From large-scale developments to smaller renovations, the ability to manage expenses can truly make or break a construction project’s viability.
That’s why, in this article, we’ll explore five highly effective methods for controlling costs that can help you ensure your construction endeavors stay both financially sound and on schedule from start to finish.
We dive into the practical tips, examples, and benefits of each method, so keep on reading to learn how to never go over the project budget again.
In this article...
Budget Management
The primary responsibility of budget management is to develop a budget tailored to the requirements of a specific project and then diligently oversee the incurred expenses in order to minimize their variance from that budget.
Hedi Ben Frej, senior project control manager at Emirates Global Aluminium, agrees that effective cost control begins before the first shovel hits the ground, more specifically, during the budgeting phase.
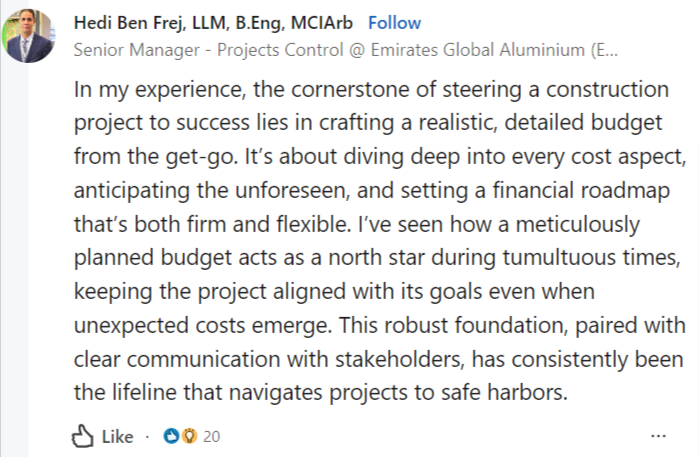
A meticulously crafted budget can indeed be your guiding beacon, he says, steering the project in the right direction, even amid challenges like delays and unanticipated expenses.
So, following Frej’s advice, make sure your budget is realistic and detailed, factoring in all relevant expenses—both soft, such as administrative salaries, and hard, including labor, equipment, and materials.
Below, you can see a more detailed list of typical construction costs to take into consideration during budgeting.
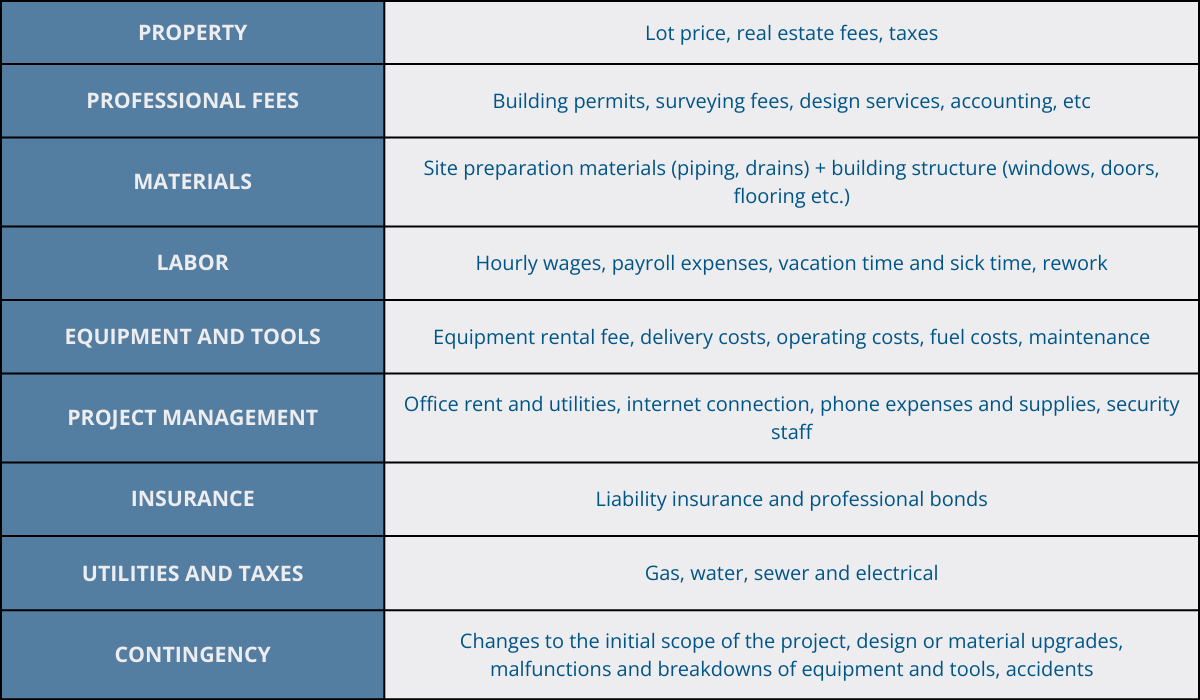
However, bear in mind that truly effective budgets don’t just list the expected costs, but address the unexpected ones as well, typically through contingency funds.
