Key Takeaways:
- Underpricing yourself wins bids, but can lead to unprofitable projects.
- Only a small number of construction companies know their costs.
- A good site manager can save you money in a few different ways.
Saving money is an ongoing challenge in construction.
Sometimes, costs keep piling up due to unfavorable industry trends and market shifts, but a lot of it boils down to the efficiency of your day-to-day operations and overall planning.
In this article, we’ll focus on what you can control, bringing you five actionable tips to turn things around for your business.
If you’re struggling to keep the costs in check and want your construction firm to turn more profit, join us for a deep dive below!
In this article...
Don’t Underestimate Costs Just to Win Bids
Winning bids means new projects which are the lifeblood of construction companies, but only if you don’t underestimate the related costs.
The construction bidding process rests on managing two major uncertainties, which require you to assess the following:
- What price works for the investor and how will my bid compare to the others?
- How closely does it reflect the actual costs of carrying out work?
Lowering the price to secure the bid is a common scenario.
The odds are you won’t win bids if you submit realistic or overestimated costs, as demonstrated by John Currie on behalf of CPA Ireland, one of the country’s leading accountancy bodies.
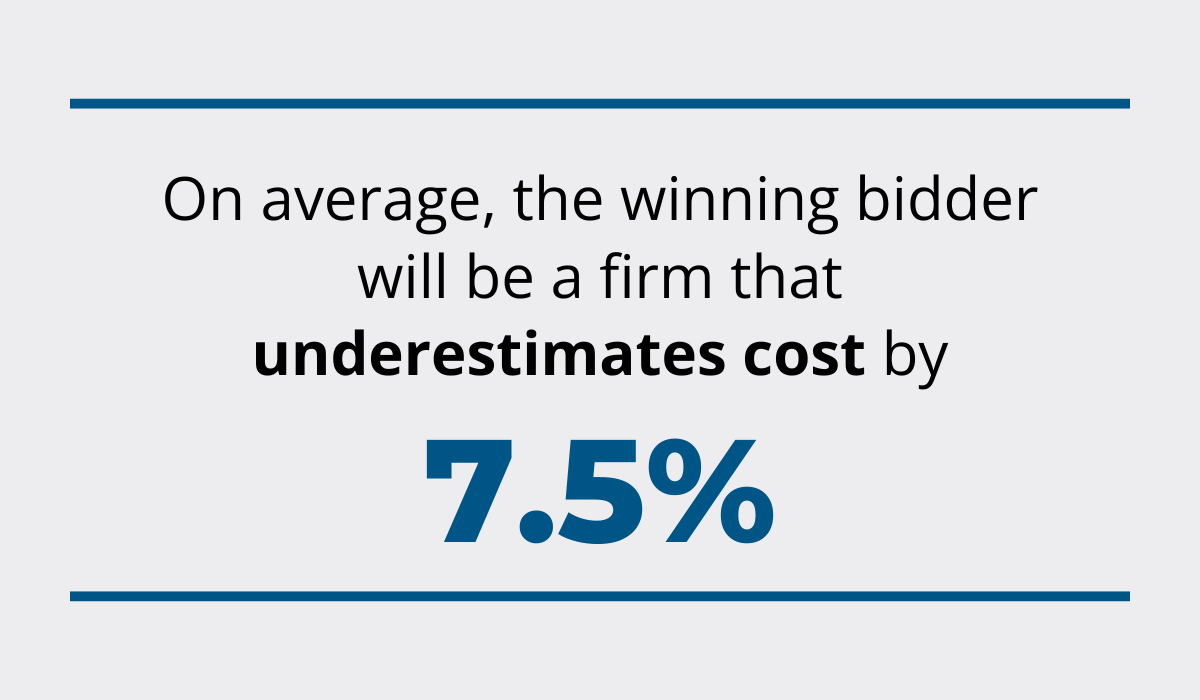
But when bidding disregards the uncertainty of actual costs, it can quickly blow up in your face.
This is why it’s important to regularly monitor your job costs, know your production rates, and actual overhead, as well as profit goals.
Unfortunately, this is rarely the case in construction.
George Hedley, a professional business coach (CPBC), public speaker (CSP), and construction company owner for 40+ years confirms that.
