Tool tracking is essential when you’re in charge of a construction company and all its assets.
You have to know where your tools are, who is using them, and what their current condition is if you want to count on your equipment and meet the deadline set by the client.
However, this often seems easier said than done, especially when you don’t know where to start.
Don’t worry—our guide will explain the benefits of construction tool tracking, give you pointers on how to implement it, and provide tips on how to be even better at it.
In this article...
Why Should You Track Your Construction Tools?
Tracking your construction tools benefits you in many ways.
It provides you with a clear overview of every asset you own, no matter how big or small.
This allows you to decide when and where to use the equipment, depending on how many construction sites you have and what tools your workers need.
Knowing what you own also saves you from counting on items that you no longer own or that are used by other employees at the time when you need them.
Keeping track of a tool’s location will automatically make you more productive.
Most importantly, it will help you leave a good impression and positively affect your reputation.
The client who hired you doesn’t want the project to suffer delays because of something you could have avoided, like equipment breakdowns, shortages, or unplanned maintenance.
Keeping track of your assets also prevents tool-related delays.
Therefore, tracking your construction tools makes you more organized, productive, and efficient.
What Do You Get Out of Construction Tool Tracking?
It will take you a while to implement a tool tracking system and perform all the necessary steps. However, it will be worth it.
We’ll explain the benefits of tool tracking for your construction company in detail to help you determine whether it’s the right decision for you.
Accurate Inventory Lists
Tracking your tools helps you keep accurate inventory.
Firstly, without knowing what tools you even own, you risk duplicate purchases.
Those cost you—you waste money not only on buying a tool you already have and don’t use but also on insurance, depreciation, and maintenance.
When you know what you own, you avoid all this.
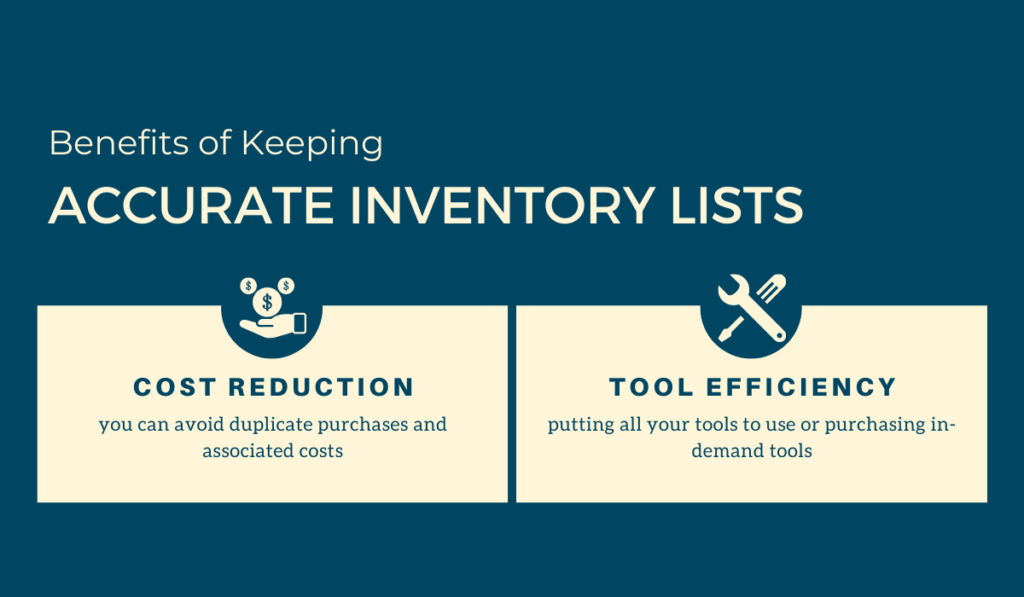
Secondly, knowing what you have helps you use it more effectively.
The inventory list shows which assets you have and can use and which ones you have to purchase to avoid downtime.
For example, if you have ten ladders but eight are already in use, you can only count on two for new projects.
If that’s not enough, you can purchase new assets before you run out, or you can schedule projects so that the second one will need the tool after the first one no longer needs it.
Having an accurate inventory list helps you be more efficient.
Saving Time
You save a lot of time when you track your inventory.
