Do you frequently find yourself cutting corners on maintenance?
Is your motto concerning equipment breakdowns “we’ll cross that bridge when we get there”?
If that’s the case, imagine if your operator overworked a poorly serviced piece of machinery until it malfunctioned, damaging the project, materials, and itself in the process.
Who would you blame?
The only correct answer is yourself, and that’s concerning.
If you want to change this and take your equipment maintenance practices to the next level —you’ve come to the perfect place.
This article will explain why you have to insist on regular maintenance and how to get there. Follow these steps to have well-maintained, reliable machinery and informed and safe staff.
In this article...
Why It’s Important to Maintain Construction Equipment
When you’re in the construction industry, you’re aware of how vital equipment maintenance is.
Without it, your company will bleed money until it runs dry, leaving you bankrupt with a lot of unusable equipment.
Therefore, it’s no surprise that the machinery maintenance and repair service market is worth $43.6bn. Equipment owners understand that no good work can be accomplished, especially not safely, without timely and proper maintenance—and it shows.
Let’s examine this more closely.
Firstly, regular servicing helps you prolong the useful life of your equipment.
While it’s true that most machinery has a long useful life (see the graph below), why not get more out of it?
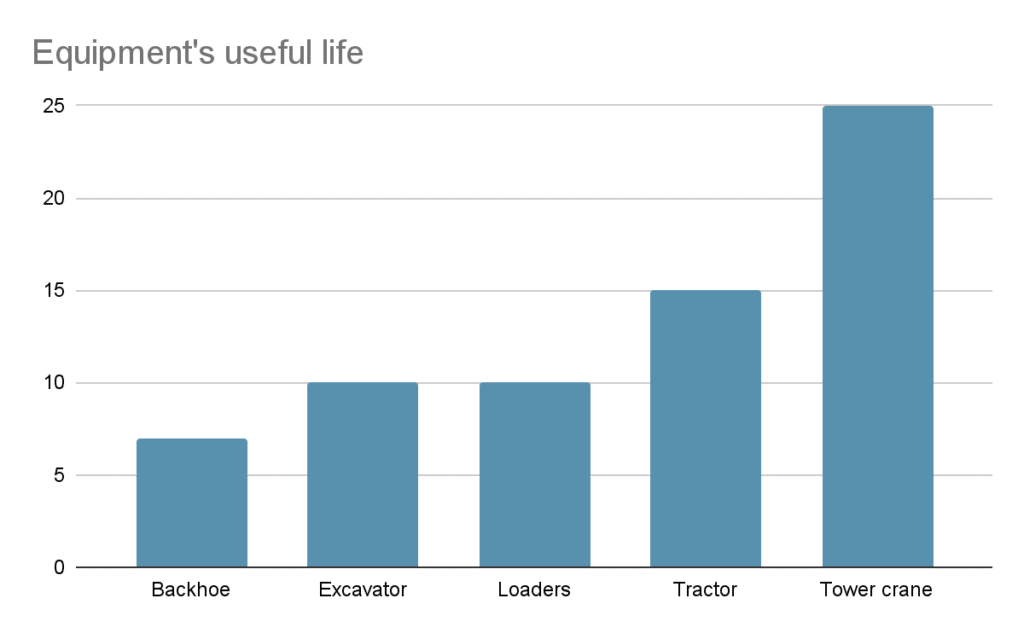
You can use an excavator for approximately ten years. However, with regular servicing, you can get another year or two out of it, which means you don’t have to buy a new excavator as soon as you thought.
Therefore, maintenance also helps you save money along the way.
Roberto Bogdanoff, a key accounts customer solutions director at Volvo Construction Equipment, agrees that maintenance saves money:
[Upkeep reduces costs] directly for machine downtime and costly unscheduled repairs, and indirectly since the equipment that is not operating because it is down can shut down an entire production site, costing thousands and in some cases millions of dollars.
Mr. Bogdanoff’s assessment makes perfect sense to anyone in the construction industry- Equipment failures represent a major drain on your resources.
