If you are an owner of a construction business, or a site manager, you probably realize how important it is to keep track of your equipment.
Workers are not able to do their job without the proper tools and machinery, which is why you need to be aware if some of it gets lost, stolen or damaged.
Equipment tracking is a modern solution that allows you more control over your physical assets.
In this article, you will find out how it works, how it can benefit your business, and what types of tracking methods exist.
In this article...
What Is Equipment Tracking
Equipment tracking is a technology-backed system designed to help you keep a record of your company’s assets. The tracking procedure is straightforward.
Every piece of equipment can be marked with tags and labels which can be scanned to show the asset’s location, usage, and maintenance schedule.
This information can be effortlessly retrieved with a designated scanner or a smartphone, or it can be transmitted over a longer distance via radio waves, or even satellites.
All you need is a tracking software solution that stores that data and acts as a centralized, enterprise-wide hub for equipment management.
This way, you can monitor all of your tools, equipment, and vehicles without the need for complex, hard-to-manage spreadsheets.
Why Is Equipment Tracking Important in Construction
Equipment tracking technology offers many tangible benefits which can help you improve efficiency and lower operational costs across the board.
Since construction is a business that requires a lot of equipment, it necessarily includes multiple types of assets in constant circulation.
And if a large number of those assets are untracked, it can lead to management problems and leave a lot of room for human error.
For instance, the equipment could get lost or stolen. Also, asset audits, although necessary, can take a very long time to complete without tracking software.
And finally, it can be hard to keep up with tool and machinery maintenance.
Digital tracking methods can provide improvements in all of these areas, increasing productivity for your business.
Preventing the Theft of Equipment
Having a real-time overview of your company’s assets can go a long way in helping you deal with equipment theft.
And theft is an unusually common occurrence in the construction industry.
According to the National Equipment Register’s (NER’s) 2016 Annual Theft Report, an estimated $300 million to $1 billion in construction assets is stolen every year.
Some of the reasons listed in the report include the high value of equipment, poor site security, an active used-equipment market, and a low risk of arrest.
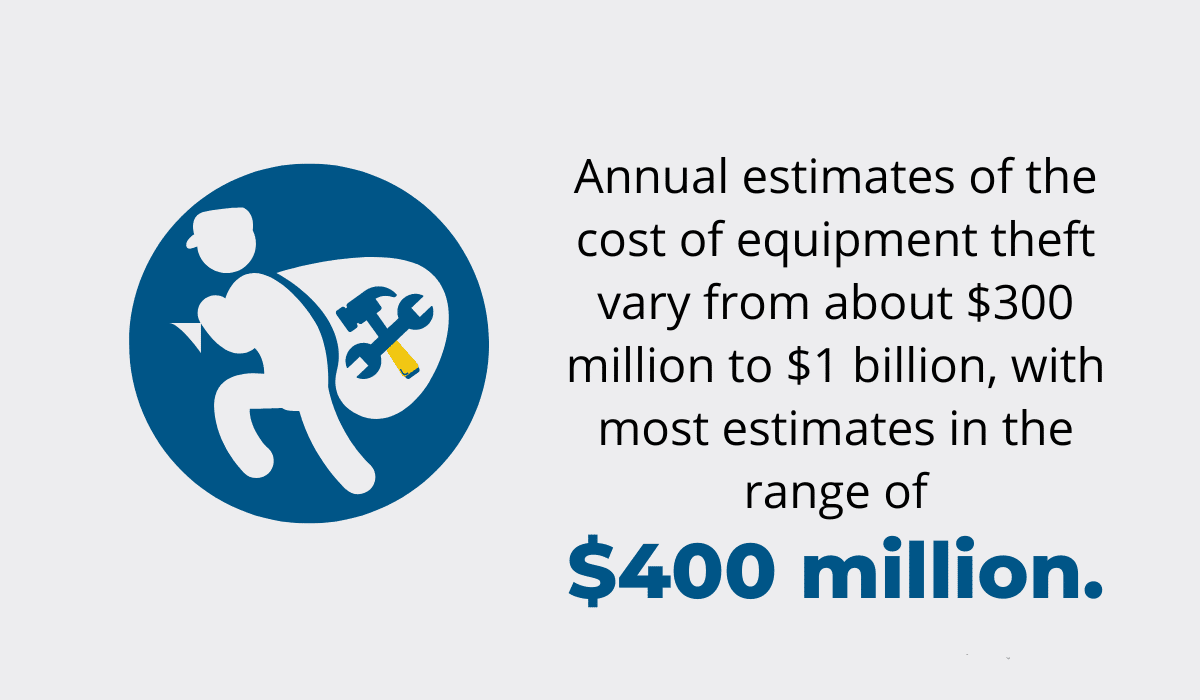
Tracking your equipment allows you to quickly determine which assets are missing and which person was the last one to use them.
