Key Takeaways:
- Equipment utilization is affected by project-related, equipment-specific, and environmental factors.
- Equipment availability, equipment downtime, and utilization rate are the key KPIs for measuring utilization.
- Telematics solutions can help optimize construction equipment utilization levels.
Optimizing equipment utilization is the key to boosting productivity, slashing operational costs, and keeping workflows running smoothly.
But there’s still a lot about this process that remains a mystery to many.
What internal and external factors can impact your equipment’s efficiency?
How can you tackle these challenges?
And what are the best practices to ensure your equipment performs at its peak?
This is precisely where this article comes into play.
We’ve gathered answers to five common questions about equipment utilization, all with the goal of helping you better understand this vital aspect of equipment management and get the most out of your valuable assets.
Let’s dive in.
In this article...
Which Factors Affect Equipment Utilization?
From the preconstruction phase to the project closeout, many different factors can impact the utilization of your equipment.
On a broader scale of project planning, several elements might influence how your assets will be used, including:
- Project scope and size
- Project complexity
- Scheduling
- Budgetary constraints
Project scope and size determine how much equipment you’ll need and how often it’s going to be used, while complexity and the type of work dictate the type of machinery required.
For instance, larger, more complex projects might require more machines along with some specialized equipment.
However, if your budget is tight, you might not be able to procure all the necessary resources, leading to higher utilization rates for existing assets.
This could also potentially cause bottlenecks or delays due to their overuse.
But there’s even more to consider.
Equipment-specific factors can affect utilization as well, such as:
- Maintenance effectiveness
- Operators’ proficiency
- Equipment age
- Availability of spare parts
If your machinery isn’t operated by well-trained personnel or isn’t properly maintained—especially if it’s older—it’s more likely to frequently break down and experience more unplanned downtime.
For example, Marius Pick, Logistics Manager at Afrigrit, a company that specializes in providing solutions for the construction industry, explains how improving their maintenance regime helped them improve equipment utilization.
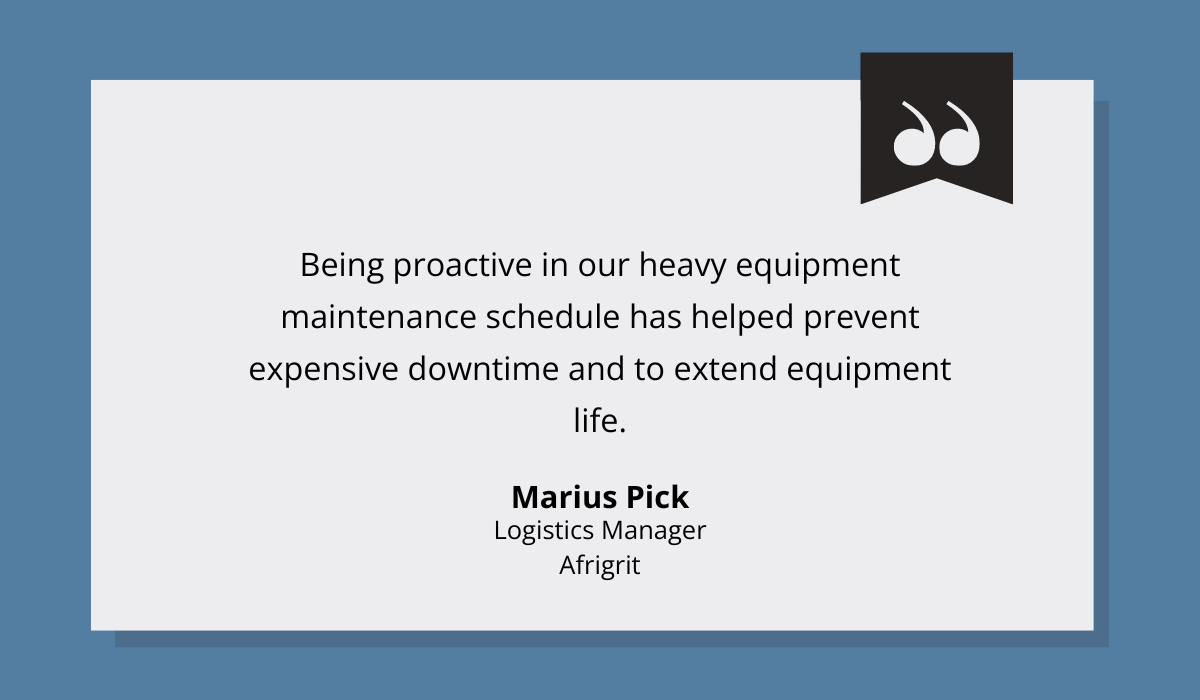
That’s right: how well you take care of your equipment can make a world of difference for your valuable assets’ uptime and useful life.
