Have you ever heard that age-old wisdom, “planning is half the battle”? Well, it holds true even in construction.
Maybe it’s not precisely half the battle—after all, you still have to physically build a house, a building, or a bridge.
Nevertheless, detailed planning will significantly ease the execution of your projects and align them with your company’s objectives.
Also, construction planning will make sure your projects are completed on time, within budget, and with minimal risks.
That is—if you are well-versed in construction planning and all the types of planning you can do to prepare for the project execution.
Today, we will explain six different types of construction planning that will pave the way for successful project execution, bringing numerous benefits along the way.
Without further ado, let’s start with the first construction planning type.
In this article...
Strategic Planning
Every construction company should have a long-term vision.
Whether it involves adopting new technologies, enhancing workforce skills, or implementing sustainable practices, it is through strategic planning that you can achieve these objectives across diverse spheres of your company.
So, at its core, strategic planning is a process that will ensure all your projects and activities align with your long-term vision and values.
For that to happen, you have to perform analysis, set goals, define high-level strategies to reach those goals, and determine the return on investment and how you will measure it.
Let’s go through these steps in more detail.
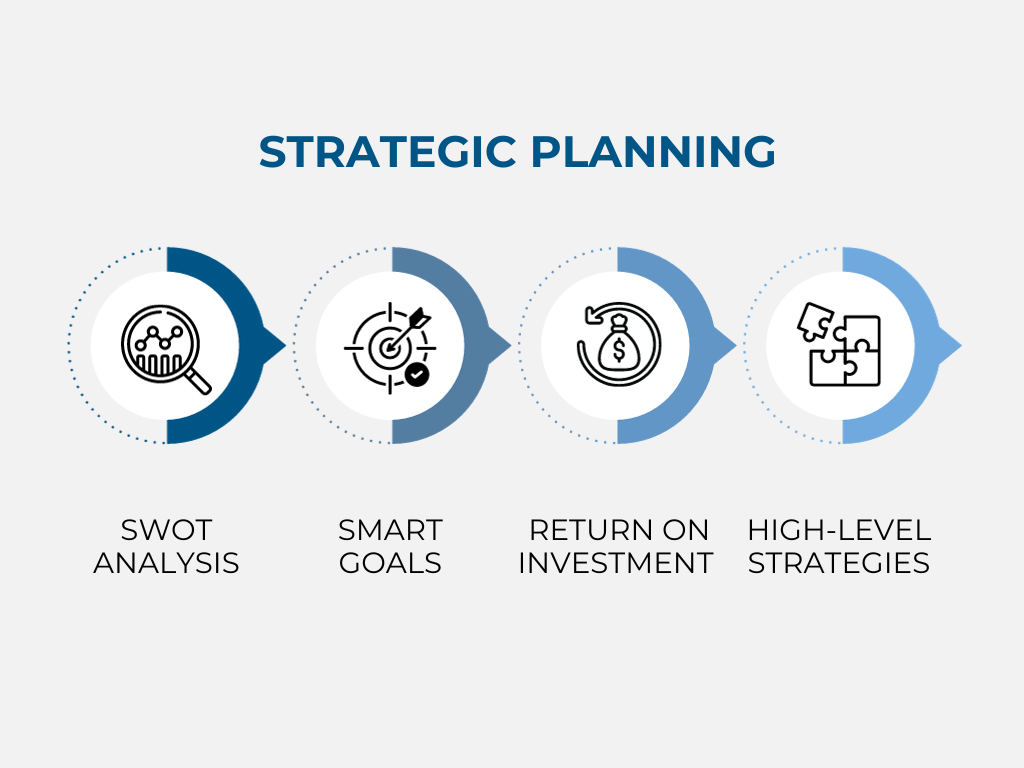
Every good strategic planning should start with a comprehensive SWOT analysis to identify your company’s:
– strengths,
– weaknesses,
– opportunities,
– and threats.
