How can your company achieve effective construction material management?
What strategies can be used to streamline materials management, both on the macro (the entire organization) and micro (specific construction project) levels?
How can one or more of the strategies presented here reduce costs and waste, thus increasing the overall productivity of your construction business?
Read on to find out.
In this article...
Having a Strategic Material Distributor
We all know what it means to have support in life.
And like elsewhere in life, being supported by a good and reliable strategic material supplier while completing a project is key for success. That’s why finding the right one is crucial if you want to optimize your materials management.
Any construction job boils down to a series of tasks that become more complex the bigger they become.
Major construction jobs consist of many moving parts that must be performed consecutively and concurrently with effective team communication and efficient distribution of labor, equipment, tools and materials.
However, according to a study by McKinsey & Company, around 80% of construction projects breach their budget and last 20% longer than originally planned.
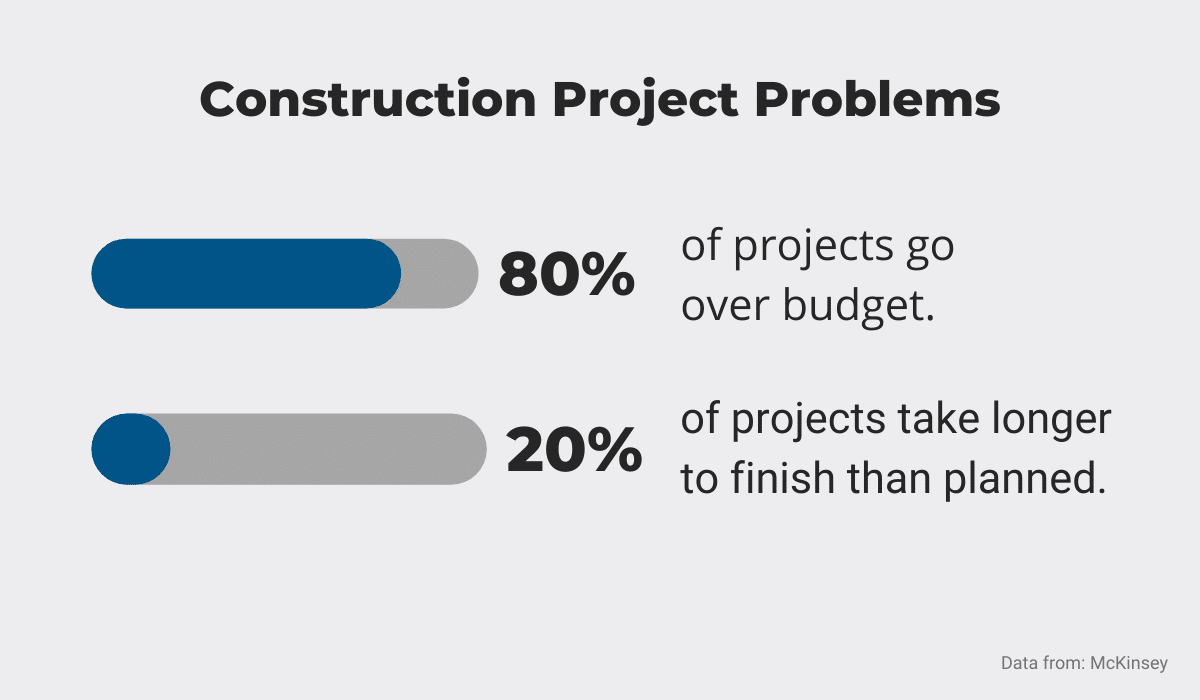
This is where your strategically selected supplier can really shine because they can ensure you’re equipped with the right materials exactly when you need them. But, to do that, they first need to check a few boxes on your “must-have” list for their selection.
Let’s begin with their offer of materials. They should have a wide range of products from several manufacturers, allowing you to choose materials that fit your quality and budget requirements.
Anything less limits your options and increases your dependence on other suppliers.
They should also come with great customer service, meaning a person or team dedicated to your project, following it through all its stages from start to finish.
Next, your ideal strategic supplier should have their own fleet of vehicles, allowing them to deliver all required materials to the right site at the right time.
Of course, the reliability and accountability of the supplier should be first on your checklist.
