Effective asset monitoring is essential in the construction business, as it allows companies to keep track of what they own, optimize their asset utilization, and improve operational efficiency.
A well-implemented asset monitoring solution not only lowers the risk of theft but also extends the assets’ lifespan, saving valuable time and resources for revenue-generating tasks.
It also establishes accountability among employees and offers valuable insights into business performance.
Without question, the benefits are abundant.
This article covers the most crucial ones that will undoubtedly enhance your company’s overall performance and foster growth.
In this article...
Centralized Asset Information
As new technologies evolve, the playing field has moved to the Cloud, especially when it comes to data storage and employing tech services.
In this intense technological era, businesses are evolving, too, embracing innovative solutions to enhance efficiency and boost revenue.
Asset monitoring solutions are a pivotal part of this game change.
One of the standout features of such solutions is centralized data management, which ensures that all pertinent information related to your company’s assets is securely stored in one place and readily accessible to authorized personnel.
This convenience allows workers and managers to access crucial asset information from any location at any time, notably simplifying the entire asset management process.
In other words, an asset monitoring solution provides a clear and real-time view of the company’s assets, significantly contributing to a streamlined workflow process.
This means knowing how many assets are on hand, where they are located, and who is using them at any given moment.
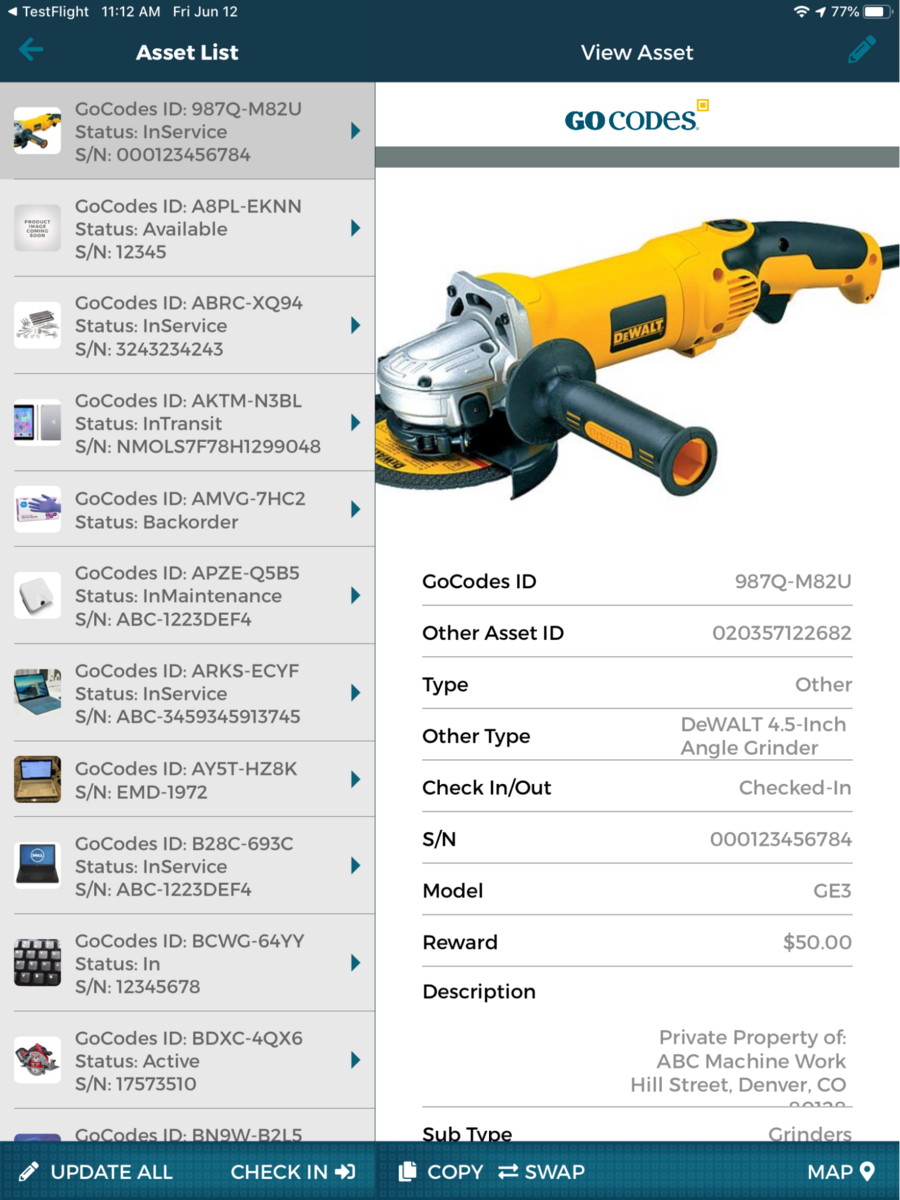
More often than not, workers find that someone else is using the equipment they need. Waiting for that piece to become available can cause delays.
