Making sure all of your equipment runs smoothly is essential for the success of any construction project.
After all, if your excavator’s tracks are slipping, or your bulldozer is always experiencing issues with the cooling system, you’re bound to face unnecessary and costly project delays.
This makes proactive equipment maintenance all the more important.
But what about tracking those maintenance activities?
As it turns out, knowing when the brake fluid was last changed or when the next inspection is due can be just as important.
That is why, in this article, we’re sharing what steps you need to take to successfully keep track of your equipment maintenance.
In this article...
Create a Digital Equipment Inventory
If you want to stay on top of your equipment maintenance, you need to, first and foremost, know exactly what equipment you own.
So, start at the beginning and create a detailed equipment inventory list.
This list will serve as a foundation for all of your maintenance-related activities and provide you with a holistic view of all the equipment you own.
But what should you use to create the inventory list?
Well, many construction companies still like to track their equipment and its maintenance using more traditional methods like simple Excel spreadsheets, paper-based logs, or custom templates like the one you can see below.
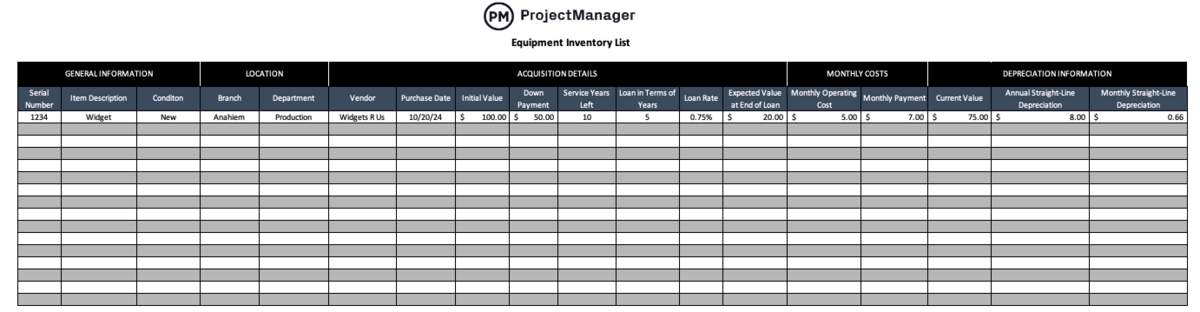
These methods are simple and affordable, so it’s not surprising that many construction professionals prefer them over digital solutions that come with a cost and a learning curve.
However, manually keeping track of all the equipment you own and its maintenance status and schedules has several downsides that are important to consider.
Firstly, there is the risk of human error when it comes to manual data entry, as well as the fact that the whole process can get quite time-consuming.
Secondly, as your company grows and your business expands, so does the number of assets that require maintenance.
At that point, manually managing all the maintenance data related to individual pieces of equipment becomes overwhelming and unproductive.
That is why more and more construction companies are choosing to go digital when it comes to tracking equipment maintenance.
Now, if you don’t want to invest in software that only serves the purpose of creating an equipment inventory, a more well-rounded solution would be the way to go.
For instance, GoCodes Asset Tracking is primarily a tool and equipment tracking software, but it comes with a plethora of other features that allow you to stay on top of all asset-related activities.