Furthermore, if you are using a GPS tracker, you can easily pinpoint the location of the stolen object.
The more you know, the faster you can file a report with the police or deal with workers you suspect of wrongdoing.
Also, since GPS is increasingly used to track more valuable equipment, especially machinery, it also serves as an effective deterrent for criminals.
After all, a potential perpetrator is less likely to steal if they know there is a possibility that they will get caught.
Making Equipment Audits Easier
Using equipment tracking makes audits much faster and less burdensome for your business.
Instead of manually listing every item, employees scan the tags on each asset, which automatically feeds information into the equipment tracking software.
All data relating to a piece of equipment is stored inside your database and can be assessed individually or in a larger context.
For example, you could choose to list the warranties of all of your power tools at the same time, instead of checking each one separately.

As you continue to enter data on every piece of equipment into your tracking software, you will be able to create an ever more exhaustive list of your entire physical asset inventory, along with all the pertinent information.
This will make asset management and auditing much easier.
Keeping Up With Maintenance Schedules
Tracking your assets can also help you stay up-to-date with maintenance schedules.
In construction especially, regularly checking the condition of the equipment is crucial for both safety and productivity.
Your employees work in potentially dangerous conditions, and faulty equipment can lead to workplace injuries.
Furthermore, if larger equipment like machinery or a vehicle breaks down during production, it can cause work delays.
A day of work in construction is expensive, and extending deadlines due to malfunctioning equipment leads to much higher operational costs.
An equipment tracking database collects all maintenance information in the same place. When you pick an item, you can see the date of its last maintenance, as well as the next.
You can set up the system to send notifications or alert you of it, which means you don’t have to worry about maintenance schedules again.
How Can Construction Equipment Be Tracked
There are multiple ways in which you can track your assets, each with its own mechanism for storing and retrieving information.
Deciding which one to use depends on the size and needs of your business.
For small companies with less equipment, barcodes or QR codes might be enough.
Companies that own valuable equipment and work at multiple larger construction sites at the same time might find that GPS tags or RFID tags work better for them.
Let’s take a look at what each of them has to offer.
Barcodes
A barcode is made up of vertical black lines and white spaces of varying width, with an optional alphanumeric code underneath.
They are the most common and recognizable method of storing information for various purposes, most notably in retail.
This is because they are inexpensive to produce and simple to use.
You can even make, print and apply barcodes yourself without hiring a third party to do the job.
A barcode scanner or a smartphone is all that is necessary to recover the data, which is then transferred to your tracking software database.
QR Codes
QR codes are a more advanced type of barcode. The tracking protocol between the two is identical, but QR codes come with some additional advantages.
Firstly, QR codes are two-dimensional, which means they can hold a lot more data than their one-dimensional counterpart, the barcode.
They can even support images, which comes in handy if you want pictures to showcase the condition of an asset.
Your employees can scan QR codes from a greater distance and angle than a barcode, making the process quicker.
