Key Takeaways
- Estimating equipment costs should include operational, maintenance, and labor costs.
- Depreciation is key to knowing your equipment’s true cost over time.
- Cost-estimating tools can make calculating equipment expenses much easier.
When you’re buying a car, you think about more than just the purchase price.
Registration fees, fuel, and repair costs all add up to show the real cost of ownership.
The same goes for construction equipment.
You need to consider fuel or electricity usage, operator wages, training, maintenance costs, and more.
Ignoring just one of these costs can spell big trouble for your profits, especially when bidding for construction projects.
But don’t worry.
Today, we’ll break down how to estimate your construction equipment costs, why doing so matters, and all the types of costs you need to consider.
Let’s get into it.
In this article...
Why Accurate Cost Estimation for Equipment Matters
Before you even start a construction project—or win the bid—you need to get your cost estimates right.
If you skip this step, you could end up over budget and with no profit.
You’d think construction companies have this figured out, but statistics tell a different story.
McKinsey reports that as much as 98% of construction projects face cost overruns, with the average cost increase hitting a whopping 80% over the original estimate.
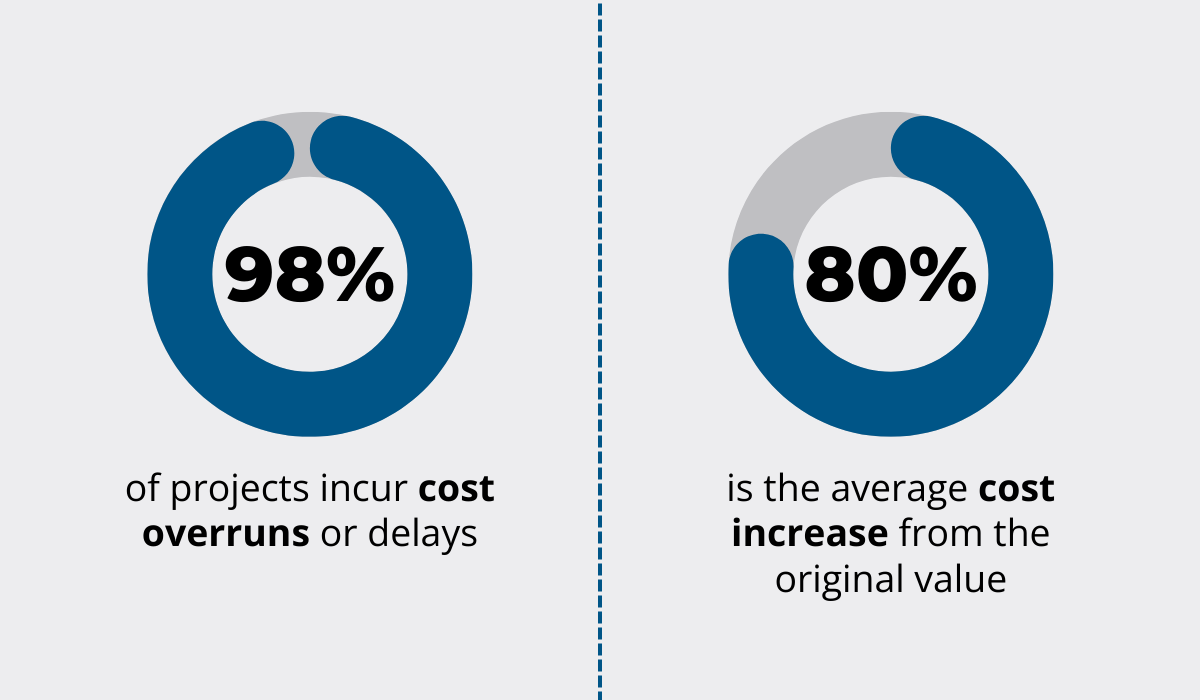
A big reason for this? Poor pre-construction planning and with it—poor cost estimation.
Now, you might have your materials and labor costs nailed down, but have you accounted for equipment costs?
To get an accurate estimate, you need to include every expense, especially for equipment.
And it’s not just the purchase price you need to consider.
You also have to factor in operating expenses like fuel, maintenance, repairs, and even operator wages.
When you have a handle on these costs, you can charge projects for the hours the equipment is used and make more accurate bids.
Ron Roberts of the Contractor’s Business Coach says it best:
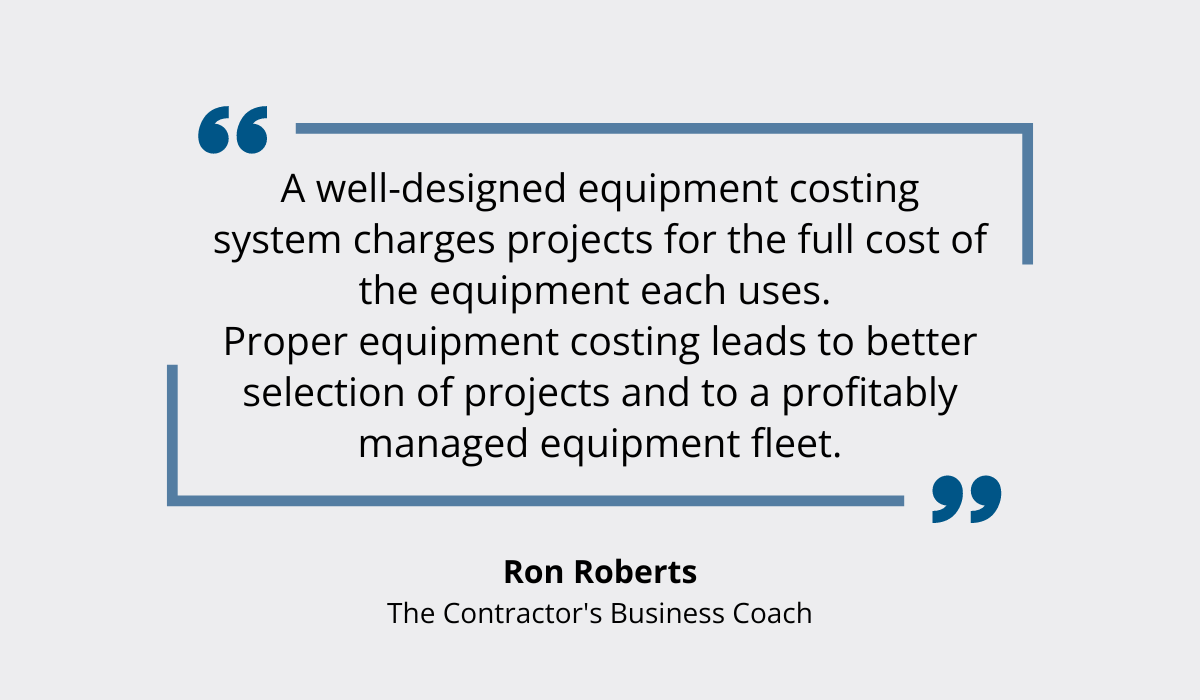
Overall, accurate cost estimations matter if you want to be profitable and keep your projects within budget.
