Without the right machines and equipment, whether bought or rented, no construction project would get done. In fact, thanks to them, the work gets done faster—and better!
In other words, construction equipment plays a very large role in a construction company’s productivity and, consequently, in its success.
On the other hand, you also know that failing to make the most out of your assets can be a huge profitability killer.
But how can you be sure that your equipment is being utilized to its fullest potential?
In this article, we’ll help you figure that out.
We’ll dive into what exactly equipment utilization is, why it’s important, and how to apply all that information to your workflow in order to raise your equipment’s productivity through the roof!
In this article...
What Is Equipment Utilization
So, a construction site simply cannot operate without equipment. That is a fact. But how efficiently is that equipment used?
If a business relies on some kind of equipment—heavy or light—understanding equipment utilization can significantly affect its overall operational efficiency.
To go even further, in the construction industry, where errors and mismanagement of assets can be pretty costly, learning how to allocate equipment efficiently can potentially make or break a company.
So what can you do to improve the productivity of your assets?
Before we answer that, let’s start with the basics and define equipment utilization.
Simply put, it’s a way of measuring how efficient and productive your equipment is by showing you when, where, and how your equipment is used.
In other words, we calculate utilization by tracking the equipment’s location, usage, and performance against the equipment’s availability or capacity.
Moreover, having your equipment utilization rate (EUR) calculated and monitored could reveal a lot about how effectively your assets are used, and, as a result, it can shed light on some patterns and areas that need improvement.
For example, if you’re struggling to meet project deadlines, it may be a sign that some of your equipment is underutilized.
Knowing where you stand productivity-wise will lead to better asset management, which means less struggle to meet deadlines and more happy customers!
Keep reading to discover the ins and outs of equipment utilization and how to make the most out of your assets.
But first, let’s get into why all of this is important.
Why Is Improving Equipment Utilization Important
We’ve already established that equipment is central to operational efficiency, especially in the construction industry. As such, a piece of equipment represents a significant investment.
But is that investment justified? It certainly is if that piece of equipment is being used effectively!
If not, look into how you can improve your equipment utilization. It will benefit you in a lot of ways.

Managing a lot of assets simultaneously is no easy feat. Therefore, measuring how each of them performs will help you in ensuring their effective allocation.
For example, based on equipment utilization data, you can make an informed decision to move a piece of equipment that is underutilized on one construction site to another, where it might be needed more.
Furthermore, successful and strategic asset management will increase overall operational efficiency.
In other words, if you work on improving your equipment utilization, you’ll be able to deliver results on time without forgoing the quality of your work.
This will, naturally, lead to increased profits and success.
Increased equipment utilization also prevents project delays, which we know can be quite costly.
For example, one big cause of delays is unplanned maintenance.
Unfortunately, you’re probably familiar with the fact that a tiny broken machine part can be more than enough to bring massive projects to a halt.
There is a way of remedying this kind of issue, though. Namely, tracking utilization data can help equipment managers detect possible problems before they occur.
By predicting issues, you can arrange preventive maintenance during planned downtime instead of postponing the project.
Finally, improving equipment utilization can save you a lot of money in the long run.
By effectively allocating your assets, you’ll be able to minimize overheads and equipment rental costs.
All in all, learning how to utilize your assets to their full potential will surely be beneficial for your business.
Find out how to increase your equipment utilization in order to optimize your workflow!
How to Track the Utilization of Equipment
In order to determine your equipment utilization rate, you first need to acquire reliable equipment usage data. This includes how, where, and when your equipment is used.
In other words, there are different metrics to pay attention to, such as equipment check-out and check-in, GPS location, ignition on and off times, miles, fuel use, and utilization of equipment parts.
Tracking all of these is crucial for the full scope of your assets’ productivity. A complete tool-tracking solution, such as our own, will help you monitor and make sense of all that data.
To elaborate, GoCodes Asset Tracking’ patented QR codes, when attached to equipment and scanned with our smartphone app, provide data pertaining to that piece of equipment.

The app shows you a summary view of your equipment and allows you to check it in/out, select the return date, and so much more.
