Tracking the locations, quantities, maintenance, and other relevant data concerning the assets a company owns is vital for the success of any business, regardless of its size.
Without proper asset tracking, companies could not function properly, so it’s no wonder that new and better ways of conducting this crucial but complex practice are always being developed.
If you’re looking for ways to improve your own asset tracking, you’ve come to the right place. In this article, we’ll cover the most common methods for tracking fixed assets.
We recommend that you analyze them, and compare them to your own budget, required accuracy, range, skill level, and other needs, and you’ll be well on your way toward effective asset tracking.
In this article...
Spreadsheets
Of all the asset tracking methods we’re going to cover in this article, this one’s certainly been around the longest.
It will come as no surprise that many still rely on spreadsheets, since, compared to their predecessors—pen and paper —spreadsheets seem like a highly advanced solution, and an affordable one at that.
This method owes its longevity to a number of advantages:
- Requires minimal training
- Requires no special equipment
- Offers the possibility of customization
However, it’s safe to say that it is not the most efficient way of tracking assets available.
In fact, spreadsheets were not designed with asset-tracking in mind at all. They don’t provide real-time data, which means that any change in asset records isn’t automatically recorded.
Instead, it needs to be entered manually, making this method highly prone to human error.
And errors can be quite costly. Depending on the situation, you could be one typo away from a disastrous financial loss.
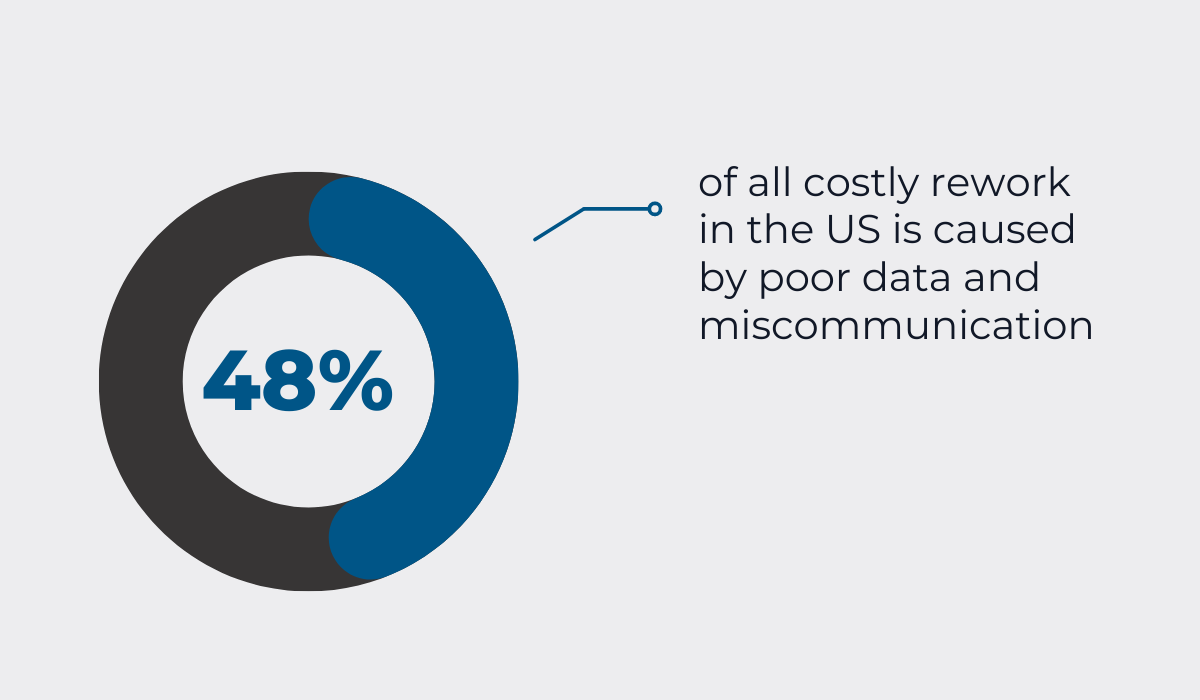
After all, spreadsheet errors pollute your data, and poor data leads to poor decisions.
What’s more, susceptibility to errors is not the only issue you risk dealing with when using spreadsheets.