The centralized asset monitoring system will enable workers to coordinate their tasks more effectively and avoid wasting time searching for tools or equipment.
With this advanced tech solution, they can quickly identify available assets and avoid unnecessary downtime, ensuring work proceeds smoothly.
Simultaneously, managers will be able to do better planning and prioritizing and optimally employ their assets on construction sites.
Having all relevant asset information stored on a centralized cloud-based system not only enhances employee coordination, it can also facilitate improved asset inventory and higher overall productivity.
Maximized Asset Utilization
To be able to run building projects and daily operations, construction companies make significant investments in buying or renting machinery, equipment, vehicles, and tools.
As an illustration, an excavator—an essential piece of equipment for any job site—can cost from $100,000 to $500,000 for a full-size rig and $80,000 to $150,000 for a mini excavator.
This isn’t the kind of machinery you’d casually leave lying around.
Moreover, you’ll definitely want to maximize its utilization and ensure a return on your investment.
It’s a fact that mismanagement of critical assets can significantly hinder productivity, causing companies to lose money.
Therefore, learning how to allocate and utilize equipment efficiently is of fundamental importance for any company’s success.
Asset monitoring software plays a central role here.
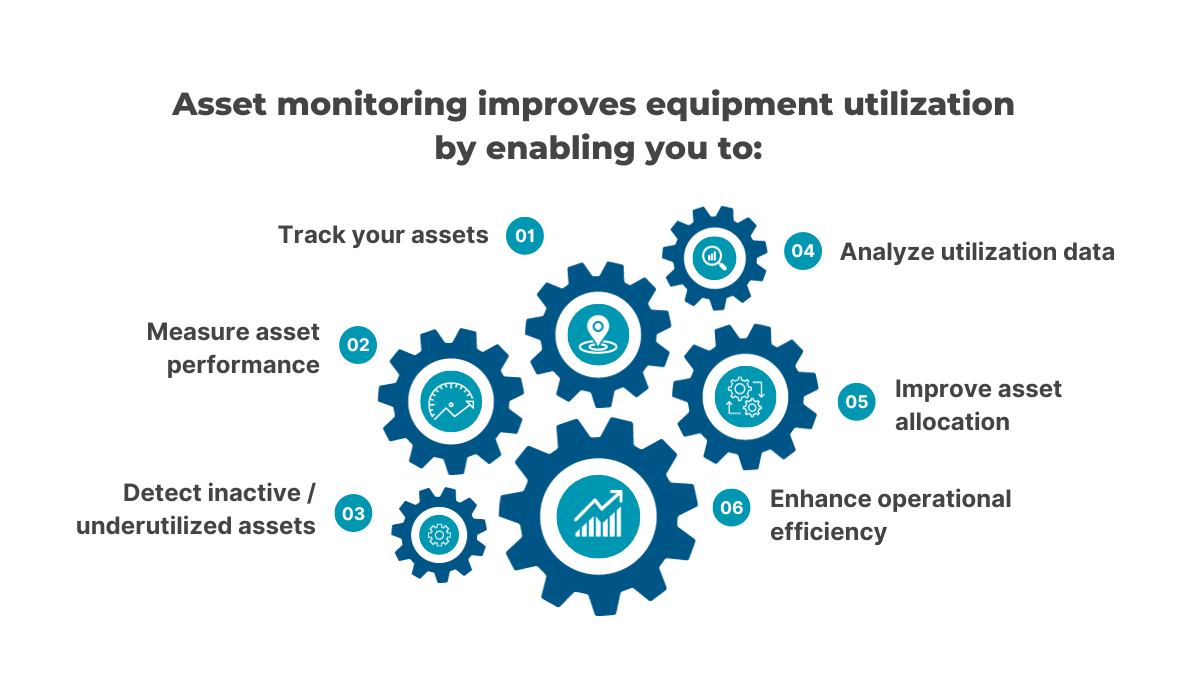
It not only enables tracking of assets, but it lets you measure how well each asset is performing and helps you identify overused items at risk of damage.
