Key Takeaways
- Setting measurable goals makes it easier to monitor productivity and motivate the workers.
- Different software can help provide an accurate picture of operational efficiency.
- For higher productivity, also monitor how much equipment is being used.
In construction, ensuring that projects are completed on time and within budget is what, ultimately, matters the most.
However, achieving this requires more than just skilled labor and quality materials; it demands keeping an eye on productivity, too.
Now, measuring productivity on your construction site can seem somewhat challenging or time-consuming, but it’s an essential step toward optimizing performance, reducing costs, and increasing overall operational efficiency.
That’s why, in this article, we’ll explore five practical tips to help you master productivity tracking and keep your workers and machines operating at their very best.
In this article...
Set Measurable Goals
Measurable goals use specific criteria such as percentages, deadlines, numbers, etc., to track progress.
Setting such objectives from the get-go will not only make productivity monitoring easier, but it will also ensure the entire team stays motivated as well as focused, and ultimately, meets their targets.
As Anthony Impey, CEO of Be the Business—a UK-based company helping small businesses boost their performance—says, measuring progress is key to improving productivity.
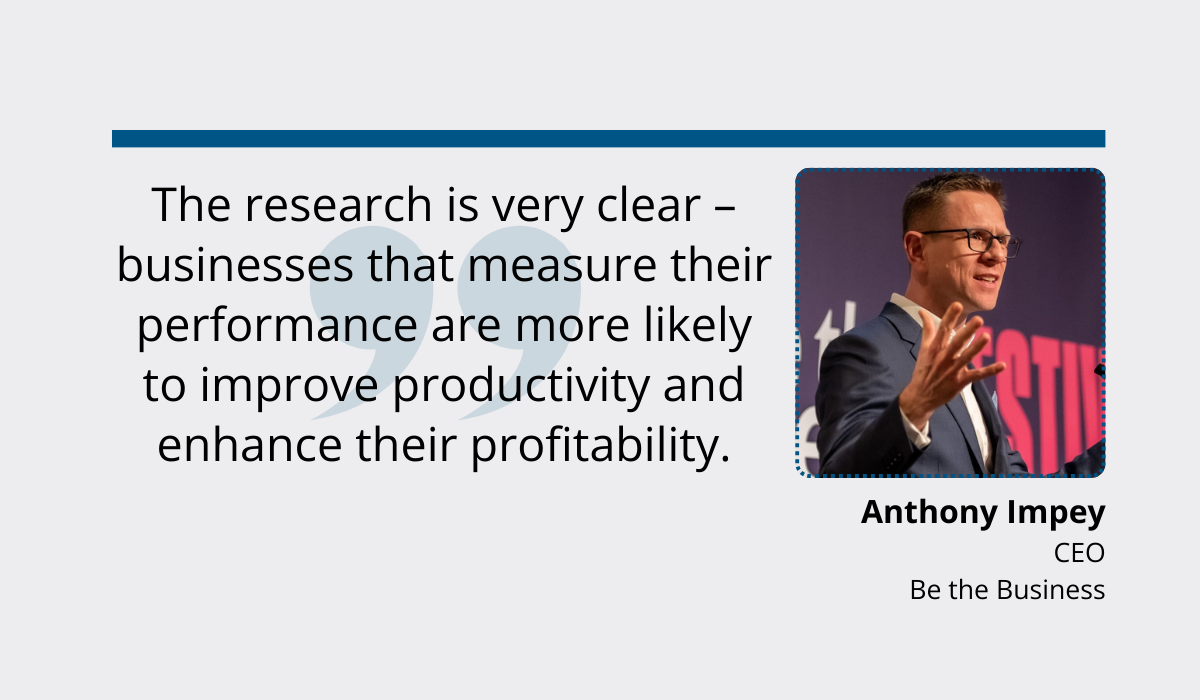
However, to be able to measure, you first need to set objectives that are actually measurable.
Makes sense, doesn’t it?
But how can you determine if your goal is measurable?
Typically, these goals address some of the following questions:
- How much?
- How many?
- What are the indicators of progress?
- How do you know when the objective is achieved?
If answers to any of these questions aren’t evident straight away, it means your goals lack measurability, making progress assessment complicated at best, and impossible at worst.
For instance, setting a goal like this doesn’t cut it:
“We need to finish the foundation for a building as soon as possible”
What does “as soon as possible” mean in this context?
How will you know when the task is done?