Usually amounting to 5% to 10% of the total budget, contingency funds refer to the amount of money allocated specifically to cover unforeseen circumstances, like equipment failure, material wastage, or even bad weather.
Given the well-known unpredictability of construction work, such proactive planning is simply a must.
This is precisely where budget management comes in.
It preemptively addresses potential risks and protects projects against expensive setbacks, thereby ensuring not just efficient cost control but overall project success.
Expense Monitoring Using Checkpoints
In the simplest terms, this method involves establishing specific checkpoints or milestones throughout the project’s lifecycle to review and analyze incurred expenses.
It proves highly effective for assessing whether you’re on track with spending at each project’s stage and for identifying cost overruns early on, thereby enabling corrective actions to bypass major overspending.
Say you reach a checkpoint (let’s call it Checkpoint C) and realize you’ve started to exceed the budget for equipment rental.
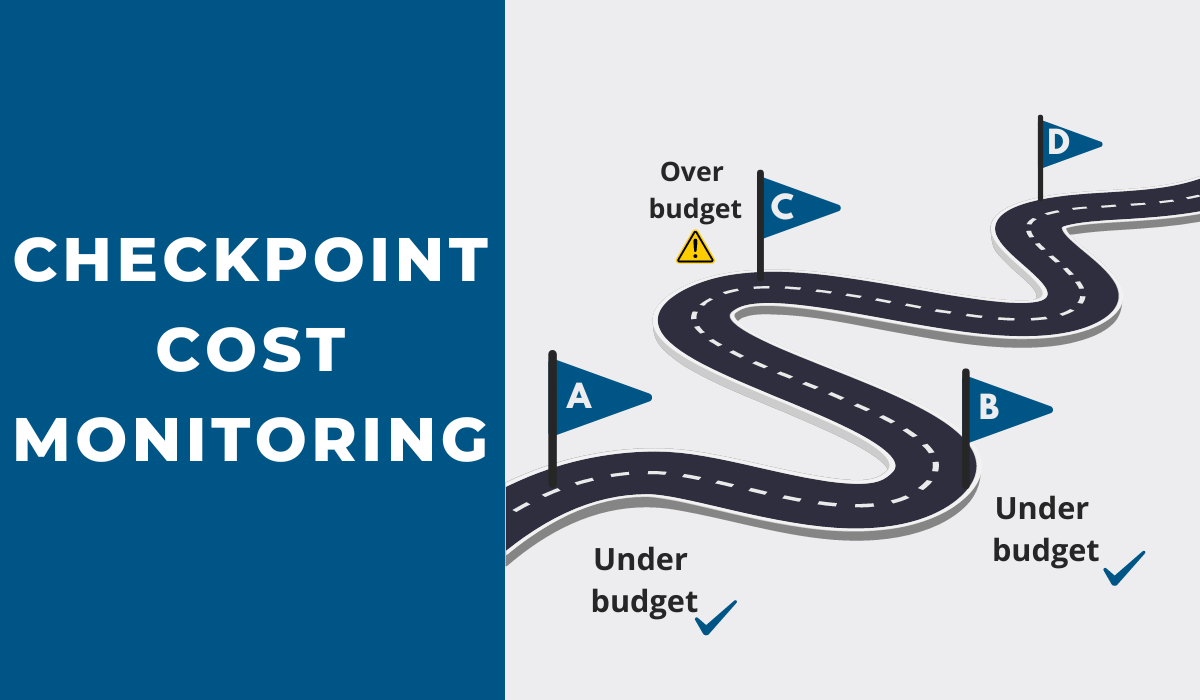
Armed with this insight, you can then reallocate funds from other areas, return some of the rented machines, or implement GPS location tracking to mitigate machinery hoarding, practically nipping the problem in the bud.
