With so many resources and activities involved in construction projects, it’s not surprising that some equipment just ends up sitting idle.
However, if left unchecked, idle equipment can adversely impact your project timelines and costs.
That’s why this article will answer six common questions about equipment idle time, helping you understand its types, causes, and reduction strategies.
So, let’s dive in.
In this article...
Key Takeaways
- There are several types of equipment prone to idleness.
- Idle time can be caused by both external and internal factors.
- Addressing the root causes of idle time is crucial for minimizing its impact.
- Trackers and sensors help in accurately measuring idle time and minimizing it.
What Types of Idle Equipment Are There?
For starters, any construction equipment (including rentals) that’s functional and available but not used for any reason is idle.
That’s why this idle time is sometimes referred to as equipment waiting or standby time.
However, equipment idle time shouldn’t be confused with equipment downtime.
Idle equipment | Equipment downtime |
---|---|
Functional but not used. | Not functional, therefore not used. |
Downtime refers to instances when equipment is undergoing maintenance or repairs.
With this important distinction made, it’s clear that all types of construction vehicles and machinery can be idle.
However, some categories of equipment are typically exposed to more extensive idle periods.
Let’s first list them, and then we’ll elaborate on each one.
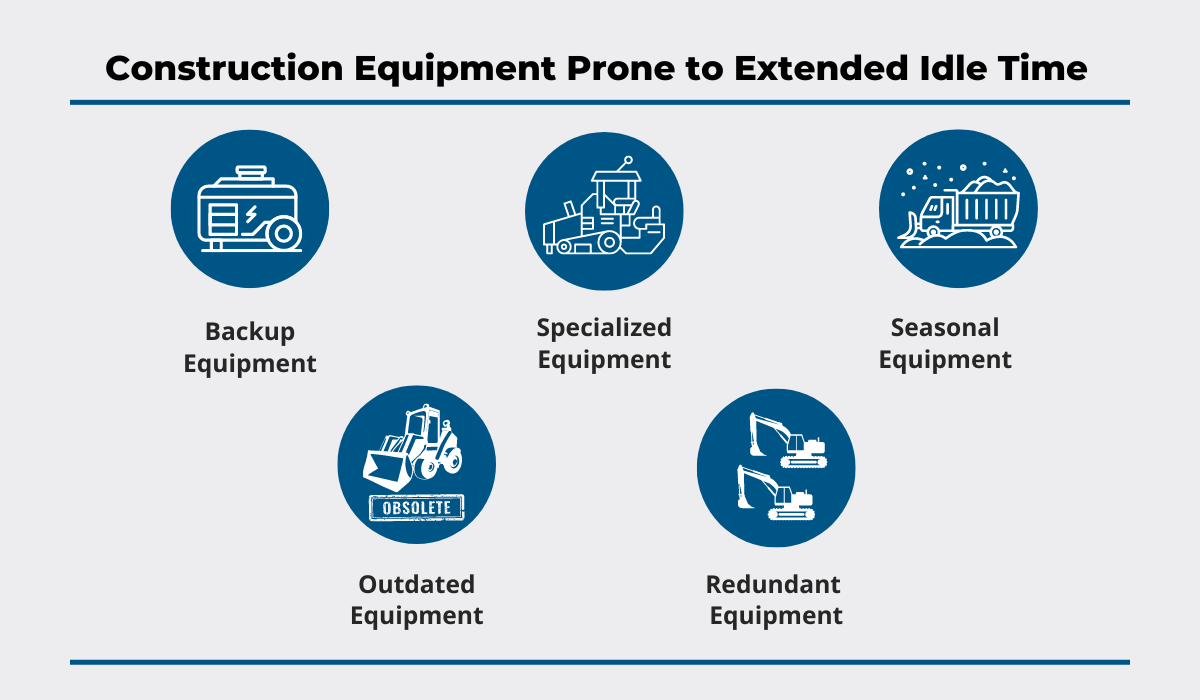
Let’s start with backup equipment.
This equipment is kept on standby to ensure construction operations can continue as planned in case primary equipment fails.
This means that such equipment is intended to remain idle for extended periods.
Power generators are a typical example of backup equipment.
Another category is specialized equipment, or machinery used for specific tasks during a specific construction phase.
Examples include asphalt pavers, concrete mixers, and trenchers, as illustrated below.
