Key Takeaways
- Current asset-tracking technologies allow you to track asset locations, usage, operating conditions, and much more.
- The most optimal tracking system typically consists of basic tracking tags and more advanced tracking devices.
- Construction asset tracking can help prevent theft, streamline operations, and minimize costs.
You want to know more about construction asset tracking?
That’s a wise decision, since effective asset tracking is crucial for improving productivity, preventing theft, and reducing costs in construction companies.
That’s why, we’ll use this guide to cover all the important aspects of construction asset tracking.
Let’s dive in.
In this article...
What is Asset Tracking in Construction?
Asset tracking in construction refers to the process of monitoring the location, usage, and chain of custody for assets like vehicles, heavy equipment, fixed assets, power tools, and other items.
A combination of hardware and software enables construction companies to have a detailed overview of asset usage, location, and maintenance status.
The advantages of tracking construction assets are so powerful that the global asset-tracking market, valued at over $21 billion in 2023, is expected to triple in value by 2032.
Here are the main benefits for construction companies:
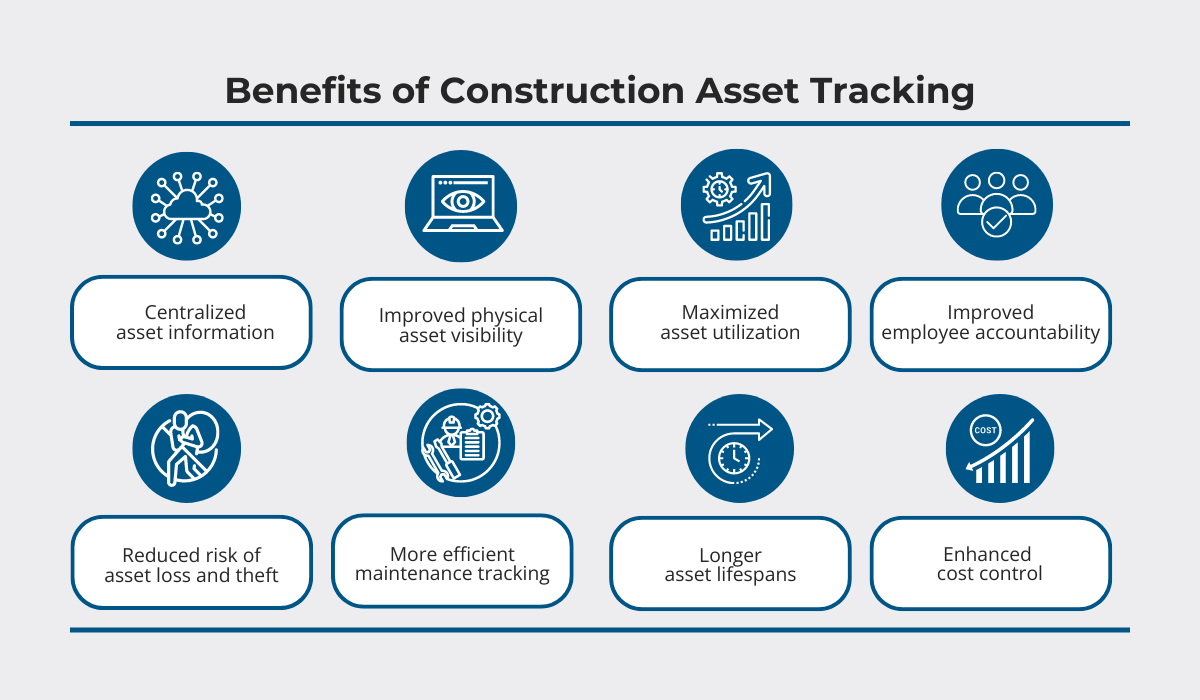
As illustrated, implementing asset-tracking brings numerous advantages that enable companies to significantly enhance their operational efficiency and cost-effectiveness.
For instance, centralized asset information allows managers and employees to quickly access asset data in one place, saving them ample time.
Likewise, improved visibility ensures that every asset is accounted for, leading to higher employee accountability and reduced risk of loss or theft.
Of course, you need to decide which assets should be tracked and how.
Which Assets Should Be Tracked?
While you can track all of your assets, from the smallest tools to the largest machinery, you don’t necessarily need to.
Sometimes, you’ll simply have too many assets to track so you need to prioritize.
Because not all construction assets are created equal.
More valuable assets will require more detailed tracking, while some less important assets might be better off with simpler tracking solutions.
For example, hand and power tools will typically need the simplest and most affordable trackers (barcodes, QR codes).
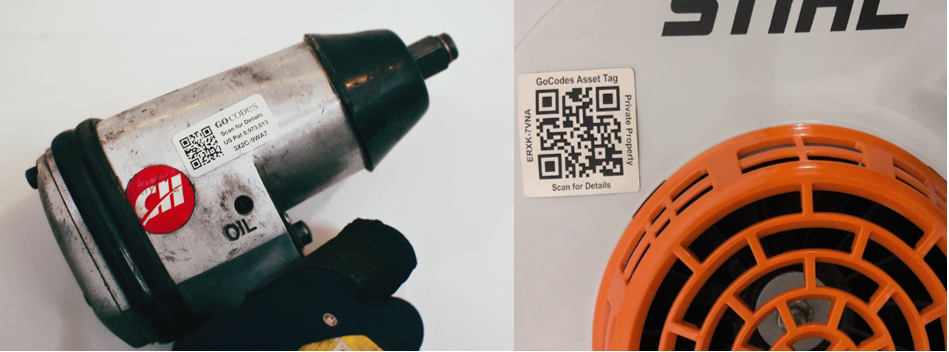
Conversely, other assets like vehicles and heavy machinery usually need more complex and expensive tracking devices (e.g., real-time GPS trackers & telematics).