In addition to not offering location tracking options, they are also hard to use on mobile devices.
Both of those are huge disadvantages in today’s fast-paced job sites, where everything and everyone is always on the move.
So naturally, it was only a matter of time before the business world moved on from Excel and similar solutions to more effective ways of asset tracking.
Barcode Labels and Tags
In the 1960s, scanning barcode asset labels became the new way of monitoring car parts along the assembly line.
This was the first step toward the automation of the asset tracking process at large.
Since then, however, we’ve started to rely on a more advanced version of barcode tags, namely, Quick Response (QR) code labels.
These, now widely known, boxes with black and white squares can contain a far greater amount of information than barcodes and can be read with a camera or an app on a mobile device.
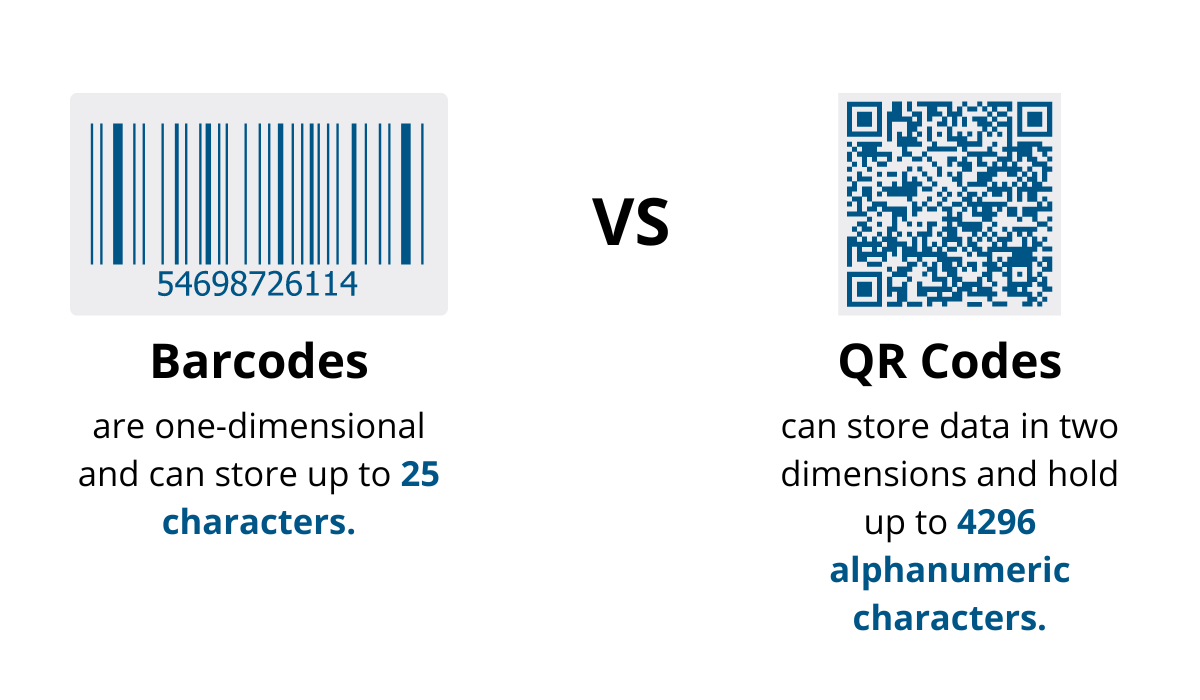
So naturally, as the popularity of smartphones spread, so did the use of QR codes.
Today, we see them displayed almost everywhere.
Thanks to that kind of versatility and cost-effectiveness, QR code labels have quickly become an indispensable part of the asset tracking process, even in the construction industry.
Our own asset tracking system —GoCodes Asset Tracking—relies on QR code labels and tags, too.
Not only is this method efficient, but it’s also immensely intuitive and user-friendly, even for less tech-savvy users.
Here’s how it works:

First, attach our customized QR code tags to the assets you want to track. Then, when you or your employees need a particular item, scan the label with our GoCodes Asset Tracking smartphone app.
This way, you can check the asset out or in and update its information in seconds. It’s as simple as that.
Essentially, each time an asset is scanned, an update is made, and you get an insight into the date and time of the update, as well as the person who made the update.
