Key Takeaways:
- By leveraging data provided by telematics systems, fleet managers can reduce fleet maintenance costs.
- Telematics can help reduce vehicle accidents, saving money on maintenance and repairs and increasing safety.
- Telematics data helps schedule maintenance proactively to reduce vehicle downtime.
Telematics systems are most well-known for providing fleet managers with real-time data on the location, utilization, safety, and maintenance status of their construction fleet.
Through a combination of GPS tracking, internal or external vehicle and engine sensors, and fleet management software, telematics solutions are transforming how construction companies are doing maintenance.
In this article, we’ll take a closer look at how telematics can reduce fleet maintenance costs by enabling companies to take a proactive and data-driven approach to their maintenance practices.
In this article...
Helps Avoid Overly Frequent Maintenance
By continuously monitoring various parameters such as engine performance, operating hours, and fuel consumption, telematics systems enable fleet managers to implement condition-based maintenance.
In other words, they can transition from adhering to fixed maintenance intervals to dynamic maintenance scheduling based on the actual usage, condition, and performance of each individual vehicle and piece of heavy equipment in their fleet.
This approach minimizes unnecessary maintenance tasks and reduces costs associated with servicing equipment that does not require immediate attention.
To illustrate, imagine a construction company with a fleet of vehicles and machinery that decided to implement a telematics system.
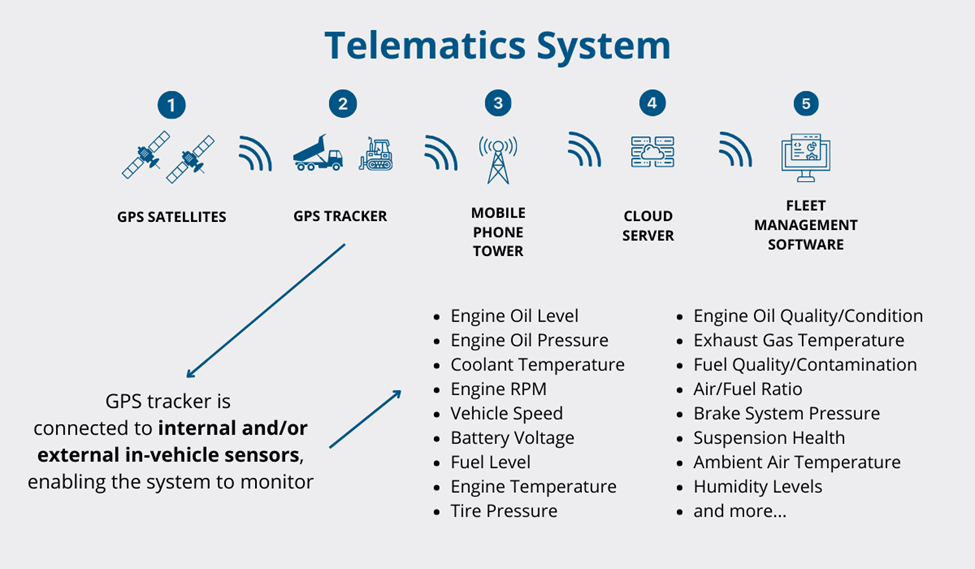
As illustrated, the key element in the above system is that the GPS tracker in each vehicle is connected to built-in (or externally installed) in-vehicle sensors, enabling fleet management software to collect and interpret a range of performance data.
In our example, the telematics system monitors not only the engine oil level and pressure (as standard internal sensors installed by the manufacturer) but also the engine oil quality (via additional aftermarket sensors for monitoring oil conditions).
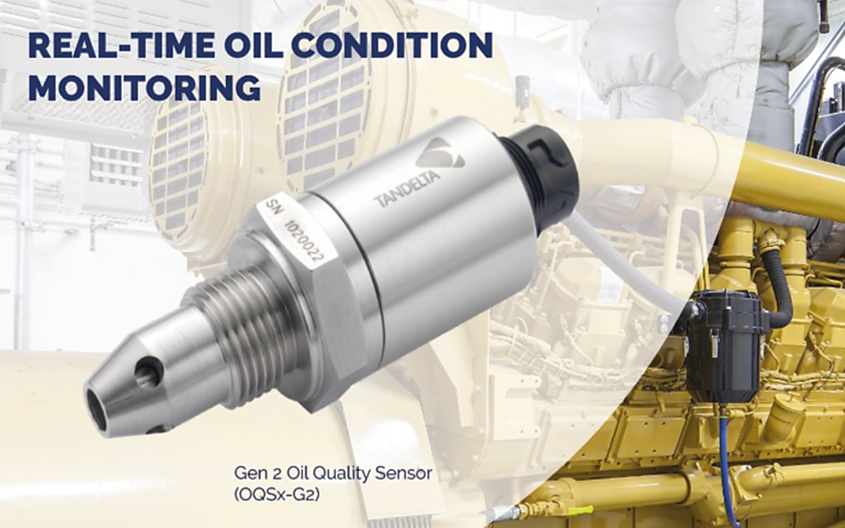
Before adopting the described telematics system, the company followed a fixed maintenance schedule for oil changes, regardless of the actual condition of the engine oil.
