Keeping track of materials in construction can be challenging, especially when you work on multiple sites simultaneously.
You need to ensure that the right materials are at the right site on time, that you have enough materials in stock, and that you use them as planned.
If not, you risk delays, extra costs, and disappointed clients.
If this sounds familiar, it’s time to consider material tracking software.
Today, we will review our top 10 tools for tracking materials in your warehouse, on construction sites, or even in transit from suppliers.
We are confident that at least one of these ten software options will meet all your material tracking needs.
In this article...
GoCodes Asset Tracking
We’re starting with our very own tracking software—GoCodes Asset Tracking.
Our tool combines cloud technology, a mobile scanning app, and rugged QR code tags to keep track of your entire asset inventory, not just materials.
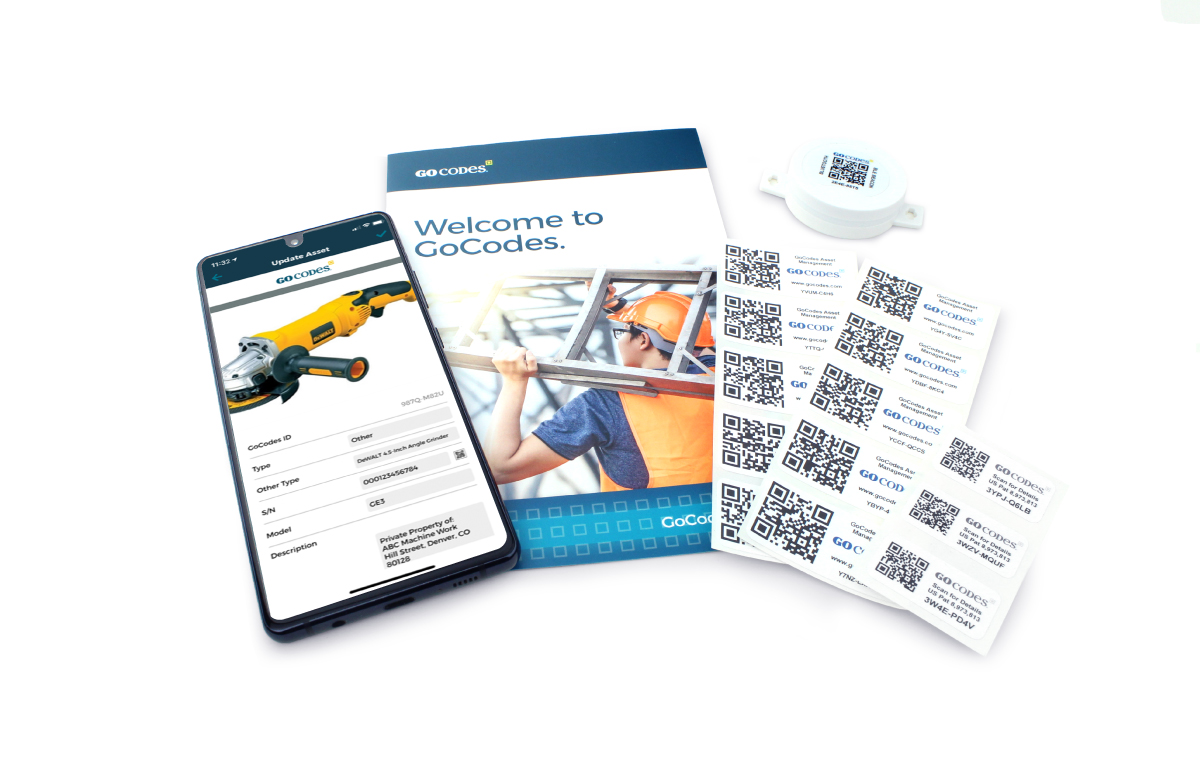
This system is perfect for companies that want to improve ownership and accountability, as it specializes in checking in and out equipment and materials, providing a clear chain of custody.
And that’s precisely what you need for better material management.
Here’s how it works.
For starters, you can attach our unique QR codes to your materials and equipment.
With a quick scan using any smartphone, you access real-time information like location, quantity, and last update, ensuring you always know where your materials are, their quantity, and their status.
Our check-in and check-out feature lets workers scan labels and check out materials and supplies. The system records every use or return of an item, including who handled it, when, and where.
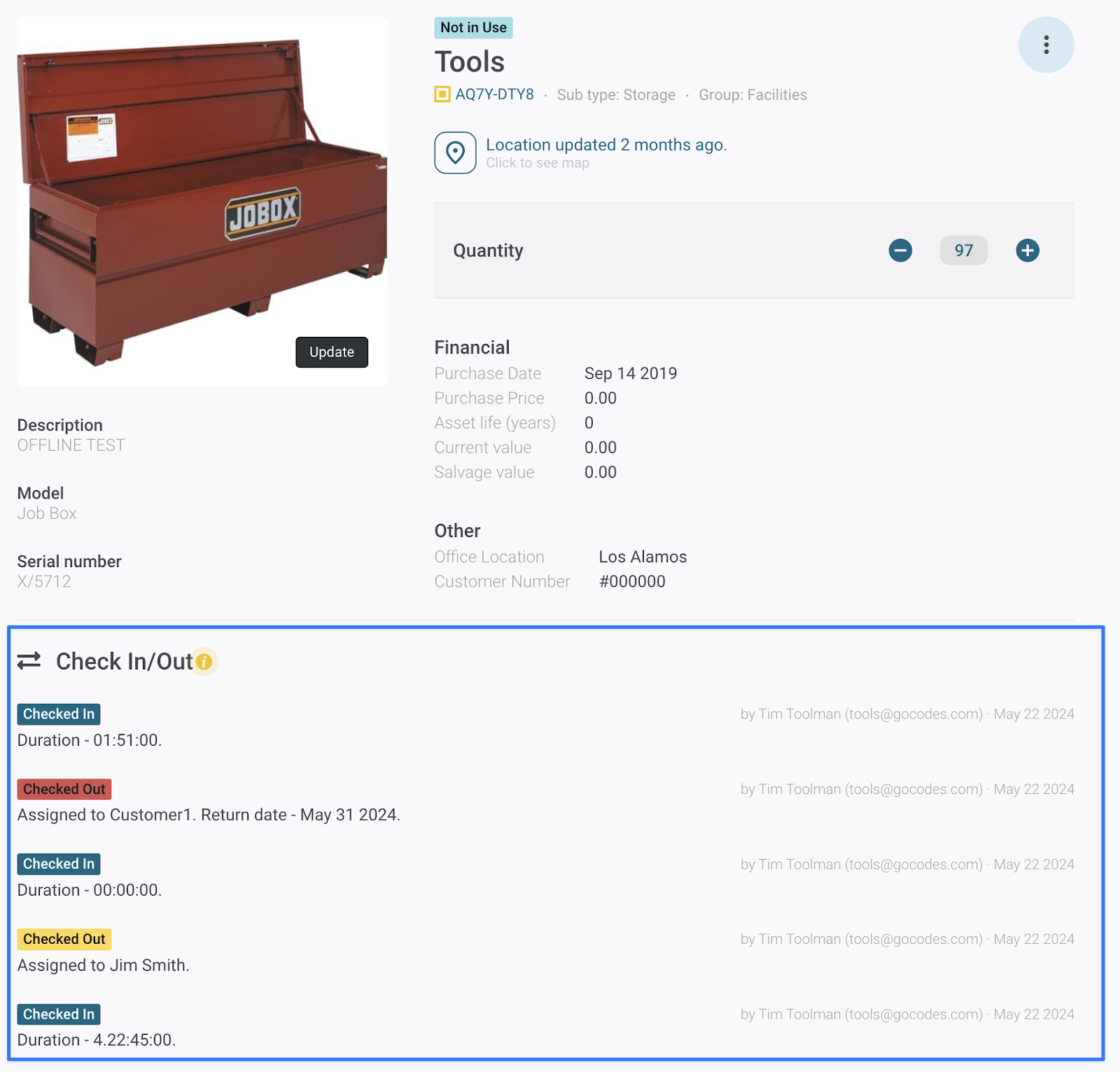
This boosts accountability, as you can easily track who is using which assets and materials.
With all this data in the system, you can quickly see when materials and supplies are running low and replenish stock as needed.
Even if you don’t notice it yourself, GoCodes Asset Tracking will help you stay ahead of inventory shortages.
You can set up a minimum quantity and enable automatic alerts via email or text that notify you when stock levels are low, so you can reorder items on time and avoid project delays.