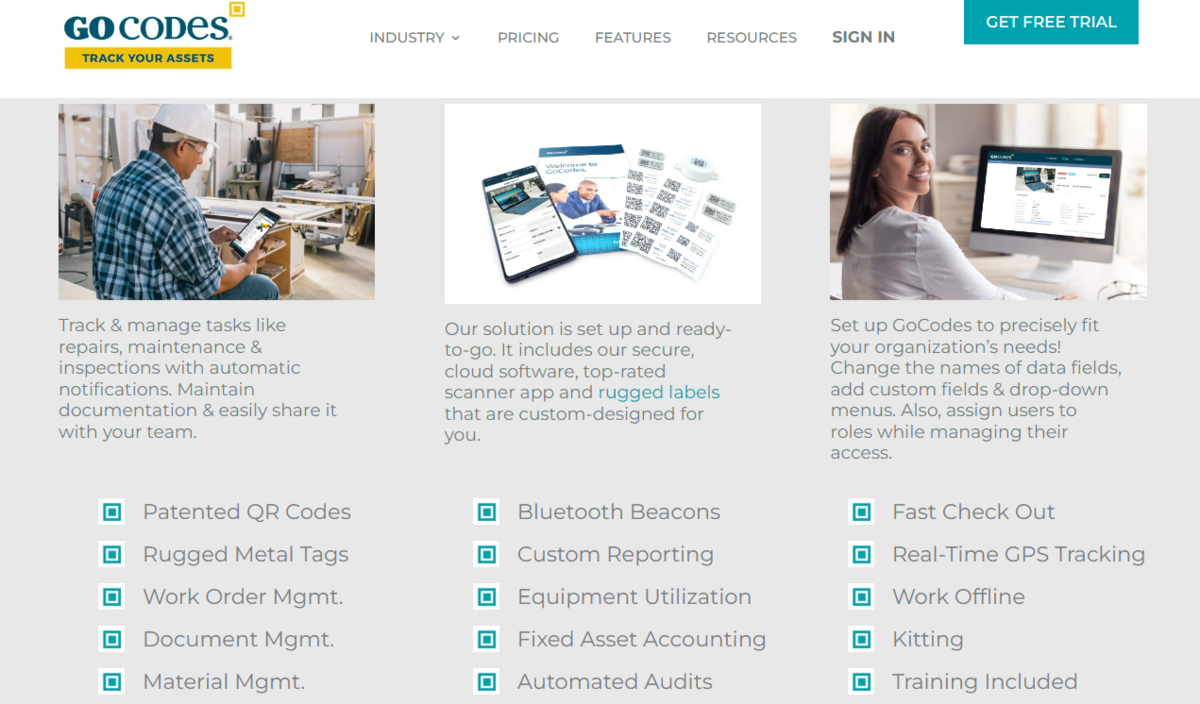
GoCodes Asset Tracking allows you to create an asset list complete with essential information about every piece of equipment you own—from asset type, model, and serial number, to who it has been assigned to and what its maintenance status is.
Our Asset List View also comes with a handy search bar that makes it easy to find the piece you need in a matter of seconds.
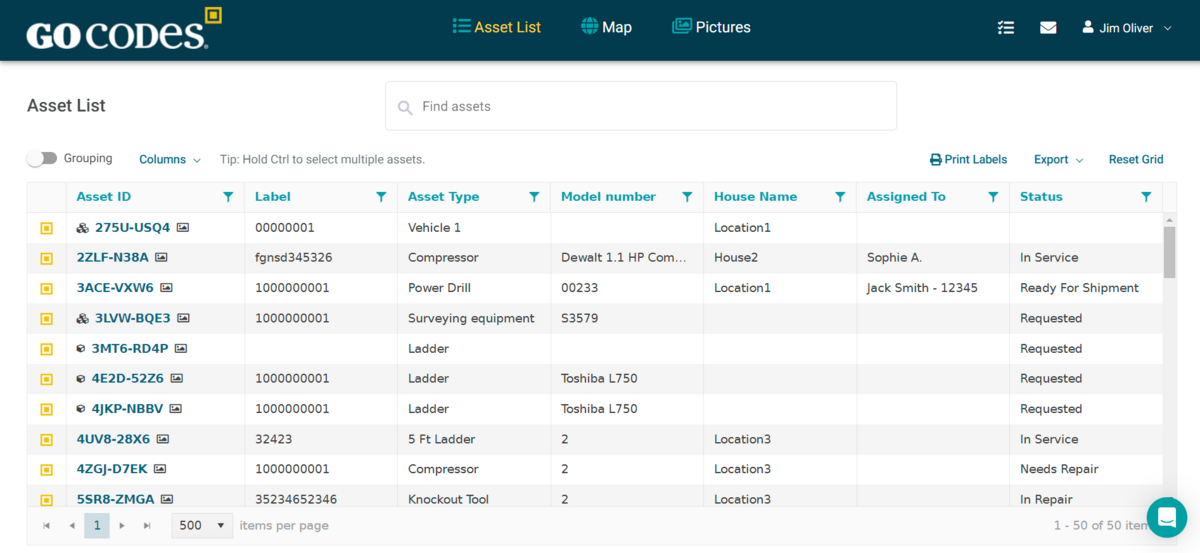
Additionally, given that the layout of the GoCodes Asset Tracking Asset List resembles the spreadsheet look you and your crew are likely used to, using it is intuitive and doesn’t require a lot of training.
