Tracking each stage of an equipment’s life cycle is important for all companies, but it’s especially vital for a construction company.
The equipment that construction company employees rely on to complete their projects is usually a major investment.
In order to maximize the cost efficiency of such items, decision makers must track all stages of the equipment life cycle.
We provide a detailed overview of the six stages in this article.
In this article...
Planning
The construction equipment lifespan begins with planning.
In this stage, decision makers should solicit the feedback of operators, equipment managers, and financial advisors to balance the needs of the company with budgetary concerns.
Contractors should evaluate the state of technology in the industry and seek estimates for suitable candidates.
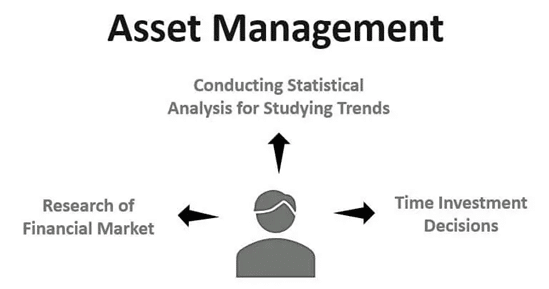
As this graphic indicates, the planning phase of the equipment’s life cycle is an important part of asset management.
Since construction equipment often involves substantial investment, especially if your company plans to rent it to others, it is vital to take advantage of demonstration offers and to consult the data it generates, along with the opinions of operators.
The decision to obtain a piece of equipment is not easily undone, especially once the equipment is heavily used or has already undergone maintenance.
Acquisition
The acquisition stage calls for a thorough understanding of the construction company’s budget. It also involves establishing a time frame for purchasing and paying for the item.
This means calculating interest rates, the item’s probable depreciation rate, and deposit terms.
Depreciation is computable by a number of different means, but the method employed by construction companies should take into account the item’s physical condition as well as how quickly it might become obsolete:
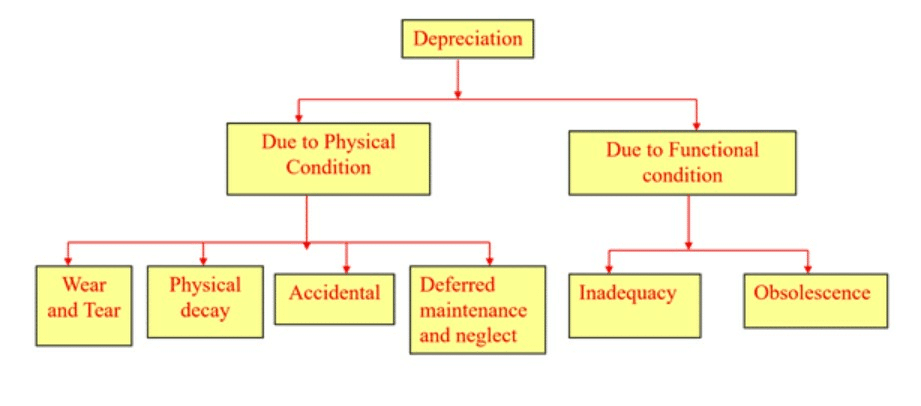
Acquisition also involves finding a reputable and reliable supplier.
If the supplier you’re working with is new to you, it is important to ask for references, seek out legitimate reviews, or ask others in your industry to vouch for their reputability.
Deployment
Deployment is perhaps the most exciting part of the construction equipment life cycle. During deployment, the new equipment is assembled or put in place, then inspected for defects.
At this point, it’s important to note that the operators and other employees should undergo thorough training, especially regarding the safe operation on a construction site and the guidelines regarding preventive maintenance.
It is best practice to immediately begin tracking your new asset, as the sooner data collection begins, the more comprehensively it will track the item’s output.
Using a system like GoCodes Asset Tracking is ideal for asset tracking because the system is extremely flexible and offers code tags to withstand any conditions and on any number of different assets.