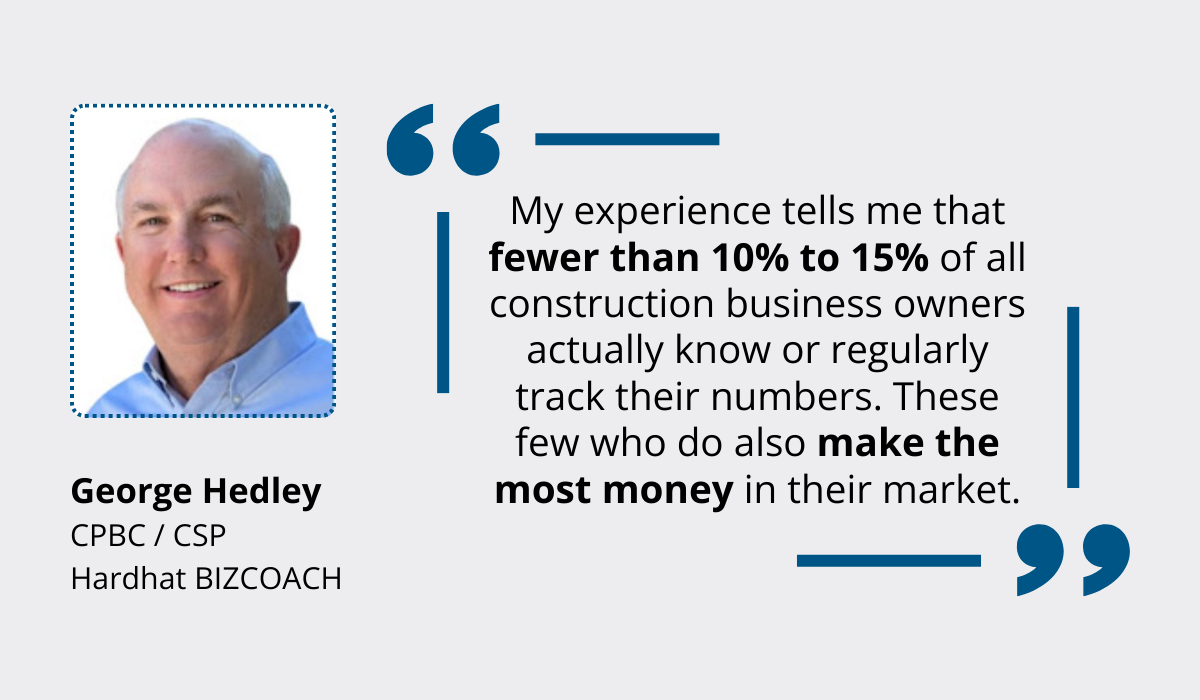
Knowing your figures is essential for effective bidding, and this checklist can be a helpful starting point.
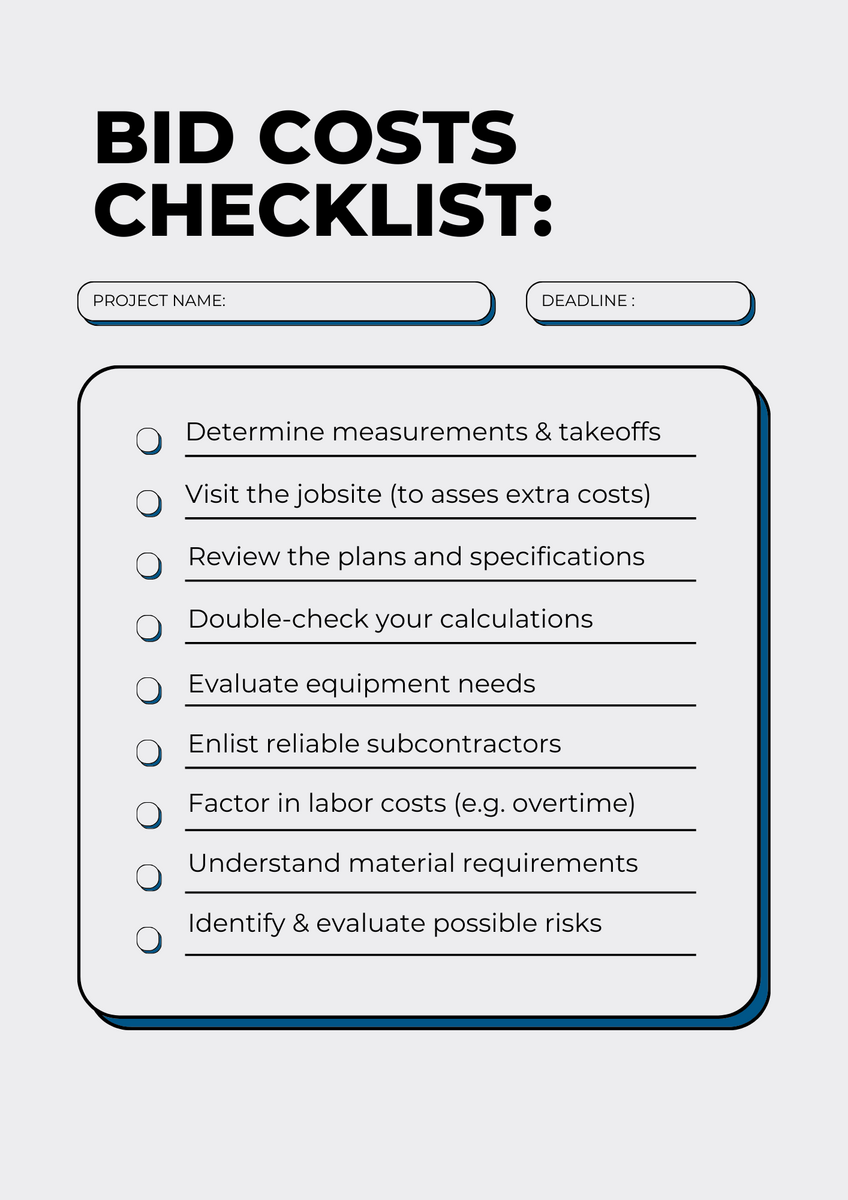
Having accounted for the different costs and preparing all the bid forms and documentation is just the first step.
Given that the cheapest offers usually win bids, the key is to find a good balance between knowing your actual costs and trying to reduce them to win the bid.
Finding the right balance can be tricky, but when you’re backed by accurate numbers, you’ll be in a much better position to navigate the situation.
Find Reliable Suppliers
Finding reliable suppliers for materials, equipment, and services is essential for successful project completion.
What makes reliable suppliers a necessity, rather than a luxury, is the fact that they can easily make or break your project, either through incompetence or deceitful tactics.
If dealing with hidden fees, inventory padding, bribery, and (deliberate) delays of essential construction materials sounds familiar to you, you’re very aware that these practices just keep mounting the costs.