Therefore, while all assets can and should be tracked, it’s crucial to prioritize them according to criteria like the asset’s:
- financial value and theft appeal,
- size and mobility,
- operational criticality,
- frequency of use.
This prioritization will clarify which assets need just basic tracking, and which require more advanced tracking methods for enhanced security and operational efficiency.
To illustrate which assets can be tracked, here’s an overview of the main types of construction assets along with some typical representatives of each category.
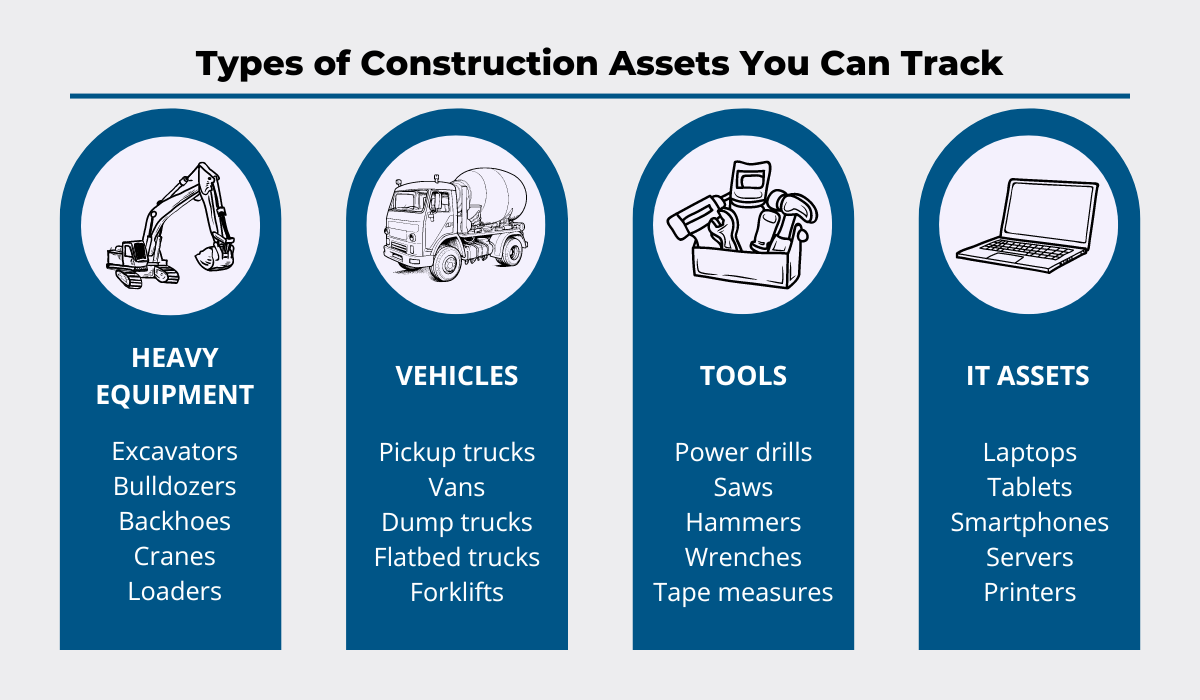
Of course, there are other categories of trackable assets.
For instance, you can track personal protective equipment (PPE), IT equipment, and fixed assets like furniture or containers.
Moreover, although they’re not strictly considered assets, we should add that consumables (spare parts, cables, etc.) and construction materials can also be tracked.
How Do You Keep Track of Construction Equipment?
To set up a tracking system for your construction assets, you’ll typically need two components: hardware (trackers or labels and a scanning device) and software.
Despite potential setup differences that depend on the selected tracking technology, the process is always the same.
Here are three simple steps to get your asset tracking up and running.
Identifying and Tagging Assets
First, count and identify all your assets, from the largest machinery to the smallest hand tools and other items.
Depending on how you kept inventory of construction assets until now, this may involve updating the spreadsheet listing your assets or doing a manual inventory audit.
With the refreshed list of assets in your hand, you’re ready to decide which asset you will start track.
Then, it’s time to tag them with labels for asset identification.
The easiest and most cost-effective method to tag all your assets is barcodes or their more advanced cousins, Quick Response (QR) codes.
