As a construction company grows, it usually acquires more and more fixed assets like heavy machinery, vehicles, equipment, tools, and facilities needed to perform day-to-day operations and generate revenue.
Naturally, these long-term assets require continuous monitoring and management across their lifecycle to ensure they bolster profitability rather than drain resources.
This is where the significance of proper fixed asset management becomes evident.
In this article, we’ll explore four compelling reasons why efficient fixed asset management is paramount for construction companies and how they can achieve it.
In this article...
Streamlines Fixed Asset Acquisition
Before diving into how a robust asset management system helps contractors decide when to acquire construction equipment and other assets, let’s first clarify what a fixed asset is.
Among many available definitions, let’s use the one by Investopedia:
The term fixed asset refers to a long-term tangible piece of property or equipment that a firm owns and uses in its operations to generate income.
Once acquired by a company, these assets are expected to be used for at least one year, and often considerably longer (e.g., 3, 5, 7, 9, 10, 15 years and beyond).
For construction companies, such long-lived assets typically include heavy machinery, vehicles, equipment, tools, and other items like IT equipment and office furniture, as well as real estate (land, buildings, infrastructure).
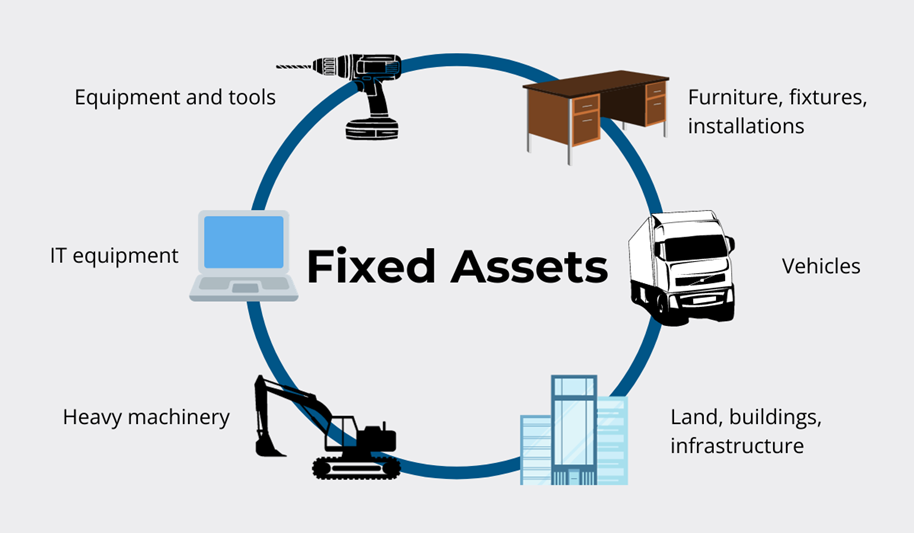
Except for land, when a construction company acquires one of the above-fixed assets, the Internal Revenue Service (IRS) prescribes that the purchase cost of an asset, say a bulldozer, can’t be written off for tax purposes all at once.
Instead, the acquisition cost should be spread over the asset’s estimated useful life, for example, 5 or 7 years for the said dozer, depending on the IRS rules and other factors like usage intensity, maintenance, and technological advancements.
This process of spreading the cost of a fixed asset over its estimated useful life is referred to as depreciation, as this definition explains:
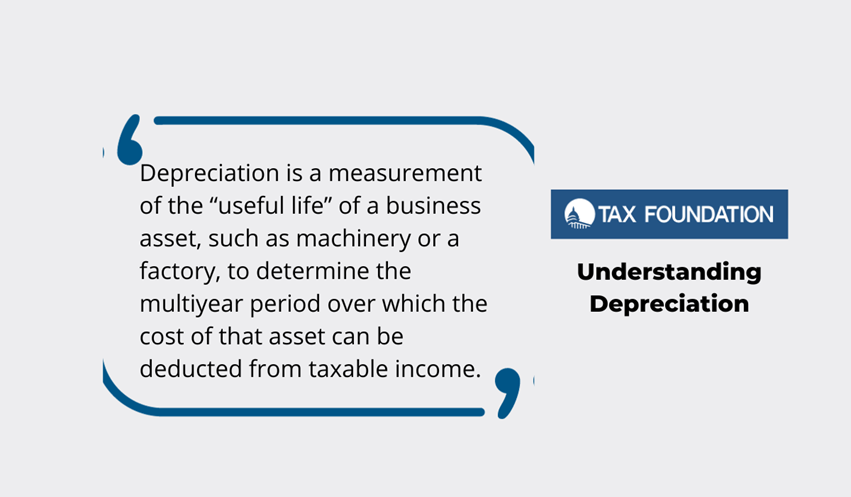
As such, depreciation plays a vital role in ensuring that companies accurately report the value of fixed assets, thereby ensuring transparency, reliability, and—as discussed later—regulatory compliance of their business ledgers and financial statements.
