As a construction company owner or manager, you’re aware of how pivotal well-maintained equipment is in your company’s daily operations.
But what happens when that equipment starts to lose its value?
In this article, we’re going to be answering some of the most commonly asked questions about equipment depreciation that will help you understand what equipment depreciation is and how it affects your construction business.
Let’s dive in.
In this article...
What Is Equipment Depreciation?
Equipment depreciation is a measure that tells you how much value a piece of equipment has lost over a period of time.
The concept is fairly simple.
Let’s say you just bought a new forklift for your construction business and assume that your employees are going to do their best to use it as intended and perform regular maintenance.
Even if the forklift is in great shape, if you decide to sell it in 5 years, you won’t be able to get the same amount of money you had initially paid for it.
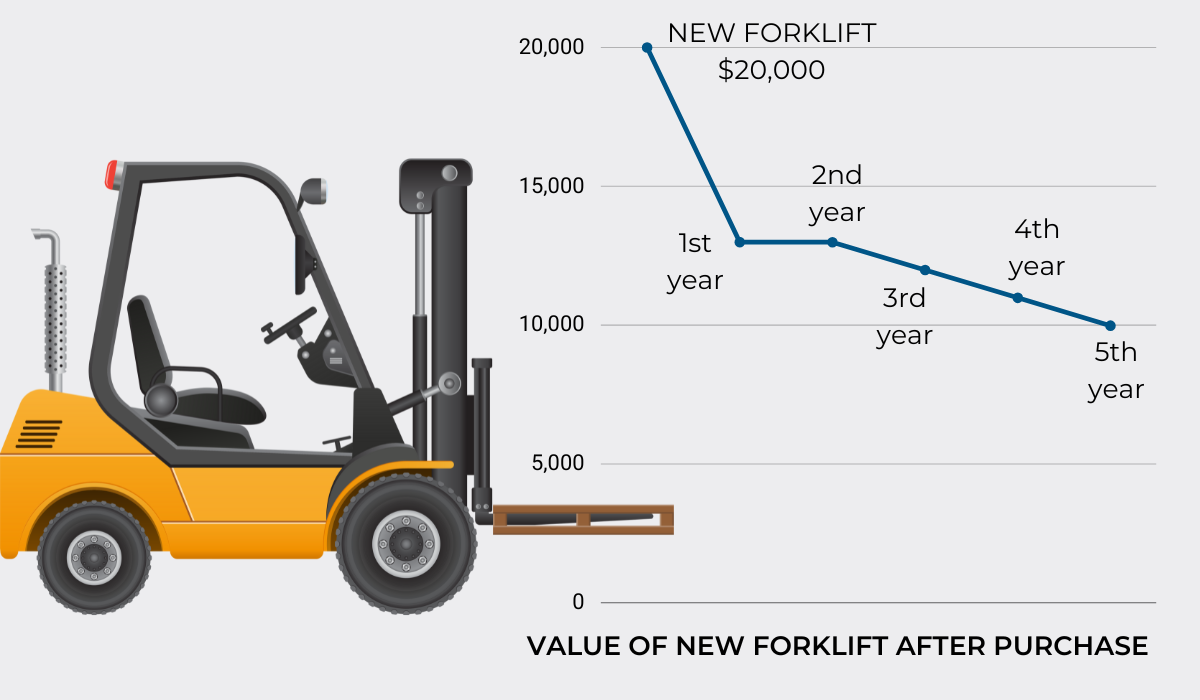
Due to the passage of time and the fact that the forklift has been used, it will have lost some of its value.
The fact that every piece of equipment you buy is inevitably going to lose its value may sound bad, but equipment depreciation is a completely normal and expected thing.
Here’s how they explain it at Stearns Bank:
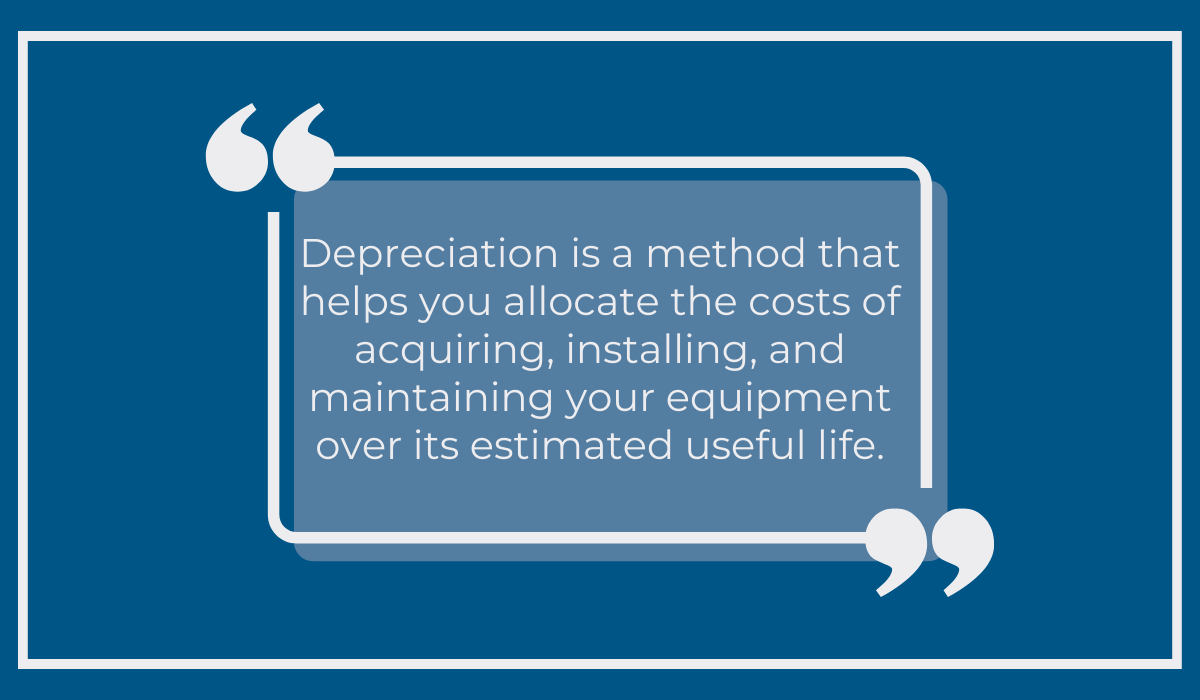
In other words, the purpose of depreciation is to help you plan for the future and maintain your company’s financial stability.
