It could be said that running an efficient and profitable construction company is hard without a great equipment manager.
To do their job successfully, these managers need to have specific traits that contribute to the holistic skill set required to navigate the day-to-day challenges of equipment management.
Understanding these traits is crucial for construction company owners, guiding them in hiring or promoting the right individuals or providing targeted support for their equipment managers.
Join us as we explore the six key attributes that set apart proficient construction equipment managers.
In this article...
Technical Proficiency
Given their job description, it’s not surprising that the equipment manager’s technical expertise and experience top our list of desirable traits.
Broadly speaking, this technical proficiency boils down to having:
- a strong understanding of the purpose, capabilities, and specifications of various heavy equipment, tools, and assets integral to day-to-day construction operations,
- in-depth knowledge of construction workflows and activities, their purposes, and the methods involved,
- the skills required for utilizing advanced software tools for equipment tracking, maintenance scheduling, and data analysis,
- awareness of emerging technologies in the construction industry and the capability to integrate them for improved equipment performance, safety, and project outcomes.
Naturally, the required level of technical knowledge in the above areas may vary depending on numerous factors, such as the company’s size and specialization, the scope of its construction projects, and the diversity of its equipment fleet.
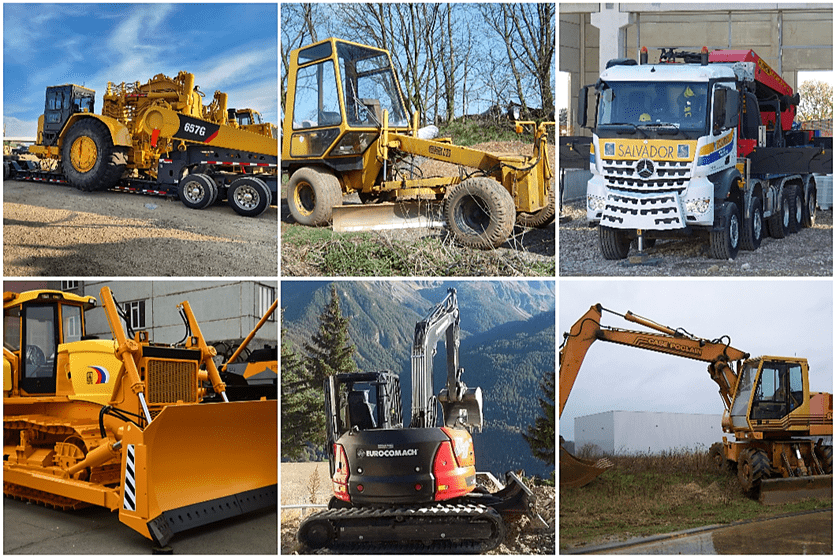
Despite possible differences in job requirements, successful equipment managers should have at least a strong knowledge of the technical characteristics of equipment, as well as workflows and methods involved in construction operations.
Moreover, they should strive to enhance their technical skills by leveraging opportunities for continuous learning, training, hands-on experiences, and proactive knowledge acquisition.
For example, if a new equipment manager feels they lack practical experience with different types of equipment, they can spend more time on-site.
There, they can observe how operators handle machinery to better understand performance requirements and challenges, and potential maintenance needs.
Likewise, they can engage with equipment operators to gather insights from their experiences.
They could enter the cabin and study controls or, if qualified, even operate the machine.
Aside from on-site experiences, they can leverage manufacturer training programs to deepen their technical understanding of specific equipment types, brands, and models.
