When battling high inflation, contractors and owners of construction companies are often eager to find ways to cut costs wherever possible.
One of the most beneficial methods is to invest in equipment tracking.
Keeping an eye on your equipment’s location and condition eliminates ghost assets, helps you stay on top of equipment life cycles, prevents equipment theft, minimizes downtime, reduces fuel consumption, and lowers insurance premiums.
Let’s look at each of these in more detail to see how they enable construction companies to cut costs and save money in the long run.
In this article...
Eliminate Ghost Assets
When working through a labor shortage while also facing premium material prices due to supply chain issues, it’s hardly possible to minimize costs by cutting employee salaries or trying to source less expensive components.
The best way to improve profits is to slash costs behind the scenes, in areas that are not immediately obvious to outsiders. One way to go about this is to squash ghost assets.
What are ghost assets?
Ghost assets are items that appear in your company’s inventory count or accounting records as available assets that your company owns and which contribute to its goals—but which are, in fact, either missing or unusable.
While this might seem merely like an annoyance, ghost assets can lead to several financial liabilities.
For instance, they can result in inaccurate financial statements, presenting a dangerously erroneous bottom line.
That, in turn, creates false compliance reports, and means that your company could pay higher taxes.
Ghost assets also cause higher insurance bills, because your bill is calculated on how many active items are in the service of the company.
They can also lead to higher maintenance costs, as it is usually difficult for third-party technicians to distinguish between items requiring preventive maintenance and those which are completely inoperable or not even on company property anymore.
Eliminating ghost assets, then, is a quick, low-labor way to save money for your construction company on several different fronts.
You may be worrying that tracking down those non-performing assets will require a lot of resources, and wondering if there are ways to get rid of them cheaply and quickly.
The answer is asset and equipment tracking.
Systems such as GoCodes Asset Tracking include QR codes that make it easy to scan and account for each item.
This setup results in a real-time register that will quickly reveal what assets are making your construction company money—and those that aren’t even present.
Monitor Equipment Life Cycle
Monitoring an asset’s life cycle is a basic part of care for the expensive items that help your construction company achieve its primary goals day after day.
The asset life cycle (or, in our case, equipment life cycle) reflects the ways in which your items age.
Here is a visual depiction of that cycle:
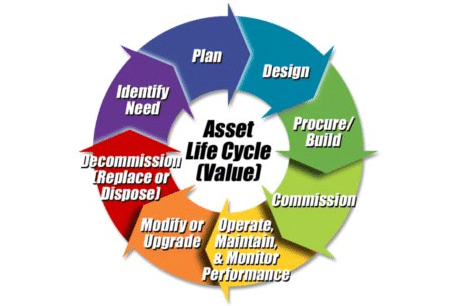
This process begins when the decision makers in your company begin to assess the needs that the asset or a piece of equipment will meet, as well as plan for its purchase and placement.
The item could be purchased off the shelf, or custom designed.
Once the piece of equipment is procured or built, it is time for equipment tracking to enter the process.
Equipment tracking measures the performance of the item as it undergoes daily operation and maintenance.
Should the piece of equipment require upgrading or modification, tracking will signal the proper time.
Once the piece of equipment in question is no longer performing as needed, or if it makes sense to replace it with another item, it will be sold secondhand or disposed of.
This also prevents assets from languishing in storage unused, and draining the company’s resources, as described in the previous section of this article.
As soon as the decision has been made to replace an item at the end of its useful life with another, the cycle begins again.
Without equipment tracking to guide the middle steps of this process, it is impossible to precisely judge when to dispose of old equipment that is no longer profitable.
Equipment tracking software makes it easy to monitor the life cycle of equipment from acquisition to disposal and aids in calculating equipment depreciation.
Prevent Equipment Theft
Construction companies can eliminate the cost of replacing missing or stolen construction tools and equipment by using equipment tracking software.
As mentioned above, GPS tracking is a powerful deterrent to thieves.