On top of money loss, the lack of maintenance can cause:
- expensive project downtime
- further delays on other projects that have to use the same machinery
- costly urgent repairs
- rent of replacement equipment while you’re working on fixing the issue
- disrupted maintenance schedule
- safety issues
- legal problems
Of course, equipment upkeep can’t entirely eliminate breakdowns, no matter how good it is, but it does give you a great start.
Regular servicing helps you find and remove potential threats. As a result, your workers will feel safer using the equipment.
On top of all that, investing in maintenance means investing in the reliability and longevity of your machinery.
Now, let’s see how to do it right.
1. Set Up a Construction Equipment Maintenance Program
There’s no maintenance without a detailed program.
Well, there is, but it won’t be as thorough or regular. Therefore, what’s the point?
Since servicing benefits you in more ways than one, you should ensure that you’re doing it right.
The first step towards that is creating a quality equipment maintenance program. It will help your team understand:
- what to check
- when to check it
- who is in charge of conducting the checks
- who is in charge of program implementation
All of these aspects are necessary if you plan to have regular servicing and keep your equipment in good working order.
Besides, without these instructions, two workers might do a completely different job on the same equipment, leading to certain issues slipping under the radar.
Here’s how to avoid that and create a bulletproof maintenance program.
You should begin by making an inventory and writing down each piece of equipment you own. When doing this, remember to include all the details, such as the purchase date and current condition.
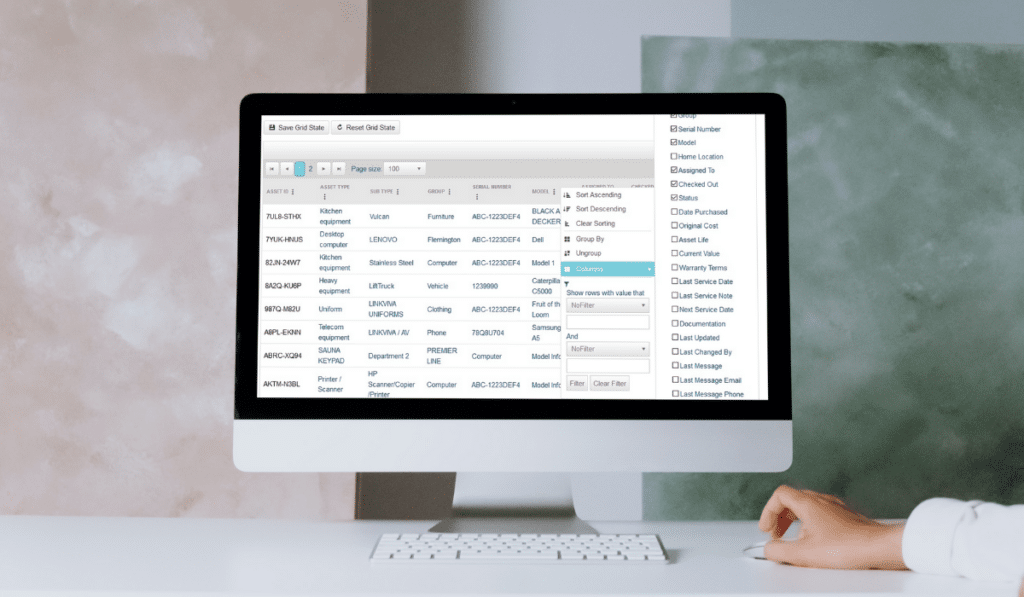
After you have a final list of machinery, it’s time to decide on the best way to service each piece.
The program should detail all the necessary servicing steps for the machinery.
Clearly, this task will be extensive and time-consuming. However, you can’t guarantee that all points are checked every time without it. Is that a risk you want to take?
You can help your maintenance staff out by writing these steps down in the form of a maintenance checklist. Having lists of necessary checks ensures that your employees never forget a step.
Of course, the checklists will be different for every type of machinery you’re dealing with, but nothing’s stopping you from creating one for each piece of equipment.

When you have a clear overview of all the activities, you should figure out how often you need to do them.