Generally, with this approach, there are no strict rules.
You can assess your expenses on either a weekly or monthly basis and set as many checkpoints as you want. Whatever works for you.
Still, for inspiration, here are some of the construction milestones that are commonly used:
- Initial planning and design
- Foundation and site preparation
- Structural construction
- Interior fit-out
- Final finishing
- Landscaping
Just be sure to establish them in advance, before the actual construction work starts, to give structure to the cost control process from the get-go.
The last thing you’ll want to do once the project’s already underway is to scramble to define milestones; you’ll want to have them at the ready.
Overall, you can view this method as a great way of detecting early warning signs of overspending.
This timely information can then empower you to take action, fix the issue on time, and prevent minor budget overruns from escalating into significant financial losses.
Usage of Change Control Systems
A Change Control System (CCS) refers to the processes designed to efficiently manage requested alterations to a particular project.
In construction, where sometimes even the smallest adjustments can significantly affect both budgets and timelines, such procedures are of paramount importance.
Their task is to prevent changes that aren’t really necessary and ensure that approved modifications are implemented in a manner that minimizes both cost overruns and delays, ultimately delivering what the client wants, but within the allocated resources.
Efficient change control typically involves several steps outlined below.
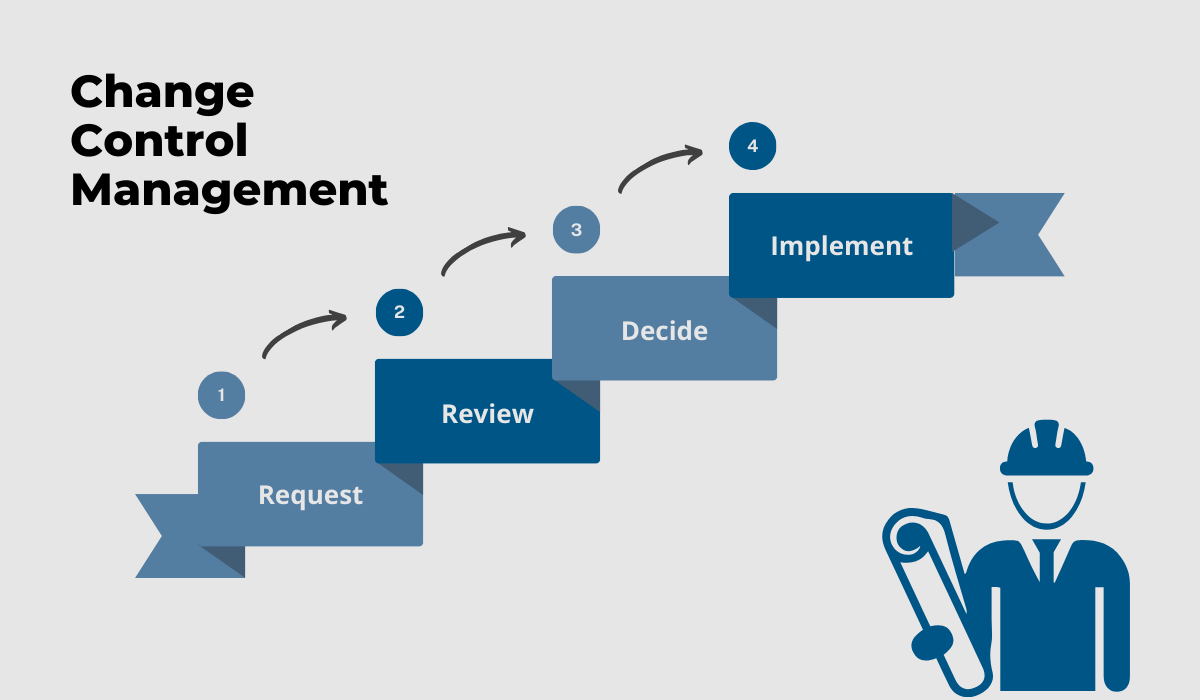
The first step, “request,” entails accurately recording the change request, including essential details such as the date, originator’s name, and comprehensive information about the alteration’s cost, reason, urgency, and impact.
