Key Takeaways
- Working with low-quality materials compromises safety and quality.
- Poor storage and material handling lead to waste, environmental damage, and higher expenses.
- Material theft is a common problem across construction sites and leads to increased costs and project delays.
- Material management tools protect materials and improve project efficiency.
Are you giving your construction materials the attention they truly need?
You might not realize just how crucial proper material management is, but overlooking it can lead to added expenses, project delays, and even theft.
That’s why it’s time to highlight the serious effects of poor material management and show you how to protect your materials to keep your projects—and budget—on track.
Let’s start.
In this article...
Overpaying for the Materials
If you’re not careful with the way you manage your construction materials, you could be spending a lot more than necessary.
One of the first steps to effective material management is doing your homework.
This means conducting thorough market research and comparing suppliers before placing any orders.
Why is this so important?
Because if you skip this step, you’re likely to miss out on better deals and pay inflated prices when there are more competitive options available.
Different suppliers often offer varying prices for the same materials, and without comparing these options, you might end up overpaying.
Also, market conditions change, and what was a good deal last month might not be the best choice today.
So, by not staying updated, you miss opportunities to save.
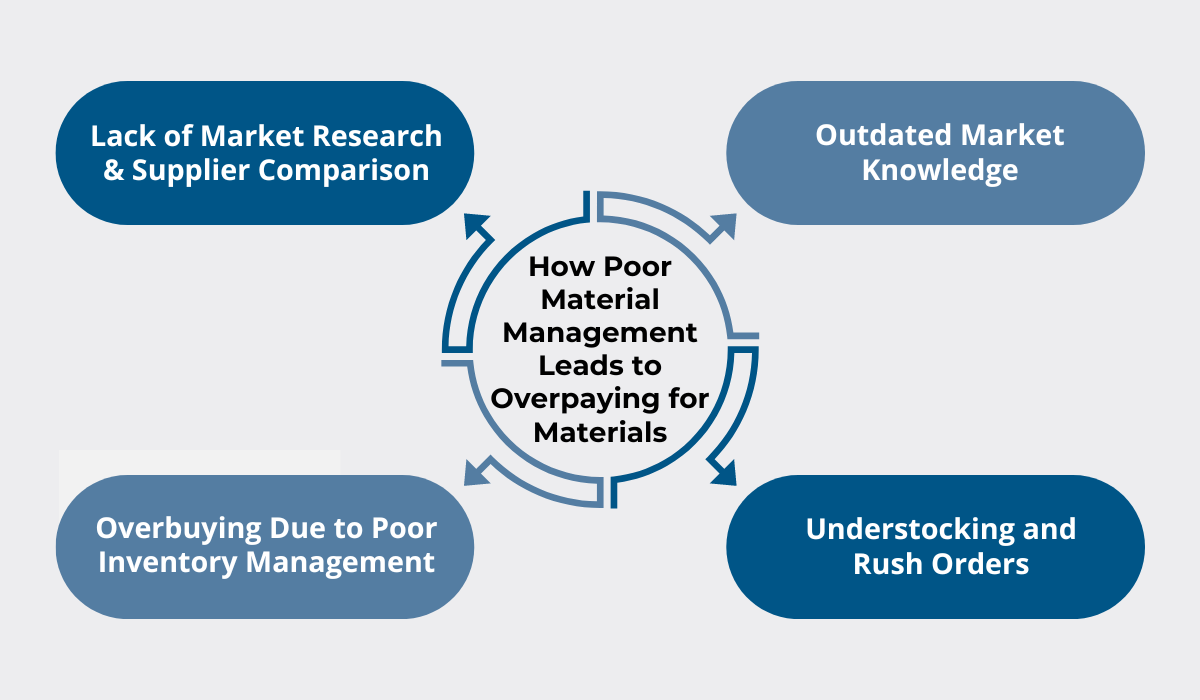
But overpaying isn’t just about paying too much upfront. It’s also about how you manage what you have.
Let’s talk about inventory management.
If you don’t have a clear handle on your materials stock, you might end up ordering more than you need, leading to overbuying and wasting money.
This also clutters your site, creating more challenges in managing space and logistics.
On the flip side, not knowing your inventory can lead to understocking, where you run out of essential materials right when you need them most.
What happens then?
Well, you’re forced to pay extra for expedited shipping to keep the project on track, which drives up costs even further.
So, what’s the key takeaway here?
