Key Takeaways:
- The construction industry is loaded with a lot of preventable risks.
- Construction site theft is creating significant financial drains for companies with inadequate security measures.
- Preventing contract-related risks requires thorough reviews of key terms, but also ongoing and open communication.
- Meeting quality standards rests on identifying risks in the execution phase.
In an industry where one mishap, one unreviewed contract provision, or one storm event can create huge, costly problems, managing risks becomes a priority.
Without thorough risk assessments, effective contingency plans, and constant vigilance, construction companies can’t hope to survive, let alone turn a profit.
If you’re wondering about how effective construction risk management can benefit your company, you’ve come to the right place.
In this article, we’ll be breaking down six key benefits of proactive risk mitigation, so let’s get to it!
In this article...
Improves Safety On the Construction Site
Identifying and addressing construction risks benefits the overall on-site safety.
The construction industry is rightfully considered one of the most dangerous industries to work in the US and globally, and the statistics confirm this year after year.
According to a recent Center for Construction Research and Training (CPWR) report, 19.9% of all 2022 fatal injuries occurred in construction.
Moreover, the number of injuries increased by 7.6% in just a year.
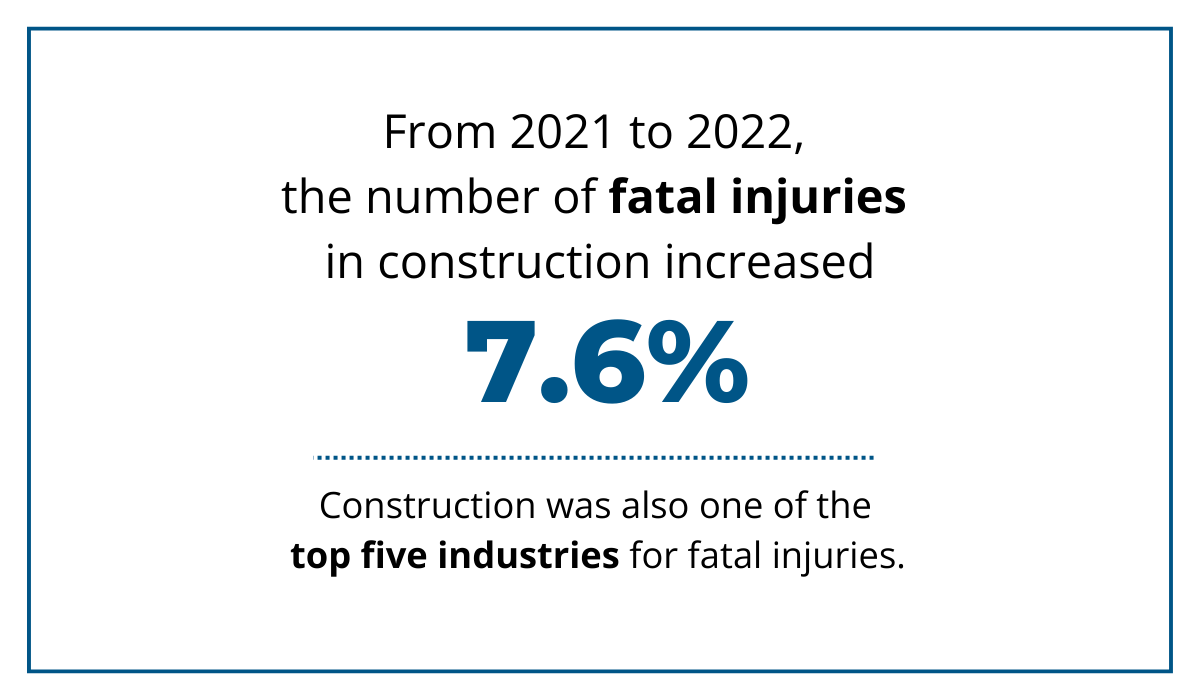
The recent figures reaffirmed the industry’s reputation, but what’s raising the alarm is the preventable nature of many of these injuries.
The data from the National Safety Council (NSC) shows that construction recorded the largest number of preventable fatal work injuries in 2022.
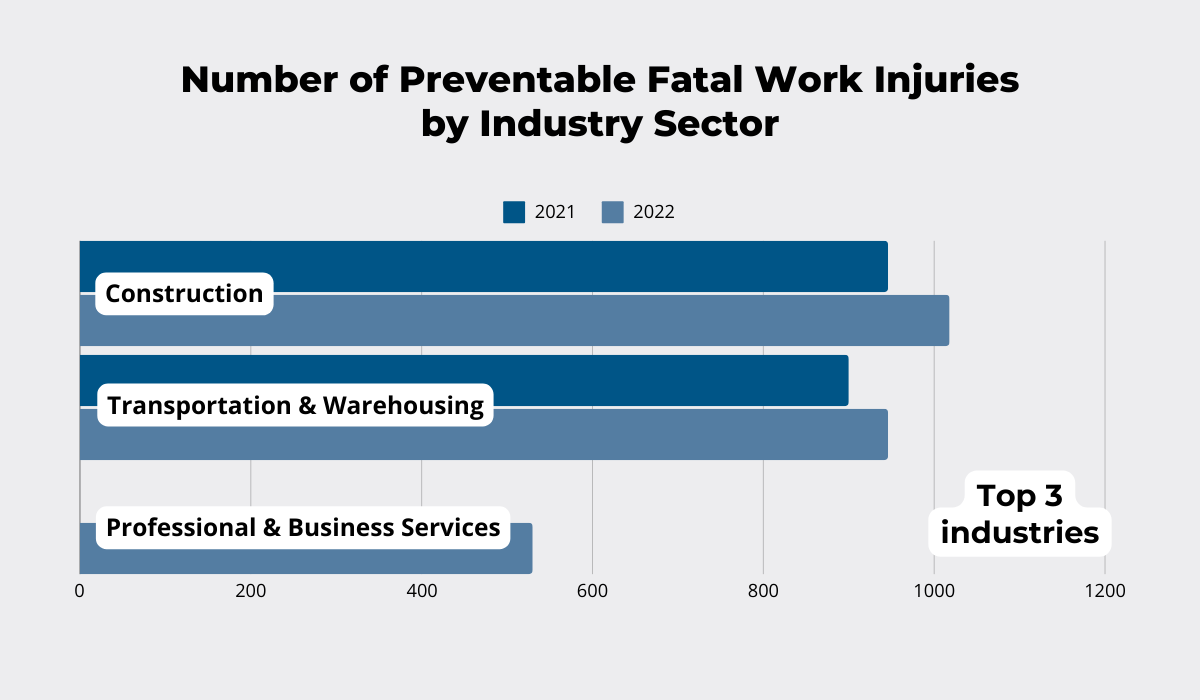
The data for the year prior is also telling, although NSC did not provide insights into the numbers for the service sector.