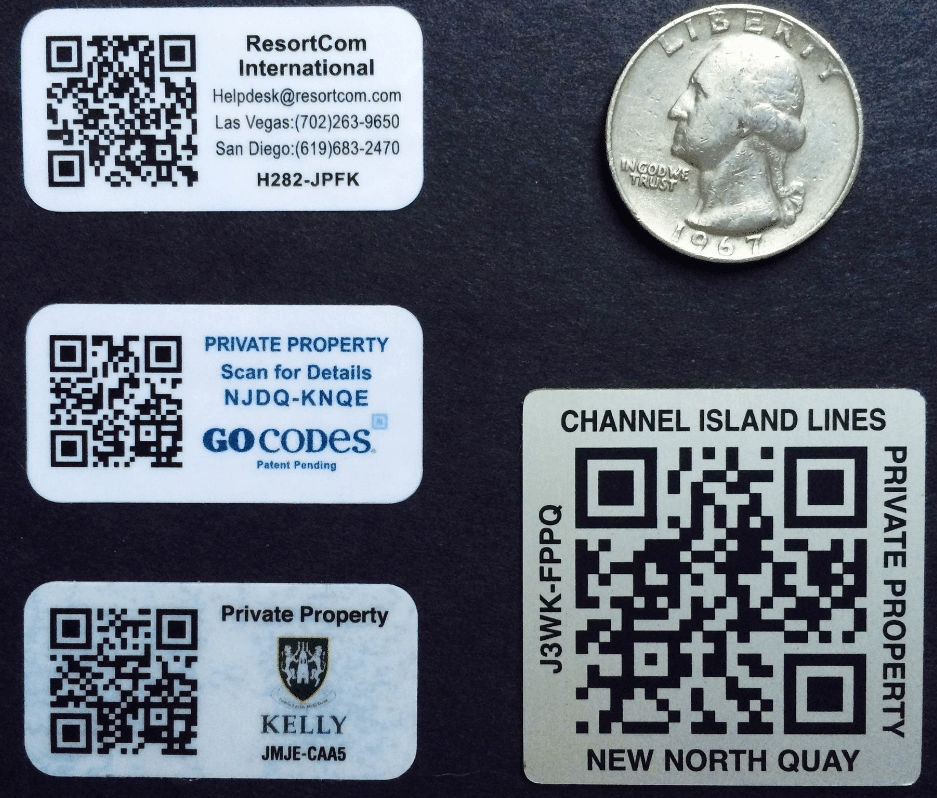
For example, assets that spend a great deal of time in harsh elements or have contact with chemicals, temperature extremes, or significant vibration probably require durable metal tags that are welded to the item.
The strategic placement of QR codes on each tag means that employees can quickly and intuitively scan each asset using technology with which they are likely already familiar, such as smartphones.
Utilization
The process of utilization is the longest part of the equipment life cycle. It is at this point that your employees settle into a routine with the new item.
Your team adjusts to the asset and learns to understand its capacities, as well as the most efficient way to operate it.
During this stage, as long as the asset is assiduously tracked, its information updates automatically.
In this way, the asset prepares for its replacement by creating a real-time record of its performance.
By the time the asset is ready for the next two stages, it will have produced a highly detailed picture of what can best replace it.
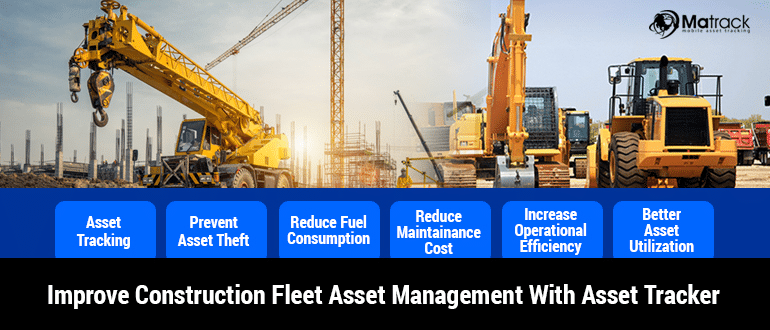
The above graphic discusses ways to improve construction fleet utilization.
Other best practices include providing strong training for operators, keeping the asset in good repair, easing communication between team members regarding its retention, and concentrating on efficient storage and maintenance.
Maintenance
The maintenance of your new asset takes place alongside utilization and is one of the most important reasons to faithfully track your asset’s performance and location.
The ongoing process of preventive maintenance involves an operational inspection schedule and careful diligence to ensure the equipment is used and maintained within warranty and manufacturer boundaries.