And equipment costs make up a significant chunk of the overall project expenses.
In the following sections, we will go through all the costs you need to consider to estimate equipment costs as precisely as possible and make your bidding more successful.
Calculate the Fixed Costs
We are starting with fixed costs, which include the equipment’s purchase price, annual depreciation rate, taxes, and insurance.
Let’s use a new wheel loader as an example.
According to Five Star Equipment, a quality wheel loader costs between $100,000 and $200,000.
We’ll go with a middle-ground price of $150,000. That’s our purchase cost.
Next, we need to factor in depreciation: the reduction in value of your equipment over time due to wear and tear.
Think of it as spreading the cost of your equipment over its useful life to get a clearer picture of the true cost of owning and operating it.
There are two common methods to calculate depreciation: straight-line and usage-based.
Straight-line depreciation divides the purchase price by the equipment’s useful life.
If our wheel loader’s lifespan is ten years, and the salvage value (the estimated value of the equipment at the end of its useful life) is $20,000, the annual depreciation is calculated at $13,000 per year.
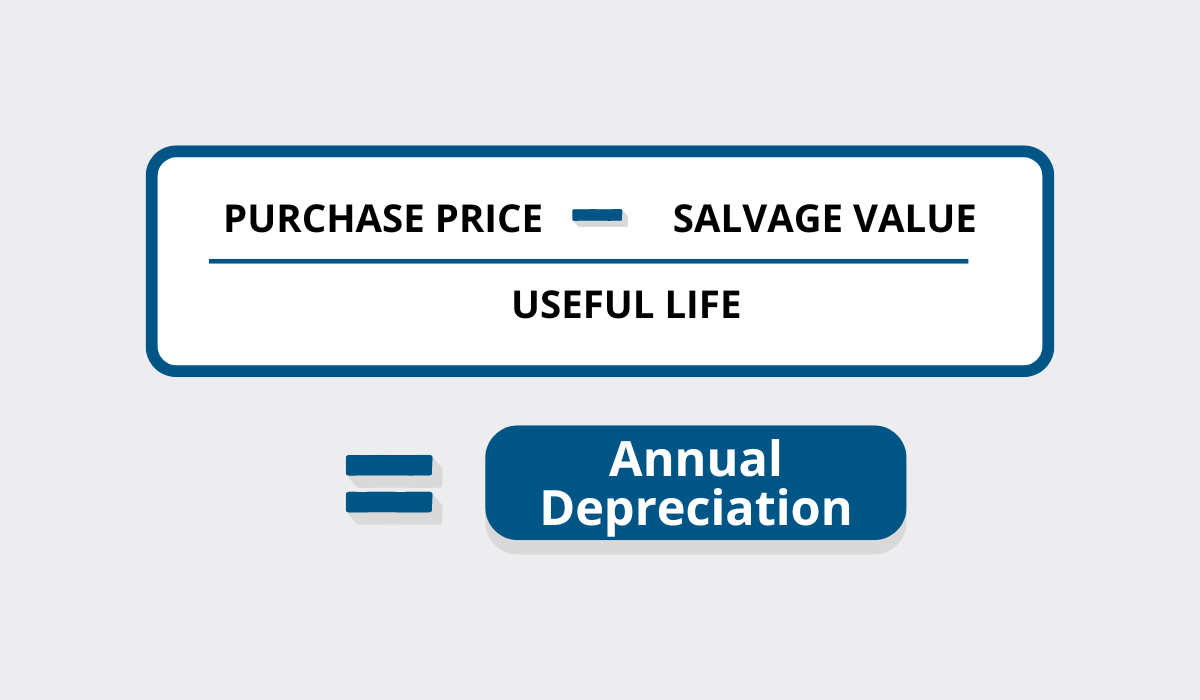
In other words, the wheel loader depreciates by $13,000 each year.
Usage-based depreciation, on the other hand, calculates depreciation based on the number of hours the equipment is used.
If the wheel loader is used for 1,200 hours per year and has a total lifespan of 10,000 hours, each hour of use depreciates the wheel loader by $13.