The high number of preventable fatal work injuries shows that construction companies must do better to manage risks proactively and adopt a more safety-oriented approach.
Creating a safety-first culture takes time and effort, but it begins by examining industry insights and your safety data.
Knowing which injuries occur most frequently, under what conditions, and which workers are particularly exposed to risks can guide your prevention efforts.
For example, the CPWR’s report revealed that “falls to a lower level” are the leading cause of fatal injuries, corresponding to the large number of roofers involved in on-site accidents.
So, one thing you can do immediately is review, improve, and talk about measures related to elevated work and fall protection.
Besides protecting workers’ lives, robust risk management helps prevent costly delays and additional repercussions of safety incidents, such as shutdowns and legal issues.
One recent example is a wrongful death lawsuit filed by the family of David O’Donnell, who lost his life in a fatal scaffolding collapse while working on the University of Chicago site.
The lawsuit against the contractor and subcontractor is based on two key circumstances: a faulty scaffold and the lack of safety precautions—since neither O’Donnell nor his critically injured coworker, Jeffrey Spyrka, wore any safety harnesses.
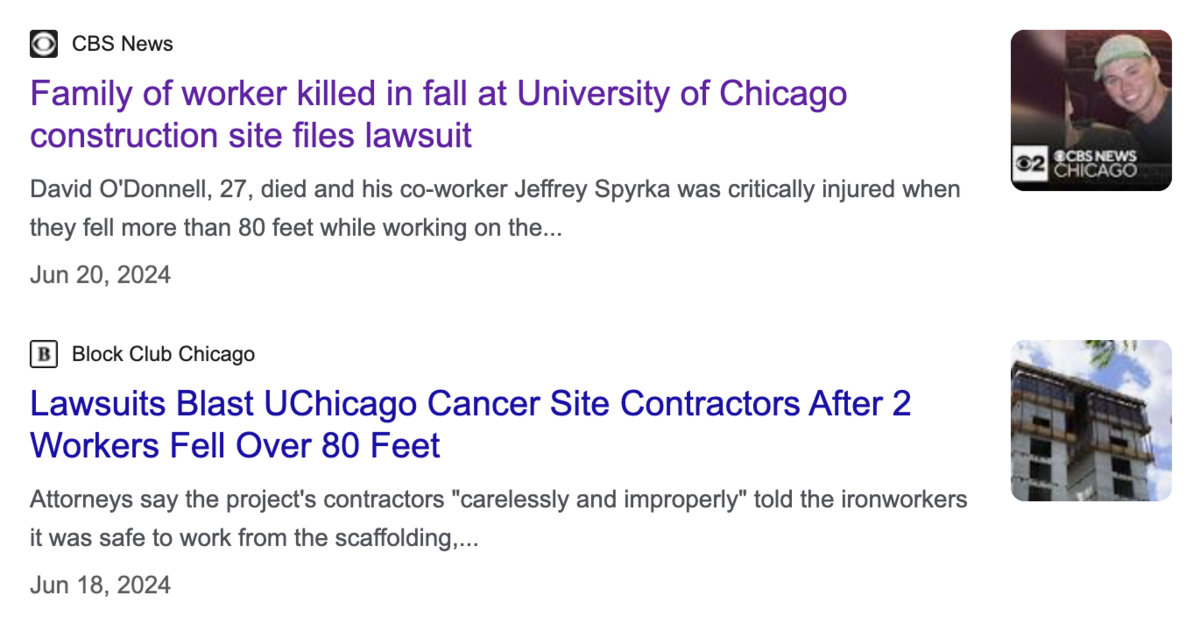
Besides legal actions taken by the affected parties and an OSHA investigation, the contractor Turner Construction and other parties are either facing or will most likely face:
- legal fees,
- potential fines,
- project delays, and
- reputational damage.
A lack of construction risk management can have a devastating effect on everyone involved in construction projects.
On the other hand, identifying risks and adopting safety measures accordingly protects all parties by enhancing overall safety.
Minimizes Financial Losses
You already saw how managing construction risks helps keep your finances in check by avoiding legal fees, but it goes beyond just that.
Proactive risk management protects both the contractor and the client from unexpected expenses, helping you avoid several financial pitfalls, including:
- cost overruns,
- contract disputes,
- design flaws,
- project delays, and
- theft.
By minimizing your financial losses through risk mitigation strategies, you’re ensuring that the project stays profitable and within budget.
Risk mitigation also helps construction companies deal with climate change.
Aon’s 2023 report explores the role of risk mitigation efforts in reducing the financial impact of climate change, which is recognized as one of the emerging issues for construction today.
In this report, Blanca Berruguete, Global Industry Solutions Director for insurance giant Allianz Commercial, identified climate change as a major industry challenge today, alongside ongoing supply chain disruptions and inflation.

At this point, it’s clear that the issue of recent and future catastrophic weather events will need to be addressed sooner rather than later.
However, the more immediate and widespread concern for many businesses is construction crime.
The survey conducted by the UK-based Chartered Institute of Building (CIOB) shows that 38% of respondents suffer a loss of at least £10,000 a year due to theft.