Likewise, fixed asset depreciation offers tax benefits, allowing companies to claim deductions and reduce annual tax liabilities according to their financial needs and goals.
Beyond these significant accounting and tax implications, understanding depreciation empowers construction companies to make better-informed decisions about the acquisition and lifecycle management of their assets.
For instance, a company may plan when to budget funds for a new bulldozer based on when the current one’s useful life will run out.
Moreover, by tracking depreciation and considering other factors like maintenance costs, usage patterns, and technological obsolescence, that company can ascertain whether it’s more cost-efficient to repair or replace equipment.
For example, let’s say that a bulldozer used for four out of five years of its estimated useful life suffered a major breakdown or accident.
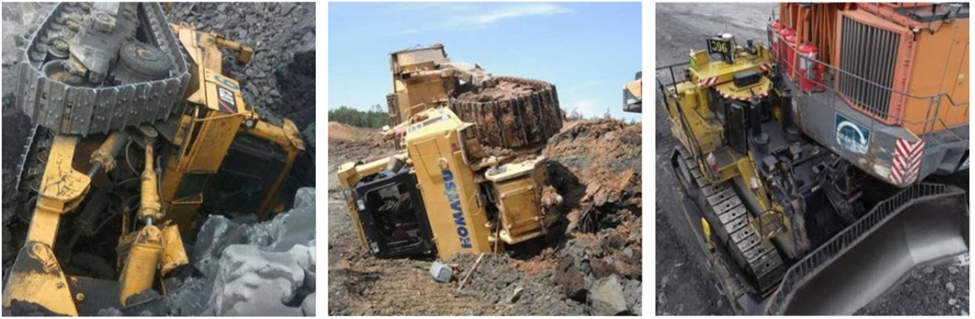
In such cases, it might be prudent to skip expensive repairs and move to acquiring a new model, especially considering that modern machinery usually provides improved performance and fuel efficiency due to technological progress.
Given the above considerations, it becomes critical for construction companies to have a robust asset management system in place to accurately track asset depreciation and lifecycle management data.
Such a system, preferably digitized, automated, and cloud-based, allows company owners and managers to streamline the process of fixed asset acquisition through informed, data-driven decision-making, and improved planning and budgeting.
As we’ll see, it also enables them to efficiently track fixed assets, reduce unplanned downtime, and facilitate regulatory compliance, all of which contribute to the company’s productivity and profitability.
Enables Fixed Asset Tracking
Having an efficient fixed asset management system extends beyond keeping track of relevant asset management data to tracking the actual location of assets as they move across different construction sites.
This is crucial because most construction assets, like heavy machinery, vehicles, equipment, and tools, are in constant motion, shifting from one project to another.
Knowing where these assets are at any given moment is critical for various reasons, including improved operational efficiency and minimized asset theft and loss.
More specifically, here are seven key benefits of fixed asset tracking:
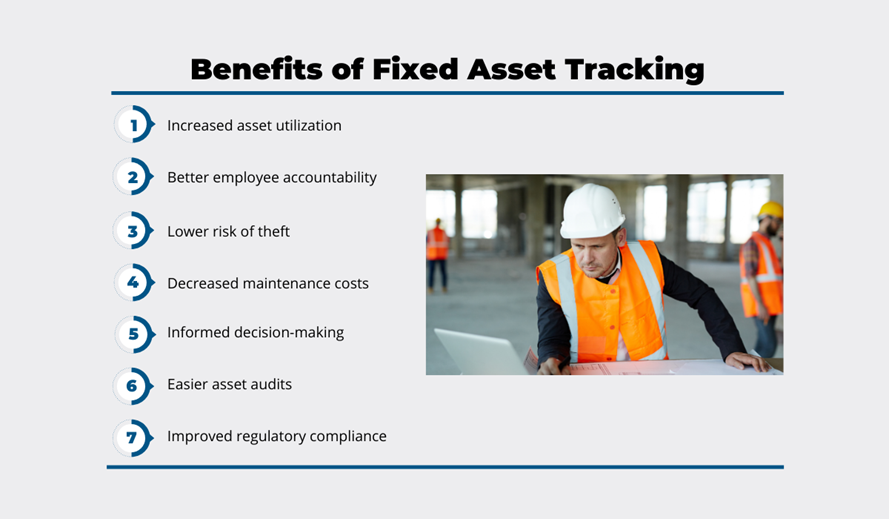
These benefits largely arise from being able to track who is currently using a piece of equipment and at what location.