Lastly, some environmental factors can influence asset usage as well, such as:
- Weather
- Natural disasters
- Job site terrain
- Daylight hours
Weather conditions in particular are notorious for affecting machine operability and uptime.
Rain and snow can create muddy or icy conditions that hinder equipment movement and operation, while extreme heat or cold can affect asset performance and operator comfort.
This, in turn, can cause a significant dip in utilization rates.
On top of that, high winds can make it unsafe to operate certain heavy machinery, especially cranes and aerial lifts.
Ultimately, navigating all these factors is no easy feat.
It requires adaptability, foresight, and meticulous planning on the part of equipment managers.
They need to be able to anticipate and mitigate risks, optimize resource allocation, and stay proactive in the face of all those challenges in order to make the very most out of their assets throughout the entire project lifecycle.
How Can Equipment Utilization Be Measured?
To effectively measure your equipment utilization, concentrate on these three KPIs:
- Equipment Availability
- Equipment Downtime
- Utilization Rate
Let’s briefly break each of them down.
Equipment availability, just like the name suggests, refers to the amount of time a specific asset is accessible for operation within a defined timeframe.
It takes into account scheduled downtime for upkeep, repairs, changeovers, and other factors impeding the usage of a machine.
Equipment downtime specifically focuses on periods when the asset cannot operate as intended.
It can be segmented into two categories: planned downtime (for scheduled maintenance and changeovers) and unplanned downtime (due to breakdowns and unforeseen events).
Monitoring both is necessary to identify the underlying causes of certain equipment inefficiencies, pinpoint areas for improvement, and get a clearer picture of your overall asset utilization.
Finally, utilization rate measures the amount of time a machine is actually used relative to its maximum availability within a specified period.
This metric is calculated by dividing the actual usage time by the total available time and multiplying the result by 100 to express it as a percentage.
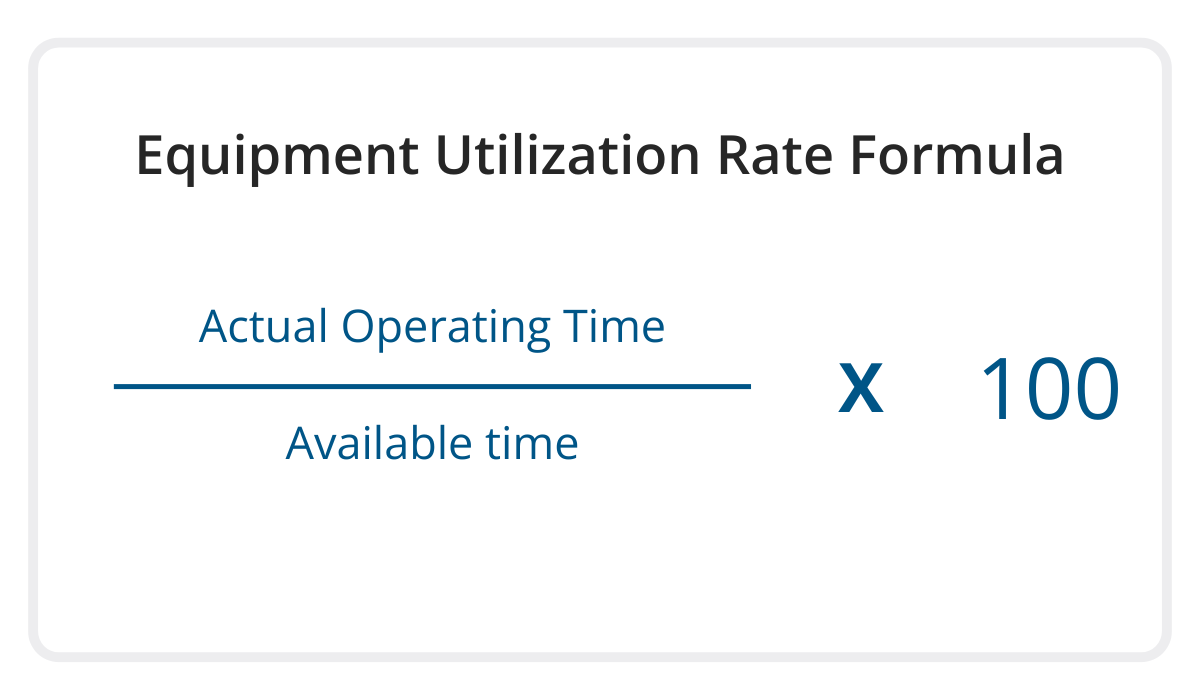
Now, you’re probably wondering: how do you capture all this information?