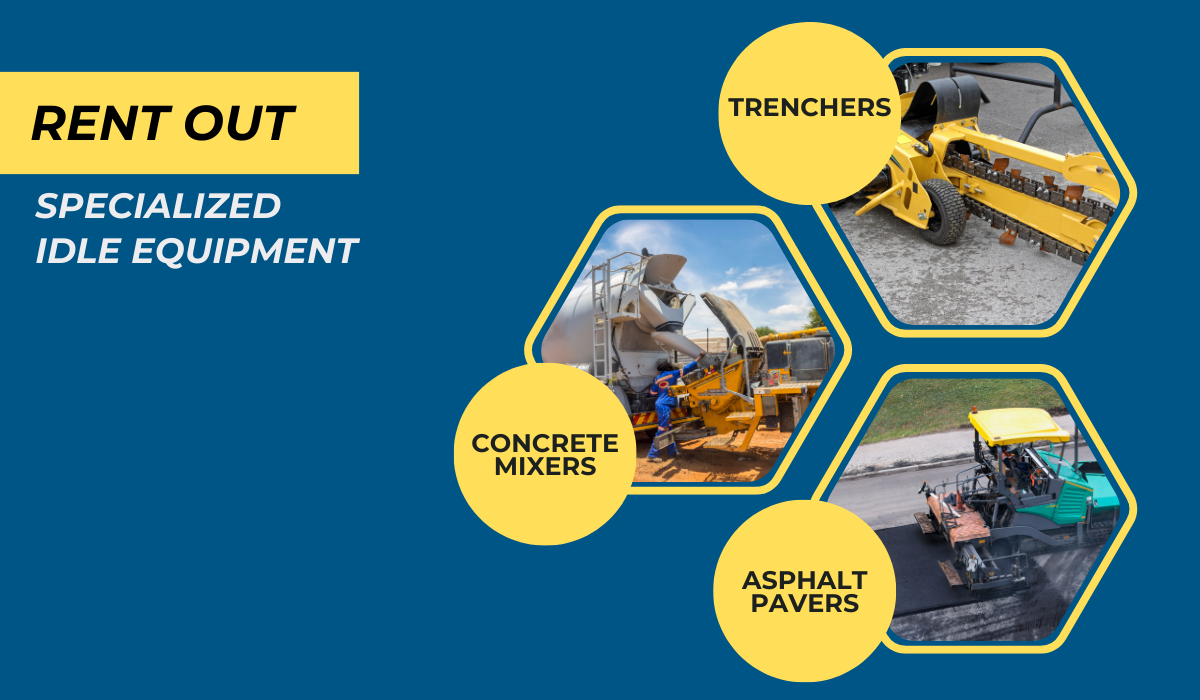
Next is seasonal equipment, which is typically used only during specific seasons or weather conditions.
Think snow plows and snow blowers for winter seasons.
As for outdated or obsolete equipment, this generally refers to older equipment models that largely sit unused because:
- they have been replaced by newer models,
- their declining performance no longer meets operational requirements,
- technological advancements have resulted in the loss of their purpose.
If not sold or disposed of, these machines can take up valuable space and resources.
Finally, redundant or duplicate equipment involves having multiple pieces of the same type of equipment.
Although this is common and often necessary in large construction companies, it can lead to redundancy, especially in periods of low demand.
Overall, having a clear understanding of what equipment idle time is and what categories of equipment are prone to extended idle time will allow you to develop appropriate strategies to manage them.
Now, let’s examine the potential causes of idle time.
What Causes Equipment Idle Time?
Equipment idle time can be caused by a wide variety of factors.
These can be roughly grouped into two categories: internal and external.
External causes of idle time include factors beyond our control that lead to equipment not doing productive work.