So, how can construction companies track the whereabouts of their assets?
What typically first comes to mind is GPS tracking, where assets are equipped with trackers used to monitor their movement via satellites anywhere in the world.
However, while this method is great for real-time tracking of vehicles and heavy equipment, GPS trackers are often too expensive to be fitted on all fixed assets that should be tracked.
Alternative asset-tracking methods include remote detection of assets within a limited area, for example by using RFID trackers or Bluetooth beacons.
These technologies are often combined with the simplest and most affordable tracking method, namely barcode or QR code tags attached to assets.
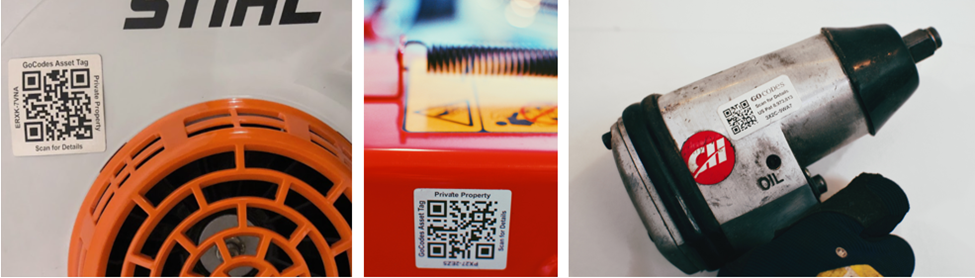
Compared to other asset-tracking technologies, such asset tags are much cheaper to produce and easier to install.
That’s why most GPS and Bluetooth trackers will also have a barcode/QR code attached to them for asset identification and data-recording purposes.
So, how do asset tags/labels enable contractors to track asset locations?
It’s simple: when an asset tag is scanned with a smartphone or tablet, cloud-based tracking software will use the scanning device’s GPS function to automatically record the asset’s current location.
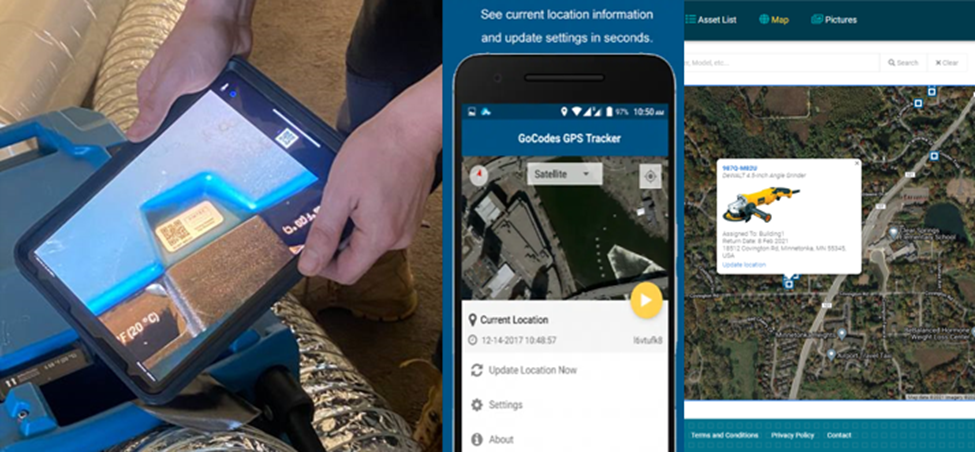
While this simple method will not provide real-time location updates like active GPS trackers, it will allow users to see where the asset was last scanned, which can help in finding misplaced or stolen equipment.
Coupled with tracking asset users via the software’s check-in/check-out function, such an asset management system can generate all the above-listed benefits, like increased employee accountability and reduced asset loss and theft.
A great example of such asset-tracking software is our solution, GoCodes.