This data is invaluable during the subsequent “review” phase, where the potential effect of the modification on the project is evaluated to determine if the endeavor is truly worthwhile.
The third step entails making a final decision regarding the change, categorizing it as either:
- Approved
- Rejected
- Deferred
- Requiring further information
Once a change is approved, the final step involves documenting it, notifying relevant stakeholders about it, and taking appropriate action to implement it.
However, you should know that simply adhering to these steps won’t be enough most of the time.
A successful CCS should also address some of the following questions.
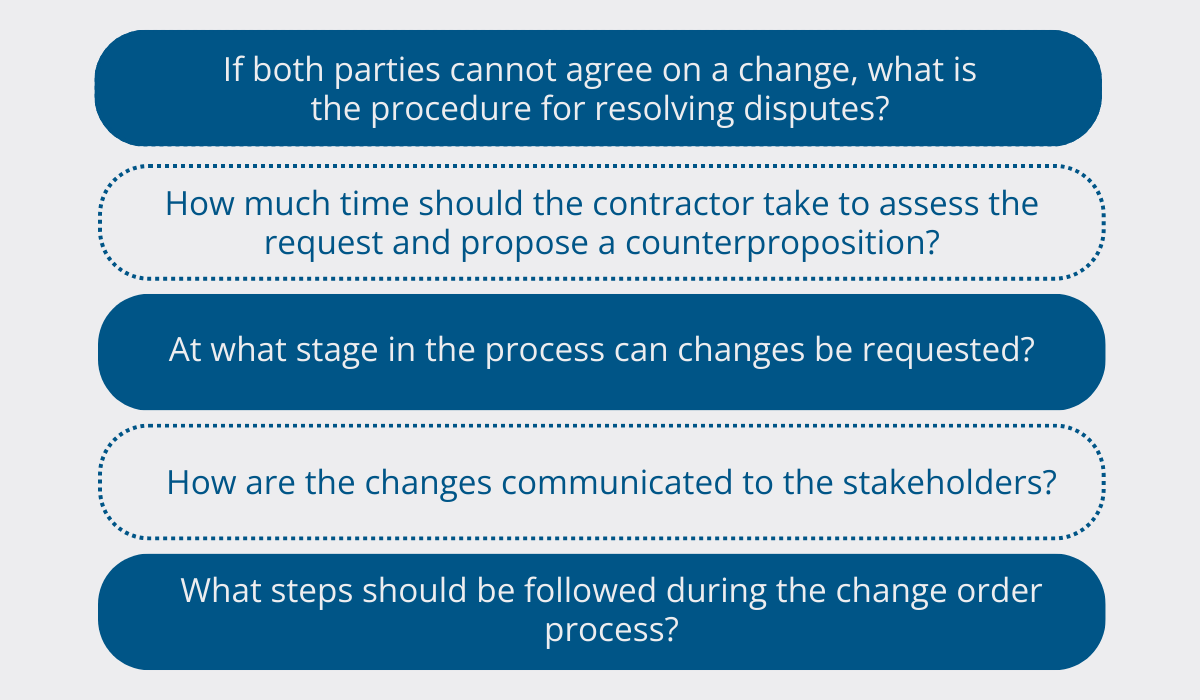
Answering these will help you verify whether the system can, in fact, effectively handle project changes and all accompanying challenges.
If you’ve answered the majority of these with “I don’t know”, then your current system might need some further refinement.
In any case, the role of CCS in cost control shouldn’t be overlooked.
If done properly, it’s an effective method that safeguards projects against scope creep, unnecessary expenses, and poorly executed alterations, all of which spell trouble for the project’s financial health.
Time Management
In construction, time truly is money.
Therefore, if you’re not careful enough with your time management, you risk significant disruptions and delays, all of which can incur considerable, yet unnecessary costs.