When you know what you own and where it is, you and your employees save the time you’d usually spend on locating the items across all your worksites.
If your employees can’t find a tool on the construction site, they have to contact you or someone else in charge to determine where the needed asset is, which takes a lot of time and energy and slows them down.
Tool tracking also helps you eliminate downtime.
A detailed list lets you know how many pieces of each tool you have and lets you determine whether that is enough for all your current projects.
If you have 50 pieces but need 60 for next month’s projects, you have enough time to order the tools to avoid project downtime that would cause postponements and unnecessary costs.
Knowing where your assets are saves time and energy.
Past and Present Tool Usage Tracking
Tracking your tools allows you insight into the tool’s past and current usage.
If you decide to inventory all your tools and find a way to mark the current user, you enable your team to know who’s used an asset in the past and how often your team even uses the tool.
This knowledge allows you to save money—you will quickly notice usage patterns, allowing you to sell and opt for renting the equipment you rarely use.
Such tools can cost more to own than rent, which you want to avoid.
In addition, understanding how often and for how long the tool was in usage allows you to plan to buy replacement parts or a new asset.
When purchasing new equipment, consider the equipment’s useful life.
Of course, factor in how long you’ve used the equipment for—if it’s a lot less than intended, you can count on your tools for a bit longer than indicated.
However, if you overwork your assets, they won’t last as long.
Understanding your tool’s usage helps you save money and repurchase tools on time.
Improved Maintenance
Tool tracking positively affects your maintenance processes.
If you track your tools’ usage, you know when to schedule regular maintenance.
This type of upkeep lets you find and fix minor issues, ensuring that the equipment continues to function properly without causing the project to stop or posing a safety risk.
Consult your equipment and upkeep specialists to decide how often your assets need maintenance and find a way to schedule it.
When you do this, you eliminate the risk of your equipment breaking down mid-project.
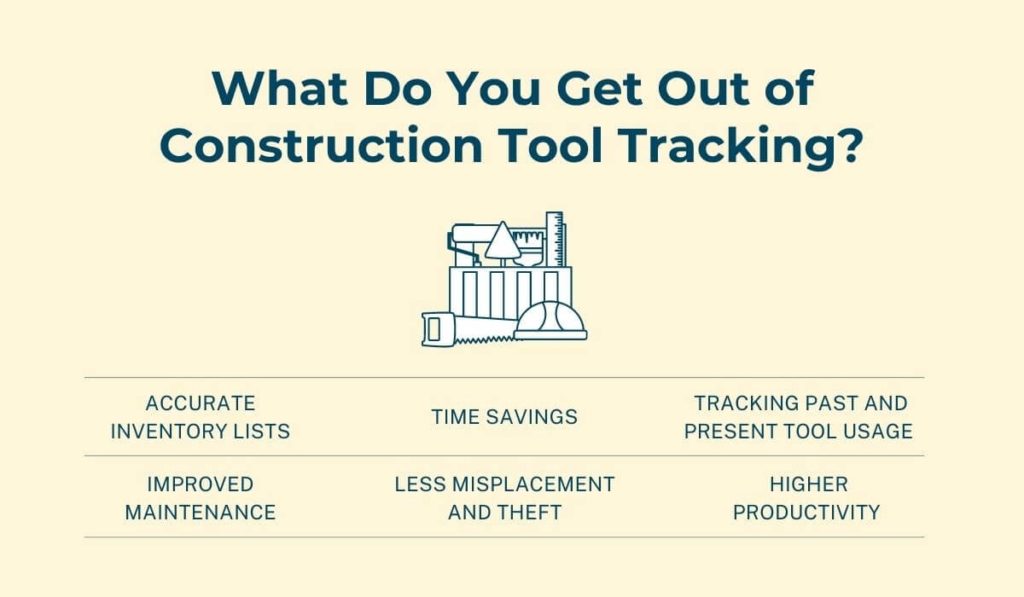
On top of this, tracking your tools and equipment lets you understand whether you’re overworking them. If so, you have to maintain the tools more often to decrease breakdown risk.
If you’re wondering when you’ll need to buy a replacement part or asset, tool tracking can help you.
Record tool usage and maintenance data to determine whether it’s time to replace an item, especially if it constantly needs corrective maintenance.
