Key Takeaways:
- Construction material management isn’t just about procuring the necessary materials.
- Developing strong relationships with suppliers is key to successful and timely material procurement.
- Tracking your construction materials can prevent inventory management issues and theft.
When done right, construction material management helps reduce costs and drive efficiency while minimizing waste.
Simply put, it ensures your crew has all the items and supplies they need throughout the project.
However, the process itself is anything but simple.
Poor planning and lack of inventory visibility can easily lead to overstocking or shortages, budget overruns, and costly delays.
But don’t worry, you’ve come to the right place.
By the end of this article, you’ll know which steps you need to take in order to successfully manage your construction materials.
So, let’s jump right in!
In this article...
1. Developing a List of Materials
First things first: you need to make a list of all the materials you’ll need for the project.
The main goal of construction material management is to ensure a consistent supply of essential materials.
Identifying all material requirements from the get-go means you’ll make acquisition more efficient and cost-effective.
Moreover, you won’t have to worry about procuring additional materials on short notice.
The materials you’ll need will depend on the project and the type of construction business you’re running, but common building materials include:
- Concrete
- Timber
- Masonry
- Stone
- Steel
- Aluminum
- Copper
- Ceramics
- Glass
- Plastic
- Fabrics
- Paper
Materials are then further divided into categories based on the activity type or task they relate to, such as structural, mechanical, or insulation.
Categorizing materials in this way makes it easier to clarify their purpose and use, cover all project aspects, and avoid confusion.
For example, simply listing “cables” without specifying either “electrical” or “mechanical” as activity type leaves room for wrong interpretations and costly errors.
Of course, your list of materials isn’t complete without accurate quantities for each item, which is the main goal behind construction material takeoff (MTO).
The MTO lists always include precise quantities and useful notes on material specifications, but the MTO template you can see below also includes weight.

The weight of each material impacts the logistics and costs of getting it to the job site, which makes it a particularly useful metric for complex projects.
Finally, keep in mind that completing the MTO process has to be a collaborative effort.
By involving construction and engineering teams at this stage, you’ll develop a comprehensive list of materials that fully aligns with project plans, blueprints, and design specifications.
Remember: Identifying the right materials ensures compliance and efficiency, and brings you one step closer to staying on schedule and within budget.
2. Determining the Required On-Site (ROS) Dates
Now that you know which materials you need for the project and in which quantities, let’s make sure you have them on-site at exactly the right moment.
Determining required on-site (ROS) dates means aligning material delivery with project phases and construction schedules to maximize productivity.
More importantly, ROS dates are a critical tool for preventing common inventory control issues like overstocking.
You don’t need all concrete blocks or steel rods clogging up the jobsite from day one, right?
The ROS for each commodity is based on two factors:
- supply chain lead times, and
- the duration of the procurement process.
For instance, Gordian’s 2024 report on construction costs outlines the current material pricing trends, noting a jump in cement prices due to shortages.
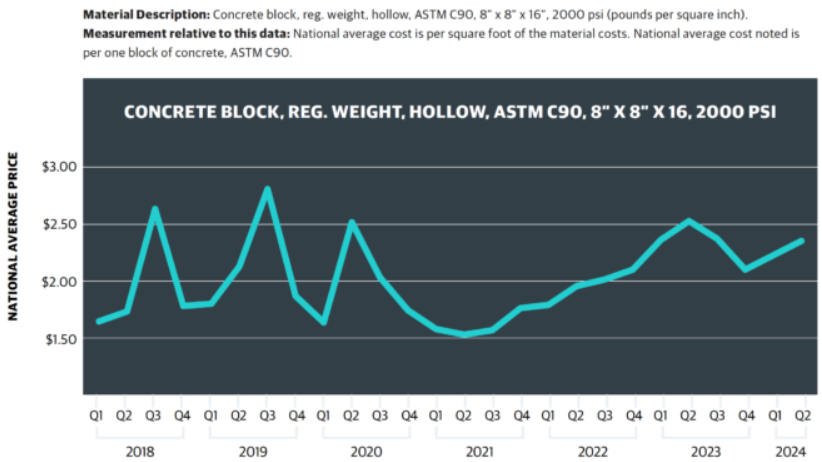
Monitoring such material shortage trends can help estimators and procurement specialists account for potential procurement and delivery delays and, therefore, accurately determine the right ROS dates.