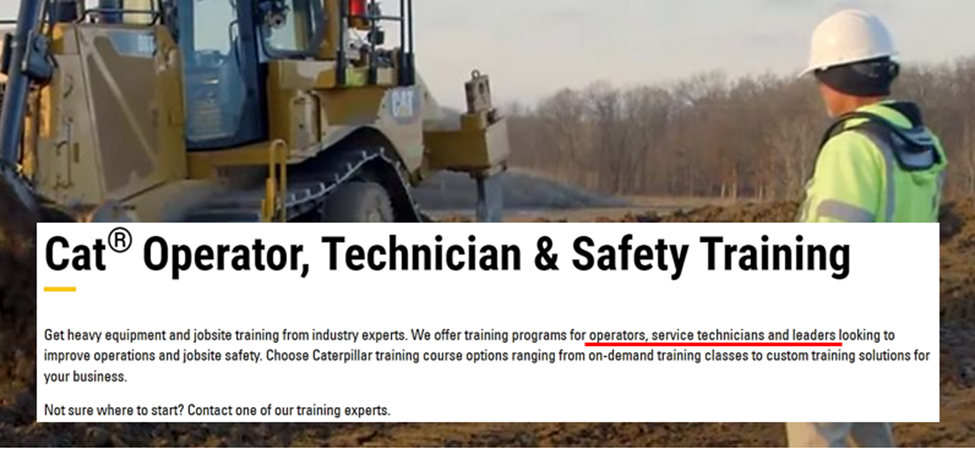
In the same vein, an equipment manager who wants to stay informed about the specifications and capabilities of various new equipment and tools and emerging construction technologies can:
- subscribe to industry publications and join professional associations,
- attend relevant workshops, conferences, and online seminars,
- network with other equipment managers and industry experts,
- attend product demonstrations,
- pursue relevant certifications in equipment management and technology.
Similarly, managers who feel they lack the necessary skills and confidence to manage new software tools and technologies can leverage resources and support provided by software vendors and participate in training programs to gain hands-on practice.
To recap, having a strong technical foundation in what processes, equipment, tools, and software solutions are used on-site is a requirement for successful managers.
Adaptability
Considering the dynamic nature of construction projects, adaptability stands as a cornerstone trait for successful construction equipment managers.
Put simply, a flexible manager knows that project requirements change, unforeseen challenges emerge, and construction timelines shift unexpectedly.
And they’re ready to adapt to those circumstances.
Of course, their ability to pivot swiftly and make informed decisions is predicated upon all the other traits covered here, such as organizational and communication skills, budgetary expertise, and technical proficiency.
The adaptability of successful equipment managers is also reflected in their willingness to adopt new technologies, recognizing the transformative impact they can have on operational processes.
This usually starts with equipment management software.
Such solutions offer a range of features that enable equipment managers to quickly adapt and competently react in unexpected situations.
Take a look at the features below and consider how they can increase the manager’s adaptability.
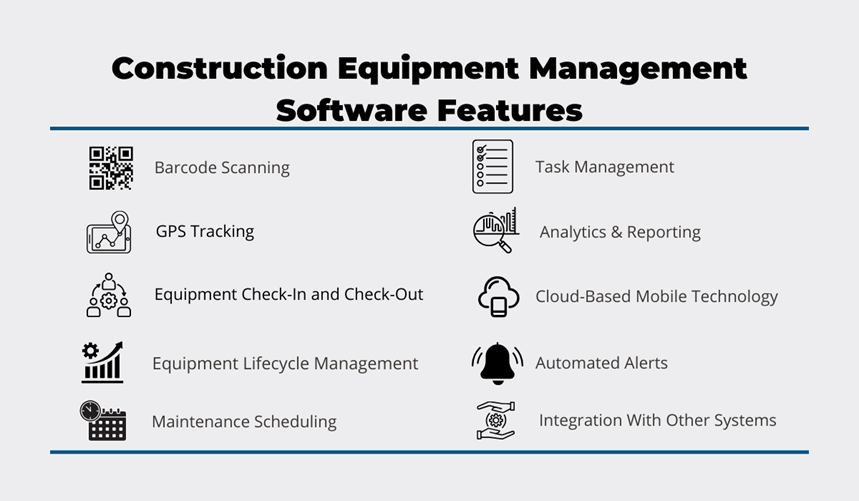
For example, when equipment and tools are tagged with barcodes/QR codes and coupled with cloud software, this enables equipment managers to track the utilization, locations, and maintenance status of each asset.
This means the manager can access the software’s database on any internet-connected device to instantly check where equipment is, who is using it, and whether and when it’s available.
Naturally, this significantly increases their ability to adapt to unexpected events that require quick equipment reallocation, such as when critical equipment breaks down on-site.