Determine whether a replacement part would fix the problem or if it would be more cost-effective to replace the tool.
When you track your tools, you improve your maintenance process.
Decreased Rate of Misplacement and Theft
If you want to eliminate tool theft and misplacement, track your tools.
Tool misplacement often happens at the construction site. Workers leave the assets lying around once they’re done with them since they have to move on to the next task.
If everyone does that and neglects to tidy up after themselves, you’ll have a large number of tools lying around the site with no understanding of whether they’re still needed.
Construction site theft happens more often than you think, which is why you should track your tools as a means of preventing it.
On 4th July 2021 alone, the US construction industry reported 219 thefts.
When you know who is using which asset and at what time, you’re assigning the responsibility for it to the current user.
They will make sure to take the equipment around the site and return it once they no longer need it, knowing you have their name on record.
Tracking your tools helps you decrease the risk of asset misplacement and theft.
Higher Productivity
Tracking your construction equipment makes you more productive.
It lets you locate your assets quickly, saving you time and energy.
When you need a specific piece of equipment, you can check who is using it if you’ve implemented a check-in/check-out system.
You should also be able to tell when the user will return the asset. That data helps you effectively plan your projects and future tool usage, maximizing your productivity.
On top of that, tracking your tools and their usage allows you to plan maintenance dates to prevent any breakdowns.
Such issues would usually cause a temporary project delay.
When you don’t have a replacement tool at hand, the project might even get postponed or canceled because the client has a strict deadline for you.
Either way, you’d be a lot less productive, which would cost you a lot.
When you track your tools and their usage, you can increase your team’s productivity.
How to Track Your Construction Tools?
Clearly, tool tracking pays off if you’re in the construction business and have lots of assets you need to track and maintain.
You not only save time and energy but get the most out of your tools and seem more reliable.
It might sound too good to be true, but it’s not—here’s how you can start tracking your tools!
Build an Accurate Tool Inventory List
Effective tool tracking starts with a detailed inventory list.
Gathering all your equipment and listing the related details is challenging—you have to find a way to inspect each asset regardless of its location.
On top of that, you have to make a note of its current status and give it a name or a code so you can distinguish between different pieces of the same tool.
You won’t be able to do all of this on your own.
First, you’ll need the help of your managers or supervisors in the field.
They can do the inventory of all assets in the field, while you can do the same for those in your office or equipment room.
Then, you’ll need to consult your equipment or maintenance specialists to determine the current state of the equipment, which helps determine the asset’s life cycle, scheduled maintenance dates, and overall cost-effectiveness.
Building a tool inventory list is the first step in tracking your equipment.
Make the Tool Inventory List Available to Everyone
Share your tool inventory list with all your employees to increase productivity.
Don’t stop once you have the definitive list. Instead, share it with all your employees who need to have access to the tools.
That way, you’ll eliminate any confusion and save time for everyone.
Your employees will be able to access the list independently and inquire about the item without asking the supervisors or managers for help.
Don’t forget to keep a manual for each tool so your workers can have it ready in case they need it.
When borrowing an asset they haven’t used in a long time, they should have access to its manual to ensure safe and efficient use of the tool.
Whatever system you choose for your inventory—pen and paper, spreadsheets, or tool tracking software—you need to train your employees on how to use it to eliminate errors.
Giving inventory list access to your employees helps them save time and be more efficient.
Install a Check-in/Check-out System
Choose a system that lets your workers check equipment in and out quickly.
An inventory list helps you understand what equipment you have, but it also makes the process of borrowing tools run more smoothly.
It will help you know where each asset is at all times, saving you time, money, and energy.
Without this system, an employee might take a tool, and, once they no longer need it, leave it in the field (resulting in misplacement), or hand it to another employee.