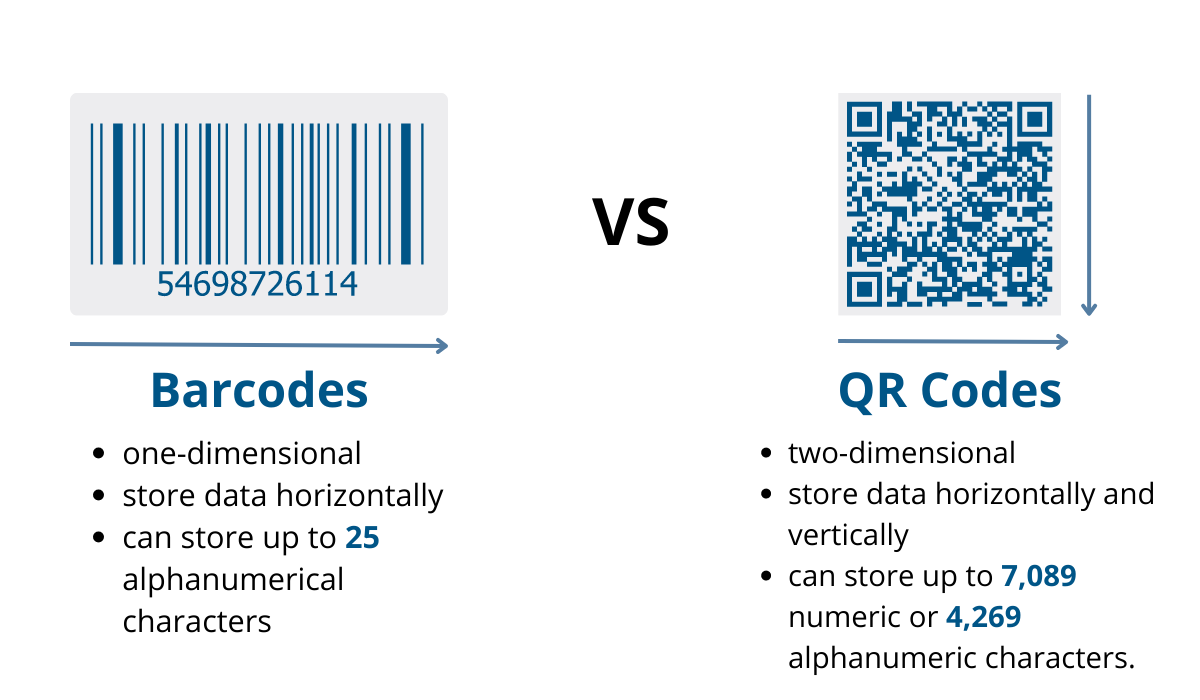
Although other tracking methods offer some additional benefits, nothing beats the simplicity and low price of ordering QR code tags (or printing them yourself) and attaching them to your assets.
That’s why barcodes or QR codes will typically be present even when other asset-tracking methods such as RFID or NFC tags, Bluetooth beacons, or GPS trackers are used.
Note that such QR tags should be affixed to assets in a place where they can be easily scanned by employees using their smartphone or tablet.
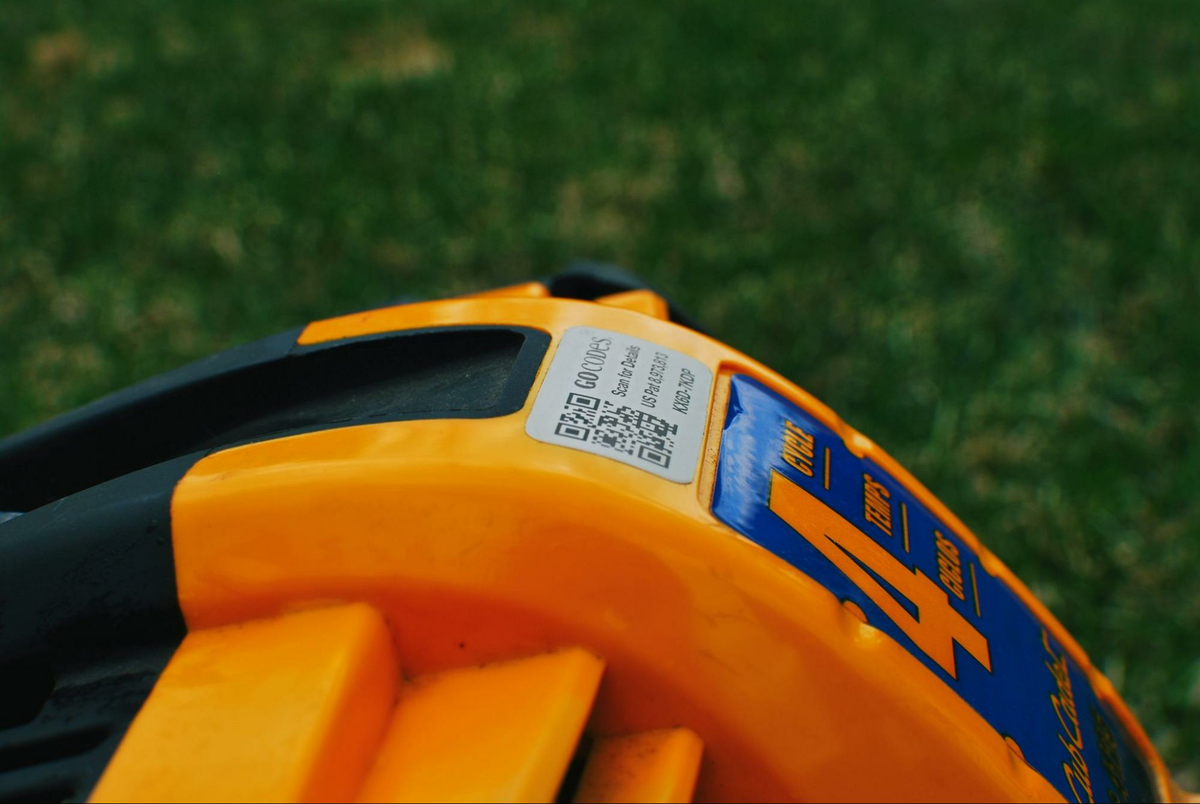
Next, your tracking software’s database should be populated with the initial data about each asset and linked to their respective QR code labels.