Despite all the benefits that can be generated by such solutions, some more traditional equipment managers used to pen-and-paper and spreadsheets might be reluctant to adopt them due to the perceived complexity of their implementation and use.
However, equipment management software can be both simple to implement and easy to use, like our solution, GoCodes Asset Tracking.
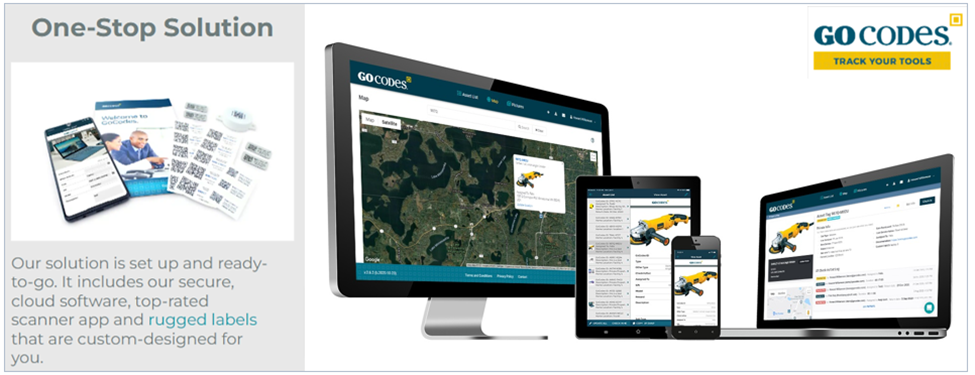
GoCodes Asset Tracking aptly combines cloud software with in-app QR code scanning, and equipment tracking tags (GPS-enabled QR codes), resulting in an affordable, ready-to-go solution.
The equipment manager receives custom QR code tags, attaches them to equipment and tools, and connects each tag with its info portal in the software’s database.
Digitized, automated, and streamlined equipment management can start.
Coupled with a user-friendly interface and strong user support, this ensures that both managers and field workers will be able to quickly adapt to using the software in everyday operations.
As for equipment managers, armed with real-time insights into equipment usage, location, and maintenance requirements, they’ll be able to make informed equipment management decisions, and promptly reallocate resources when needed.
Overall, adaptability is a critical trait of successful equipment managers. It is coupled with a readiness to adopt advanced equipment management tools and technologies.
Organizational Skills
Another top attribute of skilled equipment managers refers to having organizational abilities to schedule and manage equipment allocation and distribution, as well as equipment inventory and maintenance activities.
The ability to orchestrate these elements seamlessly is pivotal for ensuring that each piece of equipment is utilized to its maximum potential, reducing downtime, and increasing productivity.
Although some individuals may be more organization-savvy, stronger organizational skills arise from using the right combination of tools and methods.
For instance, equipment management software allows managers to schedule preventive maintenance activities, ensuring that all equipment is serviced when planned, thereby minimizing unexpected breakdowns and potential delays.
The manager can set a regular maintenance schedule for specific equipment in the software and assign the upcoming maintenance tasks to responsible staff members along with relevant details and instructions.
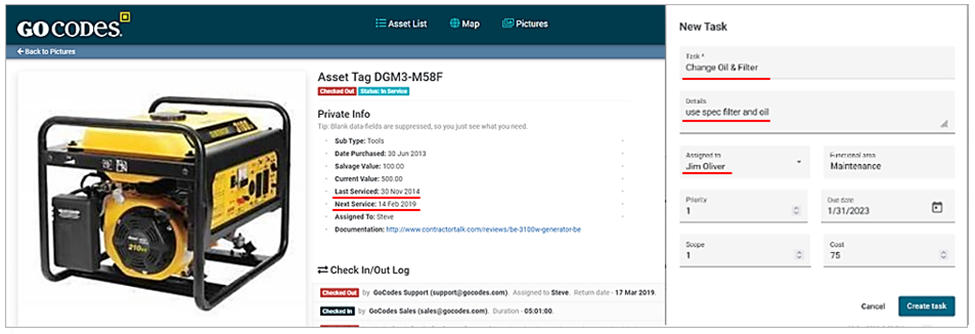
Concurrently, they can set up automated email reminders that the assigned service technicians will receive in the early morning on the day of their scheduled task, giving them plenty of time to check whether they have all the tools and supplies needed for maintenance.