This approach often resulted in premature oil changes, leading to unnecessary expenses and increased downtime.
With the integration of telematics data into their maintenance program, they transitioned to a predictive maintenance strategy based on the actual condition of the engine oil.
As a result, the maintenance team was able to extend the interval between oil changes, thus reducing the frequency of maintenance tasks without compromising equipment performance or reliability.
While this example is illustrative of what telematics can do to prevent unwarranted maintenance interventions, it barely scratches the surface of the potential benefits telematics offer in construction fleet maintenance.
As explained above, telematics systems—depending on what sensors they have—can monitor a wide range of parameters, from engine temperature to battery voltage and even tire pressure.
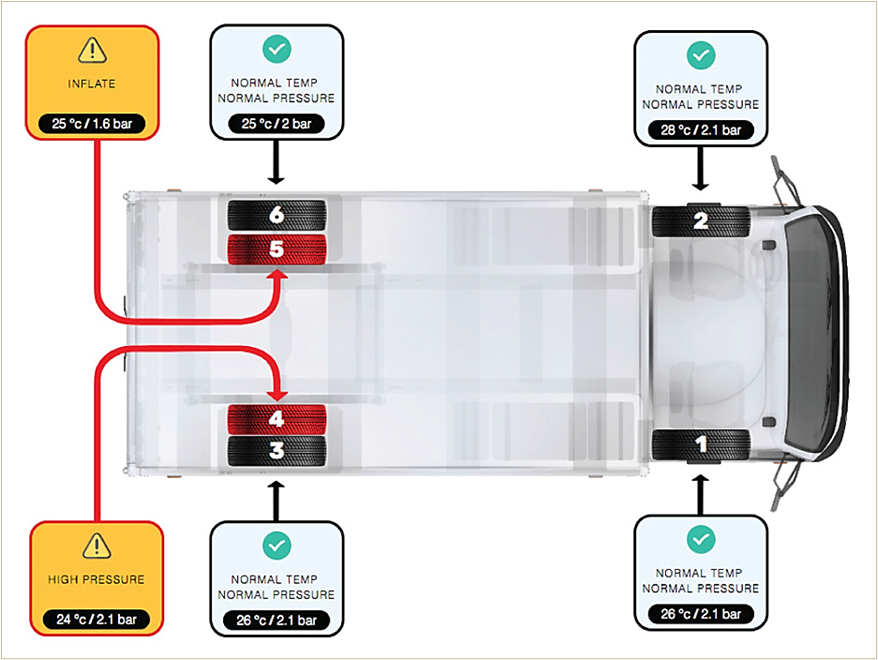
In a nutshell, the data collected by various sensors and processed by fleet management software can provide comprehensive insights into nearly every aspect of the usage, health, safety, and performance of fleet vehicles and equipment.
By leveraging this data, fleet managers can implement proactive maintenance strategies tailored to the specific needs of each vehicle or piece of equipment.
This will be most reflected in reducing the overall need for frequent maintenance caused by inefficient maintenance practices, including factors such as:
- lack of a centralized maintenance tracking system leading to missed or duplicated maintenance tasks,
- inaccurate or outdated maintenance records resulting in inefficient scheduling and resource allocation, and
- limited visibility into equipment health and usage patterns, hindering proactive maintenance planning.
Concurrently, a well-designed telematics system should provide opportunities for optimizing the sequence of performing routine maintenance tasks, thus generating cost savings.
Lastly, it’s important to note that, while telematics facilitates proactive, predictive condition-based fleet maintenance, it in no way eliminates the need for periodic inspections and regular maintenance tasks.
As we’ll see in the next section, even with telematics, certain maintenance activities may still need to be performed at predetermined intervals based on manufacturer warranty terms or regulatory requirements.
Improves Vehicle Warranty Recovery
Another important area where telematics can help involves vehicle and equipment warranties.
