Key Takeaways
- Enhancing equipment utilization allows for companies to better align equipment availability with project milestones.
- Construction companies that focus on improving the utilization of their existing equipment can save a lot of money.
- Using equipment to its fullest potential helps increase efficiency on the construction site.
If the workers are the bread, the equipment is the butter of construction, contributing to the overall productivity and company success.
No job is getting done without proper equipment, so it’s important to make sure it’s used to its full potential.
Construction companies that invest time and energy in good equipment utilization stay within deadlines and budget constraints while reaping various benefits, four of which we’ll explore in this article.
Are you eager to learn more about the revitalizing effects of efficient equipment use?
Well then, this deep dive is right up your alley!
In this article...
Improves Resource Planning
Improving equipment utilization brings you a few steps closer to better resource planning and project execution overall.
The logic behind it is simple.
Knowing exactly when, where, and how effectively each piece of equipment is being used enables construction managers to make strategic, data-driven decisions about key resources.
Effective resource planning relies on data to ensure the availability of workers, materials, and equipment for the duration of the project, which ultimately guarantees its success and profitability.
But the opposite is true as well.
The lack of data hinders resource planning, making effective utilization highly unlikely.
This creates a domino effect of downtime, delays, and costs that can jeopardize an entire project.
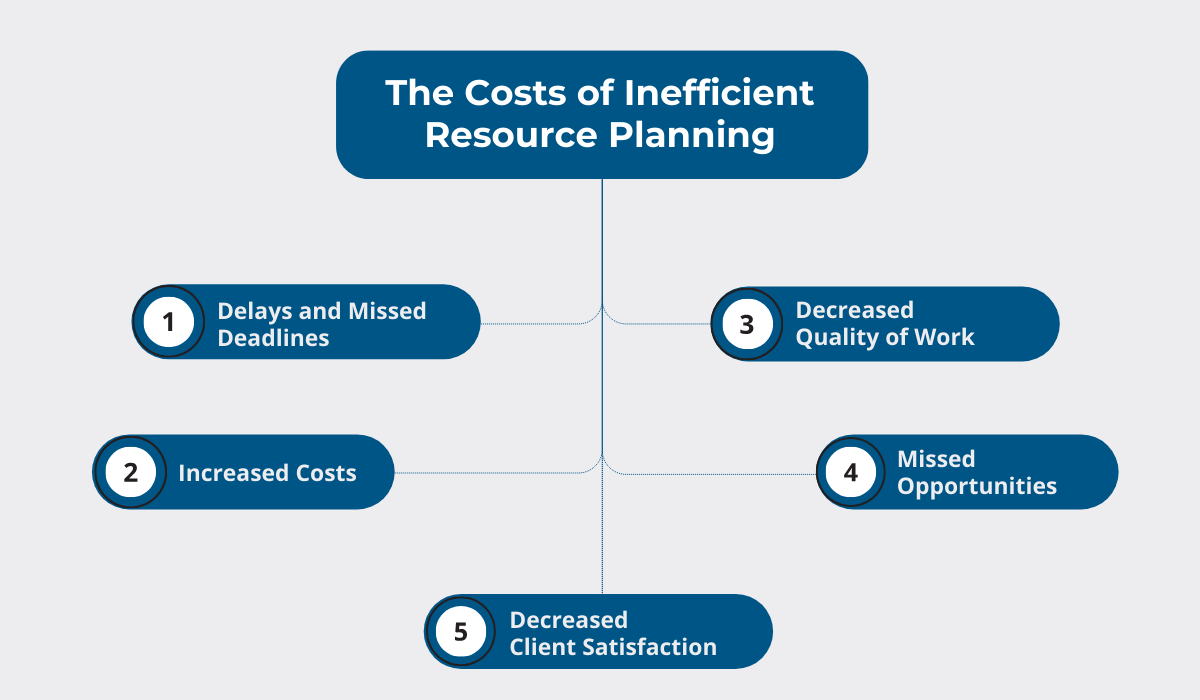
Luckily, it’s possible to combat inefficiencies through regular monitoring of equipment utilization, creating a stable foundation for growth.
Construction companies are increasingly relying on asset monitoring solutions and telematics systems to capture usage trends and make necessary adjustments proactively.