Plus, you can access that data anytime and anywhere, since it’s all stored in the cloud.
Global Positioning System
There’s more to asset monitoring than mere location tracking, but staying on top of where your assets are at any given moment certainly represents a large piece of the asset tracking puzzle.
And for many, the Global Positioning System (GPS) is synonymous with location tracking.
Relying on global satellites to pinpoint the coordinates of an asset’s location, ground stations to confirm that location, and GPS-enabled devices to receive it, GPS is among the most reliable and accurate means of location tracking, providing almost real-time data.
In the construction industry, GPS trackers are commonly used for fleet management.
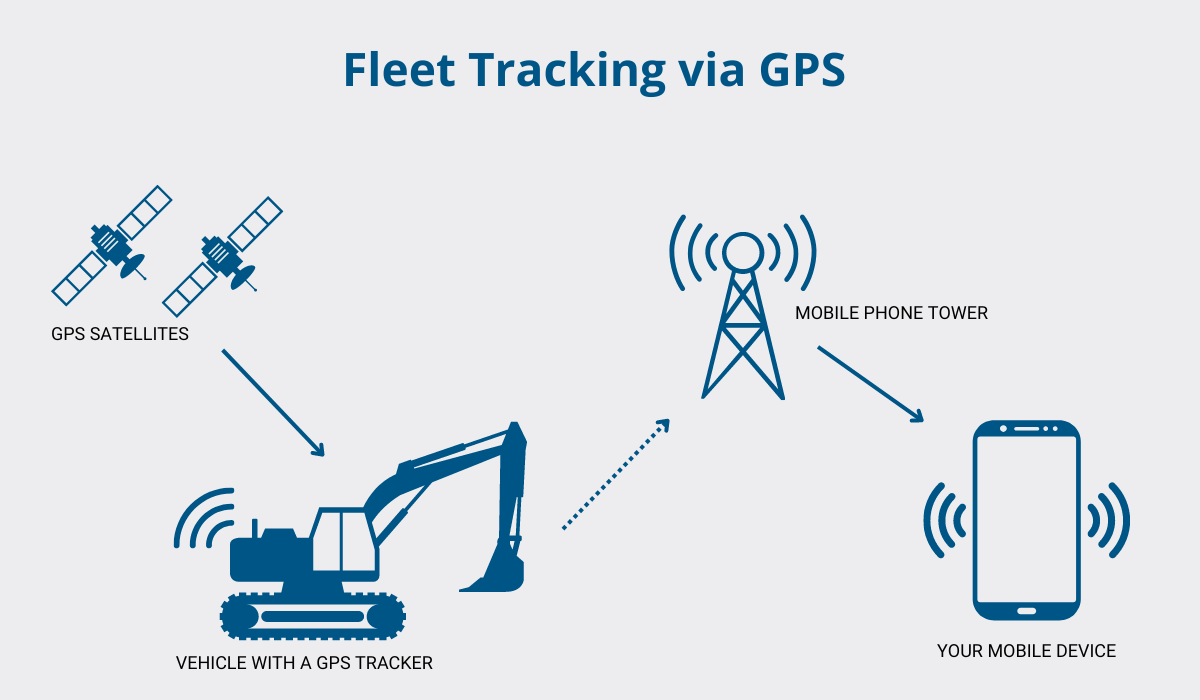
You can see the routes taken by a vehicle and whether the driver is driving at a safe driving speed.
Based on such data, you’re able to plan routes and make other decisions that’ll increase your fleet’s productivity and drivers’ safety.
GPS trackers operate on a real-time basis and don’t require workers to perform any action for them to be effective. Therefore, they are called active trackers.
Although this is a precise and real-time method of asset location monitoring, it can get pricey and drain a lot of power.
Luckily, GPS can be used in tandem with other technologies, such as, for instance, QR code labels.
This way, GPS becomes much more than the means of tracking your large assets—it helps you locate even smaller tools and further improves your asset tracking.

So, when you use a GPS-enabled device, such as a smartphone, to scan an asset’s QR code label to check that asset out, the location of the update is automatically recorded.
Essentially, the GPS location of the smartphone that the scan was conducted on serves as the location of the asset.
This method is considered passive since it requires workers to perform a certain action (scanning) for the location to be updated.
As a result, this type of GPS positioning is more suitable where real-time updates are not necessary.
