordering unnecessary supplies, missing a project deadline due to the lack of materials, and missing deadlines for warranties or compliance proofs.
Any of these mistakes can prove expensive.
When your information is hard to maintain, it easily becomes outdated, and you face the increased likelihood of having ghost assets.
These are items that appear on your inventory lists but are actually missing, damaged, donated, gone, stolen, or otherwise unusable.
Why is this a problem?
Because assets that are there only on paper can be a sign of underlying problems such as equipment theft or loss and can lead to additional expenditures like higher tax or insurance rates.
Here are just a few of these problems visually presented:
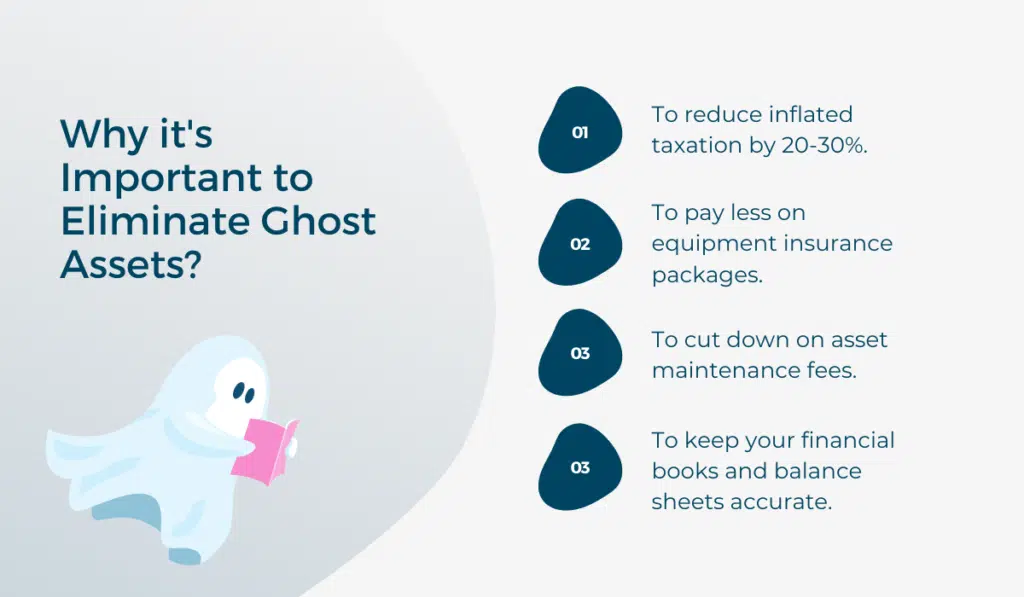
Overall, ghost assets can greatly impact your construction company’s bottom line.
Your company’s resources are indirectly spent on maintaining or serving an asset that is no longer contributing in any way.
Ghost assets can raise your property taxes and insurance premiums and present false budgeting and workflow information.
Luckily, with equipment tracking software, especially if it has an equipment check-in/check-out feature, you can quickly get to the bottom of things.
You can finally have an accurate account of your inventory and never again be haunted by asset ghosts.
You Keep Having to Rent More Equipment
By not knowing exactly how much equipment your company has, it is easy to accidentally rent unnecessary construction equipment.
The costs of renting more construction equipment than is necessary will quickly add up.
However, by using equipment tracking software, your construction company will avoid wasting money on renting unnecessary equipment.
This cost might not seem like much in the enormous budget of a large project, but the numbers for renting things, especially heavy machinery, compound quite fast:
- Excavator – $450 – $3,500/day
- Forklifts – $600/day
- Backhoe loader – $480/day
Losing money simply because your assets are hidden is an easy fix.
The right equipment tracking software can show you in an instant which assets are available, where they are located, what’s their status, and when they are needed next.
