The last decade has seen a rapid acceleration in the global shift towards a digitized economy. Every industry has been affected by it, construction included.
Today, construction companies have no choice but to adapt to contemporary business practices.
One of the most prevailing is the implementation of electronic or web-based asset tracking systems, which significantly improve workplace efficiency and increase productivity across the board.
For those that still need convincing, this article presents five notable reasons why businesses need fixed asset tracking software.
These should help anyone looking into the subject to make up their mind, whichever direction they end up going in.
To begin, let’s look at how asset tracking facilitates eliminating so-called “ghost assets.”
In this article...
Eliminates Ghost Assets
As their name suggests, ghost assets are fixed assets that are missing or unusable, but continue to haunt your accounting books.
Unlike “real” ghosts, these are actually quite a common occurrence, and can do real damage to your business.
In fact, the peculiar thing about ghost assets is not their existence. A survey from Wasp Barcode Technologies revealed that half of small business owners don’t even know what they are.
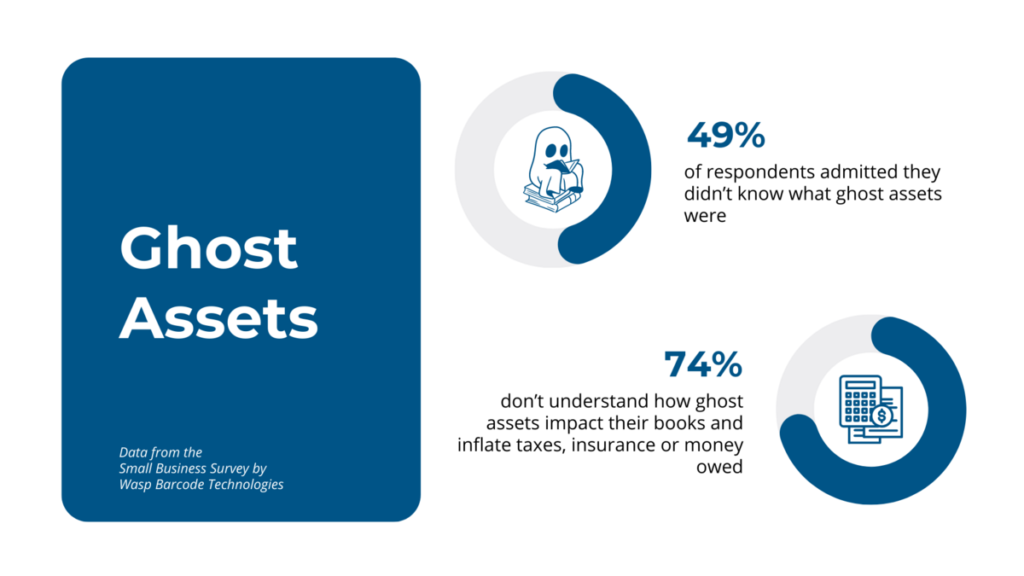
As shown above, the same study revealed that 74% of around 400 respondents weren’t aware of the negative impact ghost assets have on their finances.
What are those negative impacts?
Well, seeing as ghost assets are present in your fixed asset inventory, they fall under the same accounting rules as regular assets.
That means they are subject to taxes, maintenance fees, insurance premiums and other similar expenses.
Of course, one or two ghost assets will hardly be a problem, given the amount of equipment construction companies usually have.
However, a white paper from Klear Systems shows that around 10% to 30% of fixed assets on the books of any given company are no longer owned in reality.