Such analysis will give insights into your company’s market position, potential challenges, and areas for capitalizing on opportunities.
And based on it, you can establish SMART goals aligned with your company’s vision—that will either fix the weaknesses or take strengths and make them more profitable.
For instance, if the analysis reveals that your employees resist new technologies—a weakness and a threat because you fall behind the competition—you can set a specific and strategic goal to achieve a 30% increase in technology utilization within the next 12 months.
With the goal defined, you have to plan strategies to realize this goal.
In the case of technology adoption, this may involve implementing training programs to familiarize employees with the new technology.
At this point, you also have to plan how to measure return on investment.
You can do that by defining key performance indicators (KPIs) that will evaluate if your employees use new technology more after implementing training and how much that increases their efficiency.
In essence, strategic planning is all about setting long-term strategic goals that align with your company’s mission and values and defining strategies that will lead to realizing these goals.
Project Planning
Project planning is another step in construction planning, transforming strategic vision into actionable steps, and laying the foundation for successful project execution.
In this phase, a detailed project plan that includes tasks, milestones, timelines, and resource requirements is created.
Project planning breaks down into operational planning, where you focus on the day-to-day execution of the project.
Through operational planning, you coordinate personnel, equipment, and materials, ensuring that all the resources are allocated for the project to stay on course and meet its objectives efficiently.

Given the complexity of construction projects with numerous tasks, varied resources, and a sizable workforce, the project planning phase is challenging.
Especially if you have to manually plan (and keep track of) all these elements. That’s why there are many different tools on the market that aid project planning.
Project management software, for instance, helps project planning by:
- Organizing and aligning project tasks with the overall timeline.
- Optimizing the use of labor, equipment, and materials throughout the project.
- Enabling real-time collaboration among team members to ensure everyone is on board.
- Providing instant insights into project progress for quick decision-making.
- Reducing the risk of miscommunication among project stakeholders.
Moreover, specific tools like the work breakdown structure aid in efficiently managing the workload by dividing the project into phases, deliverables, and work packages.
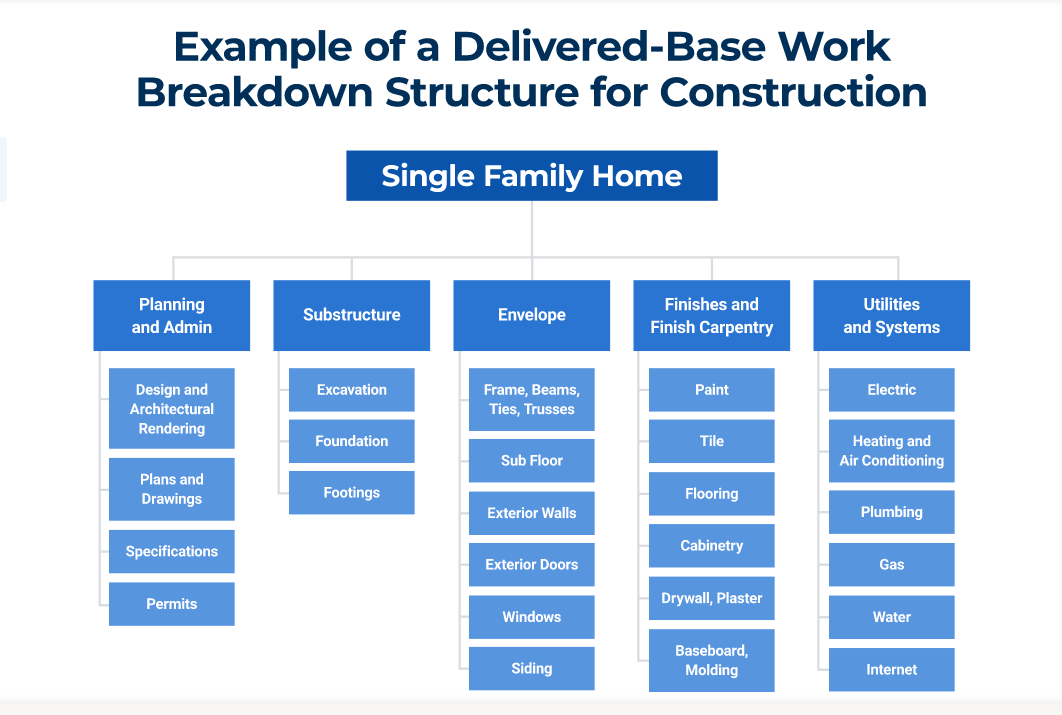
The Gantt chart, on the other hand, is instrumental in defining critical paths and improving project timeline planning.