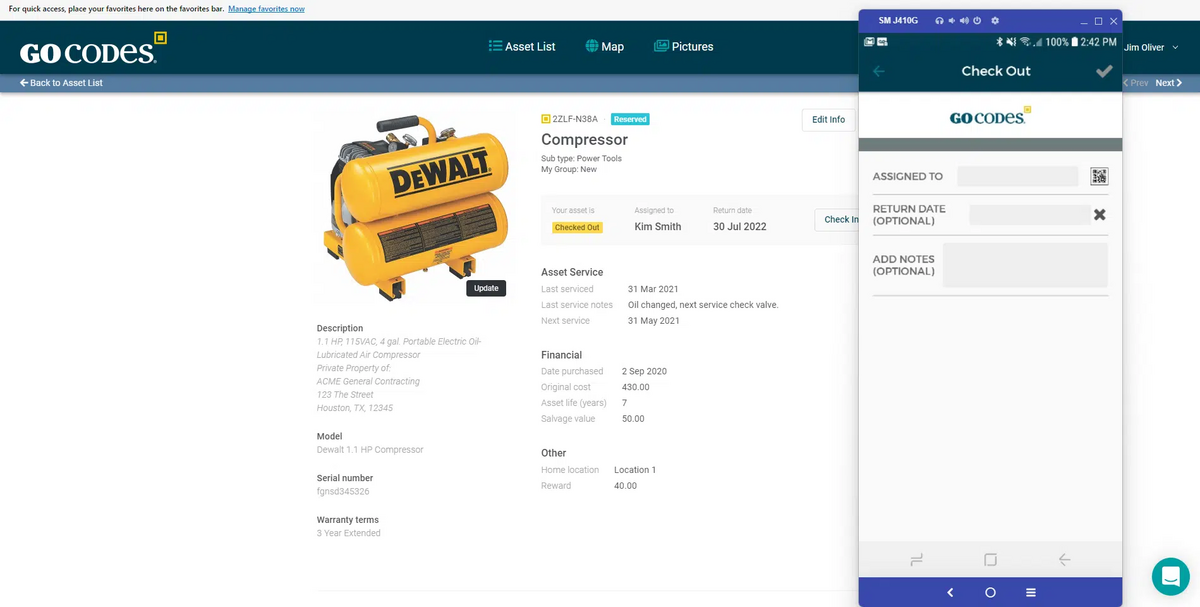
This information is invaluable when it comes to maximizing your tools and fleet.
So, if you often find yourself and your team paying for rentals you don’t quite need, consider leveling up your equipment management game to prevent such spending from happening again.
You Waste a Lot of Time Locating Equipment
Construction companies face an unusual challenge that other businesses do not. Their assets are often scattered across far-flung project sites, sometimes even several.
In addition, these sites change over time.
Movement is constant. If your company still uses antiquated inventory management methods, you are imposing inconveniences on all of your staff and imposing too much risk on your business.
First, when paper or even digital spreadsheets are the norm, someone must manually update the system every time the equipment changes locations.
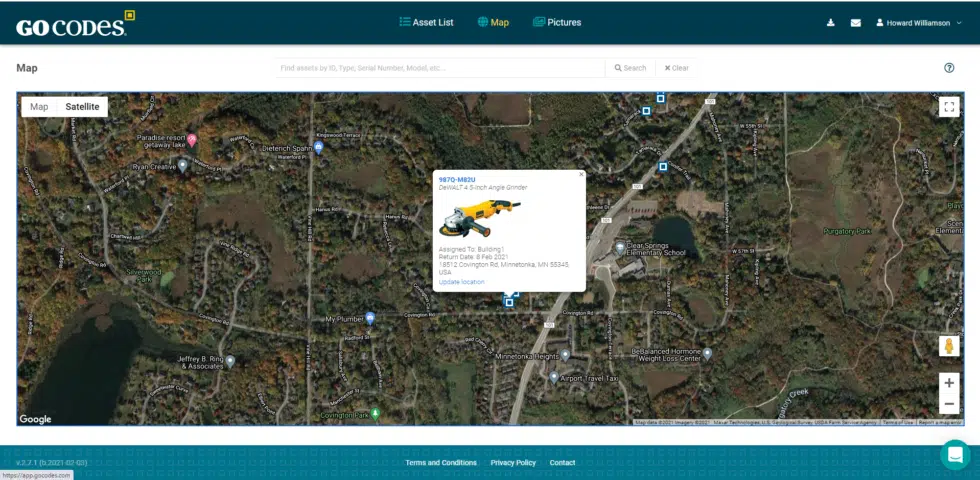
This not only invites error, but it is also inefficient and time-consuming.
And, should the task fall onto the already busy team member, it will be forgotten all too easily, causing even more inaccuracies in your business operations.
Second, equipment operators will waste a lot of time looking for the equipment they need, ending up shuffling their work schedules to accommodate available machinery, instead of concentrating on productive work.