However, it’s essential to have input from the project manager and the construction crew, too.

The project manager makes sure that the ROS dates align with project milestones and phases and integrates them into the project schedule.
Meanwhile, the site manager and crew are essential for on-site input and handling of the materials.
Coordination between all parties will ensure that ROS dates are accurately defined and that any changes or delays are communicated promptly.
3. Creating a Material Requisition Plan
Once you have the materials list and the ROS dates, you’ll be ready to develop the Material Requisition Plan (MRP).
The Material Requisition Plan is a strategic document based on key insights from the previous steps, which aims to ensure the timely availability of materials.
The Five Rights (Rs) framework illustrates these material management objectives perfectly.

However, the Material Requisition Plan goes beyond the framework, offering a very detailed outline of how these goals will be met.
It enhances inventory management and optimizes costs by defining and standardizing the process of requesting and allocating the necessary construction materials.
The MRP has six integral components:
Reviewing material needs | Check the specifications and quantities outlined in the Material Takeoff list (MTO), making sure it aligns with project phases, tasks, and activities. |
Creating requisition forms | Prepare standardized forms and templates for material requisition. They should include material descriptions, quantities, delivery dates, and project phases. |
Defining approval processes | Establish who needs to review and approve requests for materials (e.g. procurement department) to ensure efficiency and control costs. |
Planning the procurement process | Outline procurement procedures related to requesting quotes, selecting and managing suppliers, and sending POs. The procurement team’s input is essential here. |
Delivery and inventory management | Incorporate the ROS dates to plan deliveries in line with project needs and timelines, and define how materials will be tracked and managed on-site together with the site manager. |
Verification and reconciliation | Define the process of verifying deliveries, including how to address any differences between what was received and what was ordered. |
The Material Requisition Plan needs to be reviewed by key stakeholders, such as the project manager and site manager, the engineering team lead, and procurement and QA teams.
Once the plan is approved, it’s time to zoom in on materials sourcing and specific inventory management steps.
4. Sourcing the Materials
Materials sourcing plays a key role in project scheduling and budgeting.
When done right, it ensures timely delivery, cost efficiency, and quality compliance, thereby contributing to overall job success.
Staying on top of market trends, comparing quotes from different suppliers, and negotiating prices are all essential elements of successful sourcing.
But the most important thing is to find suppliers you can trust.
That way, you’ll be on track to getting the materials you need exactly when you need them throughout the whole project, all the while securing better deals.
Choosing the right suppliers requires a strict vetting process, so here are a couple of considerations to keep in mind:
- Overall experience and expertise
- Scope and complexity of past projects
- Capacity and infrastructure
- Compatibility with different aspects of your project
- Reputation and references (if available)
If you want to make informed choices, you also need to evaluate the supplier’s performance on past and ongoing projects.
For instance, too many partial or late deliveries are a clear sign you should build a strong supplier relationship elsewhere.
Unreliable suppliers are also far less likely to come through for you in cases when unexpected material shortages threaten costly delays.
This is why Lisa Sallstrom, the Executive VP of Products & Services at the Association for Supply Chain Management (ASCM), urges companies to build strong supplier networks.