In short, using a solution like GoCodes Asset Tracking to create a detailed inventory of all of your equipment is bound to simplify the process of tracking all equipment-related data—including maintenance.
Tag Your Equipment
While keeping an up-to-date inventory of all the equipment in your possession is helpful in and of itself, that is only the first step in effectively tracking equipment maintenance.
The second step is to tag your equipment.
Of course, assigning scannable identification tags to every piece of your equipment makes it easy to track the location of your assets.
But it can do more than that:
Tagging your equipment also plays an important role in streamlining the maintenance tracking process.
Knowing when each piece was last serviced or which ones need track tension adjustment is the kind of information you, your crew, and your maintenance technicians need to have at your disposal at all times.
Tagging your equipment makes this easy, and this is another area where GoCodes Asset Tracking excels.
As we mentioned earlier, GoCodes Asset Tracking is an easy-to-use equipment tracking solution, and it consists of three main components that go hand in hand:
- cloud-based software
- durable QR code tags, and
- in-app scanner.
Below is an example of what our tags look like on a piece of equipment.
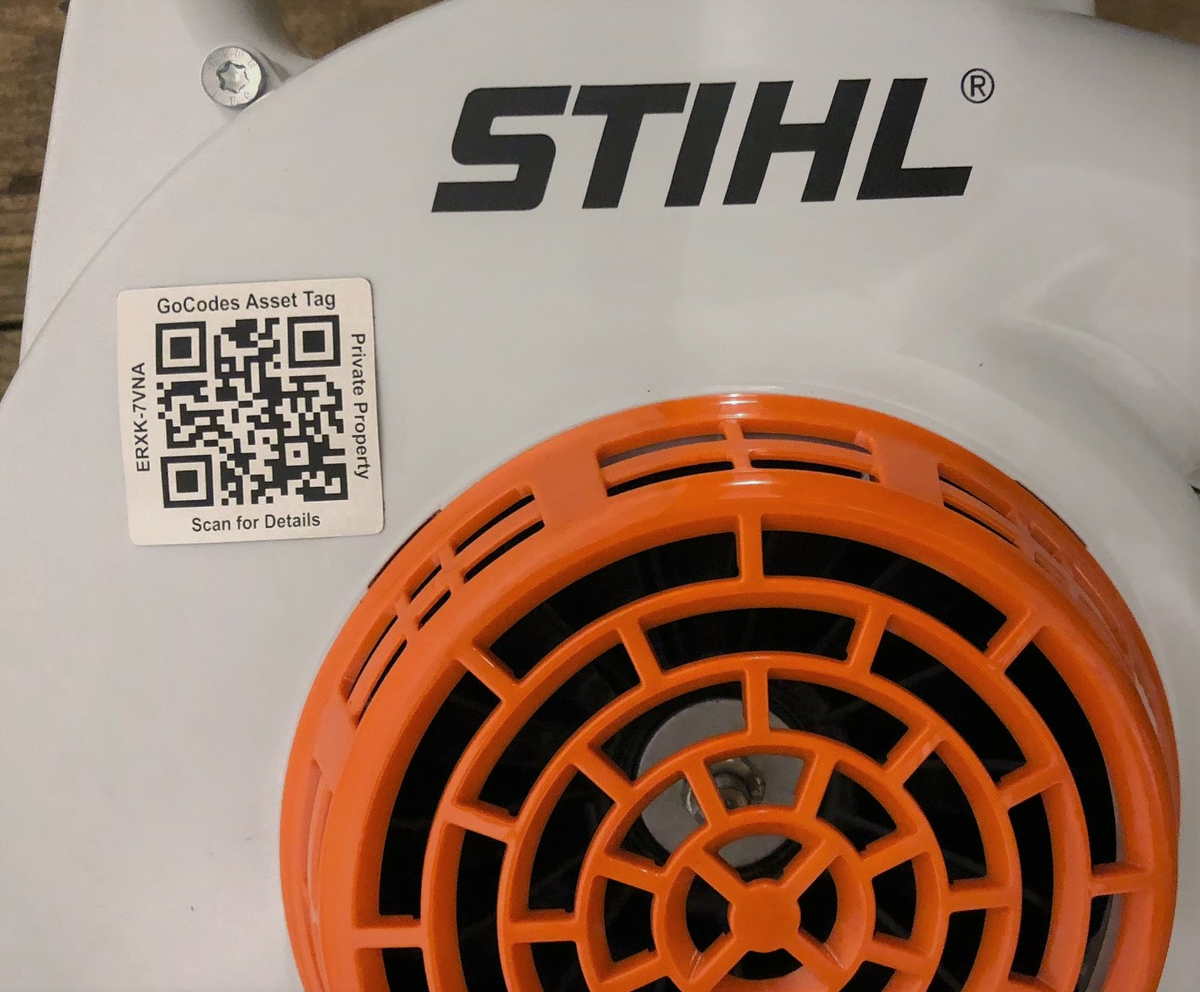
Once you (or anyone on your team) scan the QR code tag attached to a piece of equipment using your smartphone or tablet, the app will automatically pull up all the asset data you entered into the cloud-based software in the first step.
