Working in construction, you already know that the importance of maintaining your equipment cannot be overstated.
Regular equipment inspections are a crucial part of the maintenance process, but sometimes, they get overlooked among all other responsibilities. Managing construction projects, after all, is no easy feat!
To help you out, we’ve put together five must-follow practices that will ensure your equipment inspections are thorough, effective, and very well-planned so they don’t disrupt your workflow.
Let’s get started!
In this article...
Following Official Inspection Guidelines
In a hazard-prone industry like construction, adhering to rules and regulations can prevent accidents or injuries and, quite literally, save lives.
One of the most well-known organizations responsible for regulating job sites across the US is the Occupational Safety and Health Administration (OSHA), whose objective, according to their own website, is to “ensure safe and healthful working conditions for workers.”
As a way of achieving this, OSHA established a set of standards, which it enforces through workplace inspections and examinations.
Failing to comply with these requirements may result in hefty fines and penalties. Shown below are the maximum penalty amounts that have been in effect as of January 15, 2023.
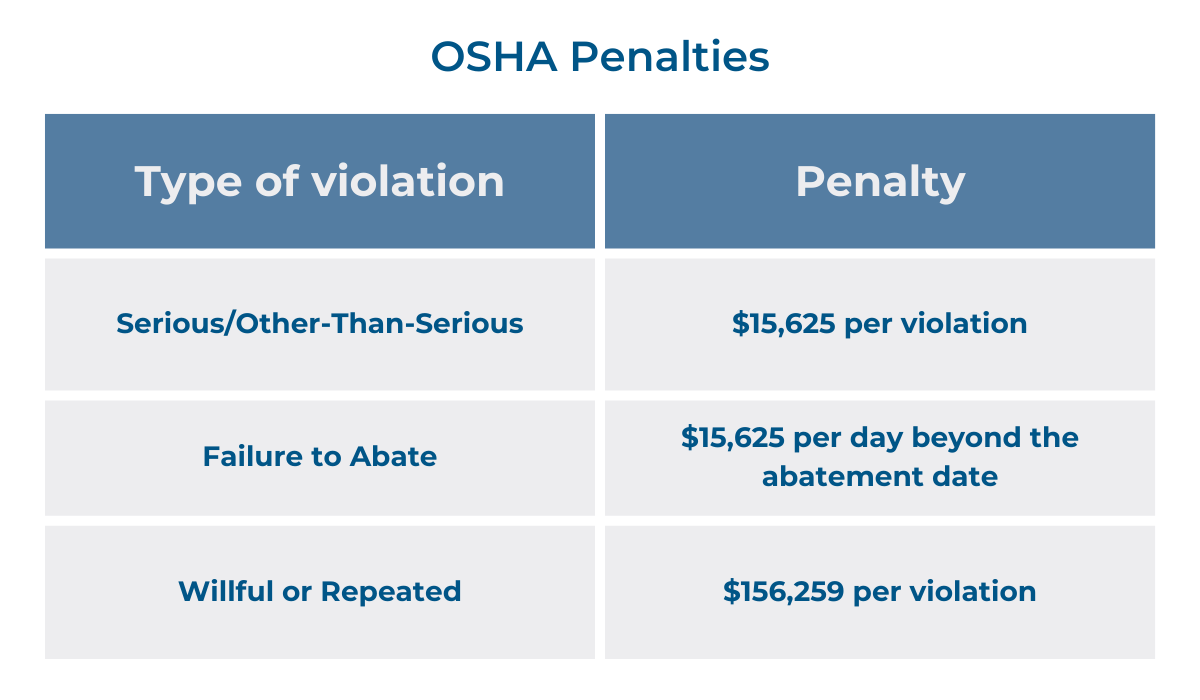
Illustration: GoCodes Asset Tracking / Data: OSHA
Employees themselves can request an inspection if they feel like they’re working in an unsafe environment, but generally, OSHA inspectors will show up without any advance notice to perform a job site audit.
Although there are some exceptions to this rule, such as, for instance, when an inspection needs to be carried out outside the regular working hours, according to the organization’s own inspection training document, this rarely happens.
The standards vary based on the type of equipment and are outlined in detail, including the procedure for daily, monthly, or annual checkups, as well as the asset documentation owners need to keep.