This is a major issue, since even as little as 12% of ghost assets can cause significant overtaxation, as illustrated in the same paper:
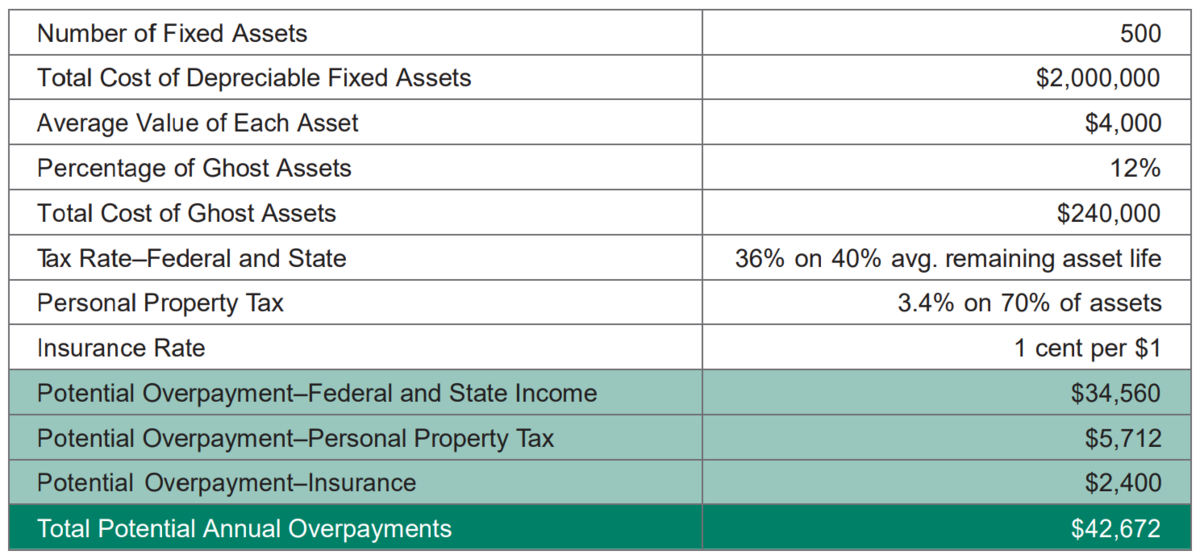
Fortunately, these costs can easily be avoided by using asset tracking software.
A fixed asset tracking system allows you to create a centralized database with accurate, up-to-date data on all of your tools and equipment.
The database is updated with new information—e.g., concerning an item’s location, condition and user—every time an asset tag is scanned with a smartphone or a reader.
This way, you have a comprehensive overview of your assets, which enables you to easily spot those that are not in use and take steps to validate its presence or eliminate it from the books.
Furthermore, fixed asset tracking software also facilitates inventory audits. These normally require manually going over every asset and verifying their information against a pre-made list.
With fixed asset tracking, audits are as simple as walking around the warehouse, pointing a smartphone at tags and clicking on a button.
Because this is a much less time- and energy-consuming method, it gives businesses an opportunity to do audits more often.
Therefore, decision-makers will have a greater chance of identifying ghost assets and rectifying their books in a timely manner.
Overall, ghost assets are invisible, yet costly entities doing damage to your company.
To eliminate them, you can use asset tracking software, which provides an all-encompassing inventory overview, as well as much simpler audit procedures.
Increases Asset Utilization
Identifying the missing or unusable assets is important, but it is as vital for companies to ensure their existing assets are used to their full potential.
Otherwise, they are losing out on the potential value their assets can provide to the business.
A metric for measuring the usage rates of tools and equipment is called asset utilization rate. It can be calculated by the following formula:
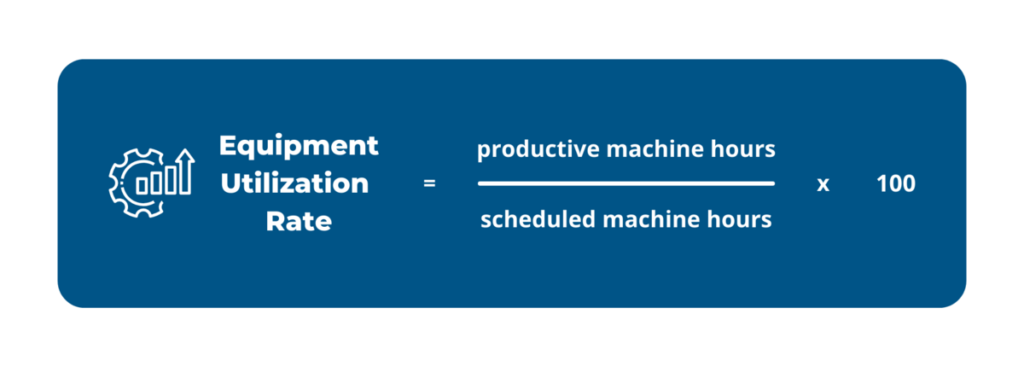
Productive machine hours (PMH) are the duration for which equipment is used for work-related tasks.