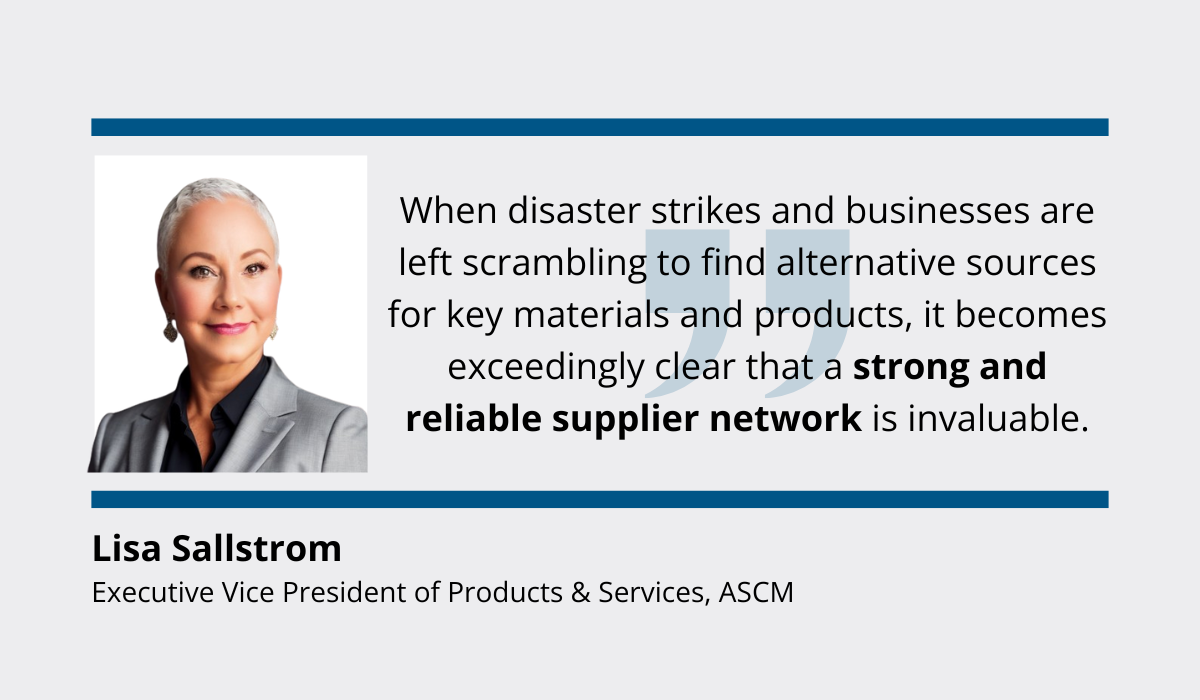
Strong relationships with suppliers translate to favorable terms and consistent material availability, even in the face of negative market conditions.
The bottom line is that paying enough attention to sourcing your materials enhances cost savings and ensures smooth project completion.
5. Planning for Material Storage
Although it’s sometimes reduced to procurement and delivery, effective construction material management requires you to plan for material storage, too.
The main reason why you should invest time and effort in your storage arrangements is to prevent avoidable damages.
By preserving the materials’ original quality, you’re avoiding the costs of having to replace them.
Adequate storing methods also ensure that the necessary materials are safely stored yet readily accessible, thereby boosting both worker safety and productivity.
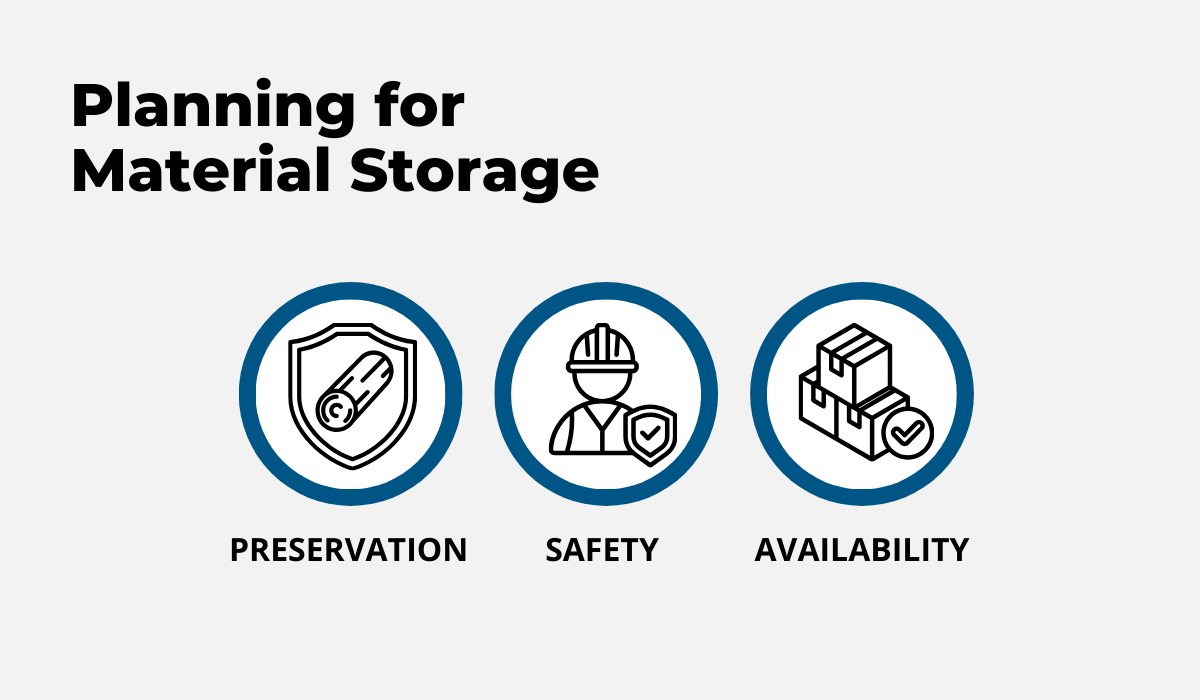
