Effective construction cost management involves planning, budgeting, and controlling costs, making it crucial for your company’s profitability.
This process—if managed properly—ensures your construction projects are completed within defined scopes and budgets without compromising your bottom line.
However, the significance of cost management extends beyond this.
Proper cost management builds a positive reputation.
When clients and stakeholders see that you accurately estimate costs and adhere to budgets, you can secure more projects and stand out in the competitive construction industry.
If any of this sparked your curiosity, keep reading as we guide you through the precise steps of managing your construction costs to stay within budget and secure a good reputation.
In this article...
Create a Cost Breakdown Structure
The first step in construction cost management is breaking down all costs of a construction project during all its phases.
Of course, it goes without saying that, up to this point, you already know the scope of your project and have also created a work breakdown structure (WBS) as a part of your construction plan.
Work breakdown structure breaks down the scope into smaller units consisting of tasks and subtasks.
With such WBS in hand, you are better equipped to create a cost breakdown structure.
In fact, a cost breakdown structure complements a work breakdown structure by providing a breakdown of the expenses associated with the execution of those tasks.
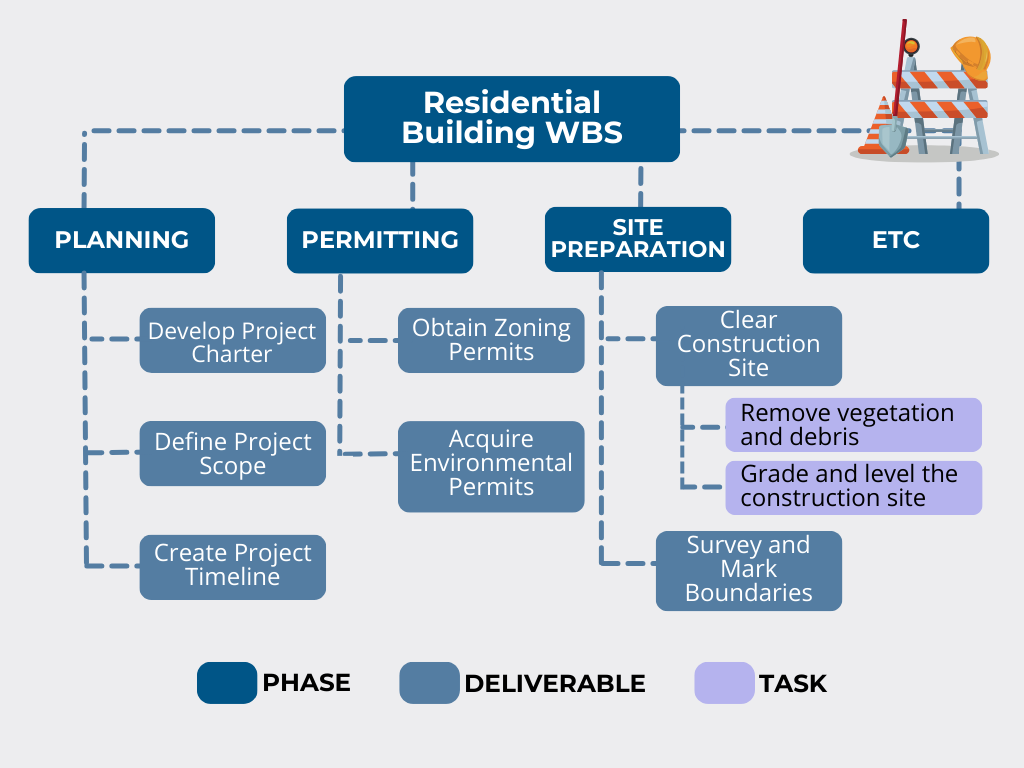
But why do you need a cost breakdown structure in the first place?
CBS will show you very vividly where you have to allocate resources.
It will show not only the total cost of the project but also how many resources you need for each task, project phase, or cost category.
This detailed overview of costs helps allocate resources more efficiently or reduce costs where necessary.
Such a granular cost view also aids in cost monitoring during the project execution.