For example, cranes and derricks, according to the regulations, require a visual examination before each shift in which the machines are going to be used.
Please keep in mind that the regulations may change from time to time, so it is advisable to frequently check the web pages for revisions. It’s always better to stay updated with the guidelines to be well prepared when an inspector visits.
Fortunately, the organization provides a comprehensive overview of its inspection process on its website. Below is a brief extract.
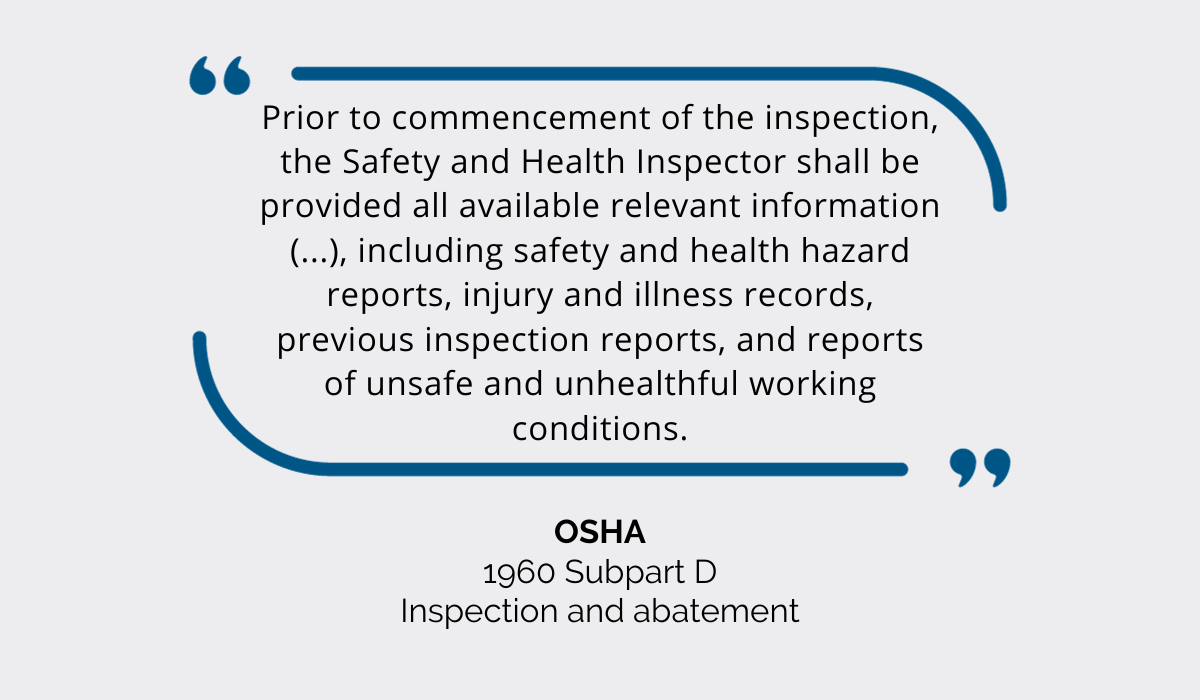
Illustration: GoCodes Asset Tracking / Data: OSHA
Overall, keeping worksites up to date is crucial for maintaining safe work conditions as well as for retaining streamlined workflow during inspections.
By staying on top of all the rules and safety measures, you can protect yourself, your team, and your assets from potential hazards and ensure that the business runs smoothly.
Creating an Equipment Inspection Checklist
Managing all the asset inspections, maintenance, and calibrations can be quite overwhelming, that’s for certain.
However, there is a method that can help you and your team stay on track with all important tasks.
Inspection checklists are designed in a way that ensures no stone remains unturned, as they contain a list of all the machine parts of each piece of equipment that need to be checked out by your team members.
Due to their effectiveness, they find their use not only in construction but across multiple industries, like warehousing, retail, and manufacturing.
Take a look at Volvo’s recommended visual inspection checklist for excavator undercarriages as an example.
