Equipment reliability is crucial in ensuring that your projects are completed on time and without going over budget.
However, you might find yourself wondering what that term even means, so let’s start by defining it.
Essentially, equipment reliability is the amount of time in which a piece of equipment will function correctly.
Prioritizing equipment reliability is important because unexpected breakdowns can result in safety issues and cost you money, especially on a construction site filled with heavy machinery.
Therefore, in this article, we’ll explain why improving the reliability of your equipment is important and provide you with five suggestions on how to achieve it.
So, keep reading!
In this article...
Use Root Cause Analysis to Identify Reliability Issues
Equipment failure happens all the time. Sometimes the malfunctions are easily fixed with minimal losses, and other times their consequences can be disastrous.
In any case, they are stressful for both the operator and company owner and can bring the job site to a standstill until repairs can be made.
Additionally, unplanned downtime can be quite costly. According to research, it leads to $50 billion worth of losses each year.
More often than not, equipment failure occurs unexpectedly and seemingly without reason.
That’s why, in order to tackle the problem and prevent it from happening again, you have to identify its underlying cause.
For instance, let’s say the engine on your excavator keeps dying after several hours. This can be due to a number of different factors, from fuel leaks to blocked filters or problems with the injection pump.
To truly resolve the issue, you have to get to the bottom of it.
This means conducting a root cause analysis (RCA).
RCA is defined as the process of identifying what caused the issue you’re dealing with and developing an action plan for addressing it effectively.
In other words, it’s a way of determining what exactly happened, how the problem occurred, and, most importantly, what led to it.
For instance, in the case of the dying engine from our example above, your team may discover that the fuel filters were clogged.
Then, a quick look at the equipment maintenance log may reveal that the filters haven’t been replaced in a while, causing the engine to malfunction.
In this case, improper maintenance will reveal itself as the root cause of the issue.
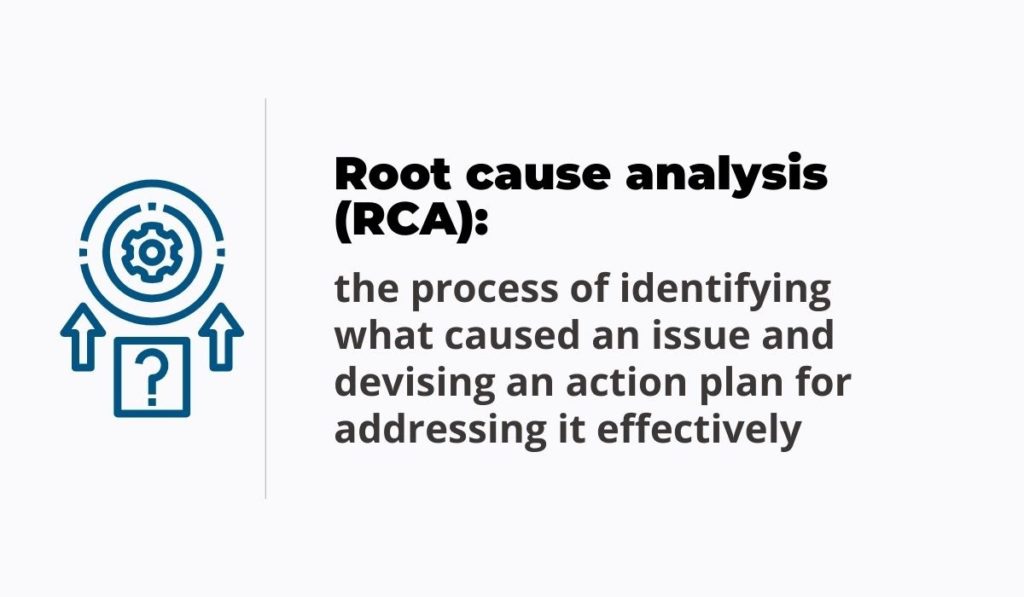
Root cause analysis teaches us to always look at the big picture. It allows you to finally put a stop to recurring failures because you can treat the actual underlying problems and not just the symptoms.
In addition to faulty maintenance, operator errors are among the most frequent causes of equipment reliability problems, which brings us to our next point.
Train Your Equipment Operators
To improve your equipment reliability, it is essential that your equipment operators know what they’re doing.
Research shows that almost 80% of unplanned downtime is preventable. Additionally, half of it results from human error, which includes improper handling or using the equipment for purposes other than intended by the manufacturer.
While many machine operators learn the intricacies of working with the equipment on the job itself, if your workers aren’t properly trained, they are especially at risk of making errors.
They can not only damage your equipment but also cause dangerous accidents.