Bluetooth Low-Energy Beacons
Of course, GPS is not without its limitations.
Namely, this method of asset tracking is not really effective indoors.
So if some of your work takes place in large buildings, underground, or underwater, GPS might not be the solution for you.
Instead, you may want to consider using Bluetooth Low Energy (BLE) beacons.
Bluetooth Low Energy is wireless technology created to, as the name suggests, consume less power than traditional Bluetooth, prolonging its service life and, in turn, making the technology more suitable for asset tracking.
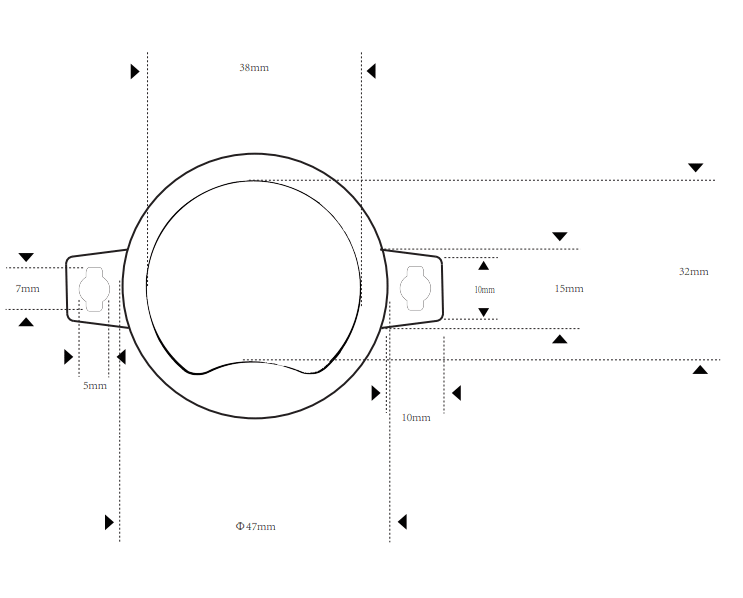
Due to their size, the beacons can be attached to almost any asset.
And when attached, they start to emit information to nearby Bluetooth receivers (i.e., any Bluetooth-enabled device, such as, for example, a smartphone).
The information might include:
- The identity of the asset/beacon
- The distance of the asset/beacon from you
- Different environmental information, such as temperature and acceleration
In other words, each time you come near an asset with a BLE beacon, you’re immediately notified of its presence.
Some apps will even notify you if the beacon (asset) is removed from within the app’s range, which is particularly useful for theft prevention.
Therefore, if affordability, long battery life, and indoor navigation are a must for you, give BLE beacons a thought.
Radio-Frequency Identification
Just like QR code labels and BLE, Radio-Frequency Identification (RFID) is another passive form of asset tracking.
This technology relies on, as the name suggests, radio waves to track and monitor assets, and it involves three components: a reader, a tag, and software.
Tags consist of two parts: an antenna that transmits the signal and a chip where the data is stored.
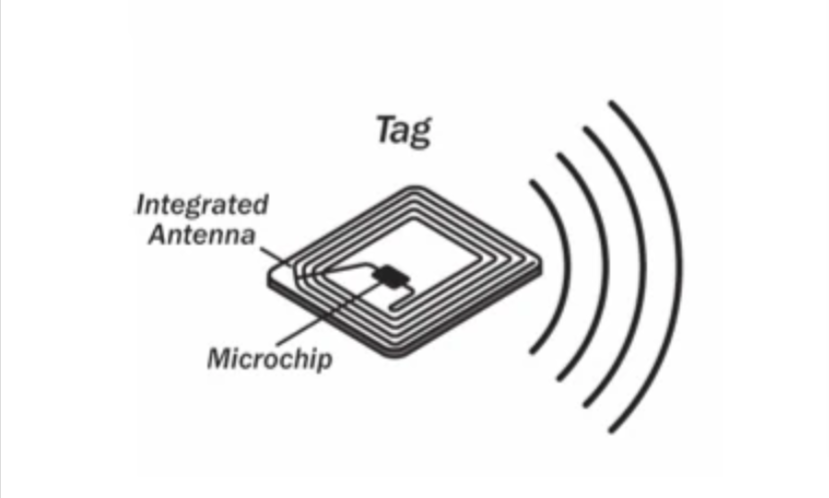
The RFID reader then reads the data, and the software is used to report and manage it. This way, you get information about the locations and quantities of your assets.
