Considering the complexity and time required for end-of-year inventory counts, it’s understandable why most businesses would skip them if possible
And yet, no business dares avoid it, because the count delivers accurate data and key profitability insights.
This ultimate guide covers everything you need to know about conducting end-of-year inventory counts, from fundamentals and strategy to practical advice.
So what are you waiting for, let’s take a plunge together!
In this article...
Key Takeaways:
- The end-of-year inventory provides more detailed insights than cycle counts.
- Performing it is directly linked to better financial performance.
- You’ll have a hard time doing end-of-year inventory manually.
How End-of-Year Inventory Differs From Inventory Cycle Counting
Understanding the difference between an end-of-year inventory count and an inventory cycle count is crucial for efficient construction operations.
Here is a brief comparison of the two practices.
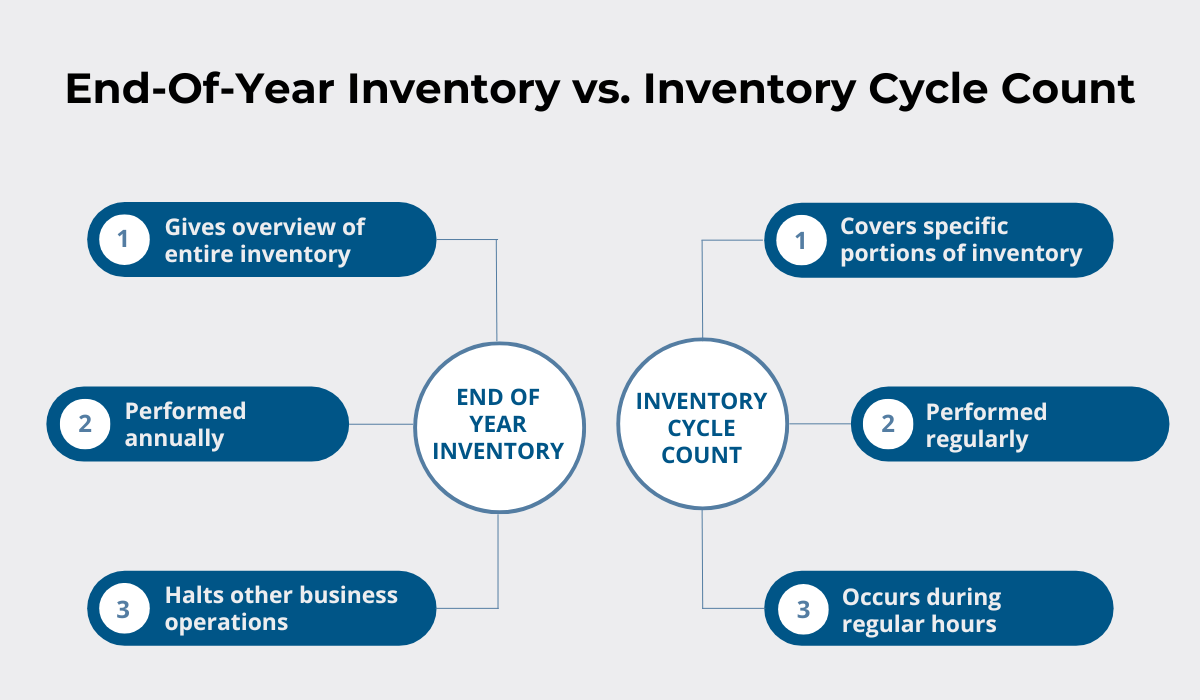
An end-of-year inventory is a comprehensive physical count that provides an overview of all inventory items currently on hand.
It is performed once a year, typically at year-end.
But here’s the important part.
The inventory list generated during an end-of-year count is exhaustive and serves as the basis for verifying records from your inventory management system.
Any discrepancies with current records will likely be revealed during this inventory count.