And that’s it, your primary asset-tracking system is ready to go.
Now anyone can log into the program to find asset info or scan the QR code to access it.
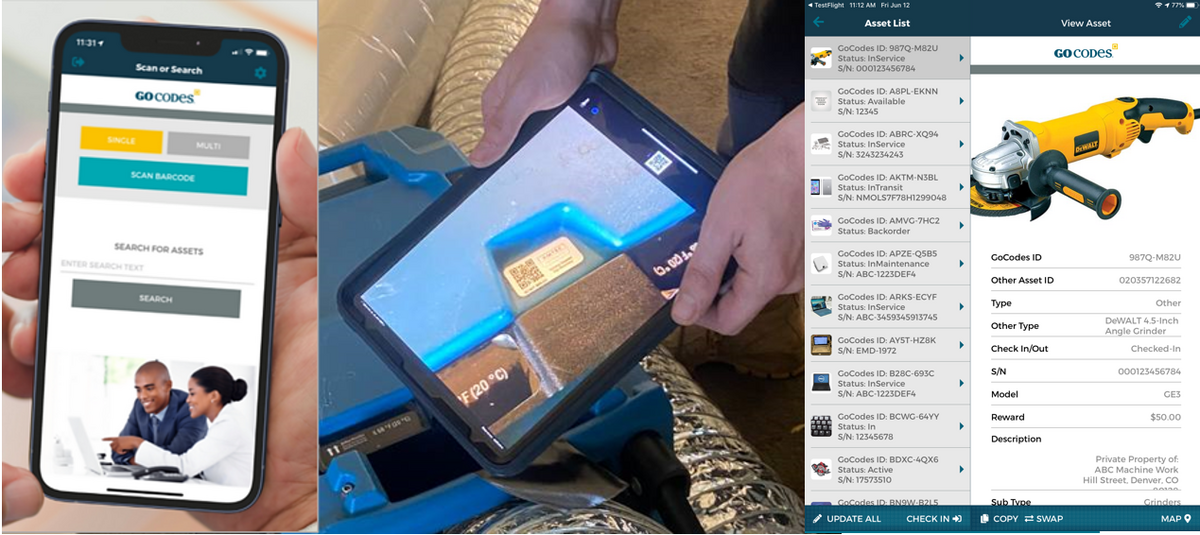
Should you decide to track your equipment with real-time telematics, you’ll have to either plug them to your vehicle’s onboard diagnostics or attach them to equipment.
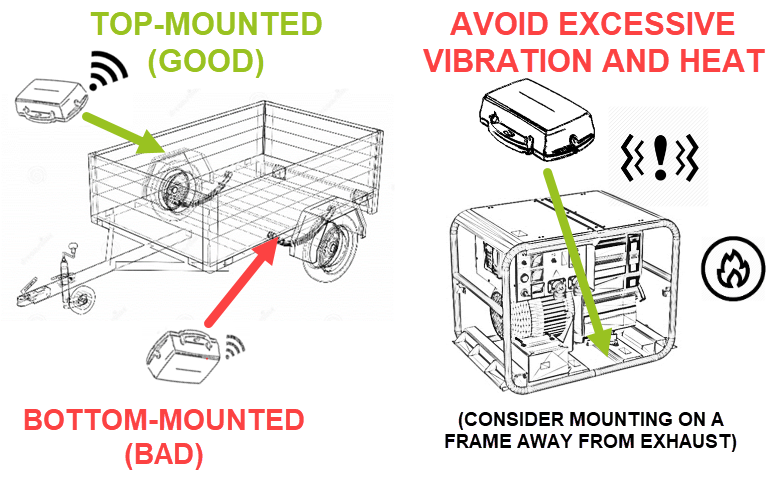
Such trackers will enable you to track the GPS position of your vehicles and heavy machinery in real-time anywhere in the world and capture additional data.
Other than GPS trackers, you can opt to track your assets with RFID or NFC tags that require no scanning or with Bluetooth beacons for remote tracking within a limited area.
