Equipment maintenance is a must for any company that deals with numerous assets.
You have to know what condition your equipment is in to avoid any kind of injuries or risks in the workplace—and you can do that through maintenance.
But how do you ensure safety for your maintenance team?
We’ll explain what risks your upkeep team faces daily and how to structure your maintenance process. You’ll also find tips on improving safety during equipment care.
Follow this advice to make sure your maintenance team is safe.
In this article...
What Are the Maintenance Safety Risks?
If you are trying to eliminate maintenance safety risks, you have to learn what they are first.
Did you know that maintenance workers are the 6th most commonly injured group of workers in the US?
This fact might not be as surprising if you consider the nature of their job.
Upkeep employees often work under unfavorable weather conditions, handle malfunctioning machinery that can hurt them, and can even suffer injuries due to making repetitive motions.
On top of that, your maintenance team gets exposed to the following hazards:
- asbestos when they’re doing the upkeep of old buildings or installations
- biological hazards such as mold
- skin and respiratory diseases caused by the substances they use for maintenance
- risk of electrocution
Remember that such employees work with different pieces of equipment, from small assets to buildings. This variety makes it difficult to keep track of every possible hazard. And yet, the law requires you to do it.
For example, your workers might deal primarily with equipment maintenance, but they also might be in charge of handling your gas, electricity, and water issues while simultaneously controlling your power grids.
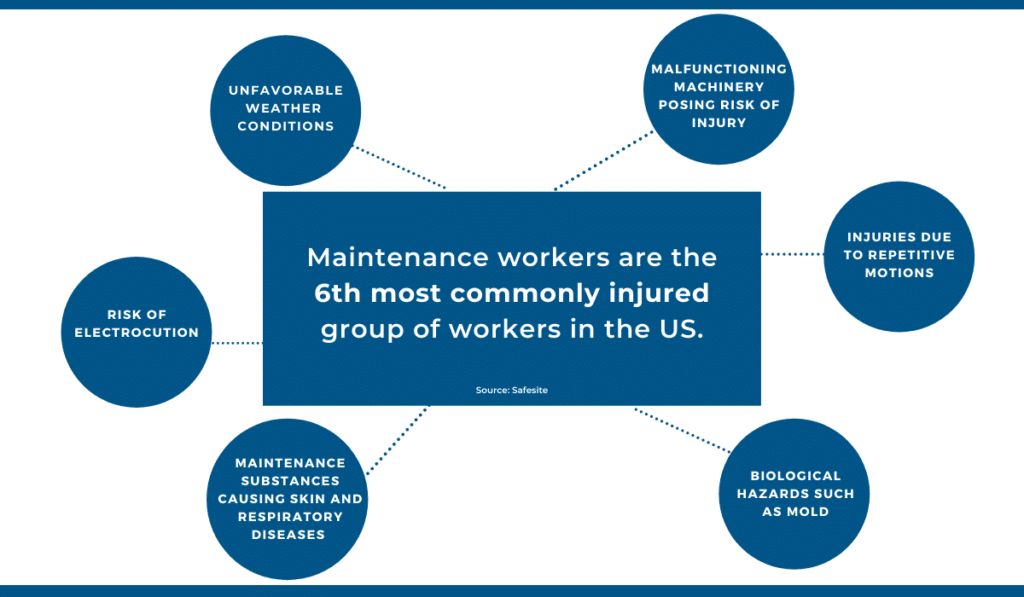
Use the following six maintenance steps to protect your workers from safety risks. They will help you cover each upkeep activity and prepare for potential hazards.
The Five Steps to Safe Maintenance
The upkeep process doesn’t start when an asset breaks down, and your team needs to step in and fix it. On the contrary, it begins before the malfunction occurs.
Before embarking on any repairs, you should have a maintenance plan, ensure upkeep safety, and make sure that you have the appropriate equipment.
During the process, your team needs to follow safe work practices, and after it, they need to check the current condition of the asset before returning it to the field.
Let’s explain these steps in detail to make your maintenance process as safe as possible for everyone involved!
Maintenance Planning
The key to safe maintenance lies in detailed planning.
Planning is at the root of all safety practices as it helps you determine maintenance stages and all the steps your team needs to take to stay safe from potential hazards.
The planning phase has to cover these steps for each upkeep activity:
- Scope: what does the task include, how long will it take, and what are its effects on other teams and activities?
- Hazards: identifying all possible risks during the activity, such as the heights at which a task will be done, the hazardous substances, moving parts, and heavy lifting it may involve, etc.
- Responsibilities: deciding who will take part in the task, what roles and skills are needed, assigning duties and managers
- Necessities: listing all the equipment and personal protective equipment (PPE) needed to perform the task
- Safe access: ensuring secure entry and exit from the maintenance zone in case of an emergency
- Training and safety knowledge: understanding the degree of expertise necessary to perform the task; determining communication channels for reporting issues
The list might seem like a lot to cover, but don’t worry; you don’t have to do it on your own! Ask the workers to help you plan the maintenance of each asset group.