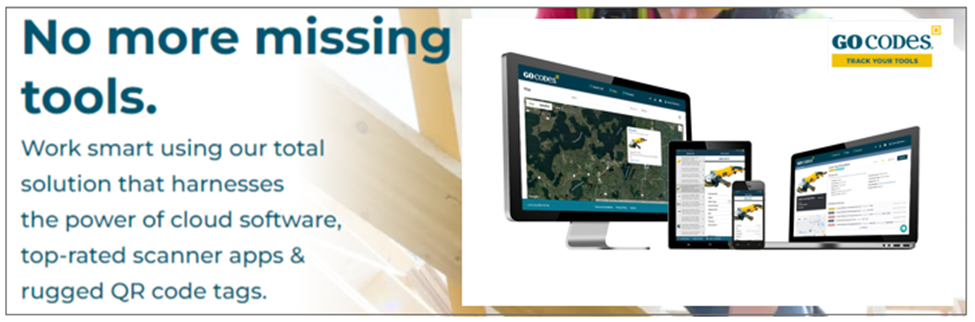
Maybe the biggest advantage of GoCodes is that you don’t need to purchase any hardware like dedicated tag scanners, which makes this solution affordable, as well as easy to install and use.
In other words, you can install GoCodes on devices your company and/or your employees already use, thus turning their smartphones and tablets into QR code scanners.
At the same time, users can access the cloud software on any other internet-connected device, such as desktops and laptops, where they can log into the central database of all tracked assets to view and update different asset management data.
To recap, an automated asset management system should enable you to track all the relevant asset data, including asset locations and users, thus helping you maximize asset security and utilization.
Reduces Unplanned Downtime
Another important benefit of proper fixed asset management is that it helps you reduce unplanned labor and equipment downtime in many different ways.
Naturally, with tight project budgets and even tighter deadlines, unexpected disruptions can be costly in terms of both time and resources.
For instance, if a critical piece of machinery breaks down on-site, this causes immediate work stoppage of that equipment, its operator, and all other workers involved in that construction task.
Moreover, identifying the problem, ordering the right parts, and scheduling repairs can take an extensive amount of time, leading to prolonged downtime for repairs or while you rent or purchase a suitable replacement.
However, with an asset management system relying on scannable asset tags, all these processes are accelerated and streamlined.
When an issue arises, on-site personnel can scan the QR code on the affected piece of equipment and use the mobile app to report the problem and request maintenance, which can prevent more serious breakdowns.
Likewise, the assigned service technician can access the equipment’s info page to review its maintenance and repair history and other relevant data.
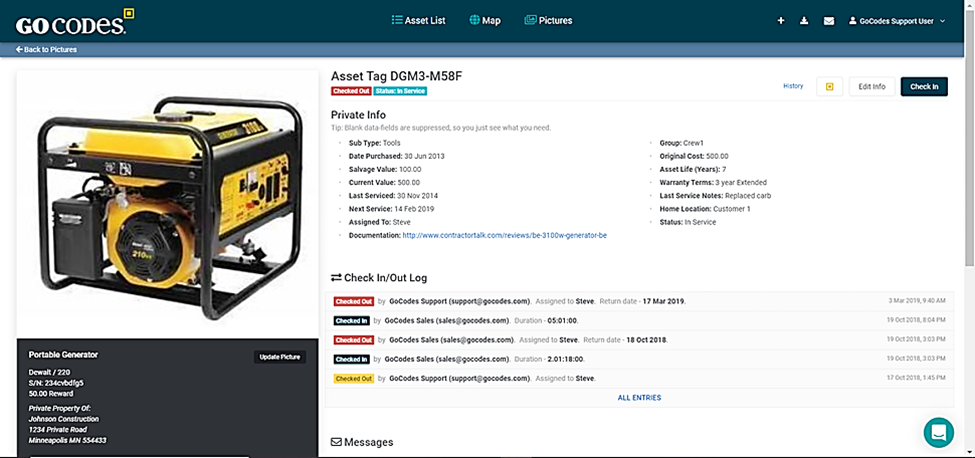
This immediate access to information facilitates quicker problem diagnosis, streamlined procurement of necessary parts, and faster repairs.
Moreover, this system goes beyond reactive measures by allowing construction companies to schedule regular maintenance and set up automated service alerts.
In other words, managers can establish a preventive maintenance schedule for a piece of equipment, assign the responsible service team or technician, and instruct the software to send an email reminder at a specific date and time to notify all involved.