The only solution to save money, both immediately and in the long run, is to prioritize finding and keeping reliable suppliers.
An inventory and procurement management expert, Gipe Sela, highlights the importance of supplier reliability and the impact of nurturing these partnerships in the long term.
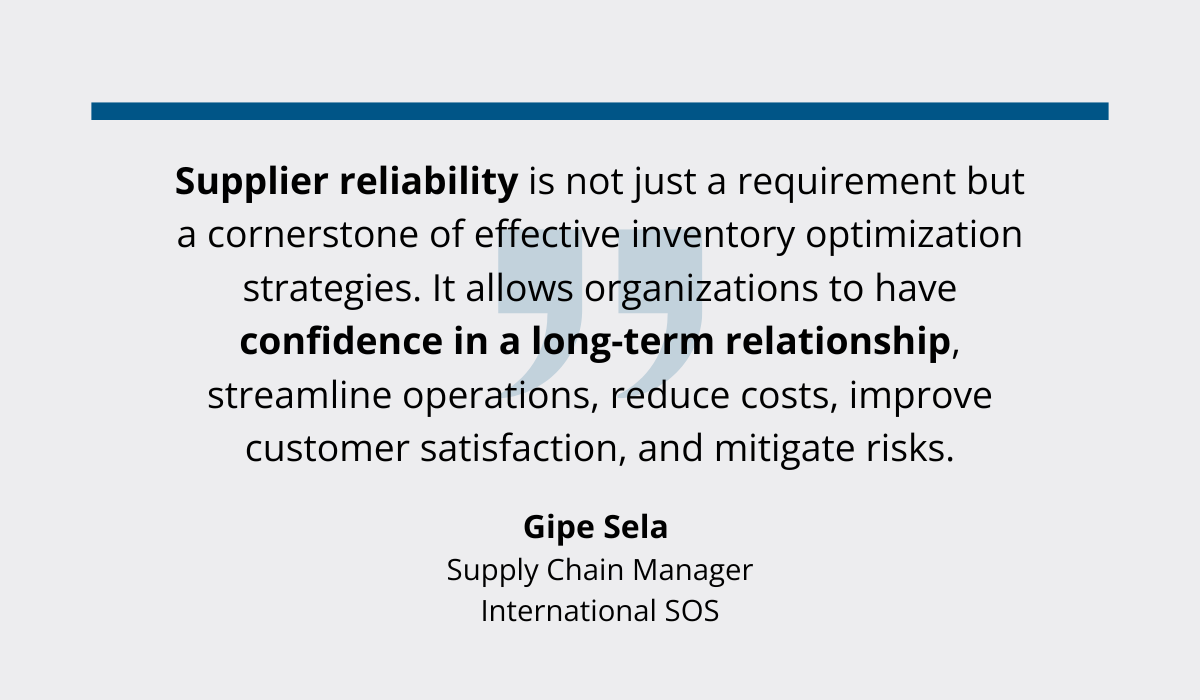
Parallel to reducing costs, companies that invest in building supplier relationships also streamline their operations, which opens the door to better risk management and profitability.
So, how do you identify reliable suppliers?
Besides checking their certifications and quality assurance processes, it’s important to nurture open communication from the get-go.
Be upfront about your expectations, and discuss the following points in detail:
- Delivery requirements and timelines
- Minimum order quantities
- Contingency plans
- Pricing structure
- Payment terms
- Warranties
If you’re satisfied with their approach and the commitment they’re willing to make, the next step is building a partnership, rather than a purely transactional relationship.
This means keeping open lines of communication, encouraging regular updates and two-way feedback, joint planning, but also periodic reassessments of the agreement, to ensure a match between needs and capabilities.
In turn, you can count on palpable benefits such as competitive pricing, bulk buying discounts, or having access to new products sooner.
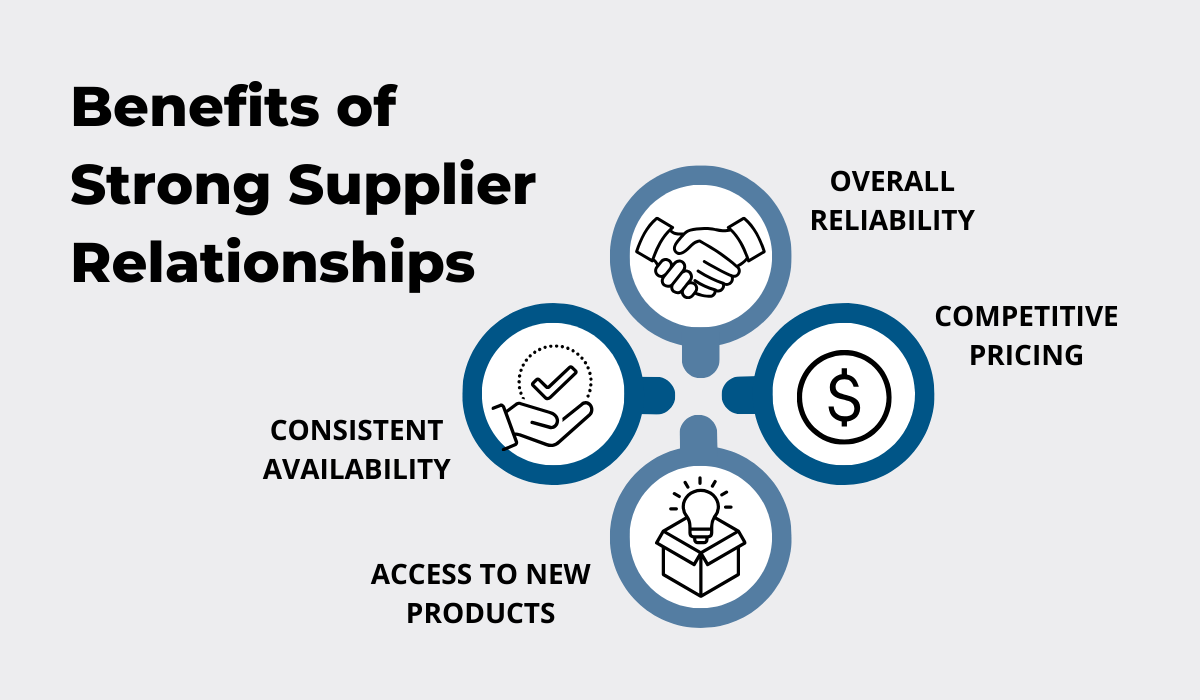
In the face of major or minor supply chain disruptions, having suppliers you can trust in your corner will be particularly worthwhile.