By collecting and analyzing data on equipment’s location, usage, and performance, project managers can identify issues and map key areas for improvement based on:
- Equipment downtime
- Utilization rate
- Availability
So, how does this translate to improved resource planning?
Since tracking equipment utilization gives managers more visibility and control, it also allows them to align equipment availability with project milestones and deliverables.
In this way, resources can be allocated and used strategically, based on project priorities.
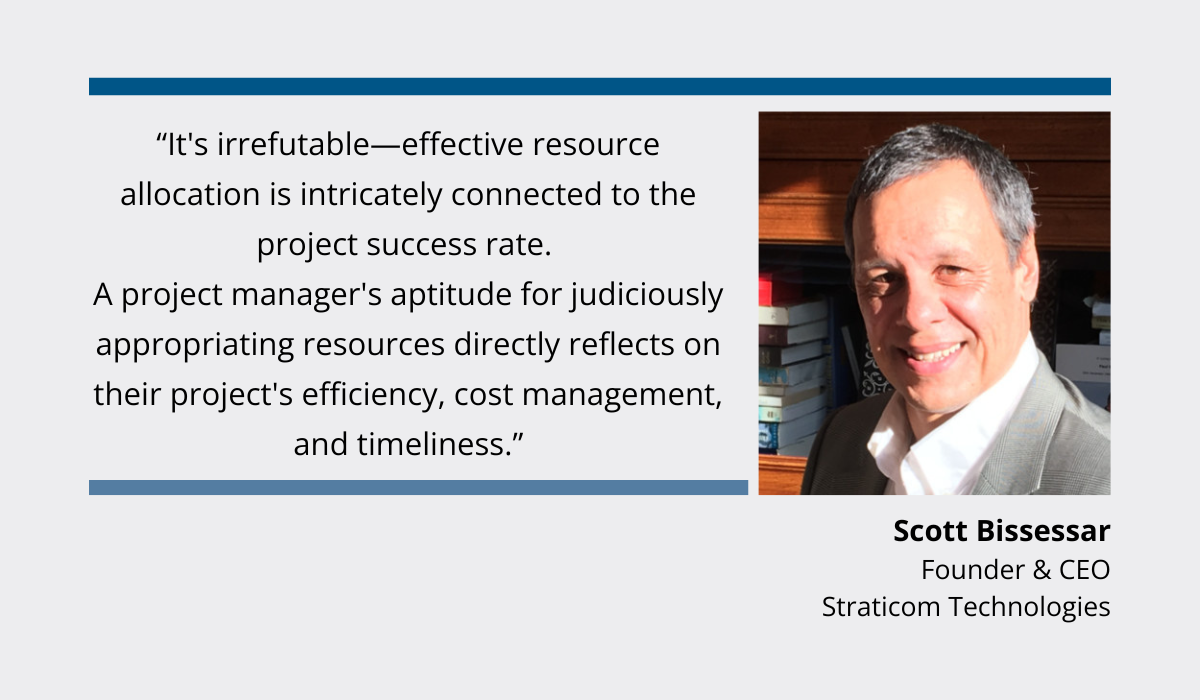
By quickly scanning asset availability and utilization rates across multiple job sites, managers can identify the optimal allocation strategy and make smarter decisions.
For example, instead of relying on heavily utilized machinery for secondary tasks, and risking equipment failure and costly downtime, the workload can be distributed across multiple assets that would otherwise remain idle.
Staying on top of project scheduling and avoiding bumps in the road is much easier with fresh insights into equipment availability and reliability.
And, as you’ll find out, these insights also contribute to enhanced efficiency that spills over onto the entire construction site.
Increases Efficiency on the Construction Site
Inefficient operations hurt profit, there’s no two ways about it.
And that is exactly what makes efficiency one of the main construction site priorities.
There are different ways to achieve an efficiency boost, and using your equipment to its fullest potential is one of them.
The fact of the matter is, equipment utilization directly impacts project costs, duration, and overall efficiency.
Since poor utilization invites project hiccups, as well as major roadblocks, looking into your productivity track record is essential.
Actually, there are a few steps you can take, as you can see in the image below.