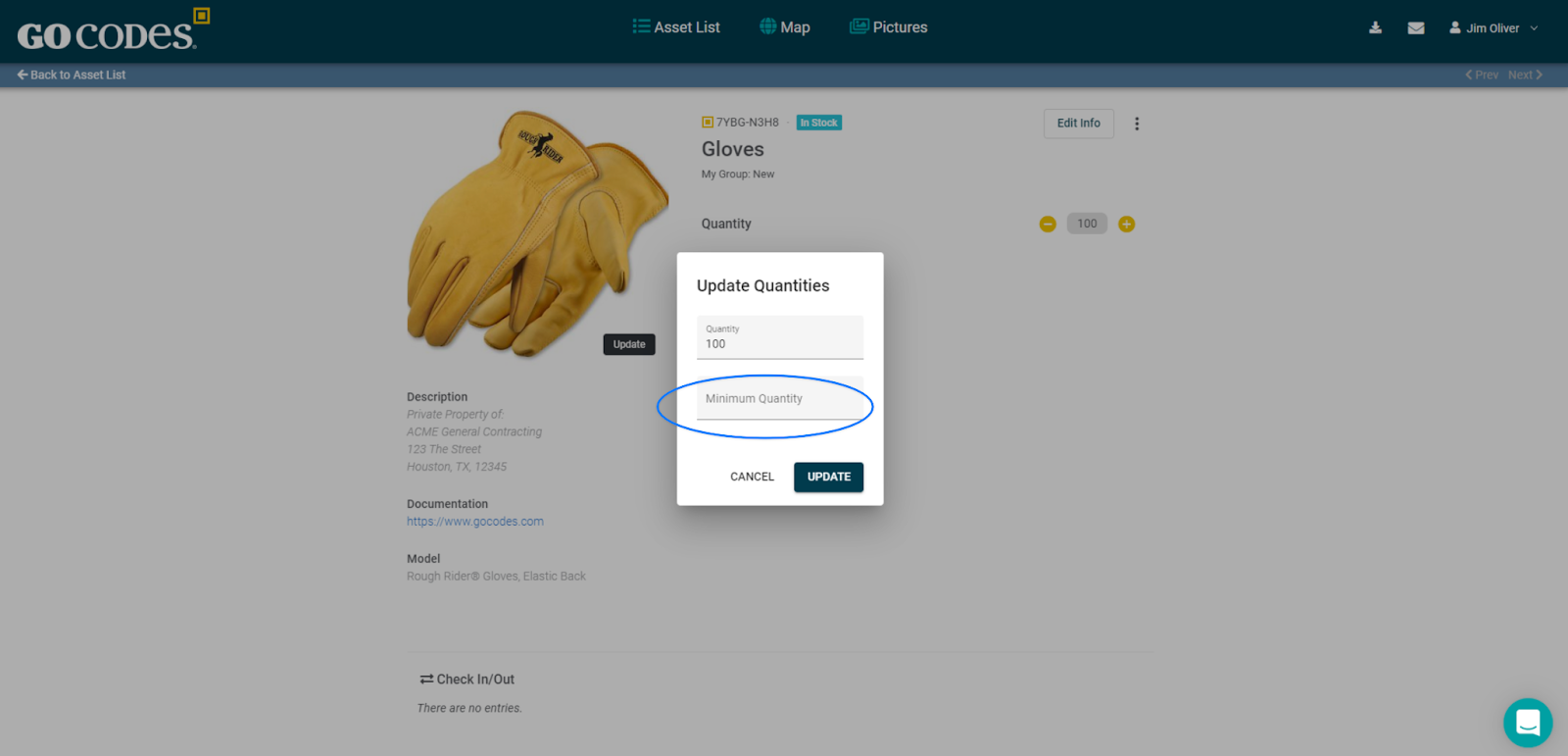
And when materials are heading to a construction site, you can tag them (or vehicles) with GPS tracking devices.
This allows you to track their journey from your storage facility to the site, ensuring you always know where your materials are and helping prevent theft.
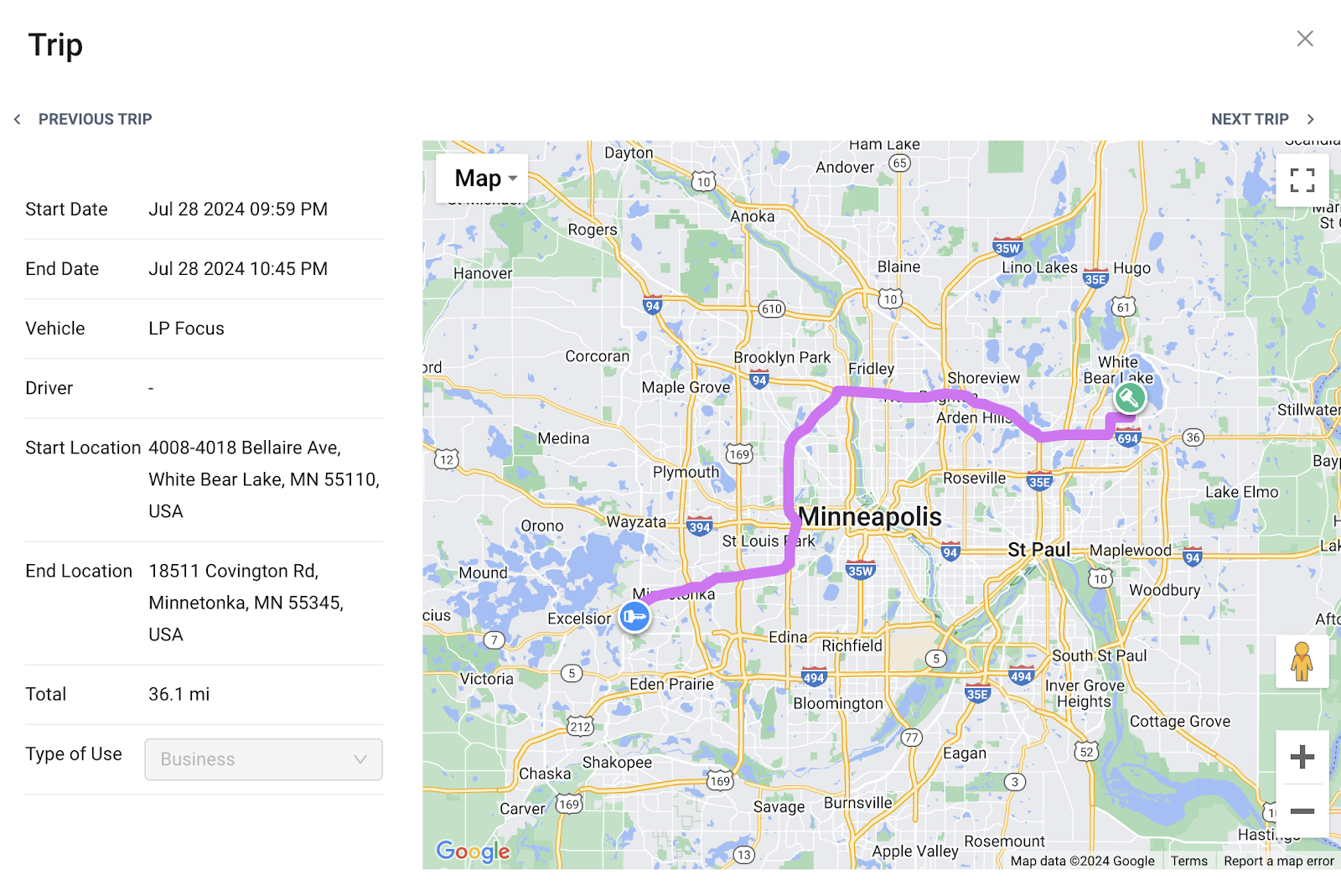
Speaking of theft, GoCodes Asset Tracking also lets you set up a geofence around your storage area.
If materials move outside this boundary, you’ll receive an immediate alert so you can take action right away.
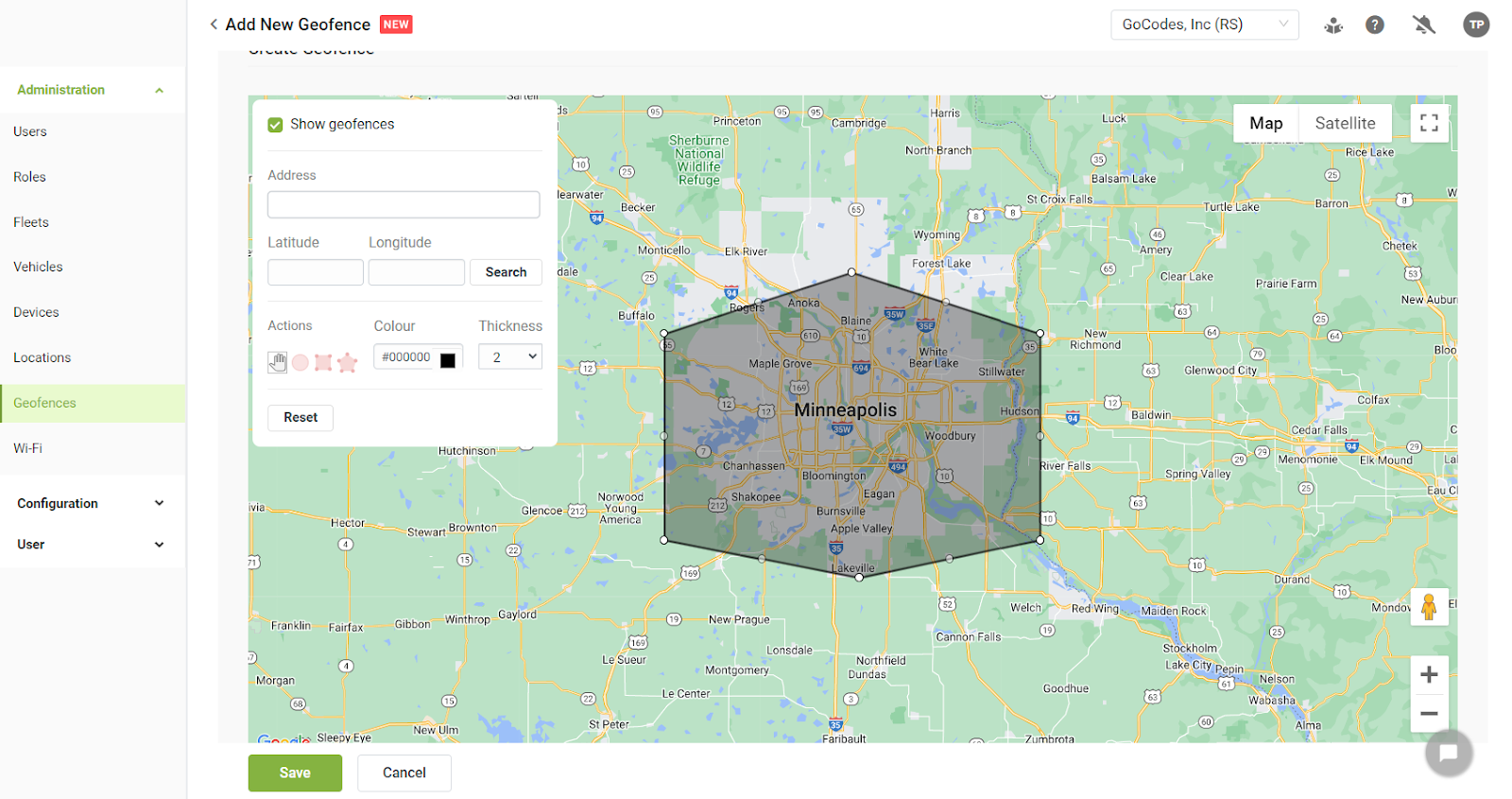
With all these features, GoCodes Asset Tracking is built to make material tracking straightforward and effective.