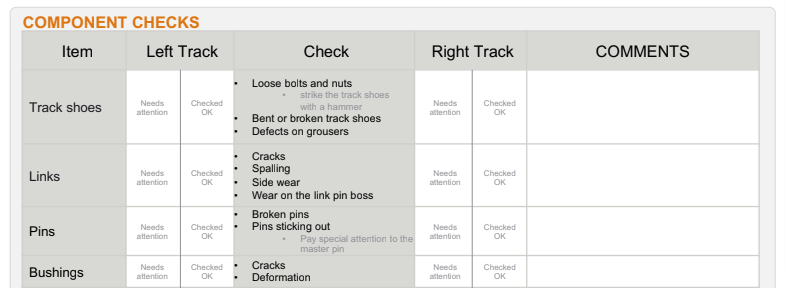
Source: Volvo
Keep in mind this is just a portion of quite a comprehensive list.
Creating such detailed lists of tasks might seem too time-consuming at first, but it does pay off in the long run.
In fact, if done right, they can increase overall productivity as they introduce a standard procedure everyone can follow. This way, any confusion is eliminated. No more fumbling through inspections.
In other words, checklists make sure the process is the same every time and every single task is carried out. No exceptions.
Before you start planning your own inspection agenda, don’t forget to examine the current condition of the machinery, figure out where it is in its life cycle, and make a record of it.
Definitely consult with the equipment manufacturer manuals (OEMs), too. They provide proven and informed ways of keeping your machines in good condition for as long as possible and, as such, should be an indispensable part of asset maintenance.
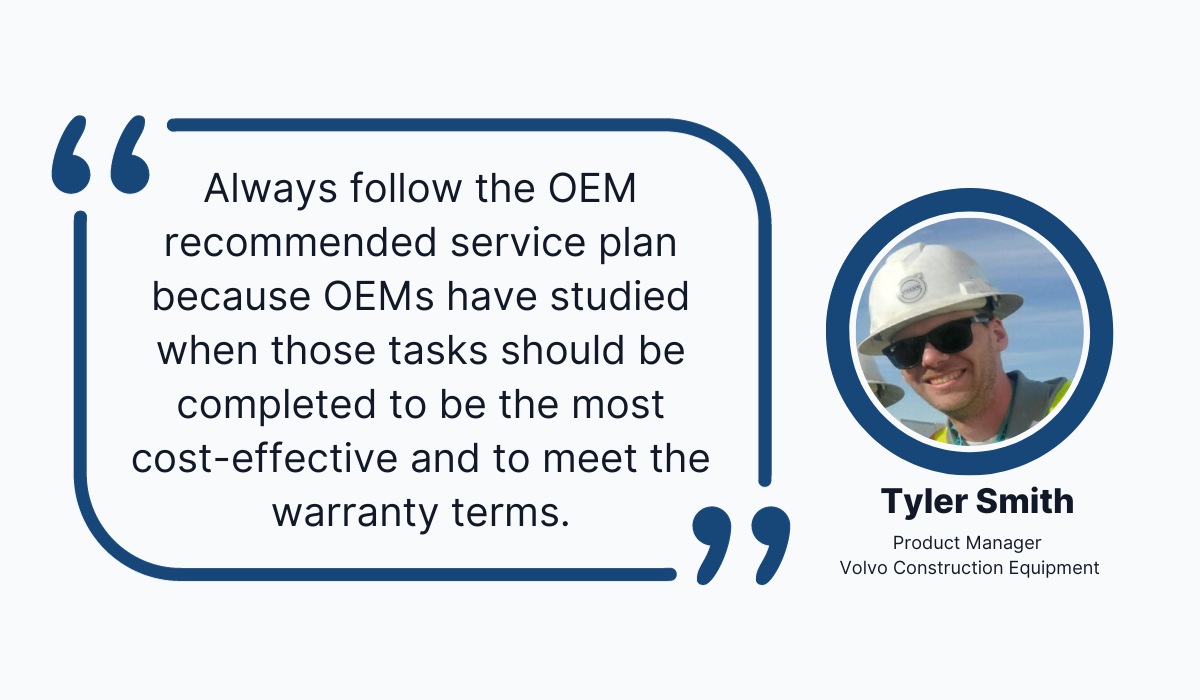
Illustration: GoCodes Asset Tracking / Data: CON/AGG
For example, Volvo recommends visual checkups of excavator undercarriages every 40 operating hours.