Scheduled machine hours (SMC) are the maximum amount of time equipment can be used for those tasks, not including planned downtime, such as for maintenance or rest periods.
Therefore, for an asset available for work for, let’s say, 50 hours a week, and is utilized for 30 hours, an asset utilization rate would be 60%.
Now, how can fixed asset tracking software rise to the challenge of improving that percentage?
Again, it mostly comes down to data access.
With an asset tracking system, businesses gain insight into different metrics that can help them deduct accurate PMH and SMC.
For example, they will know exactly how much time an asset has been used, how many hours it spends in maintenance, how much rest time it has, etc.
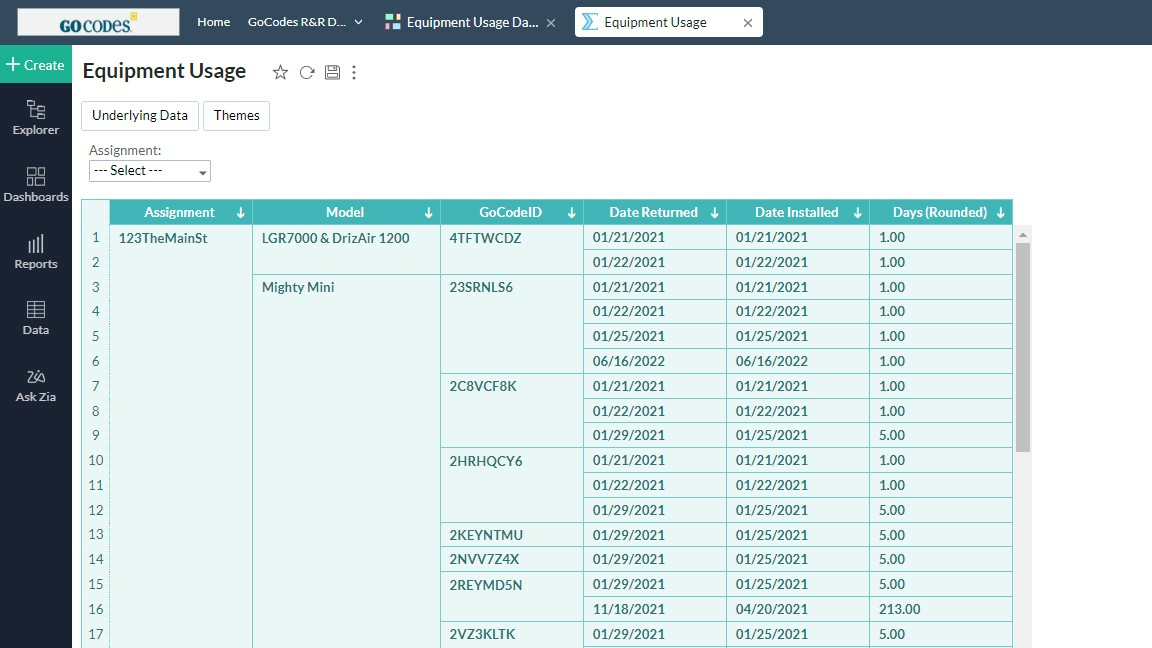
With a correct utilization percentage for each piece or category of equipment, it is much easier to create efficient usage and maintenance schedules.