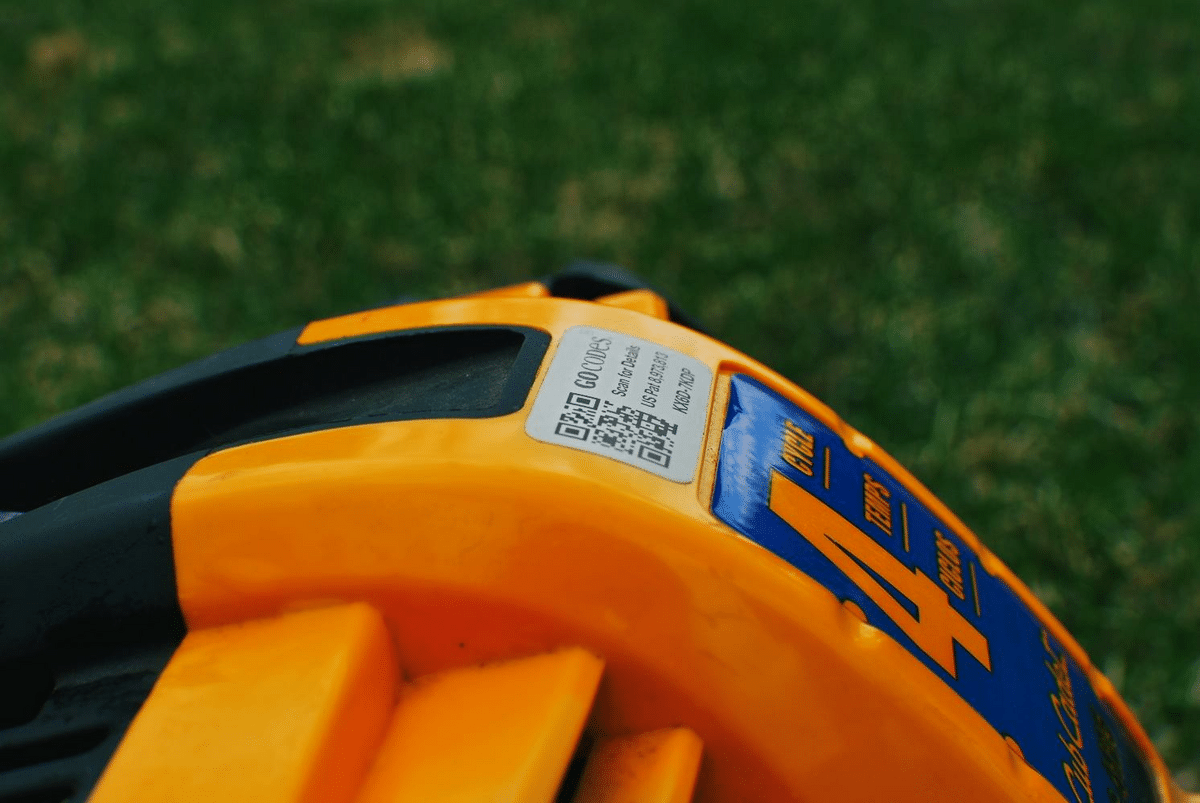
Finally, they are much more durable. While a scratch can make a barcode unreadable, QR codes can be scanned with only 30% of their original label left intact.
That’s why they’re an excellent choice for construction businesses, as they can be damaged by rough equipment handling, and still provide reliable information.
GPS
Global Positioning System, or GPS, is a satellite-based locating utility used in most navigational systems today.
Unlike barcodes or QR codes, GPS tags don’t require scanning as they automatically send updates to your asset tracking software.
But they do need a chip and batteries to work. All that, plus a durable enclosing case, makes them larger and more expensive than the previously mentioned tracking options.
However, GPS is the only tracking method that allows you to track your assets in real time over long distances.
If you own construction vehicles and other valuable machinery, a GPS equipment tracking system could provide an accurate oversight of their location.