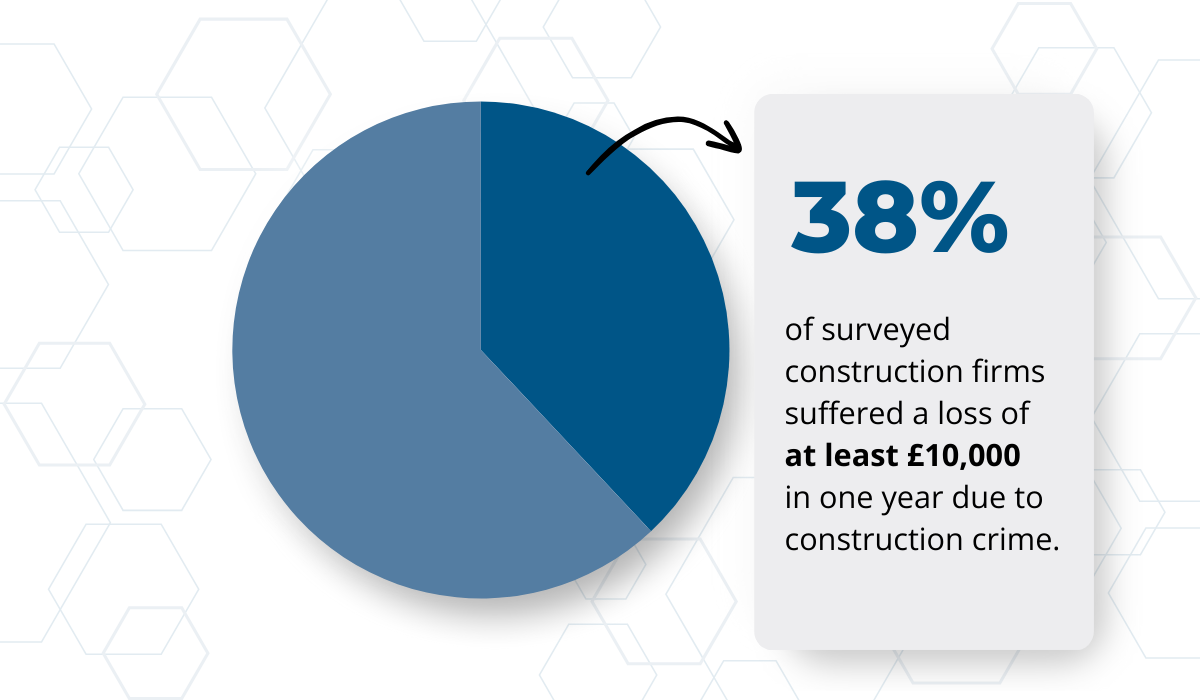
Meanwhile, 9% of companies lose over £100,000 a year, translating to roughly $130,700.
Whether it’s the petty thieves stealing power tools or more elaborate heists targeting valuable assets, one thing’s certain—enhancing construction site safety is no longer an option, but a necessity.
So, which measures are best for minimizing the risks of theft?
According to the CIOB’s findings, enhanced lighting and secure storage are the most popular options, with the majority of companies also identifying asset tracking as a highly effective solution.
Asset tracking systems come in many different flavors, offering either individual tracking devices or comprehensive solutions, such as our GoCodes.
With GoCodes’ cloud-based software, you’ll be ready to finally ditch spreadsheets or slow on-premise systems, and replace it with a centralized, easily updated database of your entire inventory.
The combination of real-time GPS tracking, scanner apps, and other tracking methods enables you to keep a watchful eye on all your tools and key machinery, no matter where they’re located.
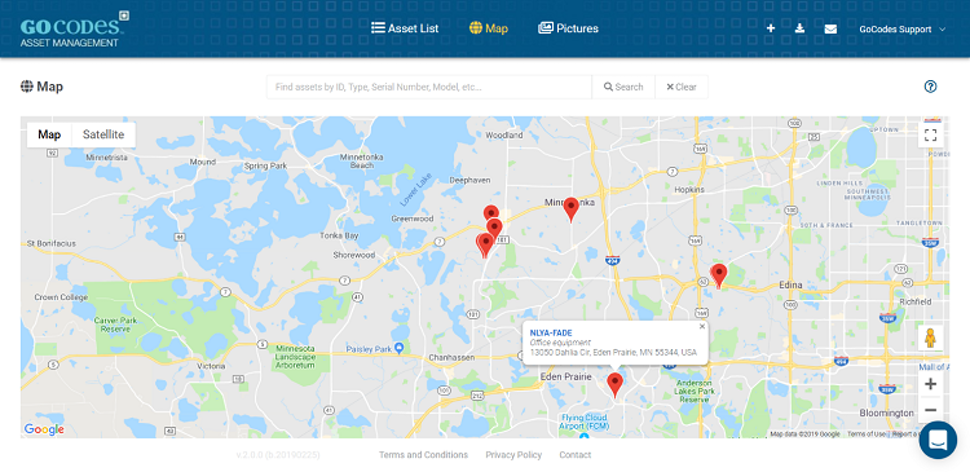
Real-time monitoring increases assets’ on-site visibility, but the true theft deterrent in this case is the integrated geofencing system.
Once implemented on your construction site, geofencing expands asset tracking capabilities by allowing you to draw virtual boundaries around entire areas or individual assets.
Any movement beyond the established perimeter immediately triggers an alert.
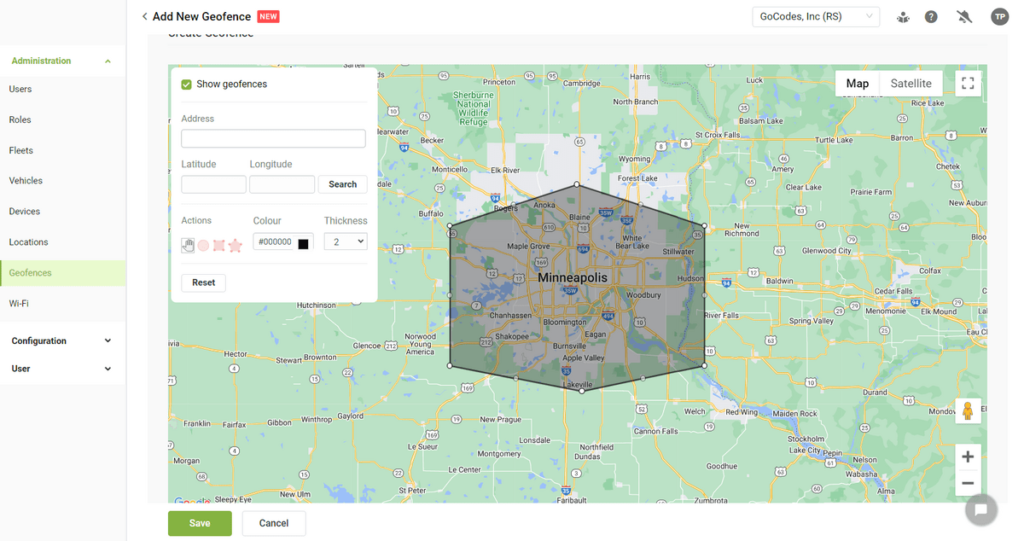
The ability to identify and address unauthorized movement or potential theft in real-time also increases the chances of asset retrieval.
