Key Takeaways
- Creating a solid plan for the end of year inventory count is crucial.
- Categorizing inventory into consumables, materials, tools, and equipment can make inventory counting more efficient.
- Investing in construction inventory management software saves time and money, and reduces errors.
Running an efficient inventory count at the end of the year is a must for at least two reasons.
One, you can’t ensure tax compliance and accurate financial reporting without a complete inventory count.
Two, the collected insights form a strong basis for effective business planning.
Since the end of year inventory counts are time-consuming and prone to human error, following a few best practices can be the game changer for your construction company.
We’ll zoom in on essential inventory count practices, so if your goal is to streamline this process and reduce inaccuracies, you’ve come to the right place!
In this article...
Create a Detailed Plan
Preparing a comprehensive plan may not be a necessity for every task.
However, when it comes to the year-end inventory count, the value of planning ahead can’t be overstated.
After all, it’s a complex undertaking that sets your business up for success come next year.
Good planning is a key starting point that ensures your overall process is well-structured and can yield accurate inventory insights.
And to make sure it runs as smoothly as possible, you simply have to account for all the details, outlined in the image below.
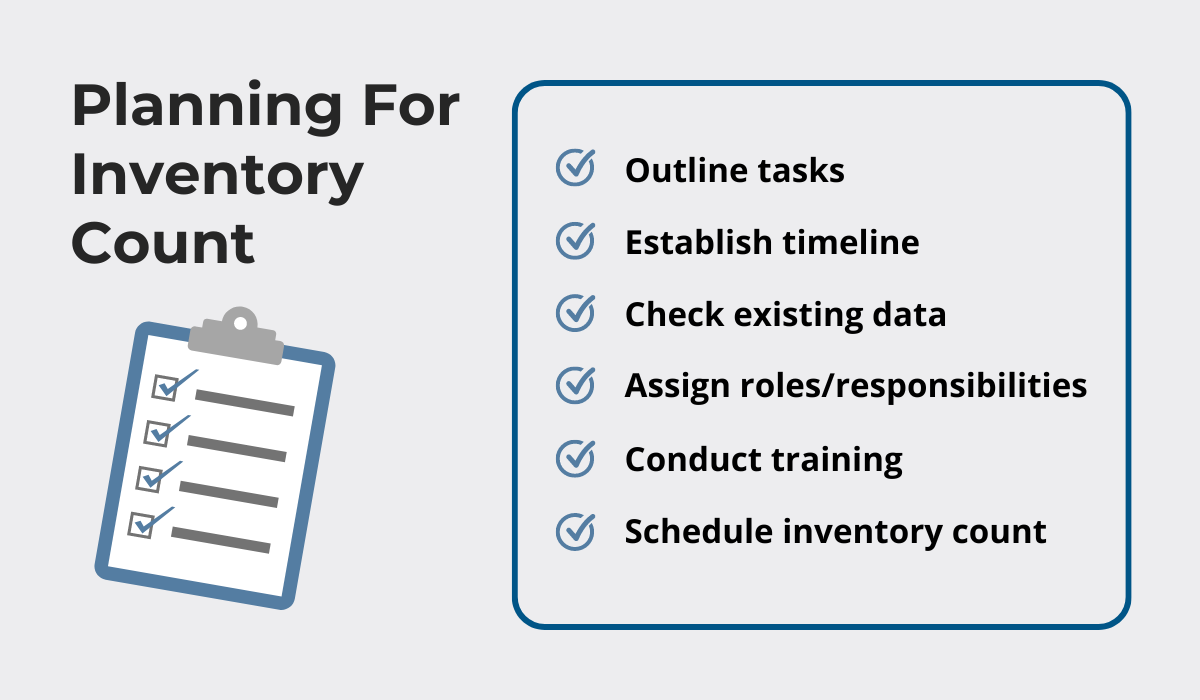
It starts with outlining all the related tasks and deadlines, from how the count should be conducted and at which location(s), to who will be doing it and by when.
Given that this is an all-hands-on-deck operation, it’s vital to think through and assign roles and responsibilities ahead of time.
Having all the team members in the know enables an organized count process and promotes efficiency, but it’s important for one additional reason.
Take into account when these end of year inventory counts are conducted.
Most businesses, construction or otherwise, aim to schedule the inventory count during periods of lower activity to ensure accuracy and reduce the disruptions as much as possible.
While this is indeed a best practice for a reason, the end of the year doubles as the time when many employees use their annual leave.
Timely planning guarantees an optimal number of the workforce for the actual count, but it also gives you a quick overview of who you can assign preparatory tasks to.
Namely, there are a couple of steps you’d be wise to take before the inventory, and it boils down to organizing space and mapping certain items in advance.