In contrast, inventory cycle counts are conducted periodically and focus on smaller portions of the inventory, providing systematic and regular audits.
Since cycle counts follow a repeatable schedule and target specific sections of the inventory, they can easily be conducted during regular business hours.
Conversely, an end-of-year inventory count typically halts the entire operation.
CATEGORY | PHYSICAL COUNT | CYCLE COUNT |
---|---|---|
SCHEDULING | Annually (or occasionally) | Regularly (daily, weekly) |
SCALE | Comprehensive inventory count, all items at once | Selective inventory count, groups of items over a specific period |
STAFFING | Involves many staff members, and demands their full attention for the duration of the count | Involves a small team of staff, counting tasks are usually incorporated alongside other responsibilities |
DISRUPTION | High, affects regular operations, requiring detailed planning and coordination | Low, once the system is introduced, counts occur alongside other operations |
FLEXIBILITY | Minimal, realization depends on other factors | High, parameters for counts are readily customizable |
COMPANY TYPE | Often preferred by companies with limited inventories or specific financial reporting demands | Often preferred by companies with large and complex inventories |
Ultimately, both practices have their purpose.
Therefore, it’s not about choosing one over the other but rather maximizing the benefits of each to best suit your needs.
Now that we’ve clarified this distinction, let’s explore the reasons for performing end-of-year inventory counts.
Why Perform an End-of-Year Inventory Count
Because knowing what you own is crucial for making informed decisions.
Conducting a year-end inventory count ensures greater visibility and accurate records, impacting businesses on multiple levels.
Construction companies usually distribute a large volume of items across jobs and locations.
Cross-checking digital records with physical inventory helps businesses manage these complexities, boosting the accuracy and efficiency of their operations.
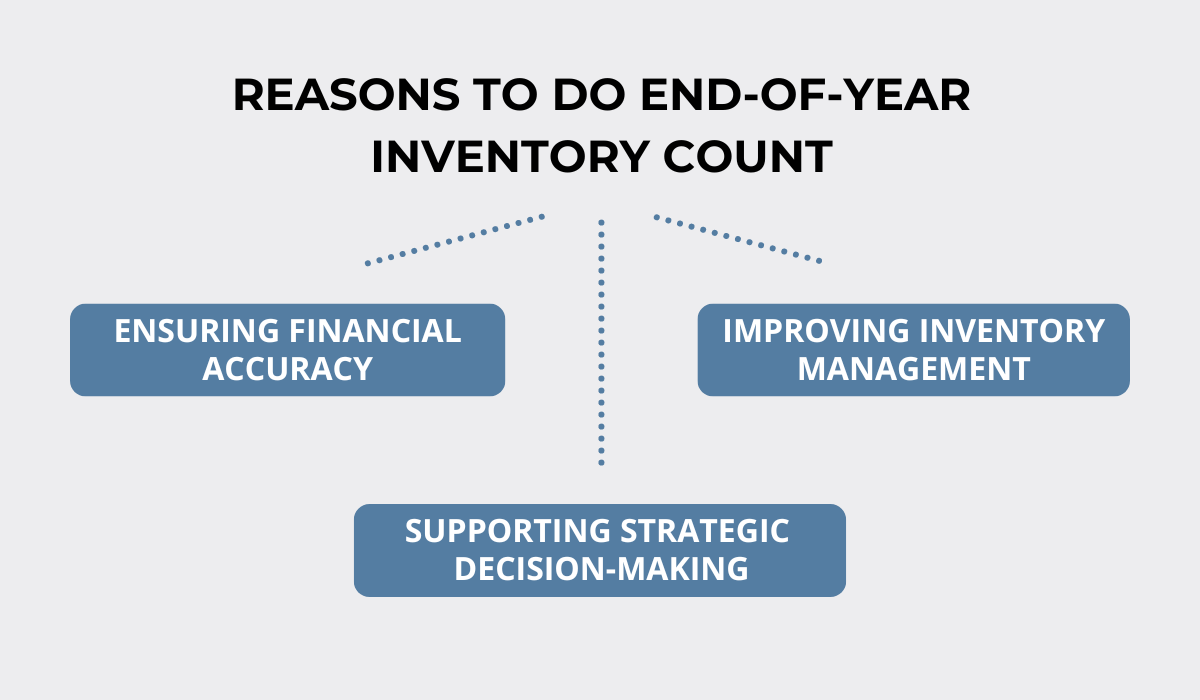
We’ll look into three key reasons behind doing end-of-year inventory counts in more detail.