When you buy a new piece of equipment, the amount you paid to acquire it isn’t the only expense you should count on.
You also need to consider installation and ongoing maintenance costs.
Without depreciation, all of these costs would be treated as immediate expenses, which can lead to inaccurate profit calculations.
With depreciation, however, all of these expenses are “recognized over the asset’s useful life”, which means that the expenses are going to be aligned with the revenues generated over the same period of time.
To sum up, depreciation will help you accurately calculate your profit and allow you to plan for replacements once your equipment has reached the end of its useful life.
What Causes Equipment Depreciation?
There are various factors that affect the depreciation of equipment, but some of the most important ones for the construction industry include equipment wear and tear and technological obsolescence.
Let’s start with wear and tear.
Wear and tear is the damage that happens to your equipment as a result of frequent usage.
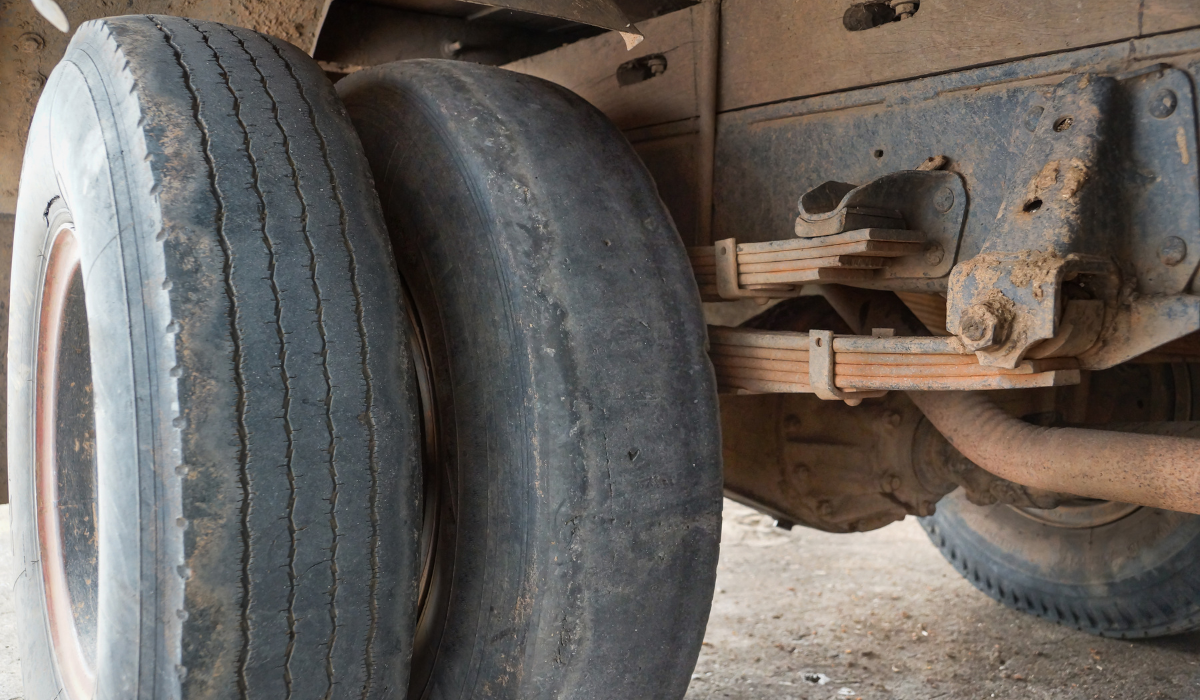
Yes, construction equipment is intended to perform demanding tasks like lifting, excavation, or loading and unloading of the materials, and it is designed to endure working in challenging conditions.
However, this doesn’t change the fact that exposure to the elements and the strain being put on parts of the equipment causes damage that negatively affects the equipment’s value over time.
Some wear and tear, such as tires and tracks becoming worn over time, is normal.
But to prevent it from becoming an issue, regularly checking for wear and tear and scheduling equipment maintenance is key. This is something we’ll go more in-depth with later on.
Keep in mind, though, that even if you take all the necessary precautions to minimize the wear and tear of your equipment, it can still fall prey to obsolescence.
Obsolescence is when a piece of equipment stops being considered current and competitive.