As a bonus, the bulk of asset data you collect through geofencing can be used to unlock several benefits, including improved maintenance and productivity, to reduce financial losses further.
To summarize, risk mitigation is paramount for the financial health of construction companies in more ways than one.
Ensures Projects Stay On Track
For your business to grow, profitability and timely completion of projects are imperative.
There are a couple of obstacles in the way, however, from supply chain issues to ongoing labor shortages.
With volatility becoming the industry norm, construction companies need to be more vigilant and proactive in addressing risks that could disrupt timelines.
KPMG’s findings show that poor risk management caused 40% of engineering & construction companies to experience either schedule delays or cost impact in 2023.
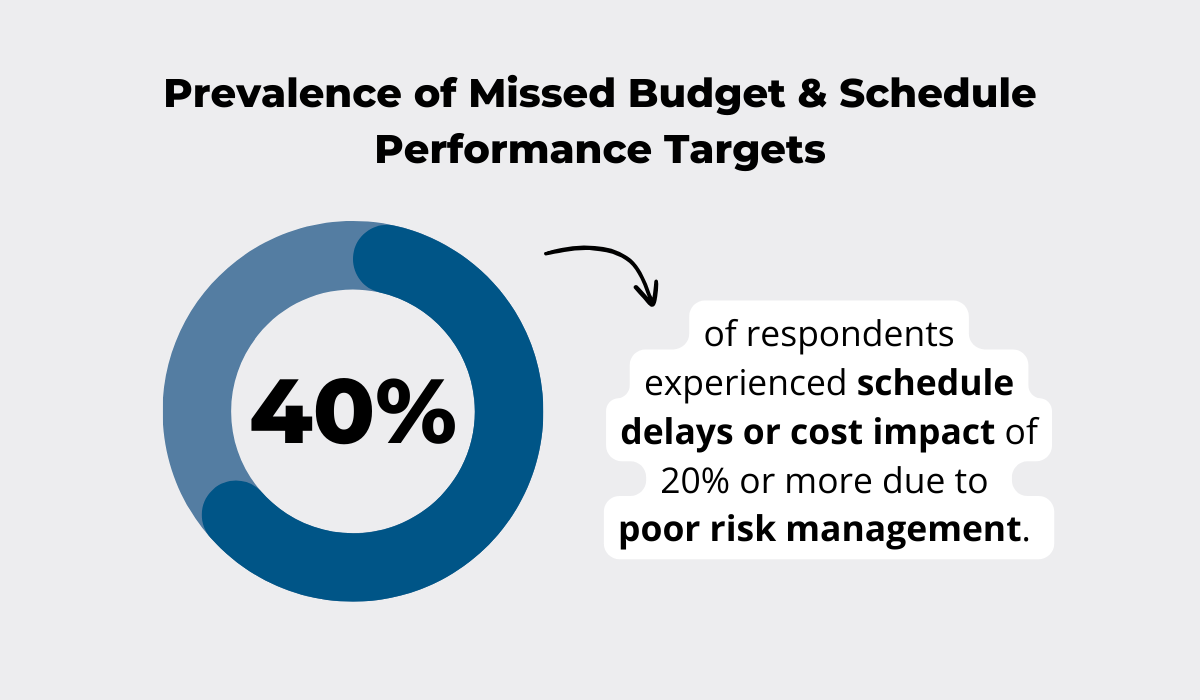
What’s more, this is a notable increase compared to 2021 when 31% of firms were affected.
Recent statistics on managing construction projects highlight complexities that have made risk management pivotal in avoiding cost overruns and delays.
Simply put, there are no alternatives for effective risk mitigation.
Developing robust risk management strategies and appointing chief risk officers are part of the overall approach, but the starting point is initial risk identification.
Only once you’ve mapped potential construction risks can you assess which methods to employ, and which risk mitigation technologies and staff training you need.
Recent reports on a new megaproject suggest that a lack of proper planning from the outset created risks that already threaten its future.
The work on the Frederick Douglass Tunnel (FDT) project, valued at about $6 billion, is a huge undertaking in every sense of the word.
However, insufficient or inadequate planning immediately carries the risk of cost overruns and delays, and that’s exactly what happened according to the the project owner’s Office of the Inspector General (OIG).