Improved Financial Accuracy
Inventory valuation affects the calculation of the cost of goods sold (COGS), a major factor in pricing construction projects.
It is also a key piece of information for defining your taxable income, and inaccuracies can cause a ripple effect. Plant Manager at S.I.L. Group, Hamed Ali confirms that:
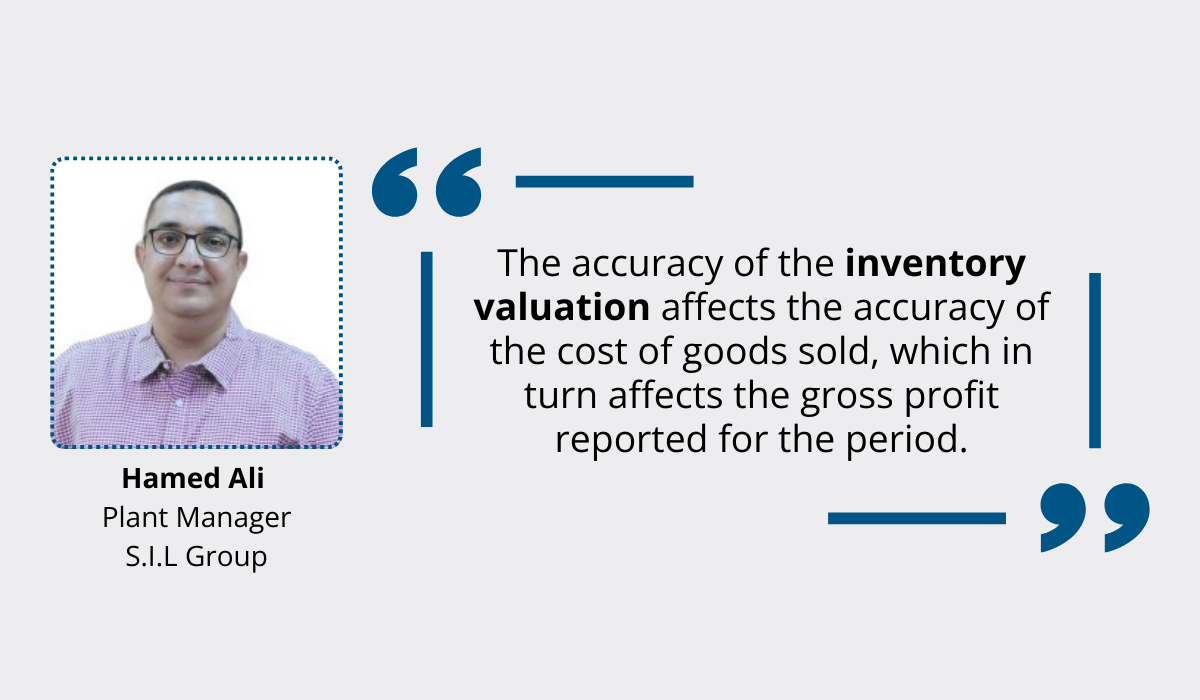
Overall, incorrect inventory valuation distorts the financial picture of your business.
In industries with strict compliance requirements, up-to-date inventory also ensures better adherence to regulatory standards, helping you avoid additional costs related to tax and legal issues.