It can also assist you in detecting inactive assets that could be better used elsewhere.
For instance, by analyzing equipment utilization data, you can decide to relocate an underutilized piece to a site where it’s in higher demand.
In other words, the asset monitoring software ensures your assets are allocated effectively and utilized to their full potential.
In turn, by optimizing equipment utilization, you’ll be able to meet project deadlines without compromising the quality of your work.
In essence, this tech tool not only ensures asset visibility but also aids in streamlining operations, ultimately contributing to reducing costs and enhancing efficiency.
Longer Asset Lifespans
One major issue at construction sites is unexpected downtime from sudden equipment failures.
These issues—often caused by poor preventive maintenance—not only lead to project delays but also unexpected repair costs.
A solid preventive maintenance schedule will keep your vital assets running smoothly and extend their lifespan.
In this case, employing an effective asset monitoring solution will make all the difference.
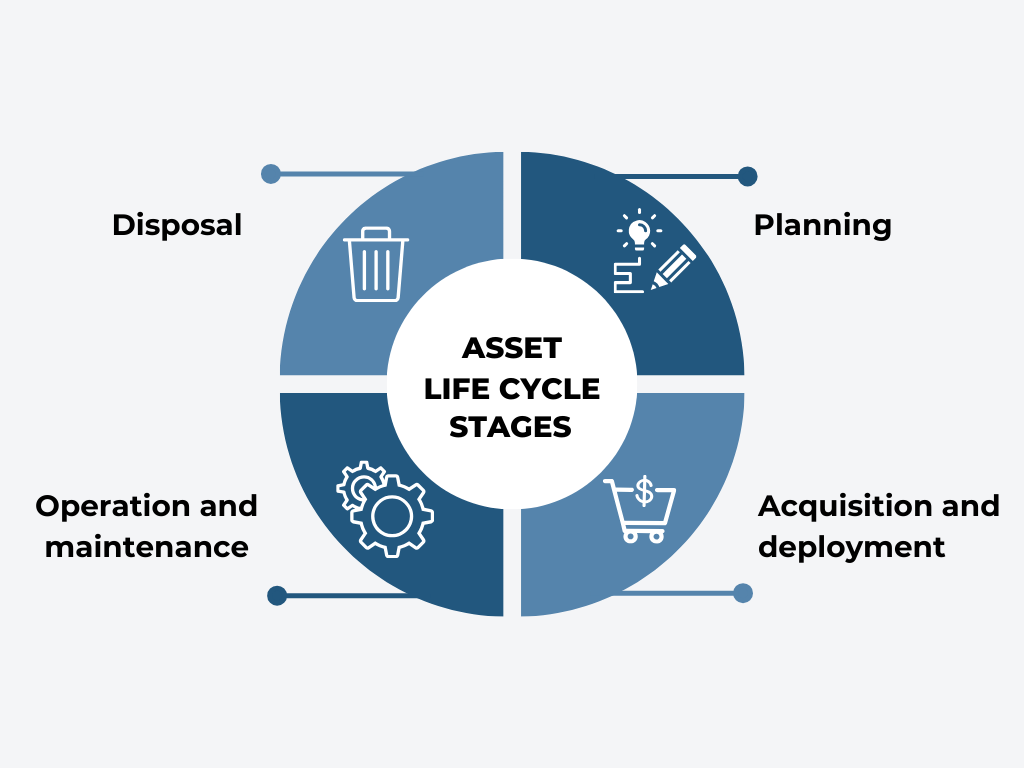
Let’s explore the tools and features that this software offers.