Have a Competent Site Manager
Being able to rely on a competent site manager to oversee daily operations and address any issues as they arise means unlocking significant cost savings.
When it comes to job sites, a seemingly minor disruption can easily create a ripple effect of delays, cost overruns, and more.
This is why site managers, who handle people, materials, and various tasks, are either the solution that drives operational excellence or a part of the problem.
The 2023 FMI study supports this claim, as the findings show the negative effects of poor site management, and underline the huge cost savings potential of improved management practices.
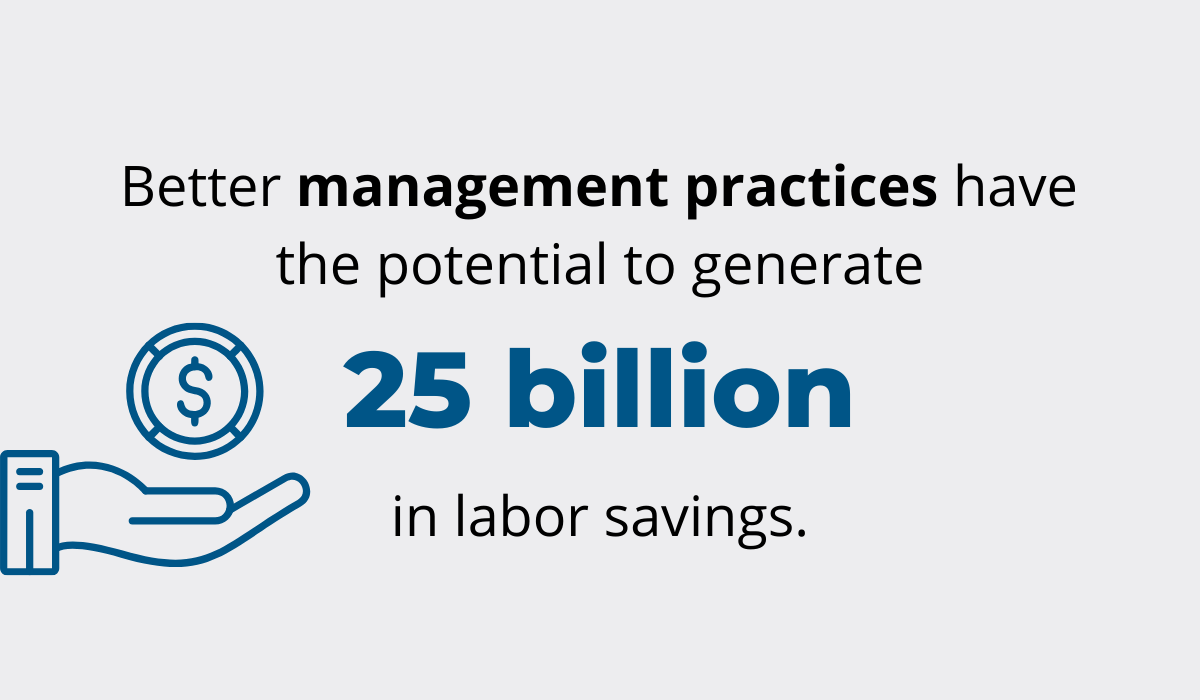
Since better management practices depend on people who implement them, your first step is hiring a competent site manager who will ensure all workers meet quality requirements, deadlines and reach targets while sticking to budget.
In addition to driving operational excellence, site managers act as the link between the senior management and the crew, sharing the most recent updates on the project.
There are a couple of things to pay attention to when selecting the perfect candidate for this role, starting with their organizational abilities and communication skills.