Here’s where your maintenance team comes in handy, as they can offer you insight into your equipment’s condition and requirements.
And finally, you have to put someone in charge of the tasks. Which team will perform which tasks? It’s up to you to determine who is qualified to complete specific steps and what kind of knowledge is necessary.
Once you have that written down, assign someone in charge of the program as a whole—a person who will track the progress and change the plan when necessary.
Creating a maintenance program is not easy, but it’s necessary for quality regular servicing.
2. Educate and Train Your Staff
Having a great maintenance program will mean nothing if your staff doesn’t know how to implement it. That’s why you need to invest in educating your team!
Here’s one more reason to focus on training: operator errors account for 18% of unplanned downtime. That percentage is really high for something preventable.
So, what can you do to fix it?
You can start by offering extensive training that will not only explain the maintenance plan and process in detail but will also teach the staff how to implement it. Arm your team with the knowledge on why and how to perform these tasks.
But, don’t stop there. Instead of settling for one training session, make them a regular occurrence to refresh your employees’ knowledge.
For example, if you know that your team will soon have to work on a bulldozer, why not go through the checklist with them beforehand? It will make the staff more confident in their work.
Are you wondering if that much education is a waste of resources? Just remember fleet manager Kevin Schlangen’s stance on it:
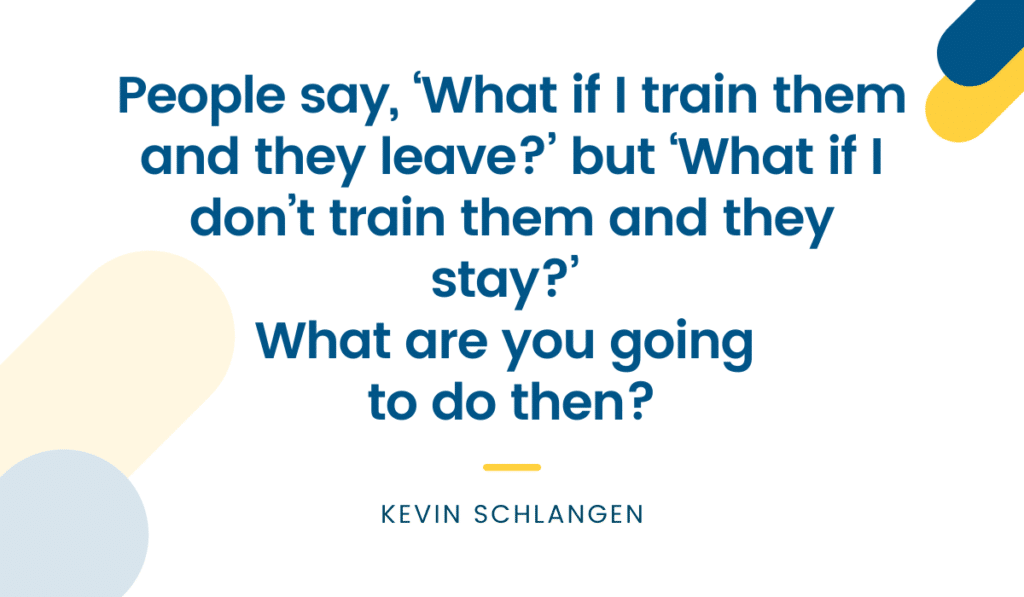
Isn’t that a scary thought? Letting incompetent or inexperienced technicians work on your machinery is a recipe for disaster.
The resources you spend on extensive and regular training are nothing compared to what you will have to invest if it comes down to fixing the errors and other consequences of inadequate maintenance.
Moreover, don’t let training stop just at the maintenance team. Instead, educate the equipment operators as well.
They should know how to use the machinery, but you can also teach them how to carry out basic repairs. On top of that, make sure you explain how to recognize the warning signs of potential issues.
That way, you’ll ensure that your operators notice a problem as soon as it appears, and notify your maintenance team, who will be armed with the knowledge to solve it.
Now that you know who to train, let’s discuss what you should teach them.
Clearly, you’ll have to discuss the maintenance program and checklists in detail during the training. That’s the basis of your upkeep, so make it informative.