Here are just some of the main culprits:
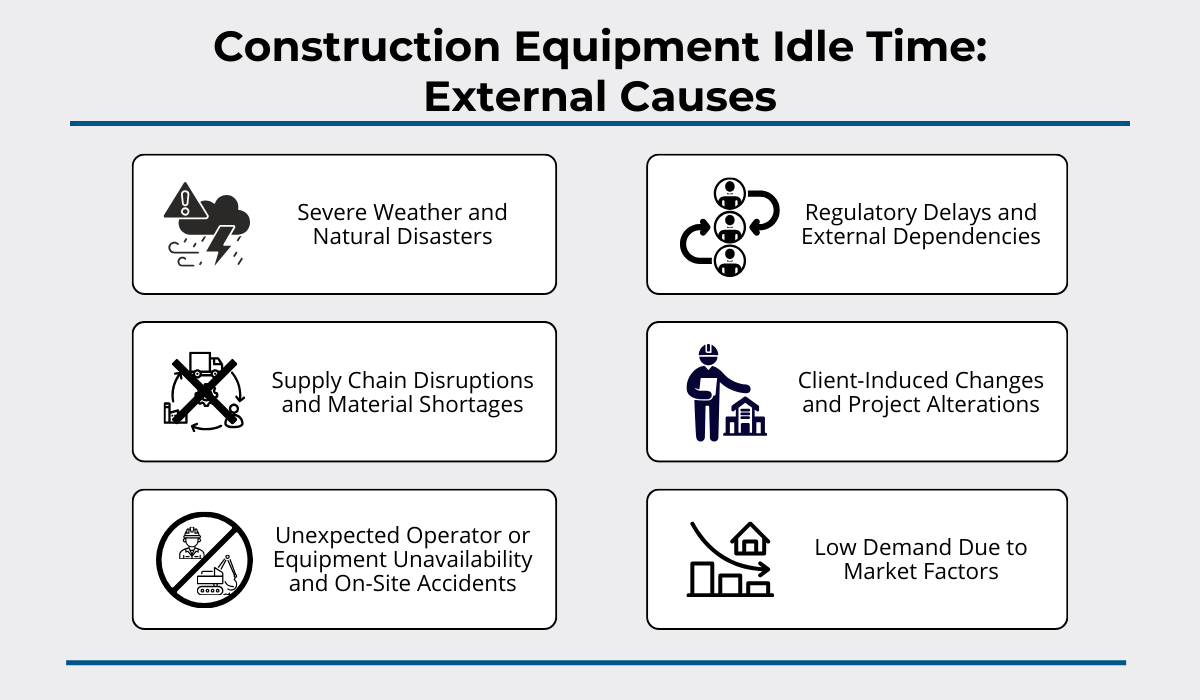
Although most of these external factors are self-explanatory, let’s go over a few examples.
It’s evident that weather emergencies and natural disasters typically halt all operations. In such cases, if equipment and labor cannot be reallocated, both will experience extensive idle time.
This also applies to delays in receiving essential materials due to shortages or delivery disruptions.
Next, unexpected operator absences, equipment breakdowns, and serious accidents can also result in idle equipment.
Delays caused by client-induced changes and regulatory approval processes can have the same effect.
Now, let’s move on to internal causes of equipment idle time.
We summarized them into four key groups:
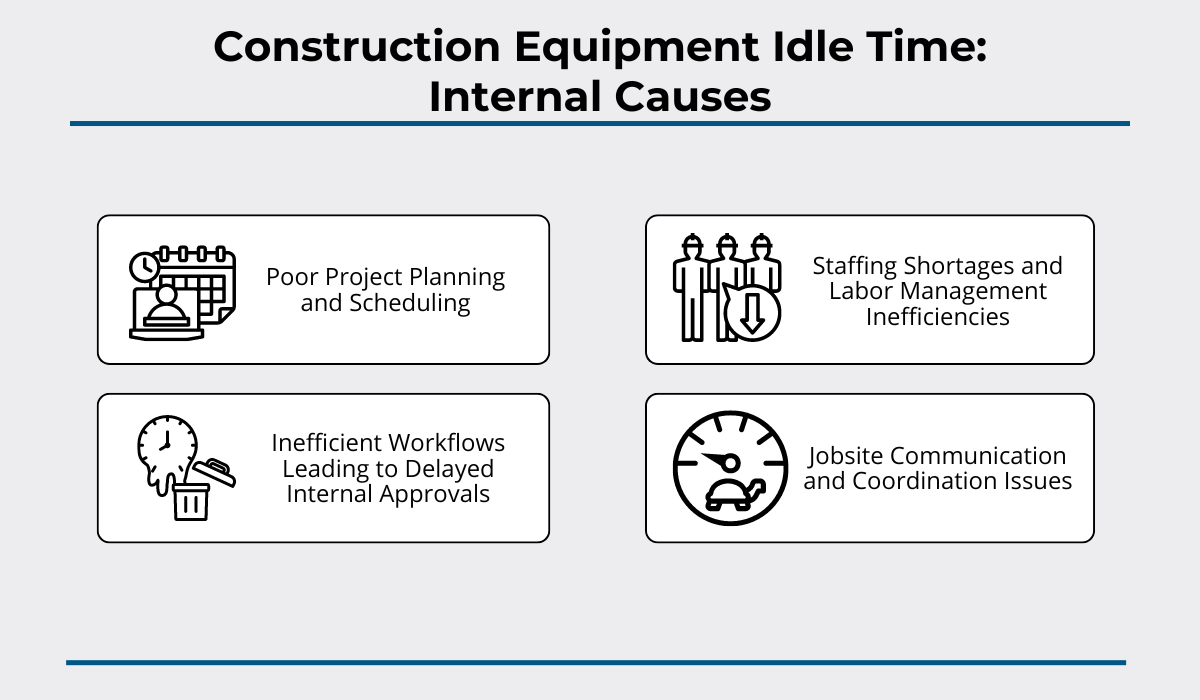
Collectively, these factors boil down to organizational and operational issues that can lead to equipment sitting idle for shorter or longer periods.