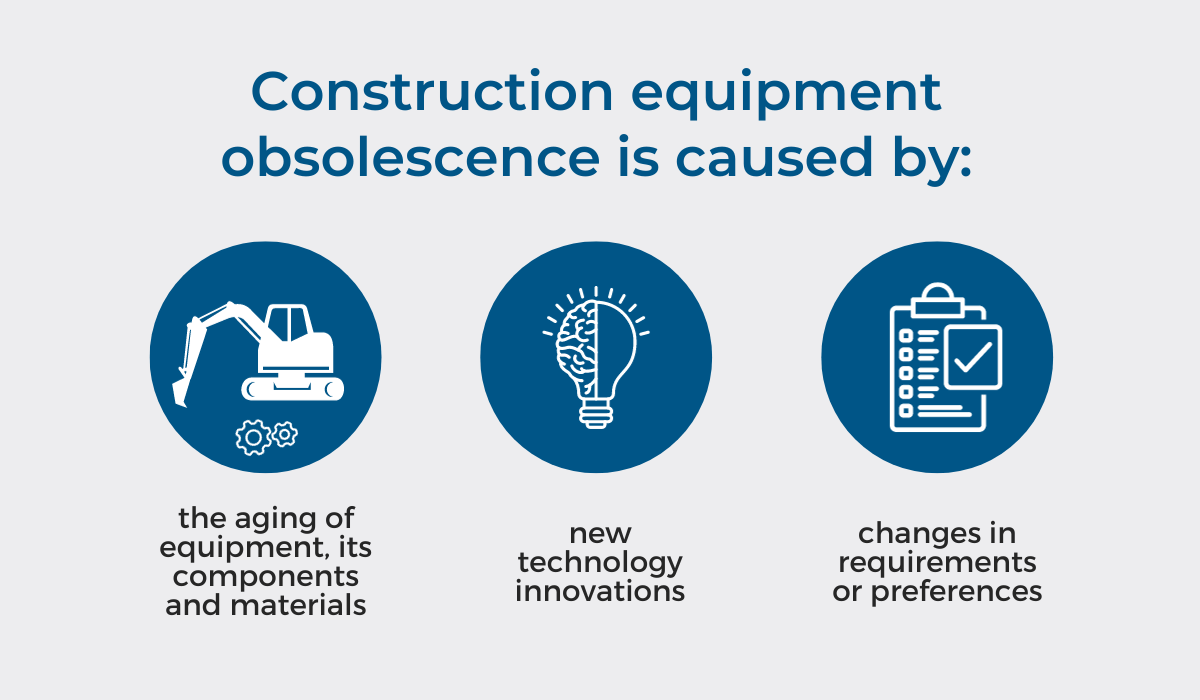
Just like other industries, the construction industry is experiencing technological advancements that make both back-office operations and fieldwork easier.
However, these advancements also lead to technological obsolescence of your existing equipment, thereby depreciating it.
Simply put, as new equipment featuring advanced technologies comes out, the older versions without these features start being less desirable and more likely to require costly maintenance.
So, does this mean you should be replacing your equipment every time a newer model comes out?
Not necessarily.
However, be careful if you’re experiencing:
- frequent downtime due to repairs
- higher replacement part prices
- increased risk of accidents due to outdated and malfunctioning equipment,
If those are all too familiar to you, it might be a good idea to consider transitioning to newer equipment.
What Equipment Is Depreciable?
According to the current revision of the IRS Publication 946, there are 4 criteria that your equipment needs to meet in order to be depreciable for tax purposes.
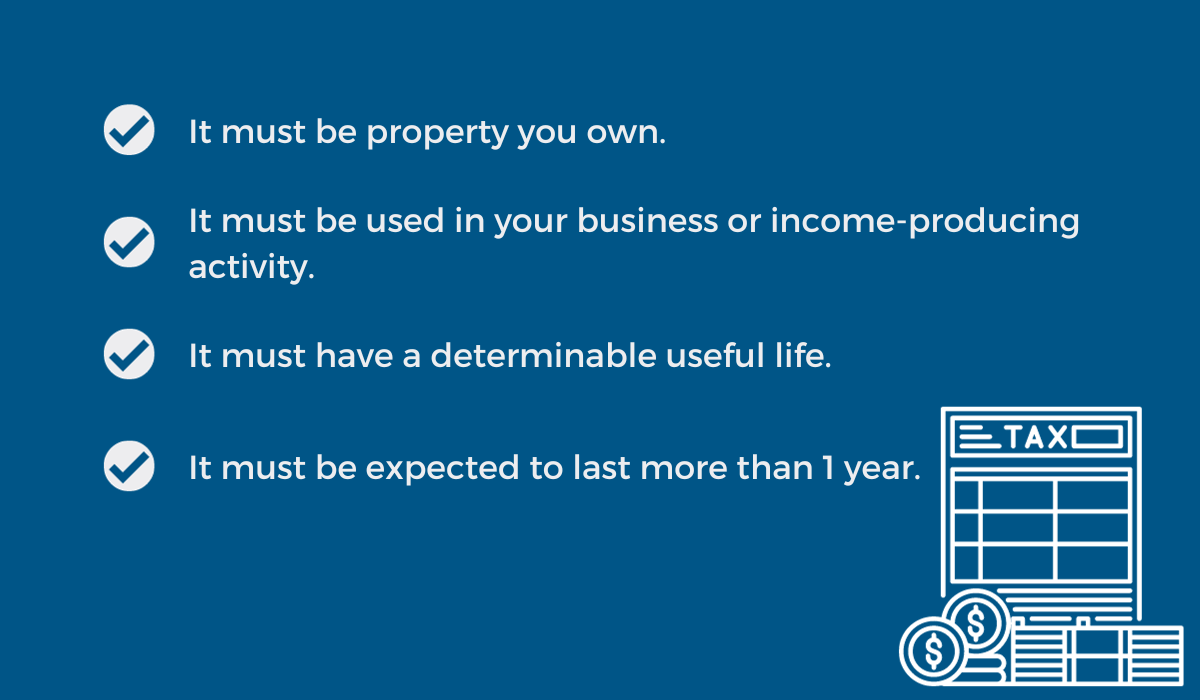
But when does the depreciation of said equipment begin?
The answer to this question depends on whether we’re talking about depreciation for tax purposes or not.
In the case of the former, the IRS explains:
You begin to claim depreciation when your property is placed in service for either use in a trade or business or the production of income.
Tax purposes aside, any and all construction equipment starts depreciating after you’ve purchased it—regardless of whether you’ve put it in use immediately or kept it in storage for several years.
In other words: depreciation is inevitable. But can it be minimized?
We’ll dive into that in this next section.
Can Equipment Depreciation Be Minimized?
Construction equipment can get expensive, so it’s only natural that you want to make the pieces you have stay in top form for as long as possible.
And while you can’t completely avoid depreciation, you can minimize it with proper equipment maintenance.