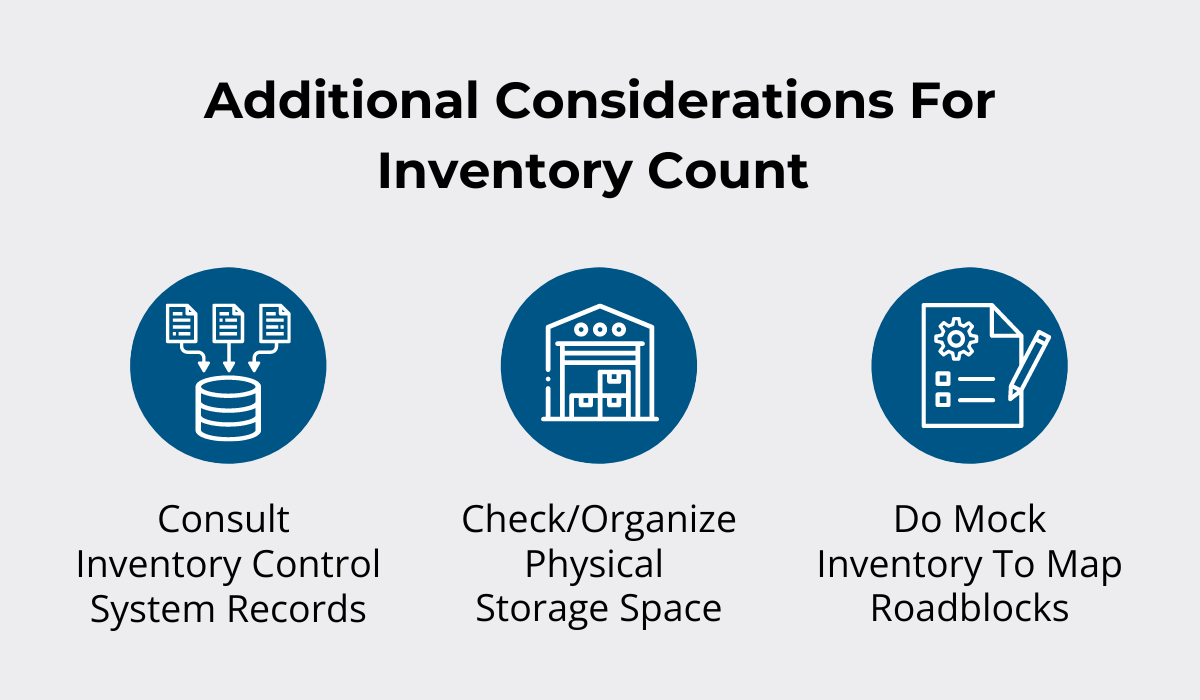
For example, if you’re using an inventory control system, you can compare the records from the last periodic inventory count with the situation on-site, checking off larger assets immediately.
Having personnel check the main warehouse and active job sites to ensure all the materials and equipment are located in their designated spots, means anticipating potential roadblocks and having a better sense of how to best allocate your resources.
And since this sort of mock inventory allows you to eliminate hiccups—from missing tags to unbagged supplies—you’ll be minimizing downtime and boosting efficiency.
Another way of enhancing efficiency is by categorizing your inventory, so let’s take a closer look at this practice next.
Categorize Your Inventory
Structuring the process and performing an end of year inventory count is much easier if you’ve categorized your inventory first.
The opposite is true as well.
Cluttered inventory prolongs the count, creating unnecessary frustration and confusion when discrepancies are observed.
There’s a good reason why warehouse disorganization ranks among the most common inventory mistakes.
But when it’s done right, construction inventory management streamlines and automates the processes of ordering, storing, and distributing inventory, thereby boosting workers’ productivity.
Making sure that everyone can find and use the equipment and materials they need at any given moment is a priority, and that same logic applies when doing an inventory count.
If your inventory is categorized in a structured and logical way, the counting process will take less energy and time.
The basic categorization typically rests on recognizing consumable items, building materials, equipment, and tools as distinct categories.