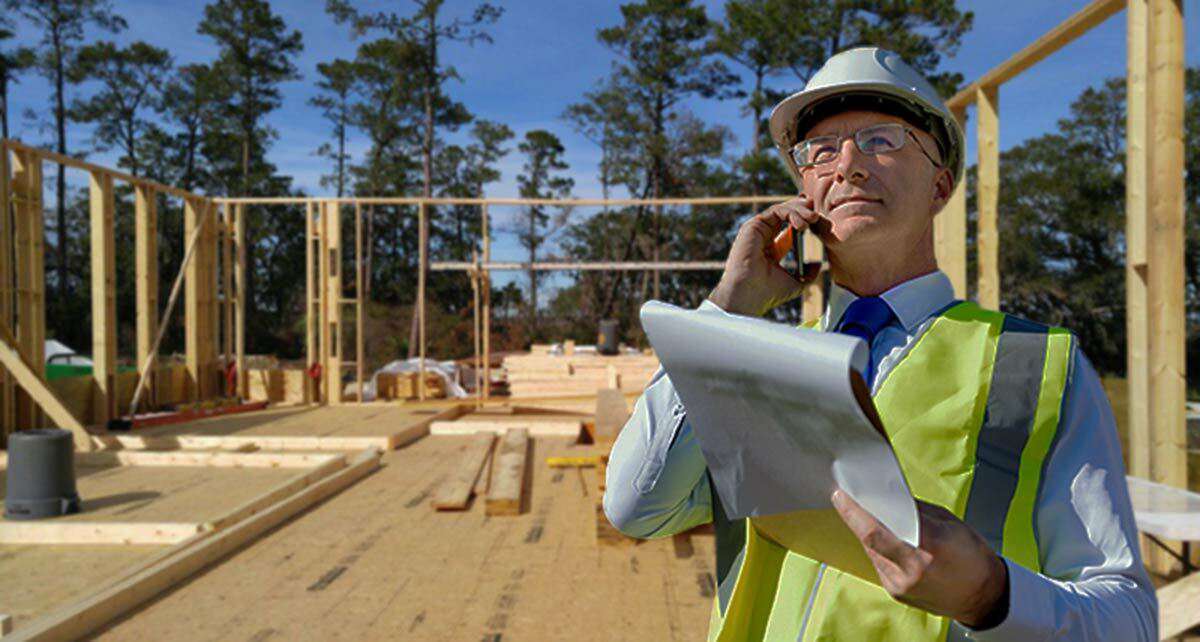
Although there may be some initial savings in finding a “mean and lean” low-cost supplier, this often entails more sizable and previously unconsidered costs.
In practice, low-cost material distributors do not keep materials on stock but rely on getting them once the order is placed. This means they’re vulnerable to additional risks compared to suppliers that keep materials in their own storage.
As for accountability, your ideal partner is the one that looks for solutions even when faced with unexpected circumstances.
This is where experience comes in.
If your supplier has been in this business for a long time, they will know all the ins and outs of almost any construction project. And they’ll be more than willing to offer their advice.
To sum up, if you choose the right strategic material supplier, they’ll be your right hand in any construction project.
Inventory Optimization
Poorly organized inventory lowers productivity and often leads to panicky overordering.
Conversely, optimized inventory—both within your company and on all its construction sites—will cut down costs and downtime that all construction projects face.
Having materials lying around the job site is never a good idea.
Even if we ignore the obvious safety hazards, you will still have to deal with misplaced, stolen, or just unused materials left after the job is done.
Finding ways to improve how inventory is kept and tracked can help you achieve lean, just-in-time construction and material management.
Here are some areas an optimized inventory improves significantly:
- Materials are delivered on time according to a predefined schedule, but not sooner.
- They are kept as close as possible to their point of installation.
- Each type of material is sorted into pre- or repackaged material kits so it can be found and used quickly and effortlessly.
As for the last one, we’ll tell you more about it in the section on material kitting.
Your greatest ally here could be using dedicated software.
An asset tracking system like GoCodes Asset Tracking provides planning tools that help optimize your company’s inventory levels, as well as the space and storage available on a construction site.
It’s a way for your company to practice both inventory and asset optimization strategies to cut down costs and boost productivity.
An effective construction material management system can be set up similarly to how, for example, Toyota uses its Kanban system to track production within a factory.
In Toyota’s car production process, parts are only ordered when a new car order comes in, enabling the factory to keep its inventory lean, i.e., have only what’s immediately required on-hand.
