Tracking construction tools and equipment can save your company a great deal of money and eliminate frustrating searches for lost or stolen items.
Making the most of tool tracking involves creating an accurate tool inventory, choosing the right asset tracking solution, and determining which tools to track.
Other essential tool tracking tips include assigning unique identifiers to each item, enabling check-in and check-out, and making the decision to track new tools immediately.
In this article, we cover all of those practices, so let’s dive in!
In this article...
Create an Accurate Tool Inventory List
It is essential to create an accurate tools inventory list in order to track all of your assets adequately.
However, this can be difficult to do when tools are constantly in use and scattered across multiple construction sites, changing hands between employees several times a day.
Project managers should consider including each separate site when building the list.
Inventory processes used to be conducted by hand and with electronic spreadsheets.
This cumbersome procedure included distributing and then collecting hand-filled spreadsheets containing information about each piece of equipment.
These were then imported into an inventory system.
Obviously, the process was time-consuming and prone to many errors. It was also poorly secured, expensive to maintain, and difficult to protect and store.
This form of information maintenance also limited the ability of employees to access it as necessary, and if the records were damaged or destroyed, they were lost forever.
Modern asset tracking can avoid all of these problems.
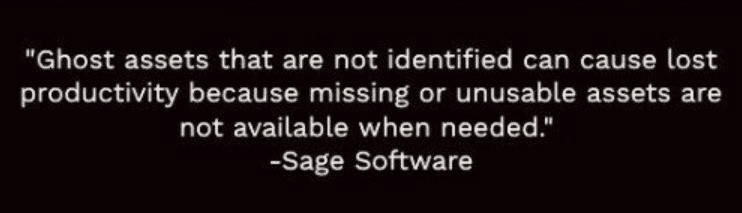
One way to build an accurate inventory list is to avoid ghost assets.
These are items that are present in either handwritten sheets, a computing system, or the cloud, but are either missing or unusable.
For example, if your company owns a cement truck, but it is out of service and too expensive to repair, keeping it on the books can result in higher insurance costs and taxes, as well as budgeting problems.
Beginning tool tracking with an accurate resource count can establish a clean and efficient beginning.
Fortunately, automatic tool tracking systems such as GoCodes provide a modern solution for quickly and accurately eliminating ghost assets.
Pick the Right Tool Tracking Solution
Choosing a tool tracking solution is a long-term investment, and it is often difficult to choose from the wide variety of options on the market.
That’s why it’s important to conduct research about the best system for your company.
The right tool tracking solution for your company is the one that best meets your needs. Here are some of the features to look for when researching a good tool tracking system:
- Central database
- Ability to track inventory
- Cloud-based storage
- Scalability
- Accessibility on a variety of smart devices
- Ease in integrating with company software
Consider where your company is at the moment, and what your plans for it involve. One way is to seek out one that can be deployed immediately. GoCodes meets this qualification.

The ability to use customizable QR codes is a major aspect of choosing a good tool tracking system. You are able to customize the tags to your project specification.
This is a major priority in fitting your company for tool tracking. For example, if the tools you intend to track will mostly stay indoors, consider using tough but flexible polyester tags.
On the other hand, tags for items that stay outside in extreme conditions should withstand item-welding and wide temperature swings.
Determine What Tools to Track
Not all of your tools and assets require tracking.
While even fixed assets (those that stay in one place) can undergo tracking for temperable differentials and the like, not all require inclusion in your company’s tagging solution.
Instead, track tools that have commanded large investments from your company.
That means choosing tools that might fall into the category of vehicles, heavy equipment, and major office equipment.
However, construction companies should also track small tools that, taken together, can represent a rather significant chunk of your company’s equipment investment.
Why small tools? As this chart shows, the cost of overlooking tools worth less than $1000 can quickly add up.