And lastly, when equipment updates do not take place across a system but only in one location, information silos occur and it becomes impossible for teams in the field to remain up to date.
To combat this problem, GoCodes equipment tracking system includes QR code tags, which are easily and firmly attached to construction equipment, no matter the type of asset or environment in which it spends the most time.
QR code tags look like this and can undergo use with just about any type of asset:
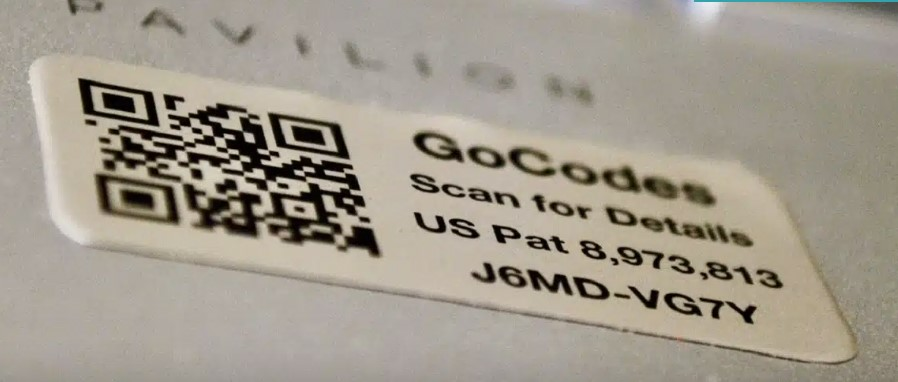
These codes are then scanned with the GoCodes app on a mobile device to update the location of equipment.
In this way, locations are quick to update, and each piece of equipment’s location will be visible in the GoCodes system to everyone who has authorization, no matter how far from headquarters your team is or which time zone they’re in.
Your Equipment Keeps Getting Lost or Stolen
In addition to all the rising costs in the industry, construction companies may spend enormous sums due to lost or stolen equipment.
This can include time wasted attempting to find the objects, money paid to security or investigators, higher insurance premiums, and the cost of replacing the asset.
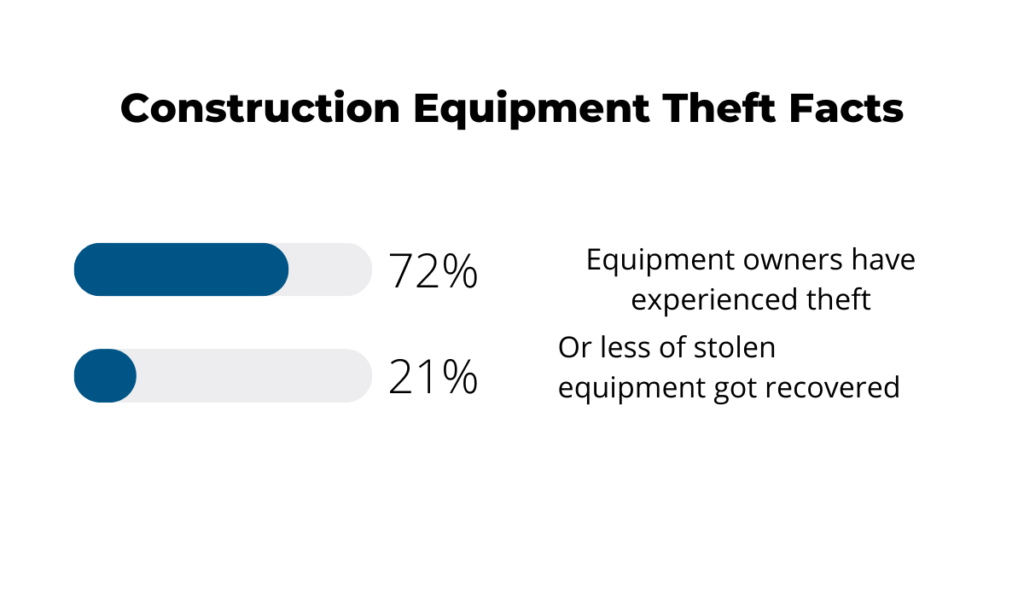
If your equipment gets stolen a lot, or you tend to lose tools you own, then using equipment tracking software might be just the right solution to your problems.
For starters, let’s mention that using such software enables your construction company to relocate and recover your missing equipment.