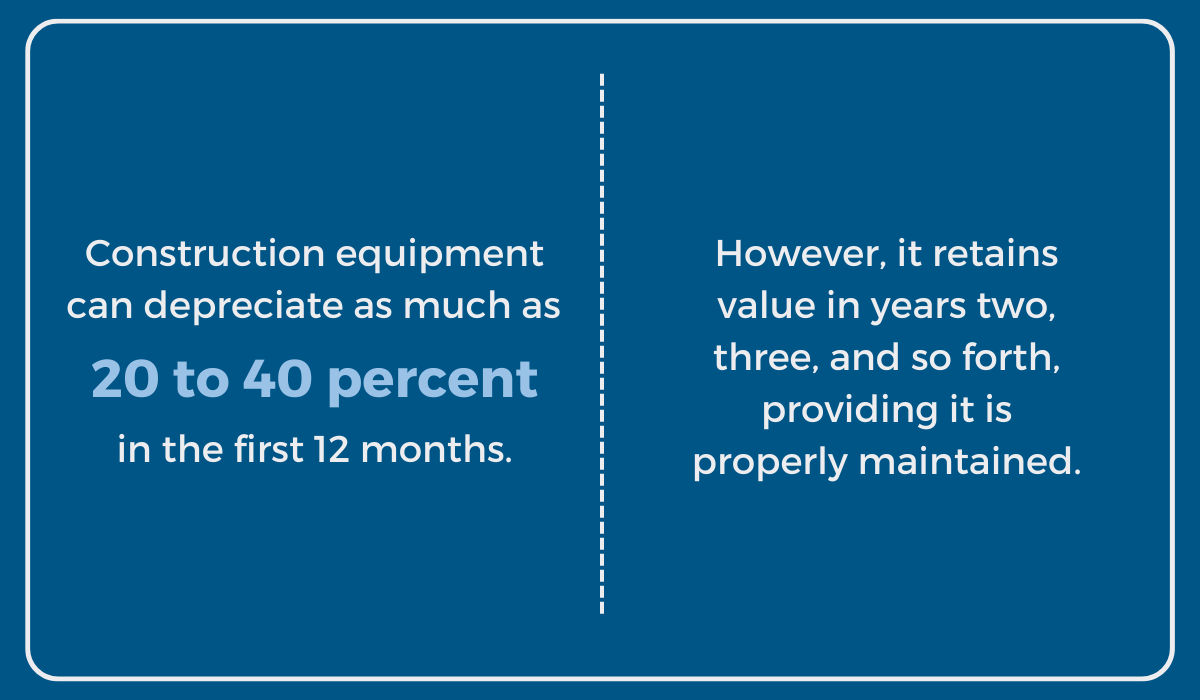
As we mentioned earlier, the conditions in which construction equipment is used are often challenging.
Your equipment goes through a lot on a daily basis—from dirt, mud, and debris getting stuck, to deterioration caused by repeated strain.
If you don’t address such matters by making a habit out of regular maintenance, you can expect your equipment to depreciate faster than necessary.
Cameron Stejskal, product reliability specialist at ASV Holdings, Inc., recommends the following:
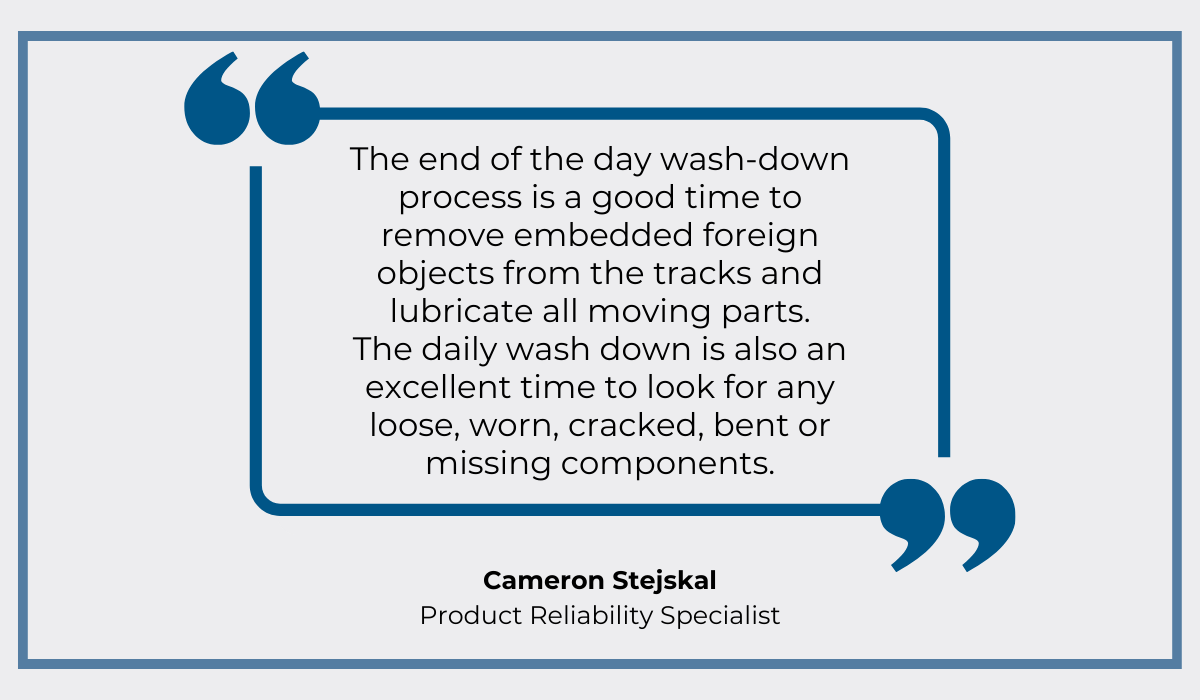
But you can do more than perform a wash-down and a quick check of your equipment at the end of the day.
In order to keep your operations and your equipment running smoothly, scheduling preventive maintenance is crucial.
Now, if you’re still working with paper-based spreadsheets to keep track of your equipment and its maintenance status, this might sound overwhelming.
In that case, switching to a digital solution such as GoCodes Asset Tracking is the way to go.