A 2022 study on the effects of poor material management in Nigeria showed that inadequate storage space and practices caused the deterioration of construction materials while also contributing to increased theft.
Both had a marked negative impact on the profitability of projects.
Deterioration is typically caused by inadequate storage conditions, which is why it’s essential to consider temperature and humidity, as well as ensure protection from the elements.
Naturally, the situation is different depending on whether you have a warehouse available or not.
A dedicated facility provides basic protection from the elements and makes it easier to control temperature and humidity in line with material type and specific preservation requirements.
Still, materials like cement should be stored on wooden pallets which are raised from the ground and removed from the walls to prevent moisture damage.
Architect Abdu-Wahab Nyanzi explains:
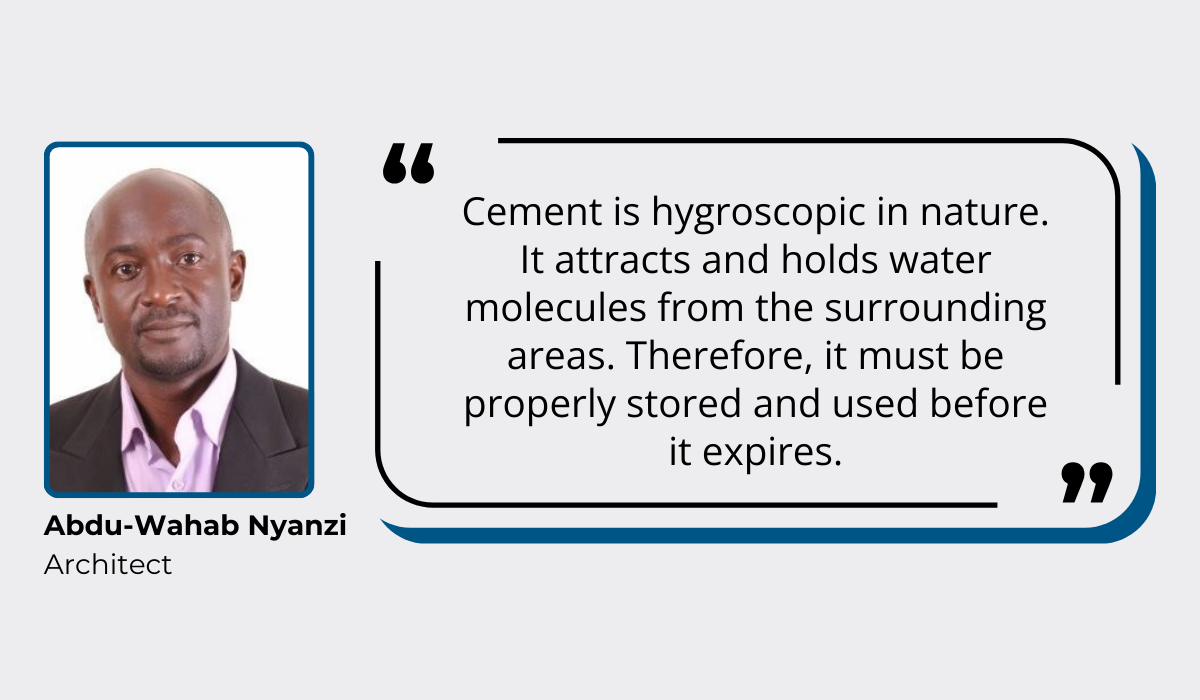
Aside from that, when you’re storing materials directly on the jobsite, it’s crucial to use tarps to shield them from rain and sunlight.