Expectedly, the biggest culprit among them is poor project planning.
This is closely related to inadequate communication among on-site and off-site staff and poor coordination of jobsite activities, resulting in countless gaps in productive equipment usage.
Next, internal decision-making inefficiencies further exacerbate these issues.
If your staff is waiting on instructions, approvals, feedback, or other decisions, that creates delays and becomes a significant source of equipment idle time.
Lastly, not having enough skilled equipment operators or failing to train them properly can also lead to periods of equipment idleness and lower operational productivity.
Having covered potential external and internal causes of equipment idle time, let’s see how you can calculate it.
How Can I Calculate the Idle Time of My Equipment?
Calculating the idle time of your equipment is relatively simple if you have the data necessary to do so.
The easiest way to collect accurate data on equipment idle time is to use tracking and sensing technologies and software tools.
Beyond that, you need to understand the components that make the idle time calculation formula.
The first component is the total time your company expects each piece of equipment to be engaged in productive work.
More precisely, you need to determine how many hours a day/week/month your equipment should be actively performing construction tasks, which frequently coincide with operator shifts.
This is often referred to as:
- scheduled production time
- scheduled machine hours
- or available equipment hours
The second component is the actual amount of time equipment was productive during the scheduled production time, known as actual production time.
Synonyms for this include:
- actual productive time
- productive machine hours
- and run hours.
So, when you subtract the actual time from the scheduled time, this yields the equipment idle time, as shown in this formula:
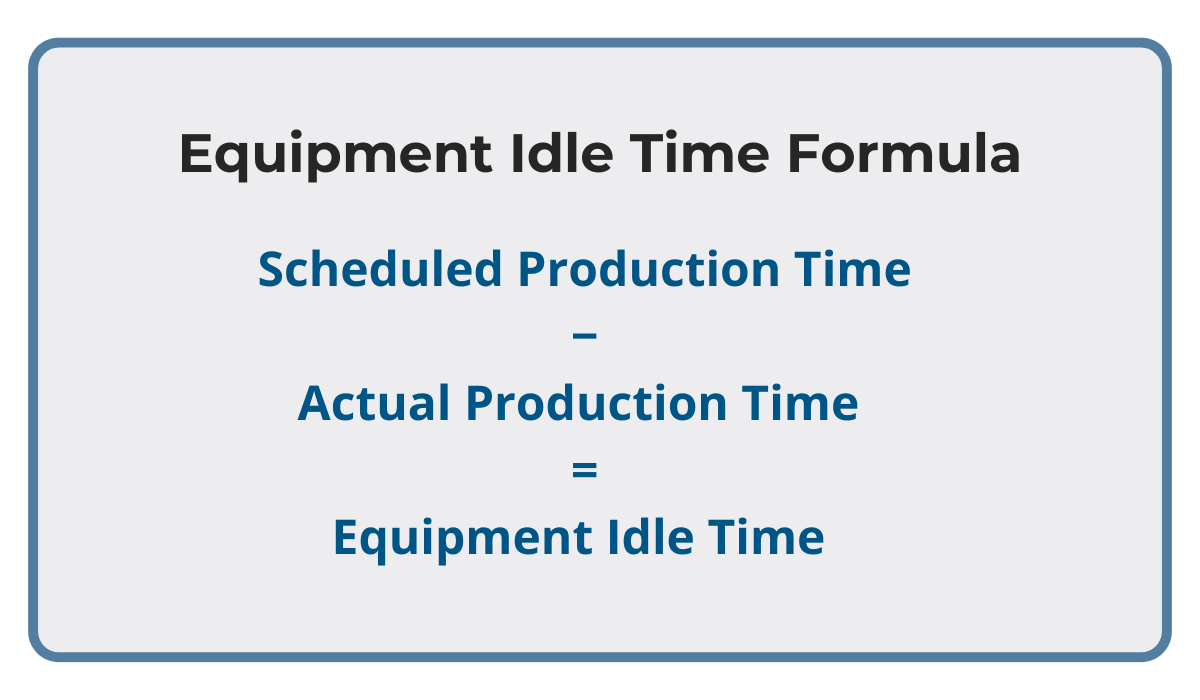
For example, if the scheduled production time for a bulldozer is 48 hours per week, but it was only productive for 35 hours, its idle time would be 48-35=13 hours.
