In construction, equipment inspections are a crucial part of effective maintenance, which helps ensure workers are safe, equipment is optimally used, and the project timeline and budget remain intact.
That said, you don’t want complex inspections to slow down your operations, creating a ton of administrative tasks workers will avoid doing even at their own risk.
To help you strike the right balance between thorough inspections and operational efficiency, we’ll cover five key factors to consider during equipment inspections.
In this article...
Original Manufacturer’s Instructions
As mentioned, regular inspections protect the safety of your workers, the efficiency of your operations, and the longevity of your equipment.
However, given the number of different construction equipment types and models (not to mention, various technological advances), determining what inspections to perform and when and how to perform them can be a daunting task.
And that’s why consulting the original manufacturer’s instructions should be your starting point, i.e., the first factor to consider.
After all, these instructions are meticulously crafted by the experts who designed and built the equipment.
As a result, they offer detailed insights into the specific inspections and maintenance procedures necessary to keep the equipment running smoothly and extend its lifespan.
For instance, the safety tips, operational checks, and troubleshooting sections of this crawler dozer’s service manual should provide all the necessary information to determine what inspections should be conducted.
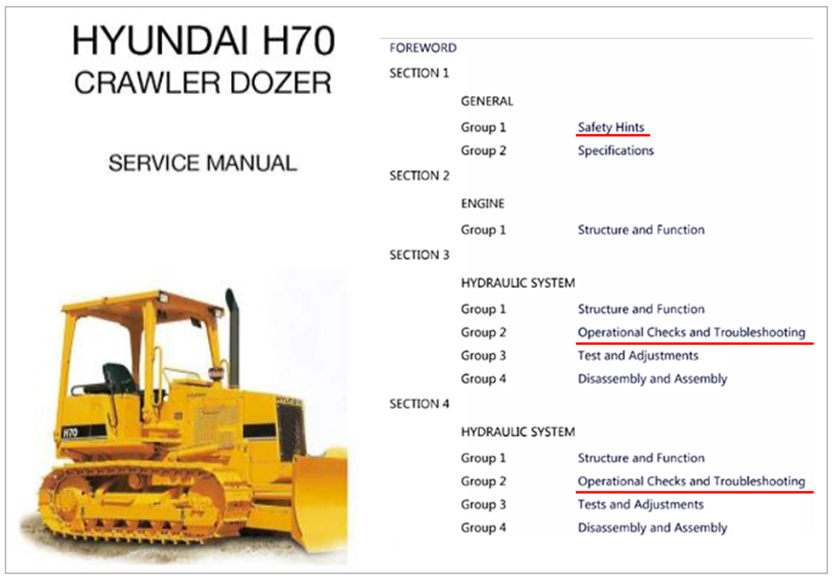
The equipment-specific recommendations in such instructions will also ensure compliance with safety standards and best maintenance practices, preventing accidents and breakdowns.
Additionally, following the manufacturer’s guidance is crucial for avoiding issues when a machine under warranty breaks down.
In other words, many equipment warranties require that inspections and maintenance be performed as outlined in the original manufacturer’s instructions.
Therefore, any deviations can void warranties, potentially resulting in significant financial setbacks.
In conclusion, the original manufacturer’s instructions are an invaluable resource in planning and executing equipment inspections, offering a roadmap for ensuring equipment safety, performance, and longevity.
Frequency of Inspections
When it comes to how often equipment should be inspected and for what purposes, you should follow the manufacturer’s instructions we just covered.
However, there are other factors to consider, such as state and federal regulations, your company’s inspection and maintenance standards, the equipment’s age and condition, and the operating environment.
Any of these factors may lead to your company establishing different inspection intervals from the manufacturer’s specifications.
Naturally, while under warranty, equipment should be inspected at least as frequently as the manufacturer recommends.
Here’s an example of a skid steer loader’s service schedule with recommended inspection intervals.
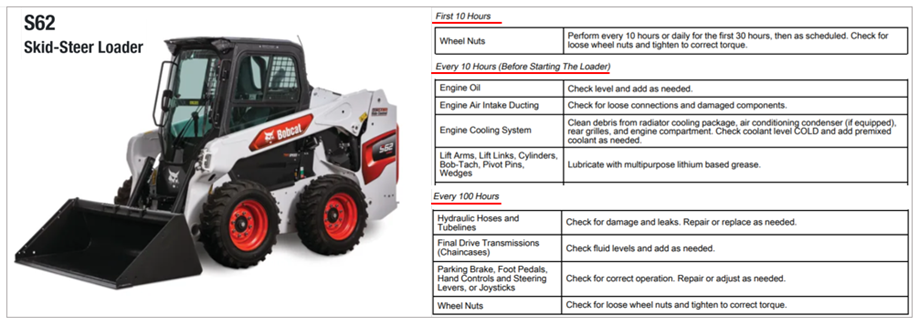
As you can see, such inspections can be pre-operational, daily, weekly, or based on specific operating hours/mileage limits.