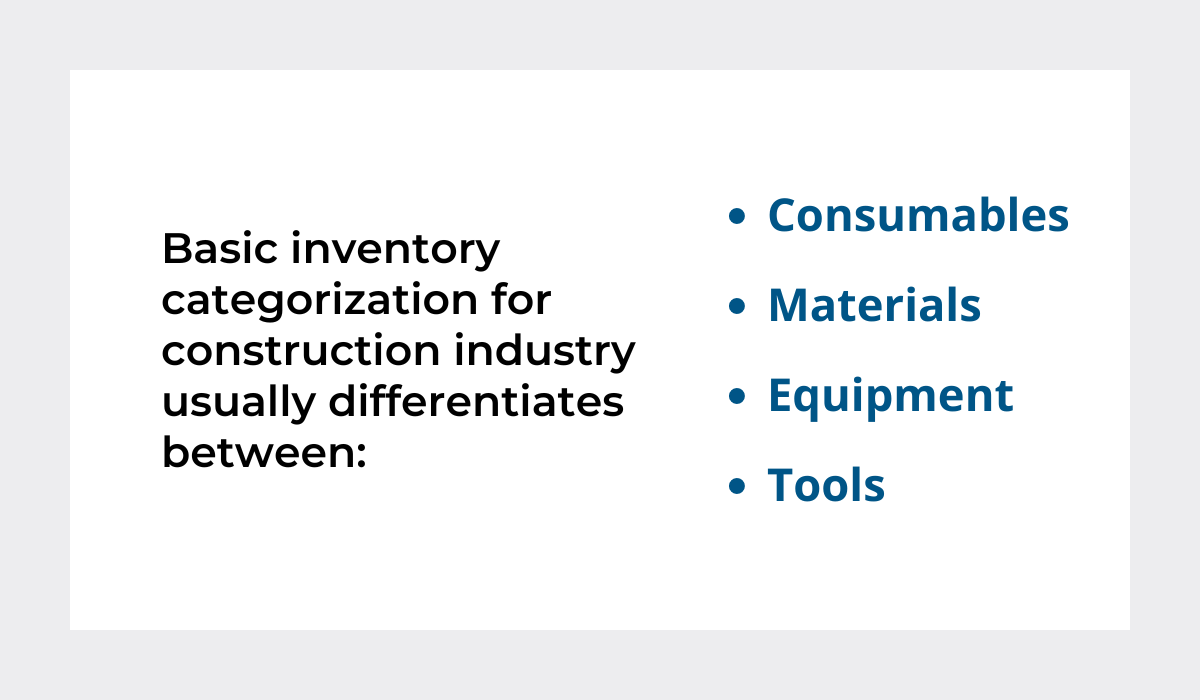
Additional attributes that determine warehouse organization may include item size or frequency of use, with the latter needing to be easily accessible at all times.
The core idea is to have similar items put together in the most logical way to reduce the risk of either miscounts or misplacements.
Naturally, this initial categorization is refined further through other construction inventory management methods, such as the ABC analysis.
“ABC inventory analysis complements physical inventory count by adopting three broad categories that are checked regularly. The frequency of counts depends on the items’ value and how fast-moving they are.”
“A” corresponds to the priority category that needs to be accounted for most frequently, while “B” and “C” designate moderately and least important categories, respectively.
This intuitive framework is used for maximum efficiency and productivity, ensuring that critical tools and materials are accessible and within reach across multiple job sites.
The general principle behind grouping equipment, tools, raw materials, and other supplies to achieve uniformity and coherence is also applied to counting procedures.
So, let’s explore why and how standardizing them works in this context.
Standardize Your Counting Procedures
Considering the importance, scope, and complexity of construction operations, establishing standardized procedures for end of year inventory counts is simply a must.
Although accuracy and consistency are paramount regardless of the inventory count type, making a record of all company assets and materials stored across multiple locations warrants extra care and caution.
One surefire way of exercising caution and achieving uniformity is to ensure standardization of the counting procedures.
The icing on the cake here is that you have plenty of reasons to do so, with some of them outlined below.
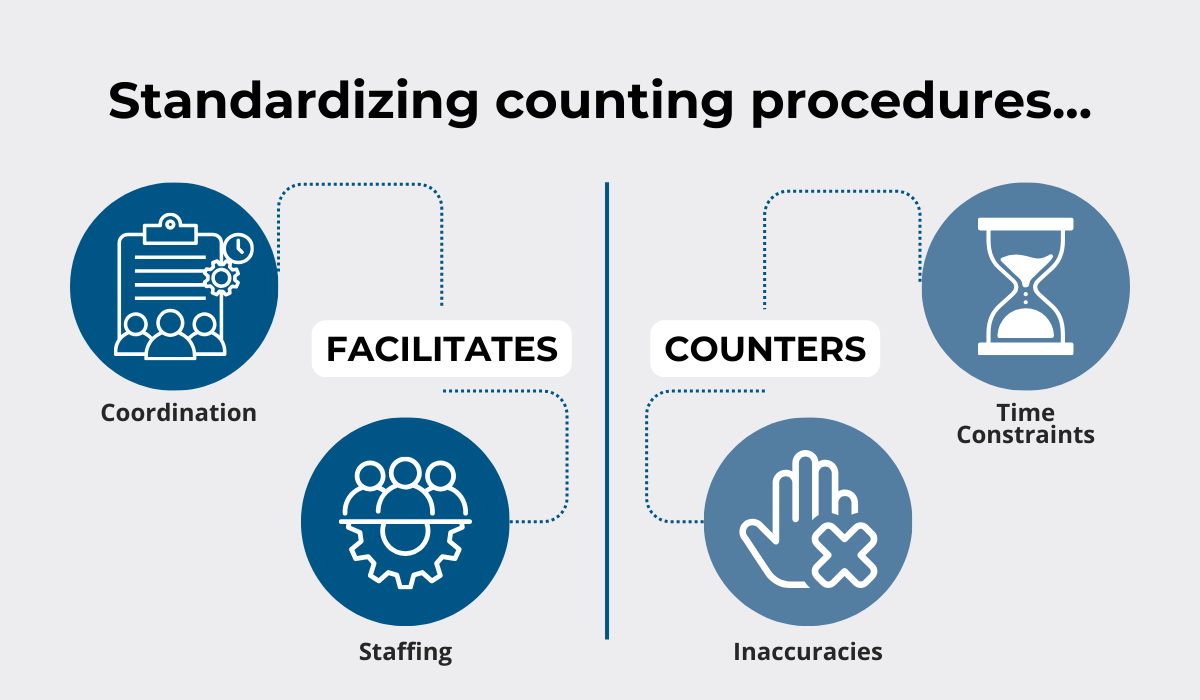
Paying attention to standardization ensures that the overall process runs smoothly, with efficient coordination and accurate estimates of the number of staff you need to involve.