Say you scheduled foundation work to be completed in two weeks, but due to untimely permit acquisition, the excavation gets delayed.
Because of this, foundation contractors cannot begin their work as planned, consequently postponing all the other tasks such as groundwork, utility installation, and building erection.
This sets the entire construction schedule off track, triggering a cascade of delays throughout the project timeline.
Such delays not only impact the building’s completion date but also lead to budget overruns through increased
- labor costs,
- material storage costs,
- equipment rental costs, and
- overhead costs.
A survey commissioned by the Association of Professional Builders really puts things into perspective, revealing that an average residential project valued at $750,000 can lose approximately $670 per day due to delays.
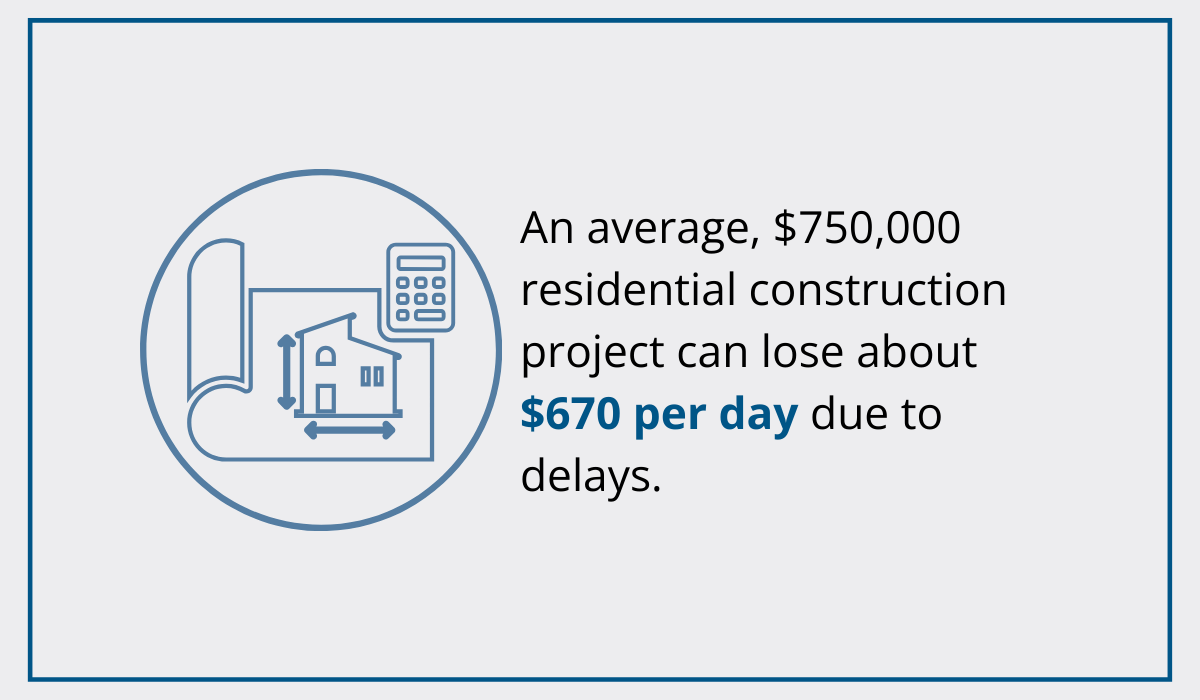
Of course, the larger the project, the greater the potential losses, too.
The key to mitigating such issues lies in developing a meticulous and realistic schedule that will ensure all activities stay on track without impacting the budget.
To make that possible, use a Work Breakdown Structure (WBS), which breaks down the total project scope into smaller, more manageable tasks.