There are, in fact, many ways to do so, from manual methods like spreadsheets to digital solutions such as equipment management software.
But if you’re after only the most accurate and reliable data—and you probably are—consider going digital.
For example, asset management systems like GoCodes Asset Tracking, which integrate GPS trackers (shown below), offer precise and up-to-date data without compromising the convenience or ease of use associated with manual approaches.
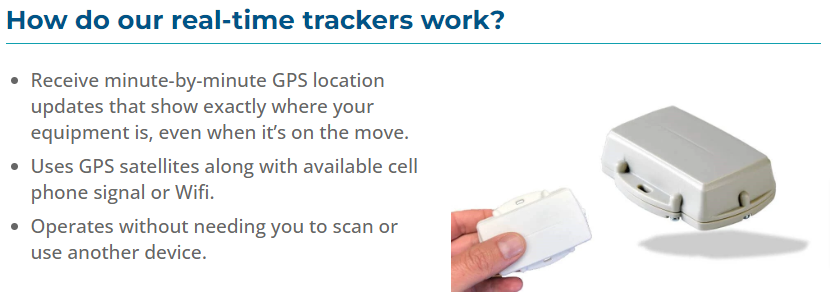
Simply attach the tracking devices to your machines, and they will continuously transmit minute-by-minute equipment information, yielding real-time insights about where your assets are and how they’re being used.
GoCodes Asset Tracking GPS trackers are adept at tracking an extensive array of data, including equipment location, speed, engine hours, acceleration, and more, providing you with a 360-degree view of your machinery.
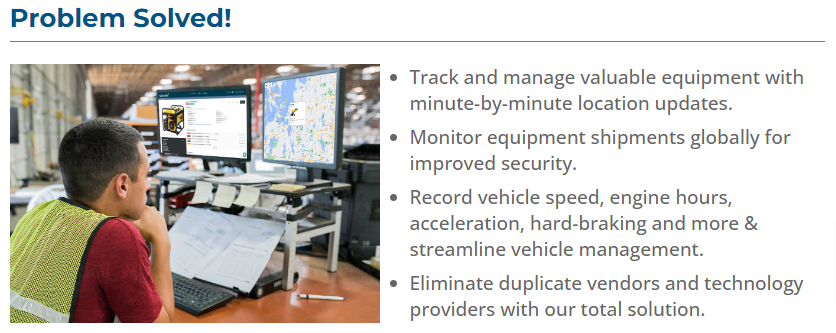
That’s precisely what you need if you want to keep your finger on the pulse of asset utilization.
Remember, measuring is the first step towards improving.
So keep a vigilant eye on all these KPIs to spot issues early on, allocate your resources strategically, and unlock the full potential of your assets.
How Does Good Equipment Allocation Increase Utilization?
Proper equipment allocation in this context refers to the assignment and distribution of machinery and vehicles across various tasks, projects, or job sites to optimize overall operational efficiency, productivity, and cost-effectiveness.
Essentially, it’s all about making sure that the right assets are in the right place and at the right time, all with the goal of completing the job on time and within budgetary constraints.
If you manage to nail resource allocation, it’s only natural equipment utilization will follow suit, minimizing instances of assets sitting idle and maximizing their contribution to revenue generation.