Paul Netscher, an expert with over 30 years in construction project management, puts it clearly:
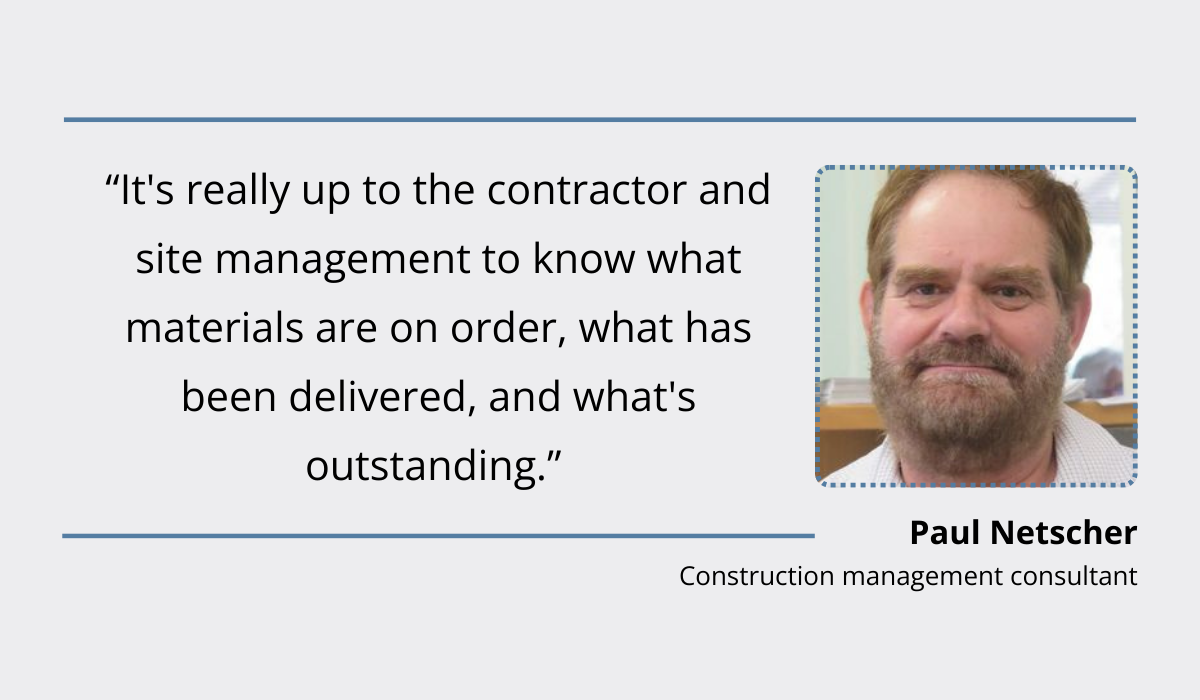
In other words, you have to keep a close watch on your inventory.
If you don’t, you could end up over-ordering, paying for rush deliveries, or dealing with costly delays—all of which inflate your expenses.
The good news?
Effective material management is achievable with the right tools.
Construction material management software, for instance, helps you track inventory in real time and alerts you when stock is low.
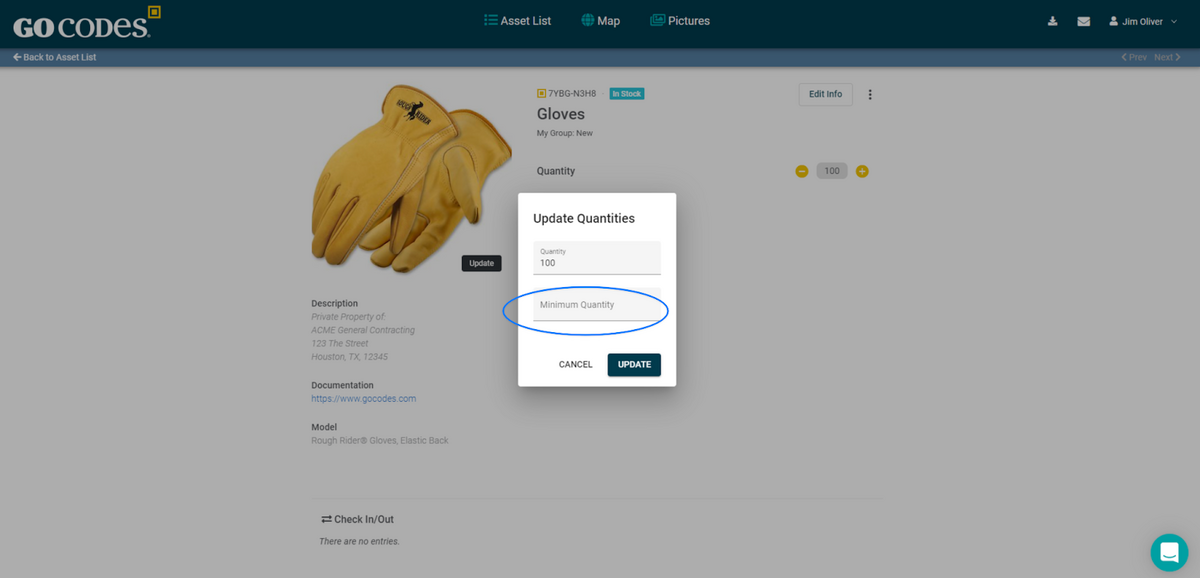
Some software solutions even provide a database of up-to-date prices from local suppliers.