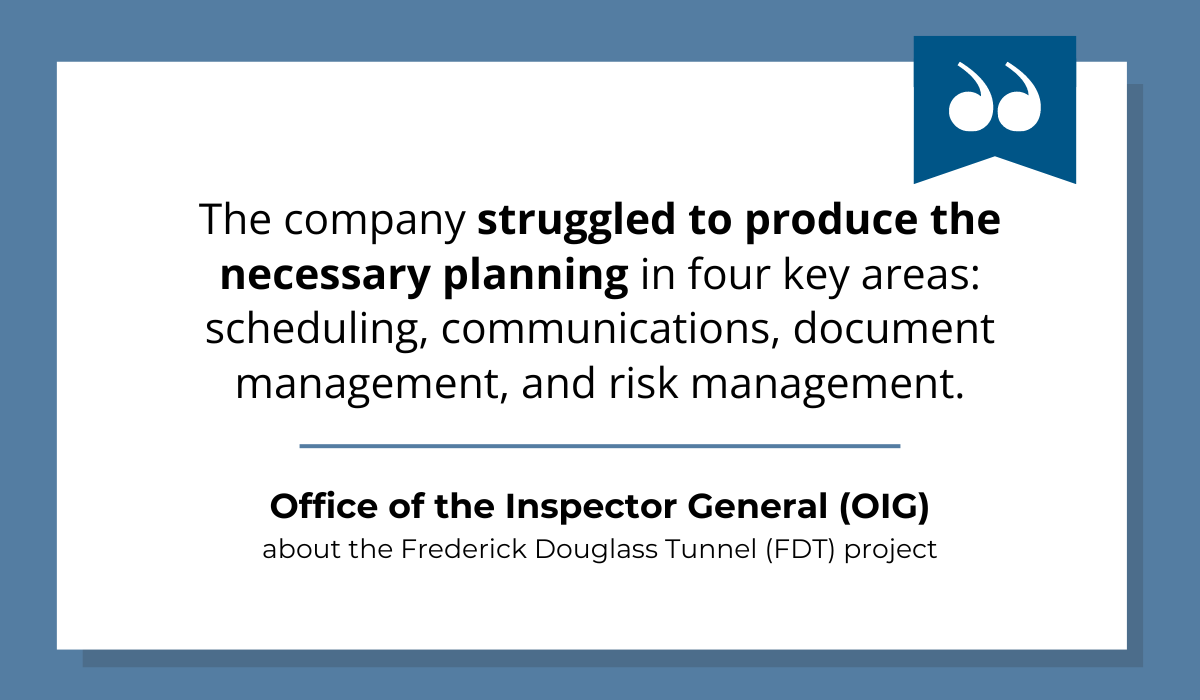
With the completion date set for 2035, there is still room to make improvements and mitigate some of the risks, but it will take considerable effort.
To sum up, if you want to minimize the risk of seeing your projects derailed, start working on comprehensive risk management strategies from day one.
Improves Contractual Compliance
Effective risk management helps companies identify and address risks preventing them from meeting their contractual obligations.
Contractual risks concern project timelines and scope, and tend to incur additional costs in situations where the company hasn’t carefully considered major risk areas.
Beyond scope and scheduling, these key areas include potential payment disputes, design and specification issues, as well as safety risks.
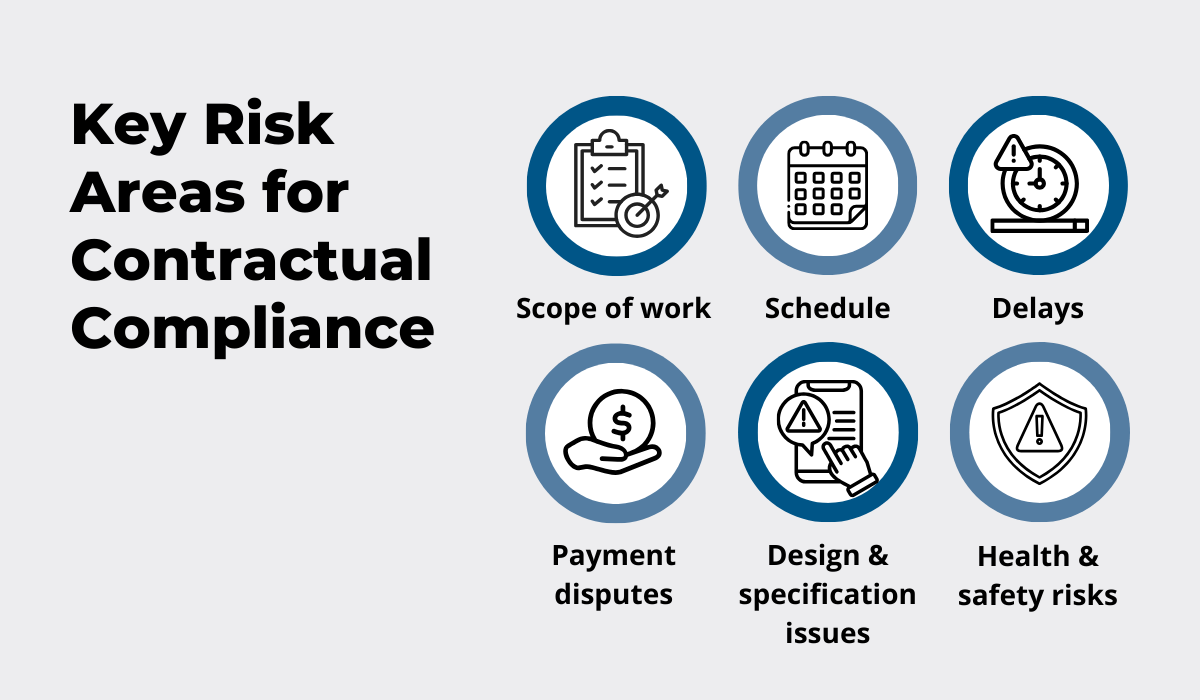
To avoid these risks, carefully review and negotiate the terms of the contract before it’s signed.
Keep in mind that every contract should offer clarity by:
- outlining the scope of work in detail,
- defining a clear payment schedule, and
- including provisions for handling delays, disputes, and any changes.
By defining and addressing these and other areas, you will get a well-made contract that enables you to effectively deal with unforeseen circumstances while protecting all parties.
Taking extra time with this means fewer breaches and resulting legal disputes and penalties.
Most importantly, it keeps the relationship with clients intact.
Lack of proper risk management is one of the most common causes of disputes within the construction industry.
Of course, setting and observing contract terms of the contract is just one part of the equation.
The other is active and open communication, as explained by Aubrey Phillibert, expert in real estate and construction management.