For example, let’s say you have two excavators, one with 40% and another with 80% utilization.
To avoid overworking the second one, you can make both work 60% of the time.
Another solution is to replace the lesser-used excavator with an adequately smaller one, allowing for it to be placed on a job where it can be used at greater capacity.
This is where it’s useful to have location- and usage-tracking abilities, both of which can be found in many fixed asset tracking software.
Knowing where assets are being underutilized, as well as who may be responsible for it, allows businesses to reallocate equipment to different users or construction sites which are most in need of those particular pieces.
Ultimately, asset tracking gives companies a full picture of how much, where, how, and by whom the equipment is used, allowing them to increase asset utilization by creating better-arranged schedules and more efficient allocation.
Ensures Proper Maintenance
There is a term mentioned in both previous sections which is of utmost importance to construction equipment management, and that is maintenance.
Construction businesses completely depend on their tools, machinery and vehicles to perform an overwhelming majority of their project-related tasks.
It’s hard enough to hammer a nail without a hammer, let alone building a house or laying down a road without excavators or pavers.
Therefore, to perform their jobs to the best of their abilities, construction companies need to ensure their equipment is properly and regularly maintained.
For that to be achieved, maintenance shouldn’t be limited only to repairs after a breakdown occurs.
Such an approach can be costly, as damage can spread to more than the original problematic part, often requiring replacement parts and plenty of time to fix.
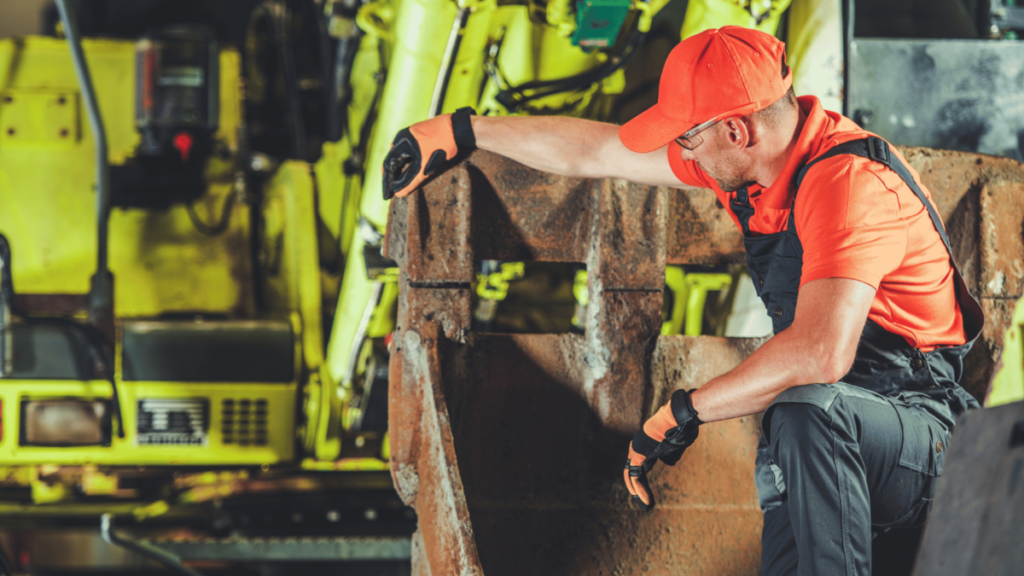
It is much more efficient to develop proper preventive maintenance practices, which is much easier to do with fixed asset tracking software.
Firstly, it provides construction companies with each asset’s maintenance history, usage and condition, as well as performance stats.
This data can be used to determine how often assets need maintenance, enabling businesses to create optimal repair schedules and adapt them along the way if needed.
Secondly, asset tracking software enables companies to put those maintenance schedules into practice.
Every asset should have an accompanying profile page, where you can assign tasks such as work orders for maintenance.