This includes various types of maintenance-related data, as you can see below.
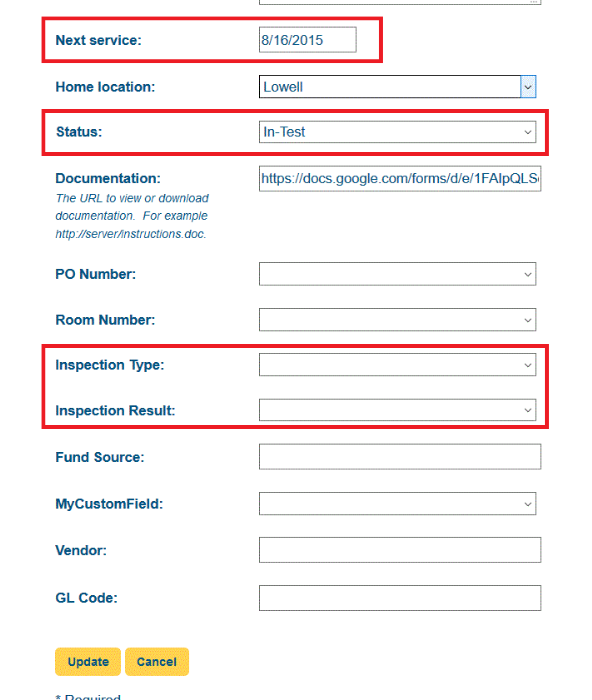
Being able to scan the tags comes especially handy when you have multiple pieces of identical equipment.
Instead of guessing which one of the two excavators on your equipment list needs maintenance due to hydraulic system failure, you can simply scan the tag and know for sure.
As you can see, tagging your equipment facilitates quick and easy access to all the essential maintenance information, thereby streamlining the maintenance tracking process.
Establish a Maintenance Schedule
Now that you have a comprehensive list of all your equipment and tags on every piece you want to track maintenance for, it is time to develop a maintenance schedule.
This step is crucial for the following reasons:
1. You can’t simply send off all of your equipment for maintenance at the same time every so often and call it a day, as this would make it impossible for you to do any work for days or even weeks.
2. No two pieces of equipment are the same—each one is going to have its own usage patterns and OEM maintenance recommendations that affect maintenance frequency.
In other words, there are no shortcuts when it comes to establishing an equipment maintenance schedule.
Though this task can be quite time-consuming—especially if you have a lot of equipment—it is vital to complete it, as a good maintenance schedule provides insight into maintenance activities, thus helping you track them.
Marius Pick, Logistics Manager at Afrigrit, a company that specializes in providing solutions for the construction industry, explains how they benefitted from a good maintenance schedule.