So, using these tools saves you time, but also ensures you’re getting the best deals on materials and avoiding unnecessary expenses.
Want to learn more?
Check out our article full of tips for saving money on construction materials.
Ending Up with Poor Quality Materials
In construction, material management can make or break a project.
And this important aspect isn’t just about keeping an inventory or placing orders, either.
Material management requires serious attention to detail and due diligence.
So, if you don’t do it—or you do it poorly—you risk sourcing substandard and low-quality materials that compromise the quality and safety of the entire build.
What is, then, the first step of making your material management not poor?
Well, it all starts with finding a reliable supplier who consistently delivers high-quality materials.
Skimp on this part, and you’re setting yourself up for trouble.
Without thorough research and scrutiny, you might end up overpaying or, worse, dealing with shady suppliers who slip in inferior materials without you even noticing.
If you’re not careful, you could end up with poor-quality concrete that cracks under pressure, faulty wiring that becomes a fire hazard, or weak roofing materials that don’t stand up to the weather.
Even something as small as low-quality nails, screws, bolts, or anchors can lead to big problems down the line.
These might rust, break, or fail to hold under load, especially in challenging conditions.
And what happens next? Endless rework, of course.
PlanRadar’s survey confirms this, stating that one of the main reasons for rework in construction is precisely poor quality of materials.
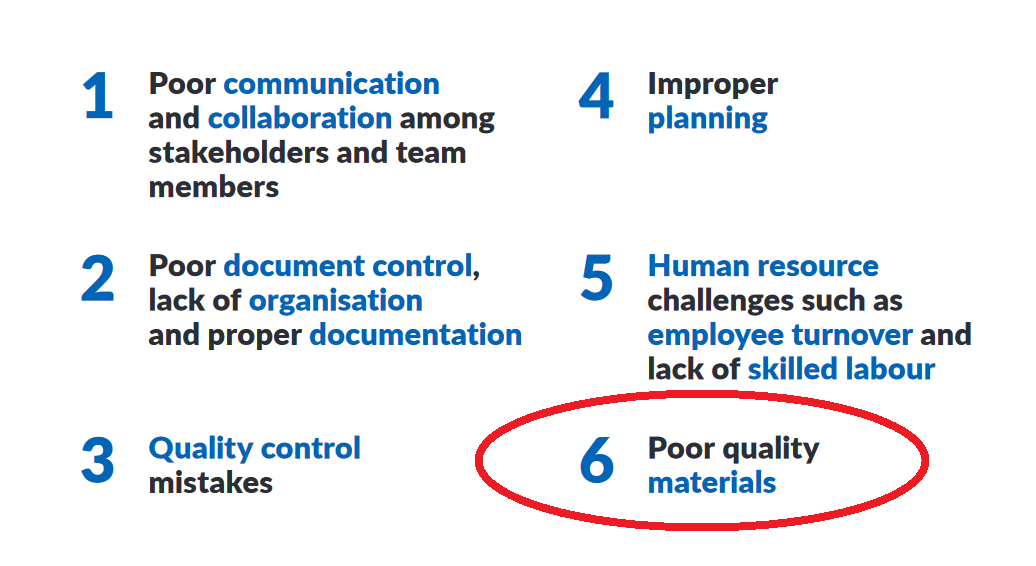
What is rework in the first place?
That’s just another way of saying more time, more money, and more headaches that eat into your budget and throw your schedule off track.
But let’s not forget the most serious consequence of working with poor-quality materials: safety hazards.
Take the Rana Plaza collapse in Bangladesh in 2013.
This tragedy is a stark reminder of what can happen when low-quality materials are used in construction.
The building that housed several garment factories collapsed, killing over 1,100 people and injuring thousands more.
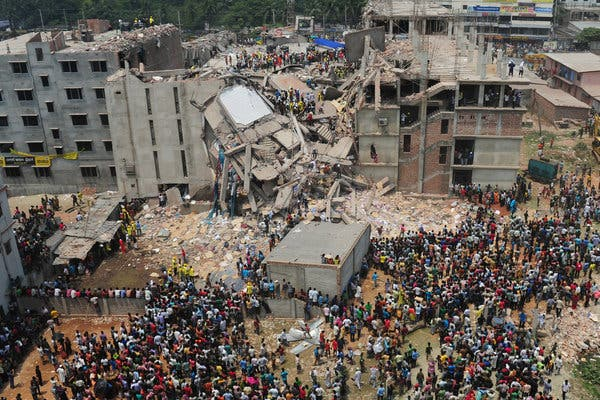
According to Main Uddin Khandaker, head of a government inquiry team, the disaster was primarily due to substandard construction practices, including the use of low-quality materials like sub-standard steel rods.