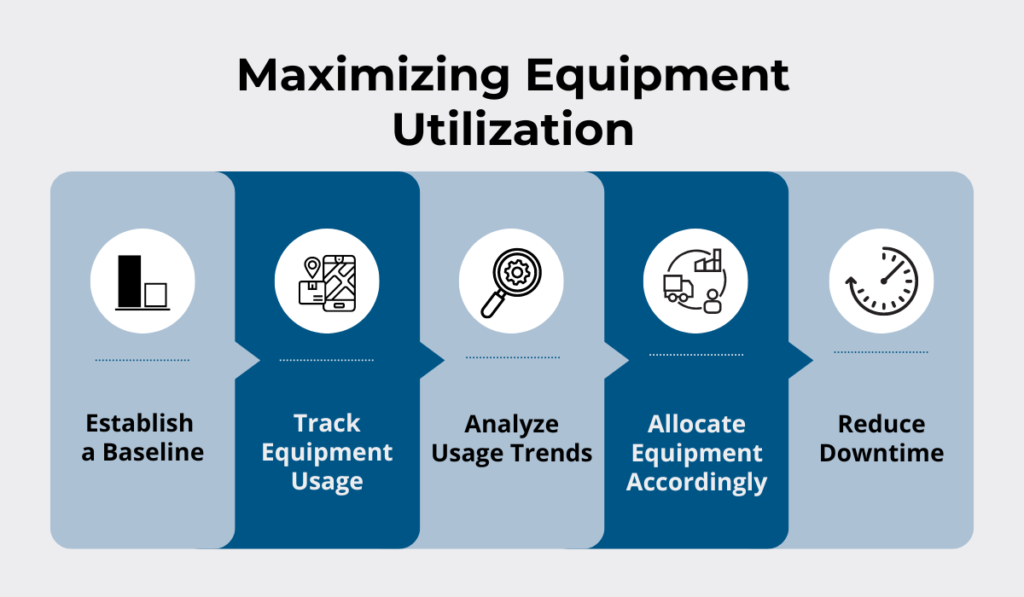
Each step builds up on the previous one, ensuring that every moment of using a piece of equipment is as productive as it can be.
At the same time, the benefits of investing in your equipment’s efficient use are also reflected in reduced downtime and smoother project execution.
While equipment downtime can sometimes be a part of planned efforts of stopping work to perform maintenance, most often it means an unexpected pause in operations due to a non-functioning asset.
And these are more prevalent than you think, with ServiceMax report indicating that a staggering number of companies face unplanned downtime.
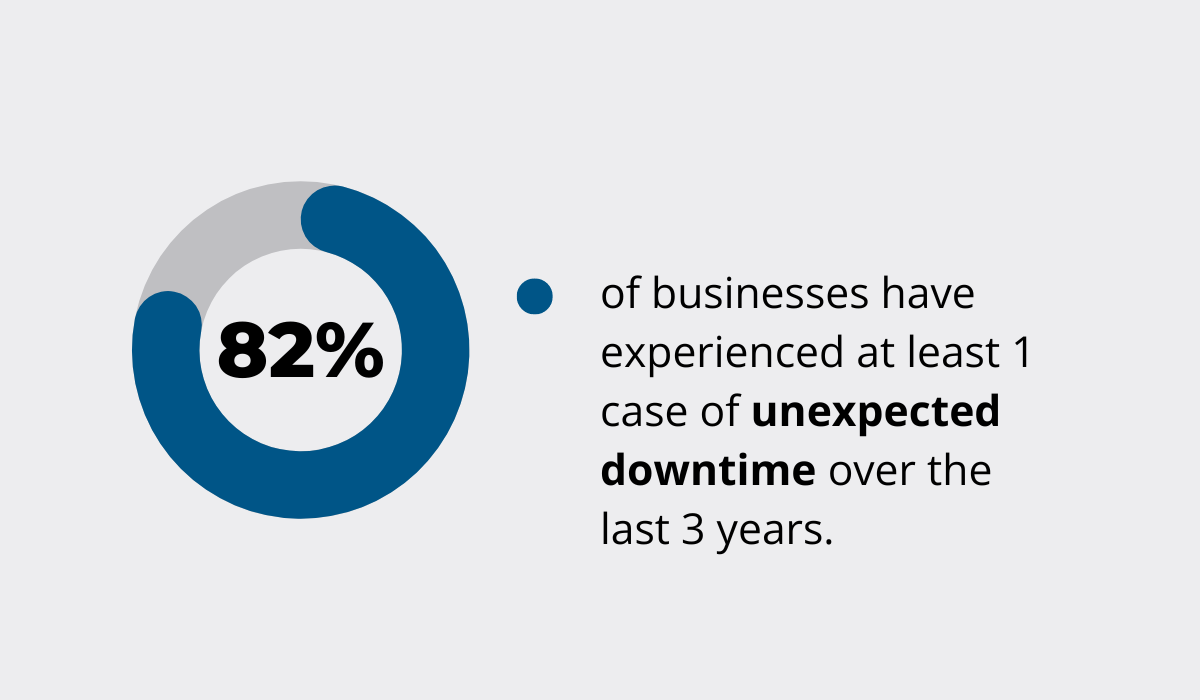
The thing about downtime is that its negative effects add up as work slows down, costing you both time and money.