Derek Grover, Senior Vice-President of Technology & Operations at Jim Pattison Lease, a fleet leasing company, illustrates the importance of asset allocation with an example in the context of fleet management:
“You’re paying X number of dollars a month to lease a vehicle, so you want to know if you’re getting value out of it. Is it on the road for two hours a day, or seven hours a day? If a vehicle is being used just for transitioning from work to home, maybe there’s an opportunity to use that vehicle in another capacity while the driver of that vehicle is at the office. Could that vehicle be freed up for midday deliveries?”
Of course, the same can be applied to any type of construction equipment.
You don’t want to place machines where they aren’t needed, particularly if there is a greater demand for them elsewhere.
That way, you might as well be throwing away your money.
You also don’t want to find yourself in a situation where there’s not enough equipment on a job site because that could lead to overuse of existing machinery, resulting in potential asset damage or project delays.
These are precisely the issues effective resource allocation tackles.
It takes into account project requirements and phases, ensuring that equipment is deployed accordingly to maintain a balanced workload and facilitate steady progress across all activities.
No unnecessary downtime, no under or overutilization of machines, and no delays.
Which Technologies Can Help Optimize Equipment Utilization?
When it comes to boosting equipment utilization, the term telematics frequently comes up.
While traditionally used for fleet management, this technology is now expanding its reach to track various other types of assets.
This shift is hardly surprising, considering the tech’s ability to provide extremely detailed, real-time information about machines’ locations, conditions, and activities.
Telematics systems themselves rely on three core technologies:
- onboard diagnostics equipment,
- GPS, and
- wireless communications.
In the image below, you can see how all three of them work together.
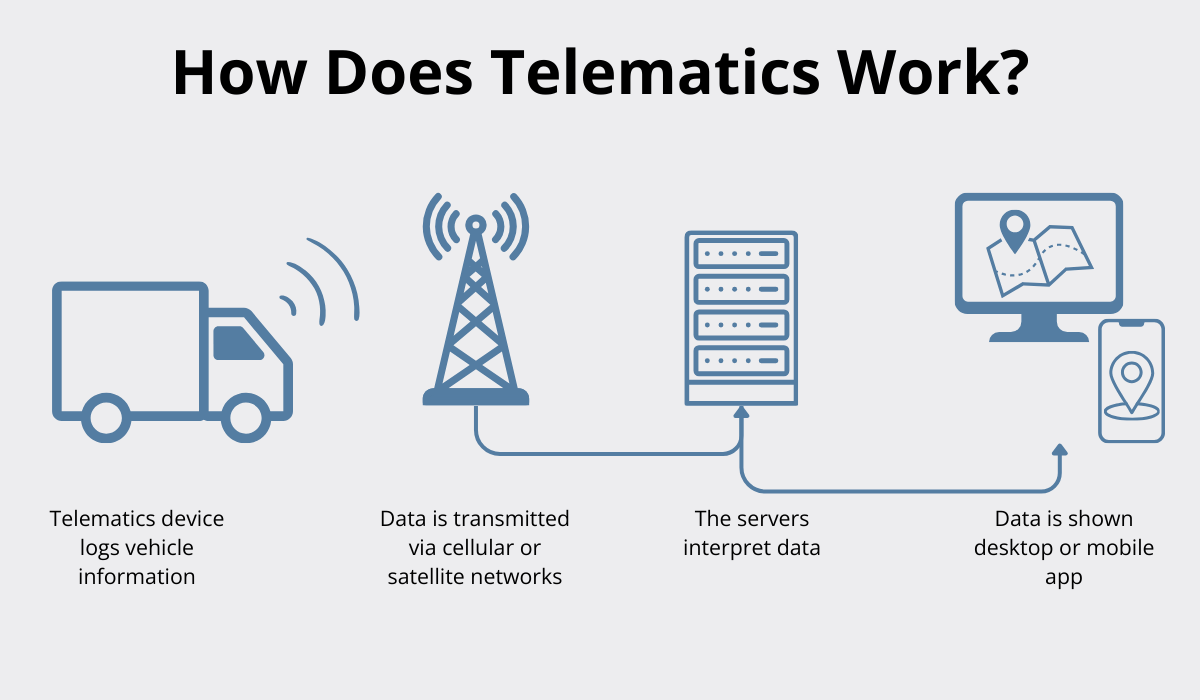
Once onboard diagnostic devices and GPS trackers are attached to equipment and activated, they begin transmitting different data points such as asset location, speed, engine performance, fuel usage, and mileage.