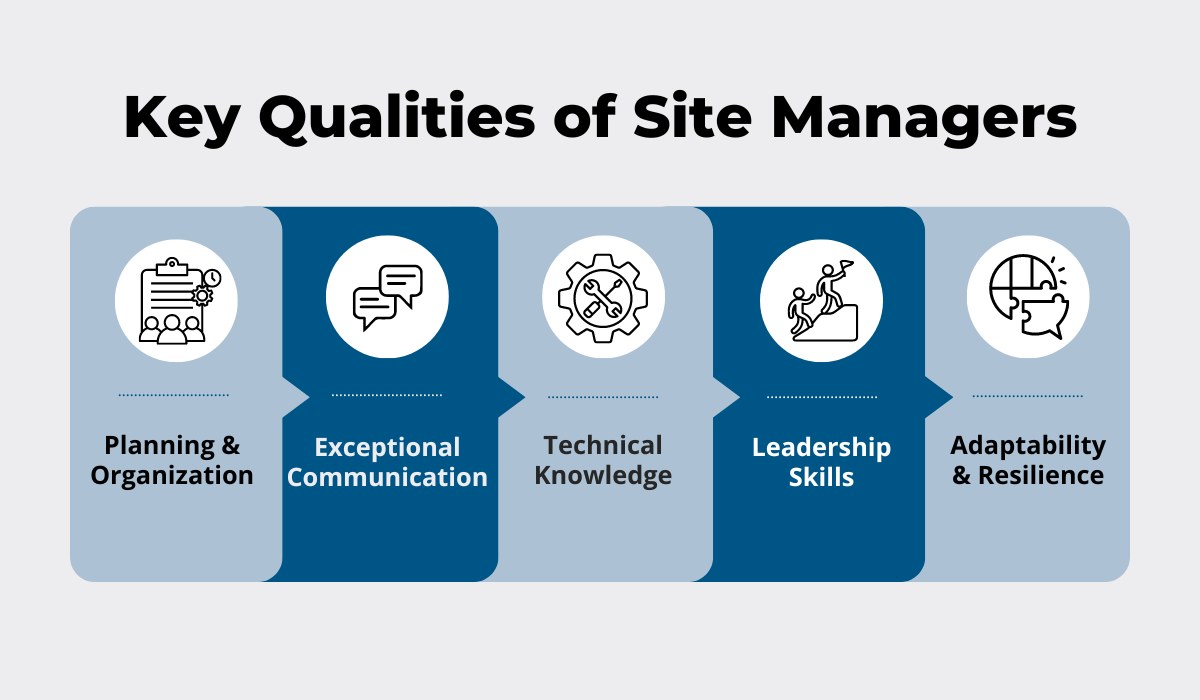
Site managers need to be adaptable to different circumstances and have a proactive approach to problem-solving, as well as excellent delegation and negotiation skills to manage the crew and all subcontractors.
However, these soft skills and habits must be complemented by technical knowledge and sufficient experience, giving site managers credibility and ensuring proper quality control.
Finally, good leadership skills make a world of difference, inspiring trust among other employees.
Construction management engineer, Pouya Partonia, shared his thoughts on this topic on LinkedIn, highlighting consistent actions, decisiveness, and diligence as central to good leadership.
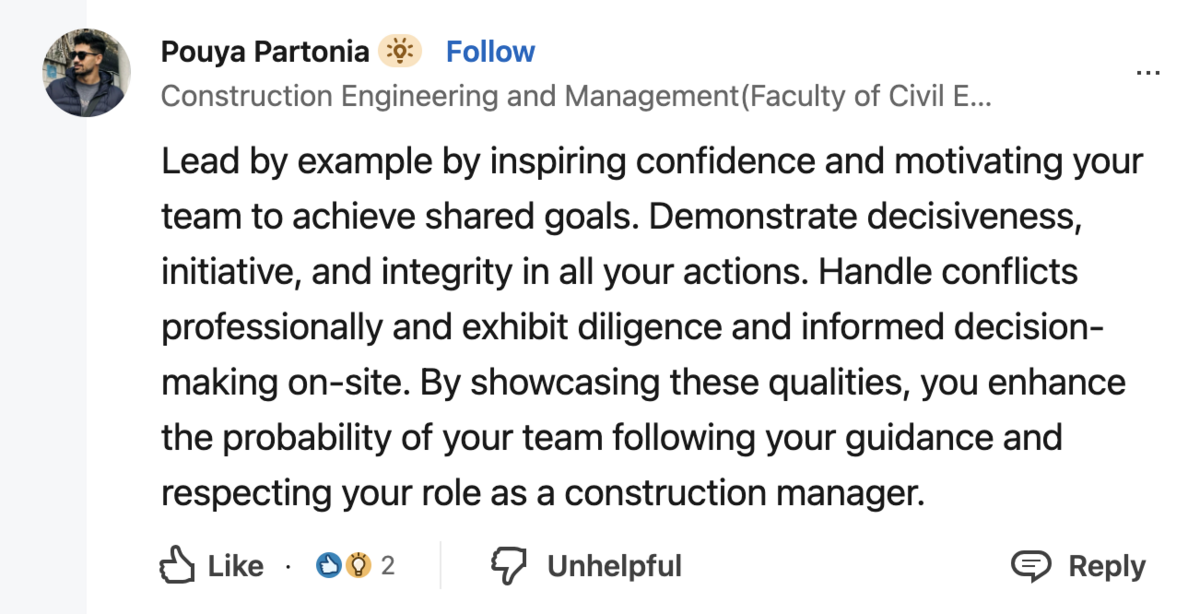
The site manager’s informed decision-making and overall approach are bound to positively impact your on-site activities, helping you control the expenses while successfully bringing projects to a close.
Manage Your Equipment Better
Properly managed construction equipment doesn’t just help you reduce costs: it actively increases profits.
To help put this into perspective, here’s one interesting finding.
A study published in the academic journal IRJET estimated that equipment costs take up anywhere from 10 to 30% of total project costs in construction.