Let us explain.
Did you notice the data point in the graphic above noting that less than 25% of stolen construction equipment was recovered? That number can rise with equipment asset tracking.
When you have equipment tags that come with the equipment tracking software, like our QR codes, you also have proof of ownership that will help you if the equipment is found.
This helps you in the wake of theft, but it can also assist anyone who comes across your asset and is seeking to return it to its rightful owner.
In the event you find yourself in dispute with another party concerning ownership of an equipment asset, the GoCodes tag, which is not easily removed, can serve as proof that your equipment is, indeed, your equipment.
But, theft can also be completely prevented with the software and hardware for equipment tracking.
For instance, GoCodes uses Bluetooth beacons to help you keep a virtual “leash” on your valuable equipment.
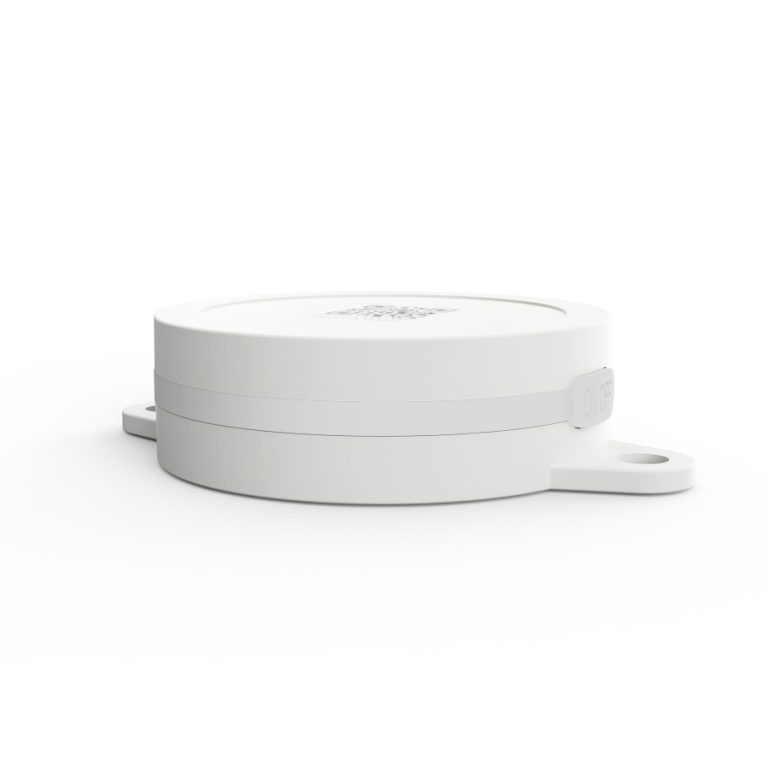
These beacons will send out an alert if the beacon is removed from the asset. This means that you get alerted as soon as the theft is attempted and can move quickly to the asset’s location.
At a minimum, the last known location of your property is recorded, which can often prove extremely helpful during the retrieval process.
You Don’t Know How Equipment Is Being Utilized
If you are tracking your equipment manually with a spreadsheet, are you able to instantly locate your equipment, even if it has moved without your knowledge or is undergoing emergency service that just began?
You are not.
What about where it’s due to go next? Can you look that up without sitting down at a desktop computer?
Unfortunately, you can’t.
Construction companies that use equipment tracking software not only have the ability to find the physical location of their property–they can also track equipment utilization.
This is all possible with a few clicks on your smartphone.