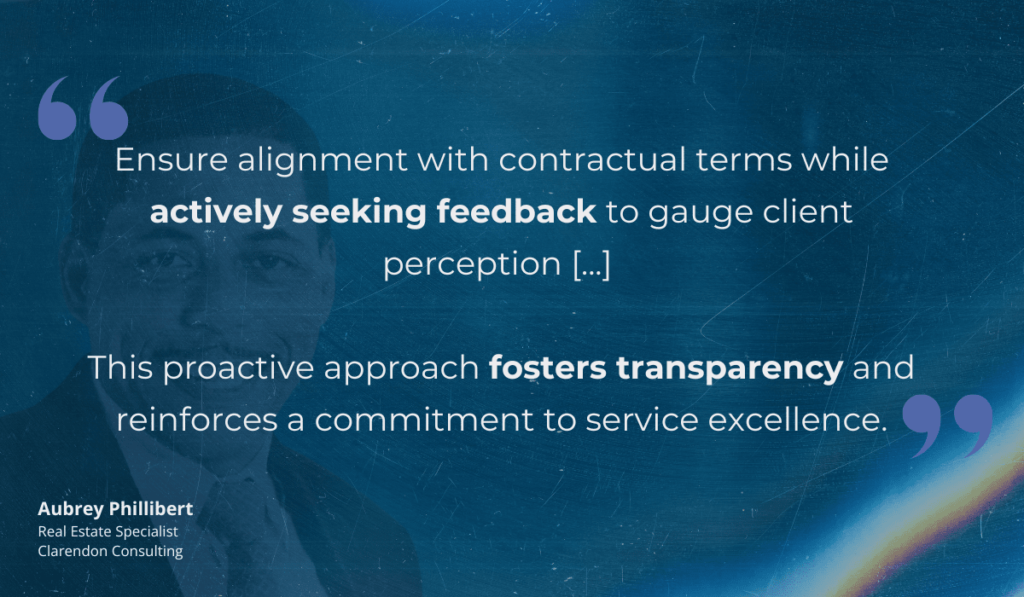
Risk assessment and mitigation are a part of quality contract management, and after the initial defining of terms, it’s important to keep communication lines open and re-evaluate risks together.
In this way, you can promptly address risks as they arise, thereby ensuring compliance and building enduring client relationships.
Allows You to Meet Quality Standards
Managing construction risks proactively paves the way to meeting quality standards.
And meeting quality standards from the get-go means avoiding construction rework.
Several older studies point to steep rework costs, with the 2012 Navigant Construction report analyzing historical data to place the median cost of an average construction project at 9.07%.
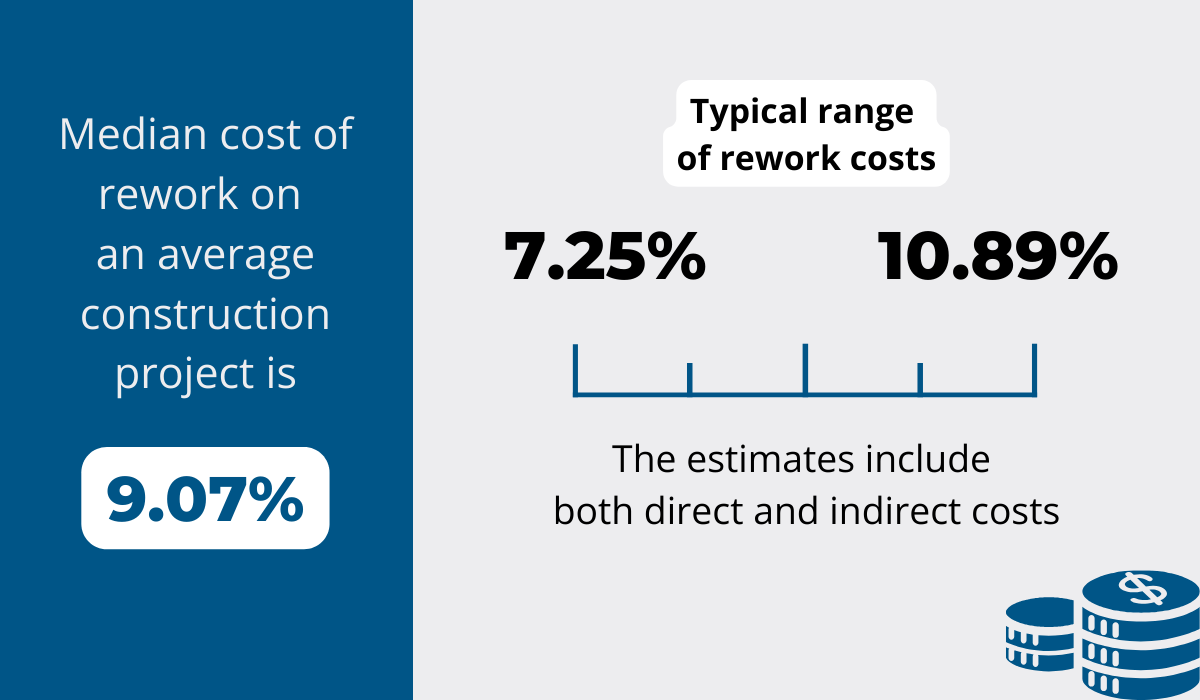
In other words, a construction project with a budget of 1 million dollars would most likely be looking at rework costs of $90,000.
The report also accounted for indirect financial expenses which can be difficult to measure, and one such example is company reputation.
One recent example of this is the case of Cy Porter, a certified home inspector who specializes in new home construction, and actively exposes flaws in these homes on social media.
One of the companies that felt called out in these videos was Taylor Morrison, which led to them filing a complaint for unprofessional conduct against Porter, putting his license on the line.
Ultimately, the Arizona Board of Technical Registration found no “specific violations of conduct” or fabrications as Taylor Morrison claimed, and didn’t discipline Porter.
The moral of the story?
Paying attention to quality will help you avoid negative publicity and unwanted media exposure in the first place.
The risk management practices you employ to ensure quality aim to eliminate rework.
The root causes of rework vary, from design phase mistakes and using low-quality materials to miscommunication that seems to be behind 52% of all rework.
Fortunately, by paying attention during execution you can catch mistakes and avoid costlier scenarios.
For starters, project managers should properly assess and carefully choose subcontractors and consultants by digging into their:
- financial stability,
- safety certification
- safety records, and
- past project performance.
Jesse Lane, a growth expert for construction businesses and the founder of several companies, advises to ask questions that ensure both reliability and agility.