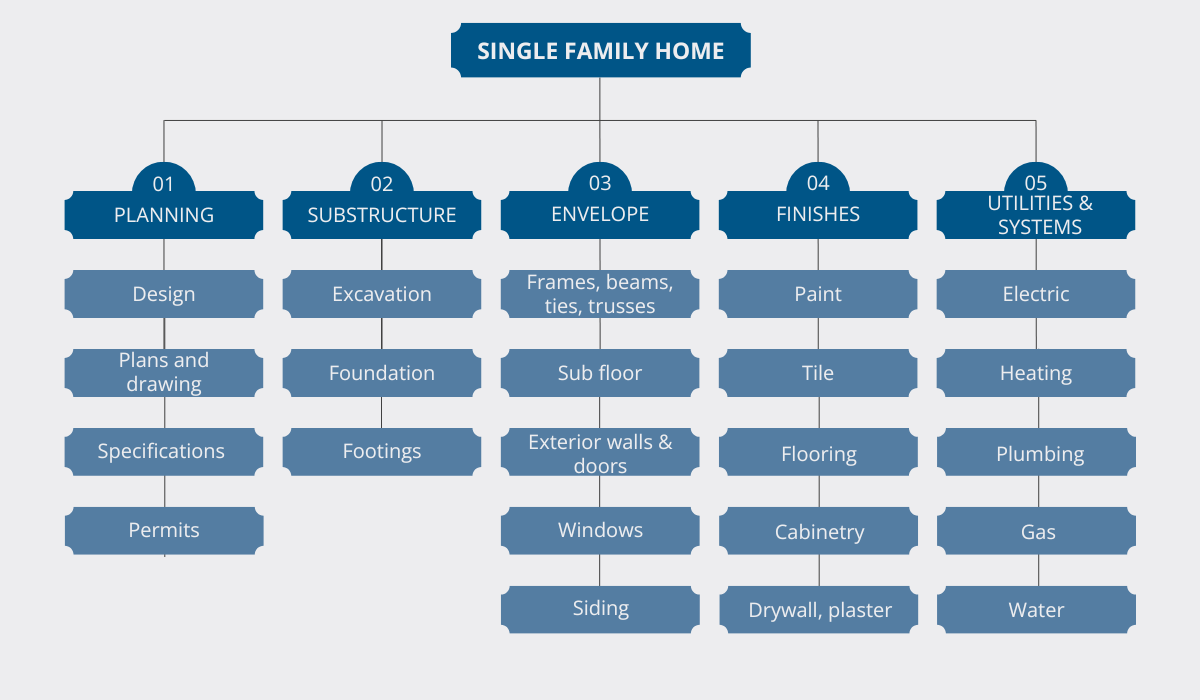
Given just how complex construction work can be, a WBS can be a real game-changer when it comes to project scheduling and visualization.
It organizes all activities into a structured format, making it easier to understand the scope of work and ensuring that no detail goes overlooked.
It also serves as a reference point for tracking progress, enabling you to compare the actual work done against the planned schedule at each level of the WBS to identify any deviations and take corrective action as needed.
At the end of the day, in construction, staying on time and within budget are practically synonymous—you really can’t have one without the other.
So, make sure to always prioritize precise scheduling, being well-organized, and timely task execution.
Better cost control will naturally follow suit.
Earned Value Management
Earned Value Management (EVM) is a common method for managing construction projects, assessing progress across three key components: schedule, scope, and cost.
The primary objective of EVM is to address two critical questions:
“Are we currently where we anticipated being?” and “Where are we headed next?”
To answer these questions, this method employs three distinct values:
Planned Value (PV) | represents the estimated cost of the work scheduled to be completed by a specific date. It establishes the benchmark against which actual progress is measured. |
Earned Value (EV) | denotes the value of the work actually completed, often represented as a percentage of the total project budget. |
Actual Cost (AC) | refers to the actual cost incurred for the work completed up to a specific date, offering insight into the financial health of the project. |
These values are actually used to calculate two key metrics: Schedule Variance, indicating whether the project is on schedule or not, and Cost Variance, determining whether the project is within budget or not.