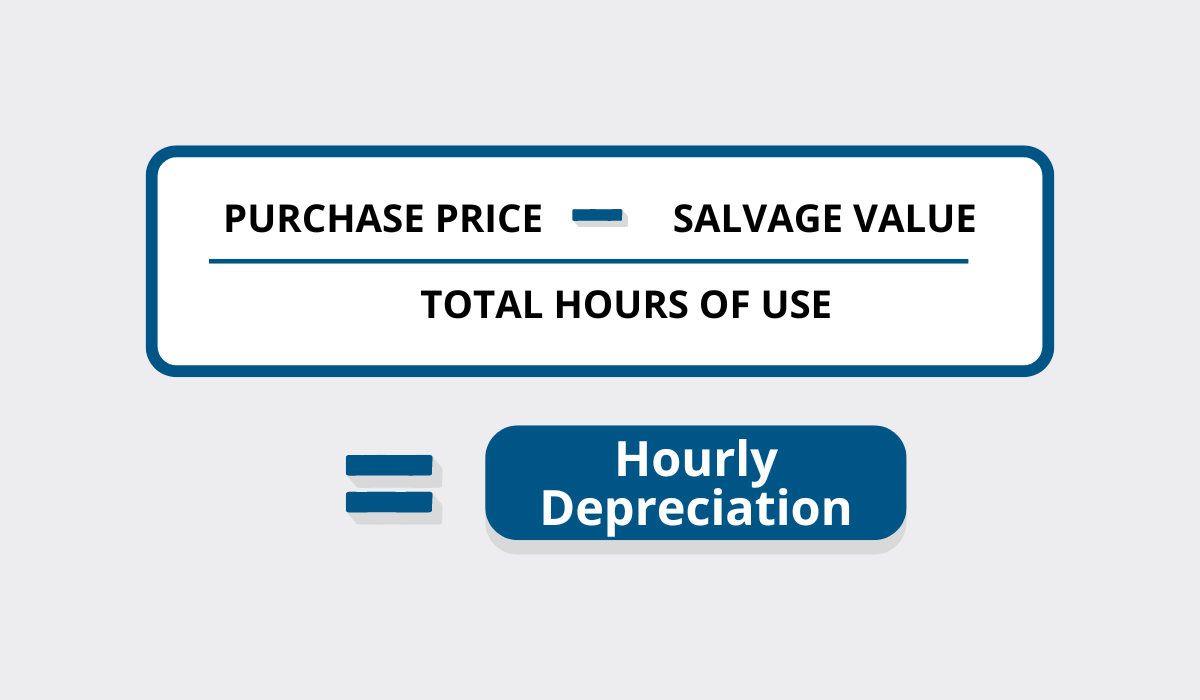
But why is this important?
Knowing how much value your equipment loses each year helps you track and allocate costs more accurately.
Depreciation affects your financial statements and tax calculations.
So, properly accounting for it ensures you’re setting aside enough funds to replace the equipment when it reaches the end of its useful life.
Finally, accurate depreciation calculations help you set realistic rates for equipment usage in your bids, balancing competitiveness with cost coverage.
Using a good equipment management system like our GoCodes makes calculating depreciation easy.
GoCodes takes your asset data—such as cost, purchase date, and asset life—and generates detailed depreciation reports with a single click, which you can use for financial statements and tax returns.
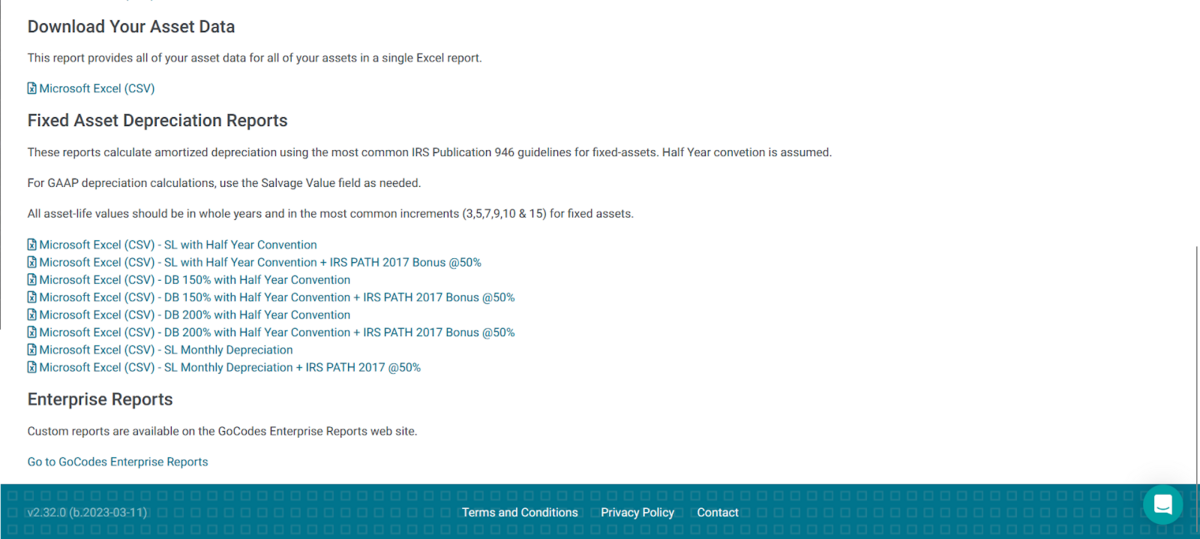
This ensures you consistently account for all fixed costs in your estimates, making financial planning more accurate and less stressful.
Besides the purchase price and depreciation rate, you also need to factor in liability and equipment insurance, as well as taxes, to get the total fixed equipment costs.
Add the Variable Costs
Fixed costs are just one part of the equation, though.
You also need to consider variable costs, which include operating expenses like fuel, electricity, and consumables.
Fuel, for example, is a major variable cost for construction equipment.
In fact, Market Research Future estimates that diesel consumption contributes more than 35% of the operational costs of construction equipment.