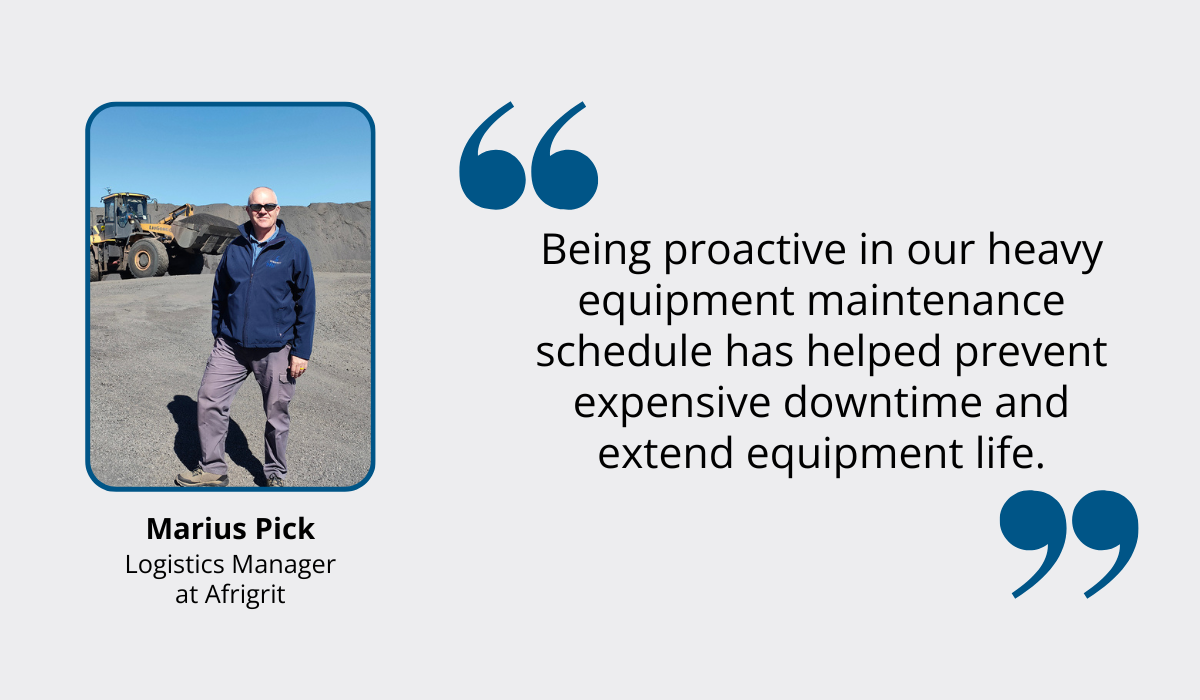
In other words, a good maintenance schedule can help you proactively perform inspections and tasks that will prevent minor hiccups from turning into expensive breakdowns and safety hazards.
So, let’s discuss what actions you need to take in order to develop one.
For starters, ask yourself some basic questions as guidance:
- What are the original equipment manufacturer’s (OEM) recommendations?
- What do the equipment usage patterns look like?
- What are the equipment’s historical maintenance records like?
- Are there regulatory standards that mandate specific maintenance intervals?
Aside from that, you can take the following factors into account when determining maintenance intervals:
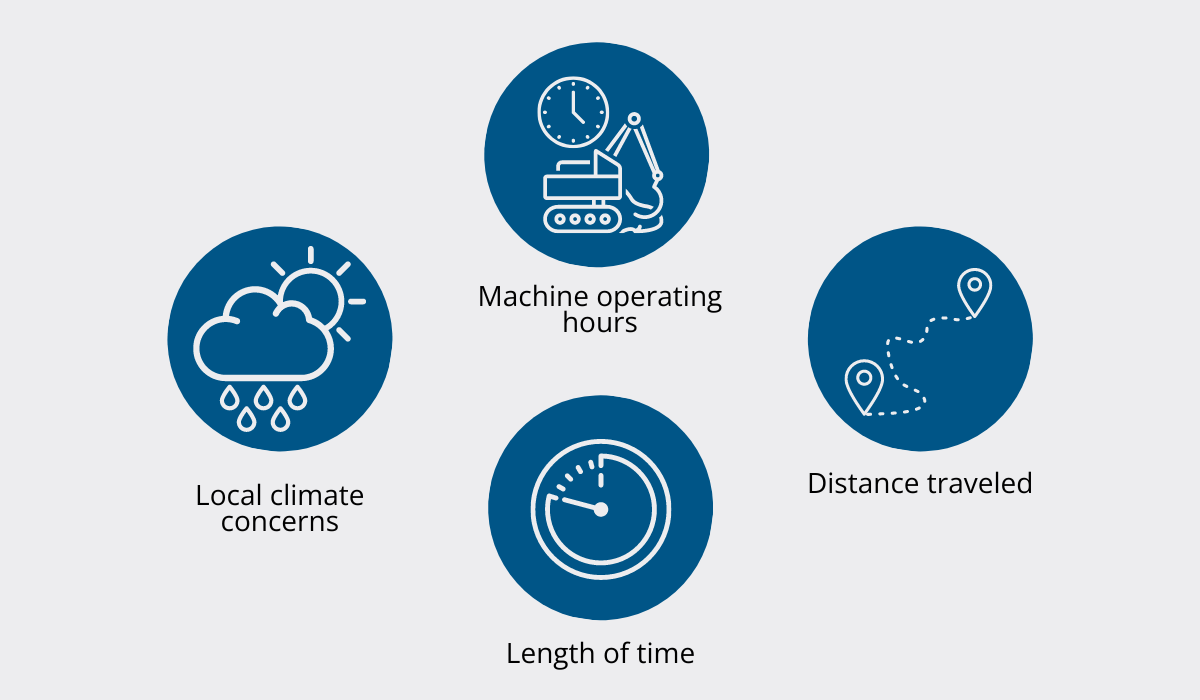
Tyler Smith, Product Manager at Volvo Construction Equipment, especially highlights the importance of following OEM recommendations:
“Always follow the OEM recommended service plan because OEMs have studied when those tasks should be completed to be the most cost-effective and to meet the warranty terms. There are daily checks, and even weekly checks and services that typically need to be completed at 500 hours – for example, oil changes, fuel filters, and service belts.”
With that in mind, you can create a schedule that will help you ensure all maintenance tasks are performed at appropriate intervals, thus making sure your equipment stays in good mechanical health for as long as possible.