After all, their knowledge of the matter is first-hand and based on years of experience in the field. Therefore, consult the maintenance team to create a bulletproof safety plan!
Ensuring a Safe Environment for Maintenance
After you identify all possible safety threats, you have to remove them.
It’s not enough to know what safety hazards exist in your workplace—you have to remove or minimize them. That way, you’ll guarantee a safe working environment for your maintenance team. If you skip this step, you’re putting your workers at a very high risk of workplace injury.
How can you get rid of risks?
First, invest in a job hazard analysis (JHA). It identifies not only the hazards but the circumstances or conditions leading to them.
In that case, you’ll be able to find the root cause of any issue and remove the risk before it poses a real threat.
What to do if you can’t fix the issue?
It’s simple. Make workers aware of the problem and take all the necessary precautions to prevent injuries.
Your maintenance workers need training to recognize the type of equipment and the amount of energy a particular piece generates, the threats it poses, and ways of controlling them.
Without adequate training, the risks multiply.
Additionally, keep the area clean and organized as this eliminates the risk of accidental falls or injuries.
If you want to prevent accidents, create and maintain a safe working area for your upkeep team.
Providing Adequate Equipment for Maintenance
Before starting maintenance work, ensure that every worker has adequate equipment.
During the planning phase, you identified all the tools and PPE necessary for your worker to perform their job safely and effectively. Now it’s time to provide the equipment to each employee and make sure they use it.
A supervisor on the scene can assist you in these checks to ensure that no one operates the wrong equipment or neglects to wear PPE. Both of these actions pose serious dangers for the worker and their colleagues.
Some of the obligatory PPE includes:
- hard hats
- gloves
- steel-toed shoes
- eye protection
- face protection
Of course, the tools, equipment, and PPE depend on the type of machinery in need of maintenance. Make a plan for each asset group and detail the tools required for upkeep.
If you want to go a step further, provide instructions and manuals for the necessary tools. Then, each employee can find an answer to their question or understand the proper use of the item at hand.
Always provide tools and equipment needed to perform maintenance safely.
Following Safe Work Practices
Your work doesn’t end with providing access to the right equipment—your employees now need to follow safe work practices!
When things are going great, it’s easy to stick to the plan.
However, as soon as problems arise and you run into a delay, some employees might want to skip a step or two to get the job done ASAP.
Bear in mind that any skipped step poses a considerable safety threat to your maintenance team.
On top of that, taking shortcuts can lead to further damage to the machinery and extra costs.
What does this mean for you?
It’s up to you to teach the employees the importance of each step. Get them to understand the consequences of skipping a single one.
Don’t rely on everyone taking your words to heart, though. Instead, appoint supervisors for each activity. They will inspect and determine whether your team is following the steps. If something is not going right, supervisors can stop the task until the issues are fixed.
Even if a supervisor is not present, your maintenance team should be able to recognize particular issues. When that happens, the team needs to stop working and notify the supervisor or the manager.
It’s up to you to impart the importance of doing so to your employees.
Final Checks
The last step towards safe maintenance is a final equipment check.
Once the maintenance is over, your team needs to examine their work. The checks, however, shouldn’t only refer to whether the equipment is running smoothly.
Instead, they should determine the efficiency of the upkeep and workplace safety.
If your team fixes the asset but leaves the tools or waste material lying around, that means they didn’t pass muster. The person inspecting the workplace should ask the team to clean up and organize the tools before marking the work as complete.
The maintenance task is over only after the machinery is ready to use, the tools are organized, and the workplace is clean and safe.