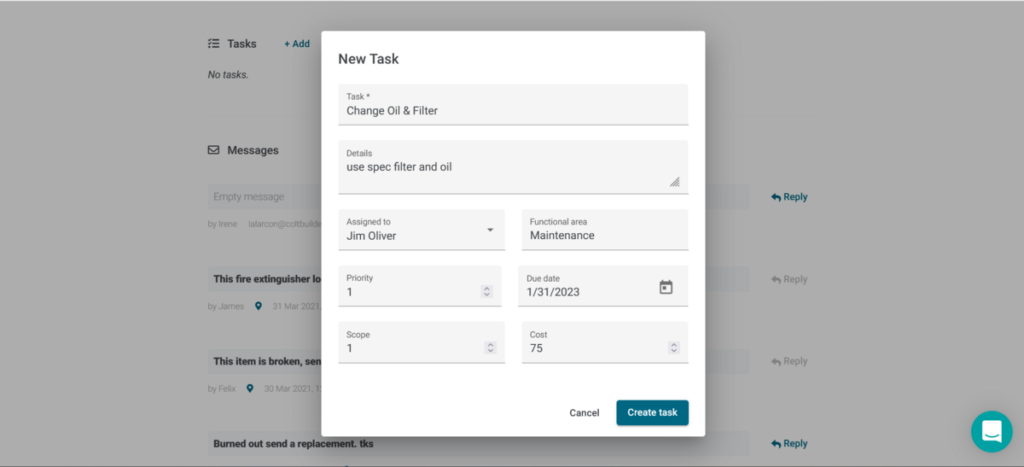
As seen in the example above, task management is an extremely useful feature as it goes a long way in helping to fairly distribute maintenance work across assets.
This way, you can ensure each one gets the proper care it needs while avoiding over- or under-working the maintenance department.
And lastly, most platforms specialized in tracking assets include alerts or notifications.
These can usually be set to trigger after a particular event, such as low inventory item quantity or overdue assets.
In a lot of cases, those events include upcoming maintenance.
With this option enabled, specified members of the team will receive notifications about all scheduled service details a day before or in the morning before work starts.
All in all, with timely alerts, access to data for proper maintenance planning, and task scheduling capabilities fixed asset tracking solutions provide, you can rest assured that your company’s equipment stays in its optimal working condition.
Lowers Risk of Theft
Another crucial area asset tracking software can be applied to is theft prevention and stolen asset recovery.
Why is this important?
Because construction equipment theft rates are unusually high compared to other industries.
According to research from East Tenessee State University, these are the most significant contributing factors:

With these in mind, it’s no wonder you can easily find news stories about construction theft across the country.
For example, just earlier this year, Fox News reported on a man from Carolina who single handedly stole $300,000 worth “of Takeuchi excavators, skid steers and various trailers.”
To make things worse, this is actually a rare outcome, as only a small amount of stolen equipment eventually gets recovered.
Having construction companies as one of our top clients, GoCodes developed an asset tracking system with location tracking features that facilitate theft prevention and stolen property recovery.
The first one comes with the standard QR code tracking system.
Here, scanning QR code asset labels with a smartphone reveals pertinent information about the asset in question, like its identity, maintenance and usage history, etc.
Additionally, because scanning requires proximity to the tag, employees can use the GPS location of the smartphone they use for scanning as that of the scanned asset and update the information accordingly.