In essence, a telematics system empowers construction companies to optimize warranty recovery processes by:
- ensuring compliance with maintenance guidelines,
- proactively addressing maintenance needs, and
- providing robust documentation for warranty claims.
By leveraging these capabilities, companies can effectively minimize maintenance costs (covered by warranty) and maximize the value of manufacturer warranties.
One major advantage is that, when a machine under warranty is bought, all the manufacturer’s documentation, including warranty conditions, can be stored in one central, digitized system.
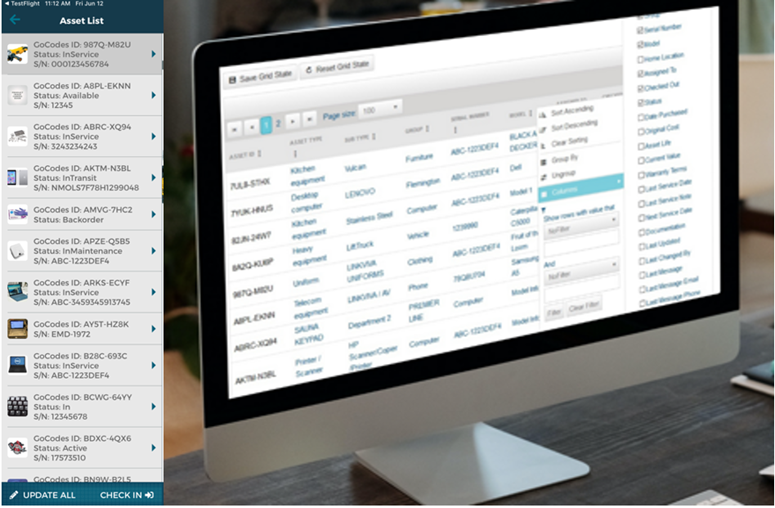
This means that, if a vehicle or piece of equipment fails, service technicians can access the cloud database of all tracked assets, and check whether the said machine, or some of its components, is still under warranty.
Additionally, this allows companies to easily verify what specific maintenance intervals and actions are required by the manufacturer for the warranty to be valid.
Take a look at the example below:
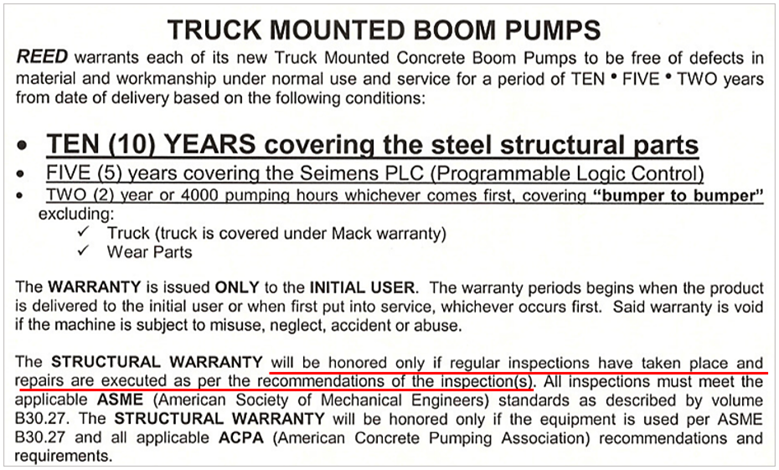
Naturally, the ability to access the manufacturer’s original instructions and warranty conditions enables companies to set their preventive maintenance programs accordingly.
This minimizes the chances of a warranty claim being denied due to maintenance practices deviating from the given warranty instructions.
Moreover, if there’s an issue concerning whether specific repairs are covered by warranty or not, the company can provide transparent data on a vehicle’s operating hours, records of previous inspections, and maintenance and repair history.
For instance, our fleet and asset management software, GoCodes Asset Tracking, can be combined with our GPS trackers (long-range tracking) or Bluetooth beacons (short-range tracking) that provide the system with real-time telematics data.
Moreover, each of those trackers will have a QR code tag that can be scanned by a smartphone or tablet to access the system and check all the asset’s details, including warranty terms, as well as inspection and maintenance notes.
You can see those details highlighted in the image below.