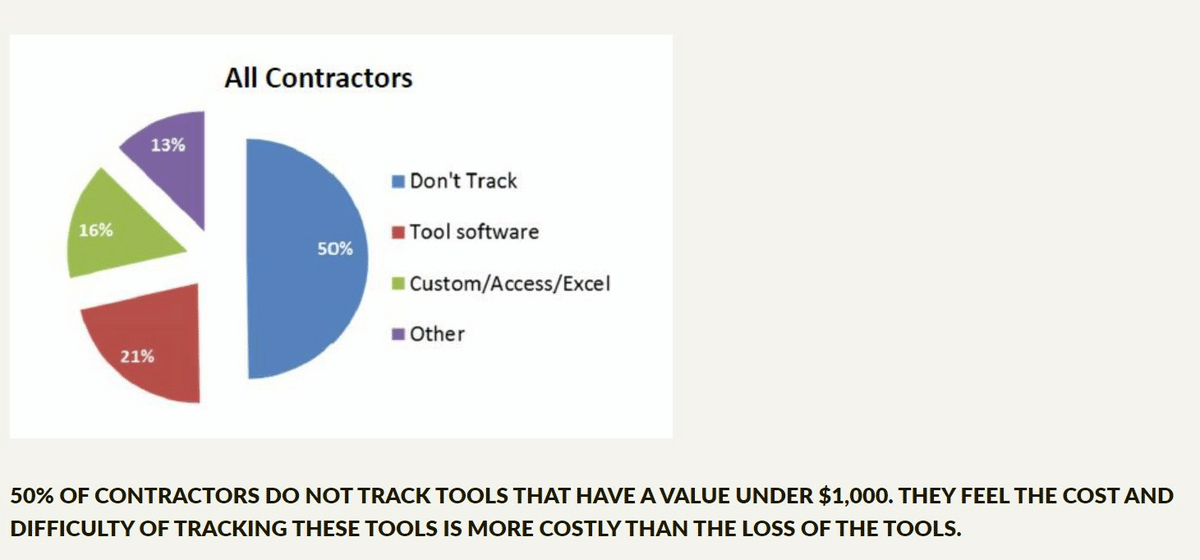
Just because your company does not pay attention to smaller tools doesn’t mean that thieves will also overlook them.
Moreover, the idea that the cost and effort allocated to tracking smaller tools are more than losing the tools is often misleading.
If an efficient and employee-friendly system such as GoCodes is in place, the benefits of tool tracking quickly manifest.
Overhead costs are lower when seemingly small items do not require constant replacement.
Employees can quickly learn to track items with smart devices with which they are already familiar.
In addition, the ability to compile and quickly analyze the data of even smaller items will save your company money.
Critical assets, then, are not just those that are large, expensive, and mobile.
They are those that your company uses frequently, makes them switch departments, and replaces them often due to theft or wear-and-tear, so they are prone to misplacement.
Track New Tools Immediately
Once your tool tracking system is in place, it is important to integrate new assets into it as quickly as possible.
It is easy to simply put the item to work or even move it through the inventory system to a client, but doing so threatens the effectiveness of your tool tracking.
If asset tags are not in place, information is not gathered. In addition, leaving several items untracked means that your system rapidly becomes out of date.
Trying to catch up with adding new items in large batches, most of which are likely dissimilar, makes for an inefficient and frustrating project for employees.
As this visual aid indicates, a wealth of information is attributable to tracking.
It can include not only the item’s location, but maintenance records, odometer information, run times, temperature history, and more.
This data isn’t just useful for company analysis—it can also help prove compliance with various codes or requirements and verify warranty observance.
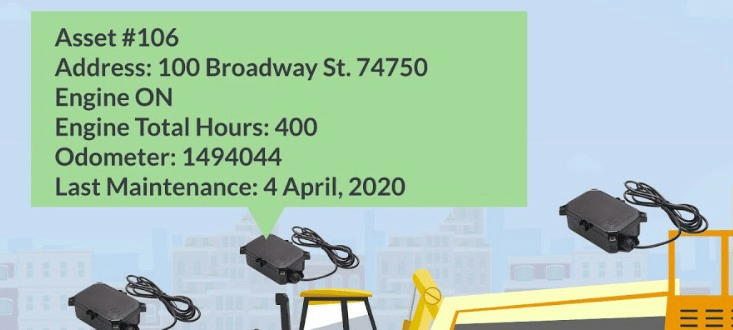
Having a unique tracking number or identifier assigned to each item yields many benefits.
Even more importantly, taking the time to include your new asset into your tool tracking system immediately will allow your company to have a full picture of its life with your company even before it reaches the site or warehouse.
This also allows you to retrieve it in the event of theft or misdirection.
Committing to immediate tracking ensures that your construction company will have a complete overview of information about the piece of equipment from the very beginning of use.
That means having an accurate idea of where the asset is in its life cycle at all times.
Assign Unique Identifiers to Each Tool
Even though your company might own ten identical hammers, it is best practice to assign a unique identifier to each of them.
This quickly differentiates each item from its counterparts beyond often-difficult visual identification.
Unique identifiers mean that each individual item can have its own GPS identifier. It also eliminates confusion regarding location and availability.
Where vehicles or other items requiring maintenance are concerned, unique identifiers assist tech teams in ensuring they have the right item for testing or maintenance.