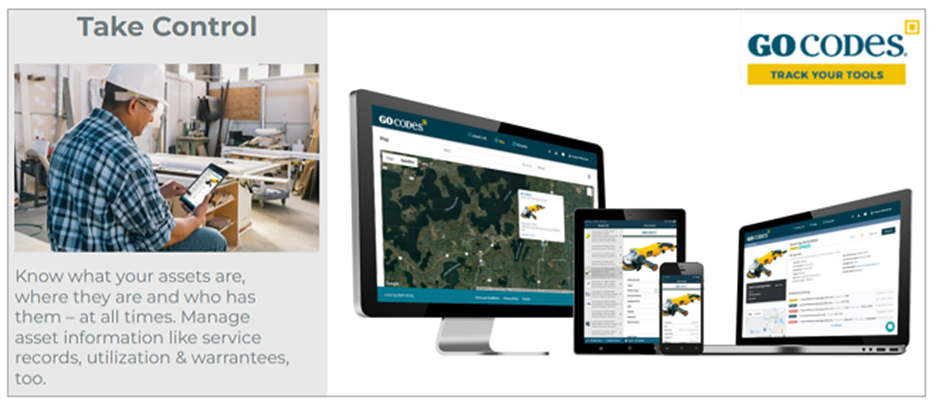
GoCodes Asset Tracking will let you store information about each piece of your equipment, as well as attach any equipment-related photos and documentation.
To access equipment information, all you need to do is scan the QR code asset tag previously attached to the piece of equipment using the GoCodes Asset Tracking in-app scanner on your smartphone, like this:
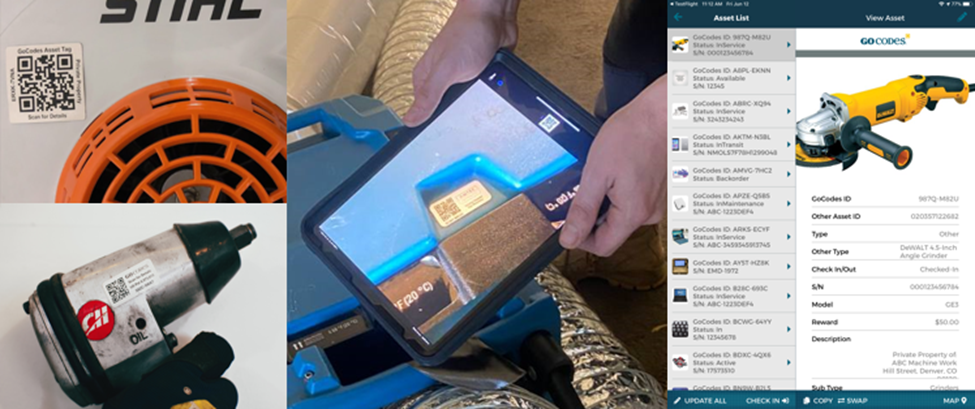
Not only will you be able to view the maintenance history and easily schedule future inspections and maintenance, but you will also be able to schedule service notification emails when a piece of equipment is due for maintenance.
All in all, sticking to a maintenance schedule will help you keep your equipment in top shape for as long as possible, thereby minimizing its depreciation.
How Do You Set Up a Depreciation Schedule?
A depreciation schedule is a table you’re going to need to create in order to keep track of the depreciation of your equipment throughout its useful life.
In order to set it up, you’re going to need the following information:
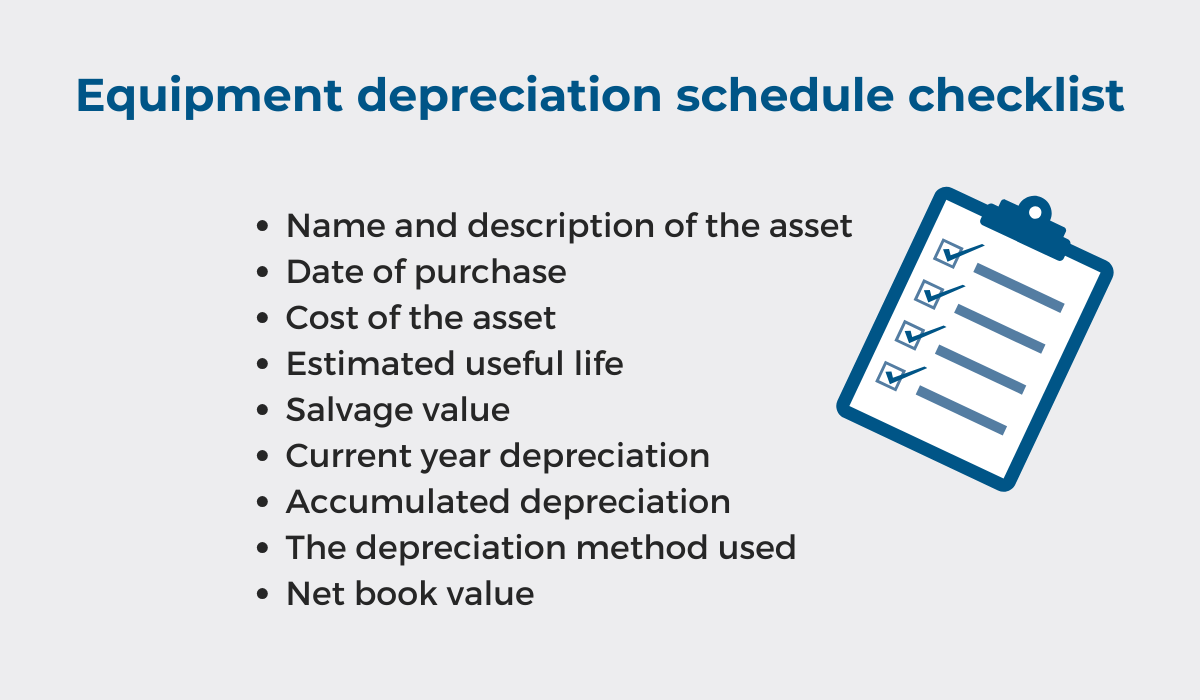
First, enter all the basic information about the equipment, such as its name, description, unique identifier, and the date it was purchased.
Next, put in the cost of the piece of equipment, which includes both the purchase price and any other related costs, such as installation costs.