Better Inventory Management
An end-of-year inventory count provides data on actual inventory levels, enabling inventory optimization and reduction of unnecessary expenses.
These costly scenarios usually revolve around inefficient ordering, which leads to either overstocking or stockouts.
Neither option is good, because the former increases storage costs and can lead to equipment obsolescence, while the latter usually means running out of raw materials and having to halt operations.
Effective inventory management and doing annual physical counts can help you find the right balance, which has its financial and operational perks.
One Supply Chain Analyst, Vinyak Bhadani, points that out in his article on LinkedIn:
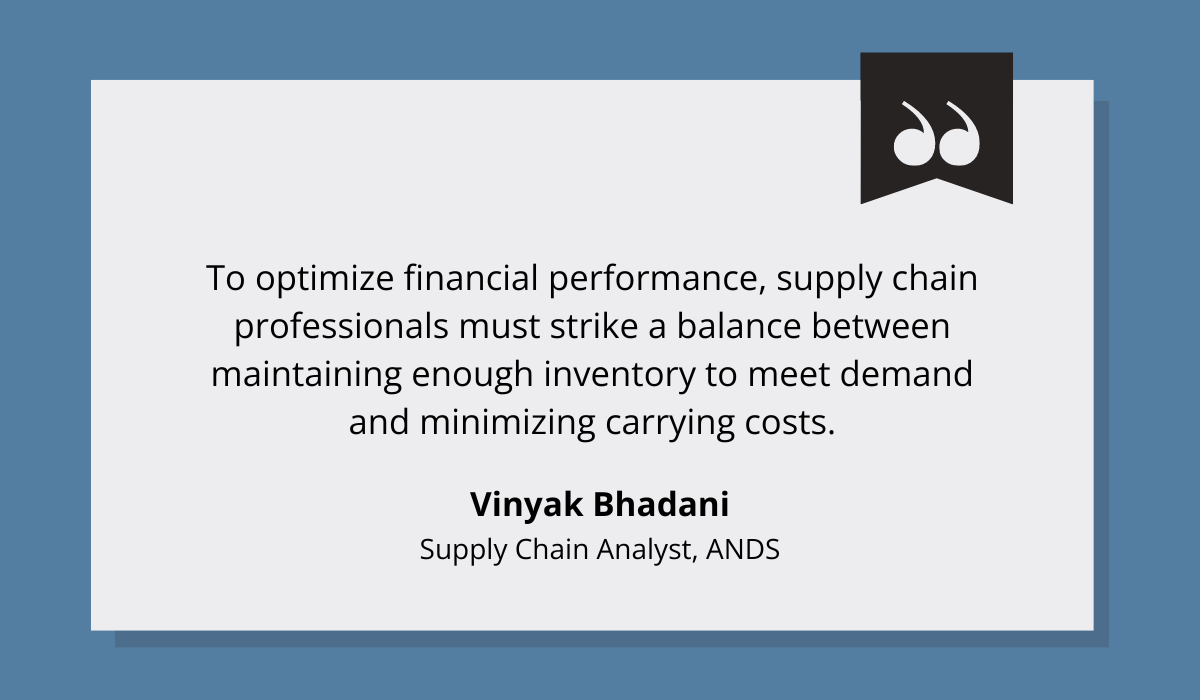
Nevertheless, the value of efficient supply chain operations can easily be offset by poor inventory control, often resulting in inventory shrinkage.
Inventory shrinkage refers to the difference between recorded and actual inventory and can be caused by various factors, including:
- Human error
- Damaged or expired stock
- Theft or loss of inventory
While some shrinkage is inevitable, keeping track of it is necessary for pinpointing the causes, because the costs can easily add up.
If we look at the retail industry, we’re talking big numbers. The NRF’s 2022 report on retail industry shrinkage indicates a shocking $95.4 billion in losses, and that’s just for one year!
One company doesn’t compare to the whole industry, but you should minimize shrinkage nevertheless.