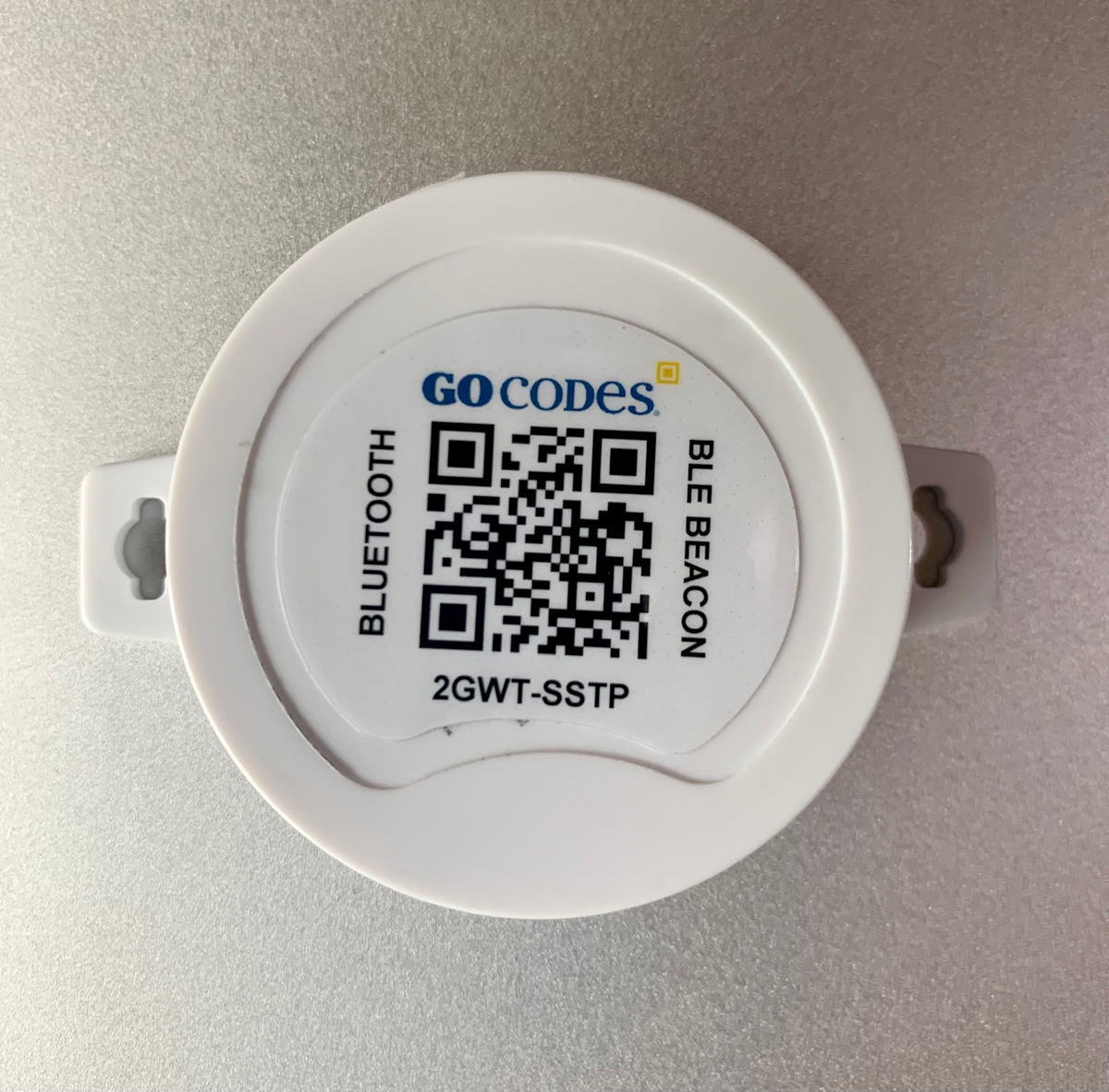
After you’ve attached trackers to your equipment, you can begin collecting data.
Capturing Data
Once your tracking system is set up, it will automatically capture some data points while allowing your staff to manually enter other relevant asset info.
In our example of a QR code-based tracking system, the program will typically automatically record who scanned an asset, when and where.
Scanning QR tags quickly and accurately records users, so you know which worker is responsible for taking an asset and returning it.
The asset’s GPS location is automatically captured every time an asset is scanned.
To achieve this, asset tracking systems leverage GPS-enabled QR codes that use the scanning device’s GPS locator to record the asset’s location and show it on a map.
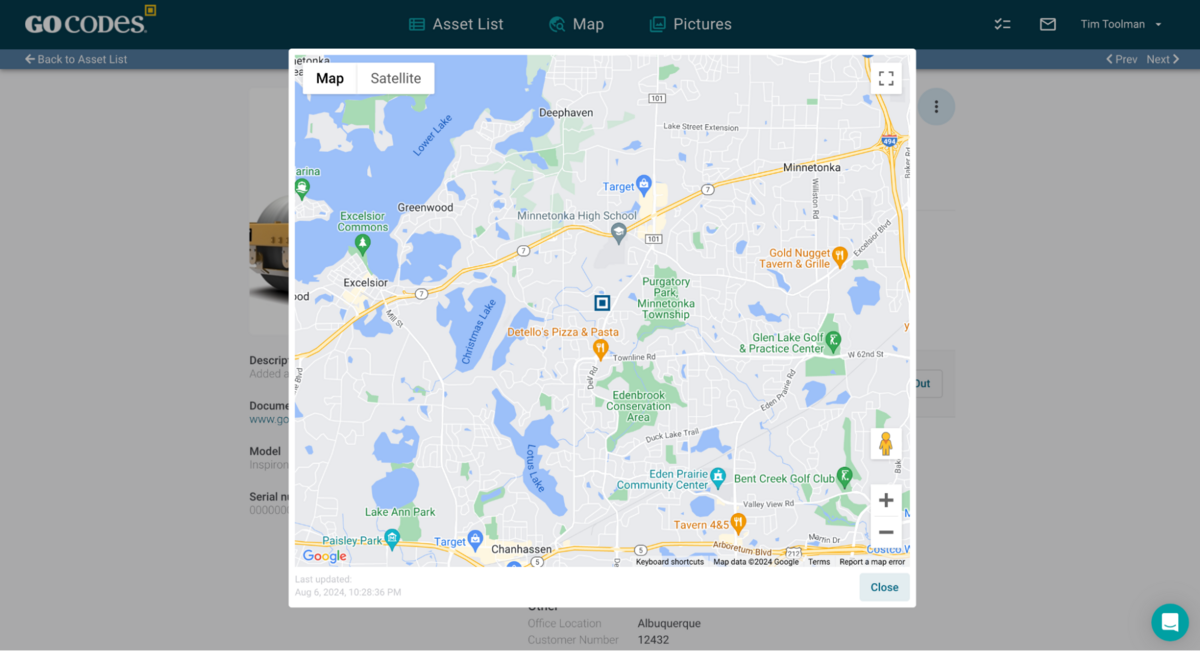
And if you are using real-time GPS trackers, besides getting GPS locations of your assets, you can also get data such as:
- engine hours,
- the vehicle speed,
- harsh acceleration and hard braking events.