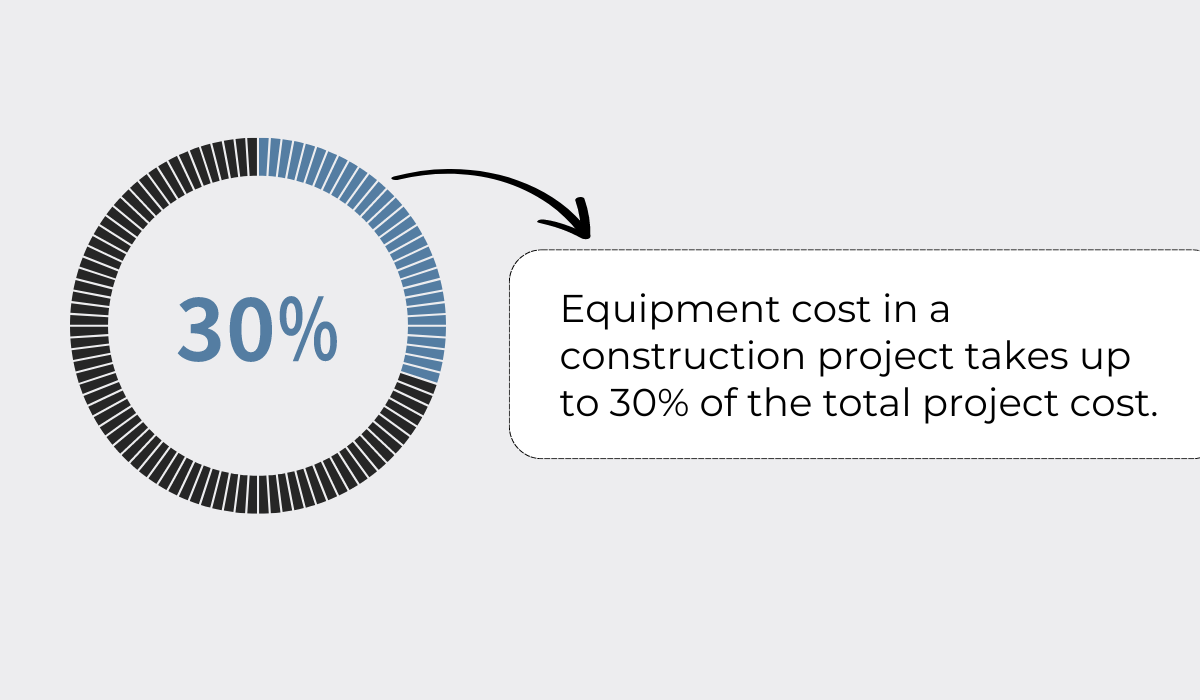
This means that equipment costs can reach nearly one-third of the project’s total costs, but how does this happen exactly?
Let’s say your company secured a large-scale project and you have to purchase new power tools and bring in more heavy machinery.
The costs add up if your existing equipment hasn’t been serviced regularly and you need to replace it sooner than expected, and every time something is misplaced or stolen.
And then there’s the productivity issue. Not being able to find equipment quickly also costs you money.
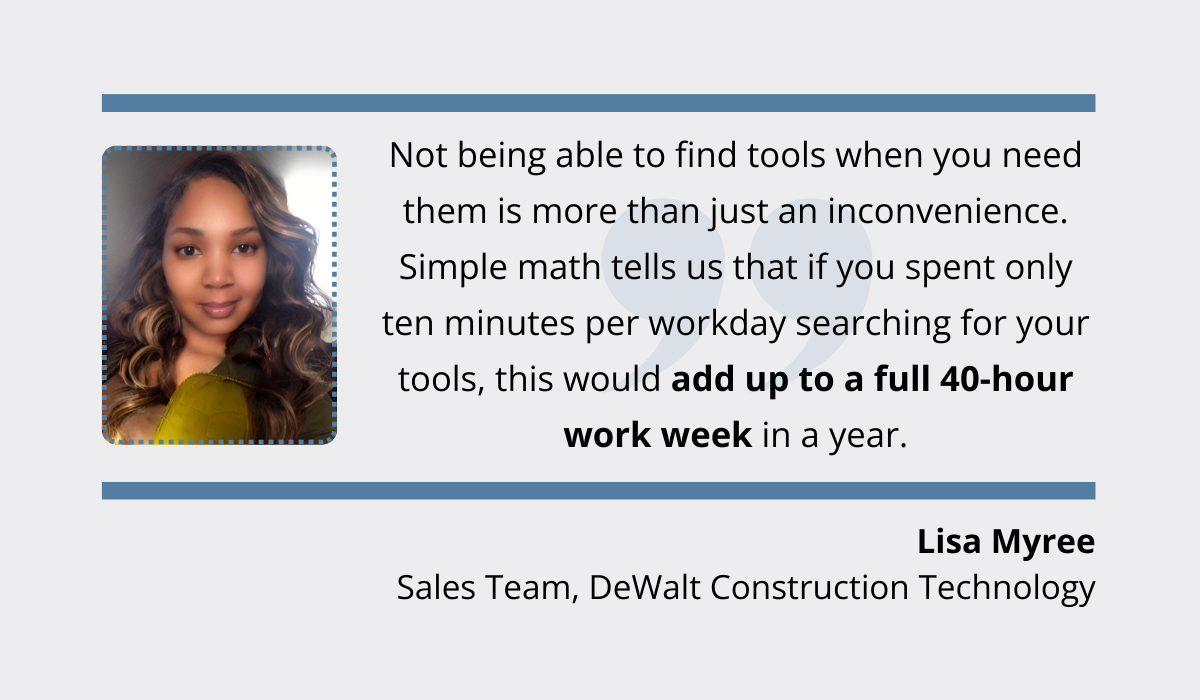
So, how can you keep equipment-related costs in check?
By better maintaining and tracking your equipment.
Doing so, you can see both tangible and intangible benefits, such as:
- improved asset utilization,
- increased productivity,
- reduced downtime,
- better compliance,
- enhanced customer satisfaction,
- improved brand reputation.