Aside from that, a maintenance schedule is going to provide you with insights invaluable for proper equipment maintenance tracking, so don’t underestimate its importance.
Record Maintenance Activities
All of the activities we described in the previous sections—creating an equipment inventory, tagging your equipment, and developing a maintenance schedule—won’t do much for your maintenance tracking efforts without this next step:
Keeping a record of all your equipment maintenance activities.
Namely, when the time comes to actually perform maintenance, you need to have workflows in place that will allow you to record it consistently.
This is going to provide you with a comprehensive maintenance database—with data about all the times the maintenance was performed, what was done, and who performed it.
That way, you can keep track of the overall maintenance status of your equipment, but also identify any recurring issues and address them accordingly.
Rex Sherburn, Heavy Equipment Mechanic at Hanford Mission Integration Solutions, explains:
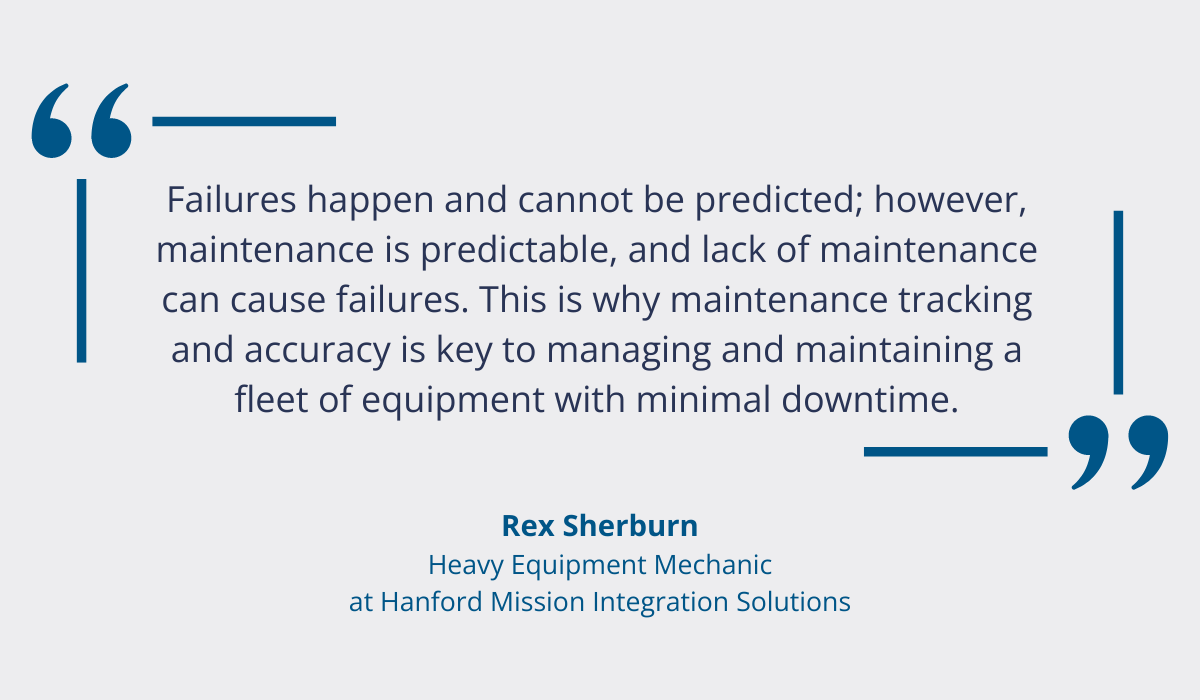
Aside from that, keeping a record of all your maintenance activities will help you stick to a maintenance schedule that properly supports the mechanical health of your equipment.