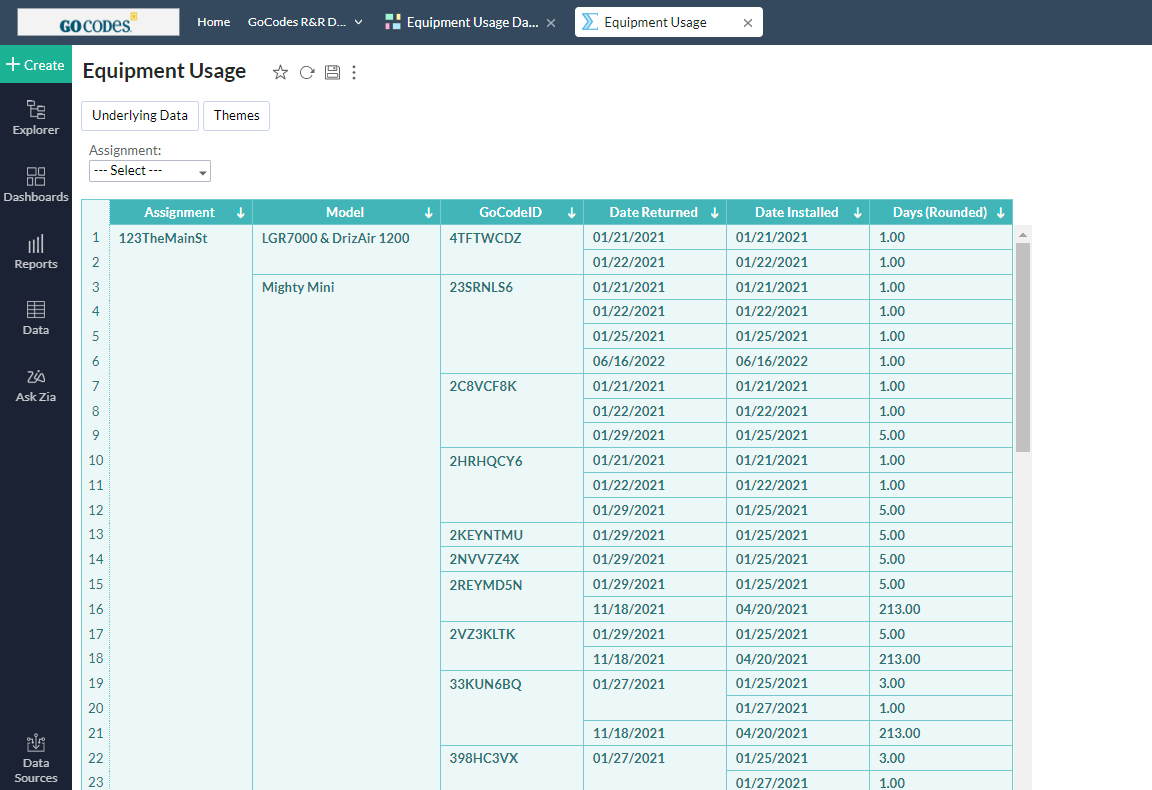
In an app designed specifically for construction equipment tracking, you can easily see who uses which equipment, when it was last serviced, what was changed, when it’s the next maintenance date, etc.
You can even assign tasks related to equipment:
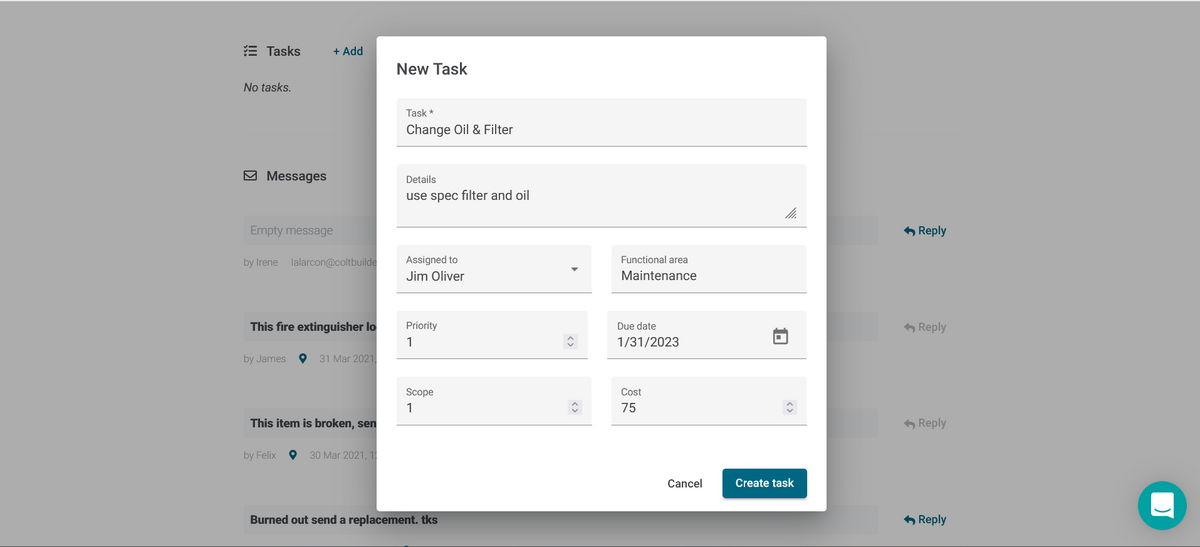
All general information related to its utilization will be available in one central place.
