Companies use work orders to monitor business tasks and employee performance.
Even though work orders are supposed to help you be more organized as a business, they can easily get overwhelming, confusing, or neglected, especially if you’re dealing with large quantities.
Because of this, it’s important to find a good work order management solution for your team to help them use this feature and make the most out of it.
In this article...
Importance of Work Order Management
Work orders are used for any business or servicing tasks that a company wants to track and control.
Nowadays, many businesses use them for any issue or an assignment within the company as they contain all the necessary information to solve the task.
Since they’re becoming prevalent, it’s essential to improve your management of them—the better your work order management system is, the more efficient your company will be.
When you have a good overview of work orders, you can understand how efficient your team is, and monitor the quality of your maintenance, as well as the costs of your business.
You can track them, and see whether you have set good standards and if you have clear instructions for servicing.
On top of that, you will be able to access detailed data on each task and its solution, as well as asset details for each maintenance operation.
This will allow you to perform analyses, reevaluate equipment and business processes, and find more efficient solutions.
Companies can opt for pen and paper, whiteboard, spreadsheet, or software work order management.
Whatever option you choose, you have to ensure that your team has access to all the current and past work orders, asset records, and information like warranties, depreciation, and similar data that can help them perform better.
Benefits of Work Order Management
Here is how your entire operation can benefit from efficient work order management.
Organize Processes
Work orders help you organize your processes better, which means that at any point in time, you and your team will be able to go through them and understand which tasks you’ve already finished, which are pending, who is in charge of them, and when the deadline is.
Each employee will understand the phases of work orders and what they need to do to create or solve one, allowing everyone to be more efficient and productive.
Instead of asking around, trying to fix an issue independently, and not knowing who is in charge of helping them, employees can simply create a work order and explain the problem, saving everyone involved time and minimizing downtime in the process.
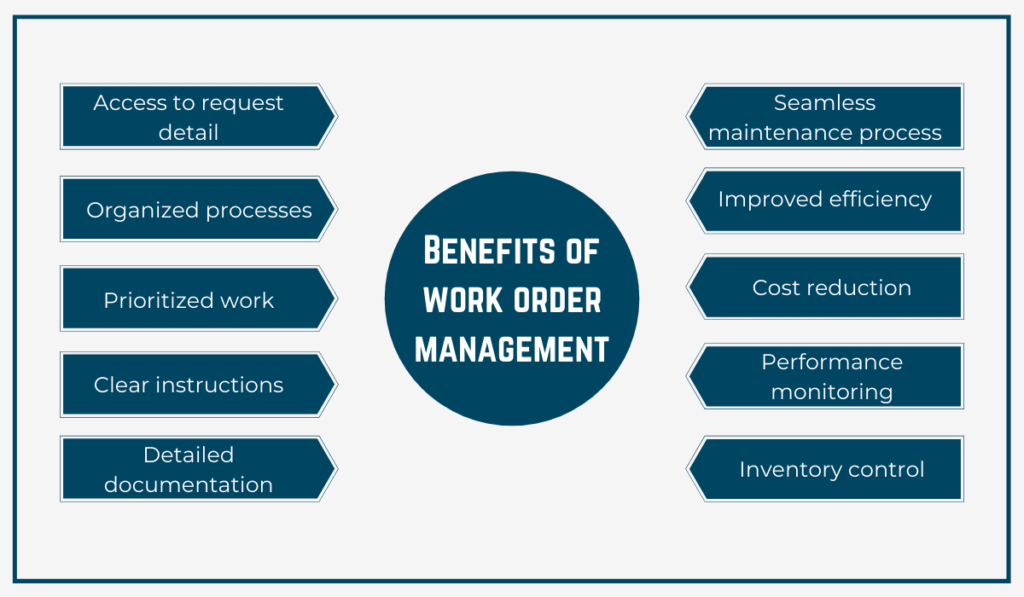
Maintenance specialists will receive a detailed description of the problem and the steps they need to solve it while using the asset’s history and details.
Organizing processes properly lets you always know what is going on, what you still need to do, and how long it takes to finish specific tasks.
This knowledge allows you to plan future purchases or hires better while giving insight into how efficient your current system is.
When you don’t use work order management, it’s challenging to keep track of who is doing what, how well they do it, how long it takes them, and the quality of the result.
Inventory Control
Another beneficial aspect of good work order management is an improvement in inventory control.
You get to understand which tools are unavailable due to maintenance and keep track of the assets you need to perform said maintenance and any spare parts the technicians might need to get the equipment back up and running.
However, you can’t rely on paper and whiteboards to help you do this.
Specialized software might be a good solution if you want to keep track of your tools, know where they are, who is using them, when they will return them, and have access to the asset’s comments and maintenance history.