Pricing starts at just $500 per year for 200 assets and three user logins.
Plus, we offer a 15-day free trial, so try it today and experience how easy tracking your materials (and other assets!) can be with GoCodes Asset Tracking.
Matrak
Matrak connects construction teams through the supply chain, from manufacturing to on-site installation.
Built for Builders, Suppliers, and Installers, this software helps track project progress in three ways:
- Builders can visually see job progress through material usage and manage schedules.
- Suppliers can track materials delivered to the site and plan upcoming shipments.
- Installers can update quality checks and share real-time progress with colleagues.
When it comes to material tracking, Matrak lets you upload your building drawings, make them interactive, and generate bills of materials directly from them.
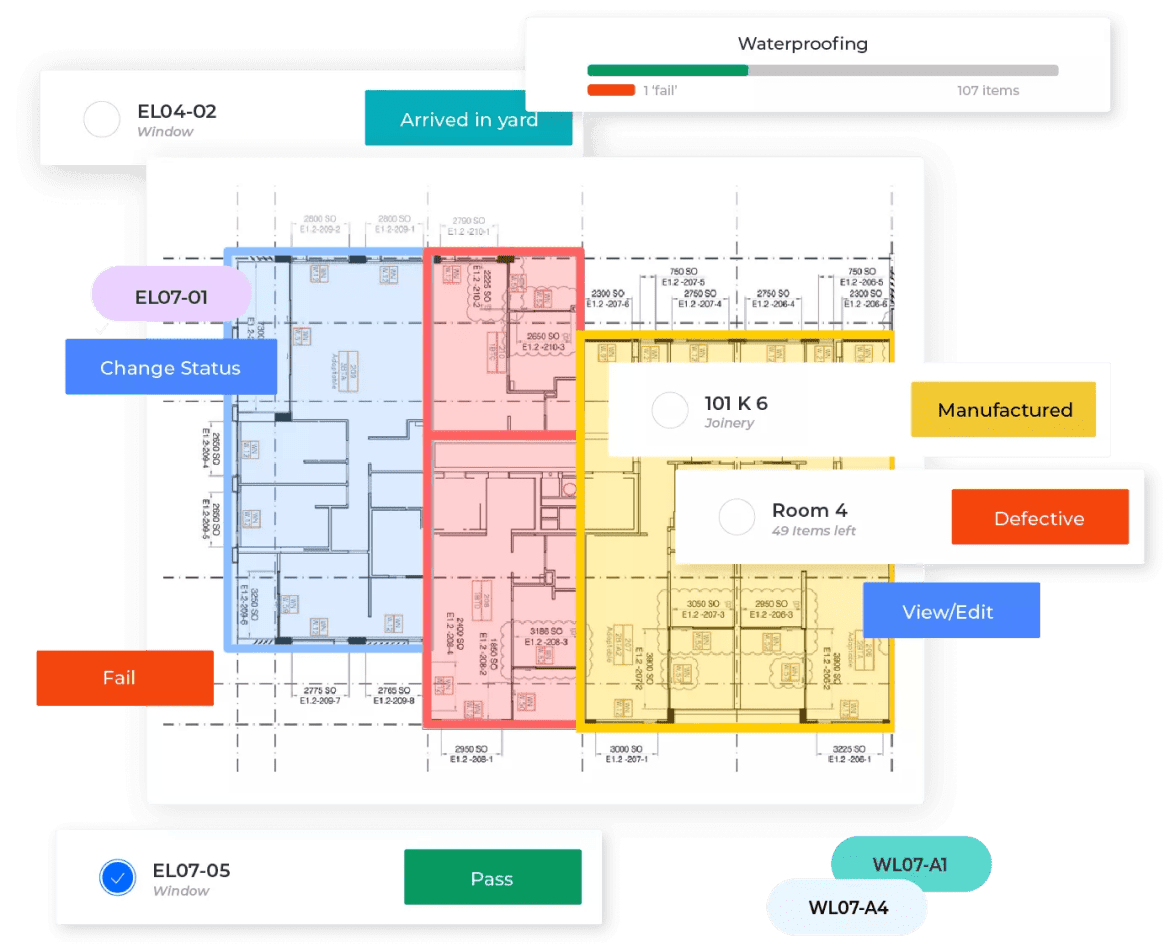
You can also assign QA inspection tasks to materials to ensure they meet standards before use, as well as track material installation and pending tasks.
Matrak provides date- and time-stamped activity logs to show every action made to materials to improve efficiencies and help resolve disputes.
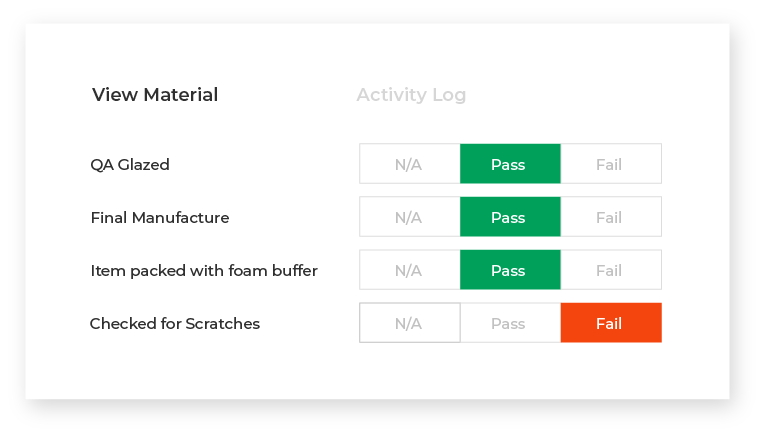
With mobile compatibility, you can manage all this on the go.
Furthermore, these features combined make it easy to track project progress and save lots of time, as one satisfied user confirms:
“I no longer have to spend hours walking the site to calculate what has or hasn’t been installed. My staff can update their work at the end of each day onto Matrak. This saves me so much time! This is also seen by the client, this saves him time also. No longer is there a dispute in our monthly progress claims as the proof of works is on Matrak!”
Similar to GoCodes Asset Tracking, Matrak uses QR codes to track materials.
However, Matrak’s approach is tailored more for manufacturing users.
They can print unique QR codes for individual materials or containers and update the status of these items by scanning the QR code.
Matrak’s pricing starts at $745 per month for tracking up to 4,000 items, with a free trial available to experience its benefits.
Sortly
Next on our list is Sortly, a material tracking app with folder-based item organization.
As its name suggests, you can sort your parts and materials by location, item type, status, and more, and grant access to the right team members.
This way, you always know exactly what’s at each job site, factory, or storage site before work begins.
Sortly lets you bulk upload your current inventory spreadsheet and provides a visual, detail-rich look at every item your business owns.
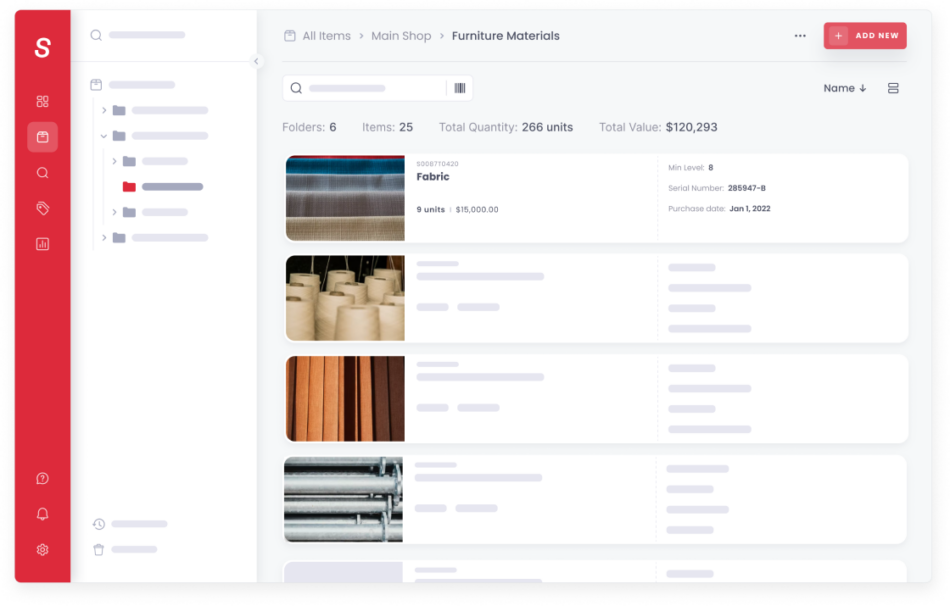
You can print and attach custom QR code labels to inventory, then use the built-in scanner to track materials.