In fact, the construction industry is particularly notorious for its dangers: almost 20% of employee deaths in the U.S. occur on construction sites. In 2019, 1,067 construction workers experienced fatal accidents.
As you can see, the importance of proper training on the construction site goes even beyond equipment efficiency.
In short, investing in proper training for your heavy equipment operators saves you money and resources in the long run. For example, a properly trained operator will use up to 12% less fuel daily than an untrained one.
If you would like to improve your current training protocols with a focus on promoting equipment reliability, here are some valuable tips.
First, it’s important to recognize and encourage employee behaviors that support equipment reliability, such as turning the engine off when the machine is not in use.
Next, aim to instill the importance of correctly using the equipment in your operators, to avoid unnecessary wear and tear.
Also, teach them to recognize potential issues on time and even conduct some basic repairs, in accordance with the manuals provided by the manufacturer.
If you create a sense of ownership by encouraging your employees to take responsibility for specific assets in their care, you’ll encourage a culture of safety in the worksite.
A good equipment check-in/check-out software solution can help here.
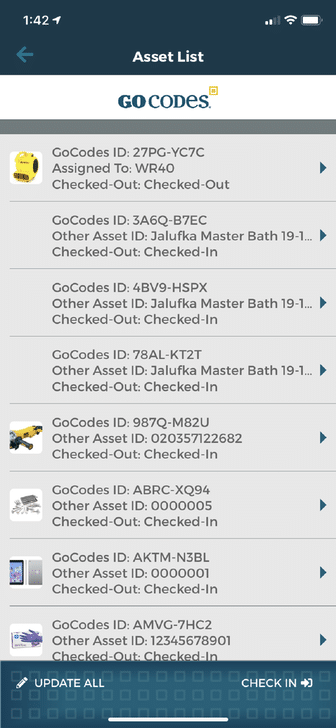
That’s because the workers will make sure to put their training into practice if they know their managers can see when they used a piece of equipment and know if the piece was in their care when it broke down.
In any case, when heavy equipment is involved, safety should be your number one priority.
Training your operators is a must if you want to improve the reliability of your equipment.
Leverage the Use of Equipment Data
Nowadays, technology enables us to monitor everything from our health, homes, and even our business processes. Machinery is no exception.
Therefore, it is also no surprise that the use of equipment data is increasing in popularity. With the right tools, you can track the location of your equipment, its condition, and operating hours.
Having 24/7 access to this data aids you in making important decisions about equipment use and maintenance, supporting its operating reliability.
Access to this type of data also improves the efficiency of equipment allocation. It can help you determine if you have too much or too little of a certain type of equipment on a site.
You can then arrange for the transfer of the necessary equipment from the nearest possible location.
Relying on this kind of technology to monitor your equipment is referred to as telematics.
Research shows that 54% of construction firms consider tracking equipment location as the top benefit of telematics, followed by improved operator practices at 34%.
Telematics systems will usually alert you when your equipment leaves the site or is used outside working hours. GPS enabled systems and geofencing features are to thank for many theft or misuse prevention.
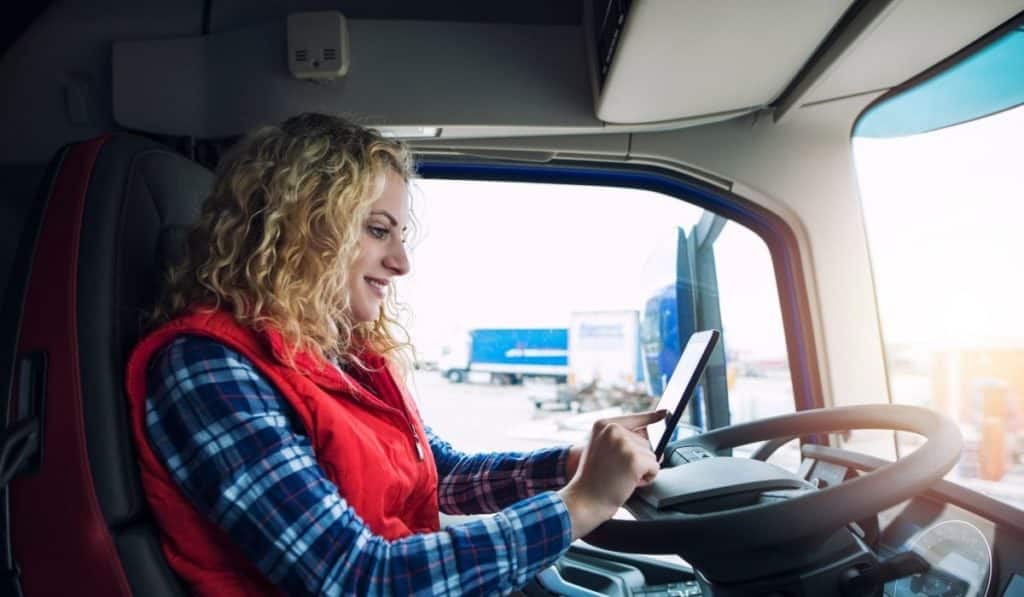
And here’s a similar story.