Moreover, standardized procedures bring greater clarity, regardless of the employee profile and prior experience.
For example, counting procedures should clearly define whether to count a box containing multiple parts as a single unit or 10 units.
Simply put, construction companies that don’t leave space for confusion or individual interpretation find it easier to counter inaccuracies and ensure timely completion of the end of year inventory count.
Here is a quick breakdown of some common counting procedures you can rely on for transparency and efficiency:
Counting in two-person teams | Pairing up helps prevent fraudulent counts, but also contributes to efficiency and accuracy. |
Doing blind counts | Avoid listing the expected quantity of items to prevent confirmation bias that could increase the chance of errors. |
Utilizing prenumbered tags | If barcode scanners aren’t utilized, use two-part sequential tags with basic info, such as name, part number, count, and location. |
One thing to keep in mind here is that, while these procedures help speed up the physical count and enhance accuracy, they are far from your only option.
Many construction companies are turning to software solutions to standardize their counting procedures and deliver even quicker and more reliable results.
We’ll explore why this is a good practice next.
Invest In Construction Inventory Management Software
What are some of the top reasons why businesses decide to invest in different construction technologies?
There are several tell-tale signs that a company needs a construction inventory management solution, but the final decision is usually reached due to one of the following objectives:
- Streamlining processes
- Improving accuracy
- Saving time and resources
Adopting a cloud-based inventory management system brings numerous benefits, helping you reduce costs and free up time by removing human error from the equation.
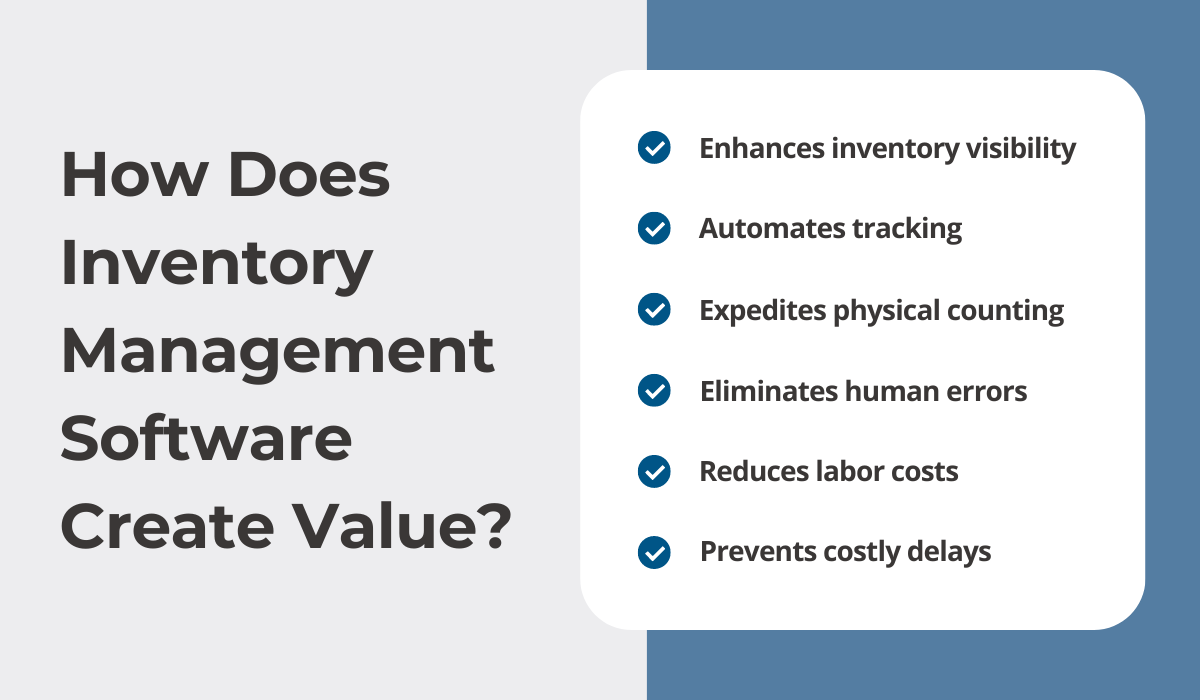
The main qualities of the construction inventory management software also come to the foreground when performing an end of year inventory count.