Instead, if you phrase it as follows:
“We need to lay 300 cubic meters of concrete within the next two weeks.”,
it becomes much clearer what exactly needs to be done and by when, making it easier to monitor and reach this target.
Similarly, if your aim is to improve safety, don’t just say:
“Make sure the site is safe.”
Be more specific:
“Achieve zero lost-time injuries in the next six months.”
Setting precise, measurable goals transforms abstract aspirations into tangible targets.
It keeps your team aligned, ensuring everyone knows precisely what success looks like and how to get there.
Plus, it gives you a clear view of your productivity levels, so you can celebrate milestones and adjust course when needed.
Help Yourself with Technology
Nowadays, there’s really no need to monitor, measure, and analyze your productivity manually when there are numerous software solutions that handle these tasks for you—automatically, more accurately, and without the hassle.
Using error-prone spreadsheets to keep tabs on goals, milestones, worker hours, budgets, and more only invites trouble anyway.
It often yields information that’s either incomplete, incorrect, untimely, inconsistent, or inaccessible, which FMI and Autodesk refer to as “bad data” in their Harnessing the Data Advantage in Construction report.
According to their findings, this bad data leads to wrong decisions more than 50% of the time.
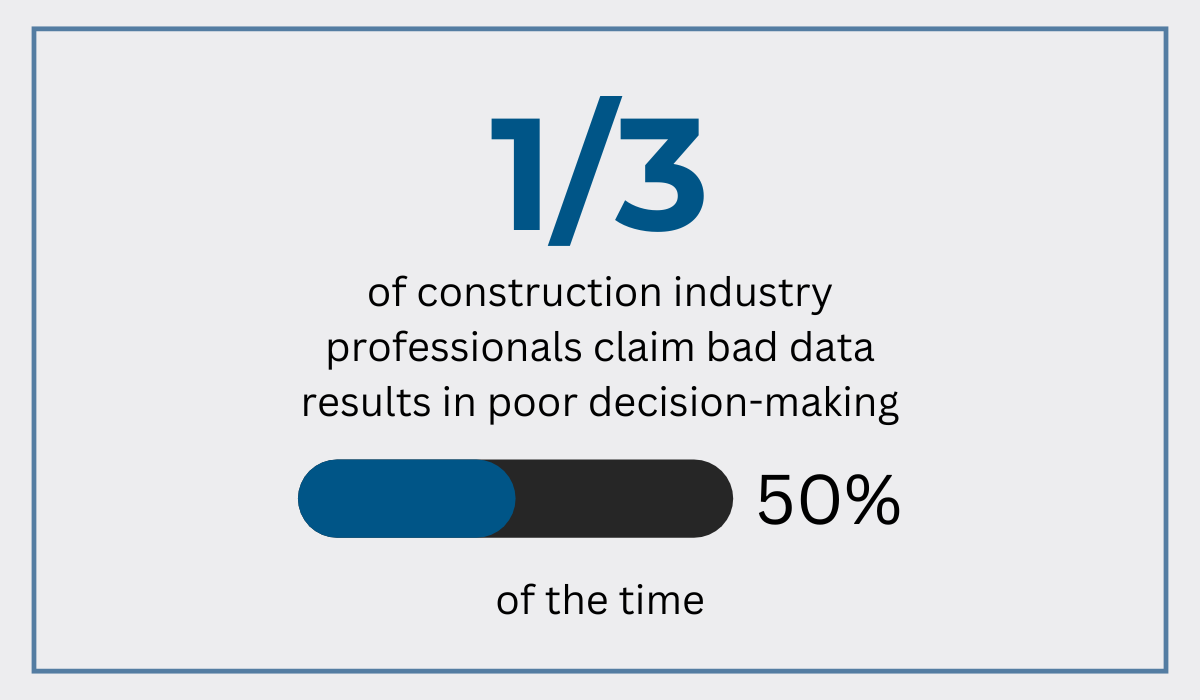
This means that, without reliable project information, you end up with a completely inaccurate picture of your operational efficiency, potentially steering your projects in the wrong direction and causing productivity to drop.
So, to improve your data effectiveness, consider automating some aspects of project management.
For example, you can use time-tracking software to monitor worker hours.
It allows you to track both billable and non-billable hours, and produce insightful reports to see exactly how your team spends their time.