Thanks to telematics, it took Maurice Piersol, owner of a small construction firm called Piersol Construction, less than an hour to locate a missing water truck.
Piersol is aware of the other benefits of telematics. He notes that he can quickly see which vehicles can handle last-minute changes.
Since he can see where each truck is headed, he can notify drivers to divert to a different job as soon as the need arises.
That way, if a particular piece of equipment breaks down, he has significant savings in keeping multiple crews supplied with the necessary tools.
Leveraging equipment data also allows decision-makers like Piersol to monitor which equipment frequently breaks down and work towards improving its reliability.
Equipment tracking and management software, such as GoCodes Asset Tracking, helps with such tasks by providing an overview of maintenance logs, as well as noting how often a particular piece of machinery is used and where.
In short, leveraging equipment data will help you get the most out of your equipment, resulting in significant savings and improved efficiency.
Be Consistent With Equipment Maintenance
Simply put, if equipment maintenance suffers, so will their reliability. So, if you want optimal performance, you need to service your equipment regularly.
A good preventative maintenance routine allows you to detect potential signs of equipment failure early on and deal with it before it escalates. This will extend the life of your equipment, and save you time and money.
Research supports this: data provided by the U.S. Department of Energy shows that preventive maintenance results in up to 45% fewer breakdowns and can reduce downtime by up to 75%.
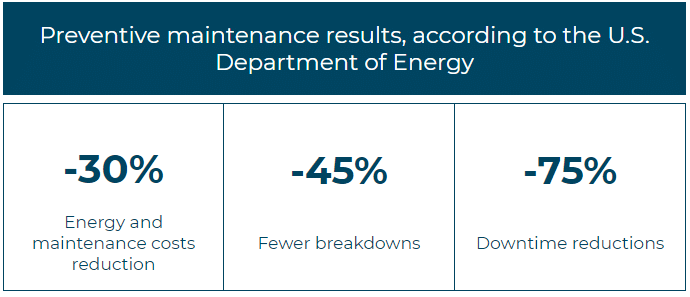
Other benefits of keeping up with your maintenance include reduced injuries and fatalities.
According to the U.S. Bureau of Labor, 17% of fatal construction accidents are the consequence of equipment issues. In other words, if your equipment isn’t working properly, there is a bigger chance of workplace injury or even death.
This shows how vital regular maintenance is: you simply can not put a price on your employee’s safety.
Another important but often overlooked benefit of equipment maintenance is boosting the resale value of your machinery.
If you keep up with your maintenance, you ensure that your machinery remains in the best possible condition, allowing you to extract the most value from it once you choose to sell it.
So, how can you keep consistent with your equipment maintenance? Here are our best tips!
First, determine what type of maintenance works best for your equipment.
For instance, for some machinery, it will be enough to conduct checks and repairs periodically, regardless of the frequency of use. We call this time-based maintenance.
On the other hand, for assets located in environments where they may deteriorate more quickly (such as engines left in humid conditions), risk-based maintenance will be more appropriate.
This is especially true if a malfunction could have far-reaching consequences. In those cases, maintenance will be conducted more frequently than a usual schedule would require.
Once you’ve determined which approach is the most suitable for your needs, create your maintenance program and stick to it.
Then, educate your staff about the proper procedures. It’s advisable to devise a step-by-step maintenance checklist that your team can rely on.
It should list not only the order in which the checks should be performed but also draw attention to the parts that are especially prone to malfunctioning.
Taking particular care to keep those parts in good condition will keep your equipment reliable longer.
You can determine which parts those are if you keep maintenance records, noting which repairs have been conducted, when and by whom.
A solution like GoCodes Asset Tracking, which allows you to print out unique QR codes for each piece of equipment that you can scan with your smartphone, makes logging this type of information easy.