Whatever the recommended frequency, you should also consider the factors mentioned above that may affect the inspection intervals your company determines.
For instance, an inspection scheduled every 100 operating hours can instead be conducted every 50 hours because your construction site operates in a particularly dusty environment, which increases wear and tear, potentially clogging machine components.
In such cases, even the manufacturer will typically recommend so, or building regulations may require the same.
Lastly, your company’s preventive maintenance plan could have specific guidelines that suggest a different inspection schedule based on your service team’s experience with similar equipment in your unique working conditions.
Overall, the frequency of equipment inspections should follow the manufacturer’s recommendations but also consider specific factors like the equipment’s warranty status, age and maintenance history, operating conditions, local regulations, and company standards.
Inspection Complexity
Considering the technical complexity of most construction equipment and all the checks that need to be performed, it’s easy to get carried away and create lengthy and intricate inspection checklists, leading to overly complex inspection procedures.
Unfortunately, however meticulous, such checklists can overwhelm equipment operators or maintenance teams, costing them precious time and making it more likely they’ll skip or rush through crucial steps.
Naturally, this increases the risk of accidents, equipment breakdowns, and project delays.
Another common issue is when all the inspection checklists are found on one form, making specific checks seem more demanding than they are.
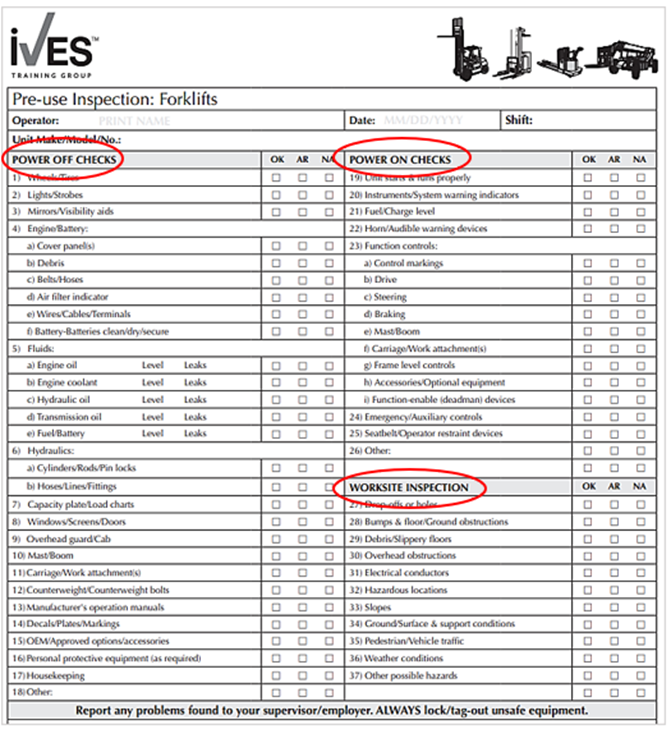
This practice stems from the fact it’s easier to distribute and collect one paper form than a whole stack of them.
However, contractors still using paper checklists should strive to separate different inspection types, at least visually.
Moreover, pen-and-paper methods are quickly giving way to software tools that offer user-friendly interfaces and the ability to create digital, customized inspection checklists and automated procedures.
Such tools can remove manual, time-consuming paper-to-digital data transfers, reduce errors, and automate inspection processes.
At the same time, keeping your inspection checklists in a central cloud database of tools and equipment allows workers to easily access them on-site, review instruction manuals and maintenance history, and use relevant information for reporting.
To recap, you should consider inspection complexity and simplify inspection checklists accordingly, focusing on the most critical items that significantly impact equipment safety and performance.
In doing so, digital tools can help you strike the right balance between keeping inspections simple yet effective.
Level of Employee Training
Since it’s up to equipment operators/workers to inspect the equipment they use and identify any potential issues, considering their level of training when preparing your inspection forms is a logical approach.
In other words, you want to ensure that all operators, regardless of their experience/training, can go through the checklist without encountering questions or instructions they don’t understand.