Materials should be placed on level ground, and not too close to active work zones to comply with safety regulations.
In both cases, easily accessible and properly stored materials can be handled safely, reducing the chances of any incidents and injuries.
6. Keeping Track of the Materials
Keeping track of construction materials is crucial for efficient material management because misplacing even one shipment can lead to duplicate orders and money drain.
Because let’s face it: if you can’t find something, chances are, it’s costing you more than you think.
On the other hand, continuous tracking and regular inventory checks enable you to keep your stock levels in check.
In their analysis of construction material management, Hendrickson, Haas, and Au list several examples of its positive impact on costs and savings.
One unnamed construction firm achieved an estimated 8% savings simply due to reduced delays and better material availability.
A surefire way of driving efficiency and cost optimization is to rely on asset tracking software with construction material management capabilities.
The benefits of using this kind of software include real-time updates, enhanced inventory management, and easy access to historical material data on the field.
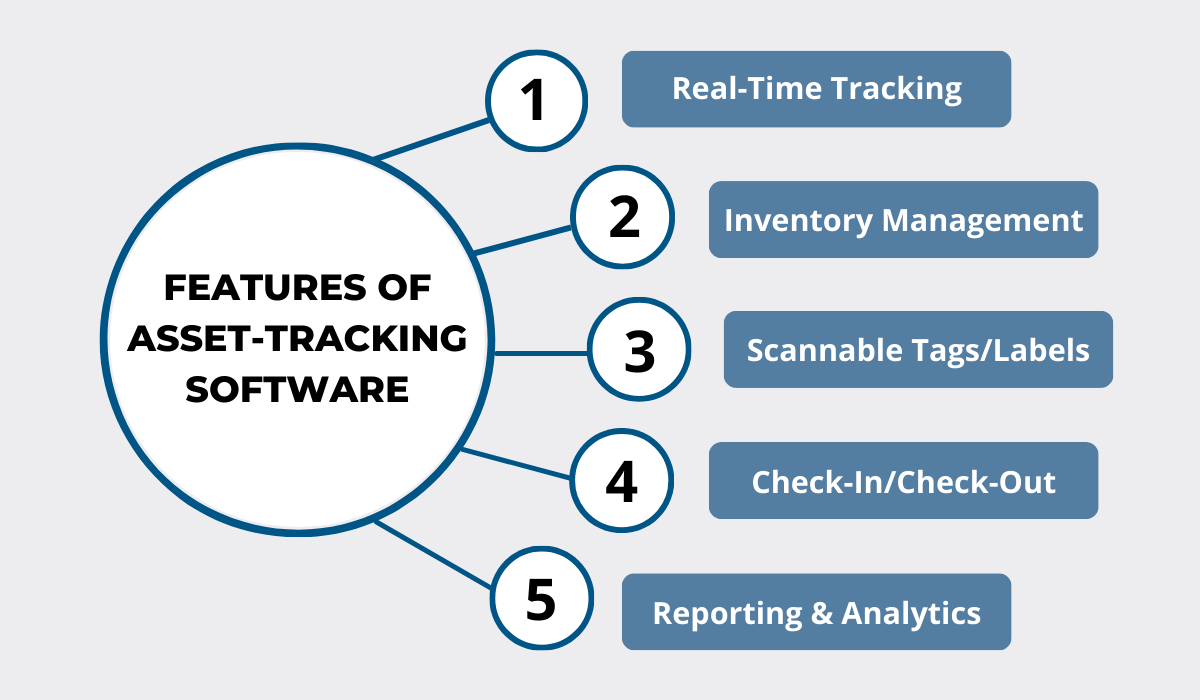
Our own asset tracking solution, GoCodes Asset Tracking, is the perfect example of how you can balance inventory levels while countering material theft.