The system provides accurate inventory records and real-time updates, but its robust tracking and monitoring abilities are used to their full capacity through barcode scanning technology or RFID labels.
Barcode tags in particular are the staple of inventory control solutions, allowing for quick and accurate identification of different inventory items during the count, as soon as they get their respective tags attached to them.
The ease of use means that the teams involved in the counting process can efficiently record counts, regardless of their prior experience and with minimal training.
And the added benefit is that they can do so without risking manual entry errors.
GoCodes Asset Tracking is a prime example of asset tracking made easy, as it provides exactly the kind of visibility you need for efficient inventory counting.
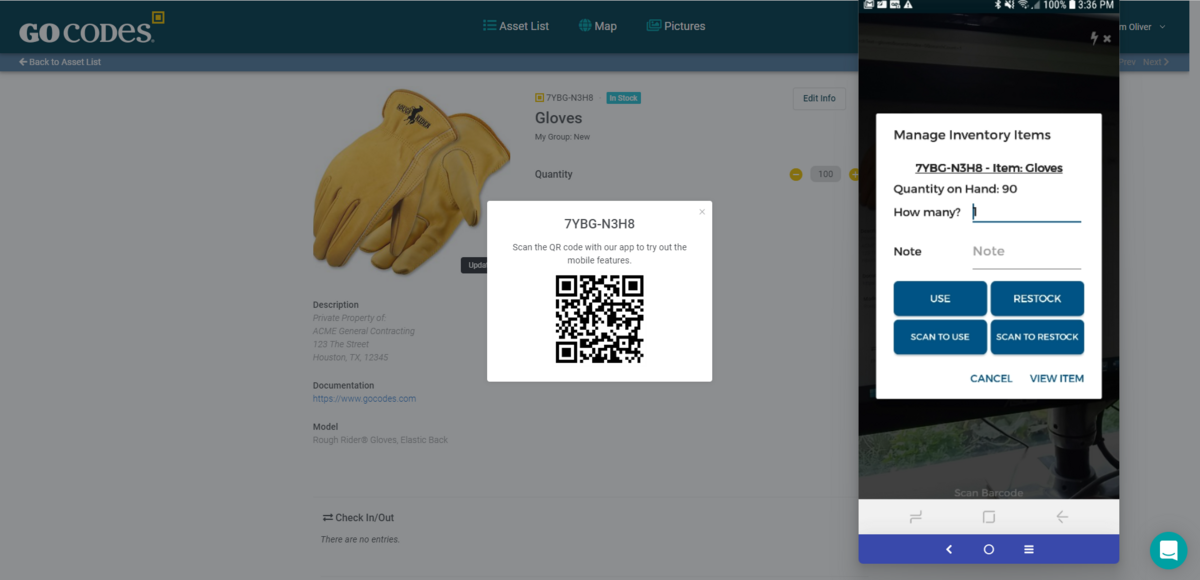
The software compiles key information on the scanned item’s location, past check-in and check-out entries, and scanning time and date, as well as the identity of the employee who completed the inventory scan.
One of the reasons why tracking and managing inventory feels effortless with GoCodes Asset Tracking is its intuitive and easily customizable quantity tracking feature.
Updating your inventory quantities during an extensive end of year inventory count seems like a daunting task, at least until you’re able to do so in just a click or two.
Want to know the best part?
All of the data and functionalities are readily available on our mobile app, which makes all of the difference when conducting counts simultaneously across multiple locations.
Nevertheless, even the best software in the world can only be used by well-prepared staff, which brings us to our next point.
Prepare Your Staff
Circling back to our initial point, one crucial aspect of devising a detailed plan for the end of year inventory count depends on informing and training all the involved staff.
Think about it: what better way to ensure the process is done quickly and accurately?
By bringing everyone up to speed on methods, standards, and protocols, construction companies can more readily rely on the validity of the data collected during the count.
At the same time, securing accurate data from the start means avoiding prolonged and expensive recounts.
Preparing staff members to contribute to the end of year inventory count can be divided into three key elements you can see below.