Unlike any of the previously mentioned asset tracking methods, RFID trackers don’t need to be in the line of sight of a reader to be scanned, and many tags can be scanned at once.
They are also more durable, which makes them perfect for assets that are used or moved a lot.
However, there are some disadvantages of this technology, too.
It’s important to keep in mind that not all RFID trackers are compatible with all RFID readers, so do your research before making a purchase.
Moreover, it might take some time for your team to get used to them as they’re not as intuitive as some of the previously mentioned methods.
Some employee training will certainly be needed.
Finally, compared to QR codes, RFID trackers can store less data and are much easier to hack.
So, if you’re looking for a highly secure system that’ll be able to store large amounts of data, you’ll probably have to give RFID systems a pass.
Near-Field Communication
RFID was the basis for the development of Near-Field Communication (NFC). In other words, NFC could be considered a branch of RFID, designed with more secure data exchange in mind.
If you have an NFC-enabled smartphone or a credit card—and chances are that you do—you’re already familiar with this technology.
It’s most commonly used for mobile and contactless payments, as well as access control.
NFC tags are an extremely short-range technology, requiring 1.5 inches or less to make a connection, and therefore, unlike its older counterpart, RFID, it cannot be used to scan multiple assets at once.
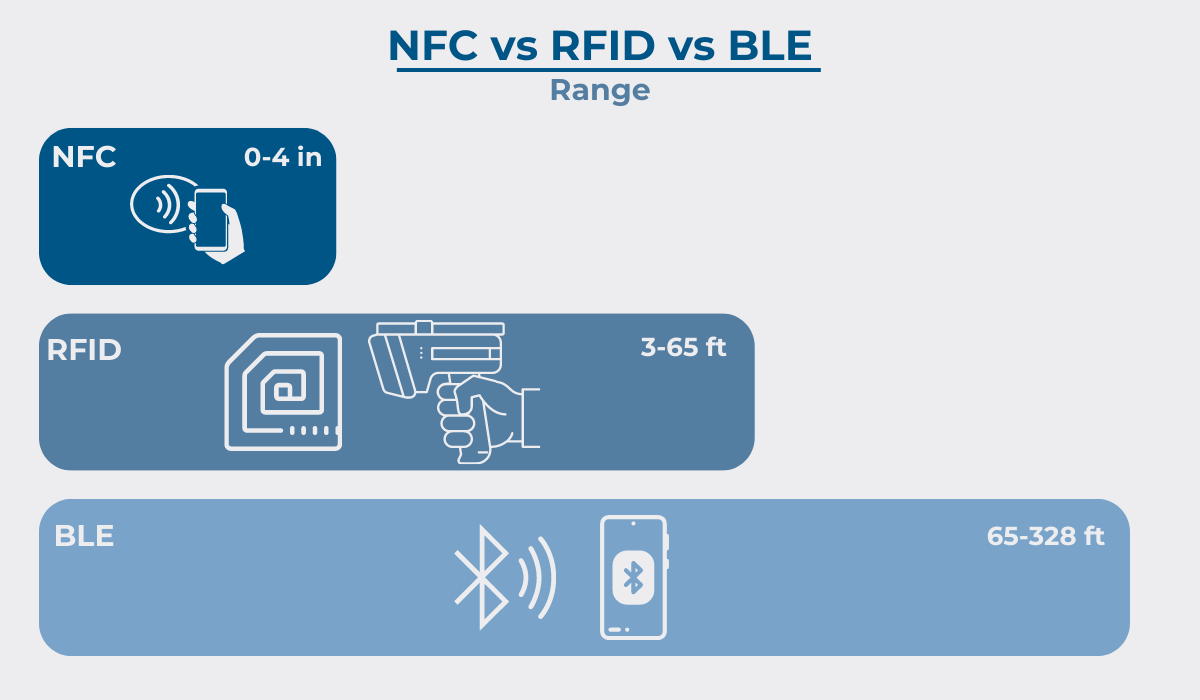
However, NFC tags can store much more data than RFID, and that data can be in different formats, including text, URL, and media files.