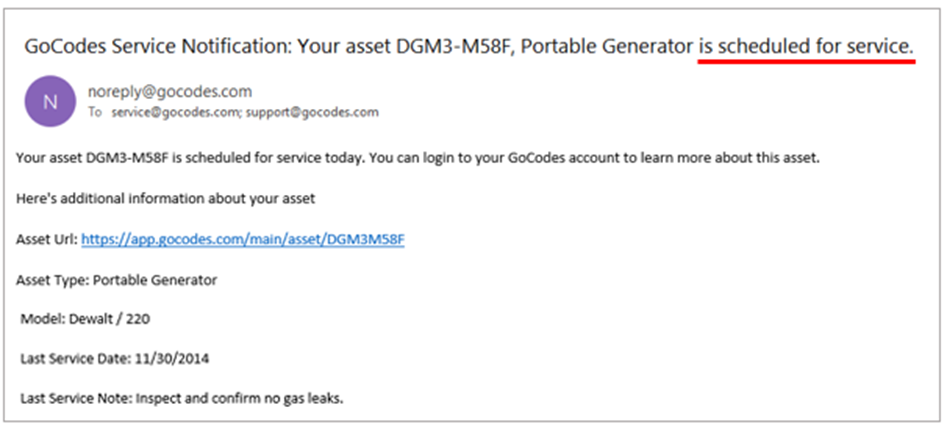
Once they complete their service task, technicians can note it in the app along with other relevant details, comments, and even photos.
Then, the manager can, if necessary, take further actions or mark the assignment as completed and schedule the next service.
The same software and asset tags can be used to streamline equipment inventory management.
Here’s how this organization-enhancing functionality works.
Managers can use this inventory-tracking feature to ensure that technicians always have the spare parts and other items required for maintenance, such as oils, filters, and cables.
Similar to scheduled service notifications, they can set the minimum quantity of items they want to have in stock, and the software will send a low-inventory alert when that quantity is reached.
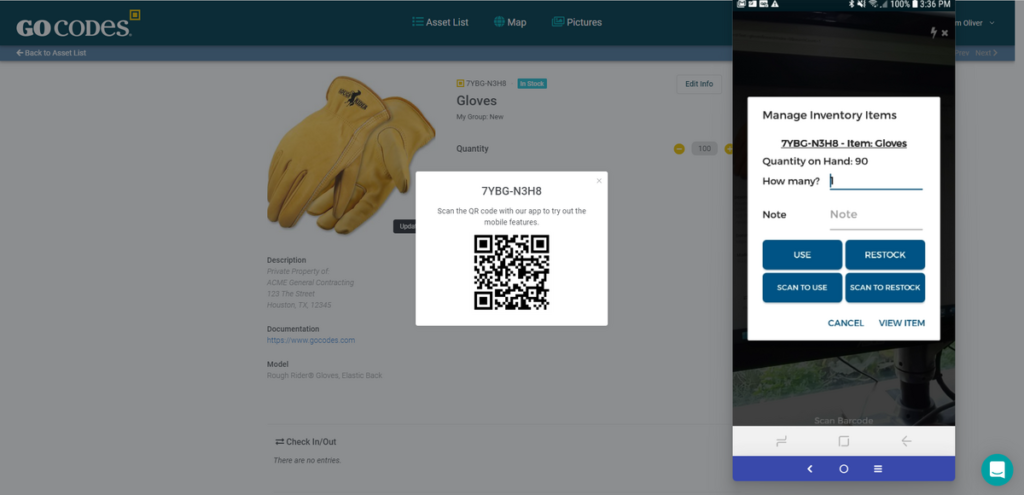
Naturally, software-enhanced organization of equipment allocation and distribution, maintenance scheduling, and inventory control should be supported by practicing clear communication (covered next).
To recap, good organizational skills allow the equipment manager to efficiently coordinate equipment usage and schedules, thus preventing delays and ensuring smooth project flow.