Sortly also allows setting quantity minimums and reordering alerts.
While similar to our tool in these features, Sortly lacks some more robust capabilities than GoCodes Asset Tracking, like real-time location tracking and lifecycle management.
For example, you can’t assign a task to an item like you can in GoCodes Asset Tracking, track materials as they travel to the site in real time, or assign an employee to order materials.
But you can, for instance, quickly create purchase orders right from your inventory data, and include photos, costs, names, and quantities, though this is limited to higher pricing plans.
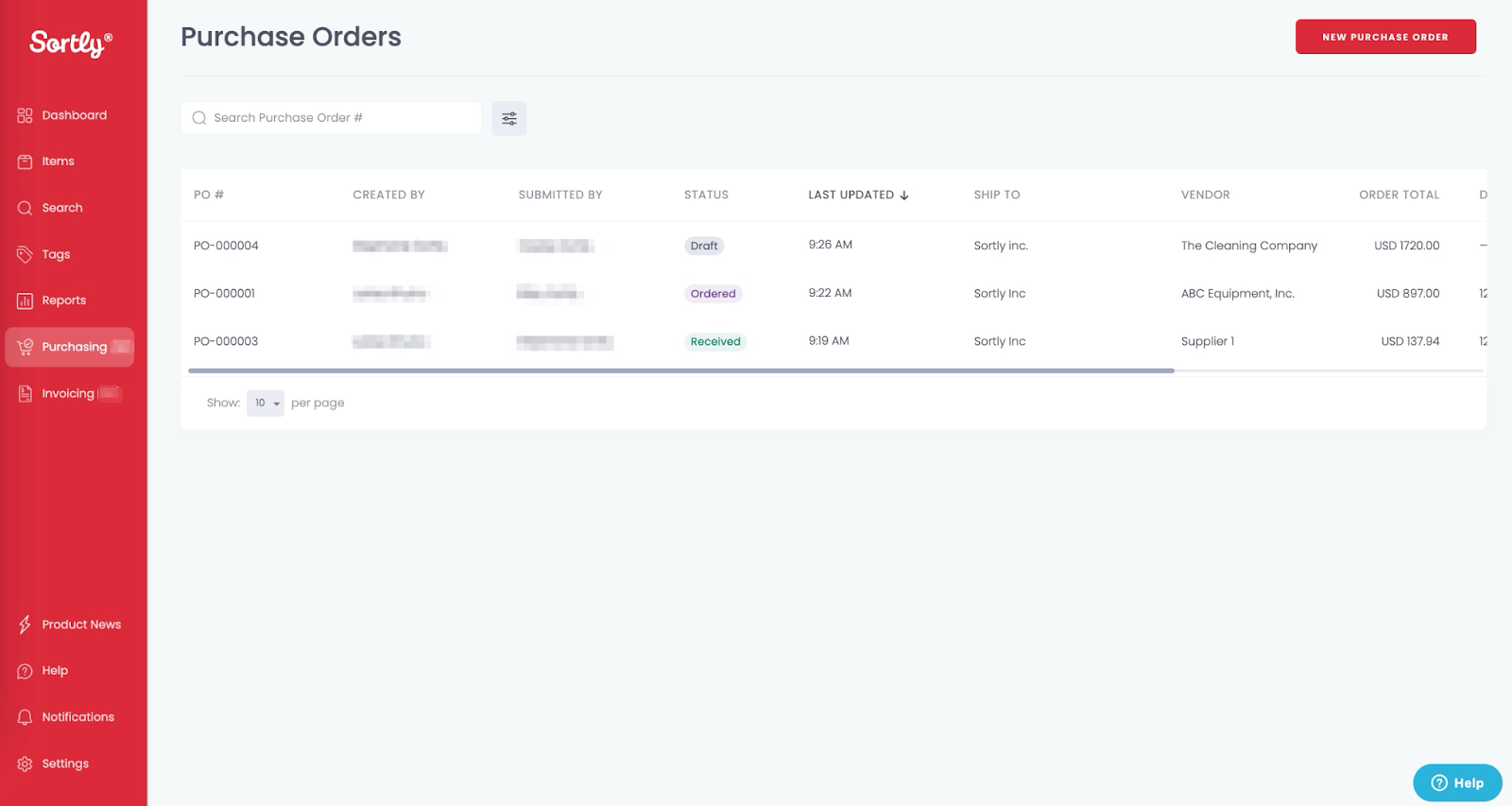
According to clients, Sortly’s reporting capabilities are decent but not perfect—specifically, you cannot retrospectively view inventory from a specific date, which complicates monthly COGS adjustments if reports aren’t pulled on time.
Sortly comes in a free version that tracks 100 items with one user and one custom field.
The $24/month plan covers 2,000 items, two users, and ten custom fields, while the $74/month Ultra plan includes 10,000 items, five users, and 25 custom fields.
For tracking more than 10,000 items, you need a custom quote.
Users find the pricing options too steep between tiers and would prefer a more flexible, cost-effective option.
Despite this, Sortly is ideal for businesses needing a simple, visual inventory management system.
Track’em
This cloud-based software is built specifically for large construction, mining, oil and gas projects.
It’s tailored for enterprises with 250+ employees, often handling projects with over a million tracked items and thousands of workers.
Track’em tracks materials from fabrication through installation and maintenance, managing inventory and shipments at every stage in the supply chain.
It will help you locate your materials and parts wherever they are.
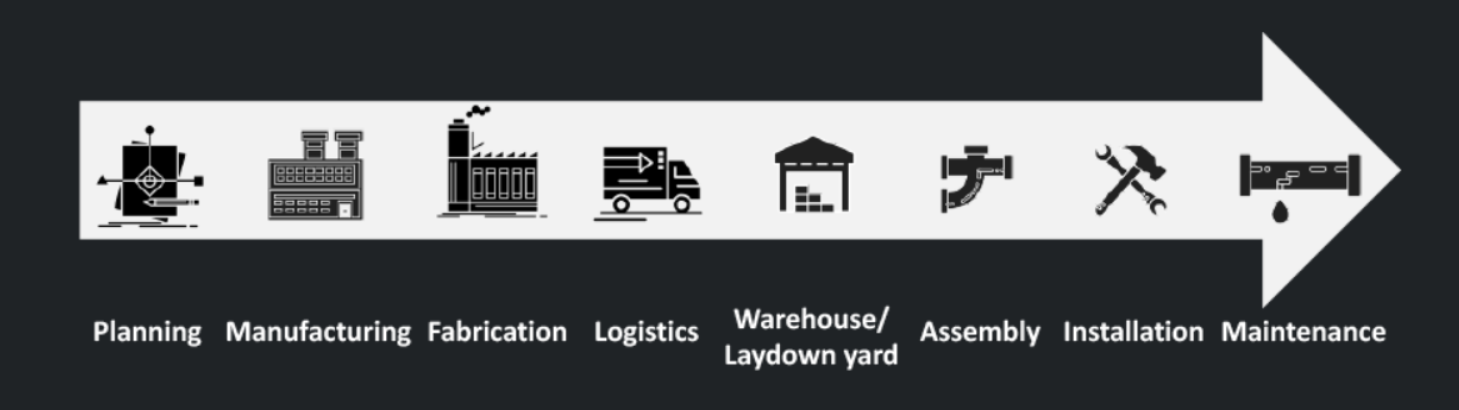
The tool logs every interaction, providing a complete history and audit trail.
It integrates with various tracking technologies like GPS, barcodes, RFID, and Bluetooth, or works with your existing systems.
Track’em also offers geofencing and heatmaps for high-traffic areas.
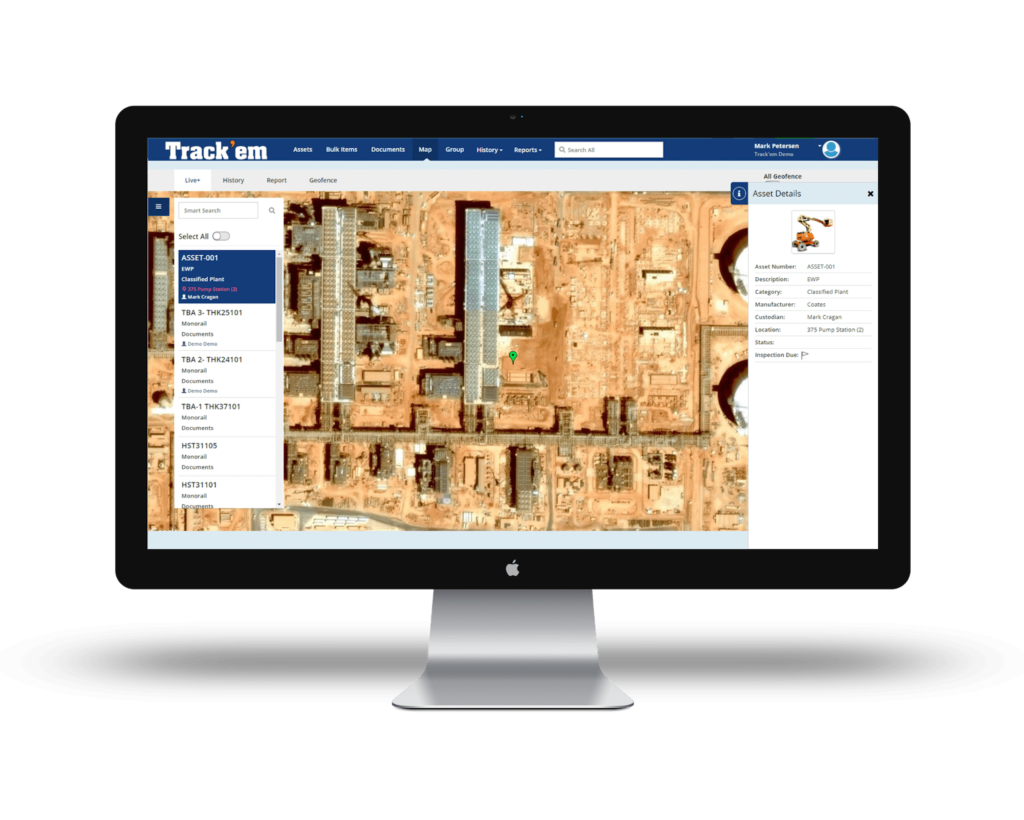
Other features include:
- QR codes for item identification and updates
- Handling material transfer requests and pick lists
- Route plotting, distance tracking, and maintenance management
- Triggers and alerts for inventory levels, progress deviations, and upcoming inspections
Unique to Track’em are its OSD (Over, Short, Damaged) material reports.