Updating the GPS location of the equipment via GoCodes Asset Tracking app is also possible. When a worker scans the QR code, the history of that piece of equipment is automatically updated.
The update shows the name of the person who updated the asset, as well as the time and place of the update. Click here to find out more about how it works!
Moreover, our Enterprise Reporting module allows you to create customized charts and reports, providing an in-depth analysis of your equipment utilization.
To illustrate, clicking on the Equipment Usage report will show you what equipment was used for each project.

Having all your metrics in one place makes it easier to keep track of all the crucial data. This way, you’ll more likely be able to spot equipment usage patterns.
In conclusion, an all-in-one tool tracking software is a must-have if your goal is to gather reliable data about your equipment utilization.
If you don’t already have such software, consider getting one.
How to Calculate Equipment Utilization
Now you’ve gathered all your equipment utilization data, but even that won’t do you much good if you don’t know what to do with it.
To get insight into your assets’ productivity, you need to calculate the equipment utilization rate.
Calculating EUR is quite simple. Take a look at the formula below.
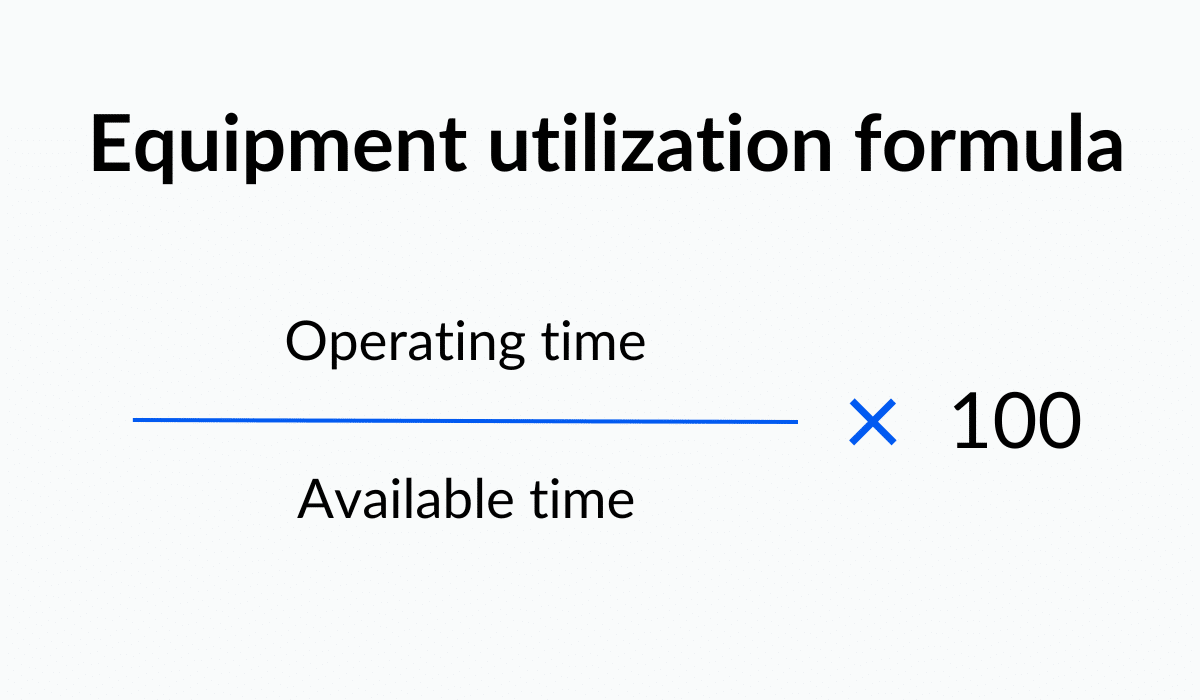
Essentially, EUR is calculated by dividing the operating time (the amount of time equipment is in operation) by the available time (the amount of time equipment is available for operation).
Multiply that by 100, and you get your utilization rate percentage.
Consider this example to see how this formula applies to real life. If a machine is scheduled to be used for 8 hours a day, six days a week, its available time is 48 hours a week.
However, if, due to some unplanned factors, the machine runs for 38 hours that same week, its utilization rate is 79%.