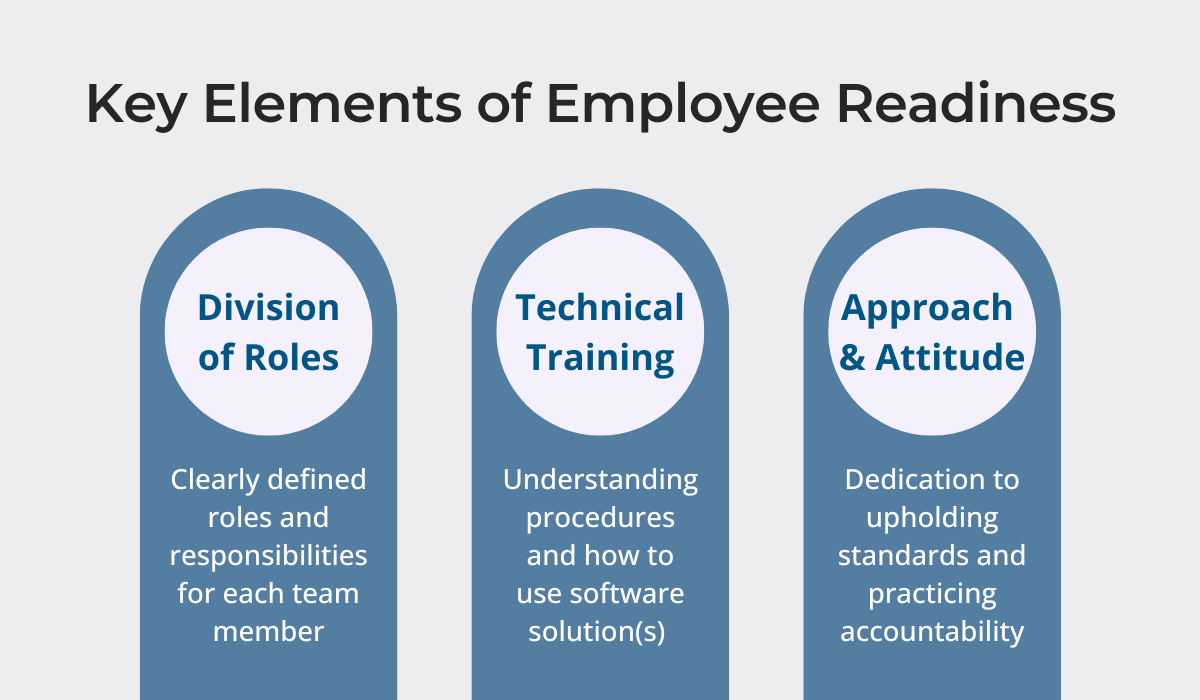
Clearly defined roles, excellent practical know-how, and an overall approach to the task are integral ingredients of any successful work process, and inventory counts are no different.
For starters, it’s essential to communicate each team member’s specific tasks and responsibilities, alongside the areas they will be working in.
After all, there is a lot of ground to cover, so if there’s any lingering confusion, you’re risking not only mounting frustration over additional work hours but also inaccurate data.
Since initial briefing is rarely enough, no matter how well delivered it may be, designating one person or a small team as the central point of contact for all questions and updates is vital for ensuring a successful count.
The coordinating team also guarantees quality, reaffirming why it matters on every occasion.
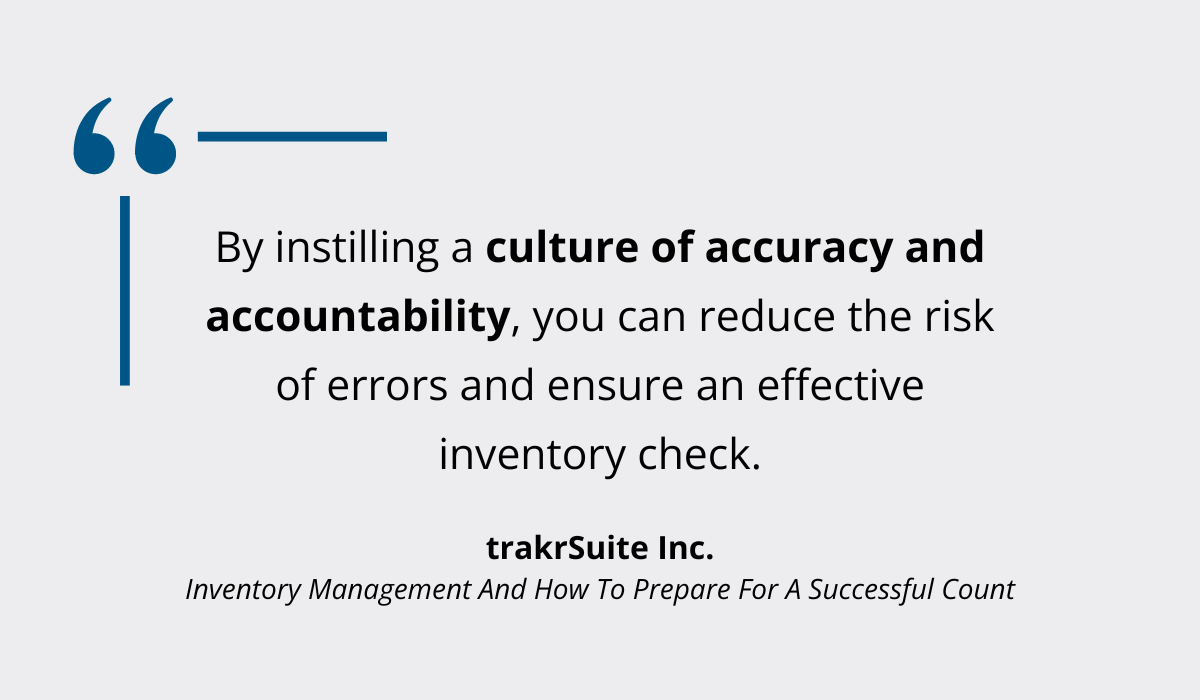
Stressing the importance of accuracy and upholding standards goes hand in hand with delivering practical training and explaining key procedures and protocols in detail.