Conducting end-of-year counts enables construction companies to detect shrinkage, and implement stronger inventory control measures to address this and other common challenges.
It also paves the way for making better future decisions.
More Strategic Decision-Making
Businesses with accurate inventory records are better positioned to make strategic decisions about current and future projects.
For example, annual inventory counts provide better insights into inventory usage.
These insights from inventory usage can help in forecasting future demand, improving budgeting and cost estimation, and ultimately helping you meet deadlines.
Additionally, inventory counts might reveal operational problems, such as inadequate storage leading to inventory damage.
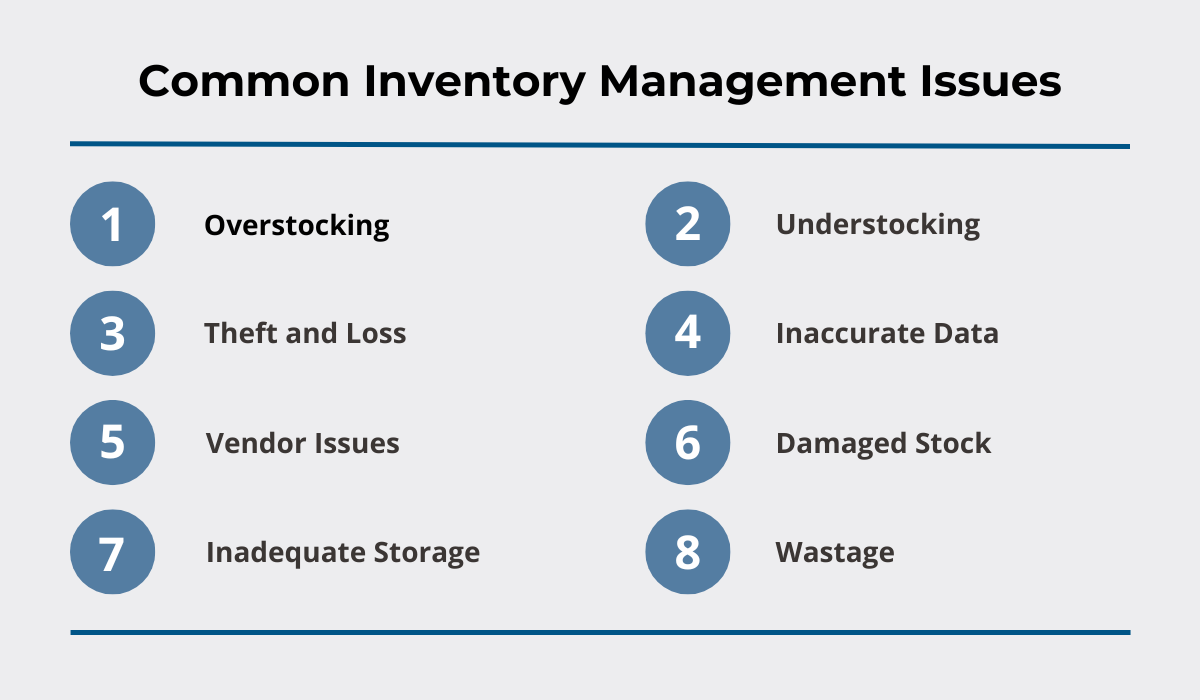
End-of-year inventory counts provide an opportunity to identify and mitigate these problems.
How Inventory Management Software Can Help
Inventory management software offers real-time visibility into item locations and usage, automating and streamlining various tasks.
For end-of-year inventory counts, the benefits of software are clear: it reduces manual counting and increases overall precision.
The advantages of specialized software become even clearer when compared to spreadsheets, the most common alternative.