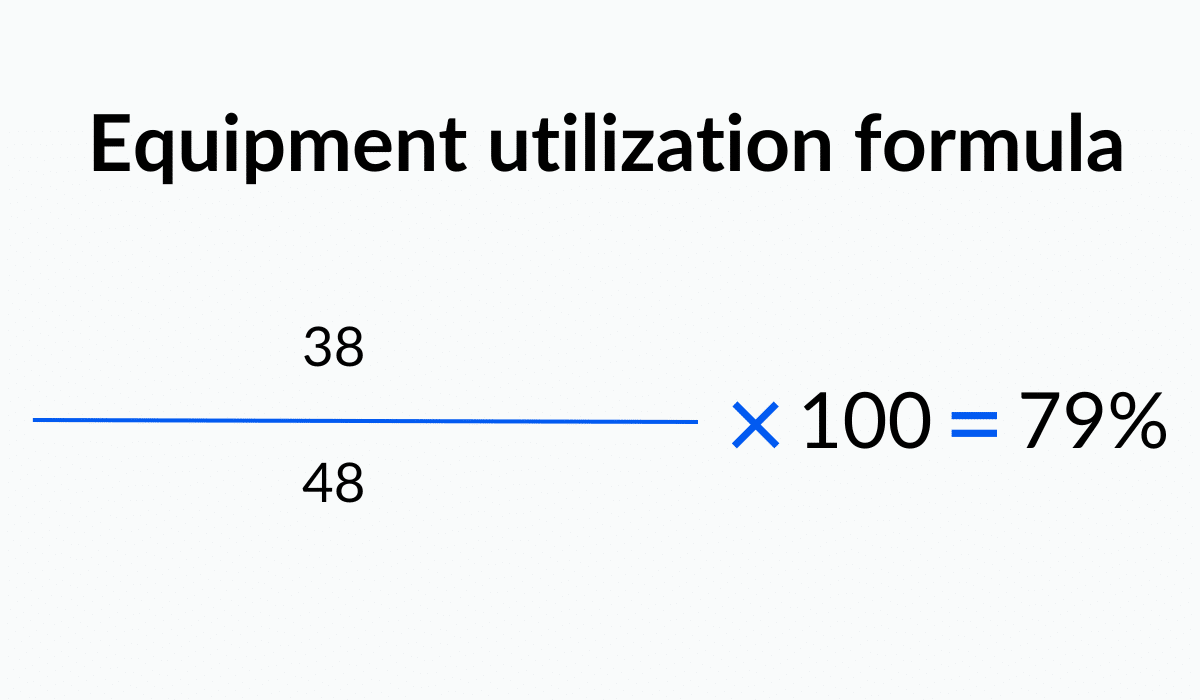
Here, it is important to note that equipment’s available hours do not include planned downtime hours, such as weekends or, for example, nights.
Available hours only pertain to when equipment is scheduled to be used.
Having these numbers in front of you will help you put things into perspective.
They will show you areas that need improvement (i.e., areas with lower EUR) and guide you during maintenance or expansion planning.
However, the formula has its drawbacks. One of its main challenges is the quality and consistency of the data input, which, after all, depends on people.
So there’s always room for error.
That’s why going digital is not a bad idea. Although it will still require an adjustment period, a tool tracking software will improve your data accuracy.
Therefore, although imperfect, the formula is an easy-to-use and useful tool for determining your equipment utilization.
How to Maximize the Utilization of Equipment
Now that we’ve covered the theory, let’s finally get into some practical advice on maximizing those productivity rates.
Maximizing the productivity of your equipment could be viewed as a five-step process that relies on some of the information we’ve covered so far in this article. Take a look at the picture below.