And why does that matter? It matters because underutilized construction equipment is a waste of resources. Why own something if it’s not being used regularly?
You can rather rent it to others, sell it, or replace it for something else you need more.
In general, this is the formula for determining equipment utilization:
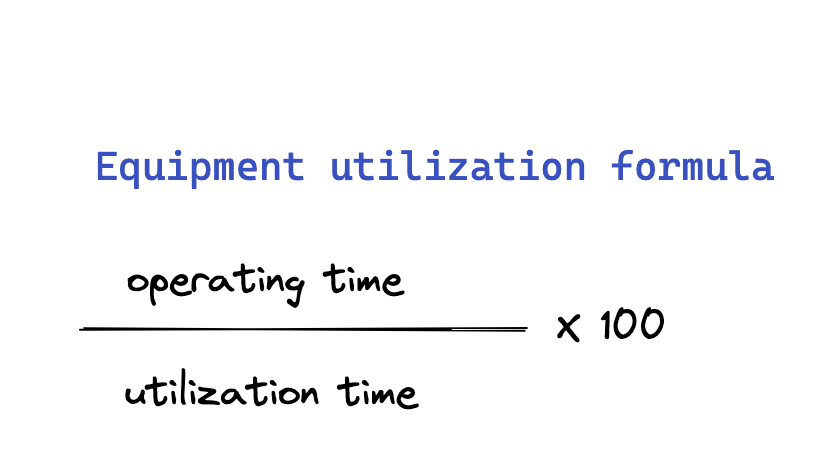
Your equipment utilization will increase with more efficient equipment inventory and scheduling practices.
And taking equipment utilization seriously and being on top of which equipment works 100% of the time and which sits idly will help you maximize your resources and make smarter business decisions.
You Don’t Know What Condition Equipment Is In
If your equipment inventory system is an error-filled mess, there’s a good chance that your understanding of the condition of your equipment is as well.
By having no idea of your equipment’s condition, your construction company is attempting to operate without a great deal of valuable information.
Your stakeholders and decision-makers will not know whether to buy new equipment, maintain their current equipment, or dispose of depreciated one.
This is fundamental knowledge of an asset’s life cycle stages.
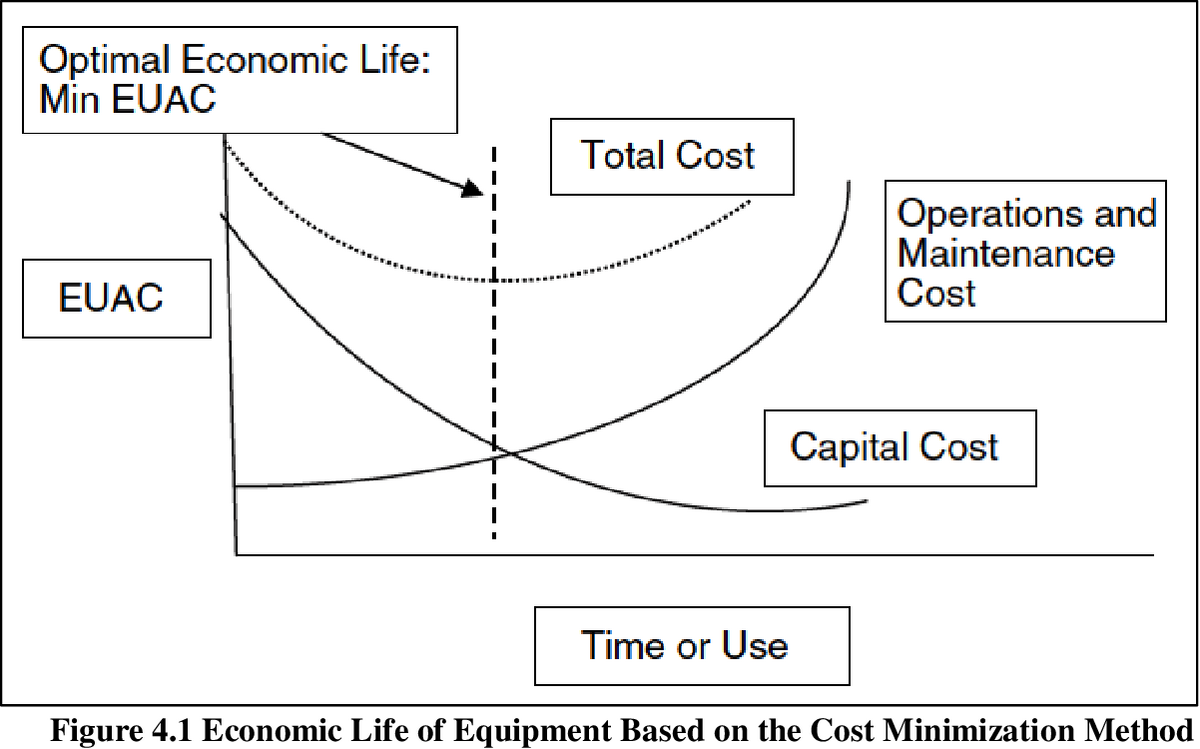
As this visual aid shows, knowing when to repair or retire an expensive asset is vital to the responsible use of your company’s resources.