You can scan or add parts, select the OSD report type, add photos and comments, assign the report to someone responsible, and track its status until resolved.
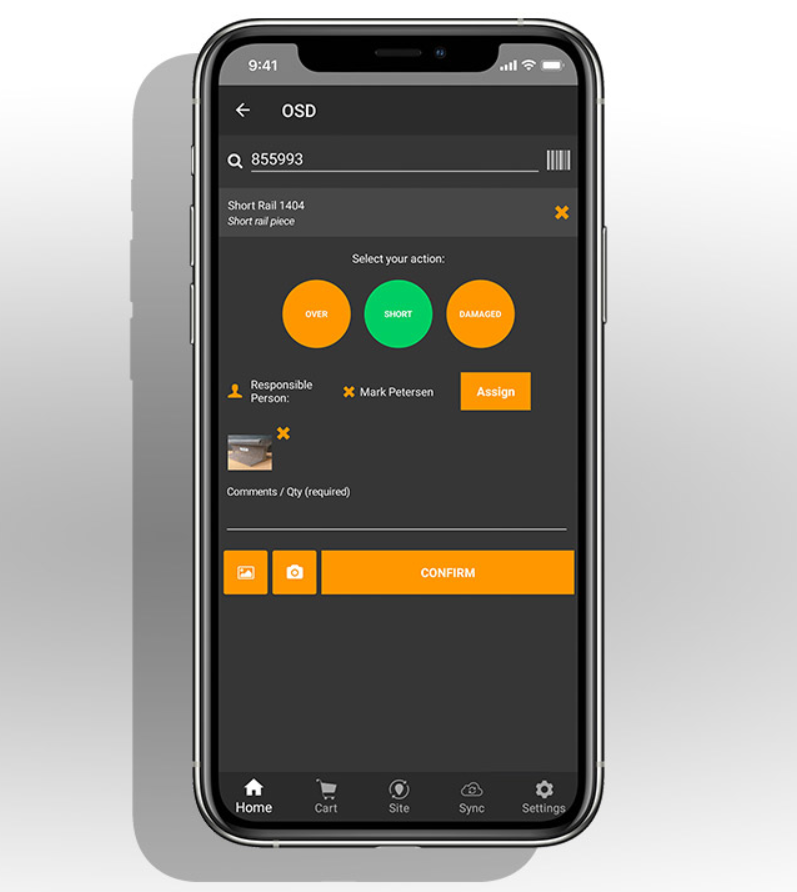
This streamlines material management by a lot.
This tool also integrates with BIM, giving you real-time visibility on progress and letting you check where parts and materials are in the supply chain.
How this integration looks like in practice, check in the video below:
Pricing information is not publicly available.
For more details about this comprehensive software or to request a demo, contact Track’em directly.
Raken
Raken is a construction management tool focused on time and production tracking, with material tracking as one of its key features.
It allows you to create tasks for employees and schedule automated reports to monitor completion.
With the mobile app, field crews can log daily work details, including materials used, and upload time-stamped photos, videos, and notes.
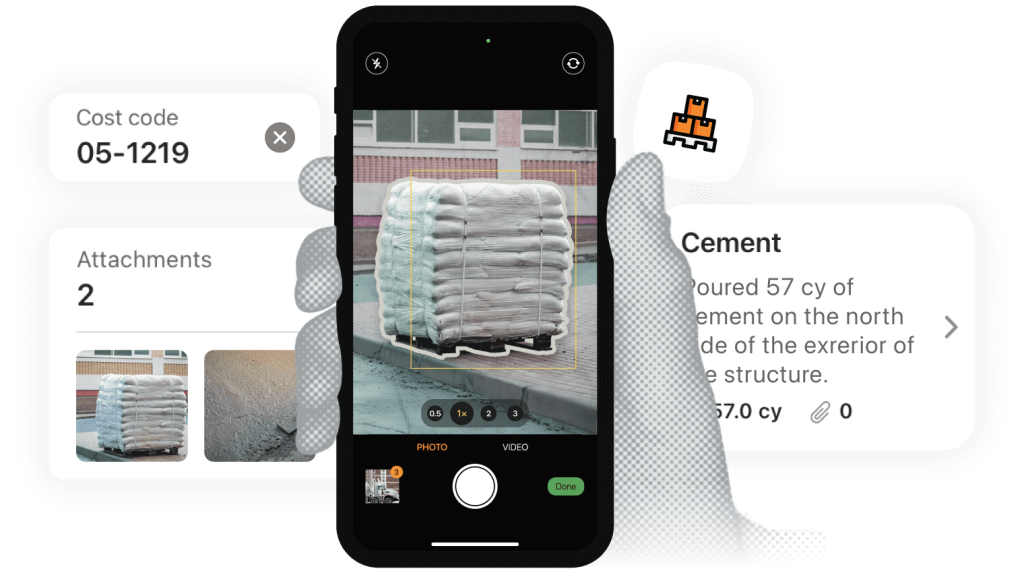
This data is automatically synced to the system, enabling real-time productivity monitoring.
The management can easily compare time and material usage against estimates using real-time charts and graphs, and generate shareable PDF reports.
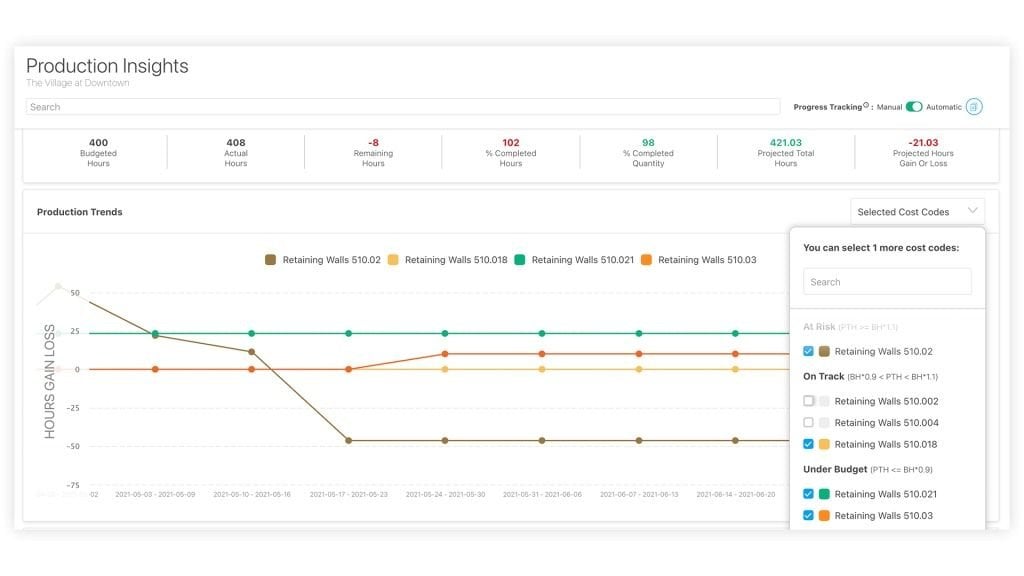
This automated material use tracking and comparison against cost estimates makes it more specific than other tools on this list.
However, while Raken excels in this aspect, it doesn’t offer material location tracking through labels or GPS.
Additionally, while you can assign tasks to workers, you cannot assign tasks to specific assets, as you can in GoCodes Asset Tracking, for instance.
All in all, users appreciate Raken for its simplicity and ease of use.
Barbara Tavares, Senior Construction Manager at RHSI Engineering, notes that even her less tech-savvy colleagues quickly adapted to the tool.
“The first person to use Raken was Wayne, who’s in his late 60s. He was a little nervous to use an app and an iPad. But he quickly got the hang of it, and he loves it. Now, with some of our new inspectors, it takes them 5 whole minutes to get it.”
Raken does not disclose pricing publicly but offers personalized demos.
This tool is ideal for those seeking an easy way to track material use against estimates and make quick adjustments.
MHS by LogiNets
LogiNets, a Finnish software company, develops digital solutions for construction, heavy industry, and field services.
One of their solutions is the Material Handling System (MHS).