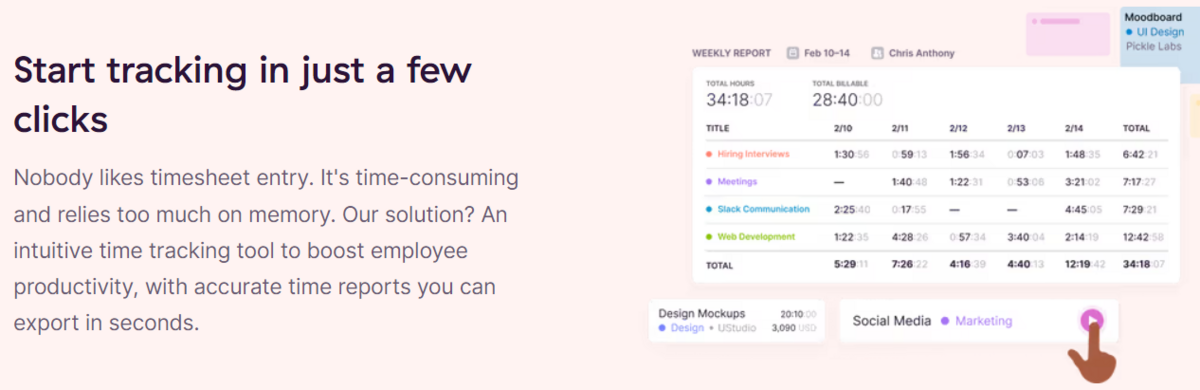
Suddenly, everyone’s contribution to overall productivity becomes crystal clear.
Or, you could use construction project management software.
These systems offer a comprehensive project overview, ensuring no crucial information slips through the cracks.
Schedules, worker tasks, RFIs, submittals, meetings, budgets, punch lists—you name it, project management solutions can track it.
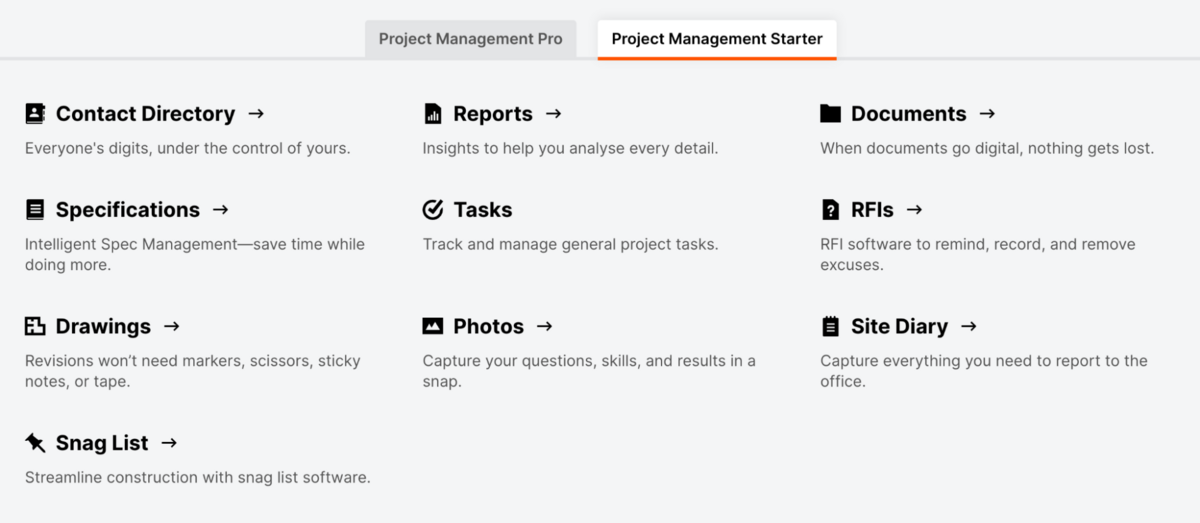
As a result, measuring productivity becomes easier, more effective, and more accurate, yielding actionable insights that would otherwise surely go unnoticed.
Conduct Regular Site Inspections
Sure, software solutions are extremely valuable for gathering project data, but to get a truly accurate and complete picture of your job site productivity, you need to step out and do some legwork.
That’s where regular job site inspections come in.
After all, software can only do so much—there’s no substitute for boots on the ground.
You’re the one who’s best equipped to spot potential safety hazards, poor work quality, or noncompliance with internal procedures.
This allows you to take immediate action, mitigate risks, and keep operations running smoothly without any drop in productivity.
Nathaniel Dobbs, a Senior Solutions Engineer at Procore we mentioned earlier, aptly explains what job site inspections are all about.