Moreover, RFID requires costly readers to access asset data, while NFC tags can be read and written on using any modern-day smartphone.
This significantly reduces implementation costs and takes less time for your team to get used to.
NFC tags are quite durable and able to withstand different extreme conditions, water, and heat.
They also do not require an internet connection, which makes them perfect for remote work in harsh conditions.
Therefore, when using NFC for asset tagging, workers need to get really close to scan the tag, but they can then access a wealth of information, such as maintenance schedules and history, instructions for use, warranties, and so much more.
Those who require high data security and accuracy, with minimal error, should definitely consider an NFC solution for their asset tracking needs.
Ultra-Wideband Technology
Another method of indoor asset tracking that is quickly growing in popularity is the Ultra-Wideband Technology (UWB).
Like WiFi or Bluetooth, this is a wireless communication technology that utilizes radio waves.
A UWB transmitter sends out billions of radio pulses, and a receiver picks them up and translates them into data.
The UWB technology relies on tracking anchors that define an operational space and on radio signals that track your tagged assets within that space. It is able to transmit a lot of data over short distances and use very little power, but the feature that truly wins people over is its highly accurate positioning.
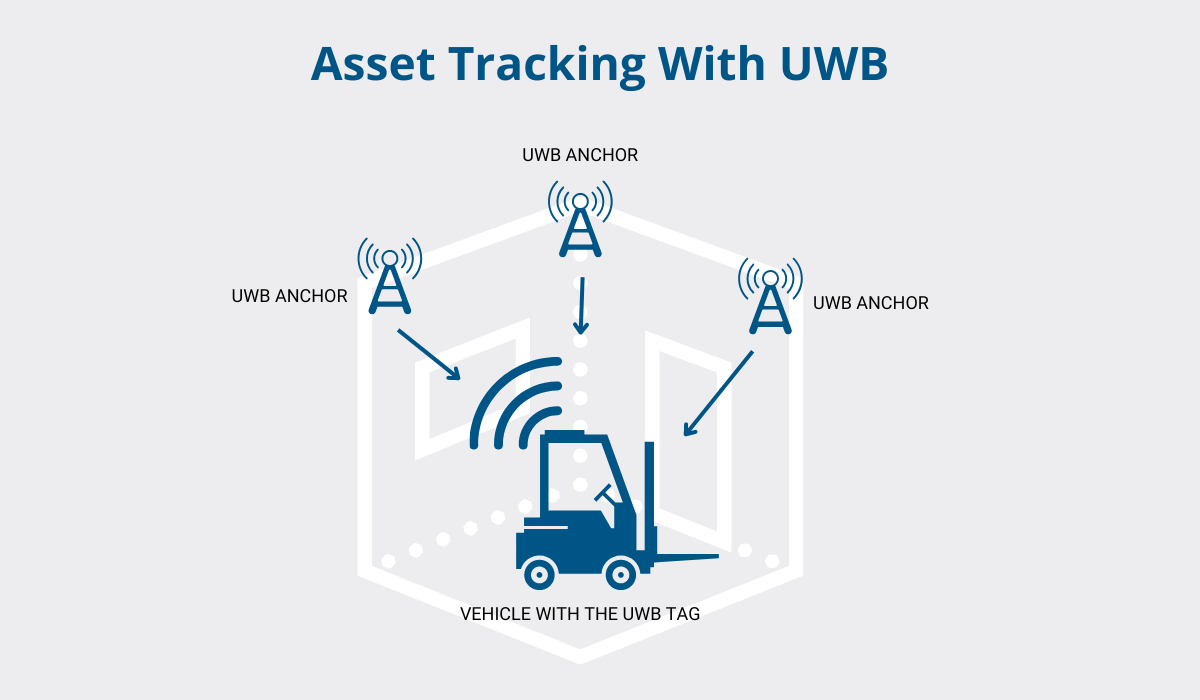
Out of all the methods we’ve covered, UWB tags provide the most accurate data, which is extremely useful for tracking your inventory in large, multi-story buildings.
With UWB, you can map all your assets easily as the technology records an item’s location in three dimensions.
It can even detect your assets through obstacles.
However, the high precision comes at a price—literally, as the UWB systems can be quite expensive.