To begin with, an efficient asset monitoring system allows instant access to your asset utilization history and maintenance records.
There, you can also find all the information associated with a given item, including operation manuals and manufacturer’s care recommendations.
You can use the maintenance scheduling feature to establish a future service date.
The notifications feature will then send a scheduled service alert to your maintenance team.
Furthermore, if a piece of equipment suddenly malfunctions or breaks down in the middle of a construction project, this software solution enables your workers to file field service requests immediately.
They can do this simply by scanning the asset label with their smartphones.
The request message, referencing the scanned item, includes a date, location, and any information concerning the issue entered by the user.
In response, management can promptly dispatch a team of technicians to the site, preventing extended downtime and saving resources. In fact, whenever a piece of equipment sustains damage or shows signs of imminent failure, you can create and assign a maintenance work order.
The detailed information and data about the equipment and the current issue will allow your maintenance team to take immediate steps and get it up and running again.
The system also empowers you to track work orders, ensuring that all inspections and preventive maintenance are completed on schedule.
This feature will support your efforts to do better budget planning and inventory control and help you manage equipment maintenance more efficiently.
Remember, routine servicing and repairs are generally less costly than reactive fixes, substantially extending the asset’s average lifespan and usefulness.
After all, the longer your assets are in use, the better your return rate.
Improved Employee Safety
It’s a well-known fact that on construction sites, potential dangers for workers lurk at every corner. Consequently, construction has the highest fatality rate compared to all other industries.
The U.S. Bureau of Labor Statistics reports that, in 2021, 46.2% of all workplace falls, slips, and trips with a fatal outcome occurred in the construction industry.
This means that nearly 1 in 5 workplace deaths occurred in construction sites.
Companies are putting great effort into ensuring their workers’ safety by enforcing strict rules and following regulations.
An asset monitoring solution can help in this area, too.
Keeping track of your company’s assets—such as power tools, heavy machinery, and equipment—provides crucial insights into their life cycle, utilization, functionality, and maintenance.
This process enables you to uncover equipment at a high risk of breakdown, that could accidentally harm your workers, and schedule preventive maintenance.
Implementing a consistent maintenance schedule will allow you to proactively identify and address potential threats, fostering a safer environment for workers when using the equipment.
Furthermore, with asset monitoring software in your tech stack, you can control employee access and ensure that only qualified and properly trained workers operate specific machinery.
This precaution is crucial to preventing mishandling-related accidents and injuries and promoting workplace safety in the inherently dangerous field of construction.
More Employee Accountability
Construction generally involves substantial investments in equipment and machinery to support complex building operations.
Despite this, workers often overlook equipment and tools, focusing solely on their tasks and pressing deadlines.
In such circumstances, tracking construction equipment becomes challenging, especially when assets move across locations on various building projects.
The asset monitoring system not only keeps track of every piece of equipment deployed on job sites but also significantly enhances workers’ accountability, ensuring proper care and usage.
Here’s how.
Namely, one of the main components of monitoring software is the check-in and check-out feature.
This requires workers to check out a piece of equipment whenever they need to use it, by manually scanning the labels or tags attached to assets. Check-out can be done on a computer or simply by using a smartphone app.