These same formula components can also be used to obtain the equipment utilization rate by dividing the actual time by the scheduled time and multiplying that by 100.
For instance, the above bulldozer’s utilization rate involving the same numbers would be about 73% (35/48×100=72.92%).
Now that you know how to calculate equipment idle time, you also need to clearly distinguish between types of idle time.
Unpreventable idle time | Out of control causes, normal operational gaps like lunch breaks, etc. |
Preventable idle time | Internal operational factors we discussed. |
Downtime | Calculate separately from idle time. |
To calculate your equipment’s idle time, you need accurate data, which brings us to the next question.
Which Tools Can I Use to Monitor Equipment Idle Time?
For monitoring equipment idle time you can use GPS tracking systems, telematics, and fleet management software. All these tools can provide data on equipment usage and idle periods.
Perhaps your company already has some of these tools at its disposal.
For instance, if your construction fleet is equipped with GPS trackers for navigation and security purposes, such devices might already be monitoring the data relevant to idle time.
More precisely, such GPS trackers should either be connected to internal (onboard sensors) or external (tracker’s own sensors), i.e., telematics.
This enables GPS tracking software to collect the relevant equipment data from which idle time can be determined.
To illustrate, here’s an example of how this is enabled by our equipment-tracking app, GoCodes Asset Tracking.
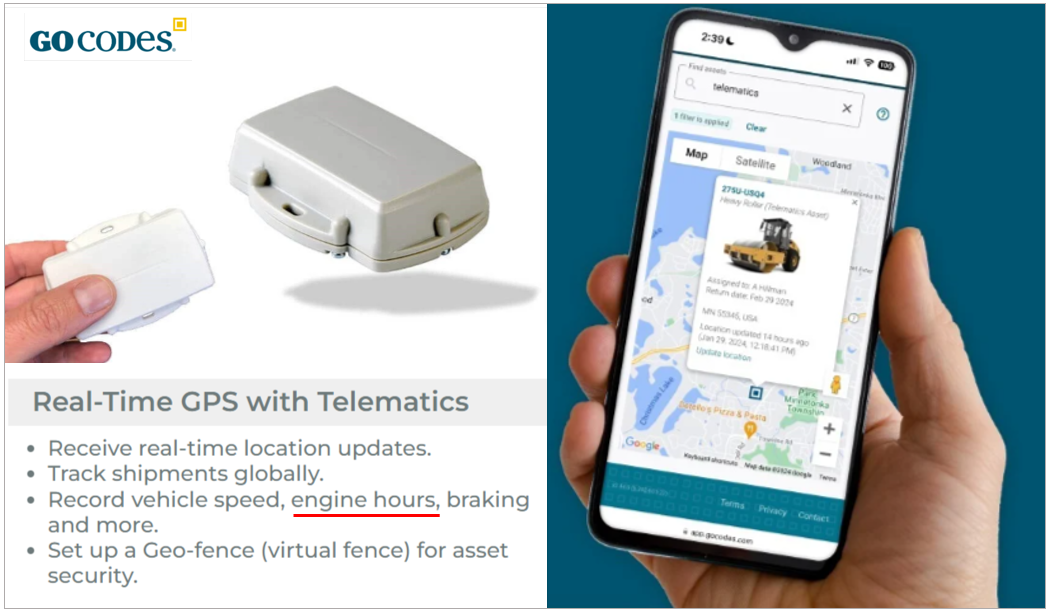
As shown, our real-time trackers allow you to track the location of your equipment, and record their movements and stops, speed, engine hours, and more.