Naturally, this should be done ahead of the inventory count, with special attention given to making sure everyone involved knows how to use the inventory management software and any additional devices.
Rather than stopping at initial instructions, the coordinating team helps ensure proper follow-through throughout the end of year inventory count.
Finally, let’s touch upon why employees’ attitudes matter for a moment.
The reason you should pay attention to this is the sheer scale and time-consuming nature of end of year inventory counts.
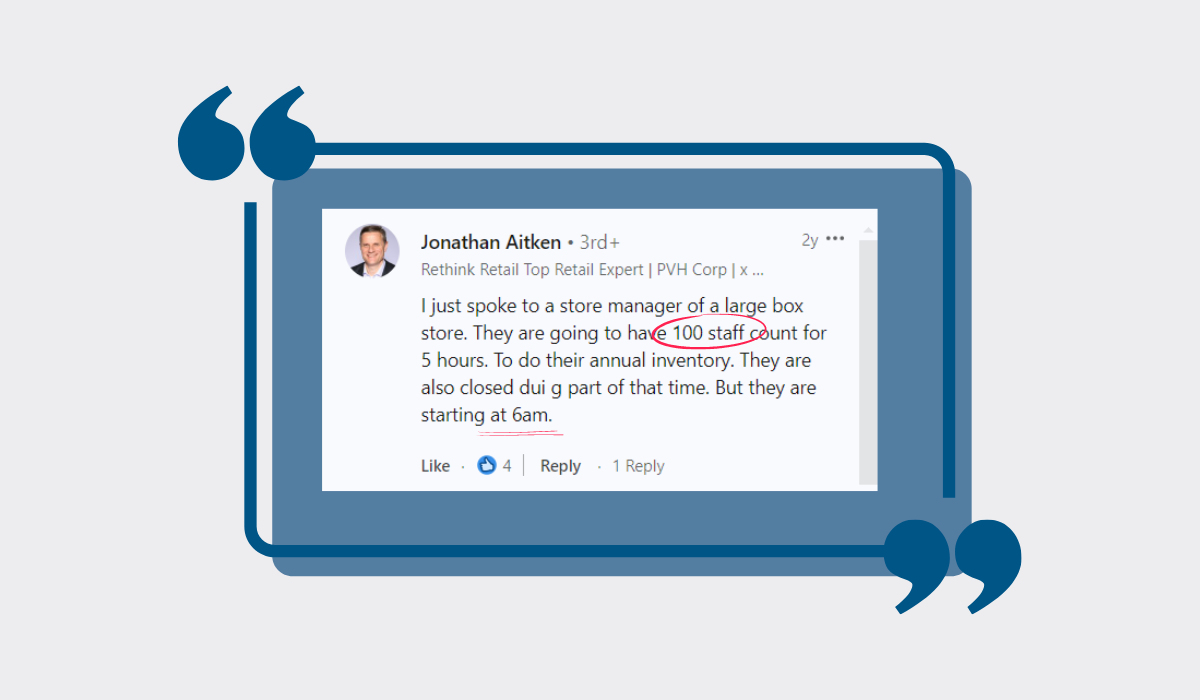
Regardless of the industry in question, inventory counts are lengthy affairs that start early and can involve quite a few employees.
It can be challenging to keep the morale up in these circumstances, but one way of doing so is to emphasize how procedures translate into positive outcomes.