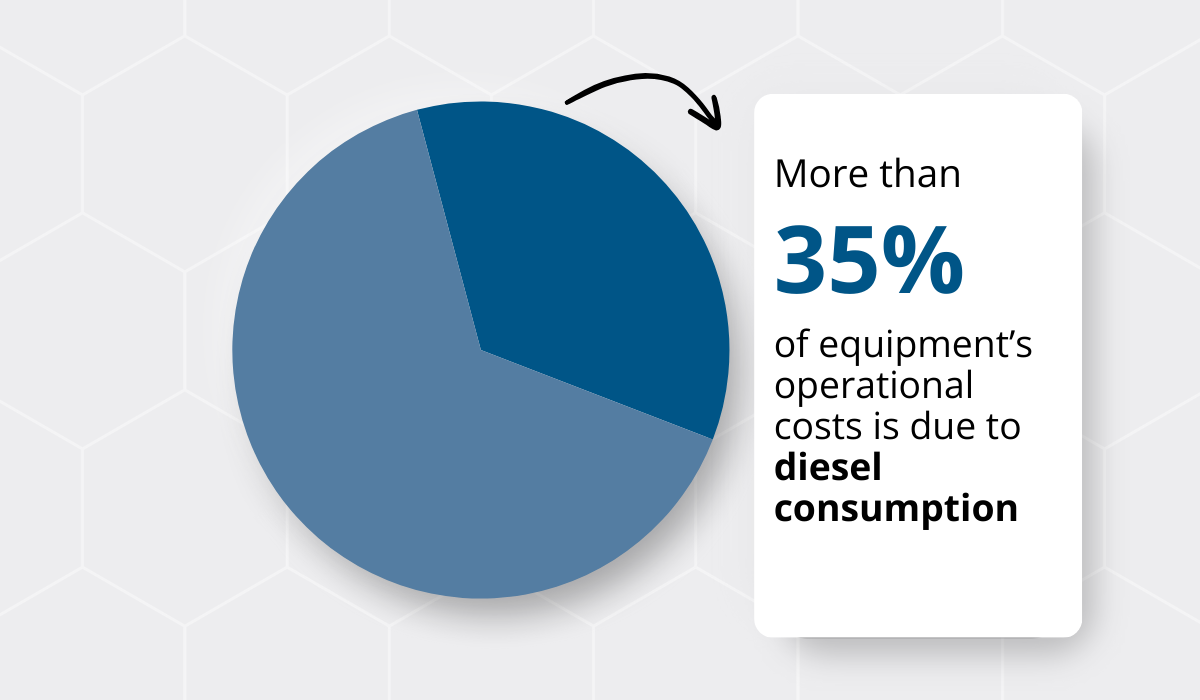
What’s more, fuel prices constantly fluctuate, impacting your company’s profitability.
Let’s say your wheel loader burns 8 gallons per hour based on typical usage.
With the current price of diesel in the US at $3.72 per gallon, this is $29.76 per motor hour.
If your wheel loader works 1,200 hours per year, that’s more than $35,000 just for fuel.
Can you believe that this is the expense that many companies simply overlook when estimating costs?
Consumables are another variable cost that can add up quickly.
These include items like liners and pistons for drilling equipment or tires for vehicles.
Below, you can see some consumables for our wheel loader example:
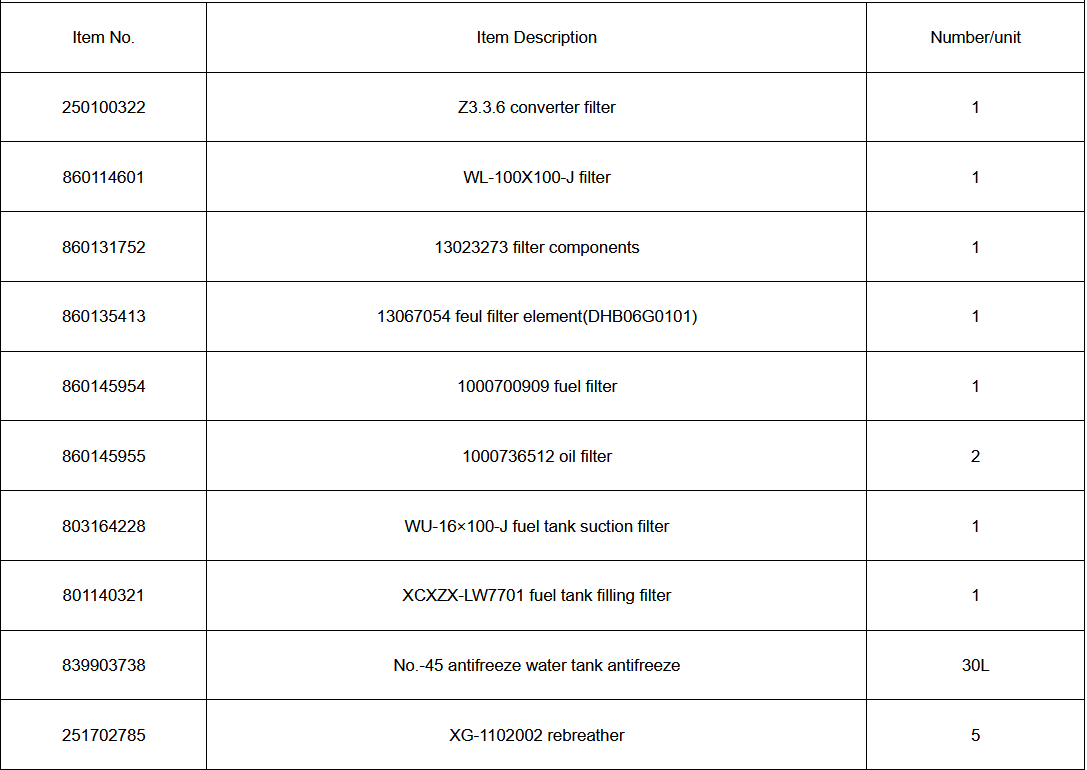
Wear and tear on parts like the bucket cutting edge, cylinders, and related hardware also contribute to variable costs.
To sum up, adding both fixed and variable costs gives you a clearer picture of the total cost of operating your equipment.
But that’s not all—you also need to consider the costs of people operating said equipment.
Include Labor Costs
So, the natural next step is to include labor costs, since they are a significant component of overall equipment expenses.
First, let’s break down the labor costs associated with operating your equipment.
According to the U.S. Bureau of Labor Statistics, as of May 2023, the median hourly wage for construction equipment operators is $26.57.