After you’ve covered all the basics and reviewed the necessary documentation, you’re ready to move on to the actual list.
Consider all the elements that might require attention and group them together. Below are just a couple of examples of possible categories:
- Outside the machine: check for leaks or fluid pools, inspect body for visual damage
- Inside the cab: remove personal objects, ensure that warning lights are not illuminated
The rest of the items can be arranged into categories such as tires, fluids, engine compartments, and others. For a more in-depth guide on maintenance and inspection checklists, click here.
In general, developing this list of tasks is a valuable investment for your team’s efficiency, equipment safety, and longevity. Therefore, take the time to establish a comprehensive checklist and reap the benefits of a well-maintained workplace.
Prioritizing Critical Elements of Equipment
However, it’s important to note that even the most detailed maintenance checklist won’t help you streamline the inspection process if you treat all the elements of equipment with the same amount of attention.
In other words, particular machinery components, such as engines, cooling systems, electrical components, and tires, should be prioritized when performing inspections. After all, there’s a limit to the time and money you can allocate to the process.
So, how do you figure out what to prioritize?
According to Dynamox, you do so by determining the machine’s criticality, which the company defines as follows:
“(…) criticality is the attribute that demonstrates the importance of a machine within a productive process, that is, how much a given machine is indispensable in the context of an operational system.”
In essence, this term defines the level of equipment’s importance for your workflow and project completion.
To determine criticality, it’s necessary to think about what would happen should a machine break down, relying on six criteria:
- Safety: how dangerous would it be for a piece of equipment to fail?
- Product quality: how much would failure affect the quality of the product?
- Impact on production: would failure lead to a decrease in productivity or even cause projects to stop?