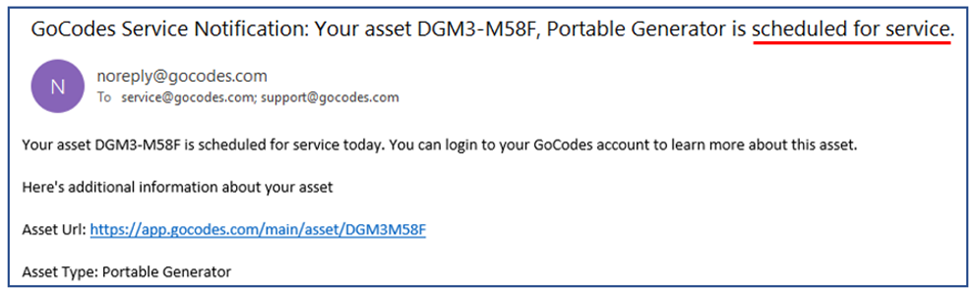
This ensures your equipment remains well-maintained, thereby preventing issues that could lead to unplanned downtime.
Furthermore, workers typically spend valuable time searching for tools and equipment, and asset management software transforms this scenario.
When a worker needs a specific tool, they can access the central asset database on their smartphone, find the asset they’re looking for, and view its availability and location in real-time.
Naturally, this reduces labor downtime and increases overall operational efficiency.
To sum up, by leveraging a cloud-based asset management system, construction companies can significantly reduce the impact of unplanned equipment and labor downtime.
Facilitates Regulatory Compliance
Since the one key requirement for regulatory compliance in asset management is accurate record-keeping, a robust asset management system can help construction companies navigate complex regulatory landscapes with ease.
We already mentioned how such software facilitates a business’s compliance with financial reporting standards by enabling accountants to calculate and track asset depreciation, ensuring that financial statements accurately reflect the value of fixed assets.
Likewise, having a single database where all relevant data is stored, including detailed logs of equipment usage, maintenance history, and compliance-related documentation, ensures quick and easy access during internal or external audits or inspections.
This is particularly useful because the construction industry is subject to stringent safety regulations governing the operation and maintenance of heavy machinery.
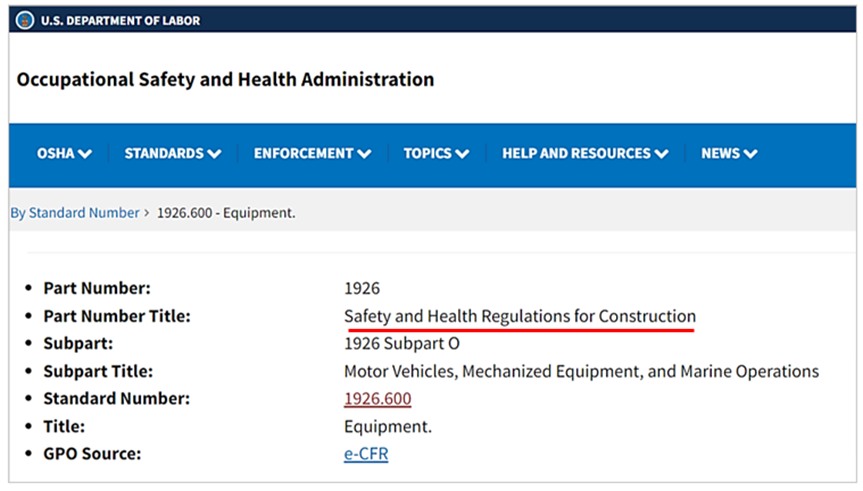
An asset management system with a comprehensive database allows companies to promptly retrieve records on maintenance, safety inspections and certifications, and other documentation that might be required by external regulatory bodies.
This not only ensures adherence to safety standards but also expedites the regulatory review process.
Furthermore, compliance often involves observing specific reporting timelines.
Asset management software equipped with automated reporting features helps construction companies stay ahead of regulatory deadlines.
For example, when making annual depreciation adjustments for end-year financial statements, accountants can easily generate depreciation reports aligned with IRS rules, ensuring compliance with tax regulations.
In summary, a fixed asset management system facilitates regulatory compliance by recording, organizing, and automating documentation while also contributing to proactively meeting safety and reporting standards.
Conclusion
Having explored these four reasons why fixed asset management is important, it can be said all of them can be achieved by using a single digital, automated, and cloud-based system.
In other words, such a system streamlines the entire lifecycle of fixed assets, from acquisition to disposal, enables tracking of equipment and tools, reduces unplanned downtime, and facilitates regulatory compliance.
By leveraging it, your company can realize multiple efficiency gains and cost savings, enabling it to stay competitive in the constantly changing construction landscape.