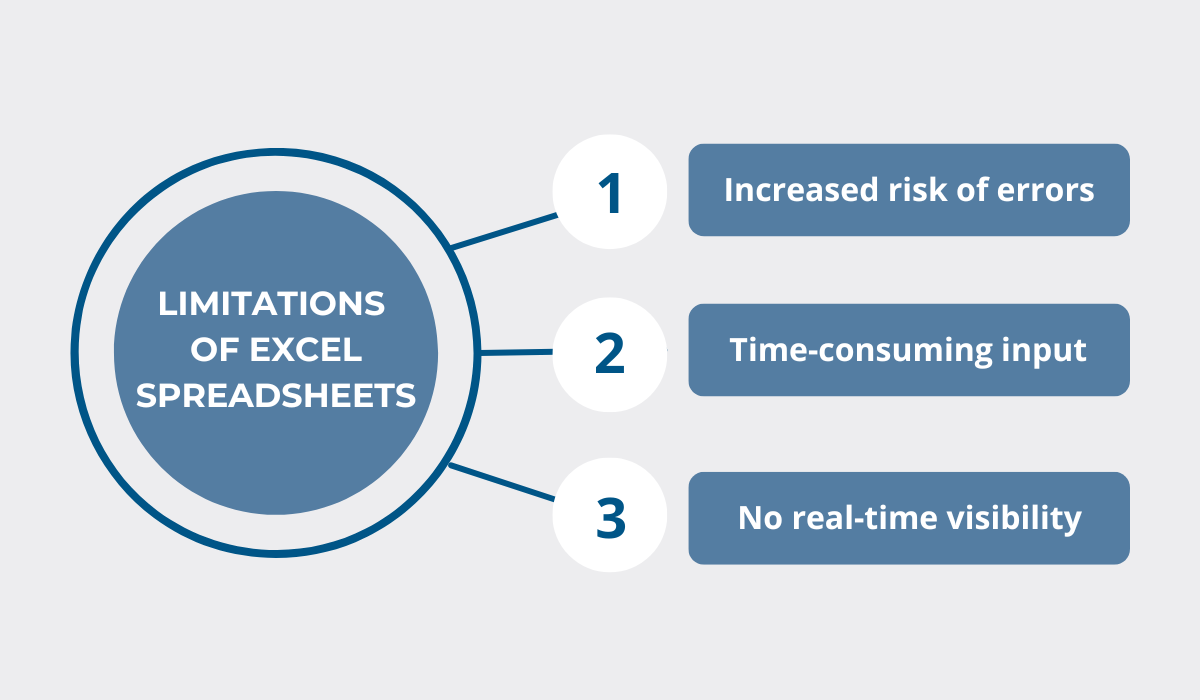
Manual data input allows for many errors and inconsistencies, consuming time without providing real-time inventory updates.
As noted by a Reddit user, even the most affordable solutions with limited features justify the investment due to significant time savings and increased productivity.
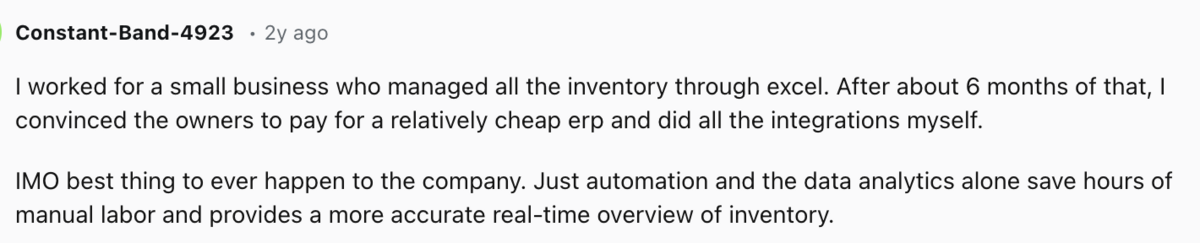
While spreadsheets may seem convenient due to their widespread use, their drawbacks become apparent over time, especially as your company scales its operations.
Inventory management software offers valuable qualities, such as a robust reporting system that enables data-driven decisions and saves time.
