Work order tracking is essential for efficiency and organization in any construction company.
When contractors track work orders, working with third-party contractors and other labor forces becomes more efficient.
In fact, work order tracking can quickly result in a host of benefits, ranging from enhanced planning capabilities and optimized workflows, to an extended equipment lifespan, and a reduction of costs.
We go over these benefits, and more, in the following sections, so stay tuned.
In this article...
Optimized Work Order Management
First, let’s define what a work order is and how it functions within a construction company.
Work orders provide the important details necessary to complete a job, allowing employees quick access to data, photos, and contact numbers.
Since they also provide a summary of the maintenance tasks that must be completed, when done correctly, they provide useful insight into maintenance history.
As such, they make preventive maintenance easier, and expensive repairs and re-dos as a result of complete equipment breakdowns are far less common.
Below is an example of a work order. Note that it includes the name and address of the company overseeing the job, the date, and the site where the job takes place:
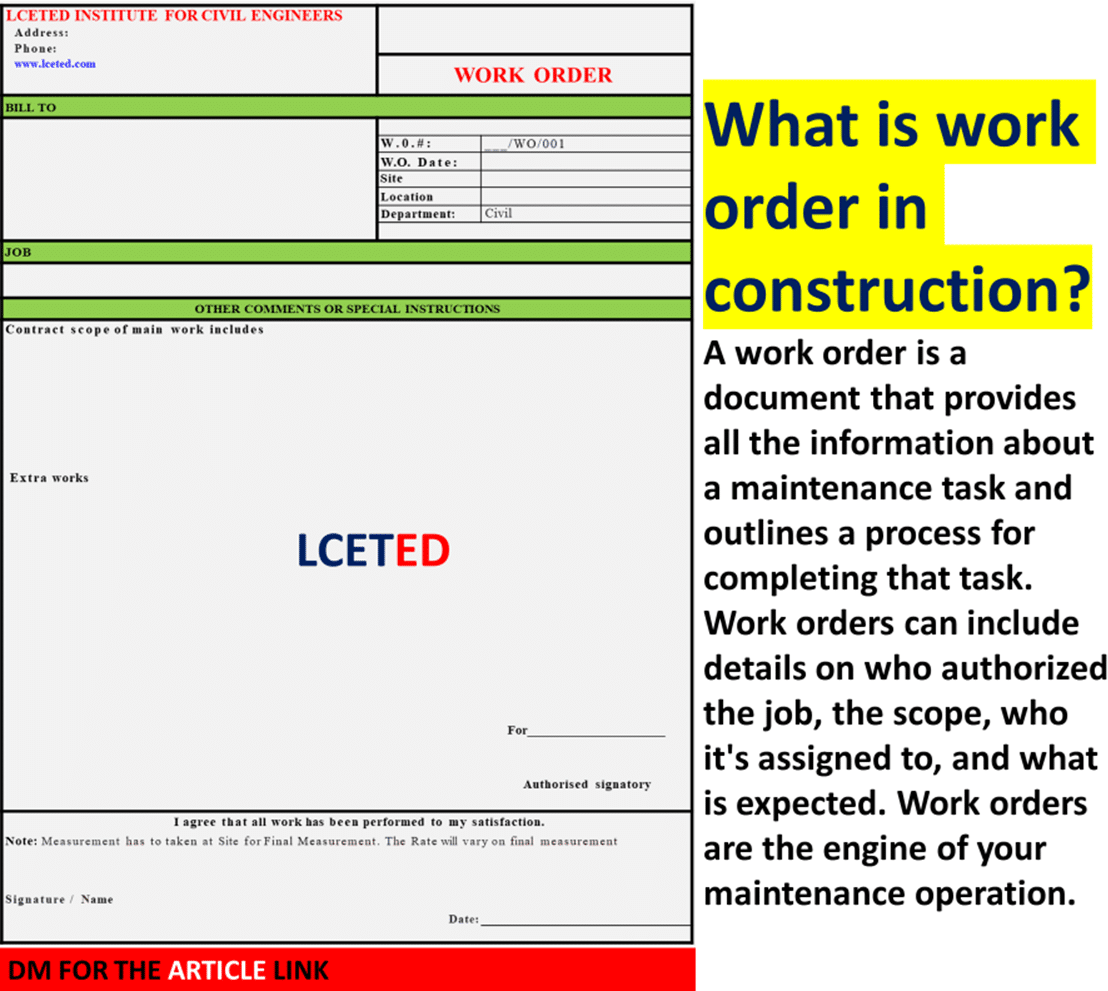
All of this information is essential for a work crew.
In addition to facilitating maintenance, tracking work orders also enables companies to have a better idea of when to replace parts or equipment, which helps them plan their future expenses and stay on budget.