- Mean time between failures: what’s the time between equipment failures?
- Mean time to recovery: what’s the average time needed to fix a broken piece of equipment?
- Maintenance cost: how much does it cost to repair a broken piece of equipment?
Asking yourself these questions will help you figure out how exactly a particular asset’s failure will affect you.
Each of the criteria then needs to be analyzed for every piece of equipment and then classified according to three levels of impact:
- A: high impact
- B: medium impact
- C: no impact
There are different ways to define criticality, and some businesses look at factors other than the six mentioned above, such as years of service or average utilization frequency, but generally, this is a good starting point for deciding which assets to prioritize during inspection.
Remember, though, that no machine should ever be overlooked. Lower priority doesn’t imply there’s no need for maintenance, only that specific components necessitate varying degrees of attention.
Keeping Track of Equipment Inspections
Performing thorough equipment inspections is only one part of properly maintaining your assets. Keeping accurate, detailed, and up-to-date records of these procedures is just as important.
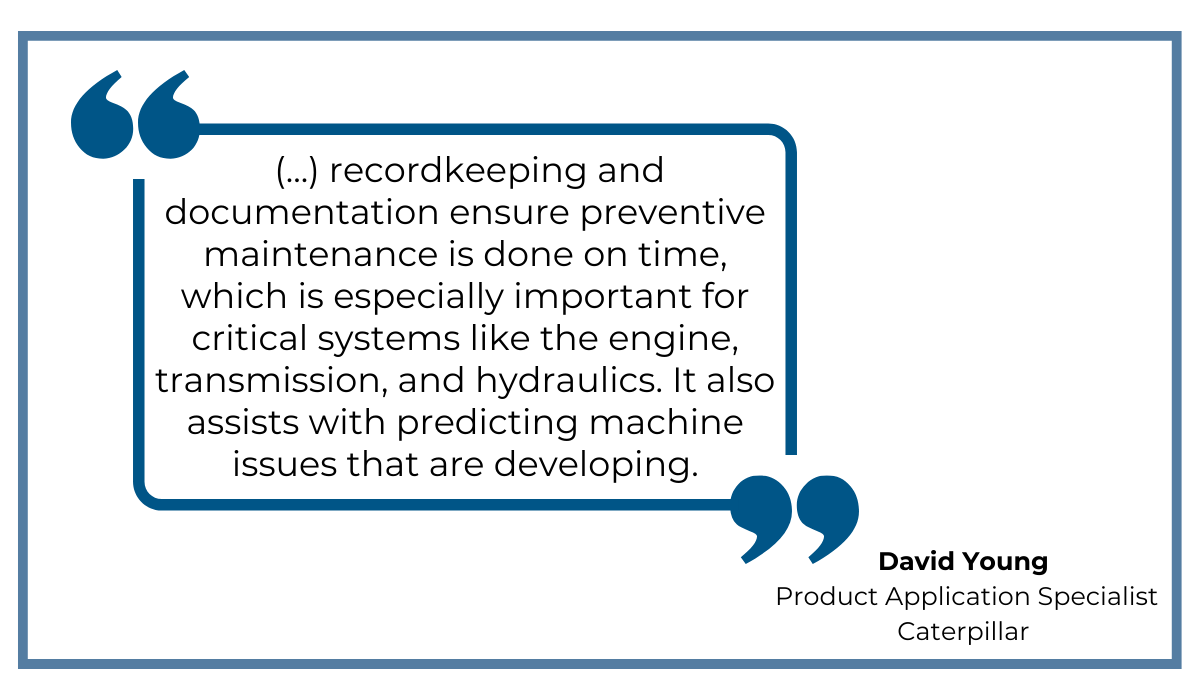
Illustration: GoCodes Asset Tracking / Data: CON/AGG
Asset history and documentation can be invaluable for businesses. They aid in planning future maintenance, demonstrate regulatory compliance during safety inspections, and serve as evidence in accident/insurance investigations.
Therefore, making sure you don’t lose those valuable documents and keeping them well-organized should be a priority.
Although this seems obvious enough, it’s not impossible to misplace paperwork every once in a while. If you rely on paper forms or spreadsheets to keep tabs on maintenance, you probably already know this.
These manual methods are highly prone to human error, inefficient, and labor-intensive.
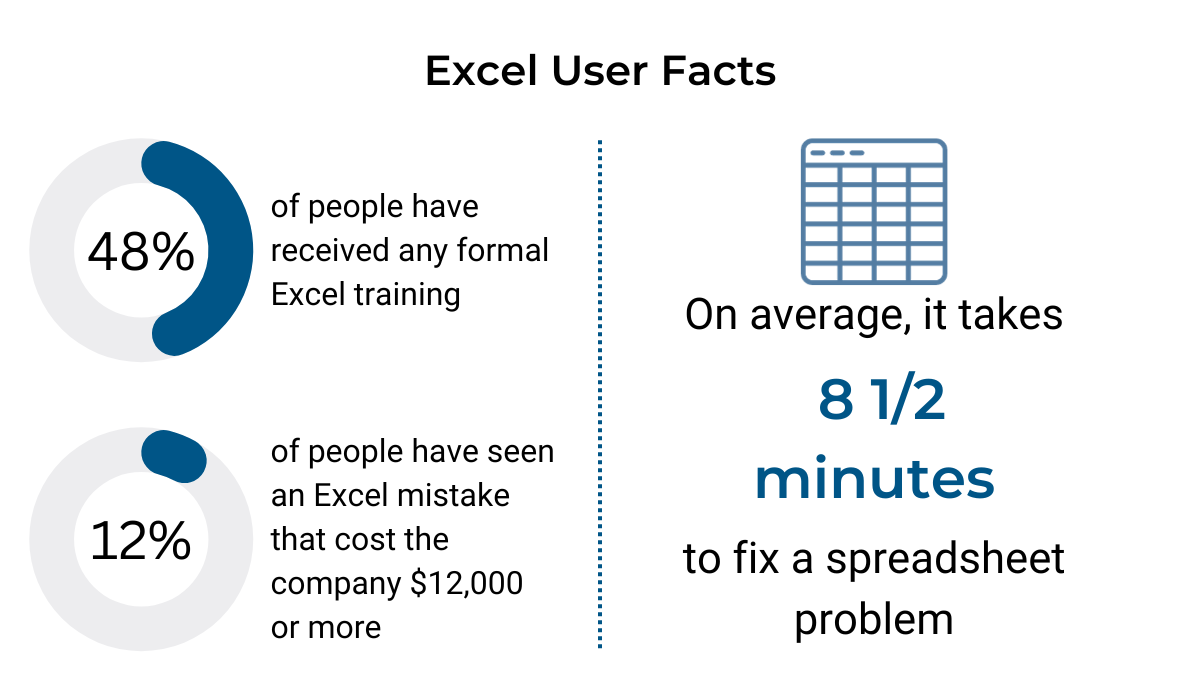
Illustration: GoCodes Asset Tracking / Data: Acuity Training
Not to mention, the mistakes they produce take too much time to fix. Survey findings on user Excel proficiency shown above prove so.