You’ll also have to let the team practice under supervision, so they get some experience before applying what you’ve taught them in the field on their own.
There’s one more thing to cover in your maintenance training: the manufacturer’s warnings and instructions. Without covering this point, your training will be insufficient.
Roberto Bogdanoff, whom we’ve mentioned before, has a word of advice for anyone who wants to train their servicing staff properly. He says:
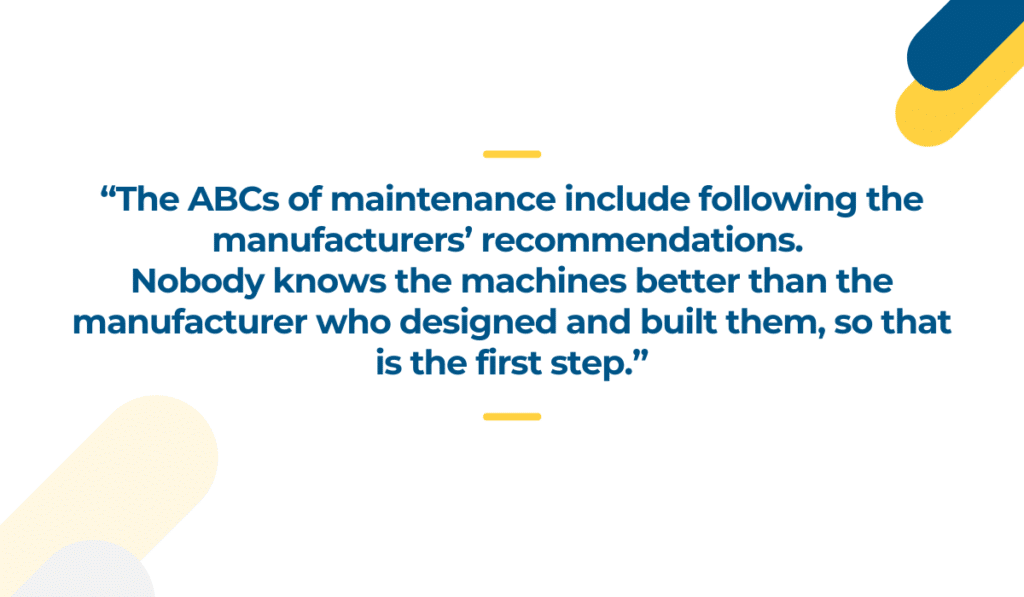
As Mr. Bogdanoff said, you can’t organize proper training without including the manufacturer’s manuals. After all, the manufacturer has more knowledge and experience with the equipment than you or your staff.
Why not use that to your advantage? Make consulting the manuals a part of the regular and refreshment training alike.
Staff education is a vital step of construction equipment maintenance. The more you spend on training, the better state your equipment will be in.
3. Implement Regular Equipment Checks
If you want to bring your maintenance to the next level, inspect your equipment regularly.
To be able to carry out these inspections regularly, you have to understand a couple of things.
First, you have to be familiar with the causes and types of equipment failure. When you understand this point, it will be a lot easier for you to repair the machinery and safely use it again.
So, what causes equipment to fail?
Most probably, it’s on these three factors:
- thermal conditions: extreme temperatures and conditions can push the machine beyond its designed limits and cause a malfunction.
- mechanical malfunction: a piece of machinery can snap or break due to wear and tear, improper use, or overuse.
- erratic breakdown: the least predictable type of failure that happens out of the blue and is usually caused by a partially malfunctioning piece of machinery which causes further damage.
Once you’re aware of the conditions that can negatively affect your equipment’s performance, you can warn your team to be on the lookout as well. The first two causes are preventable if you pay attention to them and check the machinery regularly.
Another important thing your maintenance team should be aware of is the type of failure the equipment is experiencing. The following image describes them.