As you can imagine, work orders contain a great deal of information that might change quickly.
Because of this, investing in a robust and easy-to-learn asset tracking system like GoCodes is an important part of work order management.
For instance, GoCodes offers a highly useful task feature, thanks to which your construction company employees can easily assign work orders for specific equipment to specific employees, then view all work orders that have been assigned under its “All Tasks” category.
With a solution like GoCodes in place, accurate work order details are always readily available, no matter how recently the decision was made.
Enhanced Planning Capabilities
Managers of a profitable and efficient construction company understand the importance of planning. All other aspects of a project hinge on devising a good plan.
Good construction planning doesn’t just maximize profits; it can save your company from closing its doors.
We briefly hinted at the ways in which work orders fit into an effective planning process in the previous section, but it bears a closer look.
Tracking work orders allows your construction company to accurately estimate future expenses.
These might include regular maintenance, replacement parts, tool upgrades, or extra inventory for a particularly busy season.
Not only does this capability assist in planning your budget, it ensures that you are ordering these items to be delivered just in time.
Ordering items for delivery at the optimum time is crucial, as without doing so, your warehouse space might not have the square footage for the items you need for that upcoming spring project, in addition to the cold-weather safety equipment still cluttering the shelves since January.
In short, poor planning can force unnecessary expenditures in the form of extra storage, insurance costs, and upkeep, and work orders help keep it in line.
Improved Decision-Making
Your construction company can use data gathered through work order tracking to monitor key performance indicators (KPIs).
Precise KPIs help you generate accurate reports, so you will have the tools to make data-based decisions rather than guessing or estimating.
And as you can see in the illustration below, when you’re making a difficult decision, accurate data is indispensable in multiple steps of the process.
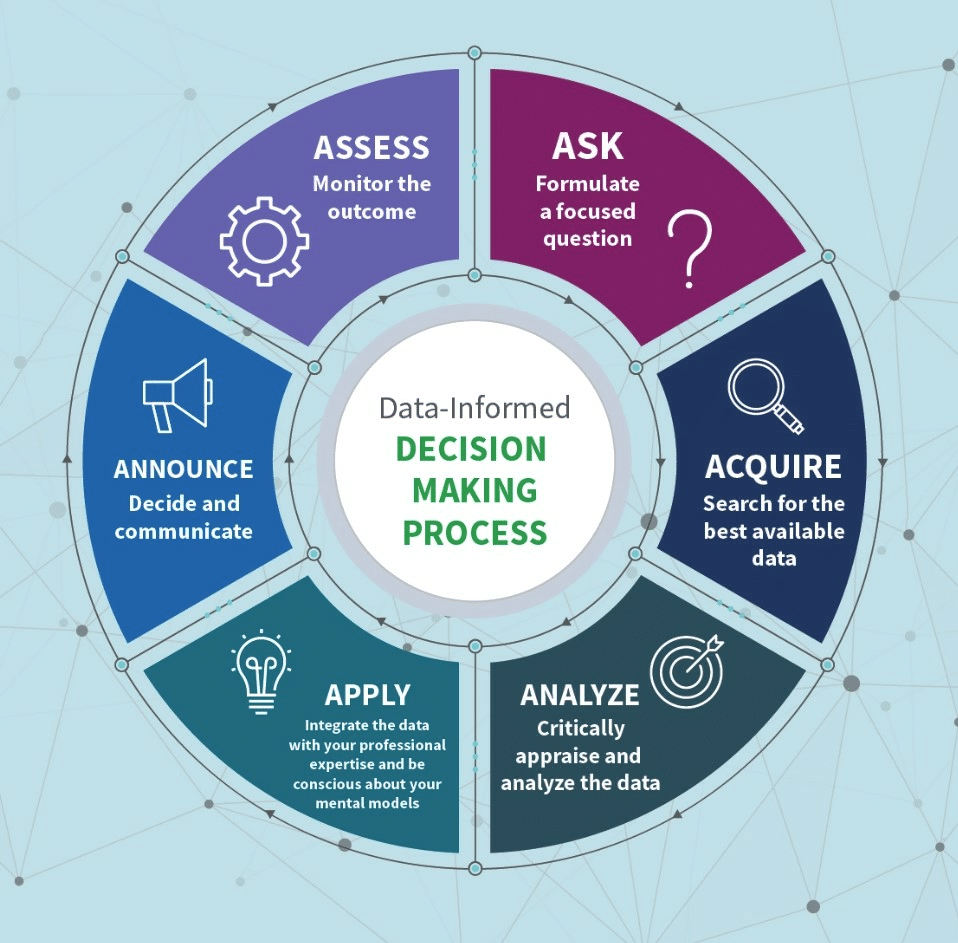
Working with poor estimates or guessing can lead to poor decisions.