They even added extra floors illegally without the proper permits or engineering assessments.
It was a deadly chain reaction that started with poor decisions about materials.
To prevent working with poor-quality materials, construction material management should start with good preparation, thorough market research, supplier comparison, and due diligence.
When you take these steps seriously, you reduce the risk of working with poor-quality materials.
But skip them, and you risk not just the quality of your project, but also the safety of everyone involved.
Having Your Materials Stolen
Proper material management is also about what happens once the materials arrive at the construction site or your storage yard.
If you’re not carefully tracking, storing, and securing your materials, you’re leaving the door wide open to theft.
And let’s be real—theft is the plague of the construction industry, and it’s happening everywhere, all the time.
We hear news stories every day about another site being hit, with the losses often running into the thousands or even tens of thousands of dollars.
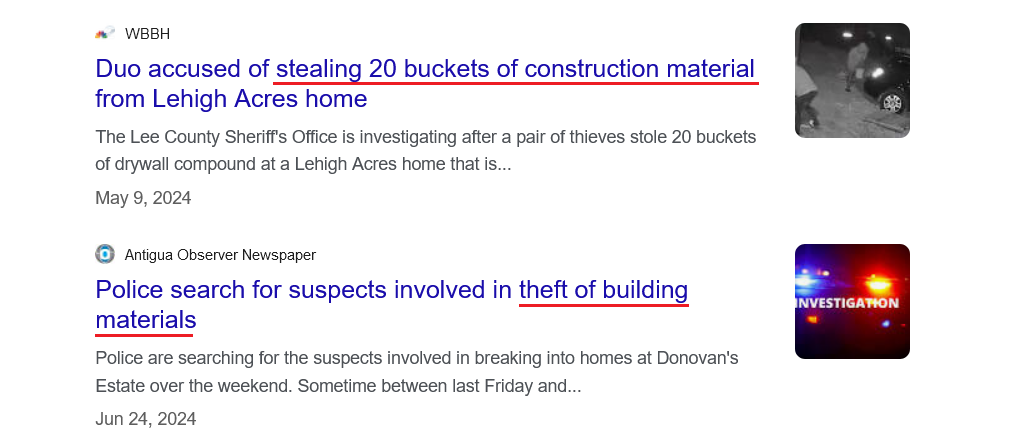
Take Simmons Masonry, for example, a company that does renovation and restoration work in Winnipeg and parts of Manitoba.
According to CBC, in the past two years, they have experienced theft of tools, materials, and even company vehicles from their job sites.
For them, this means project delays, increased costs, and frustrated clients.
Darryl Harrison from the Winnipeg Construction Association rounds up what theft does to a company:
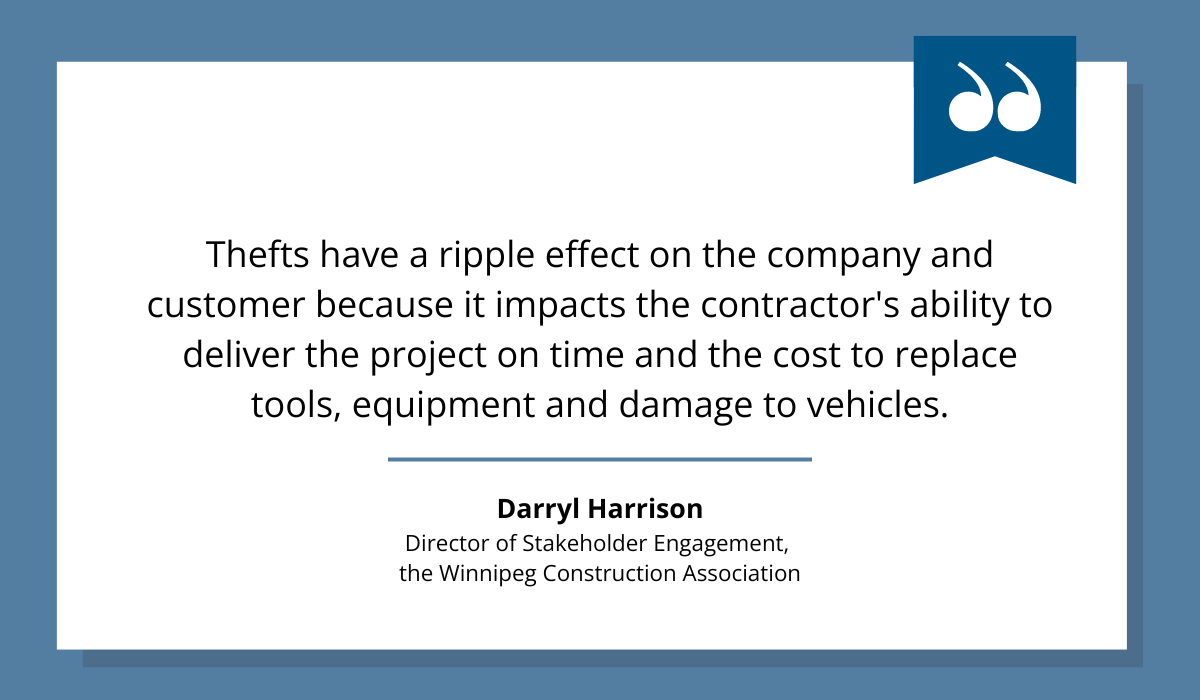
To prevent this from happening to you, consider using technology like our GoCodes Asset Tracking.