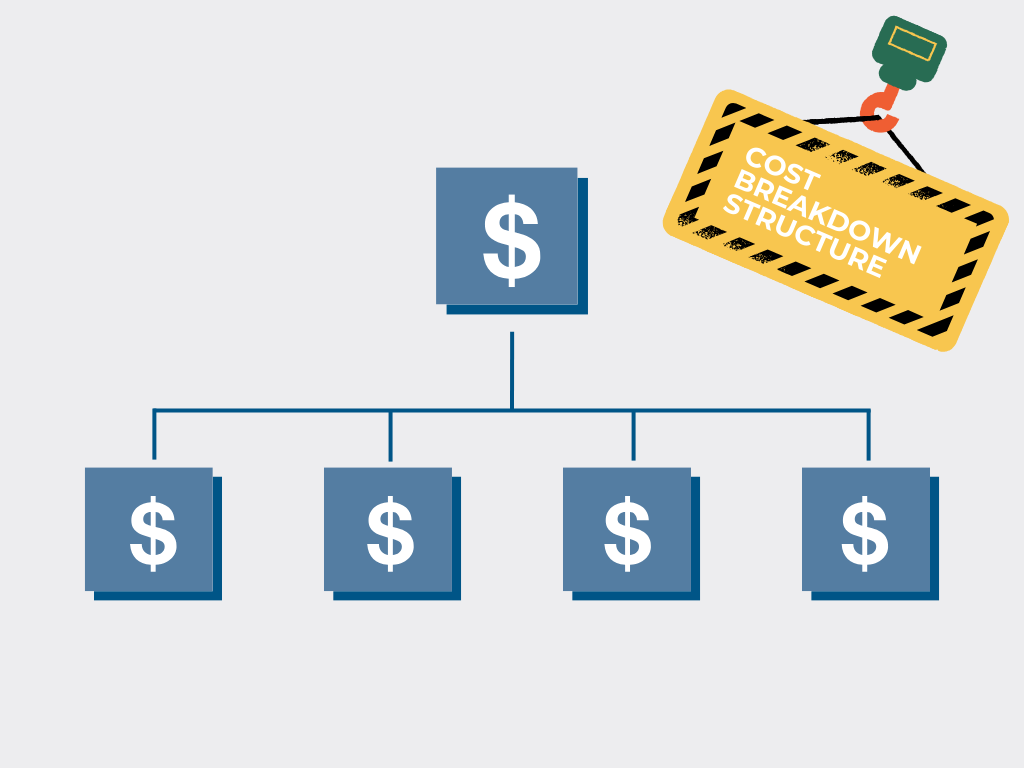
So, how do you create a cost breakdown structure?
As we said, you first need a detailed work breakdown structure that divides the entire project into more manageable units and task packages.
Then, you must consider the costs of each of those units and tasks. And you have to factor in material, labor, equipment, and all the other expenses.
For example, suppose you are constructing a residential building.
In that case, you will break costs according to the construction phases:
- land acquisition costs
- design and planning costs
- site preparation costs
- and so on, until the project’s final phase.
Then, it goes further into breaking each phase’s cost.
For instance, for site preparation costs, you must include the costs of clearing and grading the site, excavation and earthwork, utility connections (water, sewer, electricity), temporary fencing, and signage.
For each of these, you must include material costs, labor rates and hours, the cost of equipment rental, and all the other expenses.
For excavation and earthwork, costs would encompass:
- excavation equipment rental and fuel
- labor costs covering hours worked and wages
- disposal fees for removed soil
- any necessary permits or inspections.
When you factor in all these costs and cost categories, creating a cost breakdown structure is complex as there are many construction phases and tasks within each phase.
However, with such a detailed cost breakdown structure, you will control and manage costs more accurately throughout the construction project’s lifecycle, as we will see later.
Perform a Construction Cost Estimation
Once you have a detailed cost breakdown structure in your arsenal, it’s time to estimate the costs of each element on it.
Ultimately, this will help you predict the project’s total cost and set realistic budgets.
Therefore, it’s essential that you do it precisely and accurately.
For that, you will need the following information:
- Up-to-date information on the cost of construction materials, including market prices, and transportation costs.