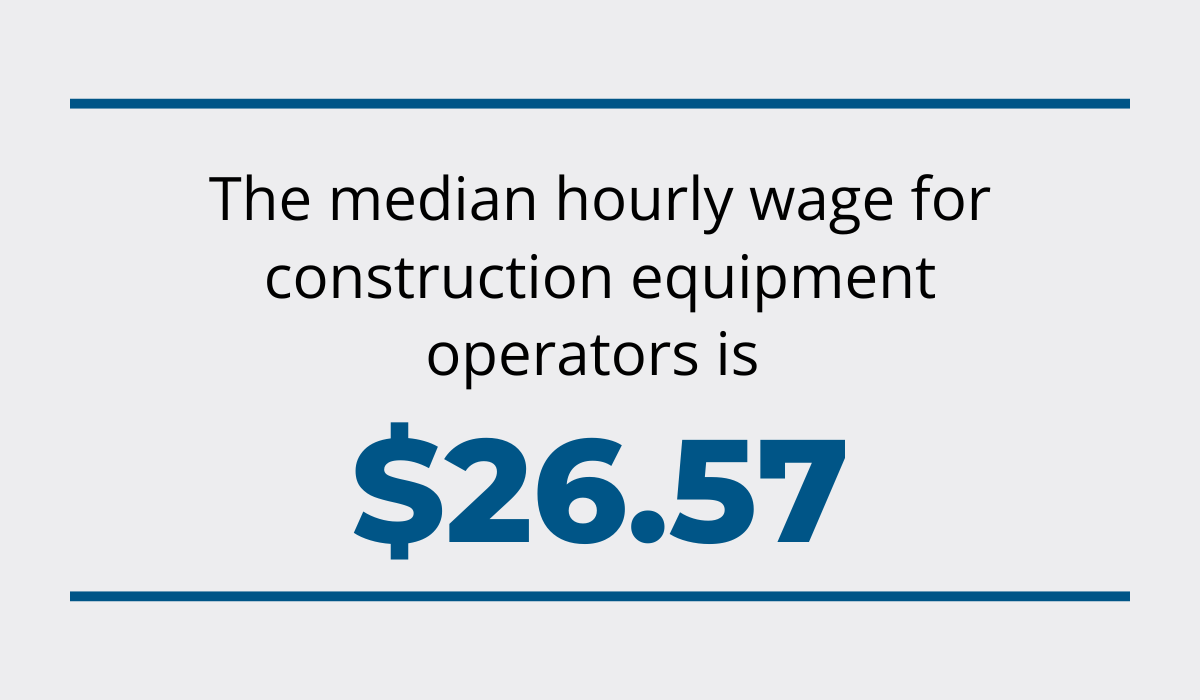
To estimate the total labor cost for operating a wheel loader, you need to calculate the average hours of operation and then apply the hourly wage.
Assuming your wheel loader is used for approximately 1,200 hours per year (a typical value for many general contractors), the total labor cost per year is $31,884.
In addition to wages, operator training is a crucial cost that should not be overlooked.
Proper training ensures the safe and efficient operation of the equipment and compliance with safety regulations.
If we go back to our wheel loader example, first and foremost, operators of wheel loaders must obtain certification and licenses to operate safely.
This often includes:
- an Occupational Health and Safety (OHS) certification,
- a Heavy Equipment Operator license, and
- specialized endorsements for specific attachments or hazardous environments in some jurisdictions.
Often, these licenses must be renewed periodically to ensure operators stay up to date with the latest safety practices and regulations.
Operators may also need to participate in ongoing education programs to maintain their skills and stay current with industry advancements.
To shed some light on how much all this costs, let’s take a look at Total Equipment Training from Pennsylvania.
They offer programs that cost around $2,100 per day for a team of 8-10 people, and the training typically lasts between three to eight weeks.
So, for five weeks, that’s $52,500.
While this may seem like a significant expense, investing in proper training is essential for safety and operational efficiency.
And it’s another important number in estimating equipment costs.
Don’t Forget About Maintenance Costs
Maintenance is key to managing construction equipment, but it’s often overlooked in cost estimates.
Don’t make that mistake—make sure to factor in maintenance costs, too.
Preventive maintenance might cost upfront, but it’s usually more cost-effective than reactive maintenance.
Why?
Because it helps you avoid the high costs of emergency repairs and equipment downtime.
Plus, it extends the lifespan of your equipment, ensures better work quality, and minimizes project delays.
Take it from Nick Howell, president of T&N Asphalt Services, who experienced this firsthand:
“Yes, preventive maintenance costs up front, but we haven’t had a wand or hose fail in service or any other time-consuming breakdown in quite a while. We haven’t had to stop in the middle of a job, pull a piece of equipment out of service, or disappoint clients by rescheduling their work.”
And GoCodes can help you here as well.
With GoCodes, you can assign maintenance tasks to your employees, set reminders, track completed work, and ensure your equipment stays in top condition.
All in one place!
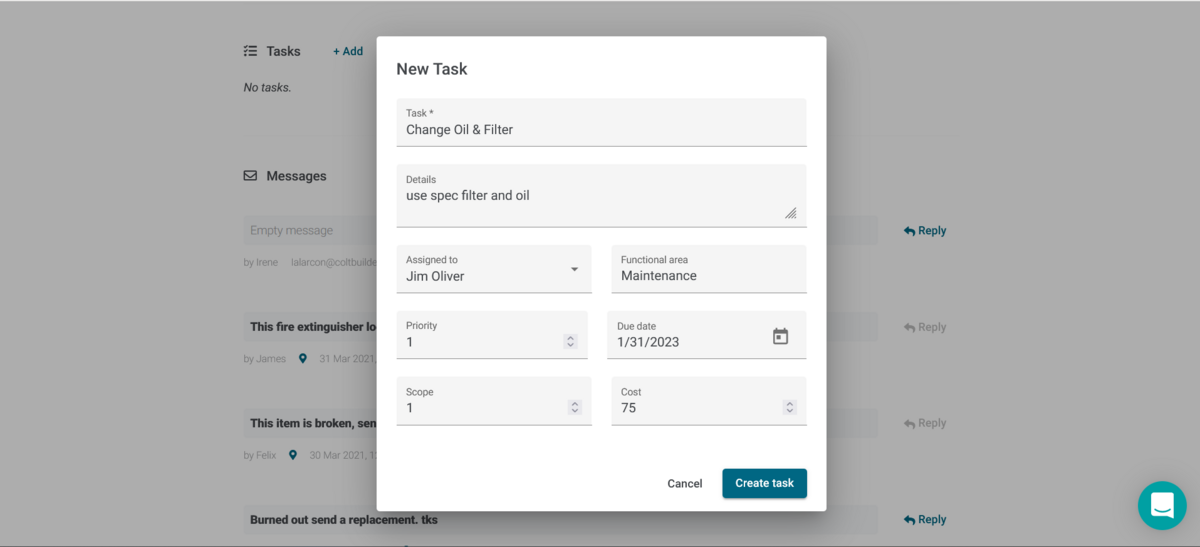
Now, how can you estimate preventive maintenance costs?