GoCodes Asset Tracking consists of a cloud-based system, a mobile app with a scanner, and a range of powerful label options.
After you’ve put a rugged QR code label on the material unit, one scan gives you all the relevant information on quantity, location, and who handled it last.
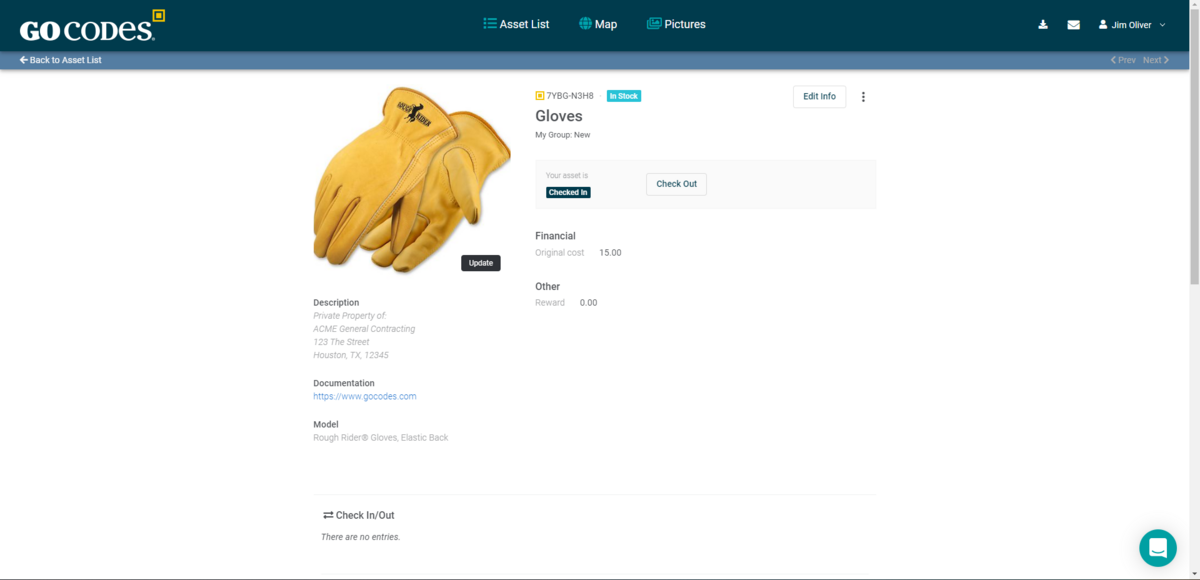
Checking materials in and out is a breeze, and you can also configure low inventory email alerts to ensure immediate response to low stock levels.
Finally, our real-time GPS trackers enable close monitoring of your materials while they’re on the move.