- Costs of equipment rental, fuel, maintenance, and any other relevant equipment expenses.
- Current labor rates, including wages, benefits, and other associated costs.
- Indirect costs such as administrative expenses, insurance, utilities, and other overhead costs associated with the project.
- Costs for obtaining necessary permits and meeting legal requirements.
- Data on current market conditions, including inflation rates, economic factors, and regional variations that may impact material and labor costs.
Let’s now explore the different methods to estimate costs.
If you take your cost breakdown structure and estimate the cost of individual tasks or work packages and then aggregate them to determine the total project cost, you will perform bottom-up estimating.
This type of cost estimation will give you a detailed and accurate estimate but can be time-consuming.
However, there are several other methods of estimating out there:
Analogous Estimating | Historical data from similar projects is used to estimate the costs of the current project.It’s a quick and simple technique but requires projects with comparable characteristics for accuracy. |
Parametric Estimating | Cost estimates are derived from mathematical models using parameters or variables.For example, cost per square foot or cost per unit. It’s particularly useful when historical data is limited. |
Three-Point Estimating (PERT) | PERT (Program Evaluation and Review Technique) involves using three estimates for each task: optimistic, pessimistic, and most likely.The average of these estimates is then calculated to determine the overall cost. |
Top-Down Estimating | Top-down estimating involves estimating the overall project cost first and then allocating portions of the budget to individual tasks or work packages.It’s a quick but less detailed approach. |
As you can see, cost estimation is a complex endeavor.
That’s why expert cost estimators mostly do the job.
However, integrating technology, such as construction estimating software and BIM tools, can significantly enhance the accuracy and efficiency of the estimation process.
For example, these tools automate the process of material takeoffs, extracting the quantities directly from models, which reduces manual errors and saves time.
And accurate material takeoff—calculating and listing all materials required for a construction project—is highly necessary for the cost estimation to be as precise as possible.
Because only on such cost estimation can you build a realistic construction budget, which is the next step in construction cost management.
Build a Construction Budget
After you have estimated construction costs, you can finally set a construction project budget.
A construction budget is essentially the financial framework that outlines the total amount of money the client is willing to invest in the construction project.
This includes various components such as the cost of land, materials, equipment, labor, and overhead expenses.
Additionally, a well-structured budget incorporates contingencies to ensure that the project remains within budget and aligned with its goals.
Even in the face of unexpected costs or unforeseen challenges, as Hedi Ben Frej, senior project control manager at Emirates Global Aluminium, points out:
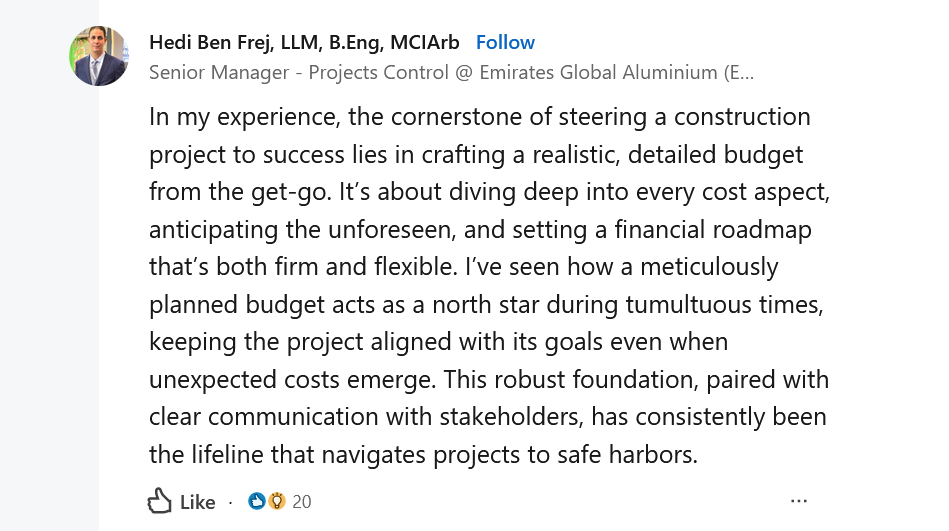
Including contingencies acts as a safety net, allowing for flexibility and adaptability throughout the construction execution.