Insisting on double-checking counts and verifying information at every step means reducing the chances of mistakes, and in turn, completing the process effectively and in record time.
Conduct a Post-Count Analysis
With the year-end inventory count finalized, it’s time to take a breather, right?
Well, not exactly.
The heavy lifting that the construction companies do during the inventory count is worthwhile, but the insights you can gain from the entire process are even more valuable.
Revisiting the data and conducting thorough analysis is an essential step in construction inventory management, and the same rules apply to end of year inventory counts.
Ultimately, even the most well-oiled processes benefit from a little bit of extra scrutiny and tweaking, and here’s a quick look at how this goes and what you can learn from it.
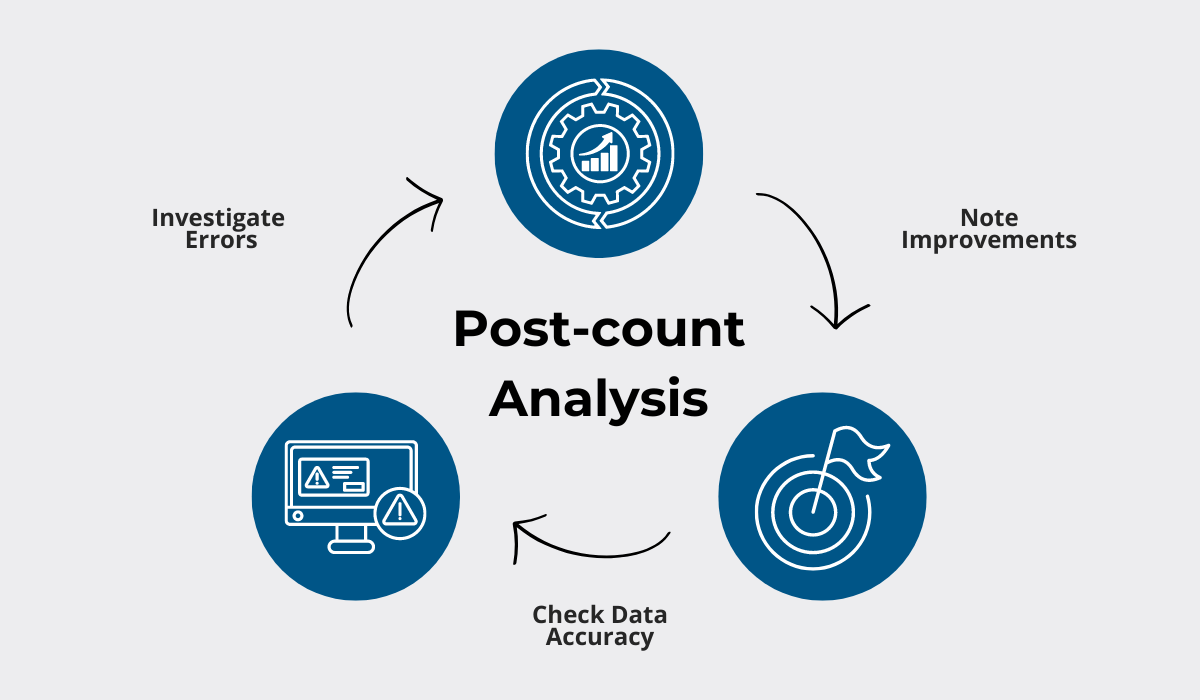
The first stage of the follow-up analysis doubles as the final accuracy check, which has two distinct purposes.
- Ensuring that the data is accurate for upcoming financial reporting and future decisions
- Making note of all errors and discrepancies
By identifying errors and understanding how they occurred, you’re gaining a fuller understanding of your overall inventory performance.
These insights form the basis for short-term corrective action, but also long-term planning.
For example, if the data indicates the location accuracy was off on several occasions, was this an issue at just one facility or across all of them?
Was it one type of asset that was frequently misplaced or different ones?
Depending on how you answer these or similar questions, your focus areas for the future will differ as well.
And remember: the data doesn’t lie, but it’s not your only source of information.
The staff members who perform the end of year inventory carry a wealth of different insights, from how the process was organized and coordinated and the specific obstacles they faced to the performance of other team members.
Taking the time to distribute quick questionnaires and gather these impressions opens up a new dimension that can help you zero in on key focus areas.
With these insights combined, you can devise the best strategies for improvement.
And seeking constant improvement means greater vigilance in responding to evolving needs and new market conditions.
Conclusion
End of year inventory counts accurately paint the present state of construction companies, while revealing critical insights for future business success.
The efficiency of the process is rooted in detailed planning and standardization of procedures and inventory categories.
If you want the best outcome, however, take the time to conduct proper staff training and introduce software solutions that make tracking and data analysis a breeze.
Embracing these best practices is sure to improve your overall inventory management, setting you up for more success in the coming year.