Instead, it’s better to use a cloud-based system with a centralized maintenance log, which will be updated automatically each time an inspection is performed.
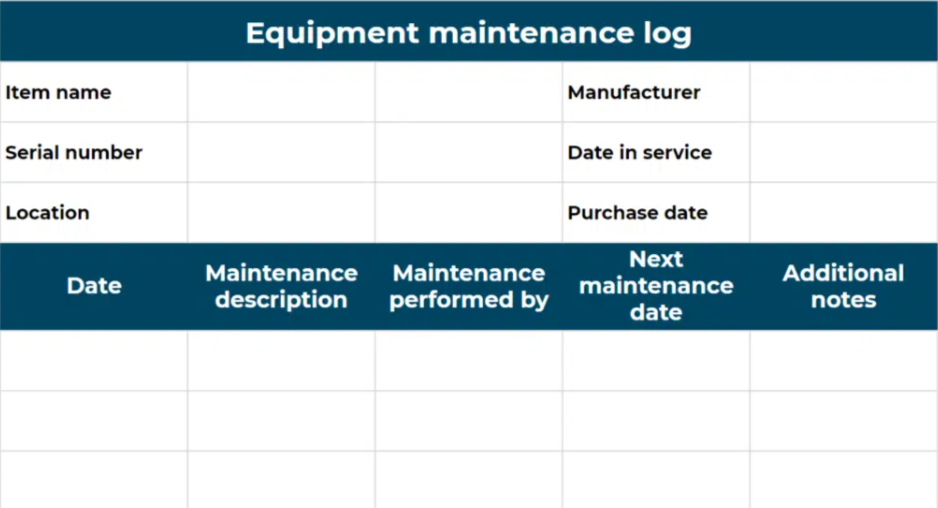
Source: GoCodes Asset Tracking
That way, you get insight into all the data related to inspections, such as who conducted them, what was done, when it was done, as well as any other relevant information, which can be accessed anytime and anywhere.
However, these automated systems offer even more benefits.
Managing Equipment Inspections With Software
Miscommunication can be a big issue when planning and implementing equipment inspections.
Who was supposed to do that oil change? Why isn’t it done yet?
So many questions and no answer in sight.
The worst part? Questions like these do nothing but slow you down, leaving your machinery in poor condition.
At GoCodes Asset Tracking, we had precisely those situations in mind when we developed the Tasks feature as a part of our equipment management system.
That means that not only will the GoCodes Asset Tracking software tell you where your assets are and keep all the maintenance data in the cloud, but it’ll also enable you to set up various tasks as well as select specific workers to perform them.
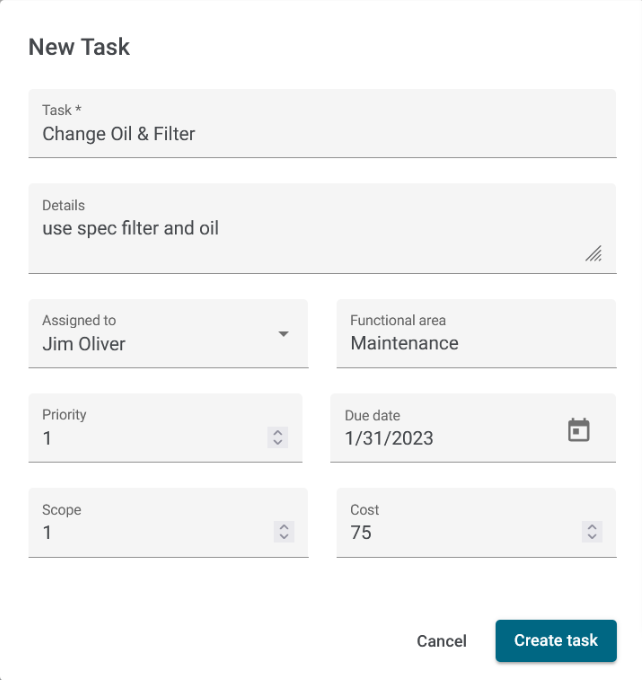
Source: GoCodes Asset Tracking
Besides, the technology allows you to establish the due date, priority level, and cost for each assignment.