This asset tracking and management software allows you to track materials and equipment in real time.
It uses QR-coded labels and GPS tracking devices to keep tabs on your assets, ensuring they are exactly where they should be at all times.
You can also secure your storage yard with geofencing.
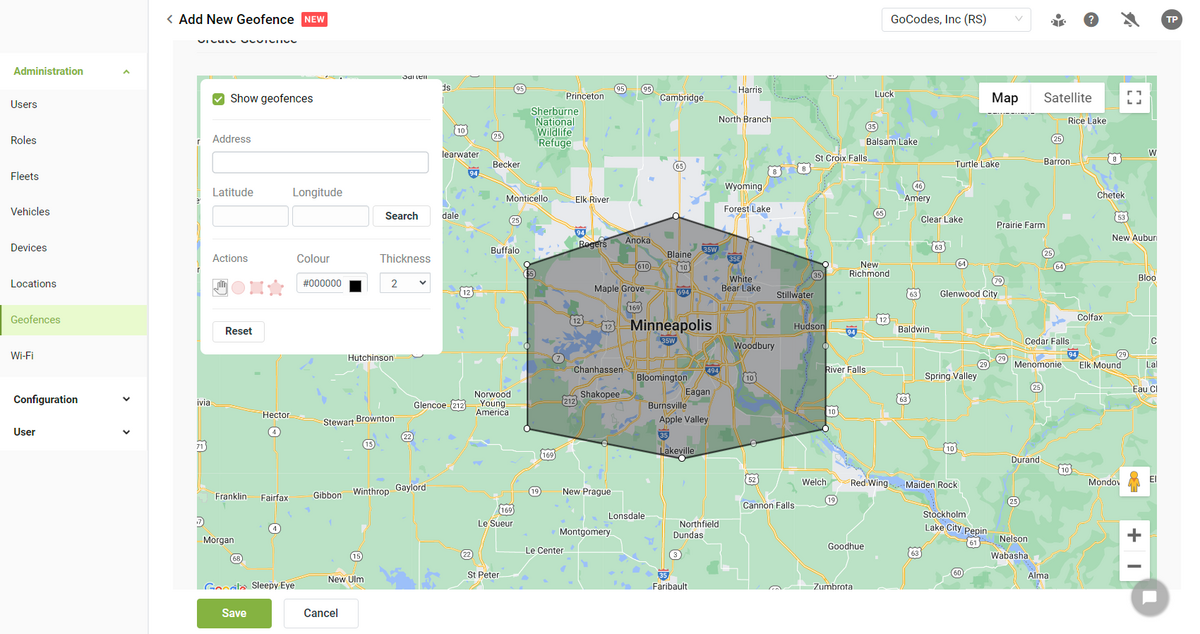
If any materials are moved outside of the designated area, you get an alert so you can quickly call the police if something seems suspicious.
Additionally, you can track vehicles transporting materials, so you know where your materials are at all times during transport.