Wireless communication, whether through cellular, Wi-Fi, or satellite networks, then helps deliver this information to end-users by enabling the transmission of data between the devices and the software.
The benefits of this technology for equipment utilization alone are immense.
For starters, telematics facilitates effective asset allocation.
It tells you all about where your machines are, or how and if they are being used, in turn leading to better-informed and more data-driven decision-making regarding their distribution and assignment.
Just ask Joseph Micheletti, Equipment Controller at Loenbro, a turnkey provider for new plant construction or expansion of existing facilities—he’s seen it firsthand:
“We’re able to provide the field engineers and project managers with the resources they need to monitor where their equipment is and where everyone else’s equipment is, and to really fully utilize our equipment. If one of our field engineers or project managers is done utilizing the majority of their sidebooms and another field engineer says, ‘I could really use another one or two sidebooms,’ he has the resources to see, ‘It doesn’t look like this one is being used too much over on Frank’s job; let me call Frank.’”
After all, when you’re running a large-scale operation with many different assets across various projects and job sites, you need some help with ensuring your equipment is exactly where it needs to be.
Telematics is just the tool for that.
Telematics also takes your maintenance scheduling to the next level.
Since it can monitor machine health and usage, maintain a record of and track past maintenance, and send you alerts when service is due, telematics helps you come up with optimal schedules for asset upkeep and inspections.
Guillaume Poudrier, the president of fleet management solution provider Géothentic, agrees.
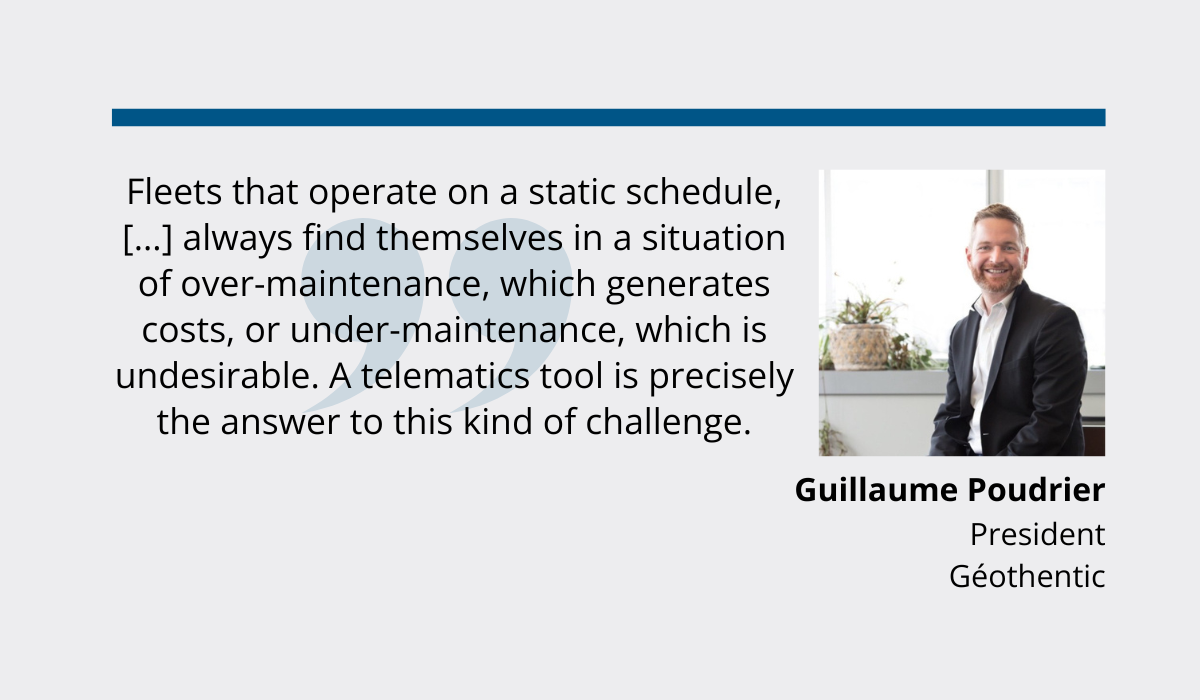
And guess what?
All of those perks ultimately translate into significantly higher overall utilization.