When the task is completed, workers will check the equipment back in, with just one click.
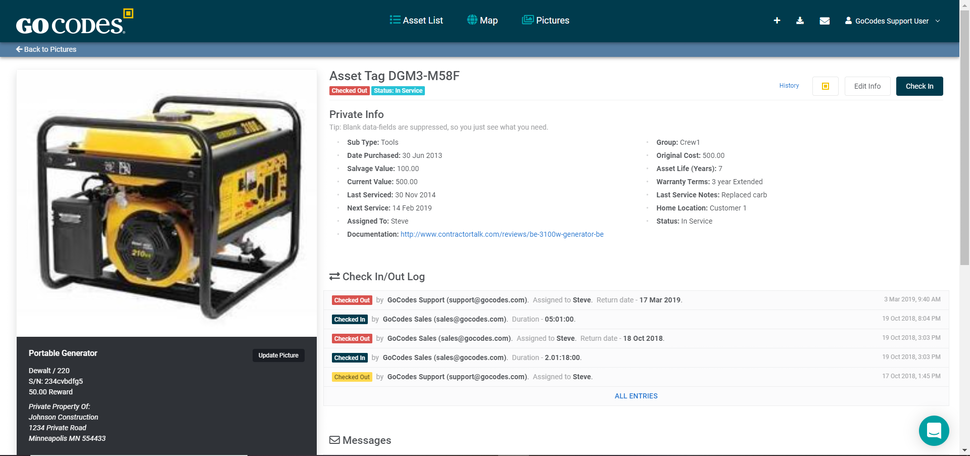
As a result, employees will be held accountable for any misuse or loss of tools and equipment while in their possession, which will motivate more responsible behavior.
Even more, if a worker fails to return an asset on time, the software will automatically send an overdue asset notification.
Establishing this practice also means actively engaging employees in implementing and using asset tracking because each scan contributes to the asset’s records.
Making this approach a part of workers’ daily routine will not only optimize asset utilization but also maintain up-to-date records of each asset’s location and status, making long-term maintenance planning possible.
In essence, an effective asset monitoring solution will allow for better asset visibility, fostering a culture of responsibility among workers and more effective management of construction equipment.
Decreased Risk of Theft
The most apparent advantage of closely monitoring your valuable assets is deterring theft.
Among the leading reasons is that high-value construction equipment, power tools, and building materials are frequently targets to thieves, mainly because they offer a high payout.
Additionally, stolen equipment can cause project delays, creating a ripple effect for construction companies.
Despite work not progressing as intended, labor costs, subcontractor costs, and overhead expenses still accumulate.
Moreover, delayed projects may incur contractual penalties, adding to the financial strain.
Clearly, companies cannot afford to lose track of their assets or fall victim to theft.
Implementing an asset monitoring solution will unquestionably safeguard your valuable equipment.
First of all, by discouraging opportunistic thieves—even within your company—who may grasp that the construction company’s assets are being monitored.
The solution provided by GoCodes Asset Tracking incorporates QR code asset labels and tags that are visibly attached to construction equipment and tools.
When an asset is scanned using GoCodes Asset Tracking’ built-in scanner, the app records and updates its location.