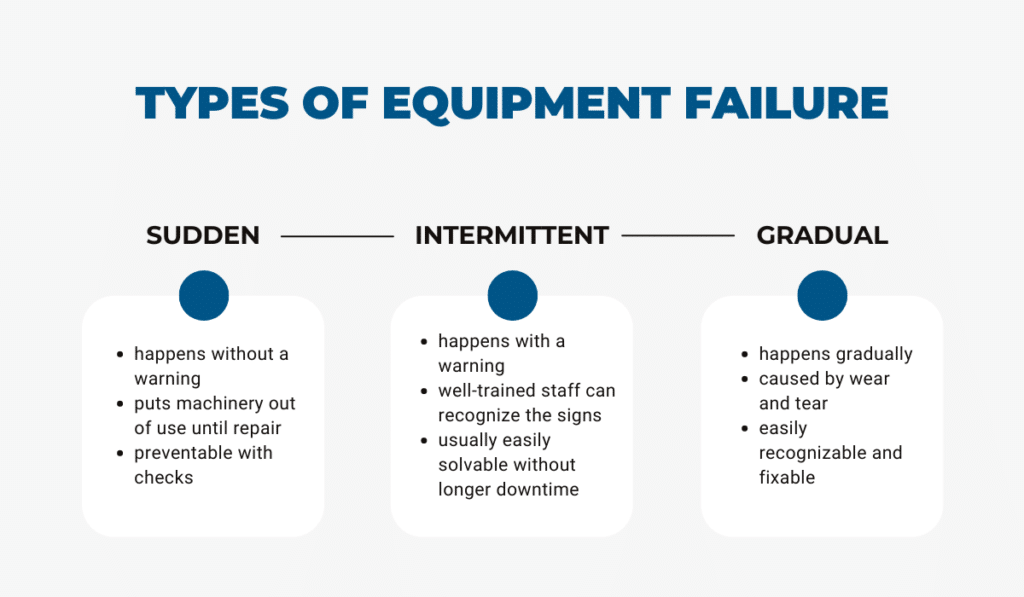
As you can see, the only unpredictable type of failure is the sudden one, as it occurs with no prior warning. Still, frequent maintenance can help you locate any weak or concerning machinery parts and monitor them, and thus avoid unwanted surprises.
Regular checks can also help with the other two types—intermittent and gradual—as they are both accompanied by warning signs. Your team members should be able to recognize these signs and warn the maintenance team on time.
Because of this, it’s essential to carry out maintenance checks regularly. So, don’t service an asset only after it breaks down, but rather stick to a schedule you’ve agreed on with your team when creating the maintenance plan. It will let you find and fix the causes of possible breakdowns to stop machinery from failing.
An extensive servicing session is something you will do once or twice a year. But, you should also plan for smaller maintenance tasks before and after every use.
Why? They help you find and prevent issues before the scheduled servicing session.
When your team does a quick check of the equipment before operating it, they ensure that it’s safe to use.
If they also do it when they return the machinery after they’re done with it, they can spot any changes or issues and notify the maintenance team.
For instance, one thing you can check to optimize your servicing is the equipment fluids.
Teach your maintenance team to do this, but don’t forget about the operators and field staff. Any of them can perform this basic check and top the fluids up to ensure smooth usage.
Besides, this is something they can check before and after every use, as well.
However, there’s a catch! If you schedule this activity too, without considering the bigger picture, you might end up wasting money.
A study by the US Department of Energy shares an example of a manufacturing company that switched the way it changed the oil in its machinery.
At first, the company stuck to preventive maintenance and changed the oil of their 400 machines in regular intervals. Then, they decided to switch to the condition-based system only for the oil and saved $54,000 per year.
Why? They were wasting oil when regularly filling it up instead of checking the levels and filling up the machines when necessary.
When your maintenance team implements service as a regular activity, you’ll start seeing a decrease in equipment failure.
4. Keep Maintenance Records
Let’s see why tracking your servicing tasks is so crucial for your business.
First, maintenance tracking helps you prove regulatory compliance. Think about it: whenever there is an accident with a piece of machinery, you can use the servicing logs to prove your constant investment in the equipment.
Service logs also let you build a maintenance database. Through it, you have access to data on the servicing of each piece of equipment throughout its useful life. Since the result of each session will be listed, you will be able to make informed decisions when investing in a new item.