It was developed to address key issues in tracking materials for capital-intensive construction projects and comes with five modules:
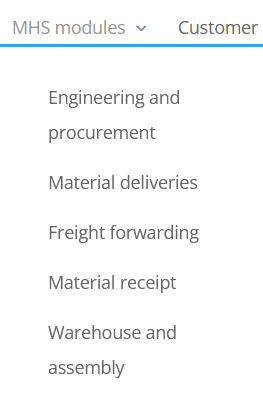
With these five modules, companies can manage materials throughout the entire supply chain, from ordering to site installation, making it similar to Matrak and Track’em.
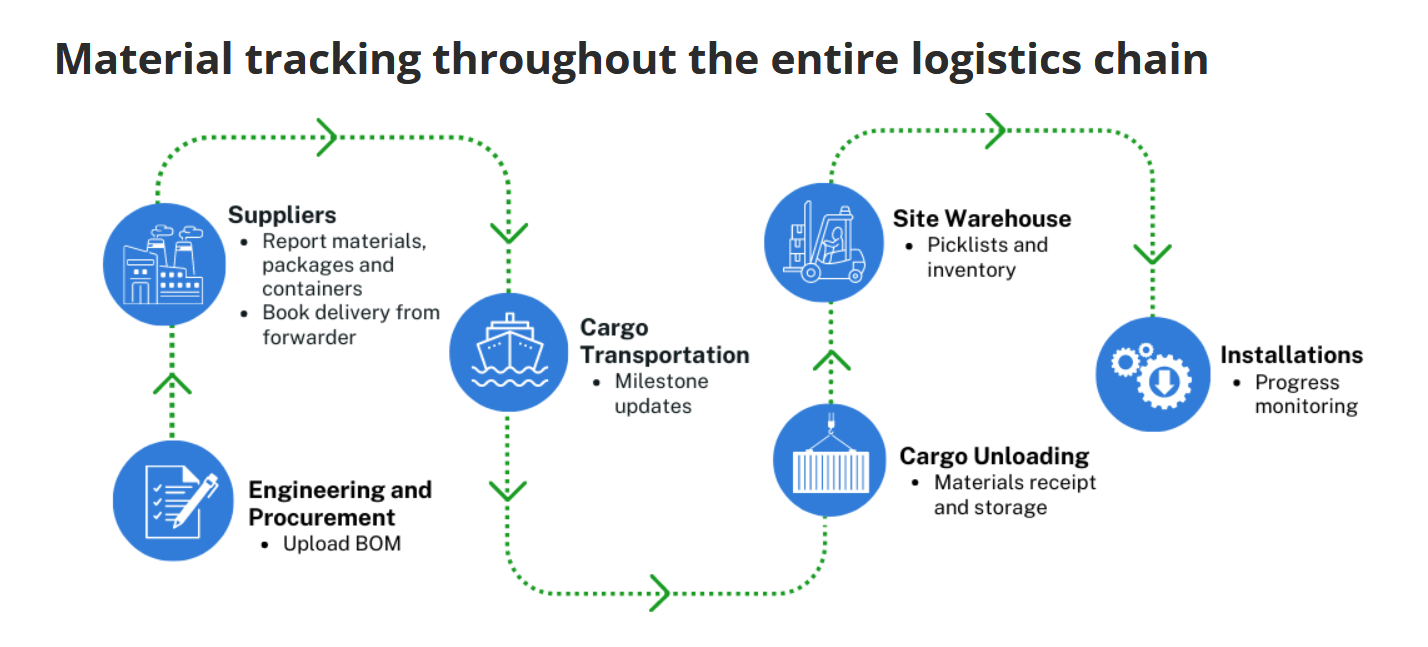
In essence, LogiNets’ material handling system can be your single database for all material deliveries within the project.
Material suppliers enter precise delivery details into MHS and attach packing lists, package stickers, and container specifications with QR codes.
The master search module then allows you to search and filter results using various attributes such as product, purchase order, package, and container numbers.
You can see which package, container, and shipment a position has been allocated to.
Finally, when unloading deliveries in your warehouse or site, you scan QR codes using a phone for easy item identification.
Overall, this tracking system gives you visibility into containers, packages, and goods arriving at the project site and helps manage material flows with accurate, real-time information.
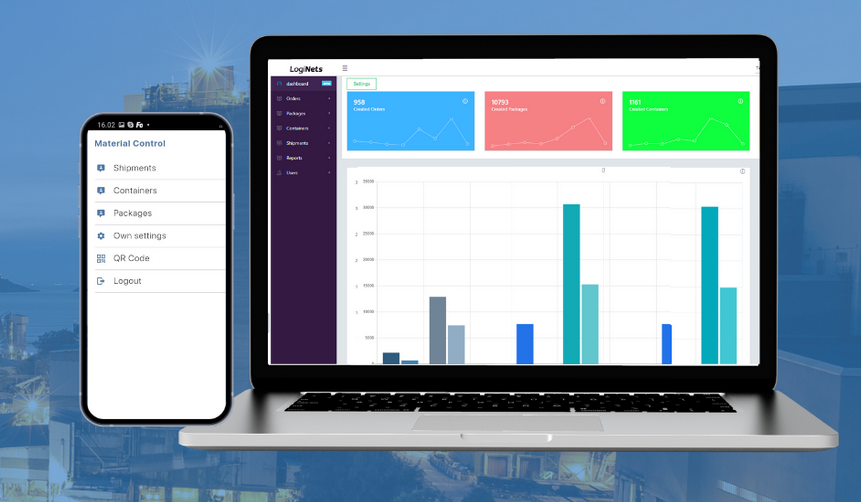
Pricing depends on the modules you choose.
If this sounds like a tool that can help you, contact LogiNets to schedule a demo, discuss module options, and get pricing details.
HeavyJob
HeavyJob is part of the Heavy Construction Systems Specialists LLC (HCSS) suite, which offers a comprehensive range of tools from pre-construction to fleet tracking.
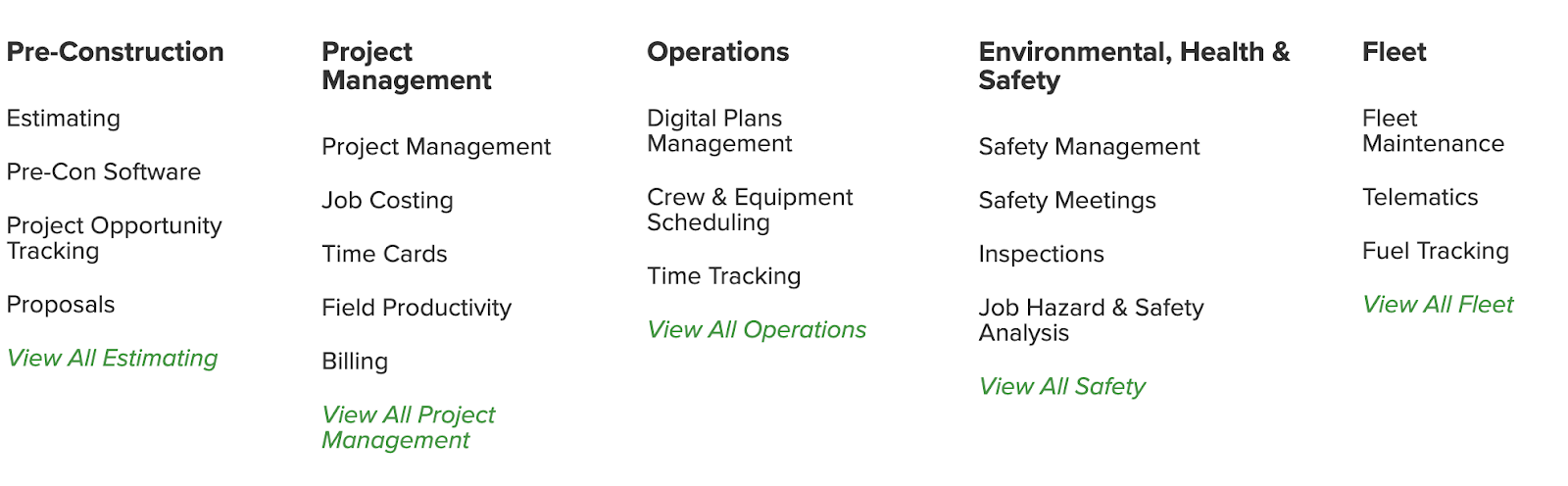
This tool lets you quickly enter quantity data (labor hours and materials used in a day on the site) using the mobile time card feature, and consolidate all crew data in one place.
It also helps track material usage and costs in relation to previous estimates and performs daily cost analyses to monitor budget adherence, similar to Raken.
In fact, the field management crew can use an iPad or tablet on-site to record installed materials and link this data to the financial snapshot in the Job Analysis feature.