And it’s a good one to have, since, unfortunately, once an expensive piece of equipment is stolen, it usually stays gone:
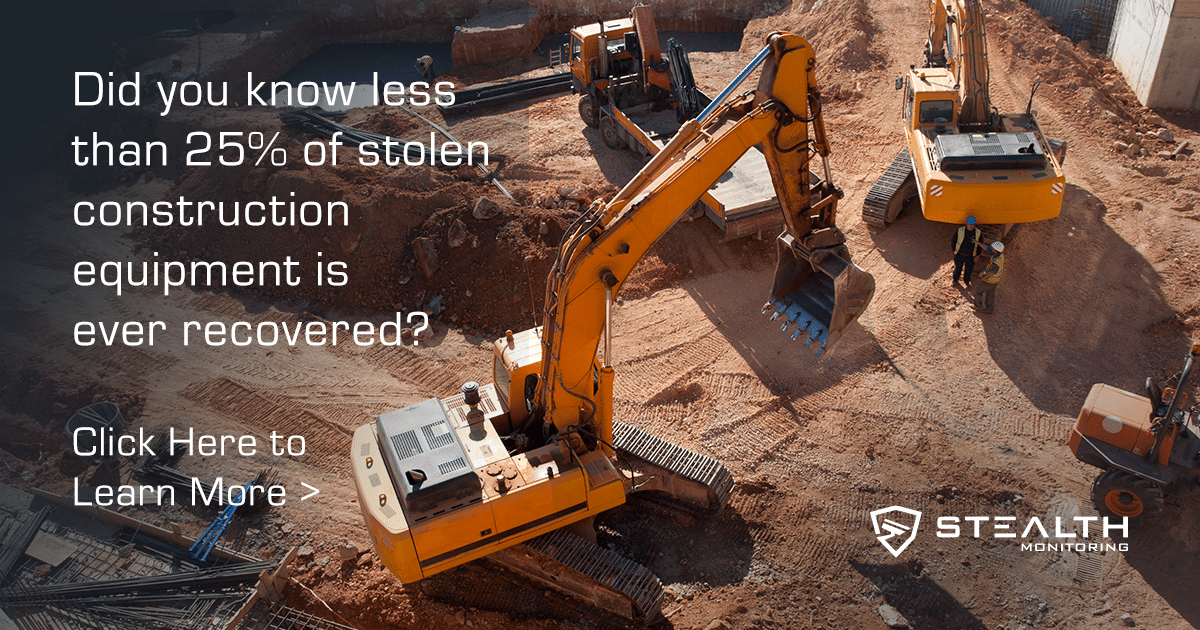
Not only that, the National Equipment Register, which maintains a database of stolen heavy construction equipment, states that “$400 million worth of backhoes, jackhammers, trucks and other industrial and construction gear walks off job sites each year.”
Even more troubling is the fact that this staggering number includes only the thefts reported to authorities.
Small, unsecured items frequently disappear and go unreported, as do entire pallets of valuable raw materials.
Some thefts are committed by petty criminals who happen upon an unsecured site, while other builds are targeted by highly organized bands of thieves that are so systemized that they carry cranes or jacks of their own to ensure a quick getaway.
The best way to avoid such expensive and upsetting losses is to establish asset tracking.
This involves tagging valuable assets with easily scannable QR codes that are simple for employees to use.
GoCodes Asset Tracking even provides a wide variety of tags that are appropriate for every type of item, from sensitive indoor art installations to rugged outdoor tags that can withstand high temperature variations, corrosion, wind, and moisture.
The precaution of relying upon these tags, along with setting up a GPS fence, will not only deter thieves both within and without the company but also increase the chance of a quick and safe return of your equipment in case the worst happens.
We explore the topic of geofencing and its benefits in more detail in the final section of this article, as this feature not only provides you and your clients with peace of mind but is also looked upon favorably by insurance companies.
Minimize Equipment Downtime
Each asset or piece of equipment, particularly those that are part of a fleet, must undergo at least some downtime to allow for regular preventive maintenance.
These maintenance actions are part of a smart, ongoing strategy to ensure the equipment is safe, operable, and in good repair.
Preventive maintenance can help to identify and quickly repair small problems, such as a new crack in a tread, before it becomes a major safety hazard that could halt work until expensive repairs are completed.
Equipment tracking can help ward off expenses associated with overtime, emergency equipment rental, last-minute replacement purchases, specialized labor, and missed construction milestones.
Unscheduled downtime, unfortunately, can become a major contributor to total equipment downtime if preventive maintenance isn’t a central part of asset care:
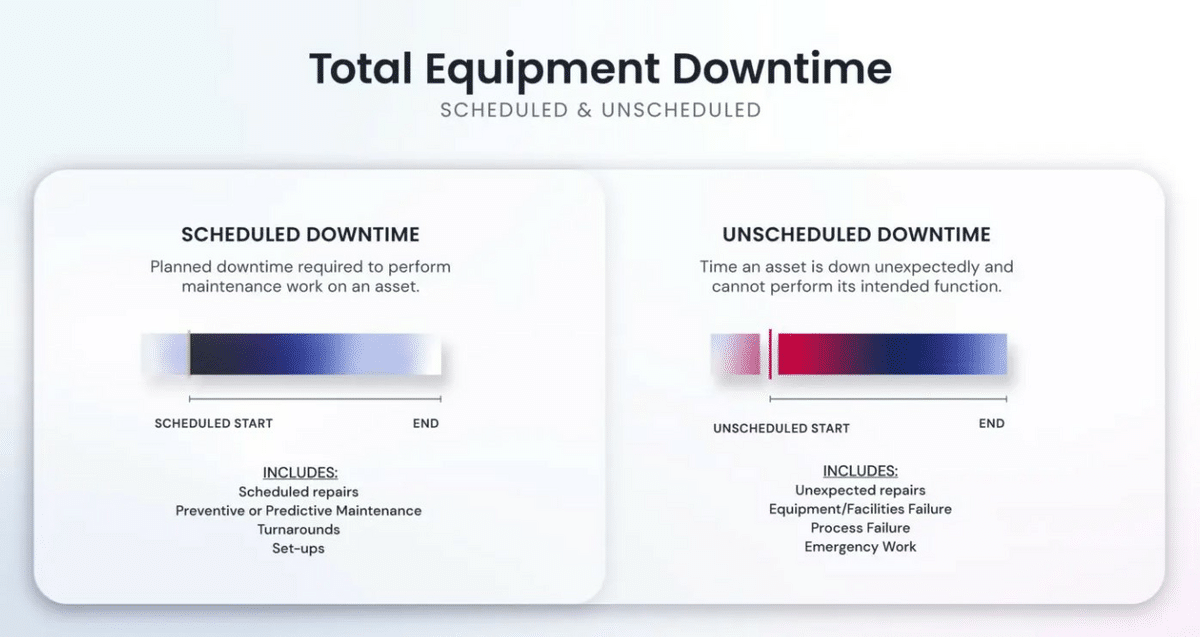
Scheduled downtime is predictable, shiftable, and easy to optimize across build schedules and sites.