In fact, research conducted by Verizon Connect suggests that telematics can actually enhance vehicle uptime by up to 25%.
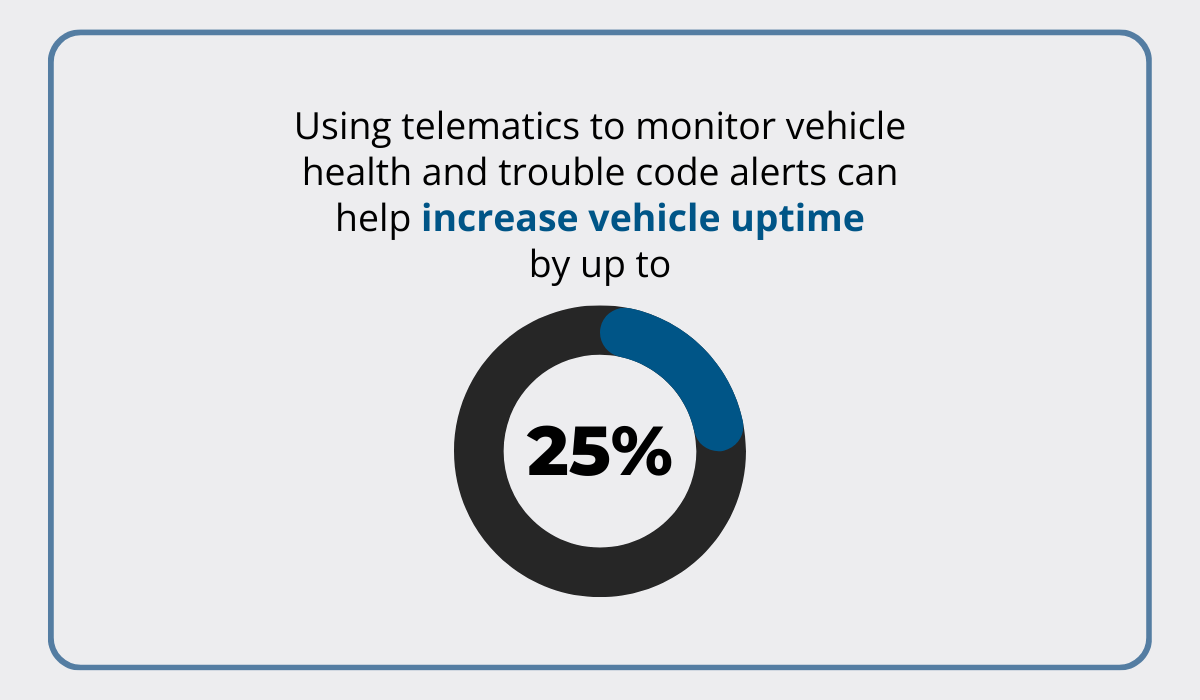
Remarkable outcomes for a single digital solution, wouldn’t you agree?
How Does Preventive Maintenance Contribute to Maximizing Equipment Utilization?
Preventive maintenance involves regular and systematic asset upkeep.
This includes inspections, adjustments, cleaning, testing, and parts replacement based on predetermined time intervals, usage patterns, or similar criteria.
The goal?
To nip equipment-related problems in the bud and forestall unexpected machine failure, maximizing its utilization in the process.
Justin Steger, Solutions Marketing Manager at John Deere Construction and Forestry, is all about this approach, explaining that proper maintenance has a lot to do with your assets’ performance.