Preventive maintenance also involves the regular cleaning of the asset and taking the time to implement common sense security measures.
As the statistic below shows, the benefits of paying proper attention to your asset are many:
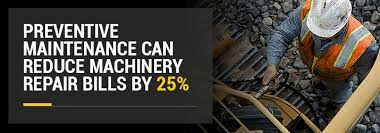
Asset tracking can play a major role in your assets’ preventive maintenance in addition to the wealth of valuable data it collects.
GoCodes Asset Tracking’ extensive QR management system, for example, provides an enormous amount of information.
QR codes can organize extensive inventory systems, keep up with an asset’s chain of custody, issue reminders for preventive maintenance, and even provide instant access to operator’s manuals, warranty information, insurance details, manufacturer contact information, and details about safe production levels.
Even with assiduous preventive maintenance, the continuous use of your asset will cause normal wear and tear over time.
While this is expected, encouraging the operators in your company to give a clear warning as soon as they spot any abnormal functioning can help to ward off a major malfunction or expensive breakdown.
Disposal
Just as bringing your asset into your construction company requires a great deal of thought and research, disposing of it is also a highly involved process.
When the equipment’s performance has significantly deteriorated and the equipment is no longer profitable, it has reached the end of its useful life.
This flow chart provides an idea of the many considerations decision makers must assess before coming to a decision about how to move the item to the end of its life cycle:
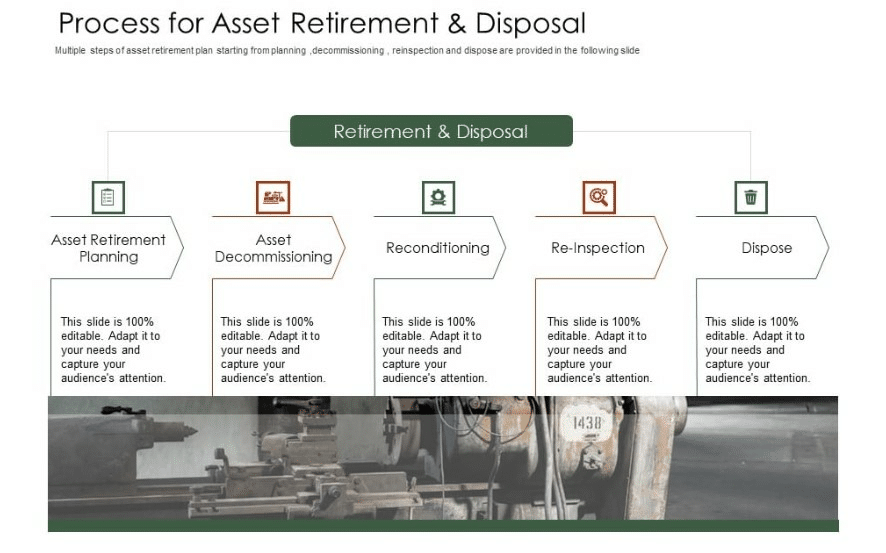
If the asset is involved with hazardous materials, it might require decommissioning. Different countries, states, and municipalities enforce varying rules about the decommissioning process.
However, if the machine no longer serves you well and it makes financial sense for you to move on, that doesn’t mean the asset’s useful life is over.
Other construction companies may find some use for it, or its parts might have value for OEM dealers. In this case, reconditioning and re-inspection are in order before passing on the asset.
If, however, outright disposal is the best or only option, it is important to check EPA rules and local codes about the correct process.
The six stages of the construction equipment life cycle are easily supportable by a robust asset tracking program.
To recap, thoughtful planning will help you and your team make financially responsible decisions regarding new equipment.
Conclusion
The acquisition process should involve a set budget, as well as consideration of depreciation, amount of interest on loans, and total cost of ownership.
When the piece of equipment is acquired, the assembly and deployment stages should include the implementation of asset tracking so that the item’s entire life with your company is documented.
Utilization refers to the everyday use of the asset; concurrent with maintenance, taking care of the machine will make the most of its lifespan.
Finally, when the asset is no longer financially serving the company, it’s time for responsible disposal.
We hope that this article has given you some insight into what to watch out for in each stage of the equipment life cycle, so that you can manage it successfully.