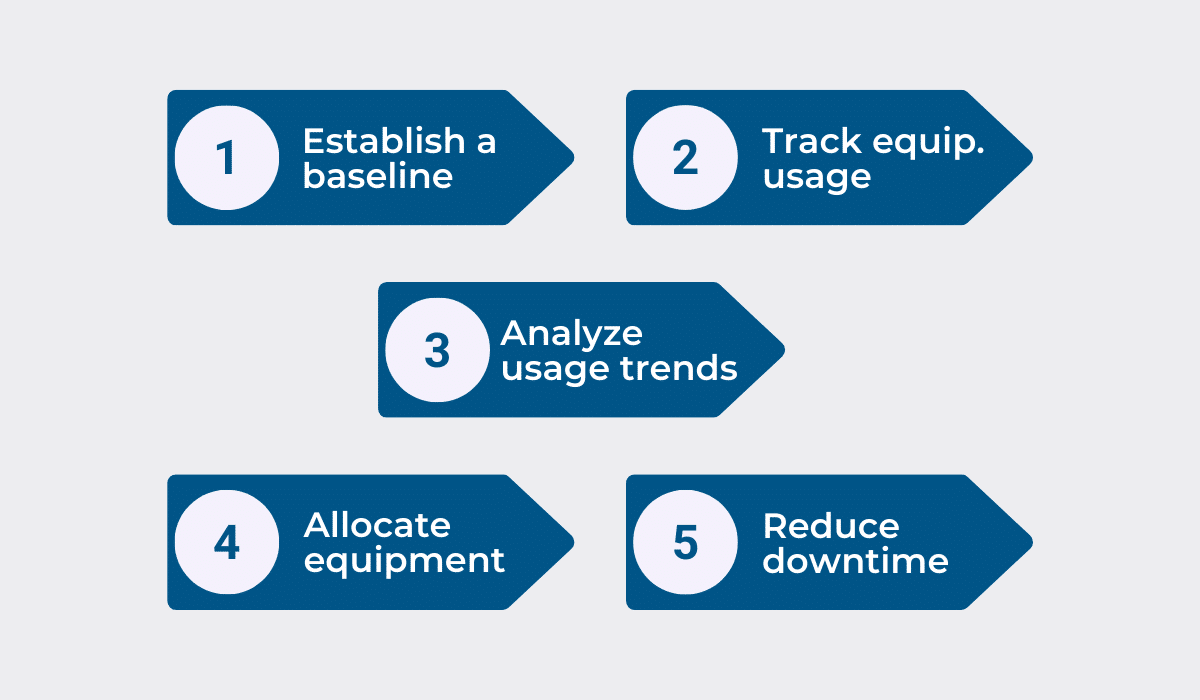
The first step would be establishing a baseline, i.e., determining where you stand asset productivity-wise.
You do that by calculating your current equipment utilization rate using the formula we mentioned earlier.
After you determine your starting point, keep tracking your equipment usage with a tool tracking software. Look for trends in productivity.
For example, you may notice that an excavator might be idle at a construction site for some time now while, at another location, an excavator’s utilization rate is through the roof.
Based on this analysis, you can now make informed decisions and allocate the assets effectively.
Move that excavator to the contraction site where it’s needed. Alternatively, consider buying or renting a new one if all your excavators’ EUR is pretty high.
Whatever you do, you’ll be more confident in your decision because you’ll have the numbers that back you up.
Finally, if you’ve been doing all of these steps correctly, you’ll also be able to reduce equipment downtime.
The fact is, sometimes idle time is unavoidable. Use such periods to your advantage and schedule preventive maintenance.
It’ll save you money and decrease machine downtime in the long run.
According to Probuilder, the numbers back this claim up. Namely, construction maintenance takes up about 30% of the total project costs, depending on the type of machine used.
A broken piece of equipment can potentially damage other equipment parts. Preventive maintenance will help you fix the problem before it gets worse.
Moreover, preventive maintenance, just like the name suggests, can be planned in advance and thus fit into your schedule. It won’t interrupt a project.
All in all, follow these steps, and you’ll quickly be able to detect inefficiencies in the workflow. And the sooner you detect them, the quicker you’ll be able to start working on removing them.
Conclusion
Obviously, construction equipment isn’t going anywhere anytime soon. Moreover, as technology advances, so will the machinery you rely on to get the job done.
However, right at this moment, there are already so many tools at your disposal that have the potential to make your business a huge success.
Still, how you use these tools is, and always will be, up to you. And knowing how to make the most out of them is, we would argue, art in itself.
Use the information in this article to start learning how to use your equipment more efficiently and reach productivity levels you’ve never reached before!