One hindrance may ripple throughout the job site, which is why it’s essential to plan for interruptions in the form of internal or external factors and look to avoid loss in productivity.
This is why many businesses are taking a closer look at their tools and machinery.
Knowing exactly when and where each tool is used, and whether there is a need for some allocation adjustments, boosts efficiency levels and maximizes output.
In turn, tasks are completed quickly and in line with time and budget constraints, ensuring successful project completion.
Prevents Unnecessary Equipment Purchases
When it comes to equipment, companies that hold onto machinery past its time routinely experience financial drains.
But rather than the fear of losses, most equipment purchases are driven by the need to see growth in one or several areas.
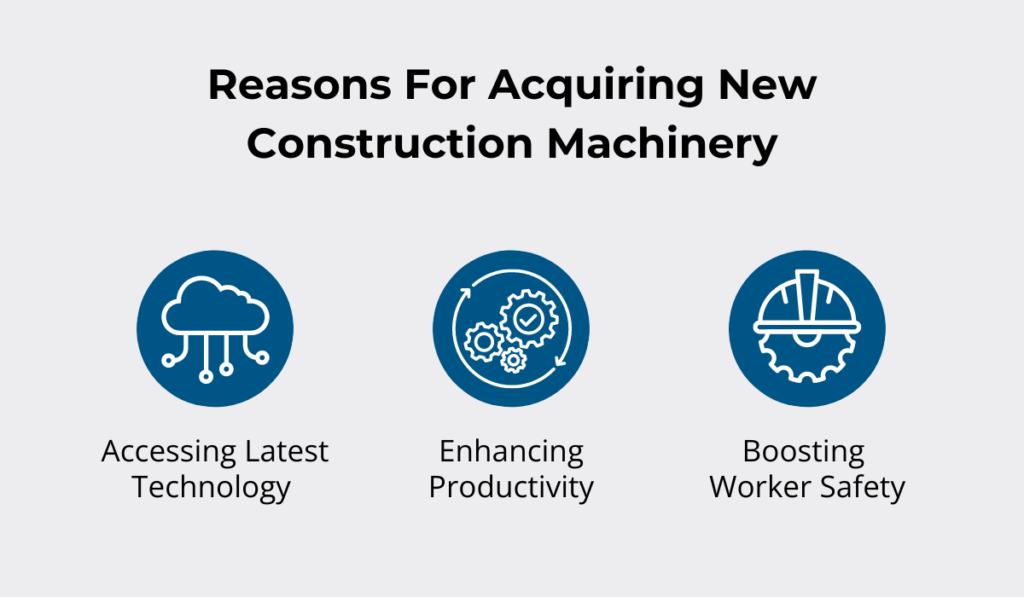
Construction companies racing against time may be tempted to try and boost efficiency by adding more machinery.
However, for all the benefits of new technology, investing in new, shiny equipment, or reliable used assets, isn’t always the wisest decision.
Now, don’t get us wrong.
There are absolutely times and circumstances when making capital investments is the only viable course of action.
After all, if the maintenance becomes a bit too frequent or employee safety is on the line, the asset has clearly reached the final, disposal stage of its life cycle.
But, this is where we need to take a look at utilization data.
Reliable insights on how the piece of equipment has been used are essential for making the best possible decisions about your equipment inventory and key investments.
If you’re using fewer assets than your operations require, you’re potentially limiting your company’s growth, but having too many means risking overhead costs.