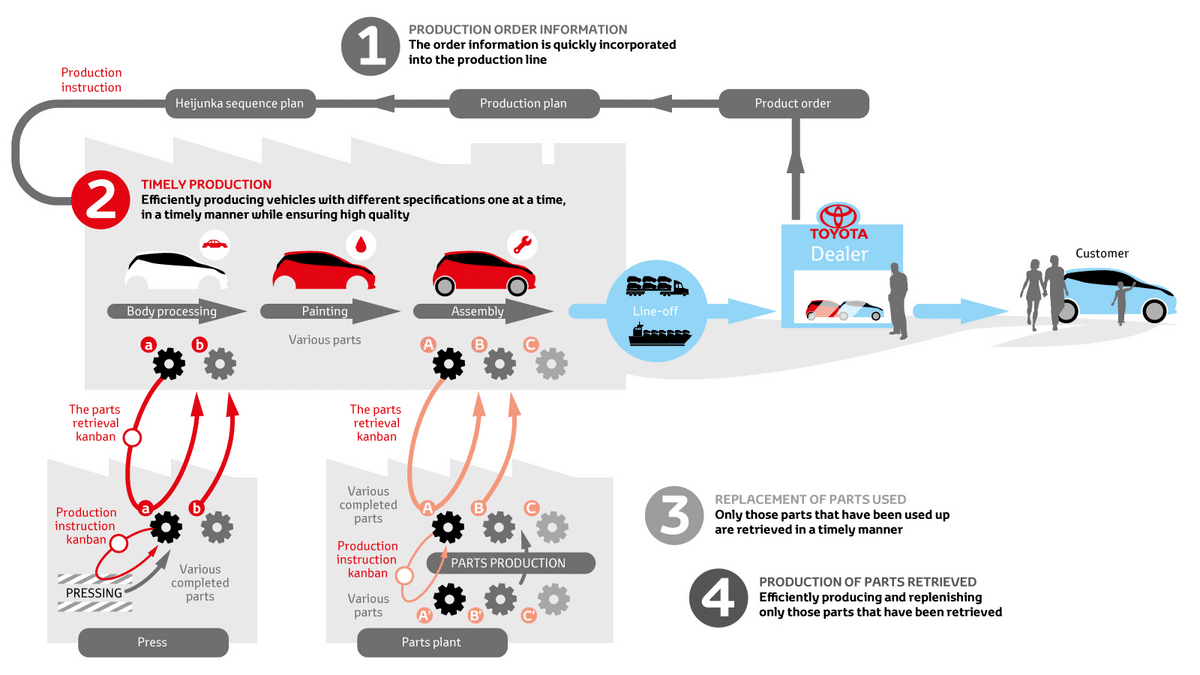
This just-in-time (JIT) production practice was quickly implemented in other areas, resulting in JIT inventory management.
In terms of an optimized inventory management strategy, the JIT principle involves close cooperation with suppliers making on-demand deliveries of materials just before their use, the goal being to have only what’s needed and when it’s needed.
After your inventory management strategy has given you an in-depth look into your material flows, now it’s time to use your supplier, namely their expertise and resources.
Knowledge about different products and their uses for your specific project is always welcome and can increase a project’s cost-efficiency, while some suppliers also offer vendor-managed inventory (VMI) services.
All in all, inventory optimization by itself can be a great strategy to keep in check all the loose ends in your construction company. When you have a good supplier, this strategy can provide additional benefits in terms of also optimizing project material planning.
Project Material Planning
Planning what construction materials will be needed on a specific job and in what quantity can be, mildly put, a daunting task. However, an appropriate project material planning strategy can make this task much less intimidating.
With so many factors to consider when trying to plan the materials needed for a whole project in advance, it’s easy to lose sight of some minor (or major) detail.
This complexity is why many contractors are still using the system of collecting on-site orders of materials a day before and having them delivered the next morning.
However, that system comes with a few flaws, the biggest ones being that materials may not be available, or their delivery may be late.
Whether big or small, such oversights lead to delays and bring down productivity.