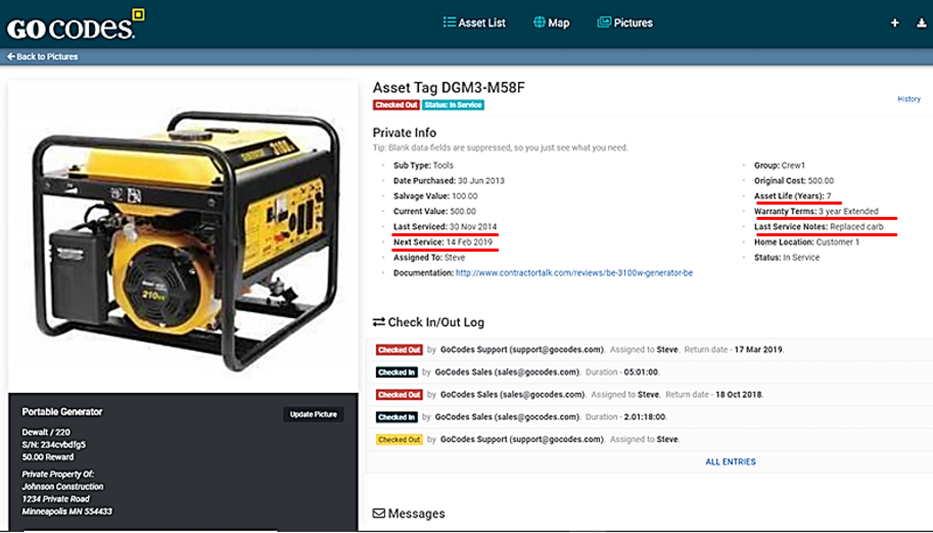
Overall, a telematics-enabled system offers a wealth of data insights that can be leveraged to ensure compliance with manufacturer warranty conditions, expedite the claims process, and increase the likelihood of successful warranty recovery.
Reduces Vehicle Accidents
Effective telematics systems can not only reduce maintenance costs stemming from on-the-job vehicle accidents.
It can also help save lives and minimize other accident-related expenses.
This is particularly true for the construction industry, where accidents often involve heavy equipment and vehicles capable of doing significant property damage, often resulting in additional costs for project delays and lost productivity.
Here’s what an average job-related vehicle accident will cost employers as estimated by the U.S. Occupational Safety and Health Administration (OSHA).
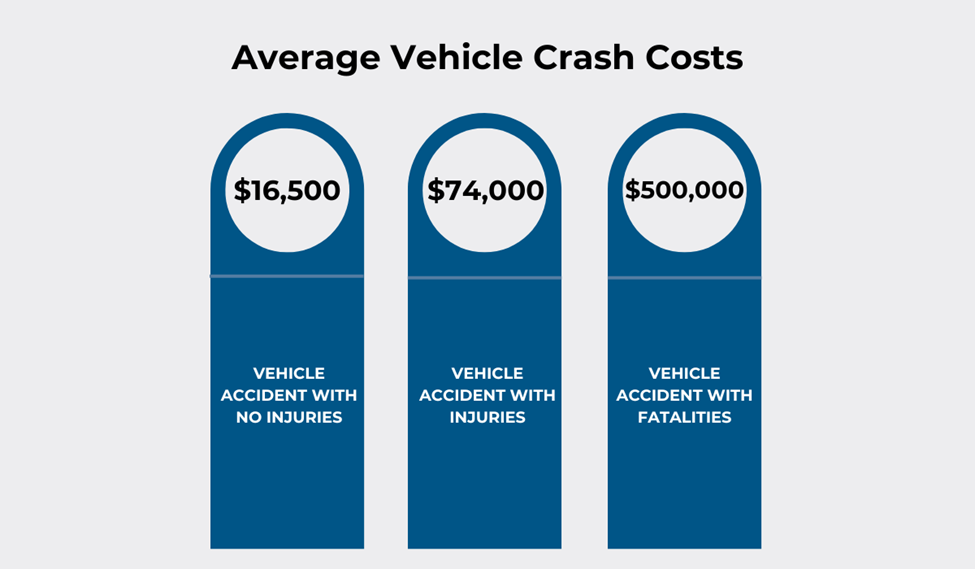
Given these exorbitant costs of any vehicle or equipment accident, it becomes clear that telematics systems play a crucial role in mitigating risks and minimizing expenses for construction companies.
As mentioned, such systems provide real-time monitoring of vehicle movements, speeds, and locations, allowing fleet managers to detect unsafe driving behaviors such as speeding, harsh braking, and abrupt maneuvers.
Therefore, fleet managers can analyze driver behavior data collected by telematics to:
- identify risky driving behaviors,
- implement driver training programs, and
- promote safe driving practices.