In fact, even the final step of making a decision, assessment, is much easier and faster with asset and work order tracking, as relying on inaccurate numbers can provide an erroneous picture of how well the decision is working.
Pertinent data with instant analysis can result in less conflict, better avoidance of downtime, and a more sensible budget.
In addition, coming to a sound decision saves a great deal of money and time in the future.
For example, purchasing an excavator that is not a good fit for your company and is often sidelined can quickly result in rising maintenance costs, lost time on a build, and increased insurance rates.
However, data-backed decision making (based, in this case, on tracking work orders relevant to the matter of the excavator) helps you spot potential pitfalls ahead of time and consequently helps you avoid an unwise purchase in the first place.
Higher Employee Productivity
Attempting to improve work order management can rapidly result in higher employee productivity.
However, in the era of smartphones, sophisticated tablets, fast internet speeds, online gaming, and widespread social media, there are many things vying for your employees’ attention.
In fact, this statistic might come as an ugly surprise to managers and business owners:
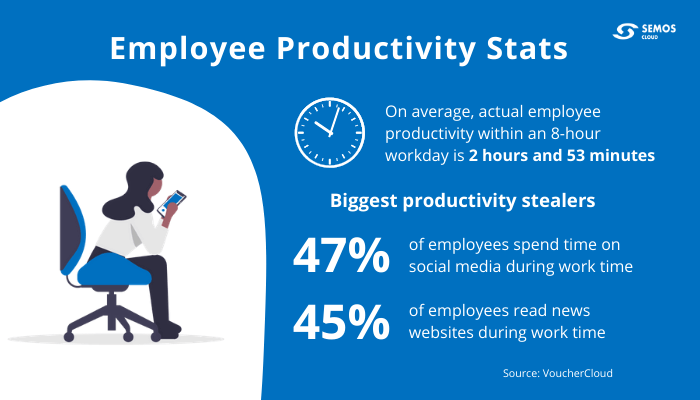
Losing almost three hours of an employee’s day is catastrophic for a construction company, where work is often done on tight deadlines and demands full attention for safety reasons.
Nevertheless, good managers understand that they should offer employees some trust instead of hovering over them.
Healthy communication patterns and respect for employees are key in boosting productivity. Micromanagement is also a waste of your own time.
So, rather than blaming technology, it’s best to work with it.
Using asset and work order tracking streamlines your employees’ tasks and puts their familiarity with various electronics to a beneficial use.
With GoCodes, for instance, maintenance teams can use their own mobile devices to quickly scan the QR code on the item in order to access the relevant information about it, such as its maintenance history.
Finally, work order tracking will result in better employee efficiency, because your team will know exactly which piece of equipment they were assigned to, which tasks they need to perform, and when they are expected to perform those tasks.
Instant communication can work for your construction company if you harness it properly.
Increased Safety Compliance
A healthy construction safety culture should be paramount on a construction site and throughout the entire business.
But as you know, workplace safety involves many facets, including regulation, training, and risk assessment. This visual lists just some of these elements:
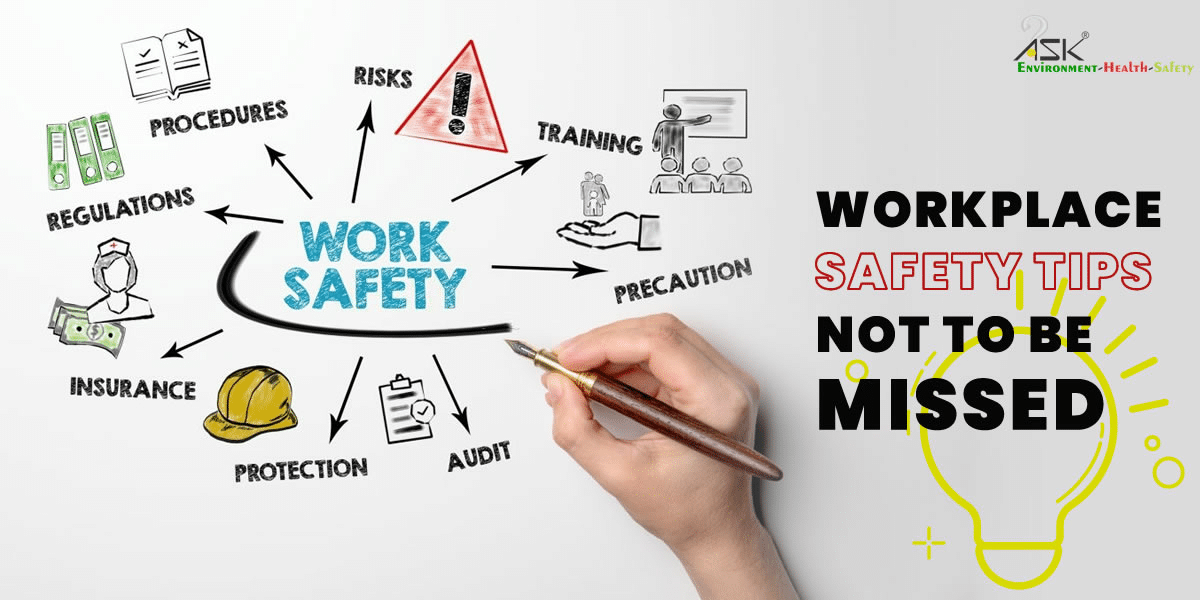
Tracking work orders can help foster a better environment for safety. Namely, by tracking work orders, your construction company will be able to comply with safety regulations more easily.