Communication Skills
Equipment managers need to be able to clearly convey equipment requirements, maintenance schedules, and safety protocols to all relevant stakeholders.
This includes everyone from on-site workers and equipment operators to service technicians, project managers, and top executives.
In general, effective communication in construction projects is essential for their smooth completion, as illustrated by these percentages from a study done by Procrew Schedule:
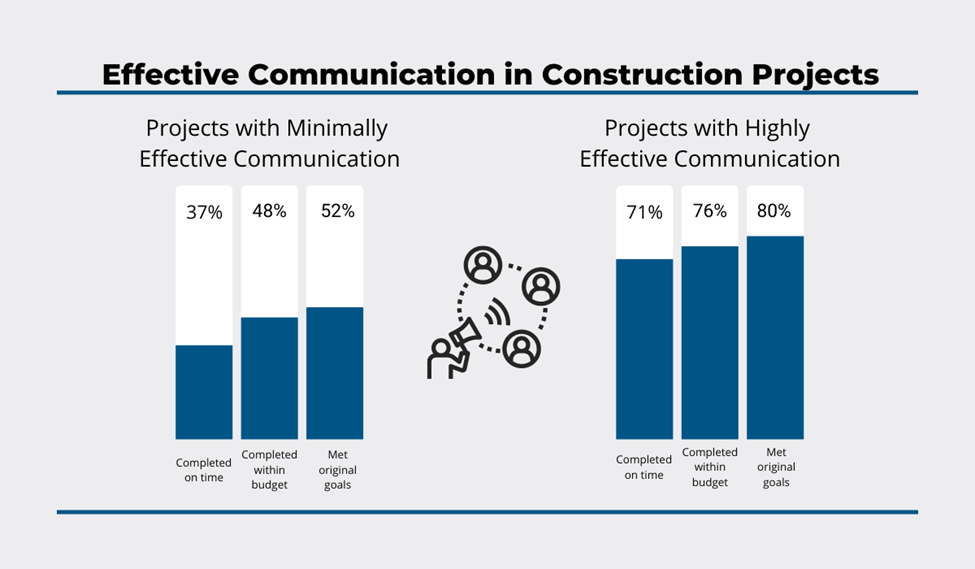
Since equipment managers often act as the link between on-site workers and office-based personnel, their ability for clear, simple, and concise communication is vital for achieving project success.
For instance, when allocating equipment for a new project, the manager needs to effectively convey to other project team members how specific project requirements and timelines affect the selection and deployment of particular equipment types and models.
The same applies to their coordination of equipment maintenance and repairs.
In such cases, streamlined communication ensures that maintenance tasks will be scheduled at times that minimize disruption to ongoing project activities.
Furthermore, since most maintenance tasks involve safety considerations (discussed next), the manager should transparently communicate these instructions to ensure the safety of the maintenance personnel and other on-site workers.
Therefore, the manager’s effective communication involves establishing the right communication methods and channels (technical and organizational skills) and using them to communicate information clearly (interpersonal skills).
The latter refers to active listening, keeping messages simple, encouraging others to confirm what they heard, and keeping records of important communications.
In conclusion, successful managers recognize that effective communication is the linchpin of project success and use hard and soft communication skills to ensure seamless information flow across all project stakeholders.
Commitment to Safety
Although they’re not the only ones in charge of equipment and jobsite safety, successful equipment managers are committed to promoting adherence to safety regulations and guidelines through implementing equipment-related safety training programs.
Naturally, this helps prevent construction site accidents and ensures that the site complies with relevant safety regulations and standards.
In turn, this aids in avoiding not only work stoppages, low morale, and insurance claims resulting from on-the-job injuries but also penalties and legal issues stemming from regulatory non-compliance.
For example, a manager can organize safety training sessions or meetings where they’ll cover various safety aspects.
This involves a wide range of topics, so here are just some general ones.