Later on, you can update the task, mark it as finished, assign it to a different person, edit, copy, and delete it, while the My Tasks and All Tasks Tab Views make it easier to stay on top of everyone’s responsibilities.
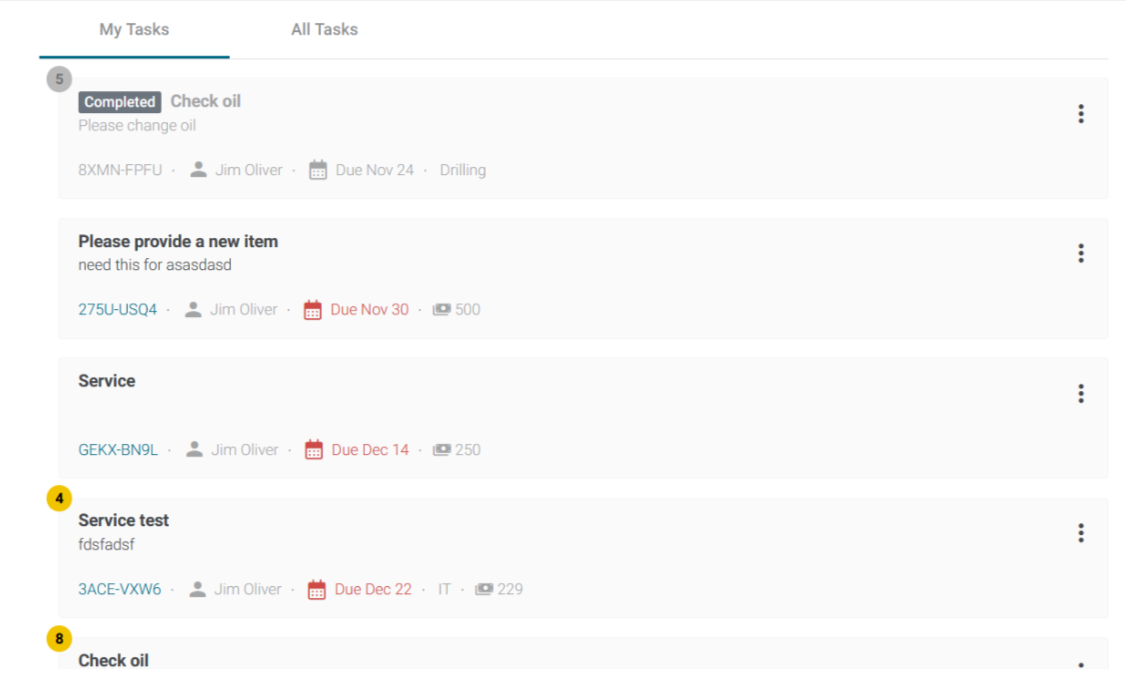
Source: GoCodes Asset Tracking
The two views provide a list of all the tasks, both completed and pending, as well as their due dates. Simple yet efficient.
What’s more, GoCodes Asset Tracking’ solution reminds you when a particular machine is scheduled for service.

Source: GoCodes Asset Tracking
You’ll receive an email notification either the day before or on the morning of the inspection, depending on the setting, making the possibility of missing it almost zero to none.
All in all, in today’s day and age, it is counterproductive to rely on manual methods for maintenance management. They are susceptible to errors, time-consuming, and labor-intensive, which can create more problems than it solves.
So why not give new technology a chance? It might surprise you how effective it can be.
Conclusion
Ultimately, it’s clear that investing time to do machine inspections the right way is a smart move for any business.
By making sure you adhere to official rules and regulations, creating checklists, documenting all the equipment checkups, and relying on centralized systems for easier management, you can significantly minimize risks and maximize equipment performance.
Prioritizing safety and striving for continuous improvement will not only benefit your assets but also your workers.
So, take the necessary steps to establish a strong inspection and maintenance routine and reap the rewards in the form of safe job sites and well-maintained equipment operating at peak efficiency.