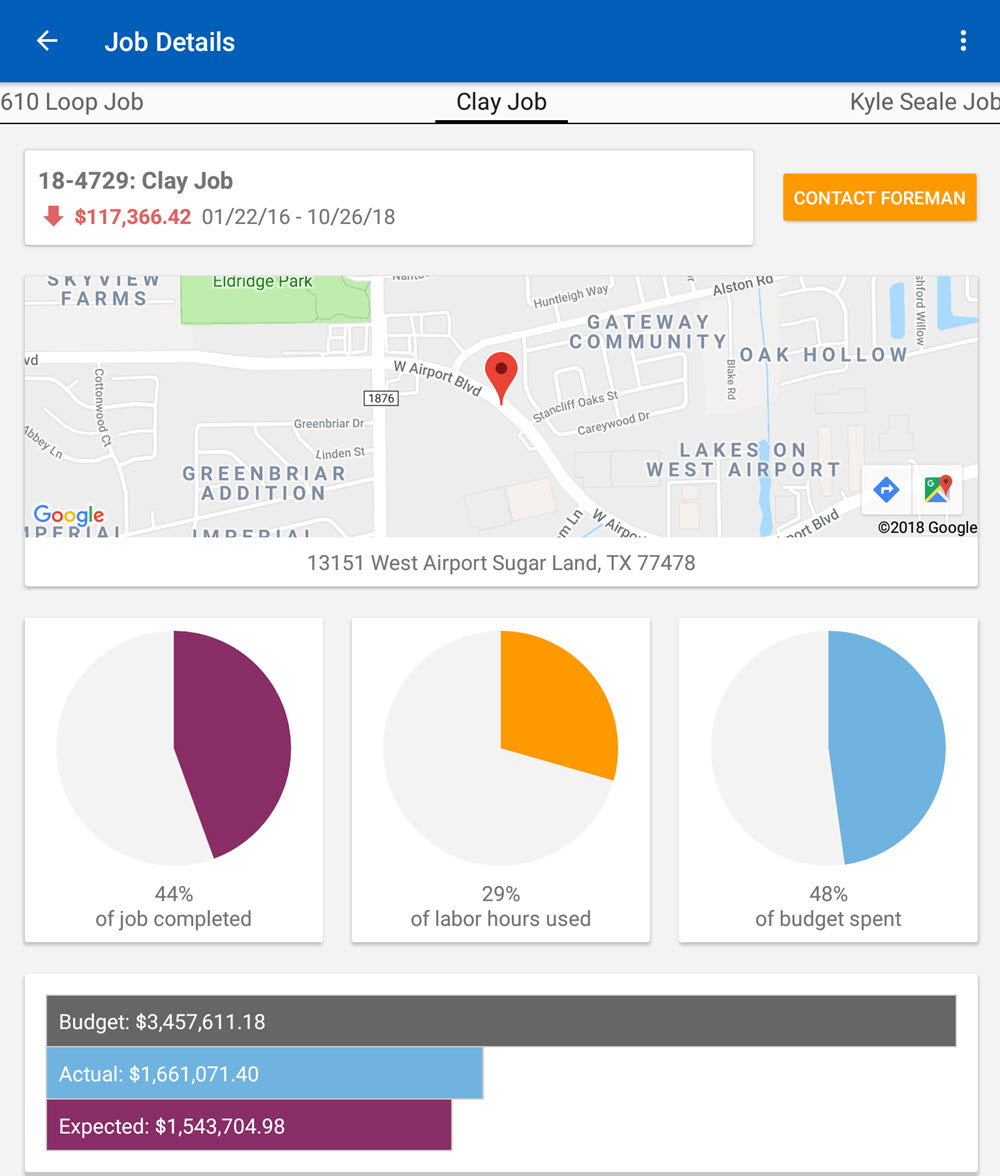
They can also add photos or notes, such as delays due to weather, so you can keep all progress information in one place.
And, as the tool tracks daily job progress, such as how many materials have been installed, it makes it easier to plan for the next day’s tasks.
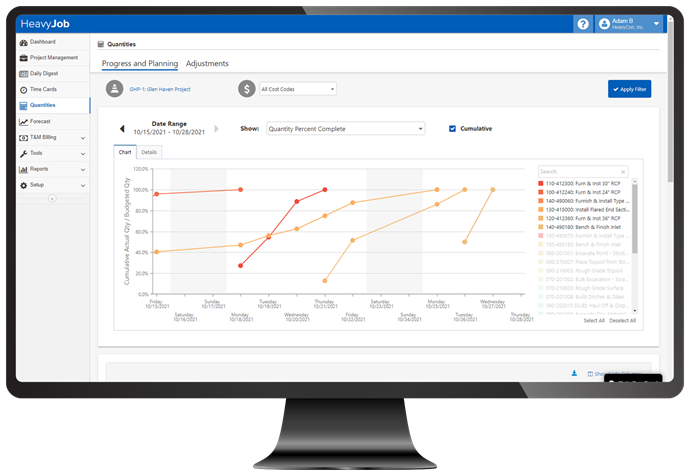
In this regard, HeavyJob is similar to Matrak.
Users often praise HeavyJob for its excellent customer service, though some mention the high cost.
Despite this, the extensive features may justify the expense.
For pricing, you can fill out a short questionnaire on their website. A free demo is also available.
Detrack
Detrack can help you deliver materials and supplies more efficiently, as it tracks shipments, optimizes delivery routes, and provides proof of delivery.
However, this tool doesn’t track materials around the site like GoCodes Asset Tracking.
Instead, it focuses on tracking materials before they reach the construction site.
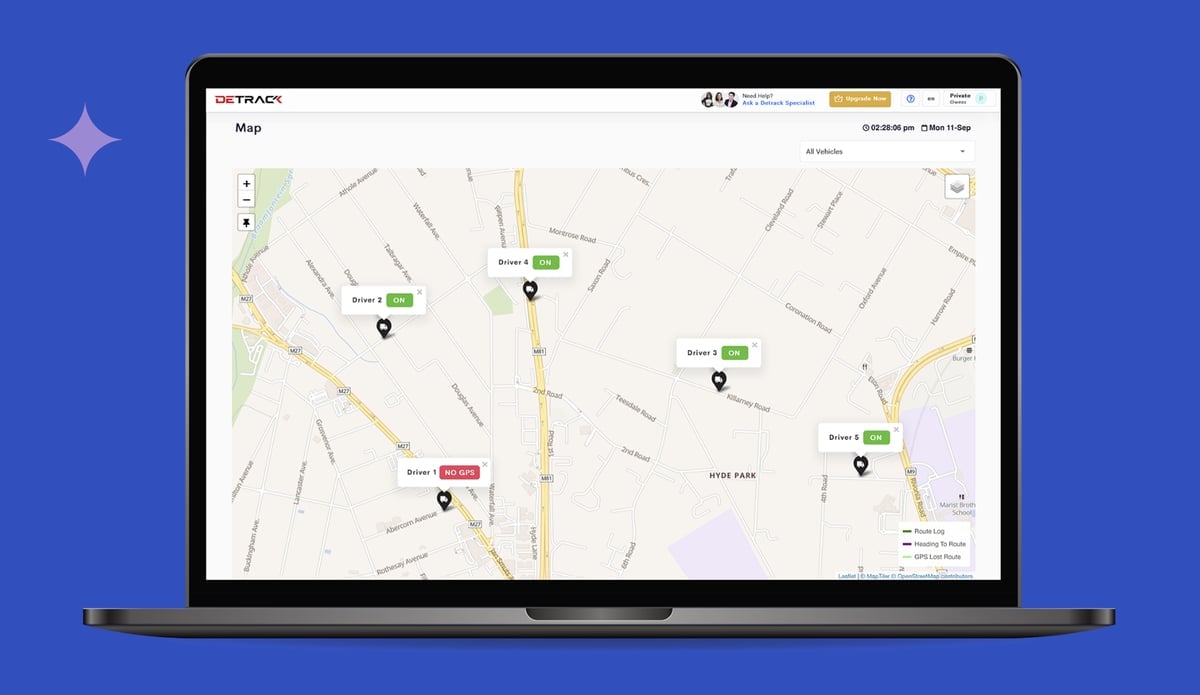
This has its benefits, too.
Detrack’s user-friendly mobile app, compatible with both Android and iOS, offers real-time material tracking data access from anywhere.
It integrates with inventory management software and includes features such as:
- Delivery progress tracking
- Delivery route optimization
- Automated communication within the app
- Real-time GPS monitoring of materials in transit
For example, you can quickly notify your construction team if delivery will be late, allowing them to adjust their tasks accordingly.
On the other hand, drivers can capture images of delivered materials at project sites, providing concrete evidence of delivery and material condition.
Moreover, the Electronic Proof of Delivery (ePOD) feature allows your construction crew to digitally sign for receipt, creating a verifiable delivery record and increasing accountability.
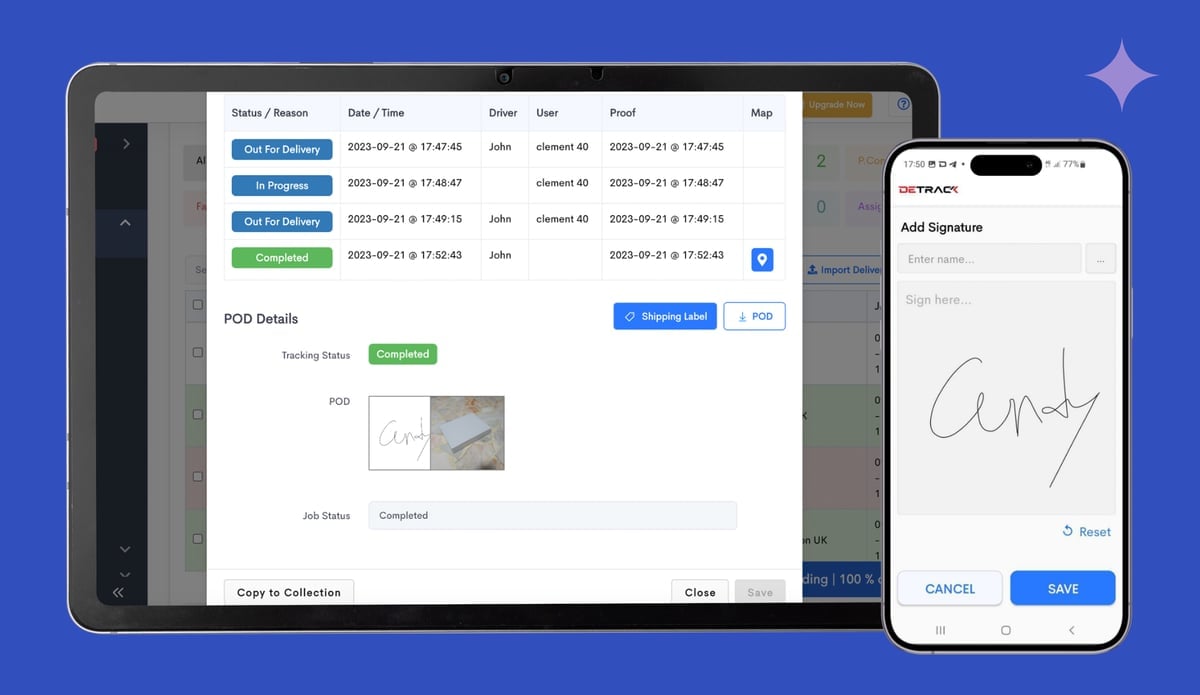
Overall, clients like this tool because it’s easy to use and set up, although some users feel the reporting needs to be more robust and data extraction easier.