Think about it:
If you scheduled your excavator for a fluid check and change sometime in the past, but there is no record of the exact date it was performed or any notes on how it went, how are you supposed to know when the next maintenance is due?
And how can you confidently let your crew use it if you don’t know whether it’s safe to operate?
That is precisely why you need to prioritize keeping detailed equipment maintenance logs containing information such as:
- equipment piece name and identifier,
- date of last maintenance,
- type of maintenance performed,
- parts replaced,
- who performed the maintenance, and
- any additional notes and observations.
With GoCodes Asset Tracking, for instance, you can also get scheduled service notifications via email.
The email will notify you when your asset is due for maintenance, as well as inform you of any other relevant details about the previous service, as you can see below:
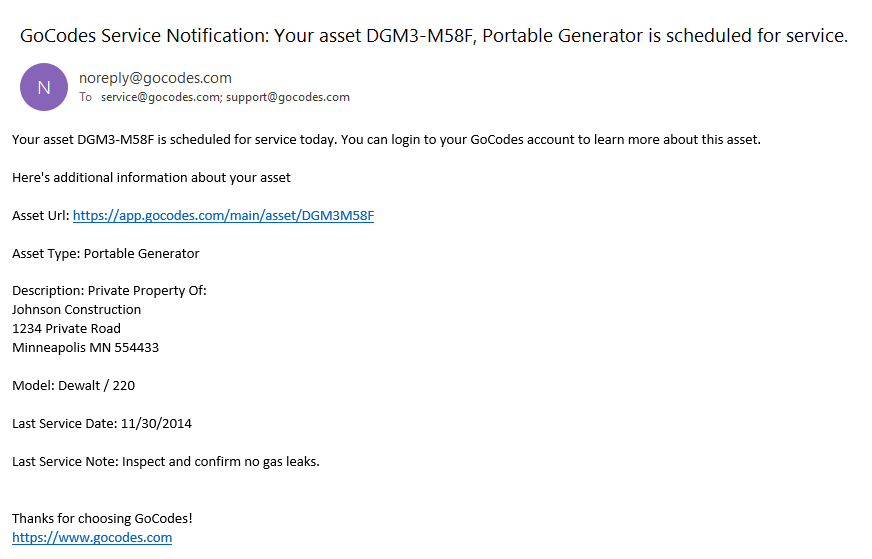
However, none of this will be possible if you don’t meticulously record all maintenance-related activities.
So make it a point to keep a thorough record of your equipment’s maintenance history, as this will allow you to make better, more data-driven decisions going forward.
Provide Employee Training on Equipment Maintenance Tracking
Now that you’ve put a lot of time and resources into optimizing your maintenance tracking process, the final thing on your to-do list is to provide training on it all to the relevant personnel.
After all, what is the point of investing in maintenance tracking solutions and the development of consistent service schedules if no one knows how to make use of them?
S.T. Wooten Corporation is a good example of a construction company that recognizes the importance of training their employees on proper equipment maintenance techniques in line with the TPR (Total Process Reliability) philosophy they adopted.
Operator care (OC) is at the forefront of their TPR approach, and its focus is on educating equipment operators on how to monitor and perform maintenance.