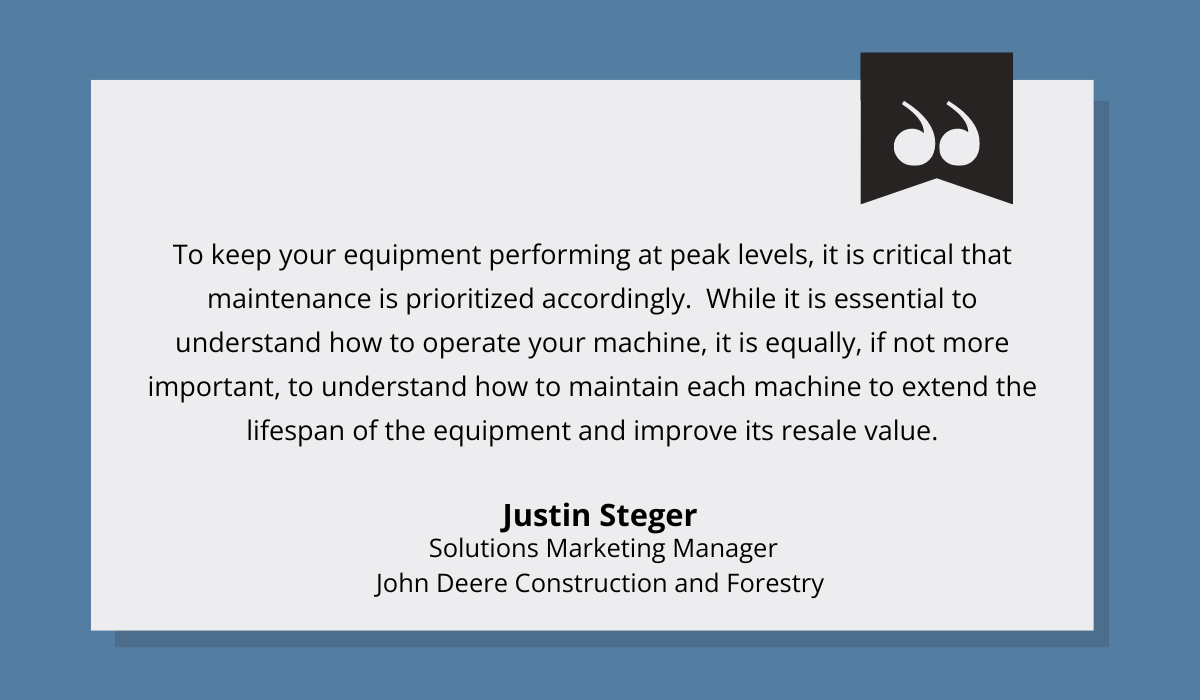
Interestingly enough, he adds that it’s just as important, if not even more, as knowing how to operate a machine.
And according to the numbers, he just might be right.
Research on manufacturing machinery reveals that companies implementing preventive maintenance experience about 52% less downtime and around 78% fewer defects.
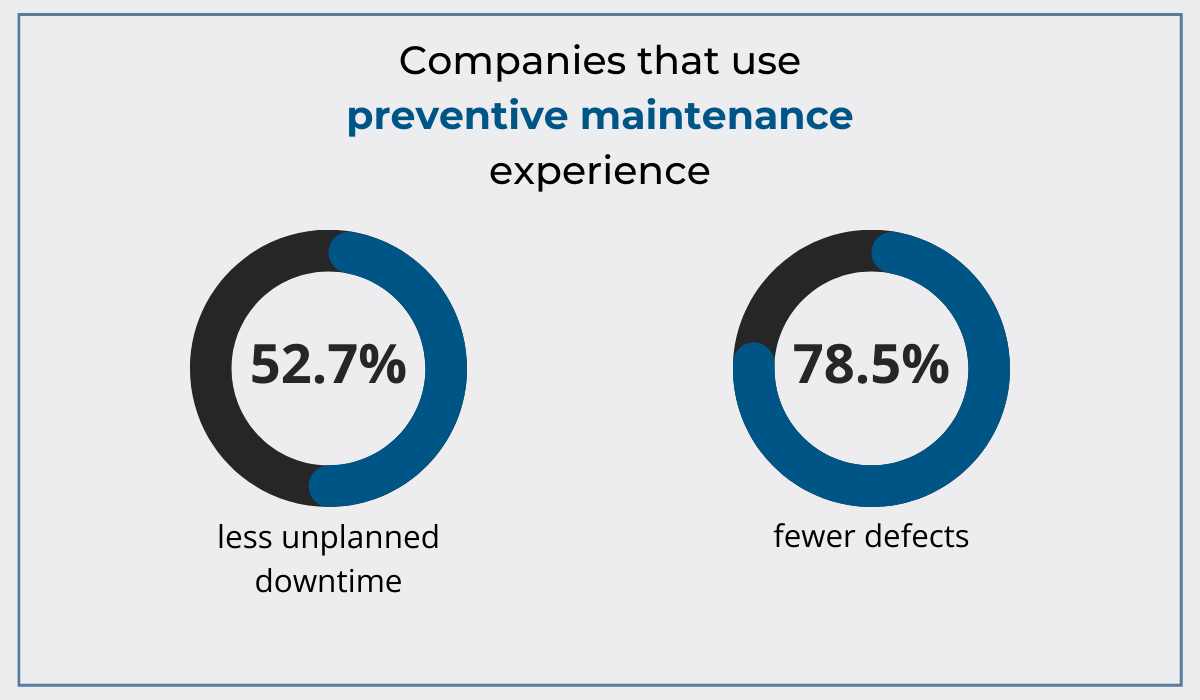
That means less time spent in the repair shop and more time getting the job done.