A prudent contingency fund falls between 3% and 10% of the total budget, with the flexibility to reach 20% for larger projects.
It goes without saying that clear and transparent communication with the client is essential at this stage to ensure a mutual understanding of project goals and financial constraints.
Now—how should you go about setting a budget?
To build a construction budget that takes into account all the costs of the project as well as the contingency fund, do the following:
- Take the cost estimates and calculate the total cost of the project.
- Then, break down the total budget into smaller, more manageable segments, like labor costs by roles or teams, and materials required for different phases or tasks.
Also, you can take a time-phased approach to budgeting.
Suppose your project spans three years with a total estimated cost of $3 million.
However, with a time-phased approach, you focus on the initial two quarters.
After identifying specific tasks that will be done in this period, you allocate a budget of $40,000 for this timeframe.
This type of budgeting allows for a more detailed and dynamic allocation of financial resources over the course of the project, which enhances control and allows for more effective cash flow management.
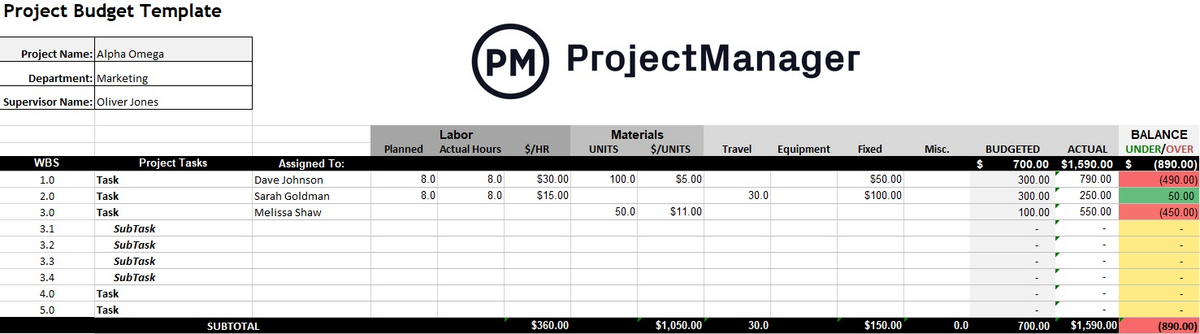
Overall, the point is to build as detailed a budget as possible, accounting for all costs and contingencies, as this will help you track and control costs throughout the project lifecycle and finish your projects on time.
Define a Cost Baseline
When your budget is approved, and you get the green light, it’s time to define a cost baseline.
In brief, cost baseline is the reference point for measuring and controlling project performance.
You need it to compare actual spending versus cost estimates to track whether you are staying within budget as the project progresses.

For example, if you establish a cost baseline, it means you’ve determined the expected costs for each phase or task in the project.
Let’s say the initial estimate for constructing the foundation is $50,000.
This becomes the baseline cost for this phase of the project.
As the project progresses, you compare the actual cost incurred for the foundation work against this baseline to assess if you are within the planned budget.
In other words, you assess project variance.
This metric is the difference between actual costs and those outlined in the baseline.
Several factors can contribute to cost variance, including:
- overly optimistic initial cost estimates
- modifications to the project scope leading to unaccounted costs
- fluctuations in material or labor prices, and
- unforeseen events like bad weather or regulatory changes.
In summary, the cost baseline is a vital tool to manage project costs effectively.
It enables you to measure cost performance, identify variances, and ensure alignment with the proposed budget throughout the project lifecycle.
But for that, you first need to track your construction costs, which is the next step in cost management.
Track Construction Costs Throughout the Project
After setting a cost baseline for each project stage, you can monitor construction costs as the project unfolds.
Continuous monitoring of expenses is crucial as teams collaboratively execute tasks, ensuring costs stay on track.
How do you track construction costs during project execution?
Remember the cost breakdown structure from the beginning? Well, it comes in handy again.
By breaking down costs into specific categories or work packages, a cost breakdown structure enables granular cost tracking.
This means you can monitor expenses at a detailed level, helping to identify areas where actual costs deviate from the baseline.