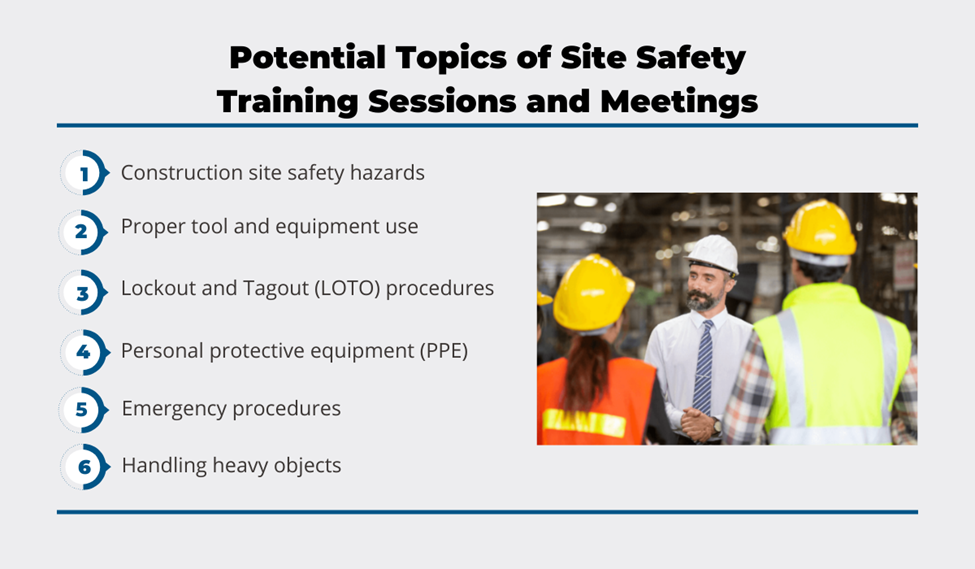
Of course, the equipment manager is also responsible for staying abreast of safety regulations, ensuring that any changes to local, state, and federal regulations related to construction equipment and safety are complied with.
Furthermore, a safety-committed manager will ensure that:
- routine equipment inspections include safety compliance checks,
- equipment operators are adequately trained and certified, and
- a safety-first culture is promoted, implemented, and followed.
In conclusion, a successful manager will put safety first, ensuring adherence to safety regulations and standards prescribed by external regulatory bodies, as well as those set by the company’s internal safety guidelines.
Budgetary Expertise
Lastly, successful equipment managers know how to build and manage equipment budgets, including procurement, maintenance, and repair costs.
More specifically, they should be able to create an equipment budget with estimated operating costs for every already agreed or potential construction project.
Among other things, this requires general knowledge and practical expertise that allows the manager to competently perform the following budgeting tasks:
- Build a list of equipment the budget will affect
- Correctly estimate, forecast, and project budgeted equipment costs
- Confirm prices and estimates for the budgetary period
- Include “hidden” costs of operating equipment, such as fuel, insurance, training, repairs, and maintenance
- Calculate and include equipment depreciation costs
- Plan for purchases ahead of time, make equipment repair-or-replace decisions
- Carefully consider financing plans for major purchases
Naturally, to do these tasks more accurately and efficiently, equipment managers can rely on specialized budgeting applications or budget-assisting features of other relevant tools such as project management and equipment management solutions.
For instance, they can use GoCodes Asset Tracking’ depreciation calculation feature to better understand whether and when to repair, rebuild, or replace equipment.
Likewise, budgeting for construction equipment is usually a collective effort.
This means that managers should leverage their team members and other company employees with specific budgeting knowledge or seek outside assistance to make their equipment cost estimates more accurate.
Long story short, the budgetary expertise of great equipment managers allows them to optimize equipment usage, control expenses, and maximize the equipment’s return on investment (ROI), thereby contributing to the overall profitability of construction projects.
Conclusion
It’s clear that the characteristics of an ideal construction equipment manager involve an impressive and comprehensive set of hard and soft skills seasoned with broad technical knowledge and hands-on experience.
Although every manager will have stronger and weaker areas, the gaps in skills and expertise can be successfully addressed through continuous learning, collaboration, and the adoption of advanced software solutions.
With the right tools and proper motivation, your equipment manager can be more successful in driving optimal efficiency, safety, and profitability of your construction projects.