First, include the cost of items such as filters, lubricants, and other consumables that need regular replacement.
For a wheel loader, this involves parts like fuel filters, oil filters, hydraulic fluid, and antifreeze.
Next, some maintenance tasks require skilled technicians.
The average hourly wage for maintenance and repair workers in the U.S. as of May 2023 is $23.87, as reported by the U.S. Bureau of Labor Statistics.
Calculate the total labor cost based on the number of hours required for routine maintenance tasks.
For the number, the type of tasks, and when you should schedule them, review the equipment’s operating manual.
For example, a wheel loader’s maintenance schedule will include checking the transmission, inspecting the engine and hydraulic system for leaks, and retightening screws.
The manual, like the one in the image below, will clearly outline how often you should perform each task.
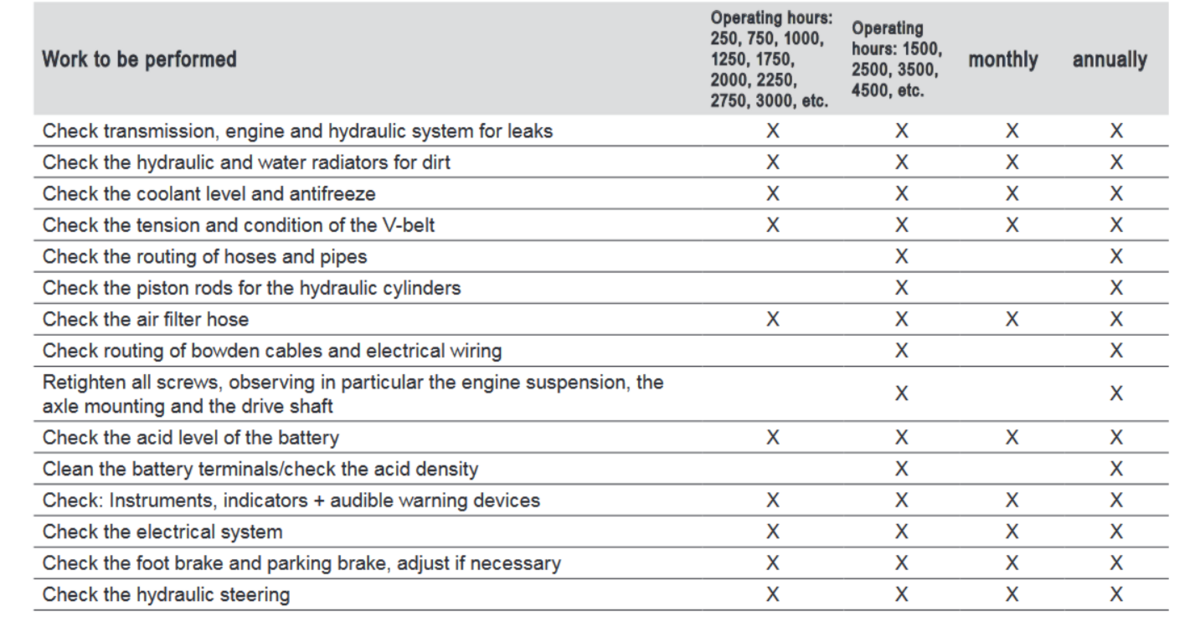
Finally, you should factor in any additional costs, such as utilities or overheads associated with the maintenance process.
All this on a yearly basis will cost you between $4,000 and $6,000.
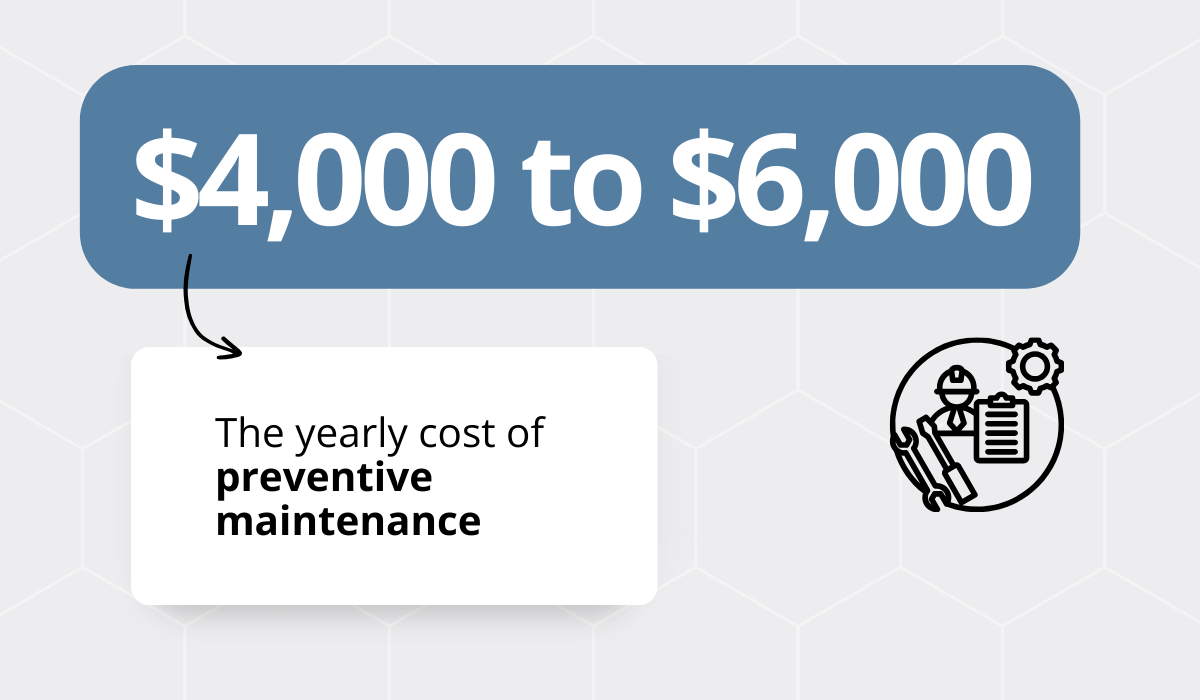
In contrast, reactive maintenance can be significantly more expensive.