Moreover, it would be wise to use project management software with a centralized platform to input and update cost-related data, including budget allocations, expenditures, and resource utilization.
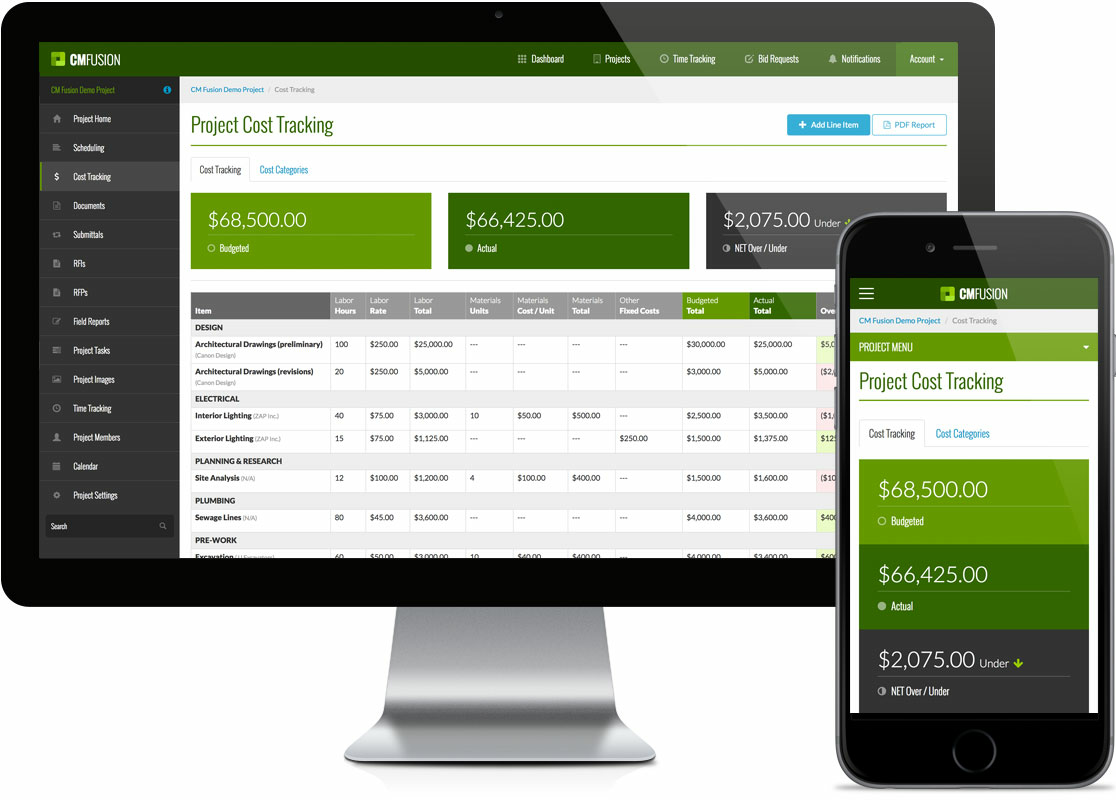
Such software often includes robust reporting functionalities, allowing you to generate financial reports, analyze spending trends, and pinpoint areas where costs may deviate from the established budget.
Many other tools you probably already use in your company will also help you track costs.
One such tool is equipment tracking software, which you use to prevent loss or theft, among other reasons.
And if you do leverage such software already—that’s great, as it can also help you track some project costs.
For example, our GoCodes Asset Tracking calculates asset depreciation based on your asset data.