And there are plenty of costs already that come with owning and managing equipment.
Given the expenses, it isn’t surprising that the latest forecast by the American Rental Association (ARA) suggests that the equipment rental industry will make quite a splash in 2024.
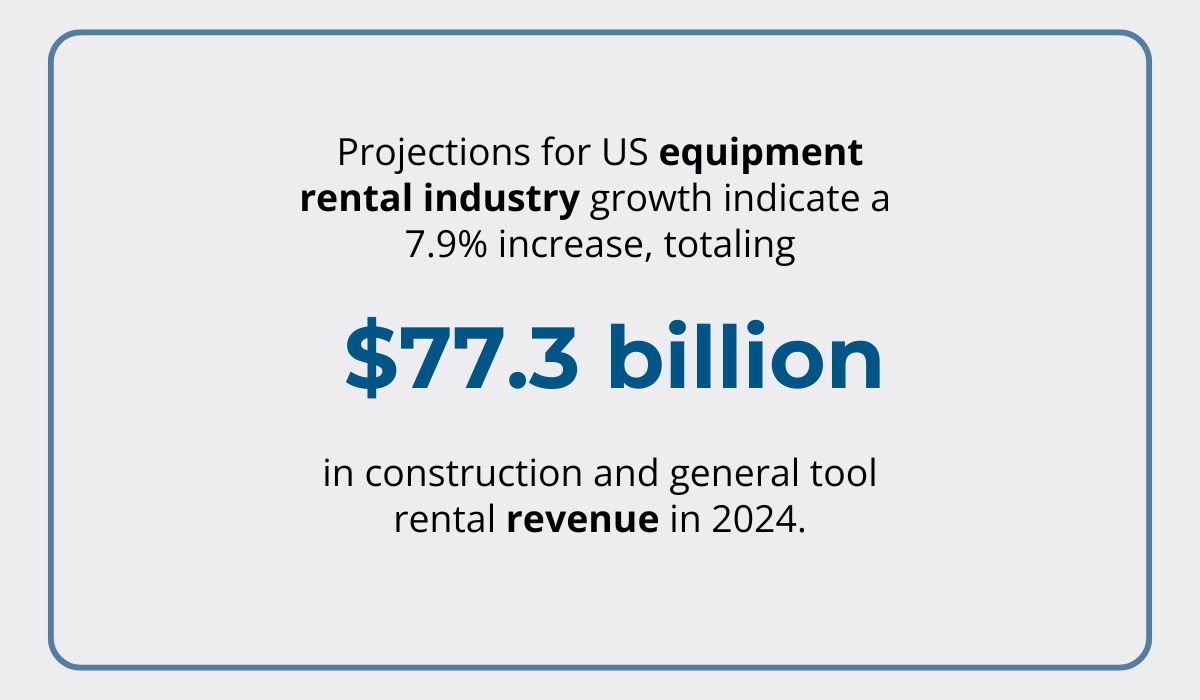
Regardless of whether you’re buying or renting, the most reliable way of keeping productivity high and the costs in check is to collect and analyze utilization data.
Taking a closer look at the data is very likely to reveal that some of your assets aren’t utilized to their full potential and that the necessary adjustments can easily be made.
This means that optimizing your equipment utilization allows you to boost the output and meet project deadlines without needing to make capital expenditures to expand your fleet.
By eliminating the need for making untimely purchases in the first place, equipment costs won’t outweigh the value that the new machinery is supposed to bring to the company.
Such substantial cost savings make all the difference for construction companies, as do the expenses that relate to idle equipment.
Reduces Expenses Associated with Idle Equipment
Overutilization of equipment creates plenty of problems for construction companies, from disruptions and costs caused by equipment breakdowns to potential safety hazards.
However, the dangers of idle machinery are perhaps even greater.
Idle equipment creates drops in productivity, with equipment or employees who are standing by easily hindering or even blocking regular construction operations.
This increases the duration of the projects, risking client dissatisfaction and burying profit.
Previously, the tricky bit was observing when the idle times occurred, and how excessively, as highlighted by Ned Boydell, Equipment Manager for Canadian Emil Anderson Construction.