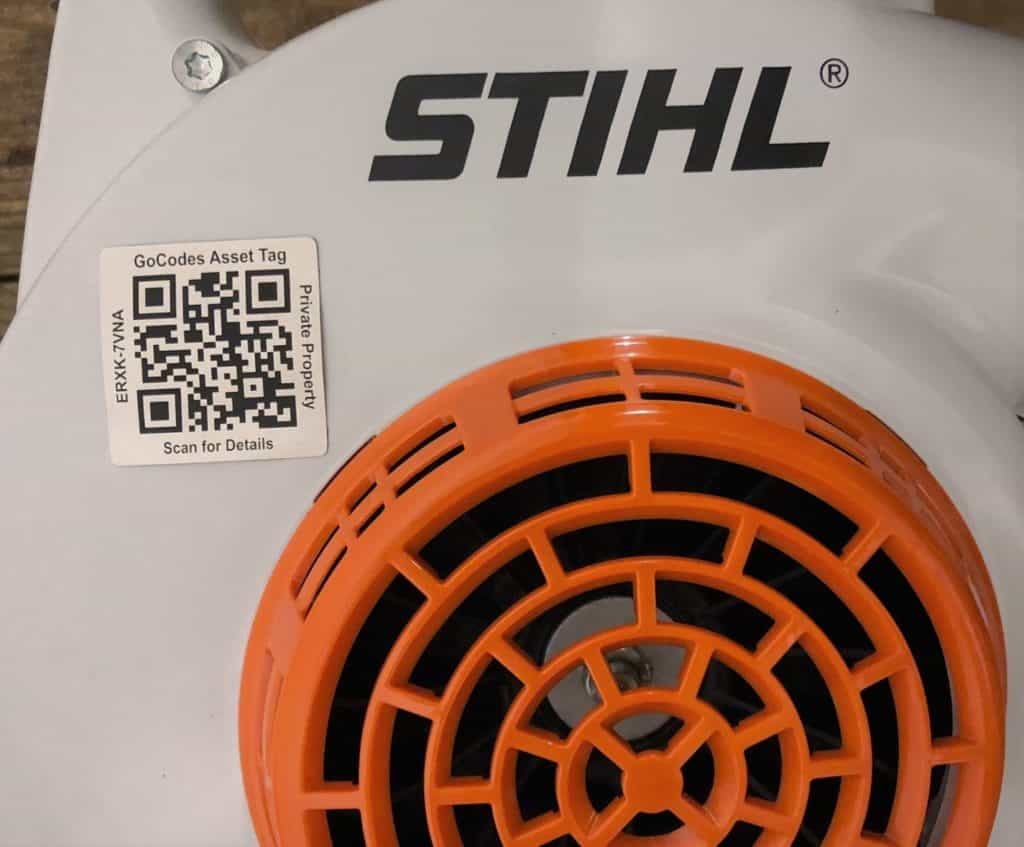
Finally, make all this information easily accessible to your team in a knowledge base to make sure they follow best practices. That way, your equipment will function correctly for a longer time.
Keep Your Equipment Clean
At the construction site, your equipment can be exposed to dirt, grease, moisture and even salt. Over time, the buildup damages your equipment and negatively affects its performance.
And while it’s impossible to keep working machinery in mint condition forever, regular cleaning will improve its long-term durability and reliability.
For instance, if you allow dust to accumulate on your electrical plugs, it can lead to short circuits, which is a potential safety hazard and can cause downtime.
But if you regularly clean your plugs, you will avoid all of those issues.
In short, well-maintained, regularly cleaned equipment lasts longer, while being safer to use and more fuel-efficient.
So, how do you keep your equipment clean?
You will likely need to invest in some specialized equipment like water cannons or pressure washes. They will blast off the grime, which means less scrubbing on your part.
To make cleaning easier, disassemble the equipment, taking off all the attachments and other removable parts. This will allow you easier access to problem areas, while also preventing splashing.
For the same reason, John Bourbeau of Champs Pressure Washing & Steaming Ltd. also recommends being mindful of the order in which you clean the equipment:
“I always start washing with the undercarriage, which will be the dirtiest. To start with the body when the undercarriage is dirty means that a rewash of the body will be required after the undercarriage is done.”
Finally, it’s important to use the right cleaning and degreasing agents.
Always check the equipment manuals to see which types of products the manufacturer recommends.
Since it usually takes a while for the compounds in the cleaning agents to break down the dirt, you will probably have to wait up to 30 minutes before you can rinse them off.
In conclusion, clean equipment will last you longer and perform better, so make sure to clean it on a regular basis.
You’ve put in a lot of resources into your equipment, so it’s in your best interest to maintain your investment.
Conclusion
So, as you can see, equipment can be unpredictable. Operators make mistakes, parts get old, and preventive maintenance often gets neglected, leading to premature failure.
All of these problems can be easily avoided if you follow the advice from this article.
If you want to avoid those issues and keep your equipment in optimal condition, make sure you address the root causes of each problem as it arises.
Train your equipment operators to use the equipment properly and spot issues early, and rely on equipment data to determine what kind of care your equipment needs.
With consistent upkeep, your machinery will be more reliable and last longer.