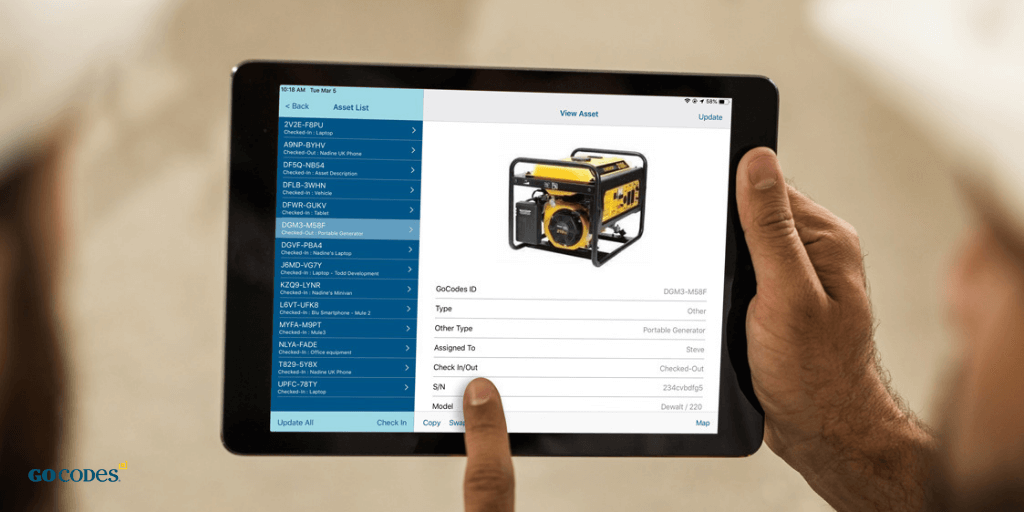
At the end of the day, five employees might use the item, and you won’t know about its usage, which will hinder the accurate tracking of various performance and maintenance metrics.
When you implement a tool check-in/check-out system, you have a way of allowing an employee to check equipment out under their name and return it once finished.
Checking equipment in and out allows your workers to be more efficient.
Place Responsibility Into the Field
Implement a system that lets you assign a tool to a user to promote responsibility.
A check-in/check-out system can benefit you in more ways than one. On top of letting you assign tools to users, it also makes users responsible for the assets.
That way, you eliminate the risk of employees simply leaving the assets behind, resulting in misplacement and, quite often, theft. How?
The employee who checks a tool out knows their name is associated with it in your system. They’re the ones responsible for the asset until they check it out, which promotes accountability.
On top of this, when employees are responsible for the tools they use, they are more likely to report a problem they notice when they check the equipment in or out, which helps you tackle downtime and avoid safety risks.
If you can’t afford lost tools, a check-in/check-out system helps you assign responsibility.
Construction Tool Tracking Best Practices
Now that you know what steps you need to take to start tracking your equipment, we want to give you some tips on how to be even better at it.
Strategically Store Your Tools
Having an excellent storing system makes your team more productive.
If your employees know where they can find the equipment they need, they save time locating it.
This might not seem like a lot, but it is, especially for the employees who work in the field and have to borrow assets from the storage room.
Even if you have a storage room on the site, the worker has to stop what they are doing and find the asset in the storage.
The more time they take to locate it, the less they spend working, which is the opposite of your goal.
Have a storage system that is easy to understand and explain to all employees.
You can color-code different pieces of smaller equipment and use the same color-coding system in all your storage rooms to avoid confusion.
A storing system saves your employees time and energy.
Create Inventory Categories
Inventory categories help you be more efficient and organized.
When you group your assets by the similarity of use, your employees will be able to locate them faster when tackling a particular task.
If your workers need a smaller tool, they can spend a while trying to find it if the smaller assets aren’t grouped together in your storage room.
However, if they are, it shouldn’t take long to locate this section of the storage room and find the asset using your color-coding or different sorting system.
Additionally, such categories allow you to place the items used interchangeably in the same section. That way, if an asset isn’t available, your workers can easily locate the tool they can safely use instead and check that piece of equipment out.
Of course, you can only do this when the assets have the same purpose.
Categorizing your inventory helps you locate the assets faster.
Audit Your Tools Regularly
Regular audits help you have correct and real-time information about your assets.
To ensure that your tools are functioning correctly, without posing a safety risk, invest in regular internal or external audits.
You can then guarantee that a preventable tool malfunction won’t hurt your employees.
With an automated tool software like GoCodes Asset Tracking, you can easily update the item’s data, allowing everyone to see the equipment’s status.
When you regularly inspect your assets and the related documents, you avoid wasting money on assets you no longer own or use.