For example, your GPS fleet tracking system might reveal that many drivers frequently exceed the speed limit.
This not only endangers other traffic participants and increases the risk of getting speeding tickets but also increases fuel consumption and vehicle wear and tear.
Armed with these insights, your company can organize targeted training sessions focused on the importance of adhering to speed limits and the potential dangers of speeding.
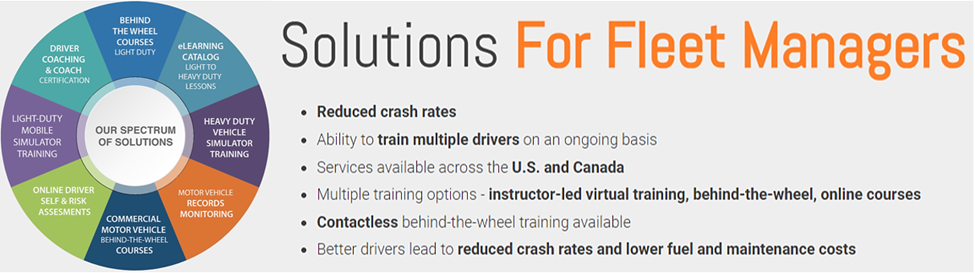
As illustrated, such training programs can include interactive modules, classroom sessions, and on-road coaching sessions to help drivers understand the impact of their behavior on safety and operational efficiency.
Additionally, a telematics-enabled fleet management solution can digitize and streamline access to—and therefore the performance of—pre-driving inspections.
More precisely, such solutions replace paper checklists with their digital counterparts that can be easily accessed and filled out by drivers on a smartphone or tablet.
This ensures that issues are caught on time and fixed before they escalate, ultimately reducing often vastly higher costs for addressing major breakdowns.
As discussed in the next section, this also helps tackle another issue, namely vehicle downtime.
To recap, by enabling you to monitor unsafe driver behaviors and take appropriate measures to address them, telematics can help you reduce vehicle accidents, thus not only saving money on maintenance and repairs but also increasing safety and potentially saving lives.
Minimizes Vehicle Downtime
We already discussed how telematics allows you to reduce vehicle wear and tear through optimized routing and improved monitoring of vehicle performance and driver behavior.
These telematics-enabled features then also translate into minimized vehicle downtime.
In addition to real-time insights into vehicle health and driving habits, telematics also facilitates proactive maintenance scheduling and streamlined spare parts inventory.
For instance, by analyzing historical data on vehicle usage and performance, fleet managers can forecast when regular maintenance will be required and what components should be serviced or replaced.
Then, they can utilize fleet management software to set up scheduled maintenance tasks, assign them to specific service crews or technicians, and specify exactly what needs to be done.
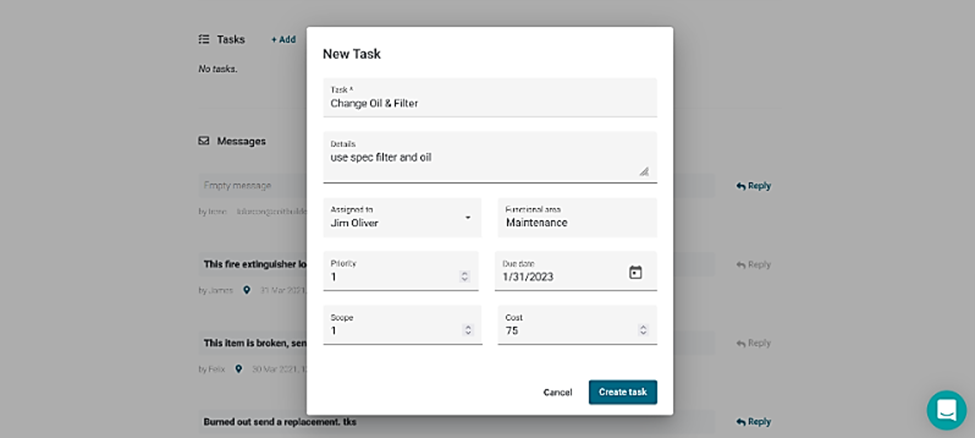
When routine maintenance tasks are cross-referenced with project schedules and planned resource allocation, this ensures that maintenance tasks are conducted at the most opportune times to minimize disruption to operations.
Because technicians are timely notified of upcoming servicing tasks, they can leverage the fleet management system’s inventory tracking feature to ensure they have all the spare parts and other supplies needed for maintenance.