Then, you’re going to enter the estimated useful life and the salvage value of the equipment piece.
Here’s how Investopedia defines estimated useful life:
The useful life of an asset is an accounting estimate of the number of years it is likely to remain in service for the purpose of cost-effective revenue generation.
On the other hand, salvage value is an estimation of the worth of equipment after depreciation, at the end of its useful life.
Lastly, you’re going to enter current-year depreciation, accumulated depreciation, the depreciation method you used, and net book value.
While current-year depreciation denotes the amount of depreciation for the current year, accumulated depreciation tells you the total amount of depreciation up until a specific point in time.
The last piece of information you’re going to enter in your depreciation schedule table is net book value.
This is the value at which a piece of equipment is documented on the company’s balance sheet.
Here is how to calculate it:
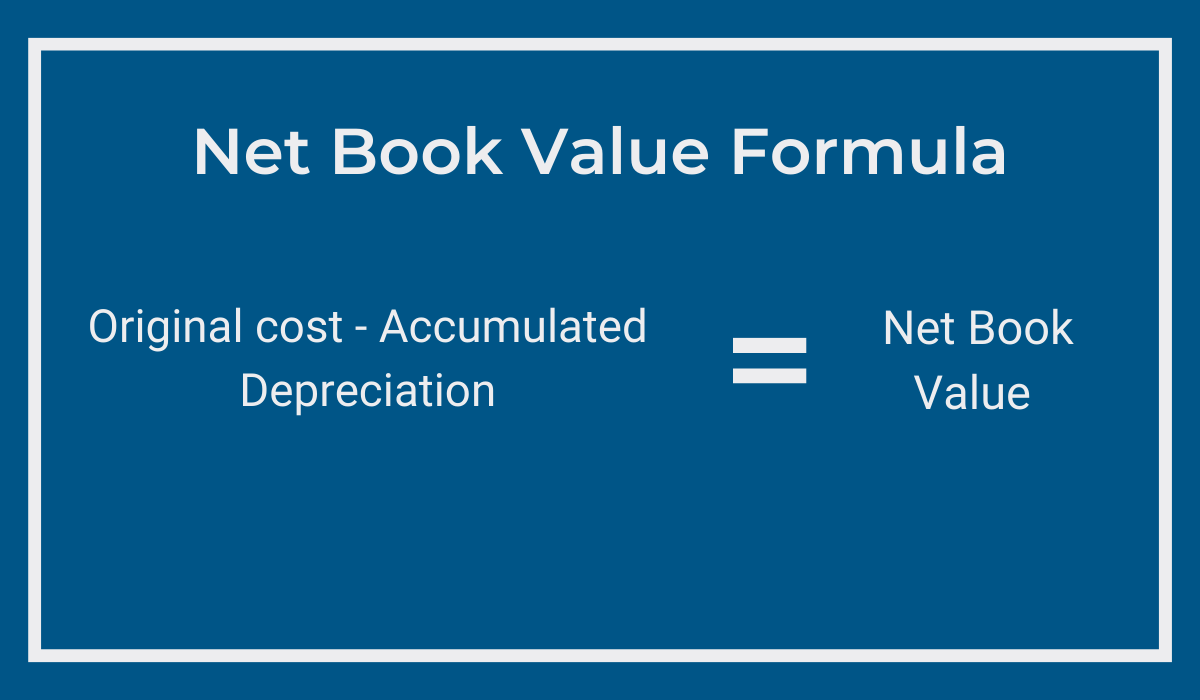
A depreciation schedule is going to help you keep track of the condition of your equipment, plan for replacements, and ensure you’re compliant with all the tax regulations, so don’t underestimate its importance.
What Is Equipment Depreciation Rate?
The depreciation rate is “the total amount depreciated each year, which is represented as a percentage”, according to Investopedia.
Here is an example of what calculating the depreciation rate can look like in practice.
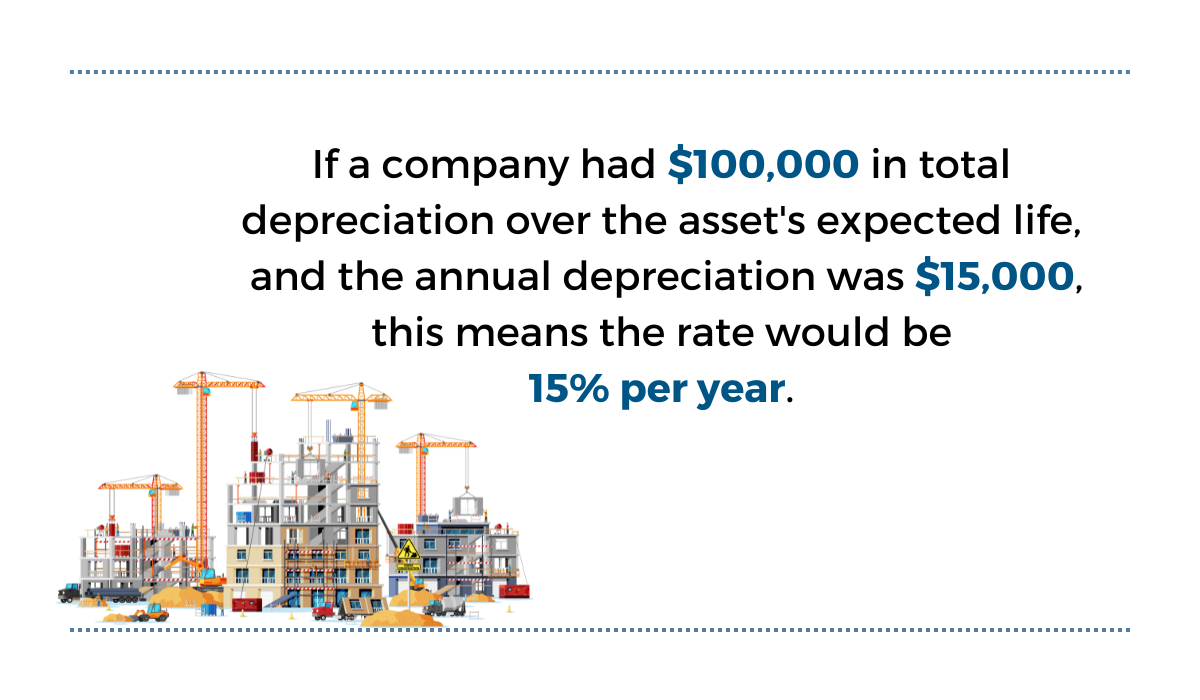
Keep in mind, though, that there’s no one standard depreciation rate that could be applied to all industries, or even just all types of equipment.