Among other things, this allows you to monitor when the equipment’s or vehicle’s engine is running, when it’s idling, and when it’s shut down.
When you have this data, you can cross-reference it with the scheduled production time, construction daily logs, or progress reports.
Ultimately, this makes it much easier to calculate the actual productive time of your equipment and, therefore, idle time.
Again, you’ll need to discern between unpreventable and preventable instances of idle time.
For example, whether the machine’s engine was idling for operational purposes (unpreventable) or due to operator negligence (preventable).
How Does Idle Equipment Affect My Bottom Line?
Whether you own it or rent it, any time your equipment remains idle instead of being used productively, this ultimately costs you money.
Even if you paid it off, when it sits idle you’re still incurring other ownership costs.
Just consider the fact that:
- equipment loses value over time (depreciation),
- insurance premiums, taxes, and licenses still must be paid,
- even idle equipment requires storage space and periodic maintenance,
- time-based warranties will expire,
- rented equipment, when unused, causes direct financial losses.
Clearly, idle equipment has hidden costs that negatively affect your bottom line.
As shorter or longer idle periods accumulate over time, this leads to equipment underutilization, which can be equated with the idle time rate.
In fact, according to Construction Exec, the underutilization or idle time rate of equipment in the construction industry stands at around 30%.
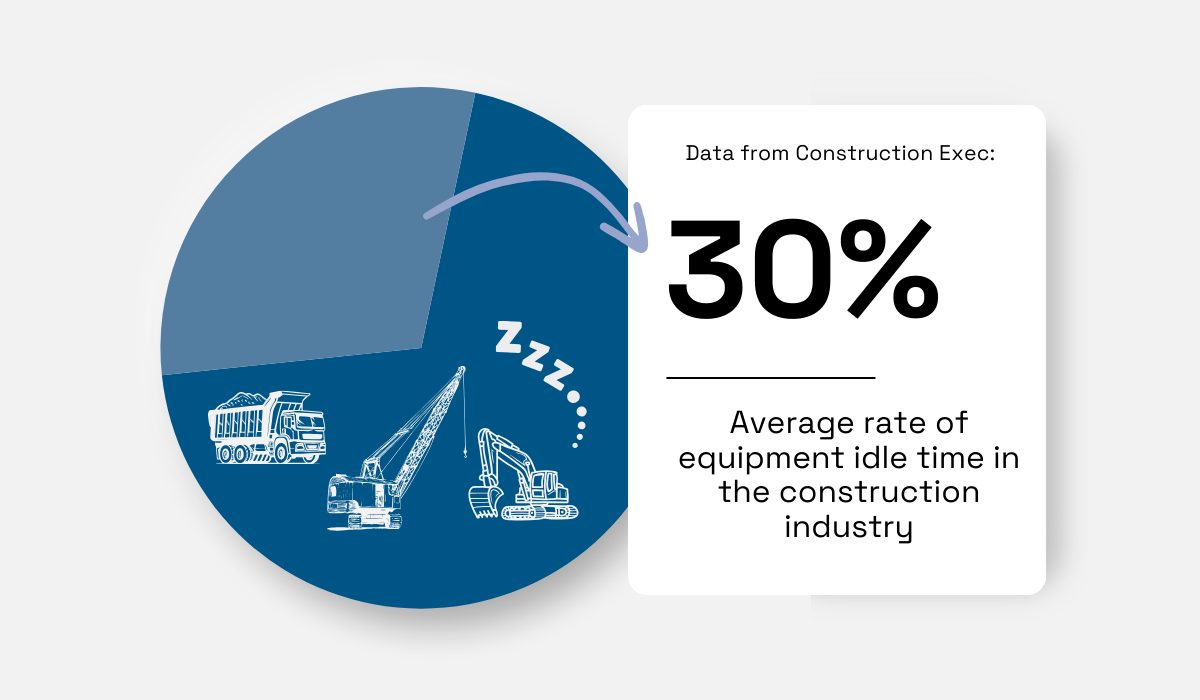
And what does this rate mean in terms of costs?
Let’s take a bulldozer as an example.
Average cost per hour | $35 |
Expected productive time per year | 1,200 hours |
Annual loss from 30% idle time | $10,800 |
For a rough estimate of the total effect of idle time on your profitability, multiply that amount by the number of equipment and vehicles in your fleet.