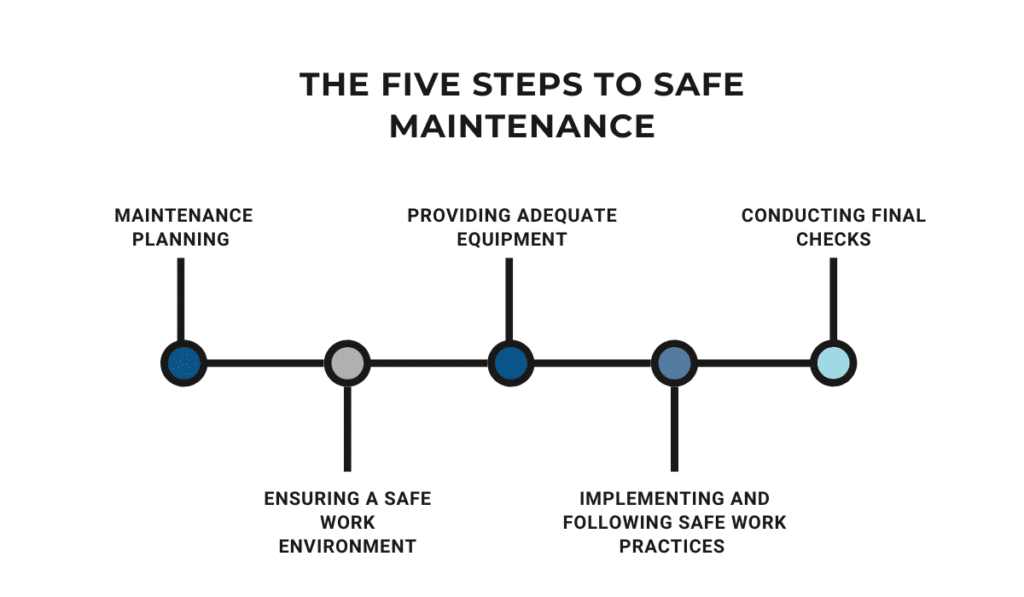
After the final check, your team should write an upkeep report covering every step of the process. On top of describing the work, the upkeep staff should explain the encountered issues. If possible, they should also make recommendations for future maintenance.
How to Improve Your Maintenance Safety?
Sadly, accidents can happen despite all the necessary precautions.
While some things are out of your control, there are many aspects you can regulate. Remember—practice makes perfect!
Let’s find out which steps you can take to improve the safety of your maintenance team.
Train Your Team
Teach your employees how to keep themselves and others safe during maintenance.
This advice might sound self-explanatory, but it is at the top of this list for a reason.
If you train your employees well, you leave virtually no room for human error. After training, the team should be able to recognize and report potential threats and know how to deal with them effectively.
Here are some of the basic areas your training should cover:
- the use of maintenance tools and equipment
- how to conduct repairs on the equipment
- a detailed understanding of the maintenance plan for each piece of machinery
- standard health and safety practices
- awareness of the workplace and machine-related hazards
- OSHA safety standards
A lot more goes into this training than you expected, right? However, it’s for a good reason. Remember that accidents in the workplace are on the rise, and your maintenance team faces different risks.
Train, train, train—it’s the key to having an expert team!
Perform Regular Preventive Maintenance
Don’t wait for something to break to fix it!
Preventive maintenance is the industry’s way to go. Finding and fixing minor issues as they appear helps prevent larger equipment malfunctions.
With preventive maintenance, your team regularly inspects a functioning asset, following the same steps during every session.
You can help them out by creating maintenance checklists. First, consult the experts and define what actions are obligatory for upkeep. Then, write them down, and repeat the process for every tool your team maintains.
Decide if your list should work on a step-by-step or a pass-or-fail principle. Don’t forget to teach each employee how to fill out the checklists and be diligent about each step.

On top of that, you can find a way to schedule regular maintenance for each piece of equipment. That way, you can guarantee that you never miss an upkeep date and keep all your tools under control.
Also, don’t forget to record each maintenance session.
Keep Maintenance Logs
Documenting your asset details leads to safer maintenance.
Think about it—the more equipment information you have, the easier it is to detect issues or reasons for concern. Besides, this data helps your team determine the cause of the malfunction and the asset’s weak points.
Start by writing down the essential details when buying new equipment.
Don’t forget to include:
- warranties
- insurance
- price
- depreciation
Then, whenever an asset breaks down or goes through scheduled maintenance, add a new record. That way, your maintenance team will always have access to current information about the asset.
The records should include details on the maintenance, possible future issues, and concerning points, as well as the issues your team managed to fix.
If you use software that lets you have an equipment database, attach all the logs to the asset’s page, allowing anyone who accesses it to see all the relevant data.
Giving your team an overview of past maintenance logs helps them work safer.
Plan for the Worst
What will your team do when the worst happens?
If you don’t know the answer to that question, your training wasn’t adequate. After all, preparing your team for any potentially dangerous eventuality is a big part of onboarding.
Sadly, maintenance work comes with its risks, so your upkeep team needs this knowledge to stay safe on the job.
How can you prepare your team to face accidents?
Rehearse! Come up with possible scenarios and play them out to teach your employees how to react to a fire, flood, machinery accident, or injury. Include all maintenance employees in the exercise. Most importantly, repeat until everyone understands the steps.
When an accident does happen, look at it as a learning opportunity. Base a future exercise on the accident and rehearse it until your employees’ reactions become mechanical.
Whatever happens in the workplace, make sure your team knows how to handle the situation safely.
Get Feedback from Your Maintenance Team
Tap into your team’s potential and use their feedback to improve maintenance safety.