Together, these benefits translate to major cost savings.
Simply knowing each asset’s location at any given moment streamlines resource allocation and on-site activities, enabling you to minimize any inefficiencies.
And any additional insights into equipment usage means moving beyond reactive maintenance and toward lifespan-extending, cost-saving preventive maintenance strategies.
Even just keeping your equipment documentation and warranties organized contributes to savings by making planning for tax deductions easier.
You can do all this and more by adopting technology to manage and track assets.
These systems cut costs by combining different technologies, such as QR-code and GPS real-time tracking, to make equipment monitoring effortless and place all the vital information at your fingertips.
Here’s an example of all the information you can get at a glance in our equipment tracking solution – GoCodes Asset Tracking.
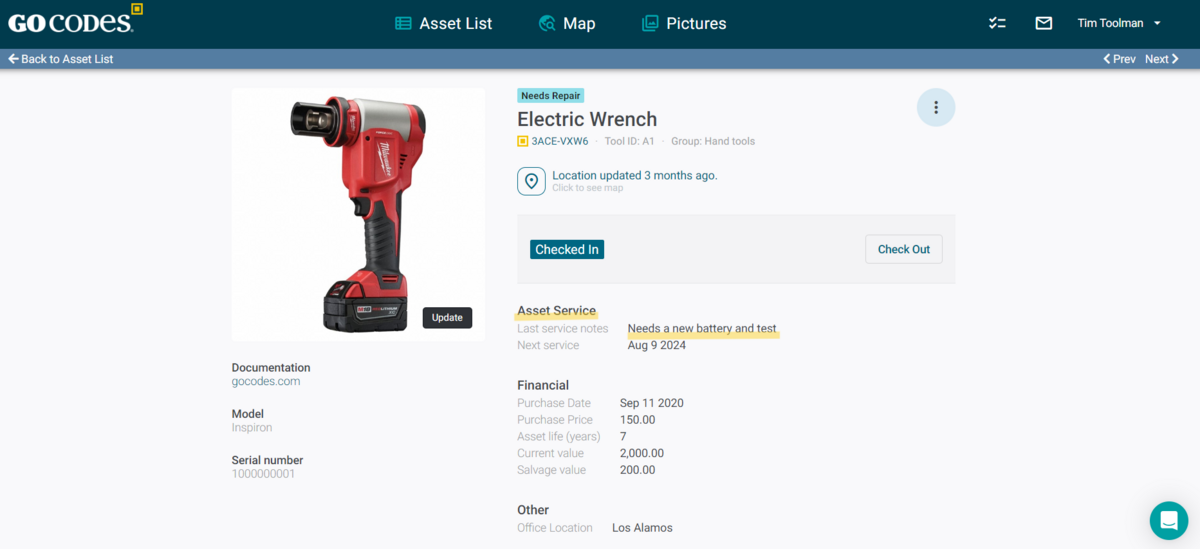
A simple QR code scan with a smartphone or direct asset search from any device tells you everything about your equipment’s location and status, from maintenance history to financial information and chain of custody.
Solutions like these transform the way you manage equipment and save you a lot of money in the long run.
If you want to check how much you can save exactly, put your numbers in our calculator.
To sum up, well-managed equipment enables and improves core construction work, which is why investing in its tracking and maintenance quickly turns costs into profit.
Manage Waste On Site
When you manage waste on-site, you keep it in check throughout all project stages, reducing both environmental impact and disposal costs.
These practices have always been a necessity on construction sites, but are getting more attention due to several worrying findings on the pervasiveness of construction waste.
One of them is the Transparency Market Research projection for the 2017-2025 period.
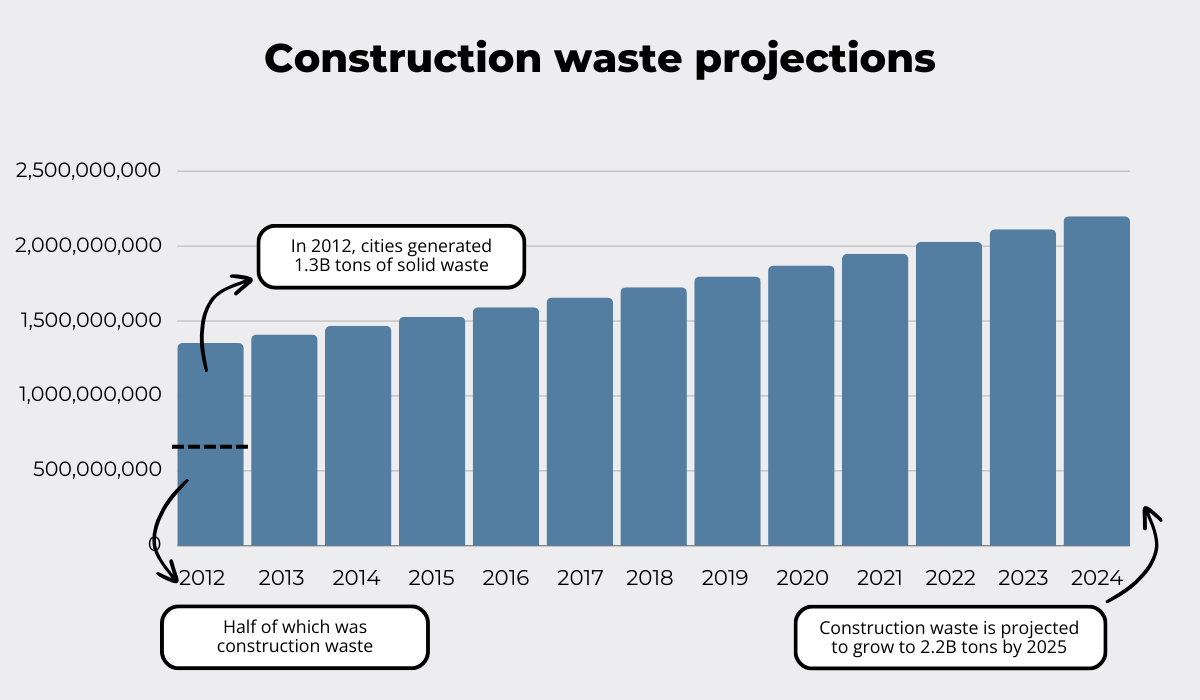
The 2.2. billion tons of construction waste annually is getting closer to reality, which is why companies look to reduce material usage and waste from the get-go, implementing lean construction practices or turning to green suppliers.