Besides, maintenance tracking helps you figure out how efficient your maintenance process is. When you notice that specific machinery keeps coming back for servicing, either your team didn’t fix it well, or there’s a bigger issue at hand.
Therefore, keeping records of your maintenance sessions is a must if you want to reap these benefits.
So let us show you some best practices for keeping maintenance records!
Keith Floyd, a plant manager at Mid-Continent Coal and Coke Company, believes that very soon, all maintenance managers will have to adopt technology in their everyday work. He says that:
Everything will have to be done through tablets and computers and those still using paper copies will be left behind.
Mr. Floyd is onto something: statistics show that more and more companies are switching to computerized maintenance management systems (CMMS) to track their maintenance. In fact, 66% of service specialists from different industries use CMMS.
Are you one of them? If not, it’s time to start.
Look into software that can help your staff quickly add data into the system. But also, ensure that all the logs can be found in the same place for a complete overview of the equipment’s condition.
Another good practice for your company is to document every maintenance session.
Think of it like this: if you don’t log it, it didn’t happen.
If a particular piece of equipment causes damage, you’ll need to have each maintenance log at hand to prove that you’ve done your part to prevent that from happening by investing in regular upkeep.
That’s why every service session matters and should be entered into the system, no matter how small or insignificant it may seem.
Besides, if you record each maintenance activity, you create a routine. According to the University of Warwick’s research, developing a habit doesn’t depend on how much you enjoy an action but how often you perform it.
So, even if recording each maintenance session is tedious, your workers will get into the habit of doing it. All you have to ensure is that they repeat the action, by recording every session.
That way, they’ll start to do it automatically, and you won’t have to worry about them forgetting to log something crucial.
So, once you start recording every session, make sure that the logs are available to everyone on your team, be it the operators, maintenance team, or those in the field.
Software like GoCodes Asset Tracking lets you tag your equipment with QR codes. Then, by scanning the tag or by simply searching your database, you can access the machinery’s page in the app and see all relevant data, including maintenance logs.
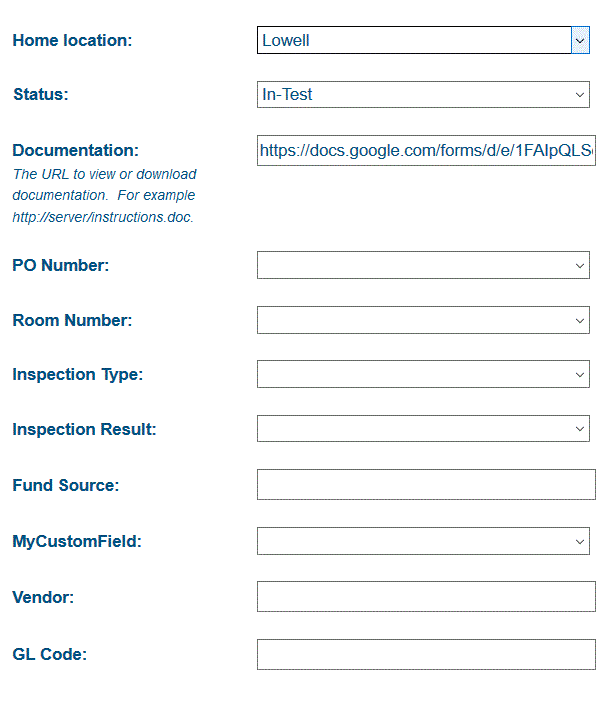
Anyone who has access to the app can do the same when scanning the code or searching for the asset manually.
In sum, using technology to help you keep and access records is a great way to optimize your team’s efficiency.
Conclusion
So, what do we want you to take away from this article?
If anything, it’s that failure-caused disasters cannot happen if you invest in the maintenance process and educate your staff about it.
The days of running equipment to the point of failure are long gone. The new way means developing a great maintenance program that covers the process from start to finish.
Pair that up with a well-trained and knowledgeable team, and you have yourself a winning combination.