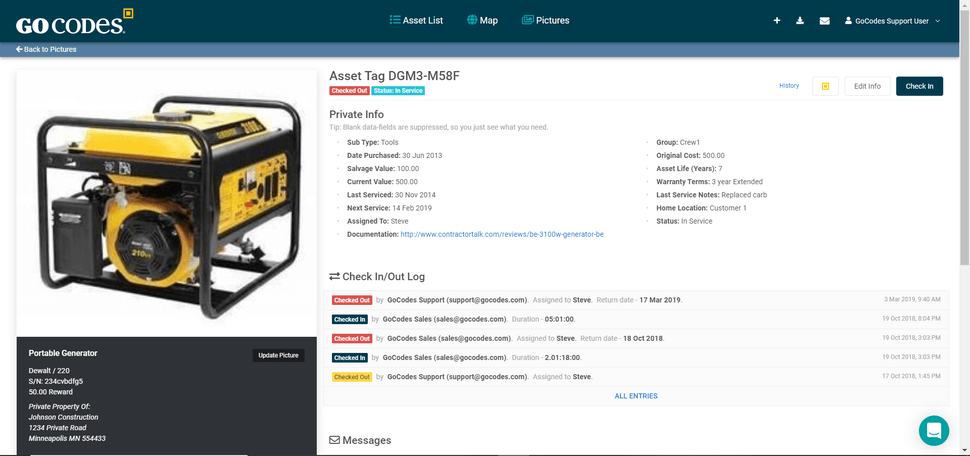
This information helps your team plan around the maintenance since they know they cannot count on the item until the work order deadline.
It also lets the maintenance team understand if they have all the necessary assets to perform servicing and enough replacement parts.
Without this insight, you can lose time and money while you wait for a tool to be available or to be ordered, shipped, and delivered.
Specialized software can notify you when you reach lower asset quantities, which means you can look into the prospect of buying new equipment to stock up on the assets or replacement parts you need.
Seamless Maintenance Process
Work order management improves your maintenance processes, regardless of what type of maintenance you’re using.
Whenever there is a breakdown or scheduled maintenance, someone needs to create a work order, explain the problem, attach any necessary documentation, and submit the work order to the maintenance team.
The person in charge of work orders will determine which tools and skills are required to perform corrective or preventive maintenance and select the best technician for the job.
The maintenance team will have clear instructions on what happened with the asset, what they need to do, which tools to use, and how urgent the repair is, allowing them to focus on higher priority tasks and get to work as soon as they read the work order details.
Everyone else who has access to work orders will understand what is happening with the assignment, and which steps the technician took.
When you use specialized software, there’s a trail of every maintenance task with all the details the requester, manager, and technicians wrote.
Whoever works on the following work order for that same asset will have the details about all the known issues with the tool and the maintenance that has been conducted.
This will save them time and make them more efficient.
Cost Reduction
When you organize your work orders in a way that is easy to follow and understand, you maximize your team’s efficiency, making the process cost-effective.
The maintenance team can spend more time conducting repairs instead of wasting it on trying to find details about the issue the reporter experienced or data on previous maintenance sessions.
They will have clear insight into what they need to do and be able to start doing it right away, which speeds them up, allows them to solve the issue quicker, and gets the asset running again.
Depending on the type of maintenance you choose, your team might submit work orders before a breakdown happens as a part of regularly scheduled operations.

This option allows the maintenance team to inspect the equipment, tweak it, replace any parts that might cause issues, and ensure that the equipment is safe to use and functions correctly.
All of this prolongs the asset’s useful life, guarantees that you will be able to use the tool longer without risking anyone’s safety, and prevents costly equipment failures.
When you perform regular servicing, you’re eliminating minor issues that might cause a malfunction later on, which could cost a lot more than routine maintenance, especially if it happens to an asset you depend on to keep working.
Best Practices for Work Order Management
Quality management of work orders is critical if you want to stay on track of all processes, be aware of setbacks, and determine employee and process efficiency.
Here are four tips you can use to get closer to high-performing work order management.
Provide Central Access to Resources and Processes
Every team member involved in the work order process needs to have access to all the necessary documentation, instructions, and resources to perform their part of the job.
You also have to train the team on how to use work orders, handle them, and why it’s essential to always create a work order when there is an equipment issue, no matter how small.
By doing this, you’re helping the team accept the new solution and get used to it.
Work orders serve as measures of the efficiency of your processes, so everyone must use them for each task they have for themselves or others.
When your servicing team has access to instructions on solving specific work orders, you’re helping them be faster and more secure in their work.