What’s more, such systems require at least three receivers, which is costly in itself, but they also sometimes need cables to keep them synchronized, which makes for a complicated and difficult installation.
Therefore, compare your required level of accuracy against your budget before you make any decisions.
Internet of Things
The Internet of Things involves a network of physical objects combined with different technologies, sensors, and chips working together and exchanging information over the Internet.
Although it was first used in households as different smart devices and appliances, the Internet of Things quickly found its way into industrial use due to its versatility.
When it comes to asset tracking, this technology provides data that is accurate, rich, and reflects the situation in real-time, helping you reduce theft, making sure your machines perform as they should, and generally creating a more productive working environment.
For example, you can place sensors that measure temperature and humidity in concrete to get accurate data about the curing process.
No need to waste time trying to figure out how long curing will take on your own—with IoT, you can do it all remotely without unnecessary effort.
Take a look at the picture below to see how it works.
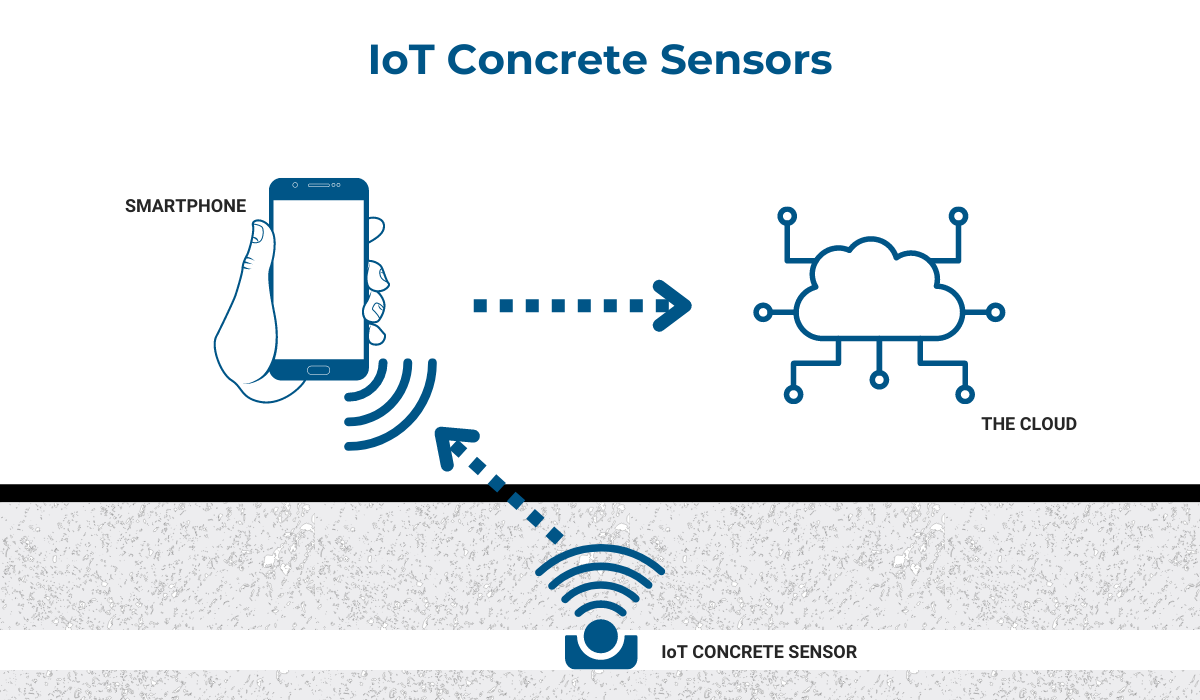
The IoT technology is still in its early stages, though, and it will certainly grow in the future. Right now, its implementation can be somewhat costly, especially for asset-rich companies.
It also requires a lot of maintenance to ensure it’s working properly, and employees might need some time to fully adopt the technology, as the learning curve can be somewhat steep for less tech-savvy team members.
Conclusion
It’s hard to deny that, when it comes to asset tracking solutions, there is a wide variety of options.
But this only goes to show how important asset management really is.
It provides so many benefits for businesses across industries, so new and improved methods for asset tracking are always being developed.
Choosing the right solution for you won’t be easy, but hopefully, this article will serve as the starting point in your search and give you a nudge in the right direction.