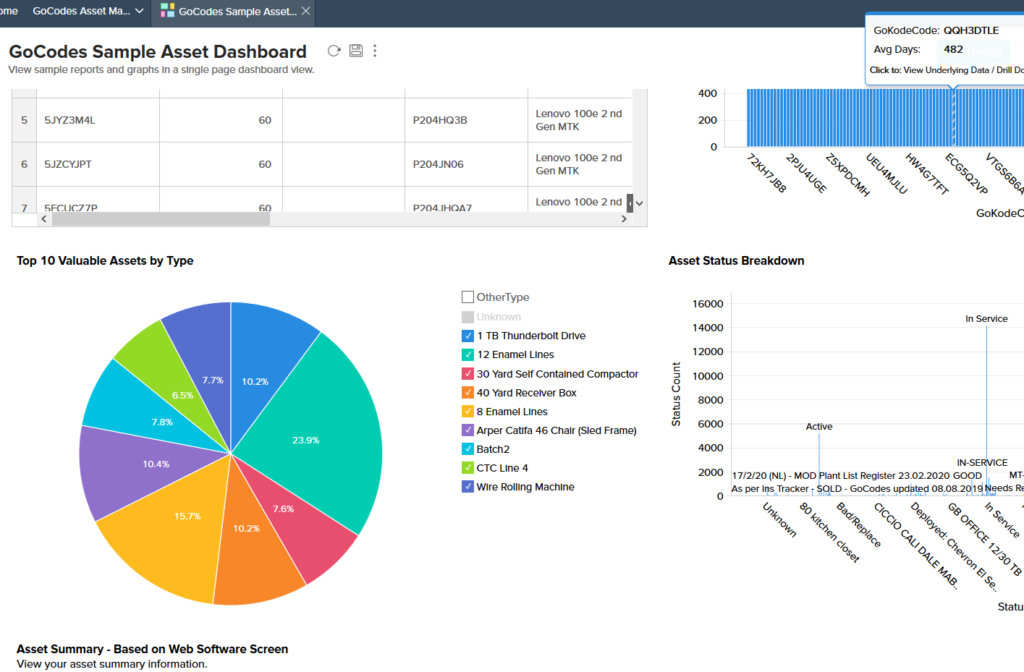
Now, how does this work in practice?
Firstly, inventory records are automatically updated with each action, such as entering item quantities during the end-of-year inventory count.
Changes are immediately reflected on the dashboard, enabling users to flag discrepancies and verify information before financial reporting and auditing.
Additionally, data can be accessed or exported on any device, improving resource management and cost savings.
Naturally, introducing new software usually requires an adjustment period, which is why companies prefer investing in user-friendly solutions.
The ease of use makes our asset-tracking solution GoCodes one of the best in its category, further supported by its versatility and powerful features.
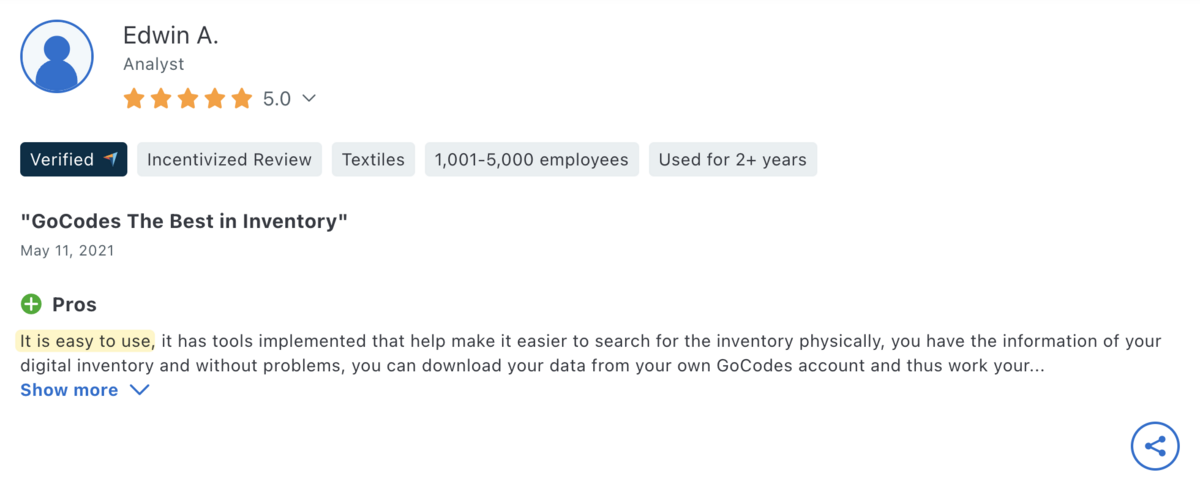
With GoCodes, construction companies can automate complex inventory tasks easily, from generating inventory reports to reordering stock.