Jeff Radack, VP of the company’s Ready-Mix Division, says:
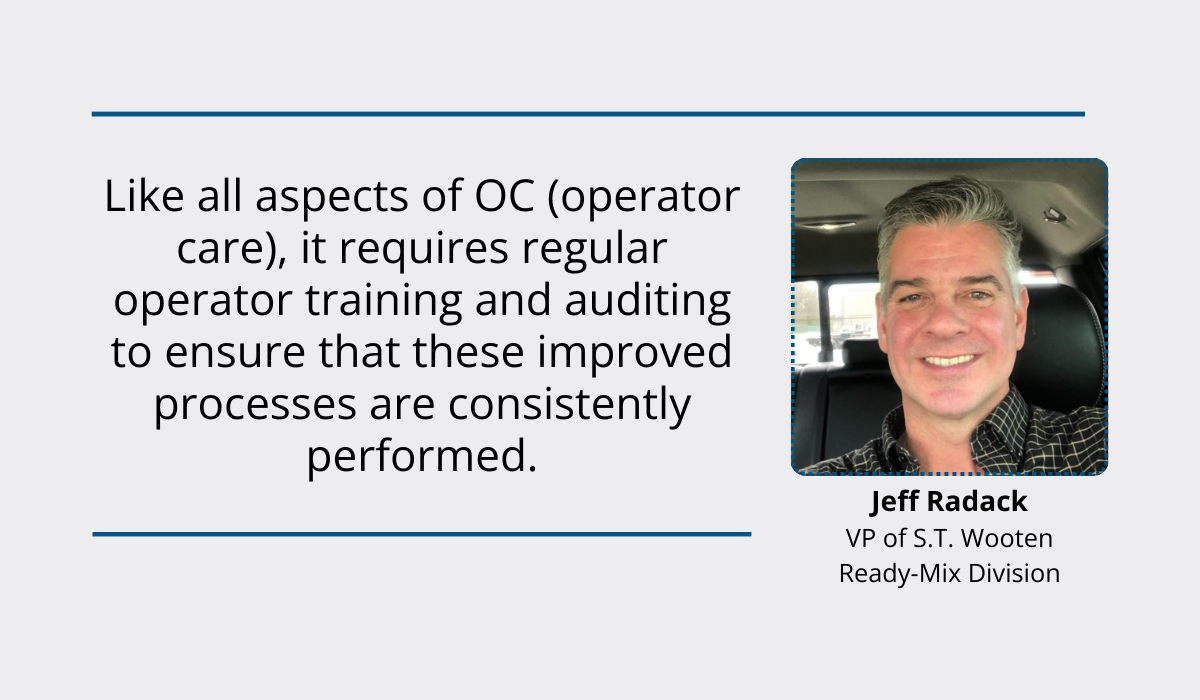
Even though it is another thing you need to invest time and money into, training your equipment operators and maintenance technicians to adopt your maintenance workflows and software solutions is essential.
Namely, not only does it increase job site safety and improve the lifespan of your equipment, but it also saves you money in the long run.
How?
Consider the following:
If you make an effort to provide training on how to properly track equipment maintenance, your employees will learn to adhere to maintenance protocols and proactively address any potential equipment issues.
In turn, this will reduce unnecessary downtime that can cause costly project delays, as well as prevent minor issues from escalating into expensive breakdowns.
So, make sure to allot some time in your schedule to explain the “why” and the “how” to your employees:
- why it’s important for them to follow the proper equipment maintenance tracking processes, and
- how to access the inventory list, follow the maintenance schedule, use the software you purchased, and keep a record of maintenance activities.
On top of that, don’t forget to let them know that you’re always there to answer any questions they may have or provide additional help.
This approach promotes accountability and gives your employees the confidence they need to bring your equipment maintenance tracking to the highest level.
Conclusion
The bottom line is: yes, performing regular and proactive equipment maintenance is key to the success of your construction projects—but so is keeping track of that maintenance.
Investing effort into optimizing your maintenance tracking workflows will help ensure that your equipment operates at peak performance levels, prevent equipment issues before they escalate, and save your construction company money.
So, if your maintenance processes still aren’t structured, try following the steps outlined in this article, and you’re bound to reap the benefits.