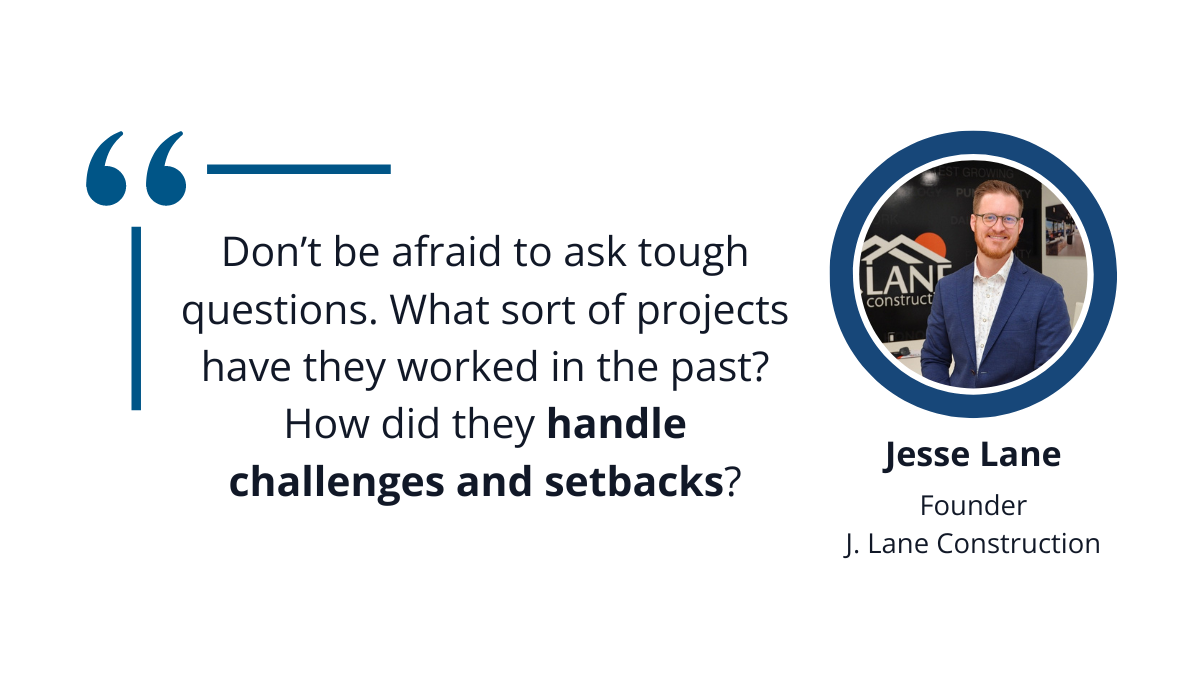
Of course, no matter the perceived quality of subcontractors, you still need to conduct regular quality audits and inspections.
Your workflows must include frequent checks on material quality and workmanship, especially at key milestones and specific construction phases, such as framing.
For example, checking for poor insulation can help prevent costly rework due to potential energy inefficiencies or structural damage.
Ultimately, proactive risk management reduces the financial and additional costs of failing to meet quality standards.
Provides a Competitive Advantage
Mitigating risks and delivering projects on time, within budget, and with high quality makes your company stand out.
From attracting more clients to improving profitability and market position, the advantages just keep adding up.
A 2013 study also pinpointed some less visible benefits of effectively managing construction risks, such as discouraging intentional harm or fraudulent attempts simply by maintaining an image of resilience and agility.
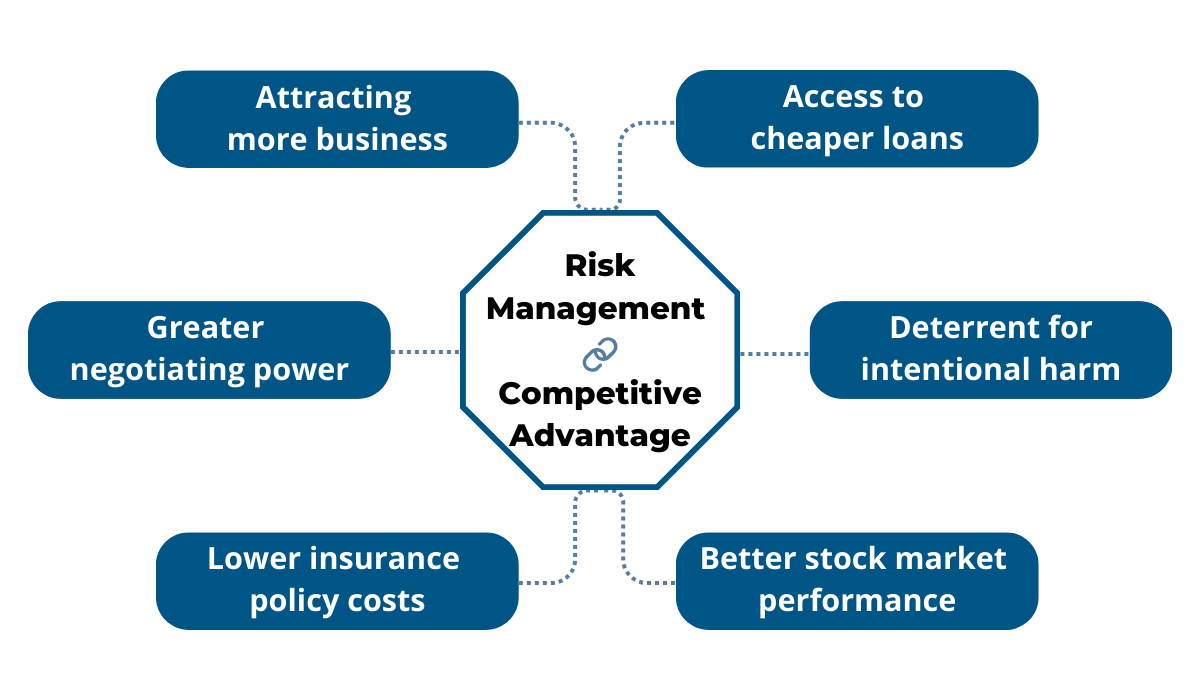
One surefire way of managing risk and gaining competitive advantage is to stay up to speed with relevant trends and technologies.
For instance, you can read the Construction Industry Institute (CII), which provides access to a robust knowledge base on various topics, including risk management.