At the same time, you want the equipment’s major components essential for its safe and efficient functioning to be effectively checked to avoid jobsite accidents and equipment failure.
For example, these are just some questions that can serve as items to include in an excavator inspection checklist.
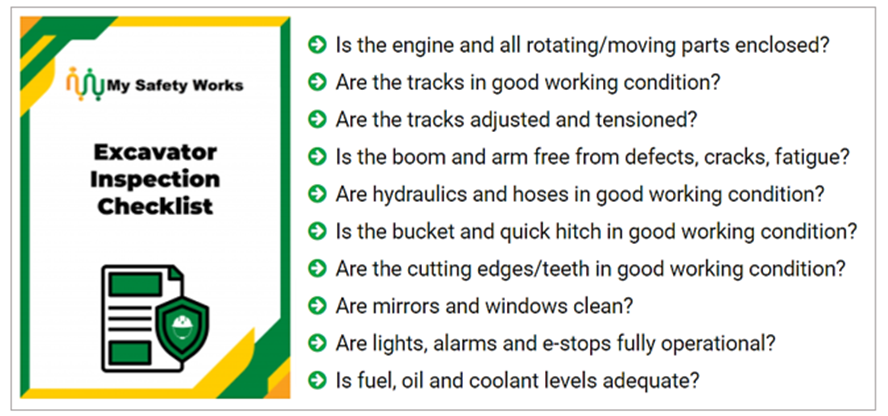
Given the above, the first thing to do is consult the manufacturer’s instructions and web sources and your team members (maintenance staff included) to identify:
- what checks must be performed for each specific equipment type/model
- what checks should an operator/driver/worker know how to perform
- what checks will be performed by service technicians
When equipment-specific checklists (one for operators, one for service technicians) are ready, you can test them on a few less and more experienced operators to identify any training gaps.
From there, you can develop training focused on how operators can efficiently conduct equipment inspections, complete checklists, submit them, and report any observed issues.
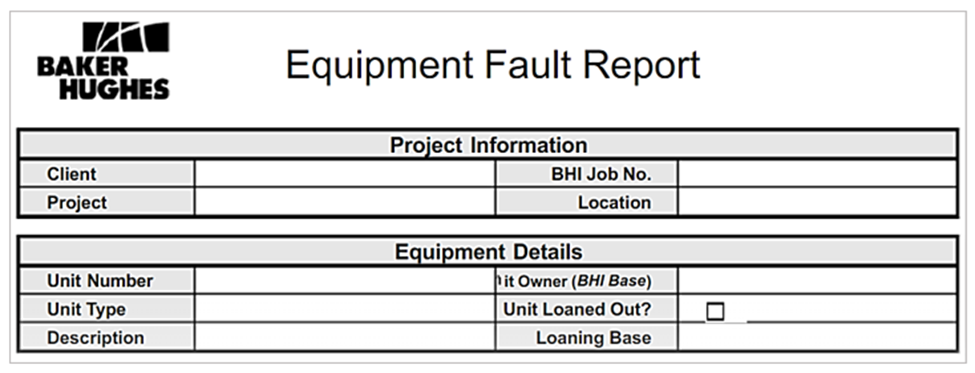
For less experienced workers, inspection forms can include guidance notes on how to inspect the equipment and record their findings.
Another measure that can be applied to ensure equipment inspections are properly conducted is to have the forms filled out by newbie operators/workers reviewed by a supervisor or a more experienced colleague.
Summing up, considering the level of employee training should help you design inspection forms that ensure all necessary checks are performed, and relevant data is collected quickly and efficiently.
Equipment Inspection Follow-up
Actions that follow equipment inspections, such as maintenance work orders and actual servicing and repairs, are probably the most important part of an actionable preventive maintenance program.
Another key component is tracking all these inspection forms, maintenance task assignments, and resulting actions to ensure equipment is regularly serviced and any issues are addressed in a timely manner.
To do that efficiently, construction companies are increasingly stepping away from time-consuming and error-prone pen-and-paper and Excel worksheet tracking methods.
Instead, they select one of many software tools available today.
For example, what if the equipment operator/worker could instantly access the right inspection checklist and other equipment details just by scanning a QR code, as shown below?