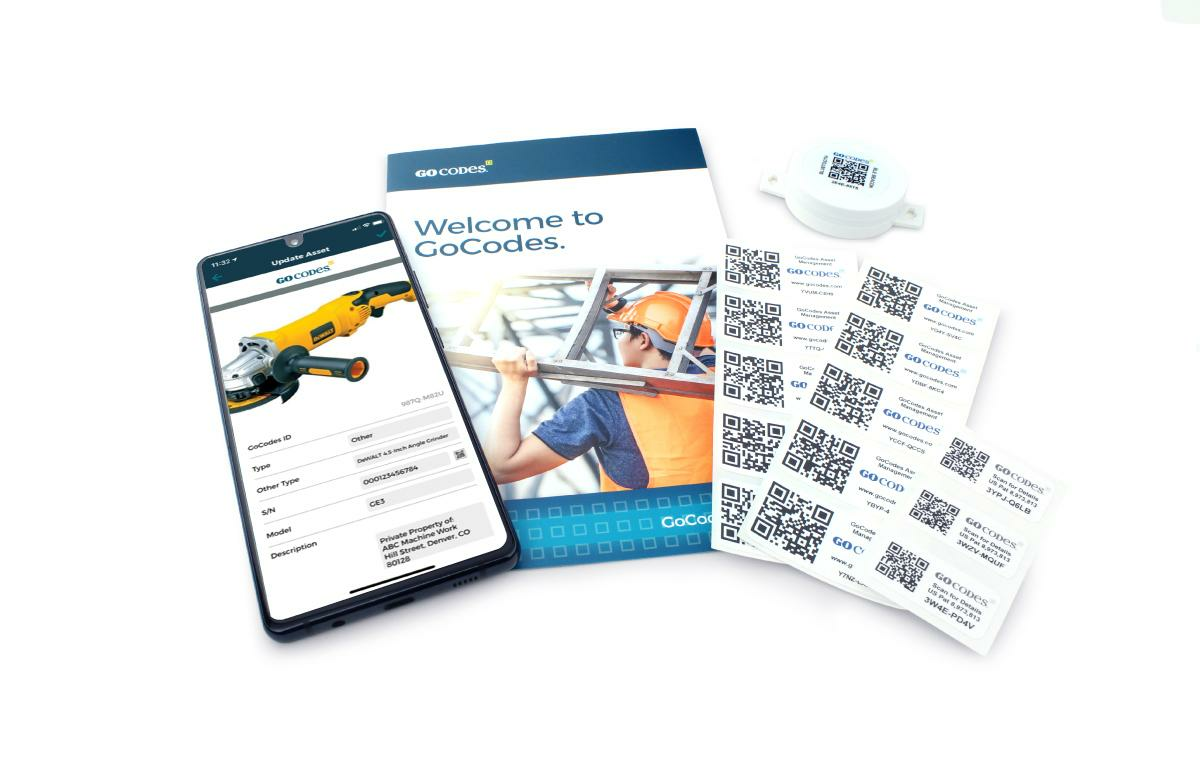
In case of theft, having the last known location of the asset proves quite helpful in its recovery.
Furthermore, the attached label or tag stores all vital information about an asset, including whose property it is. So, when the asset is found and retrieved, GoCodes Asset Tracking’ labels and tags serve as proof of ownership.
To enhance asset tracking, GoCodes Asset Tracking also offers Bluetooth beacons. If an asset is removed from within a given range, the beacon will immediately send out an alert.
This feature’s primary function is to help prevent theft.
Overall, real-time monitoring not only gives companies peace of mind, knowing where their assets are and if they are secure, but it also increases theft prevention, reduces losses, and improves response times to asset theft.
Informed Decision-Making
Access to real-time accurate information is crucial for effective asset monitoring and overall business success.
Luckily, modern asset monitoring solutions collect and store asset data within a single centralized cloud-based system.
This provides construction executives and managers easy access to information about each asset in their ownership, allowing seamless tracking of assets throughout their entire lifecycle.
Having the big picture right in front of you will undeniably help you analyze equipment performance and strategically manage your company’s assets—whether deciding when to buy new assets or repair and upgrade the existing ones.
In other words, this comprehensive monitoring system provides valuable insights into specific trends and patterns, giving you the power to make informed, data-driven decisions to plan and deploy the company’s assets optimally.
Moreover, based on the data stored within your central database, the integrated software analytics tool will enable you to generate detailed custom reports at the click of a button.
The bottom line is that asset monitoring will not only allow you to be in the know about your assets’ whereabouts, but it will also strengthen your decision-making capabilities on how to best invest in resources and respond to challenges.