But that’s not all.
By consistently and proactively servicing your assets, you’re not just preventing breakdowns, but also extending their lifespan, squeezing every last drop of value from your investments.
As Rushil Goel, former VP and GM of Fleet Management at Samsara points out, a reactive approach to equipment upkeep simply doesn’t compare.
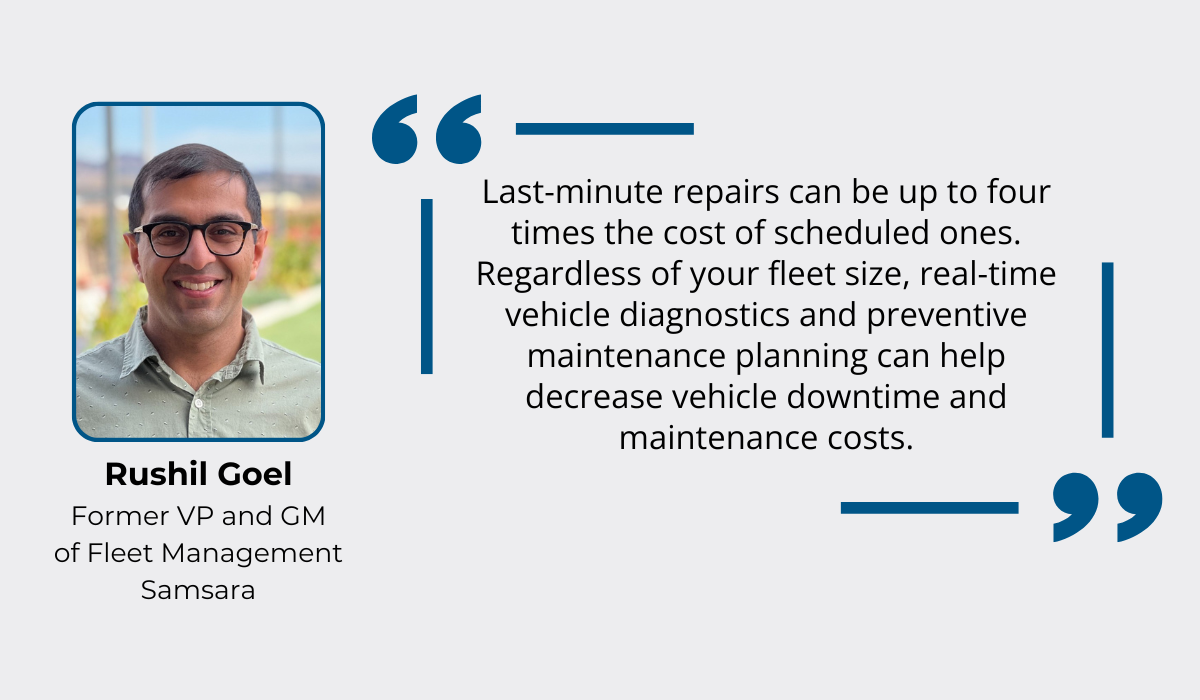
Whether it’s vehicles, heavy machinery, or any other equipment, preventive maintenance is at the core of the reliability, longevity, and efficiency of your assets.
Conclusion
Hopefully, this article really got you thinking about equipment utilization and how vital it is for getting the most out of your assets.
After all, these machines and vehicles are a big investment.
You don’t want them sitting idly in a remote corner of a job site, costing you more money than they help you make, right?
Then start monitoring your equipment utilization KPIs today.
By doing so, you’ll uncover hidden inefficiencies, discover how to fix them, and unlock your assets’ full potential on every single project.