“The idea of job site inspections, from my experience, is to document the conditions of the job. […] The intent upfront is “let’s document what’s been done, let’s document what we still need to do, and then if we can, let’s document that we corrected it.”
Essentially, this is a vital process that records current progress, identifies inefficiencies, and outlines pending tasks—all crucial for measuring productivity.
To make your inspections as thorough as possible and ensure that no stone is left unturned, consider using inspection checklists.
These documents provide a comprehensive list of all tasks and items to check, ensuring a detailed assessment of the overall situation.
For example, for a safety inspection, you’d use a checklist like the one below, provided by the Health and Safety Authority.
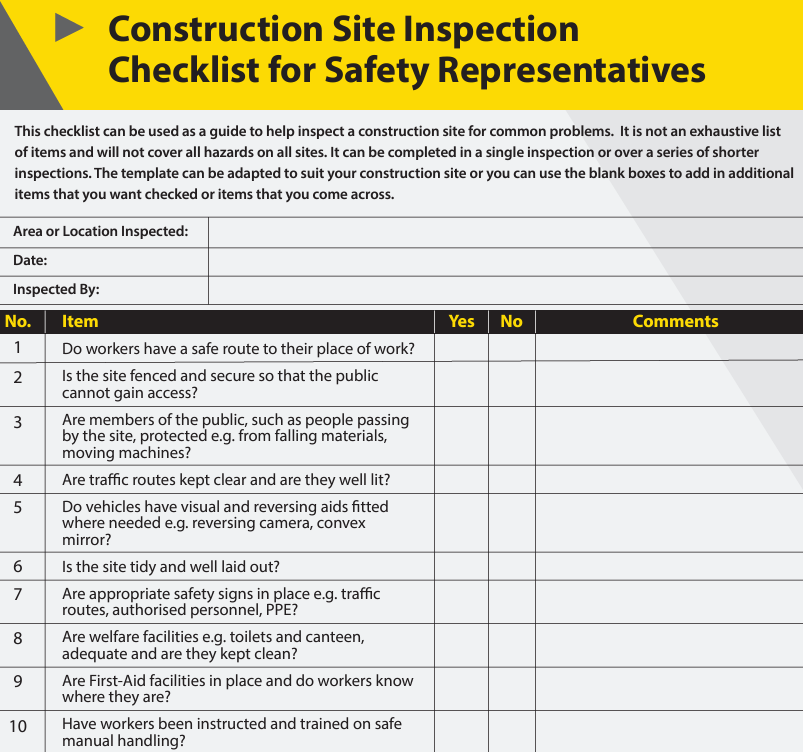
Having such a tool makes all the difference during inspections as it standardizes the whole process, making sure it’s done the same way every single time.
As a result, you get more accurate, consistent, up-to-date, and reliable data, offering an even clearer view of what’s going on at the job site.
Keep Track of Work Output
To effectively measure and maintain productivity, it’s very important to monitor your daily work output.
This involves establishing key milestones (like foundation pouring or roofing), assigning specific amounts of work to each milestone (such as specific square footage installed or cubic meters poured), and then comparing the actual output to your planned targets.
This allows you to easily identify bottlenecks and make necessary adjustments to keep your project on track.
If this seems like a lot of work, worry not.
Using daily logs or reports can aid in this process by documenting all work completed, ensuring transparency, and serving as a reliable single source of truth.
Daily logs typically include details like:
- Personnel involved
- Weather conditions
- Activities by the prime contractor and subcontractors
- Unexpected delays or problems
- Drawings
- Photos
By keeping such a detailed record of the tasks completed each day, including the type of work, the quantity accomplished, and the time spent on each activity, you’ll be much better equipped to spot trends, patterns, as well as issues in the making.
Remember, without vigilant monitoring of work output, it’s far more likely for your team to lose sight of their targets and for productivity to plummet.
But if you keep your eye on the work being done, you’ll avoid any surprises and unexpected delays going forward.
Monitor Equipment Usage
Measuring and optimizing productivity on job sites isn’t just about keeping an eye on your workers but also about ensuring your equipment is pulling its weight.
If you don’t properly monitor your machinery, including its locations, downtime, or operational hours, you essentially open the door to a myriad of potential setbacks, gradually eroding overall productivity.