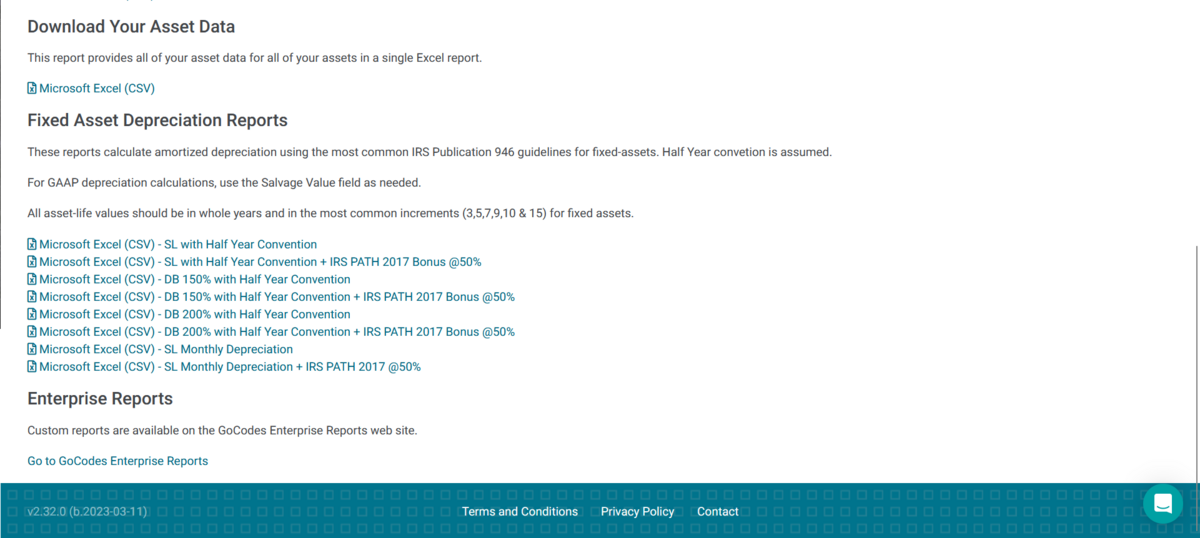
This matters because depreciation data helps evenly spread the cost of assets over their useful life, providing a realistic view of ongoing expenses.
Also, depreciation figures aid in planning for the eventual replacement of assets, preventing unexpected costs.
The key takeaway is that you must keep track of costs during project execution.
When you do so, you will notice in time if there are any deviations from the budget.
This will ultimately empower you to take timely measures, which is the last step of cost management—cost control.
Control Construction Costs
Controlling construction costs encompasses two activities: monitoring costs and taking timely measures to get costs back on track if there are any budget overruns.
At Construction Kaiser Limited, they explain how they control construction costs.
“As part of cost control measures, we monitor to ensure there are no negative variances between the actual expenditure and the cost baseline. When variance occurs, we examine the root cause of such variance, the degree and impact. In addition, we take necessary steps to bring the project back to the planned budget.”
Failing at this last step of cost management can jeopardize your company’s financial health, potentially leading to minimal profits or even losses.
However, rather than discouraging you, we believe in offering a solution to enhance your cost-control practices.
We have dedicated an entire article to this topic, so feel free to take a look!
Now, how should you go about controlling your project costs? Here is our take on it:
1. Develop a detailed cost control plan during the project planning phase. Clearly define cost categories, allocate budgets, and establish monitoring mechanisms for each aspect of the project. |
2. Implement a systematic approach to monitor actual cost against the predetermined cost baseline, as this will help you detect cost variances. |
3. When variances occur, conduct a thorough root cause analysis. Understand why the costs deviate from the planned budget, considering factors such as market fluctuations or unforeseen challenges. |
4. Assess the degree and impact of the cost variances on the overall project. This will help you evaluate how severe the situation is and decide what to do next. |
5. Take timely actions to bring the project costs back on track. This may involve renegotiating contracts, optimizing resource allocation, or revising project timelines. |
To conclude, cost control is an essential last step of construction cost management.
By regularly monitoring and analyzing the project costs, you can take timely corrective measures and still ensure your project stays within budget and scope, which is the very essence of cost management.
Conclusion
As you can see, construction cost management is an intricate process requiring detailed planning at each stage.
It starts with creating a cost breakdown structure, encompassing direct costs like materials, labor, equipment, and indirect expenses linked to construction projects.
The following steps involve estimating costs to establish a realistic budget and a baseline, which enables a comparison between planned and actual project costs.
Then, as the project execution begins, tracking and controlling costs come to the forefront.
Effective cost control ensures you promptly identify and respond to budget overruns.
Approaching cost management through these six steps guarantees successful project completion within budgets and without compromising your company’s profits.