Additionally, GPS trackers and Bluetooth beacons can be equipped with a variety of sensors that track other parameters, such as temperature, humidity, or vibrations.
Aside from automatically capturing location, users can update asset data, such as quantities and maintenance status.
All other relevant asset info can be recorded manually, i.e., by logging into the app and entering data.
Using Centralized Dashboards
All this data, along with the info entered by users, will be available in your tracking software’s centralized dashboard.
This dashboard can be accessed on any internet-connected device such as a smartphone, tablet, laptop, or desktop.
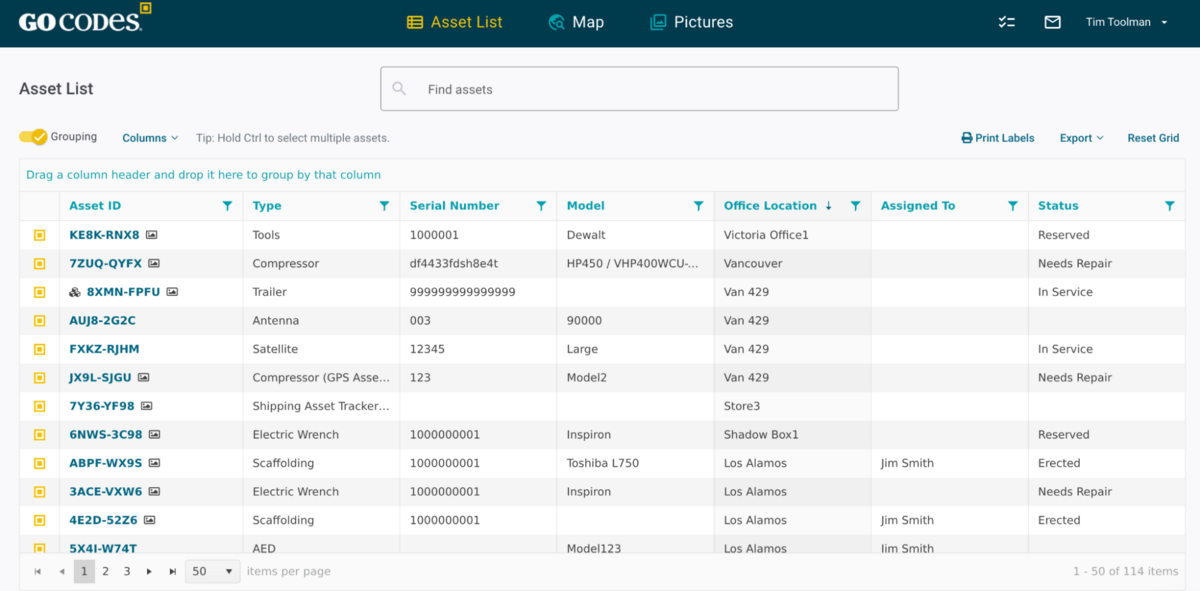
This allows your staff to easily access and review different, highly customizable data points.
By clicking on a specific asset, users get a more detailed view, including:
- Attached documentation
- Financial records
- Maintenance and repair history
- Associated tasks
- Location data history
- Usage history, i.e., chain of custody
Since all this data can be accessed and updated from anywhere, this saves time and eliminates data-reporting time lags and errors, thus streamlining jobsite workflows.
When this is coupled with your software’s reporting and alert-setting functions, this gives rise to a number of useful features.
For instance, you can now schedule regular maintenance and set automatic reminders for your staff, ensuring that no servicing task is missed.
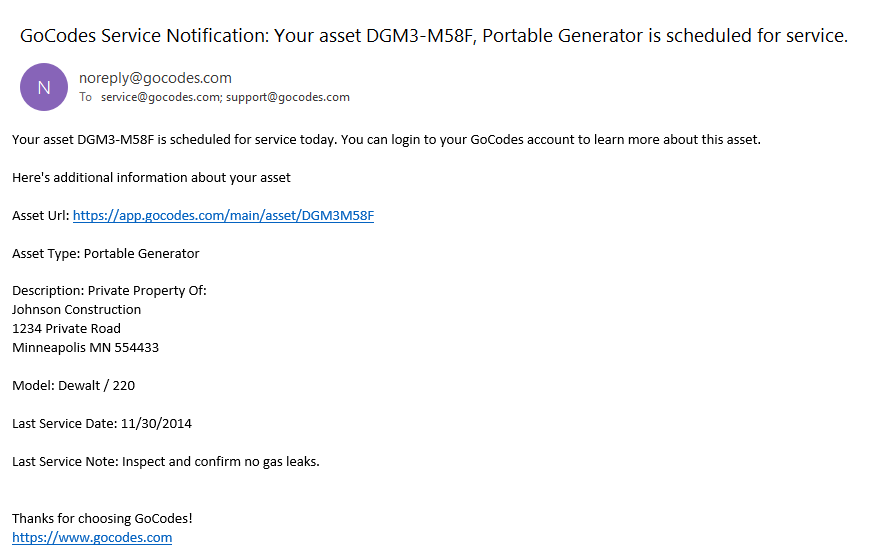
You can also review usage history and maintenance records to make better-informed repair-or-replace decisions.