Users can set up low-stock alerts to complement cycle counting efforts and use built-in barcoding functionalities to speed up the physical counts.
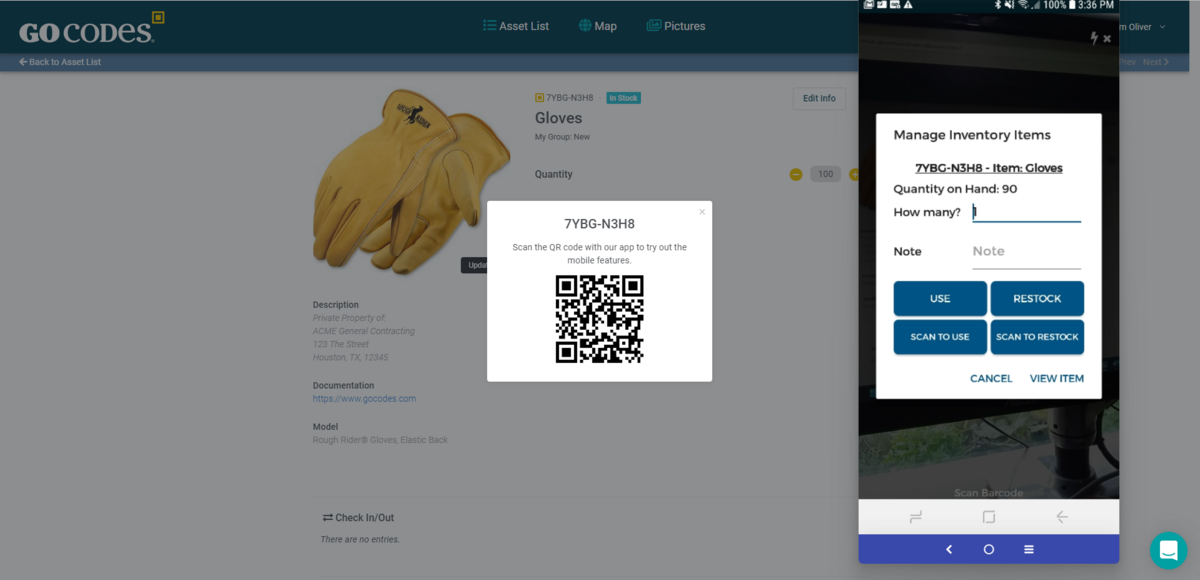
Even if we put aside the convenience of relying on software solutions for end-of-year inventory counts, these systems make inventory management as hassle-free as possible.
This is one of many compelling reasons for construction businesses to invest in technology.
Conclusion
End-of-year inventory counts are essential.
They form the backbone of accurate financial reporting, project planning, and efficient inventory management.
We hope the time-saving and cost-reducing benefits, enhanced by inventory management technology, convince you to make year-end inventory counts a regular practice.
And if you ever get stuck, feel free to revisit this guide!