Because this tool includes start and end dates of tasks, milestones, and dependencies between tasks, you can plan the project more efficiently and keep track of the project progression more clearly.
All in all, utilizing these tools in the project planning phase makes the time-consuming and challenging planning process considerably smoother.
It also makes the plan more detailed and easier to follow, which is crucial since the project planning phase sets the stage for project success.
Financial Planning
Financial planning in construction is the bedrock for maintaining budget responsibility throughout a project’s lifecycle.
It involves estimating, allocating, and managing financial resources to support the various phases of a construction project.
This encompasses everything from initial feasibility studies and design phases to procurement, construction, and project closeout.
Financial planning is also crucial in establishing budgetary controls, ensuring that the project adheres to cost constraints and remains economically viable.
Moreover, a proper financial plan will help you optimize your resources for maximum efficiency of your projects.
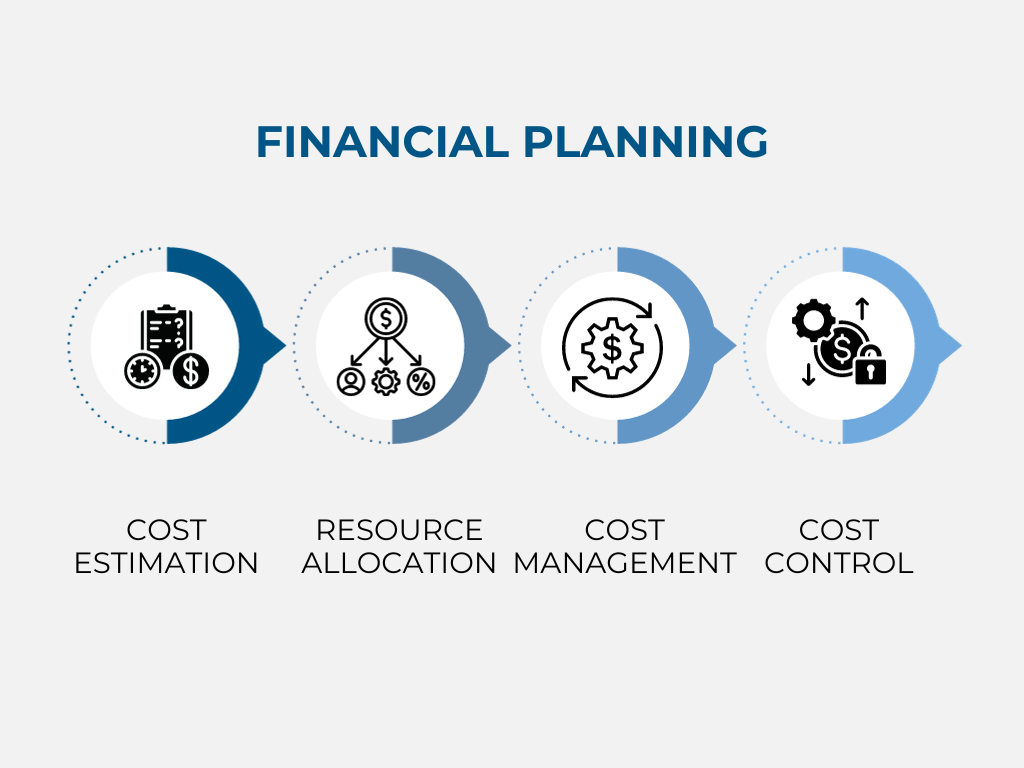
For effective financial planning in construction, consider the following few essential tips.