But what happens when you already have waste on site?
Studies show that sorting is an effective practice for reducing construction waste because it reduces disposal costs while allowing you to recover valuable materials for reuse and recycling.
Unfortunately, expensive operation costs, tight deadlines, lack of recycling outlets, and other site conditions often make contractors reluctant to implement these practices.
Misconceptions about waste management and deconstruction are also part of the problem.
That’s pointed out by Saia Latu, the Founder of New Zealand-based THROW Group, a deconstruction company that repurposes over 90% of the salvaged materials.

Many post-construction materials are easy to reuse and recycle so they don’t have to be sent directly to the landfill.
The first step you need to take is to assess your current practices and opportunities for improvement, and either develop or revise your site waste management plan (SWMP).
This plan can be drafted and refined based on three guiding principles or three Rs: reduce, reuse, and recycle.
For example, reducing waste can start with storing materials with more care to avoid unnecessary damage, and in cases of damage, setting aside the material for reuse.
The Environmental Protection Agency notes several construction materials that can be salvaged and then reused, including:
- easy to remove items like doors, hardware, fixtures,
- wood cutoffs and scrap wood,
- excess insulation,
- de-papered and crushed gypsum,
- paint.
And if materials cannot be reduced or reused, recycling is your best course of action.
Once you’ve developed an effective plan, you will have clarity on what you can recycle and reuse yourself, and which types of waste can be donated vs. what needs to go to the landfill.
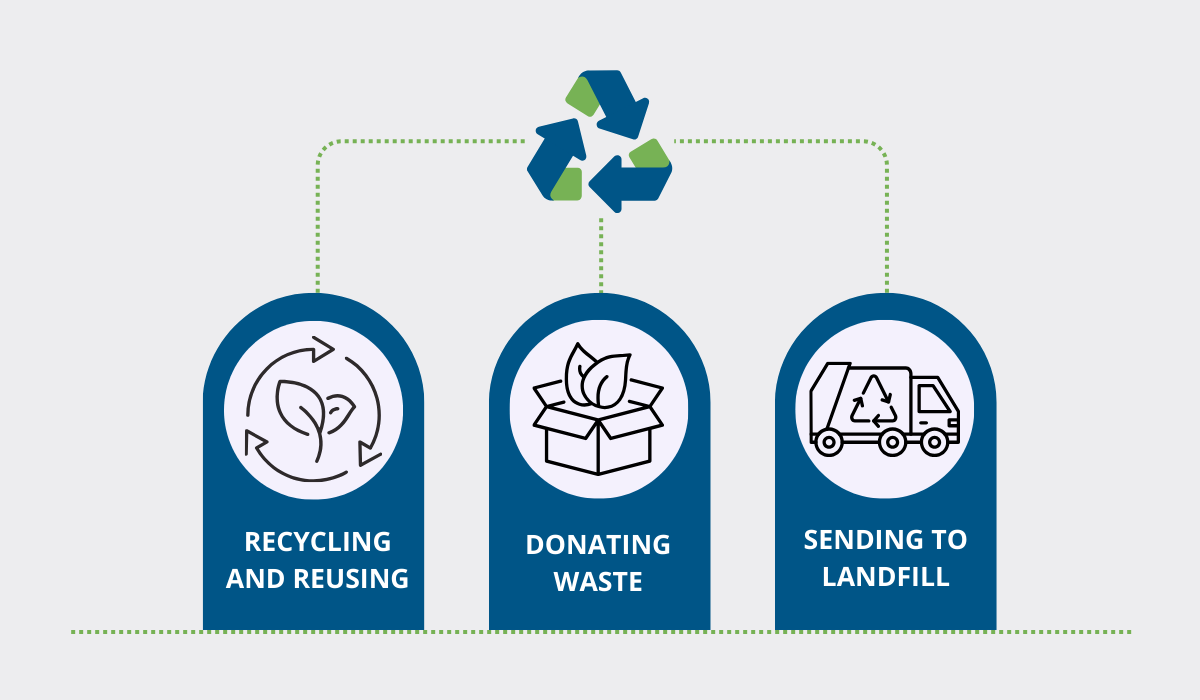
There are other innovative disposal methods, like waste-to-energy processes, but enhancing your on-site sorting practices is already a huge step toward greener, more efficient, and less expensive operations.
Conclusion
There are no shortcuts for controlling construction costs, but there are a couple of ways you can go about it.
We covered a few of them.
The one thing these tactics have in common is that they require you to play the long game while staying agile.
Being flexible and strategic enables you to reduce costs in all aspects of construction projects, from bidding to handling people, equipment, and waste.
Adopt these best practices and success will follow soon!