When your tracking system includes GPS trackers, you can monitor vehicle movement in real-time and plan optimal travel routes.
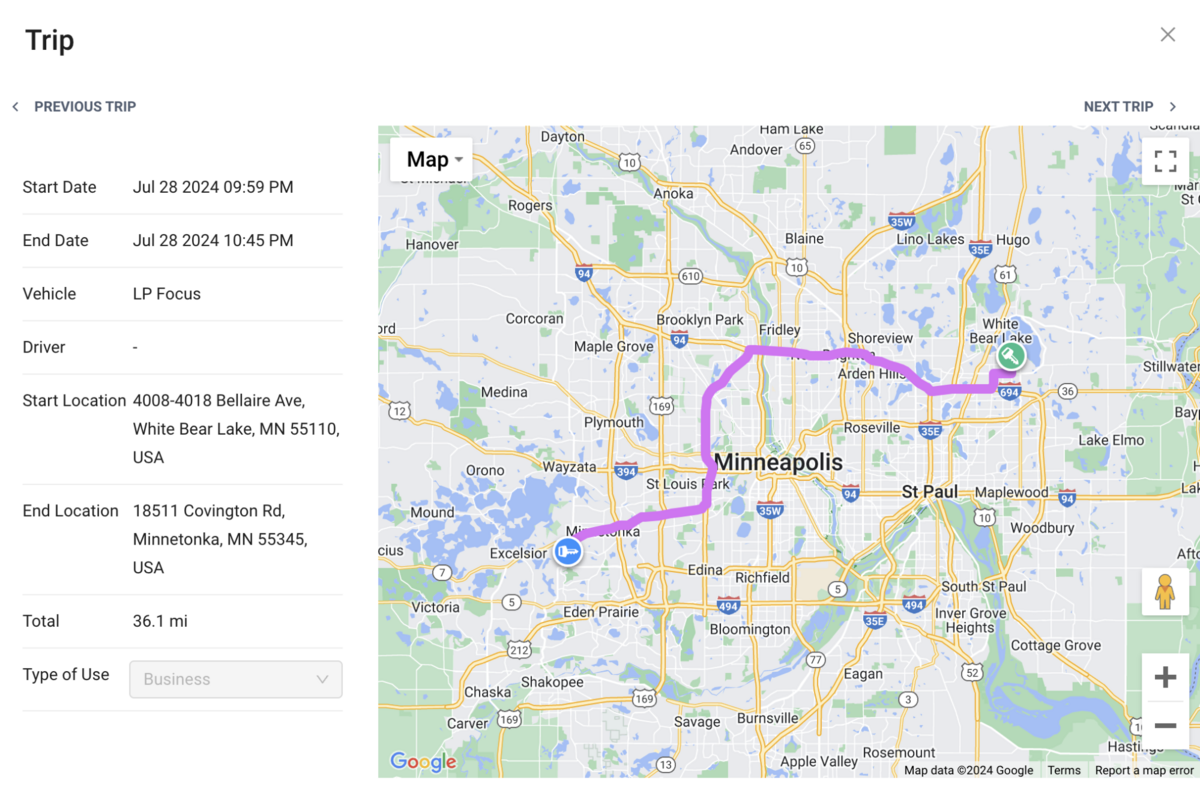
GPS trackers also allow you to set invisible security perimeters (geofences) to prevent asset theft and unauthorized use.
More precisely, you can designate a specific area of any size, and receive alerts if one of your assets leaves it without your knowledge.
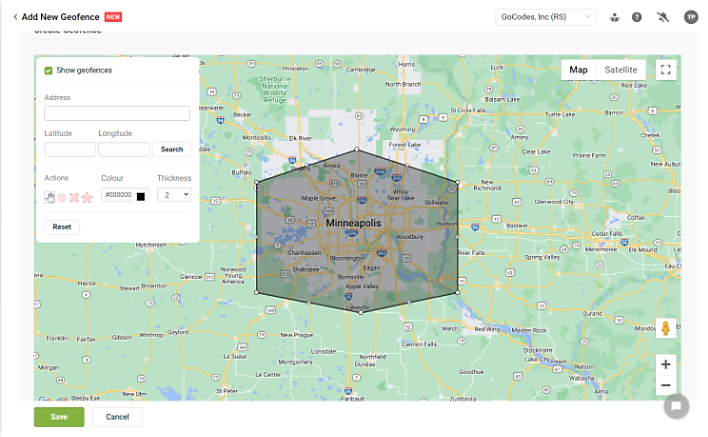
Depending on the sensors your equipment or your GPS trackers have, you can also monitor a range of other parameters from a vehicle’s speed to engine temperature and oil level.