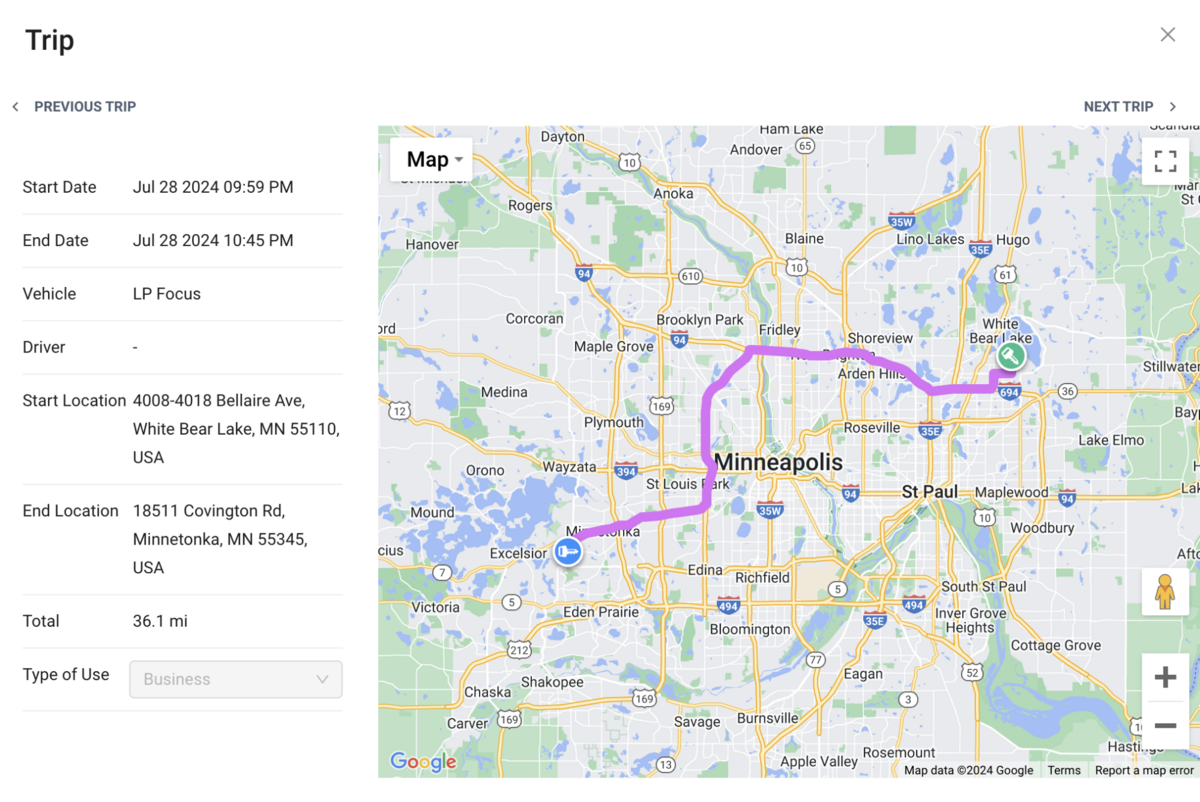
Bottom line?
Utilizing such material tracking software can help you protect your materials and prevent theft, saving you time, money, and headaches in the long run.
Dealing with Increased Material Waste
Furthermore, poor planning and handling of materials can create a mountain of waste that impacts both your budget and the environment.
One study conducted inEthiopia in 2022 found that construction waste is a challenge for almost all ongoing construction projects.
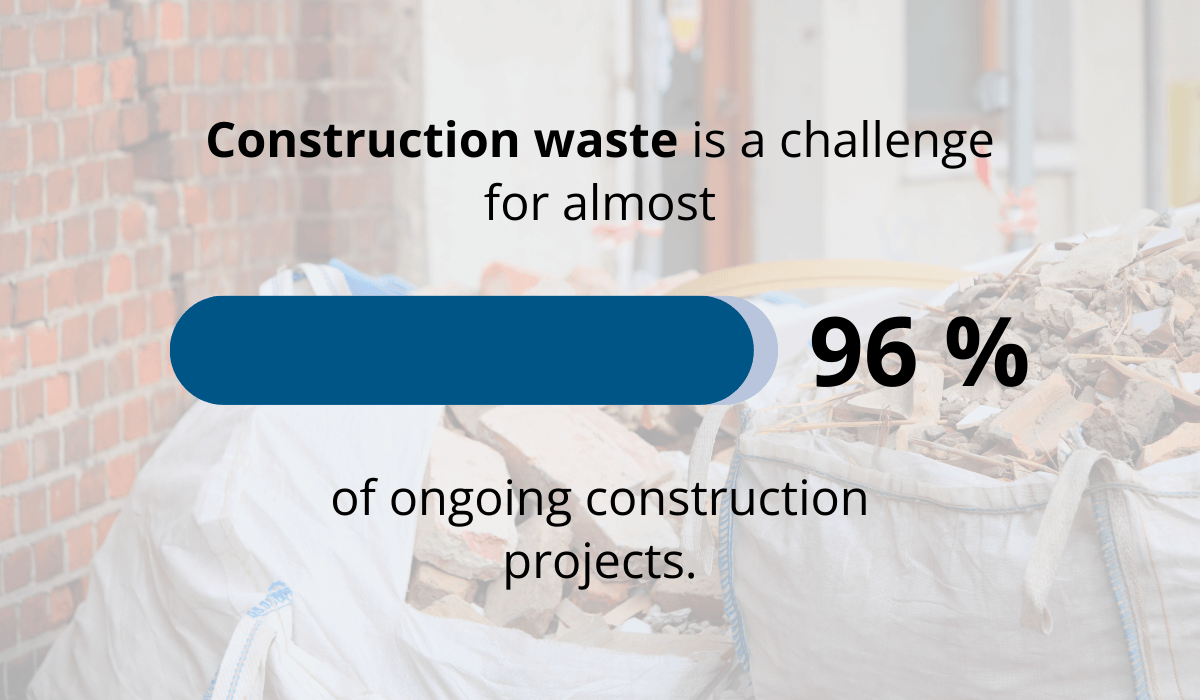
And out of all the materials purchased, 6–10% ends up as waste, which directly contributes to project cost overruns.