Pricing starts at $29 per month for a driver/vehicle.
More plans and features are available on their website, and they offer a free 14-day trial for those interested in trying it out.
CrewTracks
As its name clearly suggests, CrewTracks is software for tracking and managing construction crews.
In simple terms, it works like this:
- The crew leader takes a picture of each person when they arrive on site and leave directly from the app.
- CrewTracks adds a GPS pin to each clock event, recording all working hours in the system.
Watch the video below for a preview of all their features:
If you watched the video, you probably noticed that material tracking is very simple. Also, it is one of their less-used features.
Nonetheless, it proved to be very useful to some of their clients.
Essentially, you can assign a material quantity to a job or an item (like a piece of equipment).
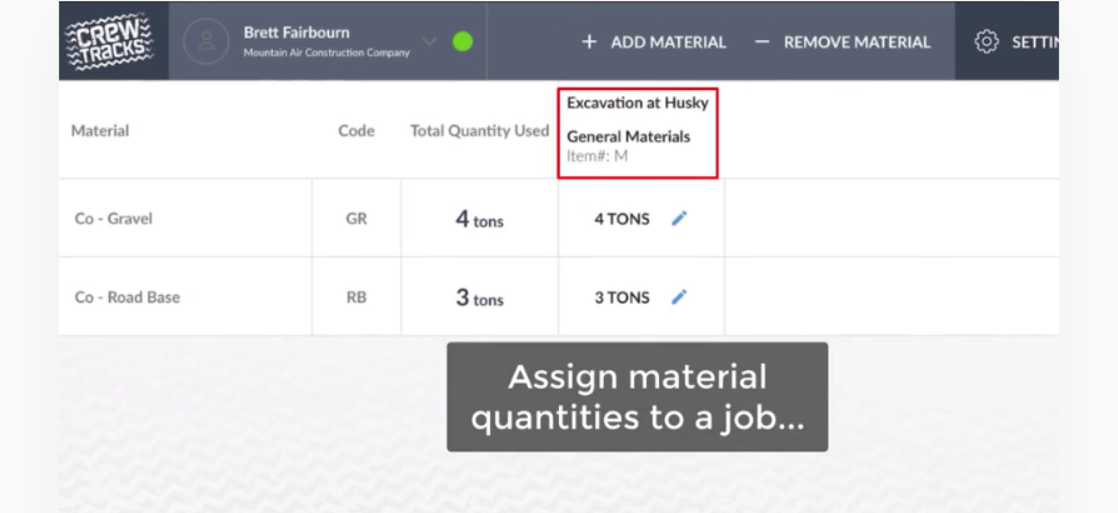
This is primarily meant to track materials consumption, but some customers use it to indicate the materials needed for the next day.
The resulting materials list can be exported as a report, serving as a pick list for loading the truck.
When you think about it, both time and material tracking make this tool similar to HeavyJobs.
Pricing is per person per month, averaging about $20 per employee.
There is also a one-time setup fee ranging from $500 to $1,500, depending on your needs and company size.
For an exact price quote, you should contact them directly or schedule a free demo.
All in all, this tool is a great fit for companies that need both material and crew tracking.
Katana
We are finishing the list with Katana, a cloud inventory platform that offers built-in inventory, production, and reporting features to help you maintain optimal stock levels and avoid stockouts.
Katana provides a complete overview of the locations and movements of your raw material inventory.
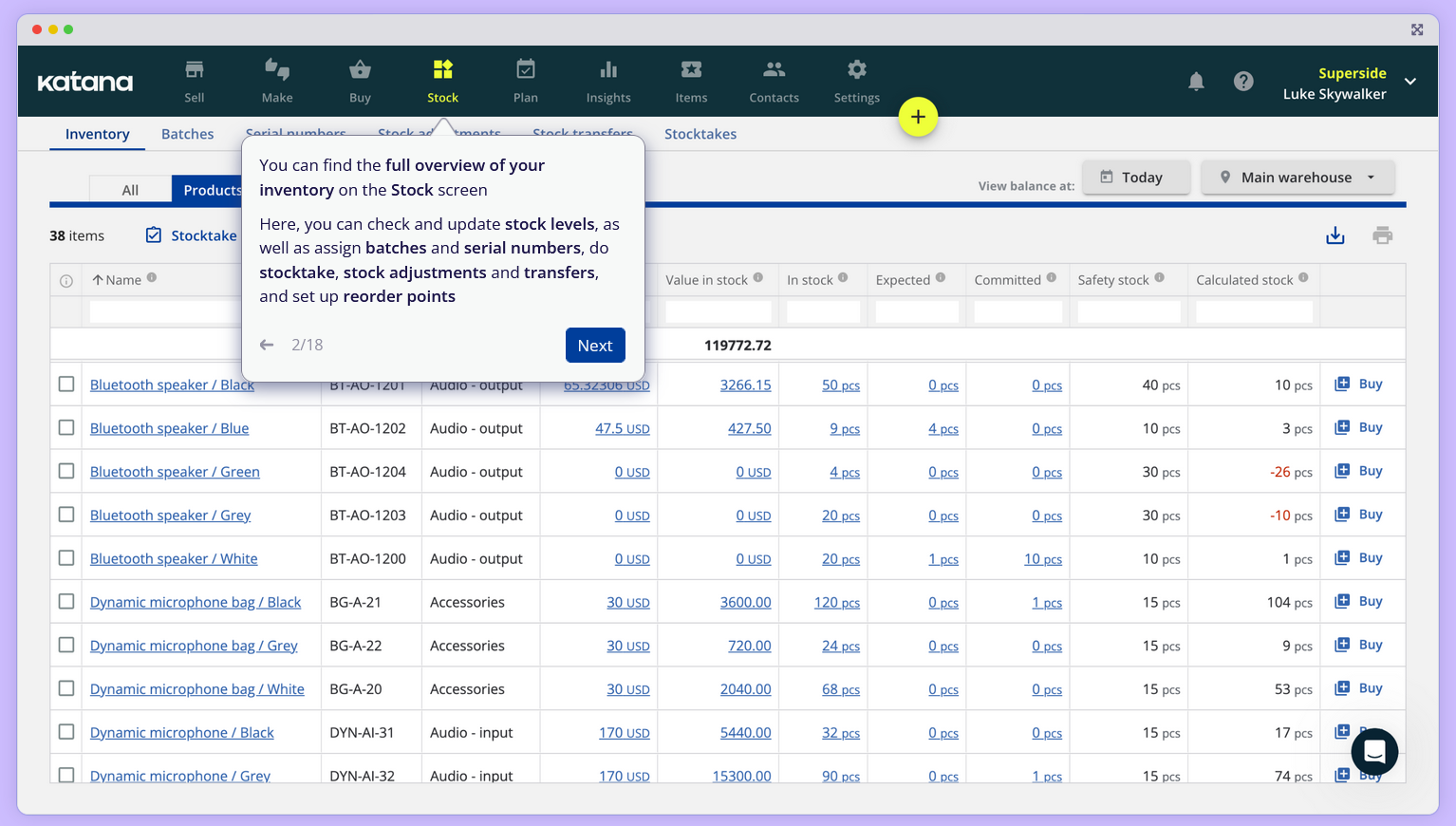
While the other tools on this list are specific to the construction industry, Katana is aimed at manufacturers and retailers.
However, it can still be valuable in construction for tracking material quantities.
But more than that, this tool can help you identify the root cause of material delays.
Katana’s material tracking across time allows you to benchmark performance by comparing data across shifts.
So, by monitoring the entire production flow, you can determine if delays are due to specific individuals or other factors.
With Katana, you can also:
- Oversee stock levels across various locations
- Receive live updates on manufacturing progress
- Create purchase orders directly within the platform
- Compare actual completion times with planned schedules
- Automatically reprioritize and reallocate items for open orders
- Allow operators to report the exact quantity of materials used for tasks
- Automatically update material levels once items are assigned to a manufacturing order (MO)
Katana’s pricing starts at $179 per month if billed annually. For more details on pricing, check their website.
If any of Katana’s features sparked your interest, you can book a demo to learn more about features and integrations.
Conclusion
At the end of the day, the goal is to have materials on-site, ready and available when needed to finish your projects on time.
That’s why each of these software was developed in the first place.
Whether you want to track materials on-site to prevent theft, monitor material usage against estimates, or track materials from ordering to installation through the entire supply chain, you’ll find a suitable tool among these ten options.
So, identify your priorities and pain points in material tracking, review the options one more time, and try free trials or book demos to see the software in action.
And then—choose the tool that best fits your needs.
Good luck!