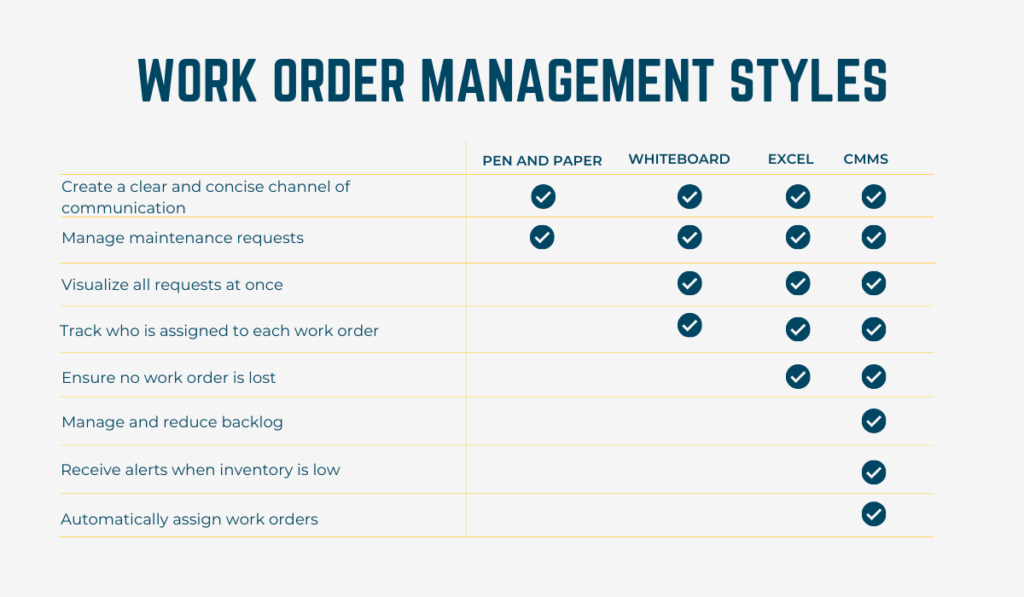
They should have insight into previous maintenance records, which let them notice any patterns in breakdowns, manufacturer’s instructions and suggestions, and recommendations on how to fix the issue.
All of this data will help them figure out the best way to solve the problem.
You can’t easily transfer such data via pen and paper or whiteboards, which is why it would be wise to opt for cloud-based solutions which allow you to store the data online and associate it with the item.
This way, everyone on your team will have access to this information, even if they’re not a part of the maintenance team.
Create Maintenance Checklists
A great option you can use in work orders is adding instructions for the maintenance team.
Doing this helps the team understand the issue and their next steps while creating a standard that they have to follow in the future.
Such instructions help you standardize each task’s solution, assuring that your team will always follow the same steps and achieve the same results.
Your team has clear points to rely on instead of improvising and trying to look for the correct answer on their own.
A good solution for providing instructions are checklists which let the technician select between passed or failed (yes or no), so everyone can see how well the tool performed on the tests or where the maintenance process was stuck.
Of course, such checklists are best used for scheduled maintenance checks.
These become a part of the routine when done often, and the risk of forgetting a step or two is high, especially when the asset is functioning correctly.
Another benefit of maintenance checklists is that even the less experienced team members can follow the steps and practice their knowledge.
This leaves the more skillful team members to handle urgent, unique situations requiring their expertise.
Prioritize Work Orders
Adding a priority to an assignment lets your team know which matters are urgent and which can wait.
Of course, priority depends on many things, and you will get to decide on it on a company level, but most of all, it depends on how urgently you need the asset.
If it’s a one-of-a-kind asset that you can’t finish a project or production without, the priority is the highest possible.
Even if you have more than one asset with the same purpose but are all in use, you need to fix the asset urgently to continue working.
Another example of high-priority fixes are tools that can threaten your employees’ health and safety.
You need to eliminate all threats before allowing workers to use the tool again, which is why your maintenance team needs to be aware of the task’s priority.
The team can handle the low-priority issues after the higher priority ones are solved since they aren’t causing any monetary losses or additional risks to the company or workers.
Prioritization guarantees that you’re using your servicing resources to their full potential—your team is working on the most urgent matters first, helping you eliminate even more downtime or health risks.
Use Scheduling Equipment Management Tools
Scheduling equipment management software and applications are a valuable investment for anyone dealing with equipment and work orders.
They optimize the work order process, simplify it, and remove redundancies and manual work, thus saving your team time and company money.
Such tools let you have a database of your assets and track them with ease using the software while understanding who is using it, when they’re returning the item, and what its condition is.
Equipment scheduling software has options like equipment tracking, updating asset details from a smartphone, scheduling maintenance dates, and making that data visible to anyone who searches for the equipment in the system.
All of this brings your employees up to speed in a couple of clicks.
Software solutions like GoCodes Asset Tracking allows you to upload any asset-related documents so your team can have a complete overview of manuals, instructions, maintenance dates, and asset history.

Your employees can also leave comments on the asset page and change the status to “needs repair” if they experience an issue while using the asset.
This option assures you that your team can report problems quickly and efficiently and that you’re wasting no time before fixing issues, which eliminates unnecessary downtime.
Conclusion
If you keep your work orders organized, they can help you manage business processes more efficiently, monitor your equipment and inventory levels, and save money.
On top of that, if assets play a key role in your company, work orders can help you create standard procedures and maintenance checklists and ensure the team follows them every time.
To automate the process and save time and money, opt for software that lets your team access a centralized database containing all the necessary data.