Regular audits help you identify any changes in your inventory as you check each tool and make a note of its current condition.
They also let you determine how effective your maintenance process and recording are since an auditor will check maintenance records and understand whether the upkeep checklists are satisfactory.
Auditing your tools regularly optimizes your inventory lists and eliminates unnecessary costs.
Tag Your Tools
Take your tool tracking to the next level by tagging them.
When you find a way to mark your tools, you will be able to recognize each asset.
If you don’t have a way to differentiate them, you risk mix-ups that can lead to additional costs and breakdowns, especially if one tool is older than the other or in worse condition.
Tagging your equipment allows you to track it more efficiently.
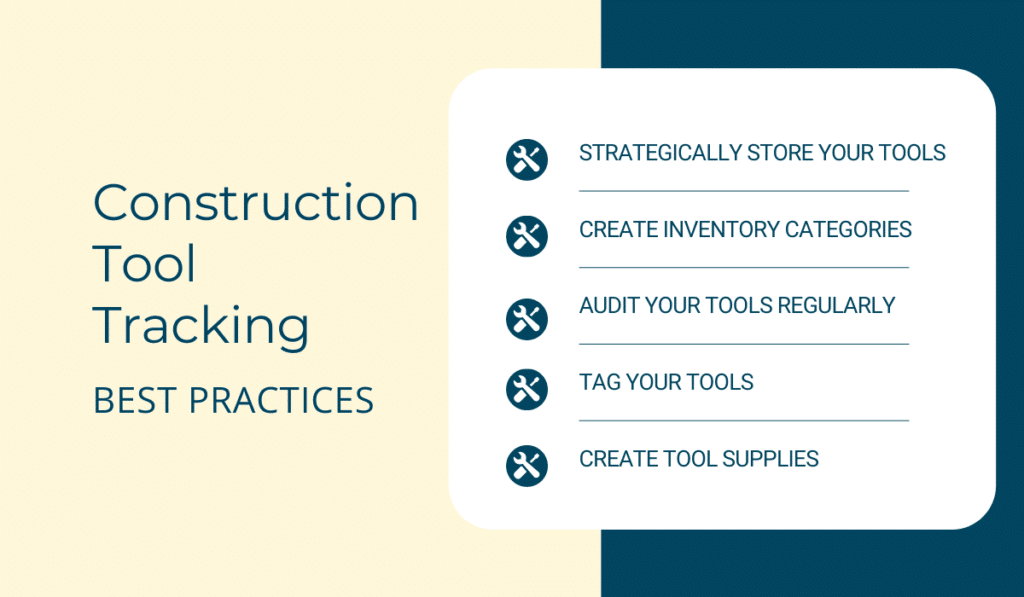
If you use tool tracking software, you can tag your assets with QR codes, allowing you and your staff to simply scan the tag when you want to check equipment in and out or inquire about its condition, maintenance, or return date.
GoCodes Asset Tracking even lets you know your tool’s last known GPS location, allowing you more control over your assets.
Tagging your tools allows you to differentiate between them and track them more efficiently.
Create Tool Supplies
Create tool supplies based on your tool usage to eliminate downtime.
Your tool tracking system allows you to see how often you use certain assets and how long it takes to reach the minimum stock of a specific tool.
With this, you can easily determine whether you need to invest in additional equipment to ensure you never run out.
If you often get these notifications for the same asset, it’s time to stock up!
By tracking your tool usage and maintenance, you can easily monitor an asset throughout its life cycle, effectively realizing when a tool is nearing the end of its useful life.
Once you notice that an asset has more unexpected upkeep dates and is often causing downtime, take the hint and purchase a new item or replacement parts—if applicable and recommended by your maintenance team.
Tracking lets you create tool supplies so you can minimize downtime and breakdowns.
Conclusion
If you’re a company that has to keep track of a lot of equipment, you should start managing it correctly.
First, create an inventory list, share it with your team, and allow them to check assets in and out to promote accountability.
That way, you can monitor who has the equipment and what condition the equipment is in.
For even better locating, ensure strategic storing, create inventory categories, and tag your tools.
Guarantee compliance by organizing audits and create tool supplies to eliminate unnecessary downtime, and you’re good to go!