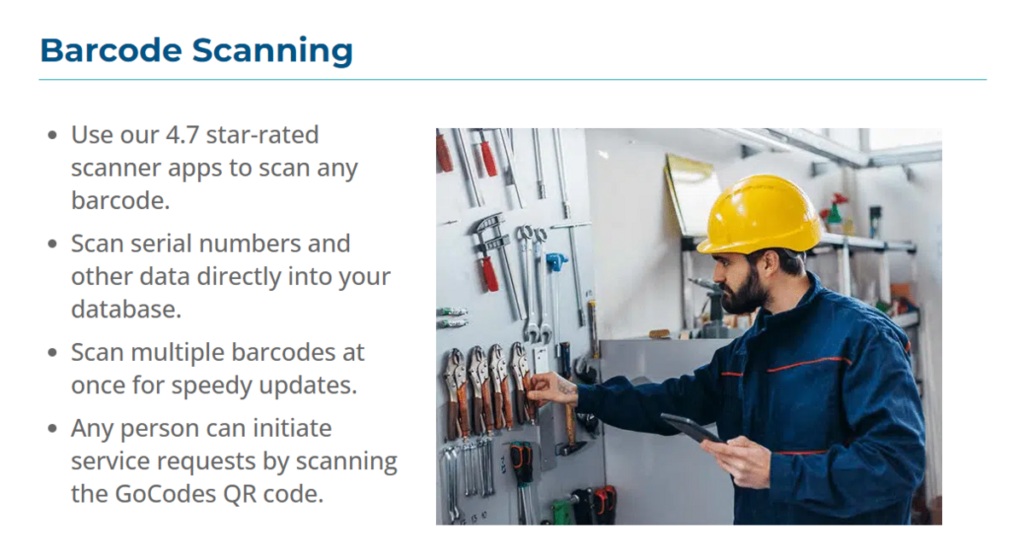
When a piece of equipment goes missing, this will allow you to have information on its last known location, time and user, narrowing down the timeframe and suspect list for the police investigation.
After all, the more information they have on the stolen equipment, the easier it will be for them to find it.
For this reason, other information available in the asset register, like serial numbers, photographs, notes and descriptions, can also be of significant use.
However, for full real-time location tracking, businesses need a solution like GoCodes’ Bluetooth Beacons.
Compact in size, affordable and long-lasting, these low-energy trackers use radio waves to communicate their location to Bluetooth-enabled devices, such as laptops or smartphones.
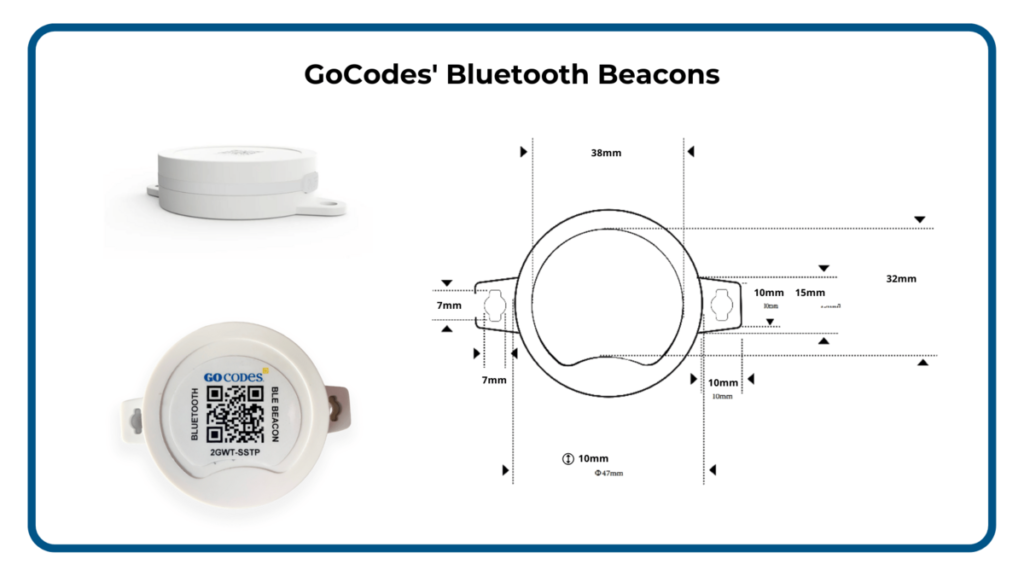
This way, companies can have a real-time overview of all assets in the range of the reader, which is around 300 feet in radius.
In addition, GoCodes’ Guardian App can send alerts whenever an asset/beacon is removed from the app’s range.