Maintained Regulatory Compliance
Construction businesses operate in a highly regulated sector.
Companies must efficiently collect and submit data to meet their regulatory obligations and avoid legal implications, as strict construction regulations come with severe penalties.
It’s crucial for businesses to proactively adhere to legal standards to ensure compliance and steer clear of legal complications.
Employing advanced asset monitoring software simplifies your reporting responsibilities significantly, especially for things like equipment calibration, testing, and maintenance.
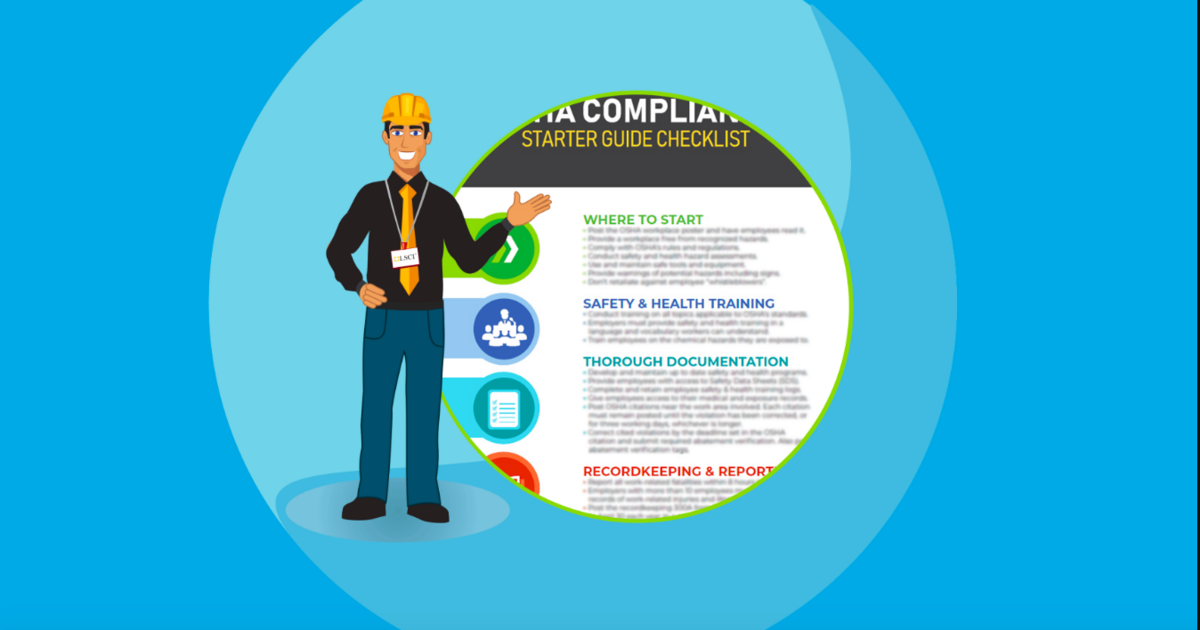
For example, generating detailed compliance reports will take considerably less time than when the same data were collected manually, which would take months to complete.
That is to say, an asset monitoring solution not only allows you to facilitate efficient tracking of your physical assets but also ensures keeping precise records and seamless compliance with construction regulations.
At last, utilizing asset monitoring technology lets your company streamline compliance processes, reduce risks, and avoid expensive fines and penalties.
Conclusion
Digital technologies change the way we do business. They come with great perks only if we know how to recognize their value and embrace what they have to offer.
An asset monitoring solution is one of those technologies that keep migraines away from construction executives.
Such solutions resolve all setbacks in tracking your assets, optimizing their usage, and extending their lifespan to better serve your business needs.
They also enhance employee accountability, deter theft, and provide comprehensive data and analytics for informed decision-making and future planning.
In the pursuit of running a successful construction business, asset monitoring solutions are increasingly becoming indispensable.