Another significant money sink refers to cases when machine engines are left running (idling) for no productive reason.
This wastes fuel (up to one gallon per hour of idling) and leads to increased machine wear and tear
Again, it’s important to distinguish between normal or unpreventable idling events (traffic lights, traffic jams, operational purposes) and those that can be prevented (lunch or coffee break).
Given all the above, it’s clear that your equipment’s idle time hurts your bottom line in more ways than one.
What Can I Do to Reduce Idle Time?
Yes, there are many ways to reduce equipment idle time.
Essentially, you have to address the internal and external causes of equipment idle time we explored.
However, the single most effective way to minimize your equipment’s idle time is to leverage technology.
More precisely, introduce construction efficiency-boosting software solutions to improve various aspects of your operations that, collectively, result in equipment idle time.
For instance, an all-in-one construction management platform can help you address many project planning, scheduling, and coordination issues that lead to idle equipment.

Such project management tools allow you to:
- establish robust yet flexible schedules and contingencies,
- manage schedule alterations due to change orders induced by the client or onsite conditions,
- communicate relevant information to all stakeholders in real-time.
Combined, these functionalities should help you avoid or at least minimize idle time caused by preventable construction management inefficiencies.
Similarly, we already mentioned how you can use sensor-enabled GPS tracking tools to monitor relevant equipment data and calculate idle time.
Ultimately, this allows you to integrate this data with other relevant project information and analyze it to reveal the main causes of idle time and take proper action.
Beyond that, such tools provide a range of other features that help tackle idle time challenges.
For instance, they act as the central database of all idle-time relevant information easily accessible to everyone, giving you a full view of your equipment utilization and status.
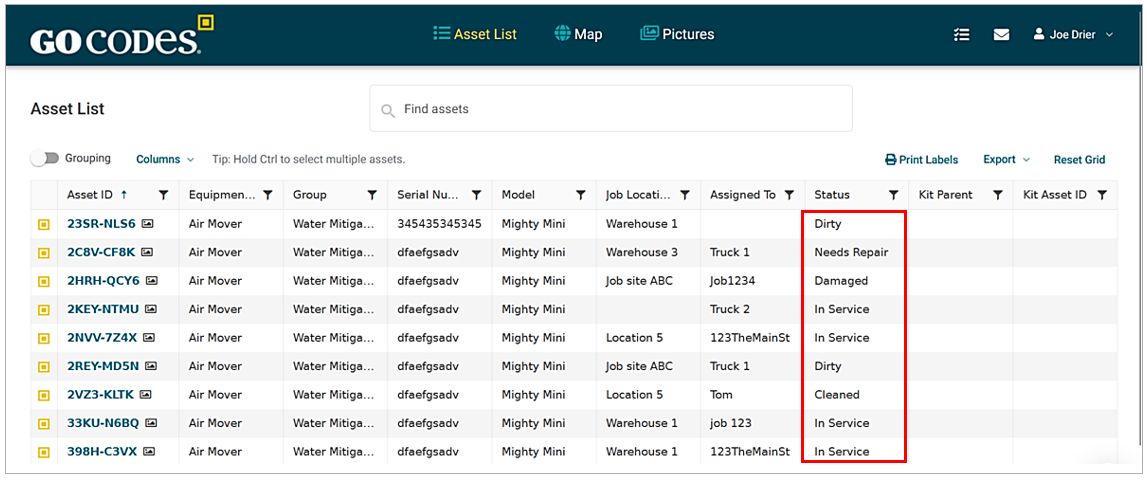
Such a database gives each piece of equipment, device, and tool its own info page.
This can be used to record and update key financial and operational information, such as equipment depreciation, maintenance and repair history, and utilization per project.
The said info helps you calculate your equipment’s life cycle costs and make informed repair-or-replace decisions.
Finally, asset-tracking apps allow your workers to quickly find the equipment and tools they need using their smartphones, thus minimizing both equipment and labor idle time.
Conclusion
Hopefully, this article has provided you with more clarity about equipment idle time intricacies, serving as a jump-off point for concrete actions.
Given that the initial cost of most construction equipment is high and ownership costs considerable, you don’t want it sitting idly when it could be earning your investment back.
So, take advantage of software tools at your disposal to track and calculate idle time, streamline processes to minimize it, and make data-driven idle time-reducing decisions.