Actually, today’s telematics technology (GPS plus sensors and/or cameras) allows you to track almost any relevant parameter, from tire pressure to driver behavior.
And the best part? The same data is accessible to all software users, so there is a single source of truth across your company.
How Do You Track Fixed Assets?
And what about construction assets that don’t change location?
You can track them too.
Just because they don’t get moved around doesn’t mean they shouldn’t be monitored.
Fixed assets include various systems and fixtures installed in your offices and storage facilities, as well as large stationary machinery and semi-permanent structures like fences and barriers.
Similar to movable assets, these can be easily tracked via scannable QR codes.
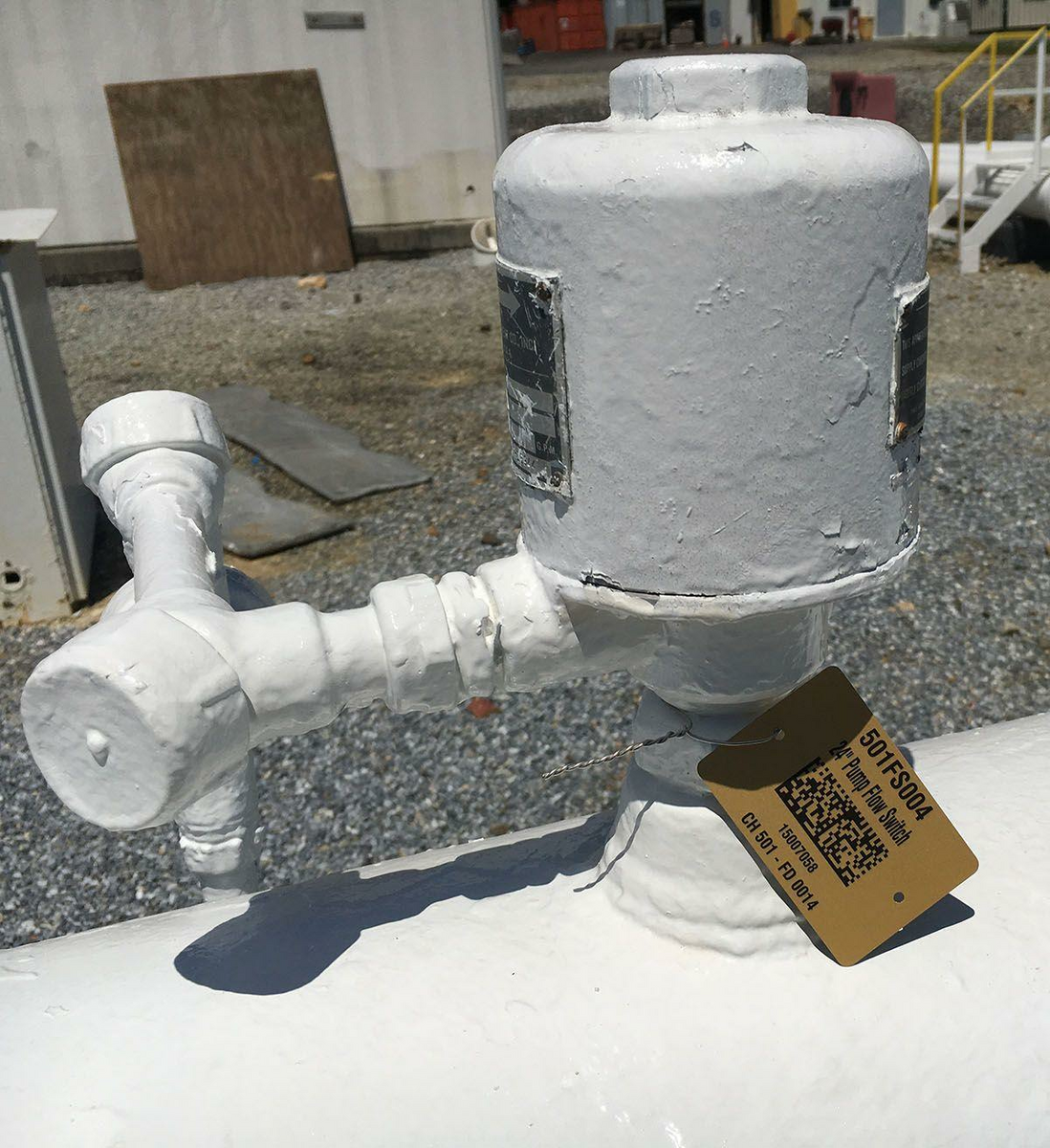
Such QR tags enable users to quickly access relevant asset information like operating instructions, maintenance requirements, or repair history.
However, some of these fixed assets might also benefit from having specific sensors attached to them.
For example, sensors can monitor for surges in electrical installations or leaks in gas lines and water pipes.
Typically, such sensors can transmit their data via an internet connection (Internet of Things, IoT), which enables you to receive alerts when something goes wrong.
This allows you to react in a timely fashion and prevent the issue from escalating.
Conclusion
Having covered the essentials, it’s clear that today’s asset-tracking technologies allow you to establish a multilayered tracking system tailored to your needs and budget.
While asset tags primarily allow for fast asset identification and data access, GPS trackers and other tracking devices enable you to track assets in real time, prevent theft, and improve operational efficiency.
So, the point is to find a user-friendly and affordable tracking software solution that combines the benefits of all these technologies in a single tracking system.