You can better project your tax options and depreciation rate with this information.
The ability to easily and accurately access this data is much more easily achieved with construction equipment tracking software.
You Experience Frequent Equipment Breakdowns
Another sign that you need to change the way you manage and track your construction equipment, and probably swap for a modern software solution is when construction equipment often malfunctions or breaks down during a project.
This is often a sign of improper equipment maintenance that can lead to longer downtimes, project delays, and cost overruns.
Too many of these problems can prove lethal to a construction company.
Keeping detailed maintenance records and tracking equipment maintenance schedules for each piece of equipment is difficult without equipment tracking software.
However, when using such software, then with a simple scan, your team members can easily find out important information about the “health” of any asset in the system.
This can help ward off catastrophic equipment breakdowns, which are expensive to repair, and can cost heavily in terms of replacement rentals and lost working time.
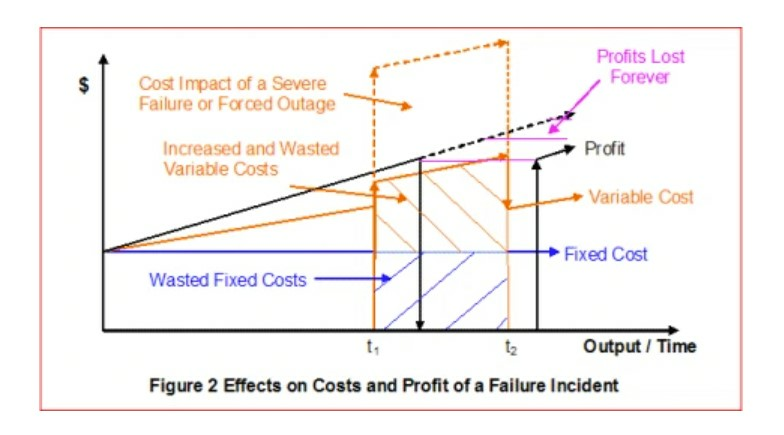
These figures show the high cost of a failure incident or equipment breakdown.
While it might seem frustrating to spend part of a budget on maintenance when a machine is still functioning well, the fact is that this is much cheaper than running an expensive asset until it fails.
Keeping track of equipment preventive maintenance can lead to a longer life for your valuable construction equipment.
Use equipment tracking software to have all this information in one central place.
Your Equipment Audits Take a Long Time
Equipment audits tend to fill management teams with dread.
This is especially the case when the assets are counted by hand, usually by bringing in expensive and sometimes unreliable temporary help. It is a labor-intensive process that will almost certainly result in errors.
Not only are audits expensive, they are becoming even more so, thanks to rising costs and labor shortages.
However, equipment audits can be easier and partially automated with equipment tracking software.
While you might not be able to avoid regular audits, the data your employees have been scanning all along will speed up this process.
Conclusion
If you have recognized your construction company in any of the above mentioned situations, it is probably time for you to invest in equipment tracking software.
A robust equipment tracking system such as GoCodes can address all of these problems and more.
So, if you want to save time and money, get more work done with less effort, and turn your equipment into true assets instead of liabilities, modernize your operations with the use of tailored software that will remove the headache from all your equipment-related tasks.