Companies rarely consult their workers despite them having first-hand experience, but that is a mistake. Especially if you consider that your team’s feedback can help you:
- improve current maintenance practices
- introduce new upkeep steps
- invest in higher-quality equipment
- spot the need for more employees or more assets
- recognize more hazards
Instead of ignoring your team’s opinion, consult them every step of the way for better overall results.
If you want to make sure your current processes are complete and helpful, simply ask your maintenance staff!
If your team has to take steps not covered on your checklists, it’s time to rewrite them.
Also, encourage employees to make suggestions or propose alternative solutions. After all, you never know how much time and resources you can save by opting for a different strategy.
When you want to improve upkeep safety, ask those with the most experience.
Promote and Ensure Easy Communication
Another step that ensures the safety of your maintenance practices is communication.
Often, your team spots issues on time, but they have no way to contact anyone in charge. Therefore, instead of waiting until they see the supervisor, the employees might continue working. In other instances, they might even make the wrong decisions on account of being unable to get in touch with a manager on time.
This may lead to workplace accidents, injuries, or fatalities.
If you want to prevent this, you have to promote effective communication!
Start by creating a communication channel. Establish an easy, accessible way for your maintenance staff to get into contact with other employees.
You can use software that allows users to upload comments and documents on the asset’s page. This option allows anyone to communicate their doubts quickly.
Allow your staff to easily voice their safety concerns if you want to promote workplace safety.
Monitor Your Equipment
Want more safety for your maintenance team? Learn everything you can about your equipment!
This includes all the basics—age, usage, and upkeep frequency.
Having an overview of this data helps you understand how safe an asset is. After all, the older the item, the more likely it is to malfunction. It’s also important to know how often your team uses the equipment.
How can you track so many assets at once?
Doing it manually isn’t very feasible, but you can invest in software that does the work for you. Tools like GoCodes Asset Tracking let you create an equipment database where each asset has its page.
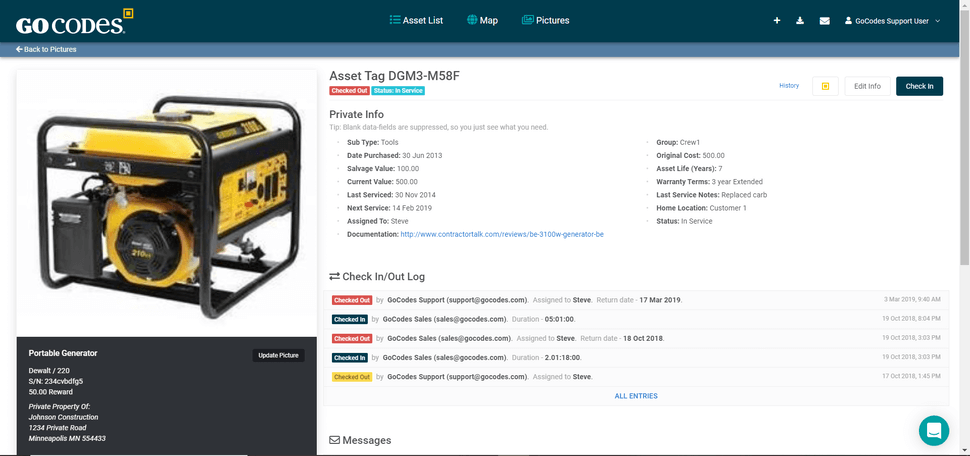
You can add details about the item there, including comments about its performance or current state. That way, the upkeep team has access to all the user feedback, usage information, and past maintenance logs.
Your team can use the equipment details to their advantage and perform maintenance safely.
Carry Out Maintenance Inspections
If you want to keep your maintenance team safe, monitor their work.
Do you know how well your team follows the safety guidelines? Perhaps they skip a step or two when no one’s watching—or maybe it’s the opposite: they stick to the rules so much they miss something obvious that’s not part of the safety plan.
The truth is, your plan might not even be fully applicable in the field.
That’s what makes workplace inspections so important.
You can include your supervisor and team in daily checks of the maintenance area. All the tools should be clean and organized, with nothing lying around, and everyone should wear PPE.
Of course, you shouldn’t stop at daily checks. Have someone regularly observe the upkeep team to detect any irregularities. People tend to forget the small details, but this can be very dangerous in the maintenance business.
Therefore, safety inspections can help you find and eliminate any unsafe practices.
Conclusion
Rethinking your maintenance safety plan should be your priority if you want to avoid workplace accidents, costly downtime, and damage to your equipment.
Before doing maintenance, you must understand its six steps, starting from planning and making the environment safe, to using the right equipment, following safety practices, and performing final checks.
To promote safety even more, ensure detailed training, communicate with your team, and prepare them for the worst-case scenarios.
On top of that, invest in regular maintenance, hold onto upkeep logs, and track the use and maintenance of your equipment.