For instance, repairing an engine failure on a Manitowoc 10,000 crane can exceed $36,000.
Or, if the engine fails on a wheel loader, a used engine might cost you as much as a year’s worth of preventive maintenance!
You Don’t Have to Do It Manually
Calculating all these costs manually can be overwhelming—we agree.
Thankfully, there are various cost-estimating software tools and online calculators that can help you quickly and accurately calculate equipment costs.
For example, PennState has a calculator that helps you estimate costs associated with equipment purchases.
It takes into account the purchase price, depreciation, and operating costs, making it a valuable tool for construction managers and financial planners.
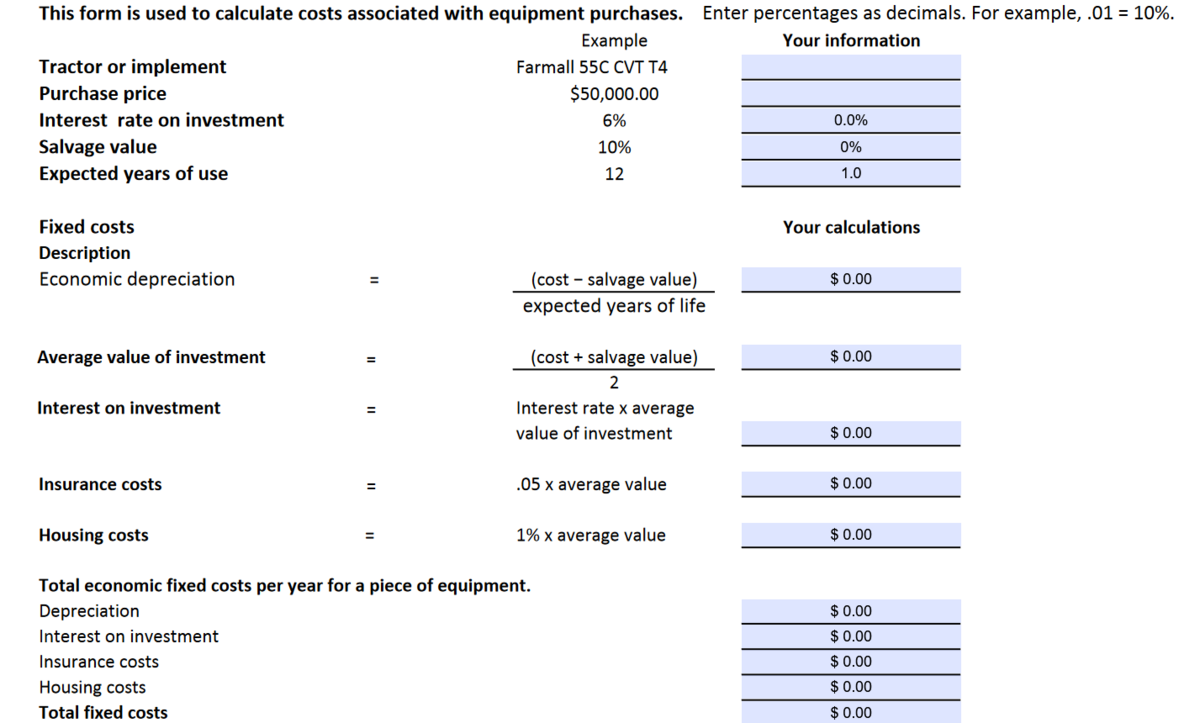
You can also easily calculate fuel and lubrication costs with it.
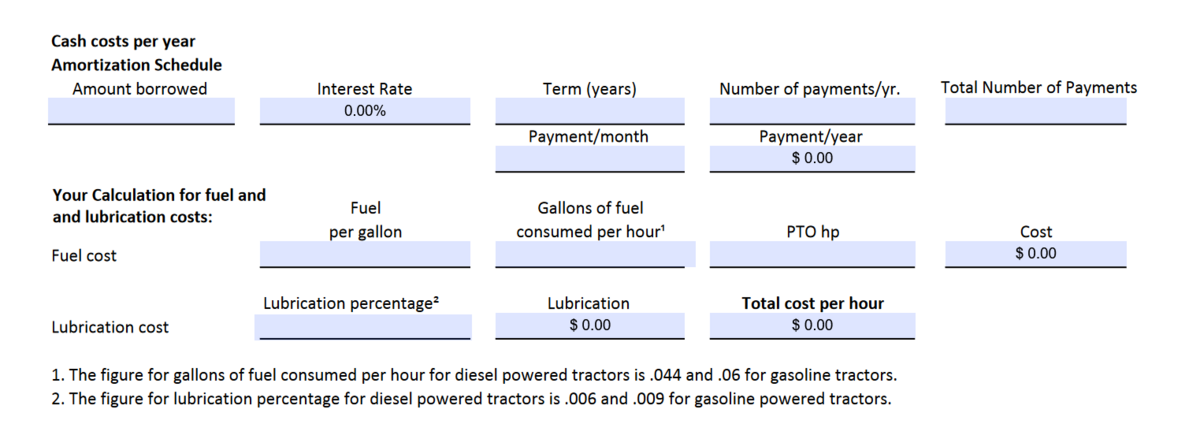
If you need to purchase, for example, an excavator, Volvo’s TCO calculator can help.
This tool breaks down the equipment cost into:
- Total annual ownership cost, including depreciation, interest, and other ownership-related expenses.
- Total annual operating cost, covering fuel, lubricants, repairs, and maintenance.
- Total annual operator cost, including the cost of labor for operating the equipment.