Work order tracking enables your construction company to communicate, organize, and evaluate safety risks and compliance with regulations.
With up-to-the-minute data at your fingertips, you have the ability to better plan your safety actions, ensure that maintenance is correctly performed, and provide documentation and proof of compliance procedures.
Extended Equipment Lifespan
Do you know how long your expensive construction equipment is supposed to last?
Research shows that the expected lifespan of construction equipment extends to as much as a decade and a half.
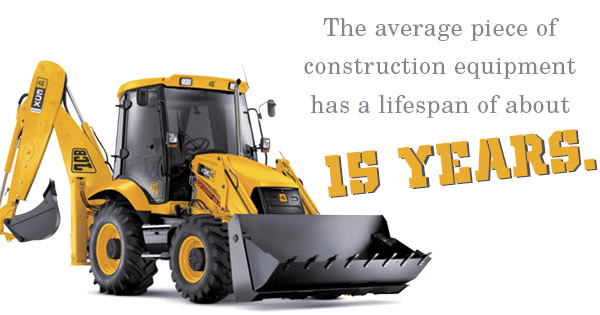
Fifteen years is a long time to own a single asset, but the enormous cost required to purchase these specialized fleet vehicles means that it’s best to keep your investment in as good condition as possible, through regular maintenance.
Tracking work orders allows your company to schedule the timely inspection and maintenance actions required to keep your equipment in operable condition for a longer time.
Doing so helps extend the overall lifespan of the equipment in your construction company.
When it’s time for a regular maintenance appointment, your asset tracking system will alert you to make arrangements with a third-party specialist or to ask your maintenance staff to clear some time for these check-ups.
Once the day of the maintenance check arrives, a tracking system can provide valuable information to the technicians.
This includes the name of the manufacturer, the serial number of the piece of equipment, and when the vehicle was purchased.
All of these let your specialists know as much as possible about your vehicle and its history.
For example, if the pivot point of an attachment was recently repaired, your team might then know to ensure that the repair was thorough, lasting, and safe.
Tending to regular equipment maintenance can help to avoid unforeseen breakdowns, which are not only frustrating, they can prove expensive when your construction company must rent a replacement vehicle and scramble for a fast repair on the idle equipment.
Focusing on extending the overall life of your equipment might require money and time, but the cost is well worth it compared to nursing machines through breakdowns or trying to work with shorter timelines on construction milestones.
Reduced Costs
Controlling costs is essential to operating a well-run construction company.
One way to do so quickly and with great accuracy is to use asset tracking to enable automated work order tracking.
GoCodes stores data on the cloud, which saves your company money on storage costs and keeps your data safer than in a physical location, where theft, fire, flooding, and misplacement can quickly destroy years’ worth of important information.
Errors are a major culprit for reduced profit.
Anywhere between 10% and 20% of the cost of a construction project is attributable to errors.
Therefore, it’s no major leap to conclude that minimizing errors is a way to also cut down on costs.
The good news is that this is a factor of a project that you can almost certainly control.
Not only will digitizing work orders help reduce errors by keeping your employees accountable, your workplaces will likely become safer, more efficient, and more easily audited.
Conclusion
Instituting work order tracking is helpful to construction companies in a number of ways.
Doing so easily optimizes work order management and enhances planning capabilities.
Tracking work orders can also help to improve decision-making by consistently providing accurate data. It results in higher employee productivity as well as increased safety compliance.
Moreover, reducing costs is easier with automated asset and work order tracking, and the useful life of your construction equipment is increased as maintenance becomes more efficient.
We hope the benefits we’ve listed here have convinced you to start tracking work orders, and a robust digital solution like our own product, GoCodes, can help you with that, so don’t hesitate to get in touch and book a consultation.