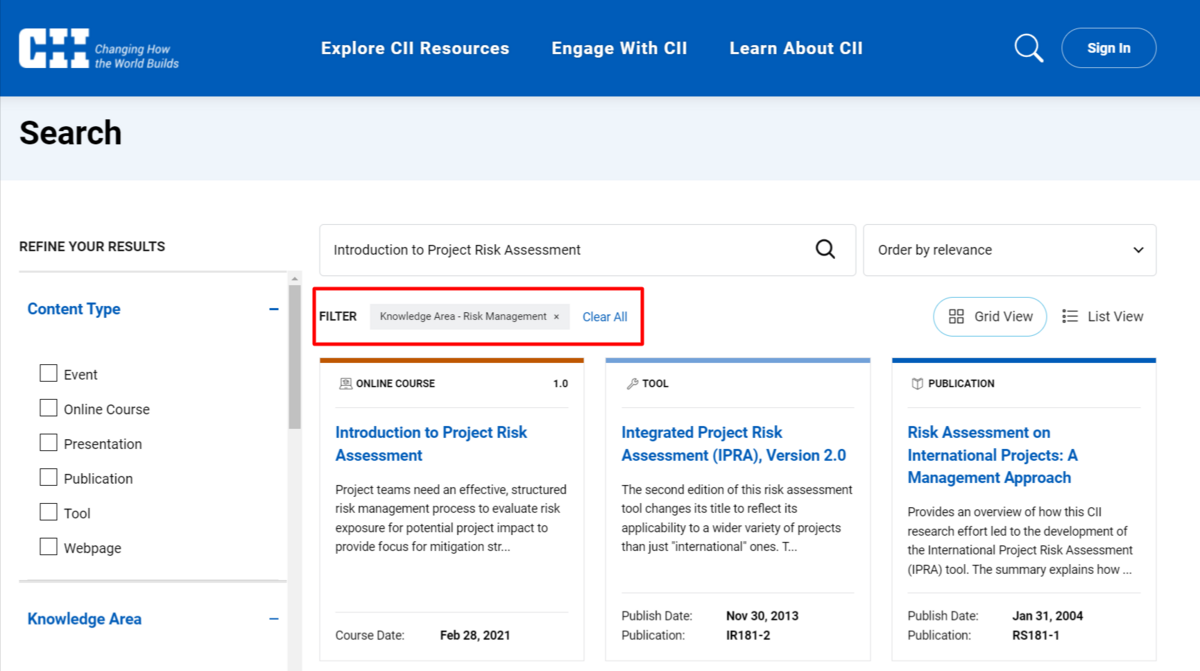
Besides examining different resources compiled by industry experts, leveraging advanced technology is sure to propel you ahead.
Today, there are different kinds of essential risk management technologies such as BMI tools, construction wearables, and collaboration platforms.
In addition to that, having a centralized database and collaboration platform helps a lot.
It reduces miscommunication by keeping everyone aligned about project deliverables and specifications.
Then all parties stay in the loop, no matter when and how often the changes occur.
This is particularly important when it comes to communicating potential risks across the board.
However, competitive advantage is usually mentioned in the context of predictive analytics.
In a segment centered around AI and machine learning, Josh Kanner explains the impact of technology that analyzes historical data, identifies trends, and predicts crucial outcomes for businesses.
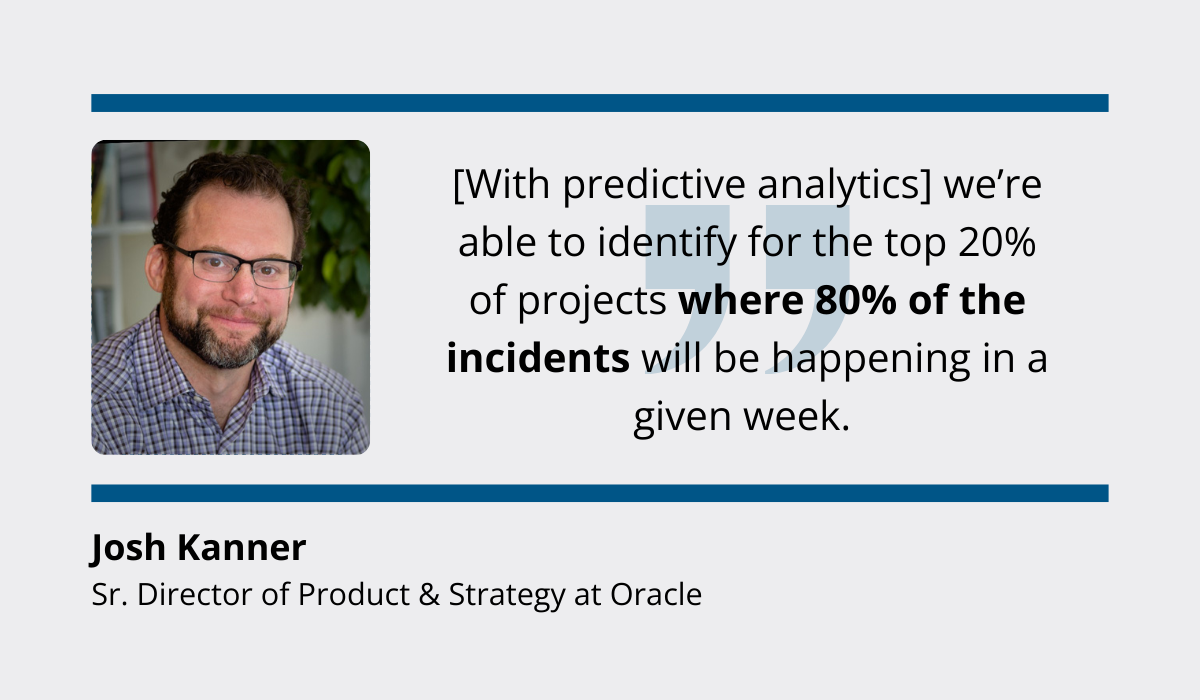
Kanner founded Newmetrix, which was later acquired by Oracle, to reduce jobsite risk through construction-trained AI.
Of course, the ability to predict where to turn your attention and what the best course of action is goes beyond construction safety and can aid businesses in multiple ways.
As you can see, gaining an advantage over the competition depends on many factors, but it often begins by anticipating risks and staying ahead of the curve.
Conclusion
For construction professionals, working on projects usually means dealing with one challenge after another.
Some of these challenges can be seen from afar, but what about concealed dangers and emerging risks?
To deal with them, companies must expand their capacity for dealing with change.
The best course of action is to invest in construction risk management.
The several benefits we examined today make it all worthwhile.