Besides costly overruns and reduced profits, material waste leads to:
- environmental pollution,
- public health and safety risks,
- the failure of construction firms, and
- excessive consumption of raw materials.
So, how does poor material management contribute to all this waste?
For starters, not storing materials properly is a big part of the problem.
Here is why.
The useful life of any material depends heavily on how it’s stored and handled, so if you don’t store them properly, materials turn into waste.
Below are some construction materials and how that happens:
Material | What happens when not properly stored |
---|---|
Cement | Hardens if exposed to moisture |
Plaster/drywall compound | Dry out or become contaminated if not sealed properly |
Paint | Spoils if left open or if stored in extreme temperatures |
Insulation materials (fiberglass, foam boards) | Become damaged or degrade if exposed to water or sunlight |
Certain metals | Corrode or rust if not protected |
Even wood isn’t immune to turning into waste.
If it’s not kept in a dry, covered space, it can warp, rot, or become infested by pests.
As Fred Mpalanyi, a carpenter from Bukoto, Uganda, points out, timber absorbs moisture and needs to be stored in a well-ventilated area to prevent rot.
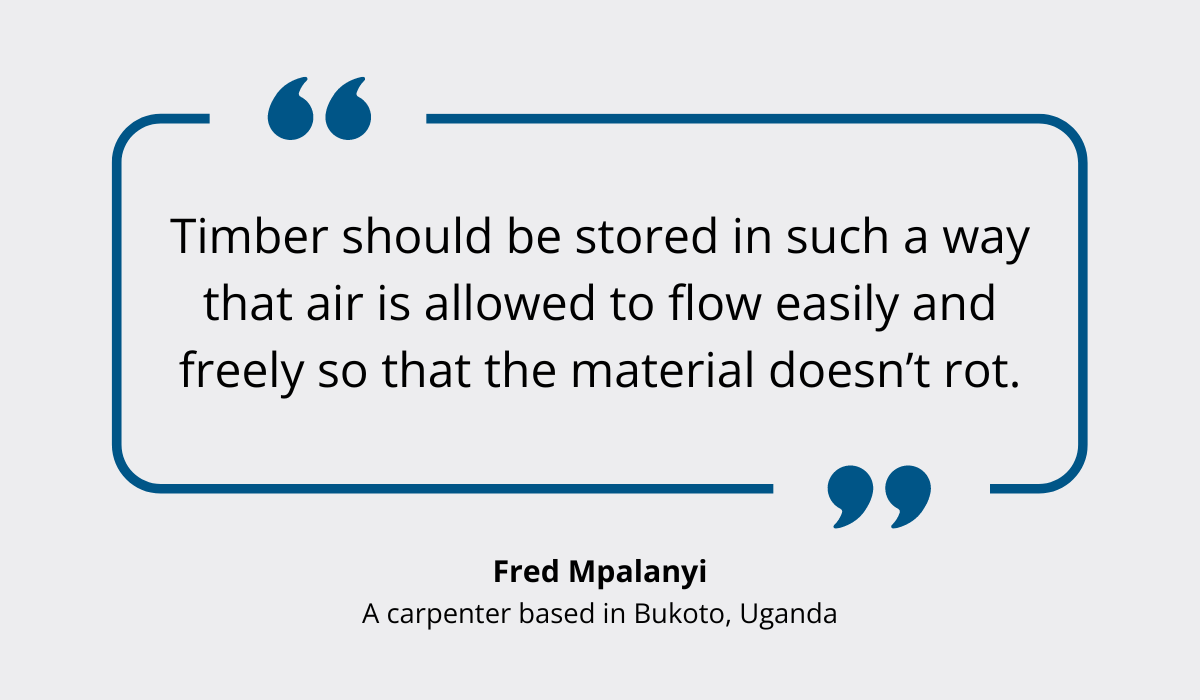
Then, there are also materials that degrade over time if not used promptly, especially when over-purchased.
Take adhesives and sealants, for example.
They have a shelf life and can lose their bonding strength or harden in their containers if stored for too long.
When that happens, the only thing you can do is throw them away.
Naturally, all this waste and unusable materials add to landfill waste and contribute to environmental degradation.
So, what’s the solution?
It all starts with proper material planning, smart material purchasing, and choosing the right place to store materials.
By managing these factors carefully, you can reduce material waste and minimize both your costs and your impact on the environment.
Experiencing Project Delays
Construction project delays can happen for many reasons, like bad weather, supply chain issues, material shortages, or unexpected events like natural disasters.
But a lot of the time, project delays are caused by something entirely preventable: poor material management.
Maybe you’re not managing your inventory well, or you don’t have a clear system for tracking where your materials are.