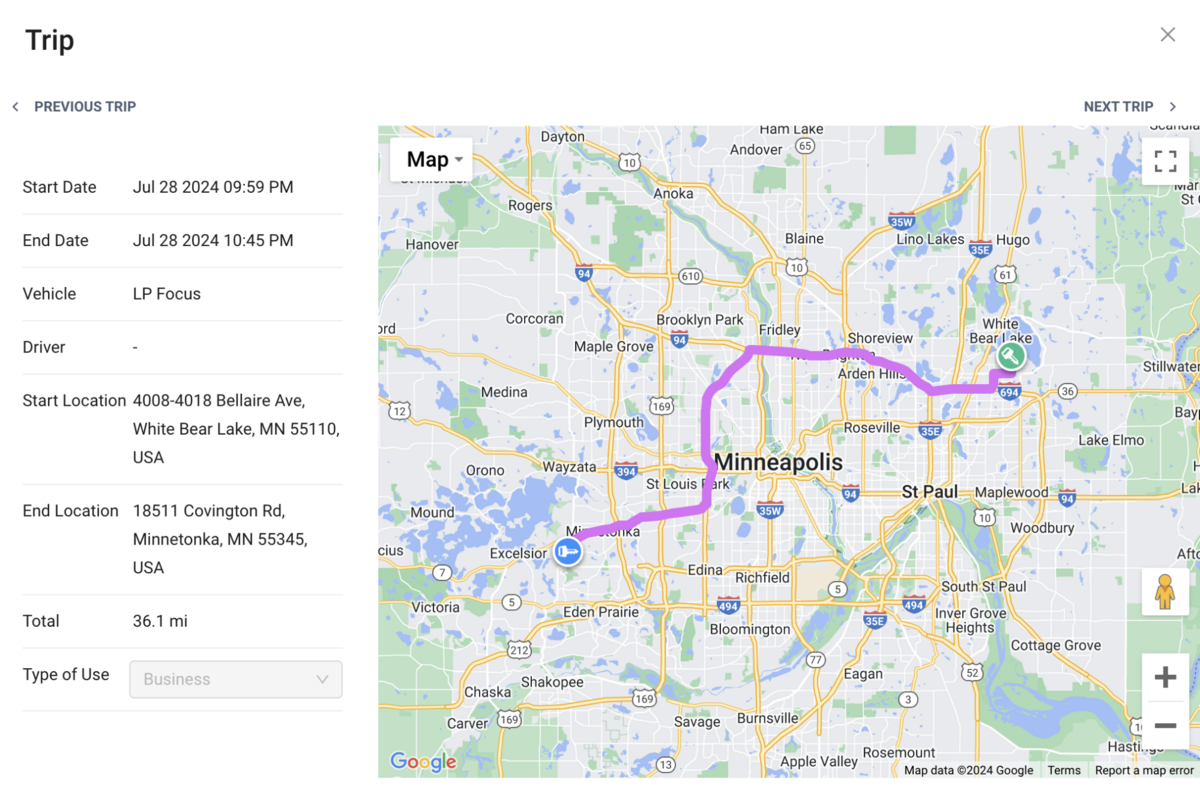
Real-time trackers give you the ability to check the location of every tagged unit and where it’s going, aiding both theft prevention efforts and shipment retrieval.
Perhaps even more importantly, tracking systems give you peace of mind, which is why technology is your best ally when it comes to keeping track of your construction materials.
7. Managing Material Waste Reduction
Ensuring that waste is minimized and disposed of systematically is the final step of construction material management.
Excess materials and other leftovers create clutter that’s costly in more ways than one.
It often means paying both the price of materials that go to waste and their disposal fees.
However, neglecting to handle material waste also carries indirect costs of decreased productivity and environmental pollution.
On the flip side, having an effective waste disposal and management strategy makes the site safe and efficient while also contributing to environmental sustainability.
Waste management practices can be summed up as:
- reducing
- reusing
- recycling, and
- disposing.
Ideally, you’re looking to reduce material waste from the get-go and along every step of the process, from choosing sustainable construction materials to eco-friendly packaging solutions.
But sorting on-site waste is already a huge step forward.
Sorting helps you establish whether it’s possible to recycle, reuse, or donate leftover materials, instead of opting for the least favored option of sending them to the landfill.
For example, Graham Construction installed recycling bins in both the field and offices, sorting not just paper or plastic waste, but also clothing and batteries.
Naturally, special care is given to separating and sealing off hazardous materials.
These efforts are part of a wider site waste management plan (SWMP) which helps them anticipate and measure waste production, maintain sustainability standards among contractors, and more.
Ultimately, diverting waste from landfills paves the way to better resource efficiency and a greener, more sustainable future.
Conclusion
There you have it—following these 7 key steps is bound to transform your construction material management!
While it may seem complex, it comes down to figuring out what materials you need through joint effort, and then carefully planning how to procure and manage those materials on-site.
Moreover, implementing the right practices and using technology will streamline these processes further.
And once you have total visibility and control over your materials and inventory, both your material management and business are sure to reach new heights!