Russ Young, Chief Business Development Officer at Tenna, underscores this point with an example:
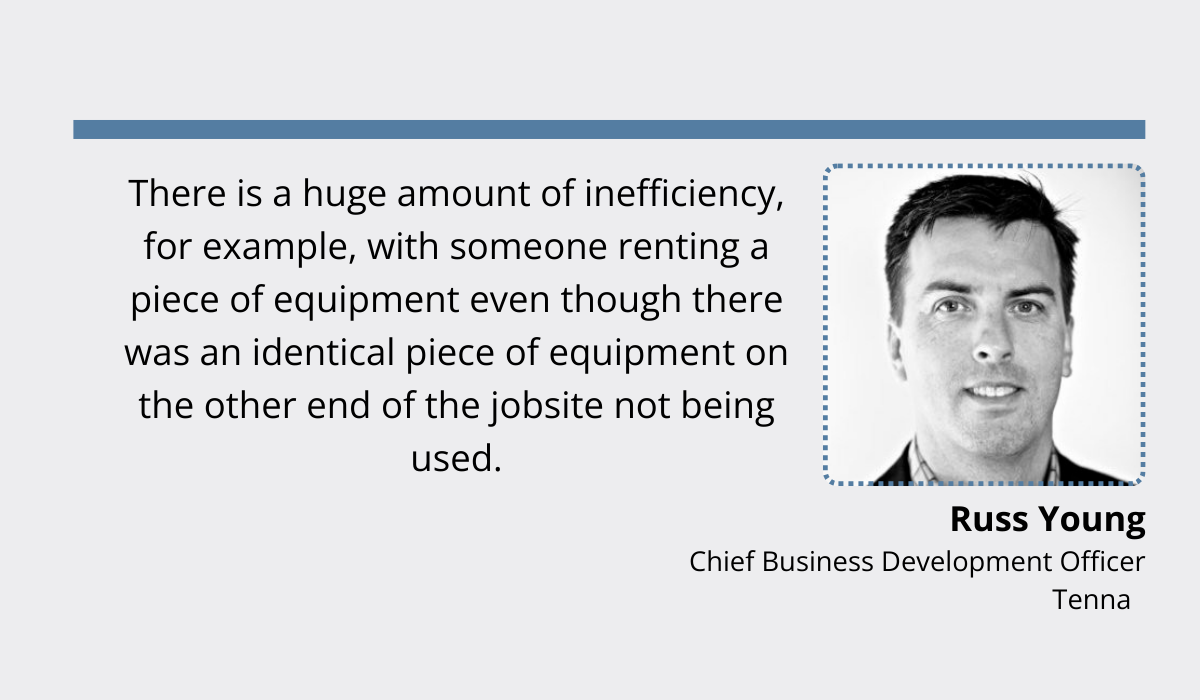
That’s right, without asset monitoring, you have no way of knowing how, or even if, your machines are being used.
This blind spot, in turn, leads to poor equipment procurement decisions or inadequate resource allocation across projects, ultimately impacting both your productivity and bottom line.
Fortunately, there are now digital solutions available that were developed precisely to mitigate such risks.
One such solution is GoCodes Asset Tracking, which integrates cloud-based asset management with real-time GPS trackers to provide you with only the freshest and the most detailed information on your equipment’s utilization.