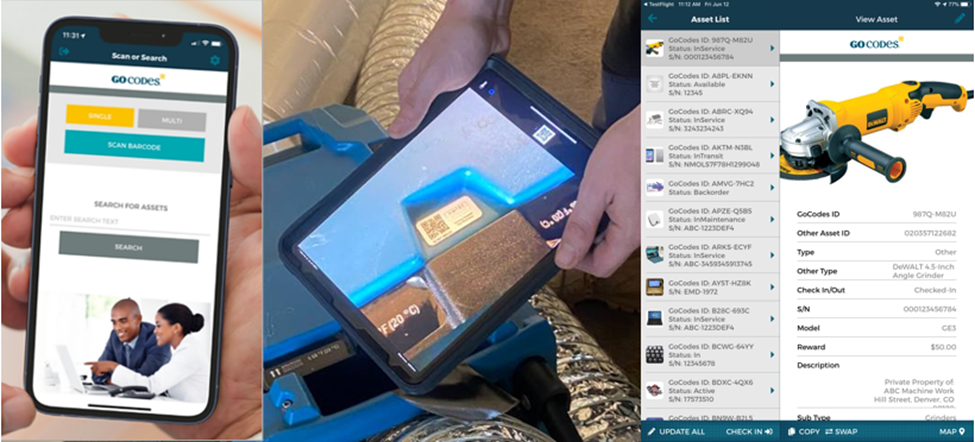
As you can see, when the QR code label affixed to equipment is scanned with a smartphone or tablet with the tracking app installed, users can use the in-app scanner to access the equipment’s info page.
From there, it’s easy to find any linked inspection checklists.
In parallel, they can see the equipment’s general information, safety guidelines, instruction manuals, inspection and servicing history, scheduled maintenance, as well as notes on recurring issues.
Simply put, the QR code acts as an instant gateway to a central database with all the records and forms required to track inspections and follow-up actions like work orders and task assignments.
Moreover, some QR code-based solutions, like our asset-tracking app GoCodes Asset Tracking, also enable you to automatically track the location of your tools and equipment.
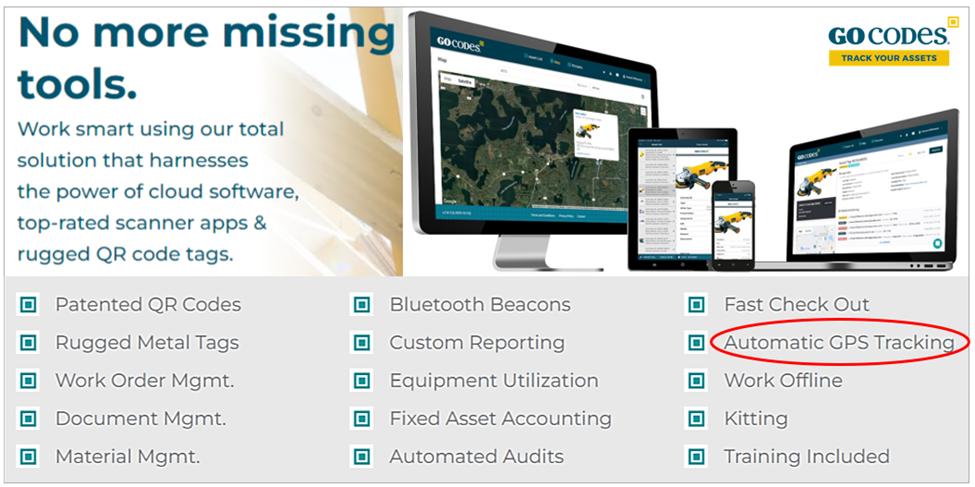
Among its many features, GoCodes Asset Tracking utilizes patented GPS QR code labels to automatically capture the equipment’s GPS location whenever a worker scans it with their phone or tablet.
That way, it’s easy to track the chain of custody and know where your tools and equipment are and who is using them, thus reducing the risk of theft and increasing worker accountability.
As for equipment inspections and follow-ups, you can track and manage the completion of inspections, detect reported issues, assign and schedule maintenance tasks, and monitor their execution.
All in all, equipment inspections and follow-up actions can be efficiently and affordably tracked and managed using cloud software that collects all equipment data, which can be easily accessed with a simple QR code scan.
Conclusion
Now that we have covered the five factors to consider during equipment inspections, all that’s left is the main takeaway.
In a nutshell, you should find the right software tool(s) to streamline your equipment-related workflows (including inspections). That means you should define, digitize, and automate inspection and maintenance processes.
Then, you should consult the equipment manufacturer’s instructions, determine what inspections should be performed and when, how inspection lists and procedures can be simplified to fit the employee training level and ensure inspection follow-up.
Ultimately, this will enable your company to establish effective inspection workflows, thereby protecting your workers’ safety and extending your equipment’s lifespan without compromising the efficiency of your construction operations.