The formulas for these calculations are as follows:
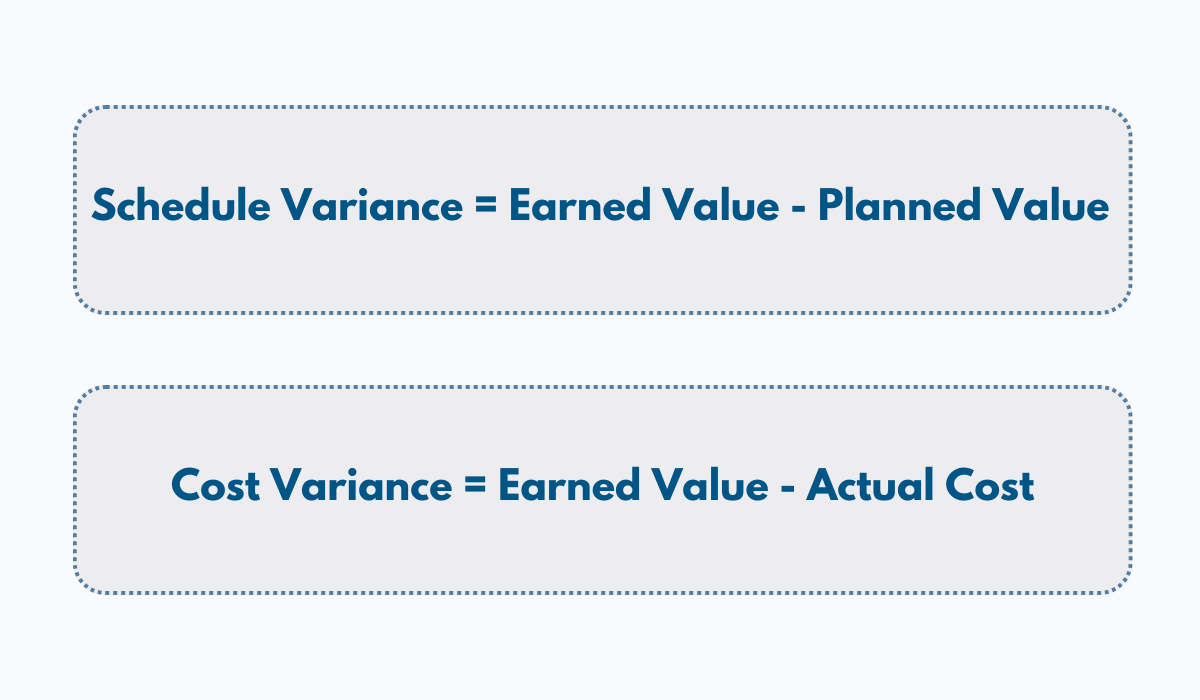
The variances can be classified as either favorable or unfavorable, revealing whether the construction team is performing better or worse than planned.
Let’s illustrate this process with concrete figures.
Suppose you have a project requiring completion in four months with a budget of $4,000 and you want to assess its schedule and cost variance after two months of work.
Obviously, first, you’d need those three values we mentioned earlier: PV, EV, and AC.
We determine PV using the following formula:
PV = Budget x % of total project duration
In this case:
PV = $4,000 x 50% (representing 2 out of 4 months completed) = $2,000
For EV, multiply the percentage of work completed (actual) by the project’s total budget (BAC). If 50% of the work is completed, the calculation is:
50% x $4,000 = $2,000
AC has no standardized formula. It involves simply summing up all incurred costs to date. For the sake of the demonstration, let’s assume you’ve spent $1,500 so far.
Now, let’s calculate the schedule and cost variances, beginning with the schedule variance:
SV = EV - PV
SV = $2,000 - $2,000 = 0
A result of zero indicates that the project is on schedule. A positive result would suggest being ahead of schedule, while a negative one would imply falling behind.
Moving on to the cost variance:
CV = EV - AC
CV = $2,000 - $1,500 = $500
In this example, the positive cost variance indicates that the project is under budget.
Overall, EVM provides a sort of bird’s eye view of your overall project progress, helping you assess efficiency, identify trends, and forecast future costs and schedules.
This, in turn, informs your decision-making, helps develop effective corrective strategies, and, ultimately, prevents costs from spiraling out of control.
Conclusion
Ultimately, the key takeaway is this: effective cost management isn’t about choosing just one of these methods.
Instead, it actually involves integrating several of them strategically to get the best results.
Yes, it all begins with establishing a solid budget.
However, it’s equally important to continually monitor expenses throughout the project’s lifecycle and compare them against the anticipated outcomes.
While this might seem somewhat labor-intensive at first, remember that, with a bit of diligence and patience, it can become second nature.
Soon enough, you’ll become an expert in cost control, adept at avoiding budget overruns and guiding projects to successful conclusions.