Your equipment’s depreciation rate is going to depend on a variety of factors, such as the equipment type, the intensity of use, and its estimated useful life.
For example, pieces of equipment that are nearing the end of their useful life are going to start depreciating at a faster rate.
However, it’s important to note that your choice of depreciation method is also going to impact the depreciation rate of your equipment.
So let’s look into how you can calculate the depreciation of your equipment and what the depreciation rate is going to look like depending on the method you choose.
How Do You Calculate Equipment Depreciation?
There are 5 common depreciation methods you can use to calculate equipment depreciation:
- straight-line
- declining balance
- double-declining balance
- sum-of-the-years’ digits
- units of production
Let’s briefly go over each of them.
The straight-line method is one of the more popular depreciation methods due to its simplicity.
Under this method, you are going to be deducting the same amount of depreciation every year throughout the useful life of the equipment.
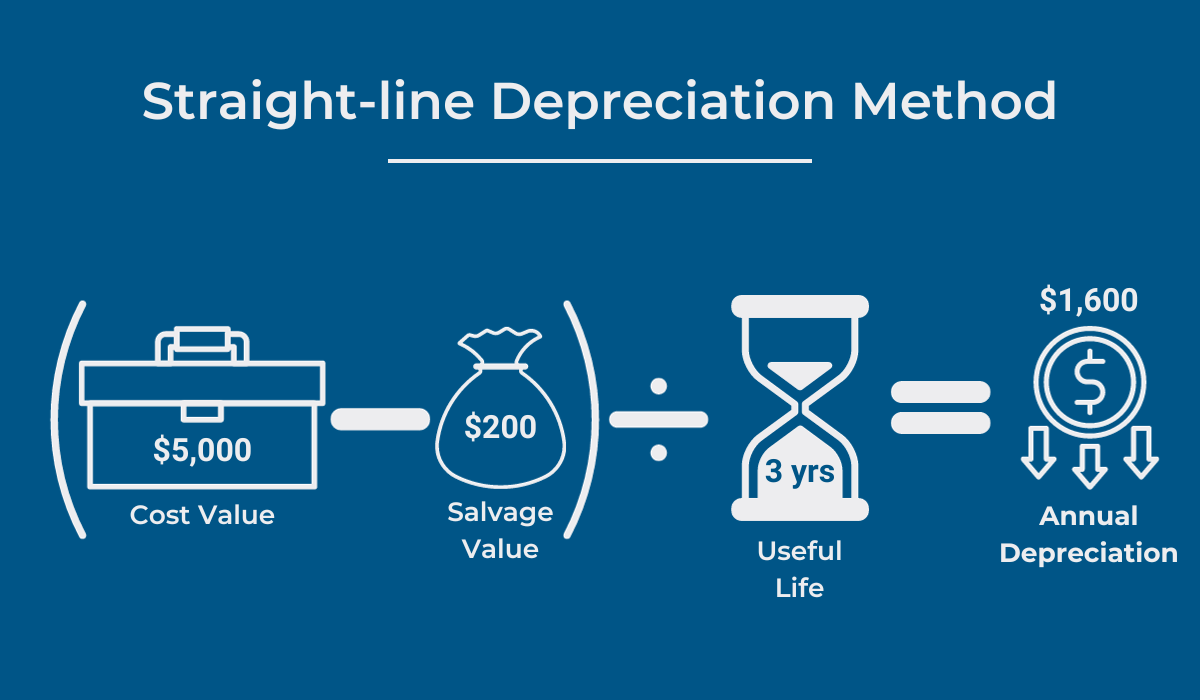
Using this method, the depreciation rate of your equipment is going to remain constant year over year.
In other words, the value of the equipment piece is going to decrease steadily.
Some of your equipment, however, is going to generate less revenue as it ages.
In such cases, you might want to use one of the accelerated depreciation methods: the declining balance method, the double-declining balance method, or the sum-of-the-years’ digits (SYD) method.
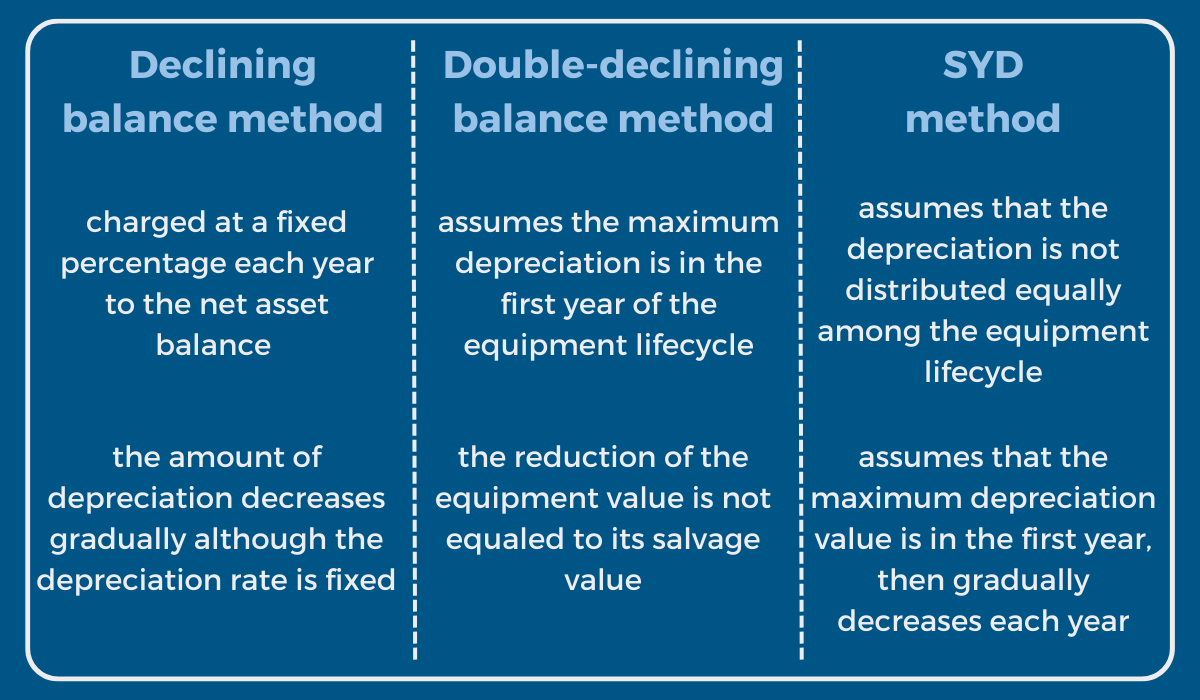
Under these methods, the depreciation expenses are going to be higher in the early years and then decrease over time.