However, unscheduled downtime takes place without warning and can even involve process failure, which immediately affects the entire project.
Consistent equipment tracking is a vital part of keeping downtime planned, instead of unscheduled.
Reduce Fuel Consumption
According to the United States Bureau of Transportation Statistics, fuel prices are undergoing a historic rise, thanks in part to a reduction in fuel sources:
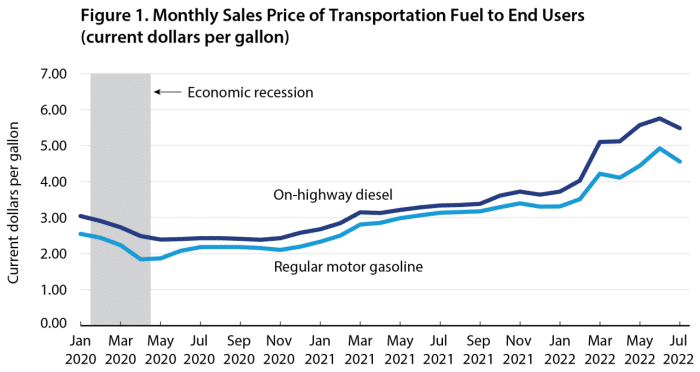
How can construction companies combat this, especially when they must constantly transport heavy, fuel-inefficient machinery and heavy items, sometimes across large distances?
In addition to all these other advantages, assiduous equipment tracking can result in lower fuel prices.
This is possible when GPS tracking is employed not just to deter theft or assure clients of an impending delivery, but also to provide invaluable data as to which routes are most efficient.
GPS tracking can help to avoid gas wasted from sitting in traffic jams and reduce the amount of fuel consumed during idling.
By also slashing the amount of time that equipment is running but not in motion, construction companies can apply holistic approaches to fuel savings.
Lower Insurance Premiums
Construction companies can cut costs by lowering their insurance premiums with the help of equipment tracking software.
When construction companies have an equipment tracking solution that offers GPS tracking, insurance companies will offer them lower insurance premiums.
Here’s why.
GPS tracking is one of the most exciting aspects of the digital revolution for companies dealing in physical goods.
As mentioned in the section on theft prevention, GPS technology is easily deployed in creating a geofence around valuable equipment, such as heavy machinery and appliances recently installed in a building under construction.
When items cross the geofence without approval, the system sends an alert to law enforcement, as well as the company in ownership.
That means the item is usually quickly returned to its home base, or that it is easily located if not.
Here is what a GPS tracking system in action looks like.
As you can see, it is laid directly over a real-time satellite map:

Geofences are invisible and entirely mobile, not physical, which leads to a more navigable site, as well as one that is better protected from thieves.
This type of protection indicates to insurance companies that there is a lower risk involved with a construction company’s equipment, leading to more affordable premiums.
In addition to theft prevention, eliminated ghost assets, improved maintenance and higher accountability of equipment operators associated with GPS-powered equipment tracking all contribute to lower insurance premiums.
Conclusion
Construction companies that invest in a robust equipment tracking system, such as GoCodes Asset Tracking, stand to cut costs in a number of ways.
Ghost assets are easily eliminated, which means that the company is no longer paying taxes, storage fees, or insurance premiums on items that no longer exist or are not serving the company.
Monitoring equipment life spans on a regular basis helps to build an efficient preventive maintenance plan and replace assets at advantageous points in their service cycle.
Tracking can help to prevent equipment theft and even increase the chances that an item will quickly return to the fleet.
Equipment tracking can minimize equipment downtime and cut down on expensive fuel consumption.
All of these benefits, combined with lower insurance premiums that tracking can offer, are available with GoCodes Asset Tracking and its cloud-based tracking system.