Upon receiving the notification, you can promptly react, greatly increasing the chance of recovery and discouraging criminals from making future attempts on your site.
In summary, fixed asset tracking software with location tracking capabilities can help construction businesses protect their equipment from robbery, as well as access and provide pertinent information for more efficient police investigations.
Improved Decision-Making
The final reason you need asset tracking software to be discussed in this article is improved decision-making.
If that sounds vague, it is only so because it can be applied to the entire asset life cycle, instead of only one area.
The life cycle is usually understood to consist of six stages:
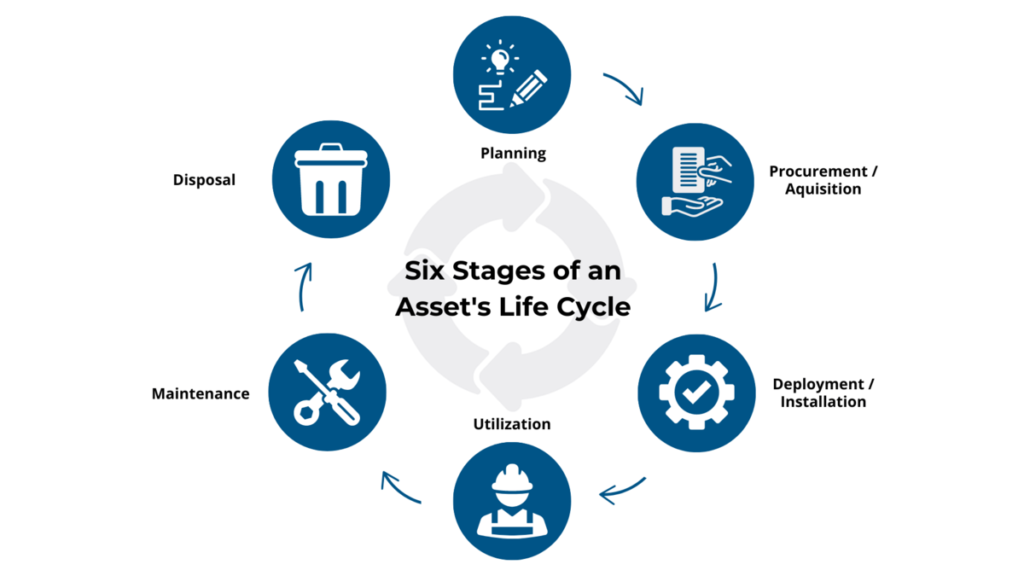
Businesses can use the data procured from their asset registers to gain actionable insight related to each one of these phases.
This way, they can decide on what assets to purchase and when and how to use them, as well as when to repair or replace them.
The data is usually analyzed with the help of the report feature.
In most cases, asset tracking software allows you to add any number of custom data fields to your asset database.
Reports allow you to use those data points to analyze your assets in a number of different ways.
For example, you can single out all assets of a given type, or purchased after a given date, or used in a particular location.
When you define the scope of the report, you can choose the numbers you need to crunch, such as depreciation rates, overall values, or maintenance frequencies.

Moreover, as seen above, businesses can use various visualization methods—graphs, charts, bars, etc.— to more easily share the findings with the management team or inquiring clients.
Some tracking software even has the ability to generate dynamic reports.
Basically, a report with given parameters is assigned a web URL. This URL is used to host the report, which updates in real-time, saving you time for ones that need checking on a daily or weekly basis.
In essence, fixed asset software provides construction companies with data, as well as methods to utilize said data to make better-informed decisions, therefore leading to an overall more successful business.
Conclusion
In conclusion, it’s important to mention that these reasons are not exhaustive by any means.
For those truly interested in fixed asset tracking software, it is advisable they go through other resources on the subject exploring the benefits, and the drawbacks, of using this system.
In the end, you’ll hopefully come to a decision and find the right asset tracking solution, equipping your business with tools for better operational efficiency, proper maintenance strategy, greater security, and a prolonged life cycle.