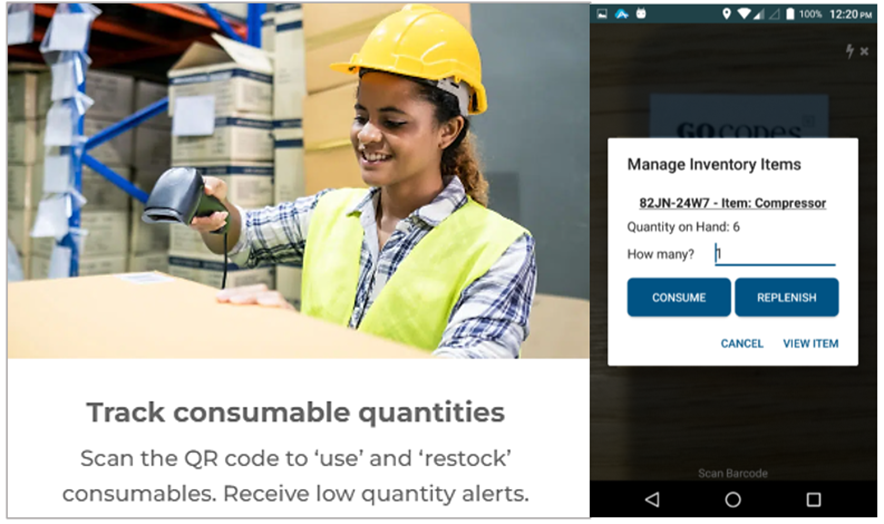
As illustrated above, fleet managers can monitor stock levels in real-time, thereby ensuring that spare parts are readily available when needed and eliminating delays caused by waiting for parts to be sourced or delivered.
Moreover, some software solutions allow managers to set up automatic reminders that the assigned technicians will receive in the early morning of the scheduled maintenance day, ensuring no maintenance tasks are overlooked.
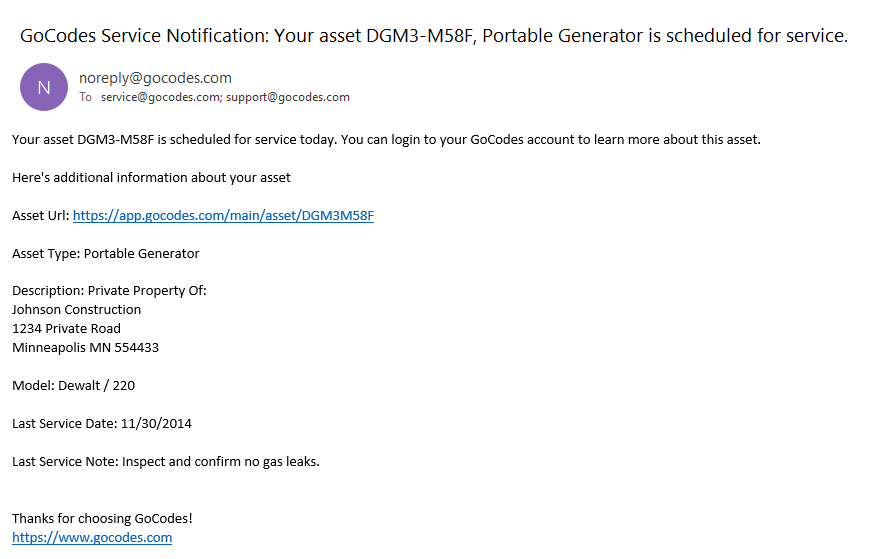
In summary, telematics provides a wealth of real-time data that can be leveraged to monitor vehicle and driver performance and catch issues early, therefore minimizing vehicle downtime.
Furthermore, telematics data enables managers to schedule maintenance proactively and optimize spare parts management, which can also significantly reduce vehicle downtime, minimize maintenance costs, and maximize fleet utilization and productivity.
Conclusion
So, we’ll use this closing to reiterate that construction companies can leverage real-time data insights provided by telematics (GPS trackers, sensors, and fleet management software) to transform, automate, and optimize their fleet management practices.
We’ve described how telematics can help reduce excessive maintenance costs without risking under-maintenance, improve warranty recoveries, enhance driver safety, reduce accidents, and minimize vehicle downtime.
We should add that telematics, namely GPS trackers, also play a significant role in preventing theft and detecting unauthorized use.
Given all the above, embracing telematics-based solutions is quickly turning from a choice to a strategic imperative for forward-thinking construction companies seeking to thrive in a competitive landscape.