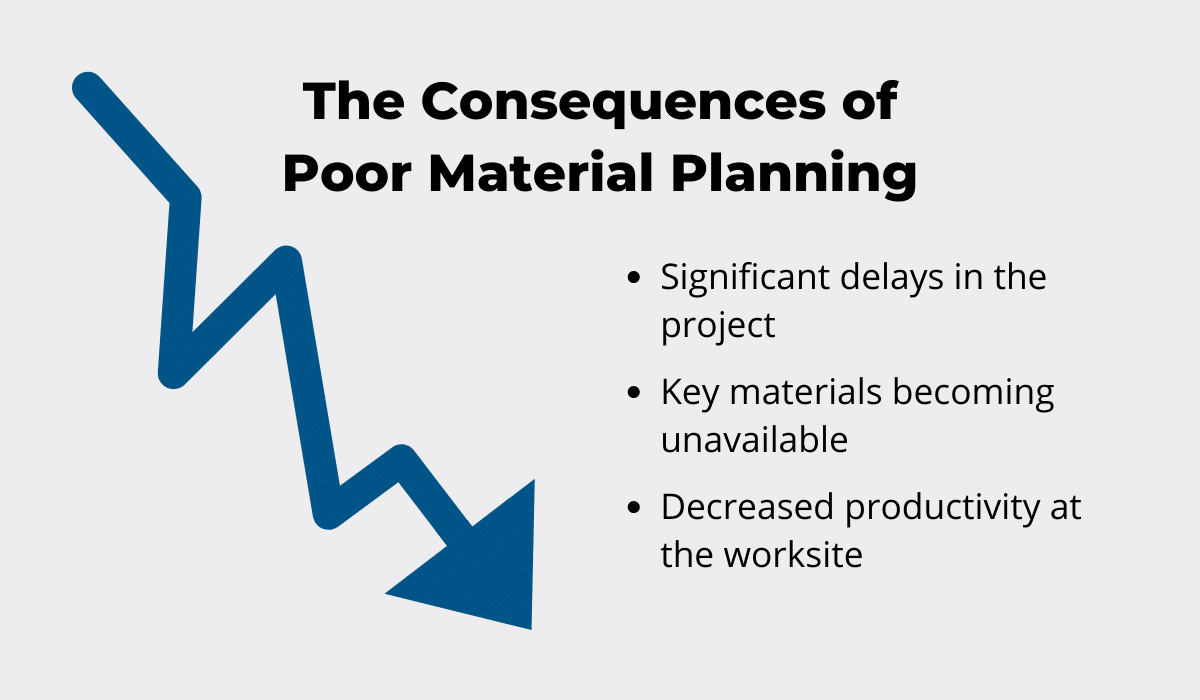
Therefore, it’s important to know how many materials you’ll need for each stage of the project lifecycle.
Your planning of materials for a specific project should start at the end.
What do we mean? Well, every endeavor starts with a vision. When applied to material planning, this means having the desired project outcome and timeline in mind from the outset.
Equipped with deadlines for each project phase and the sequence of actions required to meet them, it’ll be easier for you and your distributor to devise a material management strategy that’s custom-made for the project at hand.
Moreover, if you’ve selected a good supplier, you’ll be able to set up pre-scheduled deliveries in increments that come:
- when planned (meaning that workers don’t have to leave what they’re doing just to unload materials, for example)
- packaged so that everything needed for a specific task is already there
But, as we know, even the best-devised plans can go wrong. That’s why it’s important to keep open communication lines with your construction supervision team.
They’ll be the best source of information about any deviations from the schedule or emerging issues on a construction site.
So, an effective project material planning strategy means you’ll have all the materials in one place, and you’ll be able to track them throughout their lifecycle.
Efficient Material Storage
No matter how efficiently you plan the materials for a site, you’ll still need someplace to store them.
Hence, the objective of an efficient material storage strategy is to seamlessly tie the on-site storage of materials with all other steps involved in smooth material management.
If this part of construction site management is neglected, it can cause a whole bunch of problems – from delays and lost time while looking for them to severe or even fatal injuries.
The first thing your material storage strategy should do is to clearly define where materials will be stored even before there is a construction site to store them at.