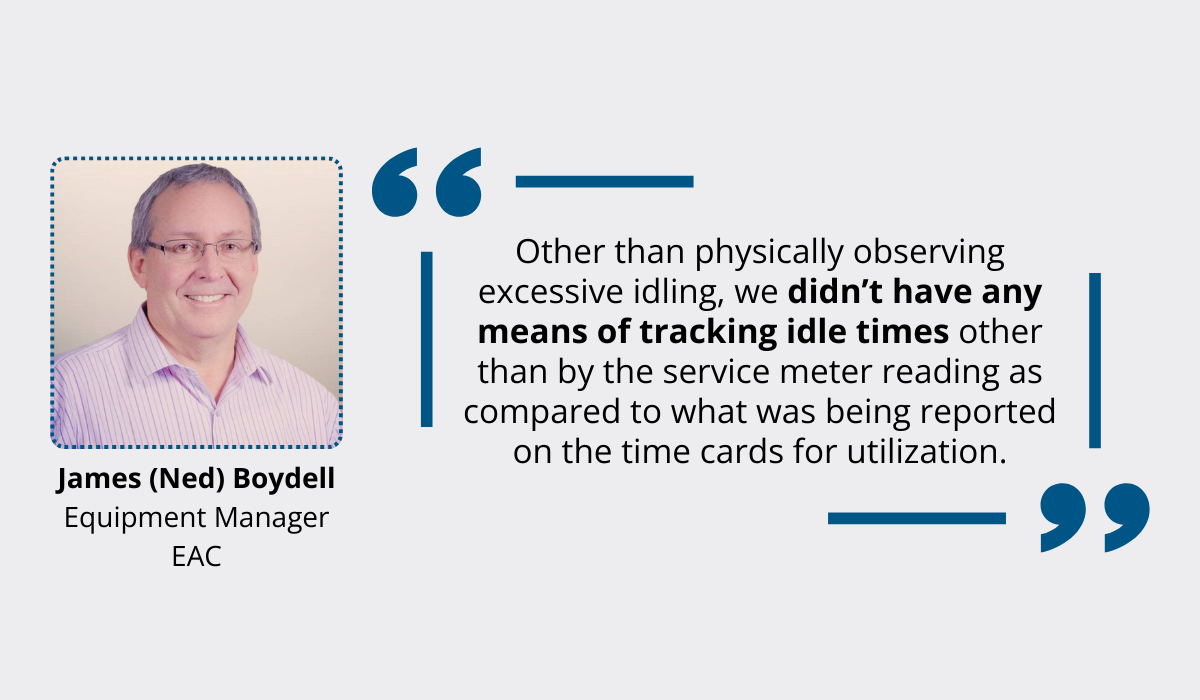
Luckily, telematics and different asset-tracking solutions have been around for a while now, yielding crucial data on various segments of equipment use, including maintenance.
Among the expenses which are directly related to underutilized equipment are:
- Insurance costs
- Storage costs
- Maintenance costs
Idleness is particularly costly when it comes to maintenance, because it leaves plenty of room for the underutilized machinery to malfunction unnoticed, while other assets suffer extra wear and tear due to extensive use.
But this is where comprehensive solutions like GoCodes Asset Tracking, our asset tracking software, make all the difference.
Firstly, combining advanced GPS and geofencing technology with easily scannable QR code labels and RFID tags allows users to locate equipment in real-time, and effectively manage the life cycle of each piece thanks to a bulk of data.