Any of these material management mistakes can lead to costly delays.
Think about it.
When you don’t have the materials you need on-site, or when deliveries show up late, incomplete, or not at all because you didn’t order them in time, everything grinds to a halt.
Your crew stops working, waiting around for materials to arrive, which means progress slows down or even stops.
And this has serious financial implications.
For starters, workers have to get paid whether they’re working or not, and that adds up fast.
Let’s talk some numbers here.
For instance, research showed that in the course of a day, bricklayers wasted 45 minutes, carpenters 62 minutes, roofers 75 minutes, electricians 80 minutes, and plumbers 83 minutes on a construction site.
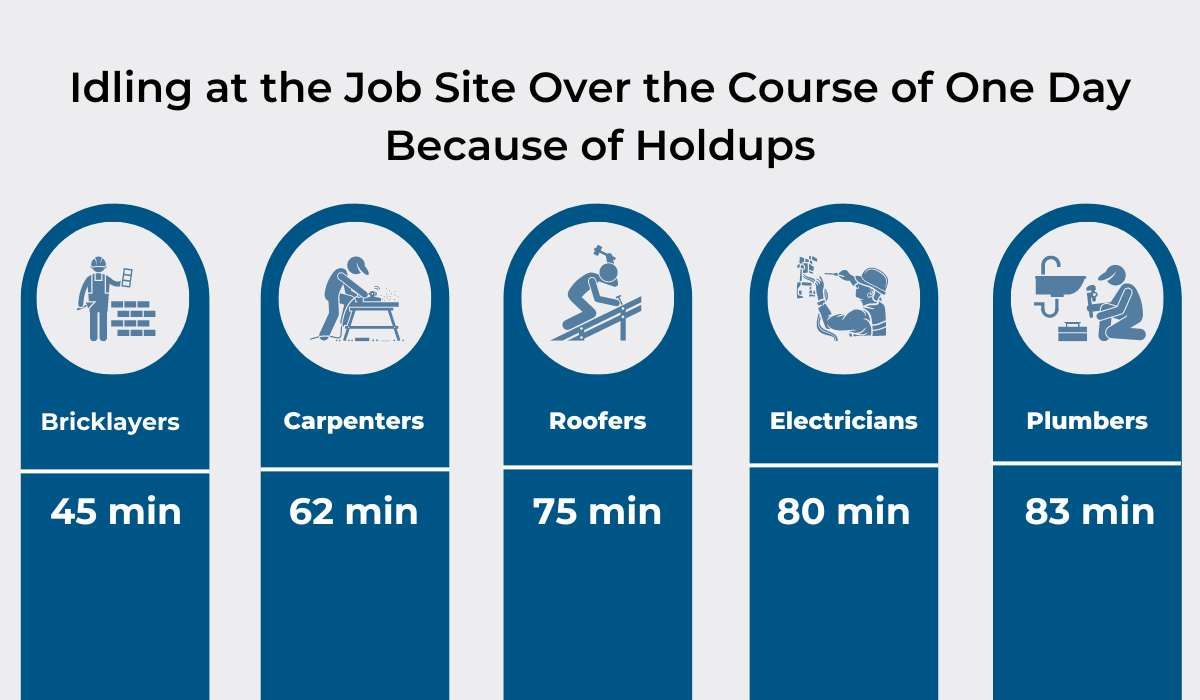
Illustration: GoCodes Asset Tracking / Data: University of Michigan’s CCEM cited in Trekker Group
What does that mean for your budget?
For a carpenter making $23 an hour, that wasted time costs you about $23 every single day.
Multiply that by five days a week, and you’re losing over $100 a week per carpenter.
Over a year, that’s almost $6,000—just for one worker! And that’s not even counting everyone else on your team.
On the other hand, delays lead to aggravated clients.
Michael Hydeck, owner of Hydeck Design Build Inc. in Telford, Pennsylvania, draws from experience:
“If you told the client you were going to be done in [20 days] and now you’re not done by day 30, you’re now getting an aggravated client who’s not going to recommend you.”
All in all, poor material management leads to delays, which drain your budget and hurt your bottom line.
You either end up paying for it out of your own pocket, or you have to ask your client for more money—which is tough to justify when the delays are because of something you could have prevented.
So, ask yourself: are you on top of your material management?
Are you ensuring everything is ordered on time, delivered when it should be, and tracked properly?
Every day you neglect material management is another day you waste time and money, and possibly endanger your reputation.
It’s worth getting construction material management right—right now.
Conclusion
As you have just seen, each of these effects of poor construction material management unfolds into at least one or more negative consequences.
And to be honest, we barely scratched the surface here.
Don’t let it happen in your construction company.
Make sure to research suppliers, track your inventory accurately, and use the right technology to protect your materials.
With more effort put into construction material management, you can save time, reduce costs, and keep your projects running uninterrupted.