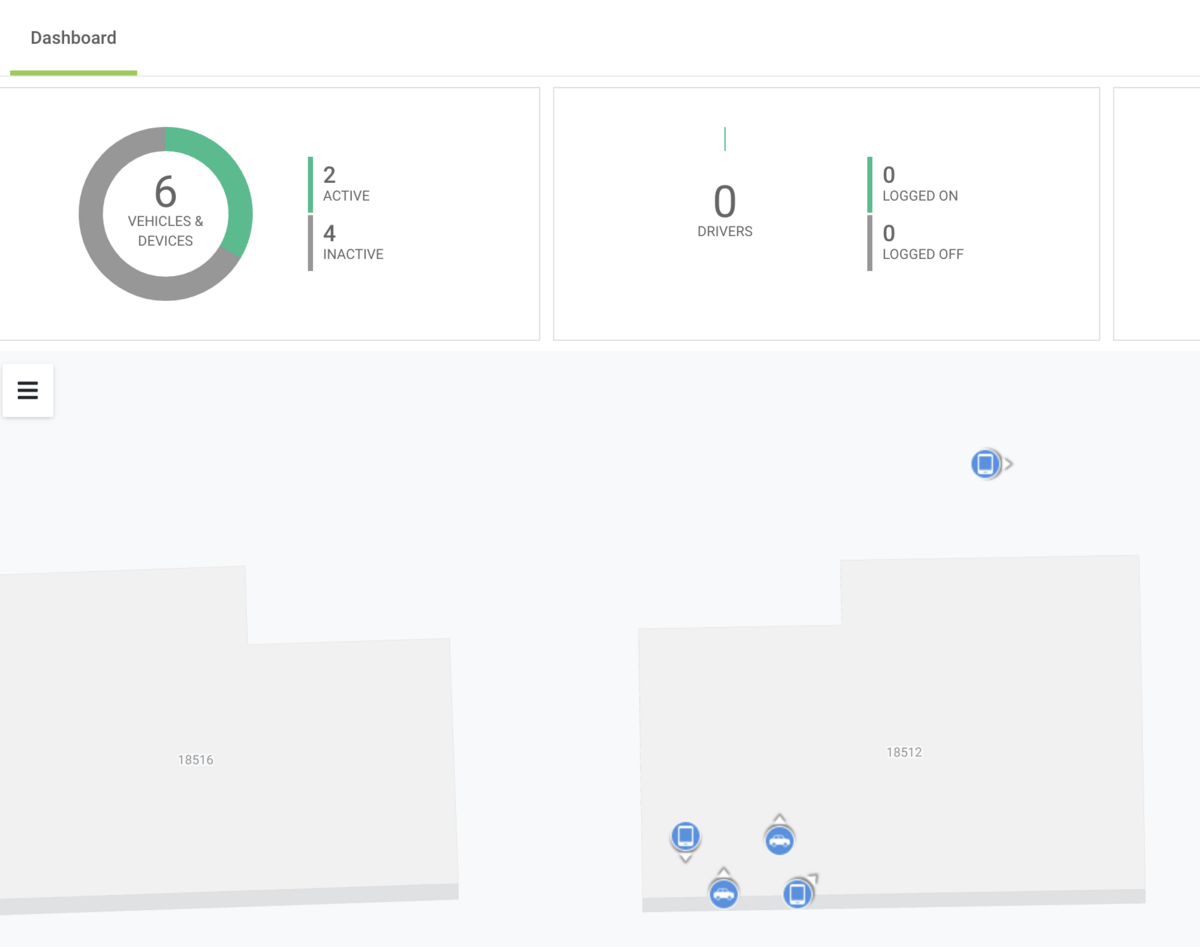
Once you attach the tracking devices, which you can see below, to your machines and vehicles, they start transmitting minute-by-minute data on asset location, speed, engine hours, acceleration, hard braking, and more.
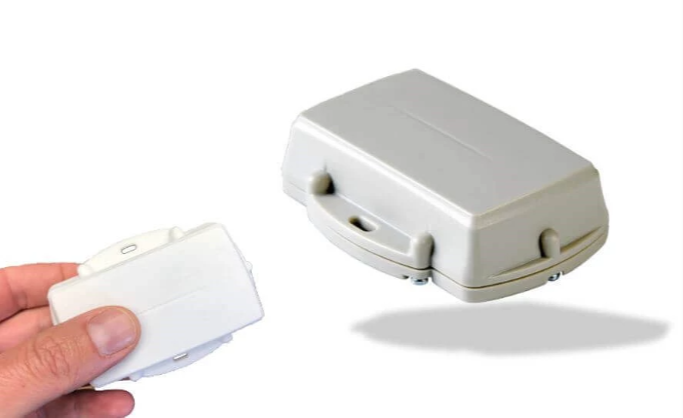
That way, you always know exactly where they are, how they are used, by whom, and for what project.
Besides, this rich data also helps you spot common productivity killers such as equipment hoarding, or unscheduled downtime, and nip them in the bud.
In other words, diligent asset monitoring isn’t just about ensuring resource availability—it’s about extracting maximum productivity from every machine in your arsenal.
And with the right tools and insights at your disposal, you can ensure that your assets are always in the right place, at the right time, ready to deliver peak performance whenever and wherever they’re needed most.
Conclusion
Hopefully, this article has demystified the process of measuring productivity, making it feel much less daunting.
Yes, it involves gathering and analyzing a variety of project data, but with the right tools and documentation processes, you can easily do that without breaking a sweat.
And once you have the data, don’t forget to compare it to your baselines to see if you’re hitting your targets.
Remember, this process is more than just a routine task—it’s the key to prompt risk mitigation, informed decision-making, and skyrocketing productivity.