Not only will this enable you to see exactly where your equipment is at any given moment, but it can also reduce the risk of assets being stolen or driven away without your knowledge, as already discussed.
RFID
Radio-frequency identification (RFID) technology sends or receives data via radio waves.
In short, RFID tags emit a small signal which is picked up by an antenna and relayed to an RFID reader.
There are passive and active RFID tags.
Passive RFID tags do not need a battery to work.
They only transfer data when they receive a signal sent from the RFID reader, which at the same time charges the asset tag enough to respond.
Passive tags are smaller and lighter than active ones. Because they are inexpensive and long-lasting, they are best suited for inventory purposes.
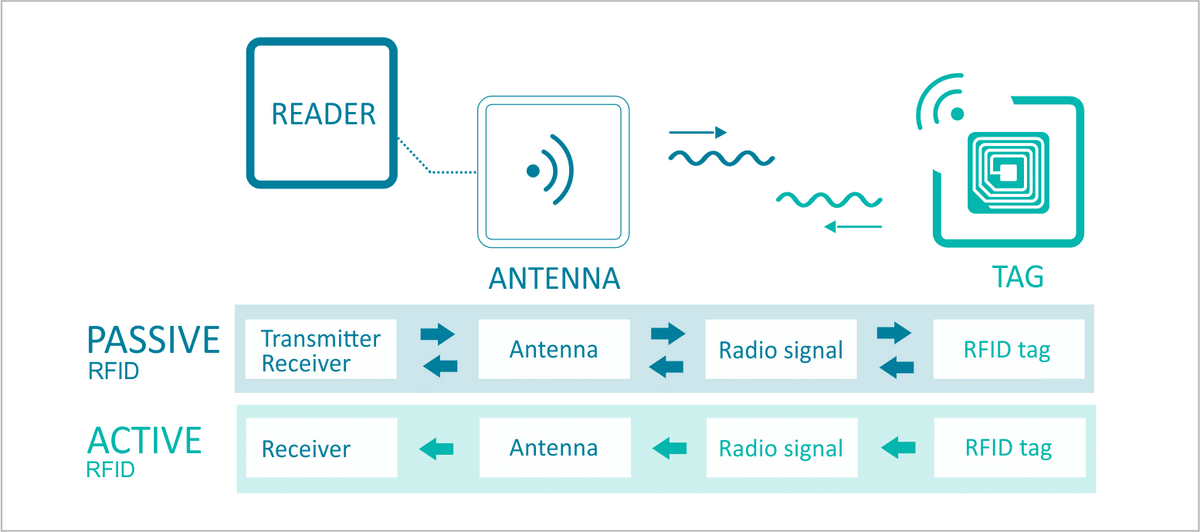
Active RFID tags are powered by batteries and continuously transmit signals. You can follow the location of your assets in real time, and over distances of up to 150 meters.
They are very useful if you need to track movable equipment on a construction site.
BLE
BLE stands for Bluetooth Low Energy, which is the most recently developed technology used in equipment tracking.
It shares similar functions to active RFID tags, but also has features that make it more beneficial.
Like RFID, it can wirelessly transfer data and provide real-time location information over short distances.
However, BLE tags are smaller, and therefore more convenient to use on a greater amount of assets. They are made for low power consumption and can last for years with just one charge.

You don’t need designated devices or scanners to interpret the signal because it can be done by any device that uses Bluetooth. And to top it off, they are very cheap to make!
Conclusion
Construction companies make money by using their assets, so they have to make sure their tools, machines and vehicles are accounted for and in good condition.
Equipment tracking helps you by automating much of the asset management process.
Using an asset tag system and an equipment tracking software solution, you can follow the movement of your vehicles, create an equipment database for faster audits and be notified of maintenance checks on time.
There are several tracking methods, and learning more about their differences will make it easier to decide which is right for your business.