Unique identifiers can look like this on asset tags:
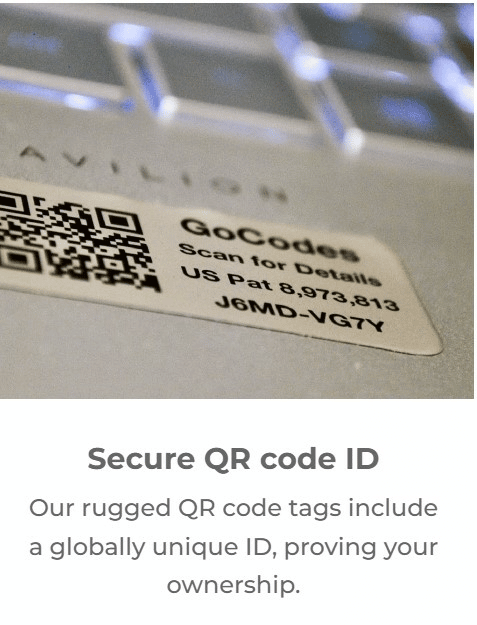
They include QR codes for easy scanning. The unique ID is often alphanumeric, which means it is a combination of letters and numbers.
Some companies use manufacturer’s serial numbers as a company ID, but this is rarely a good idea.
A part or small tool might have the same serial number across several companies and is therefore repeated several times.
This makes it difficult to retrieve the item if it is stolen or to prove ownership in the event of a dispute.
However, when a secure and globally unique ID is part of your tool tracking system, it is much easier to establish possession.
Enable Tool Check-in and Check-Out
A robust and streamlined tool check-in and check-out system is crucial for a construction company that has decided to invest in tracking.
Providing easy tool check-in and check-out for your assets offers your company many benefits:
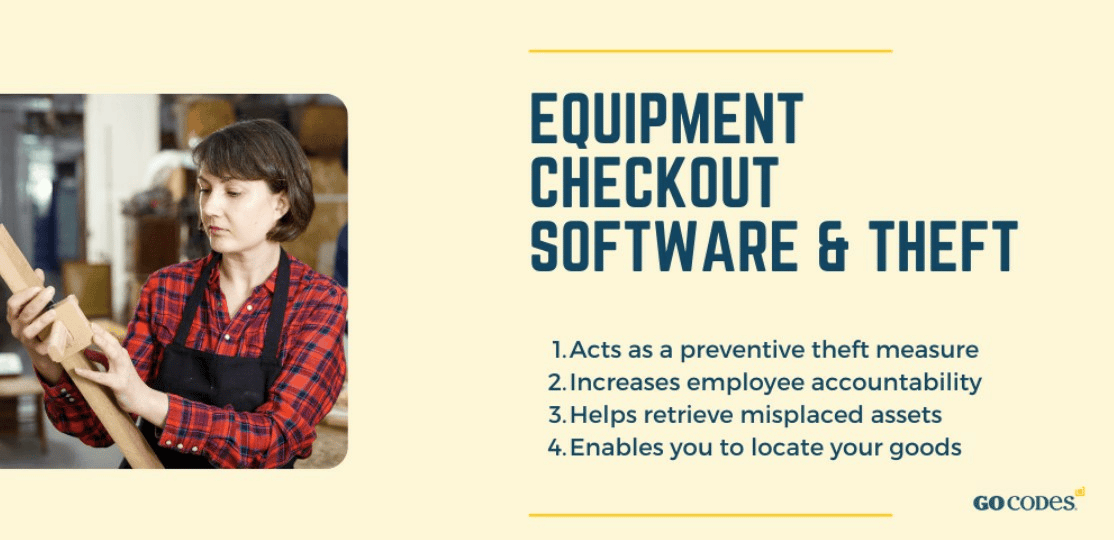
Implementing a system that allows a simple QR code scan for quick and easy check-in and check-out provides a time stamp and an easily traceable chain of custody.
This helps to make sure that information about the availability and whereabouts of individual tools is always up to date.
Check-in and check-out features can improve accuracy in data collection and ease in allowing employees to leave quickly after completing a shift.
For example, some systems allow employees to check in and check out many items in a single transaction.
Conclusion
Whether your company is new to asset tracking or looking to replace a system that is ill-suited for your purposes, these tips are extremely useful in integrating assets with scanning.
A system like GoCodes enables quick and easy check-in and check-out, which benefits a company in a number of ways.
By taking accurate inventory from the beginning of possession and determining which tools to track, as well as assigning unique identifiers to even identical items, a company can lower costs and raise efficiency.