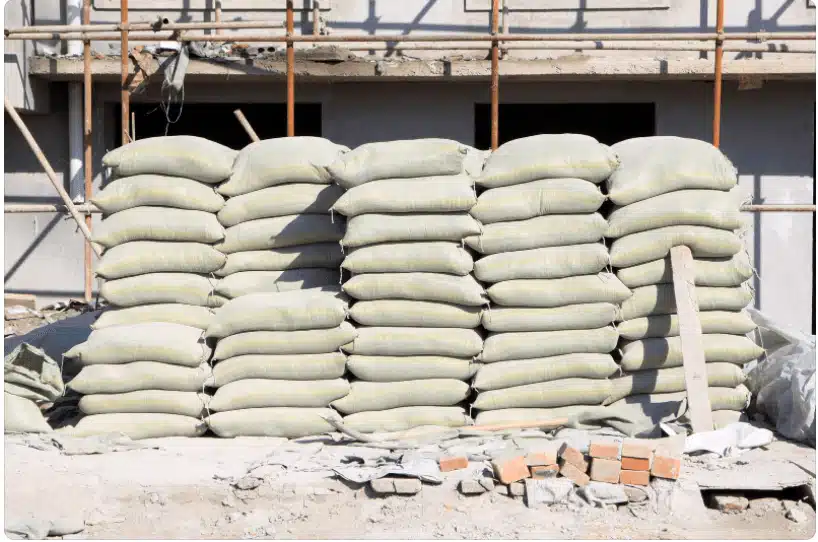
This also means thinking ahead in terms of which materials are going to be kept together and which ones cannot be stored together under any circumstances.
For example, if you store incompatible materials like chlorine and ammonia and they come into contact, this will result in the release of toxic gas.
As for non-toxic materials, another tip is to store together materials with similar use, thus increasing their utilization and reducing the leftover quantities.
Efficient material storage also involves deciding where different types of construction waste will be stored.
With the rising concern about the environmental impact of construction waste and its reuse, this will enable your company to adopt a cyclical approach to waste management, thus demonstrating your concern for the environment.
You may, for example, have designated areas for different types of waste, such as wood and metal scraps, glass, paper/cardboard, and waste chemicals.
When planning storage, you should also estimate where the main vehicle and foot traffic routes on the future construction site will be and try to keep materials away from such areas.
This can greatly improve safety at the site.
Another thing that can bolster site safety is clear rules and procedures for transporting, stacking, and storing materials at height. This is where things like a shrinking wrap, guard rails, and safety straps can be very useful.
If you want to learn more about material handling and storage, you can find OSHA’s guidelines on how to do it here.
As we wrap up this section, it’s evident that the strategy of having well-organized material storage on construction sites brings loads of benefits, which include improved workflows, enhanced safety, and effective waste minimization.
Material Kitting
Material kitting plays an increasingly important role in effective material management. And that’s no surprise since this strategy can improve productivity and minimize waste in construction sites.
Kitting refers to a material management strategy where different materials that are not related in any way other than the place of their installation are collected, packaged, and delivered together as one “kit”.
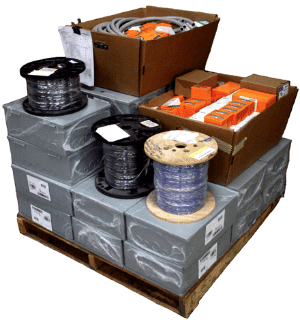
That way, the workers immediately have all the materials they need for a particular construction task at their disposal.
Although kitting has long been proposed as an effective way to organize JIT material deliveries to construction sites, there are still too few studies concerning its effects on on-site workflows.
In one case study that aimed to correct this, the authors researched a company that was transitioning between a traditional, non-kitting model and a new kitting strategy.
Long story short, they found that kitting can streamline installation works and considerably increase labor productivity.
Seeing as the time (and thus also the money) wasted on searching for materials on a construction site accounts for 10-15% of the total work time of construction crews, it’s surprising that the construction industry has until recently more or less ignored kitting as a viable material management strategy.
However, the use of digitalized construction processes and real-time tracking is quickly making up for this.

Source: GoCodes Asset Tracking
The benefits of kitting include the fact that materials are usually not pre- or repackaged on-site but elsewhere, which reduces the amount of packaging waste and non-compliant materials found there.
Furthermore, unlike bulk materials, kits can be delivered as close as possible to the planned place of installation.
In terms of material management, this reduces the number of times workers have to stop what they’re doing to get materials out of storage or move them from one storage unit to another, more convenient location.
So, kitting is an excellent material management strategy that, when fully integrated into the supply chain management process, produces many benefits.
Material costs and waste go down, while on-site safety and productivity go up.
Conclusion
In conclusion, we hope that the strategies given here provided you with some valuable insights into how to enhance construction material management.
As we’ve seen, applying just one of them can bring a multitude of benefits. Implementing more than one or all of them can thus hugely improve your company’s bottom line, propelling it into a better future.