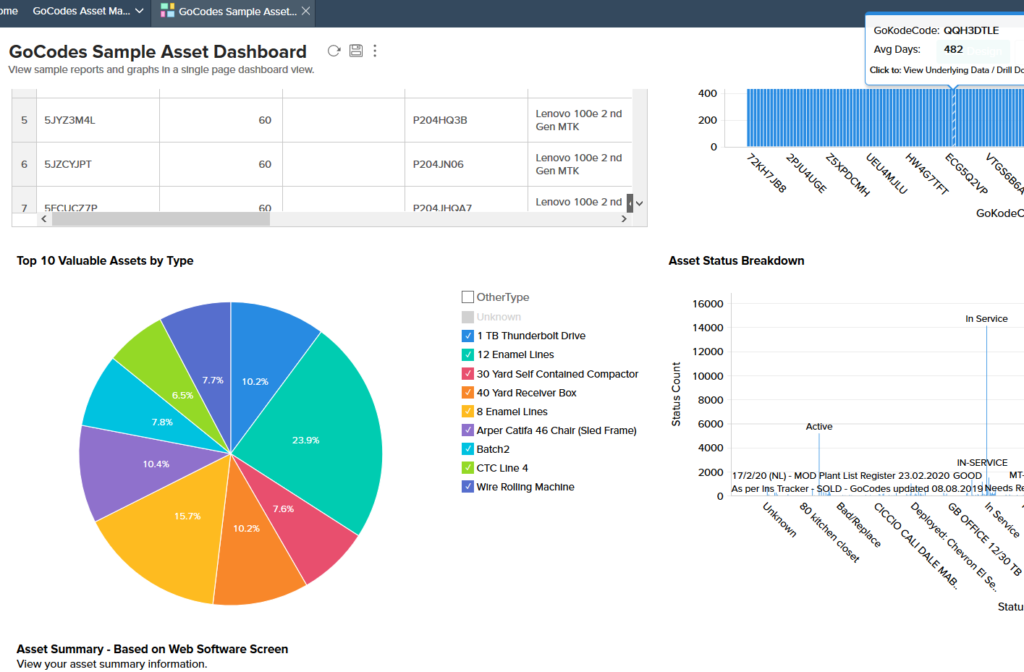
Insights on equipment utilization are particularly valuable for preventive maintenance, and GoCodes Asset Tracking features allow the users to:
- Quickly add notes about an asset’s condition, for repairs or maintenance.
- Schedule maintenance and inspection tasks based on asset utilization data.
What makes the process of sending field service requests intuitive and virtually effortless are the earlier mentioned QR codes.
By scanning the code, the users are issued a prompt to enter all the necessary information on the asset in need of maintenance.
Upon hitting submit, the administrator will instantly receive an alert, with the request available for tracking on the GoCodes Asset Tracking app, alongside all other field service requests.
Likewise, the notification about scheduled maintenance is shared just as promptly.
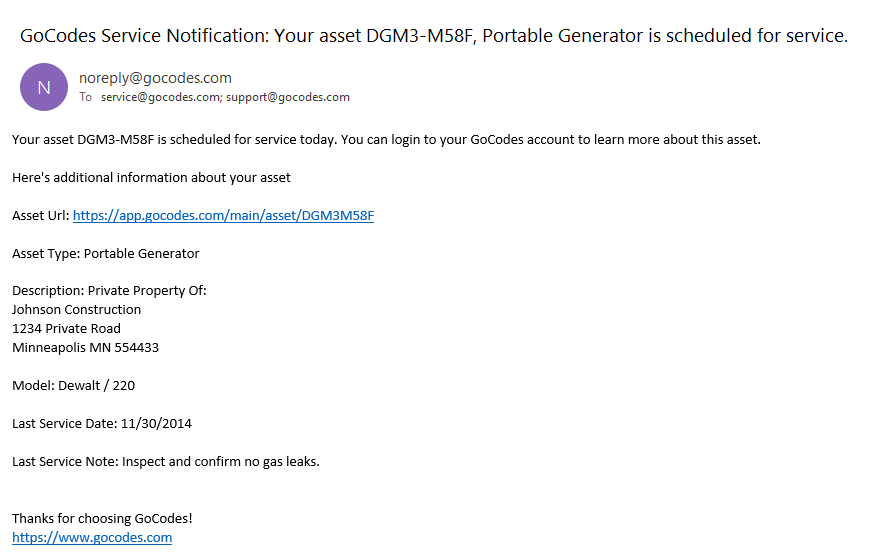
This, in turn, helps you curb idle time and associated expenses, enhancing the overall financial performance of your construction projects.
Conclusion
The setbacks related to inefficient equipment utilization accumulate over time, hurting the productivity and profitability of construction businesses.
However, the benefits of improved utilization are felt even more strongly, in the sense of reduced expenses related to downtime and idle equipment, as well as maintenance.
Moreover, optimized operations efficiency and resource planning allow for more strategic and agile decision-making, putting a stop to new purchases before assessing and maximizing the productivity of existing assets.
The moral of the story is this: unlocking the full benefits of improving equipment utilization is worth the investment, and software solutions will get you there quicker.