Take a look at Volvo’s calculator below:
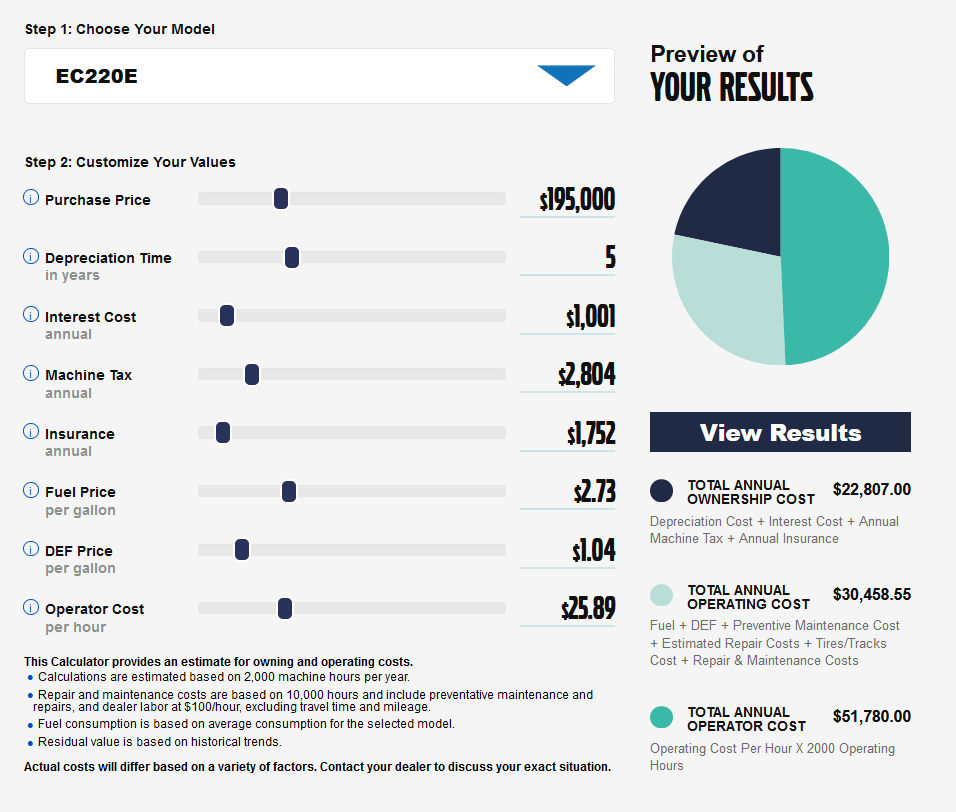
Definitely check these calculators out if you want to quickly calculate your equipment costs, or just to remind yourself of all the costs you have to consider.
What If You Don’t Own the Equipment?
If you don’t own the equipment, renting is your next best option.
For one-off, last-minute rentals, you can browse different websites to get a sense of the average daily or hourly rates.
However, if you’re looking at longer-term rentals, specialized rental websites are your go-to.
For example, let’s say you need to rent a backhoe loader for a month in Wisconsin.
Rental companies will give you a breakdown of costs, including transportation fees if they’re delivering the equipment, and sometimes an environmental fee.
They’ll also show you rental rates by the day, week, or month, as you can see in the example from United Rentals:
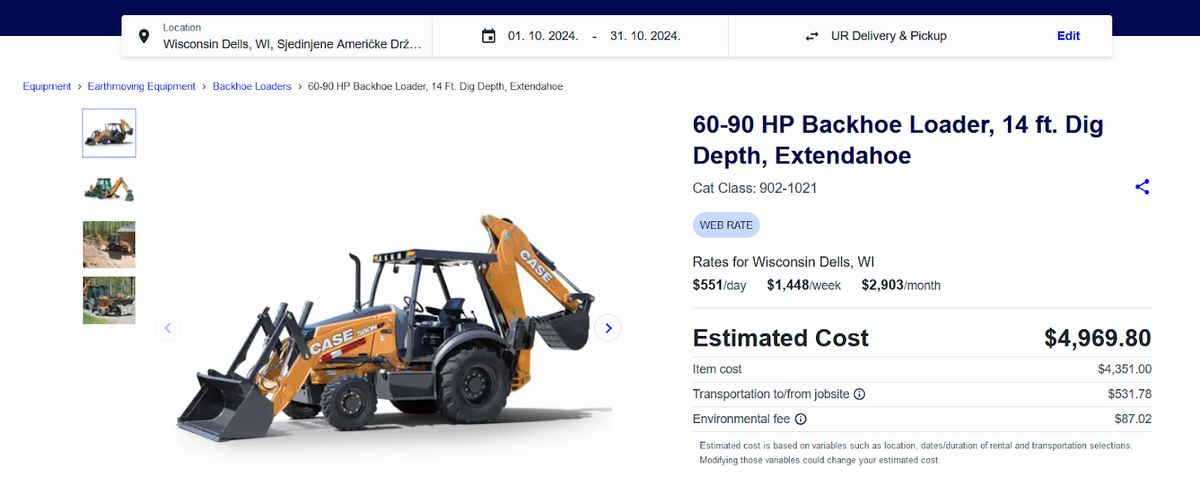
But here’s a crucial tip: pay attention to the included hours in the rental agreement.
Rental contracts often specify a certain number of hours the equipment can be used during the rental period.
For example, a daily rental might include only 6 hours of use instead of 8.
If you go over those hours, you could face extra charges.
So, it’s important to accurately estimate how many hours you’ll need the equipment for in order to avoid unexpected costs.
Another thing to watch out for is maintenance fees.
Make sure you understand who is responsible for maintenance during the rental period.
Take the time to clarify all of these details upfront to avoid any surprises later, as this will help you determine whether renting equipment is the right choice for you.
Conclusion
All in all, estimating construction equipment costs is crucial for better project planning, staying within budget, and ensuring profitability.
But to estimate costs properly, you need to consider more than just the initial purchase price.
From depreciation, taxes, and insurance to fuel, consumables, labor hours, and maintenance costs, you need to account for everything to get an accurate estimate.
So, make sure to do it properly next time you plan to buy a piece of equipment or when preparing a bid for another project!