Lastly, you can consider using the units of production method.
This method will allow you to depreciate your equipment based on the number of hours of operation.
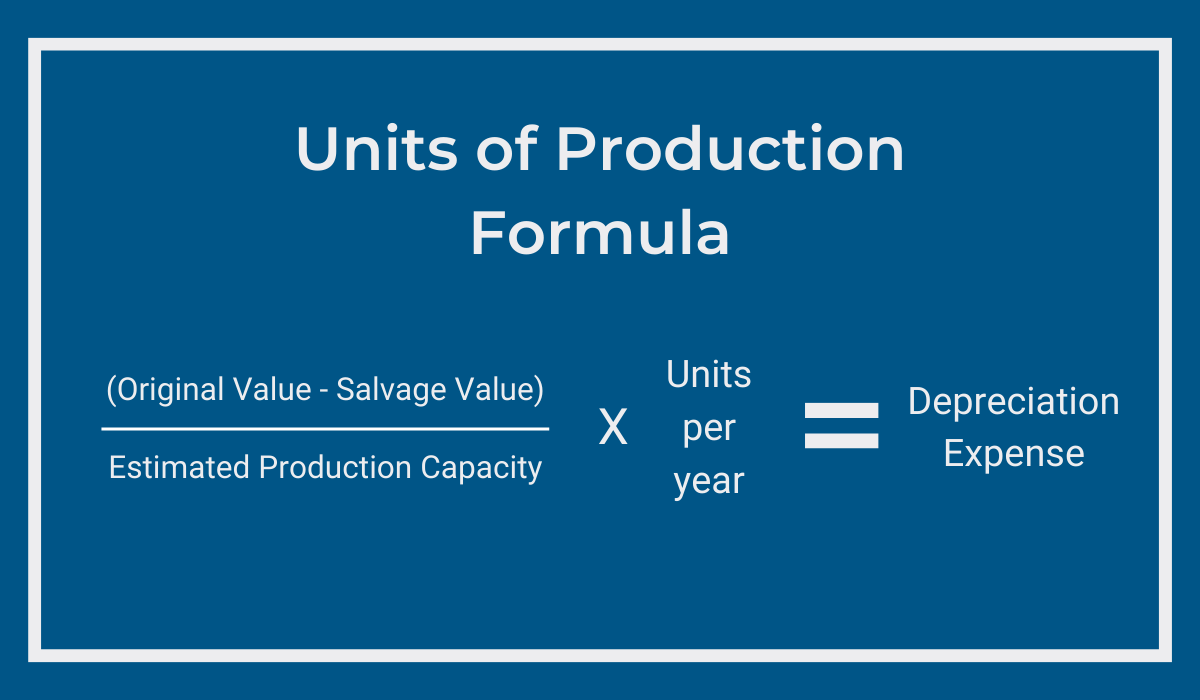
This means that the depreciation expense is going to vary depending on how many hours the piece of equipment has spent working—the more you use it, the faster the depreciation rate will be, and vice versa.
If you’re not sure which depreciation method is the right choice for your construction business, it is advisable to consult an accounting specialist to provide some guidance.
But if you’re ready to tackle the process of calculating depreciation, you may want to invest in software like GoCodes Asset Tracking to help you with that.
With our asset management solution, all you need to do is input the basic data about your equipment: the cost of the asset, the date you purchased it, and the asset life.
Then, GoCodes Asset Tracking uses this information in order to calculate annual depreciation using a range of the most common IRS MACRS schemes.
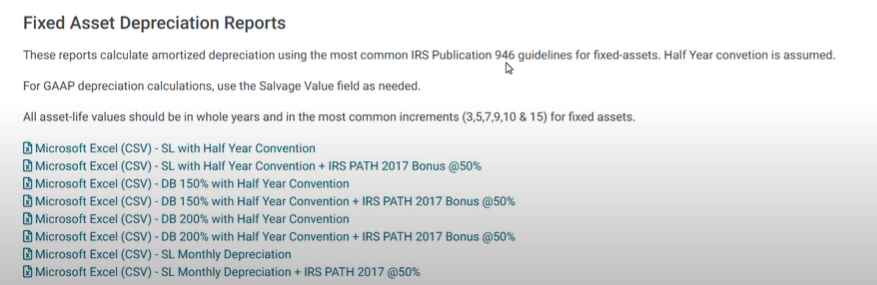
Automating this process is not only going to save you time but also help you avoid costly errors that can happen when calculating depreciation manually.
Conclusion
The topic of equipment depreciation is multi-faceted, but extremely important for every construction industry professional.
Equipment depreciation comes with various benefits, so having a thorough understanding of how it works is essential for maximizing the success of your company.
We hope that we’ve answered all of your depreciation-related questions in this article and that you’ll be able to apply this knowledge to your own construction business.