First and foremost, conduct a thorough cost estimation at the project’s start, factoring in all potential expenses:
- Labor costs
- Material costs (sourcing materials prices, accounting for material waste and storage)
- Equipment costs (rental vs ownership, maintenance, and fuel costs)
- General and administrative costs (office, project management, insurance, and legal costs)
- Contingency funds
After estimating project costs, conduct benchmarking and market analysis and leverage historical data from previous projects to compare and improve cost estimations.
Also, regularly revisit and update the budget as the project progresses, accounting for any changes or unforeseen circumstances.
Another crucial part of financial planning is planning cost control through the project.
These can be periodic financial reviews and audits that will identify potential issues early on and allow timely measures to stay within the budget.
Lastly, emphasize transparent communication with all stakeholders to ensure everyone is on the same page with budgetary constraints and financial goals.
To conclude, proper financial planning is essential to maintain fiscal discipline and ensure the economic viability of your project from its start to the end.
Risk Management Planning
The next type of planning in construction is risk management planning. And it’s safe to say this is one of the most important planning you can do to safeguard your construction project.
Through risk management planning, you identify and mitigate potential threats that would otherwise harm your projects in terms of cost, time, quality and safety.
In essence, preparing a risk management plan involves systematically identifying, assessing, and defining strategies to address and manage risks throughout the construction project lifecycle.
Let’s focus for a moment on one commonly encountered risk on construction sites—the loss or theft of material, tools and equipment.
Did you know that this year, on Labor Day alone, there were 179 instances of heavy equipment theft in the US?

While this risk is unfortunately all too common, it can be mitigated with technological solutions that use GPS to track tools and equipment.
Take, for instance, our GoCodes tool tracking software. This software allows construction companies to tag and track tools and equipment using QR codes.
When these codes are scanned with a scanner, phone or tablet, software saves the location and allows you to monitor where your assets are in real-time.
In the event of loss or theft, the system enables you to see the asset’s last location, and this information can help law enforcement retrieve the equipment.
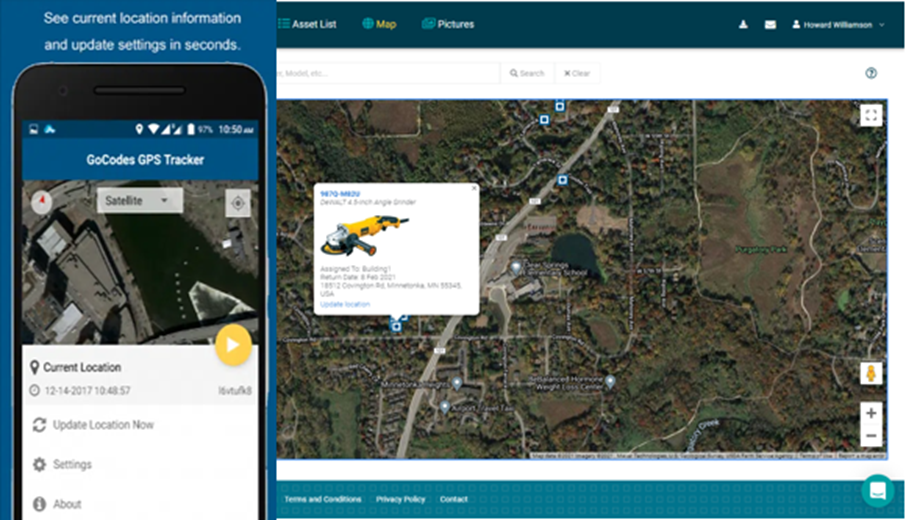
Beyond this specific risk, a comprehensive risk management plan will help you prevent all types of risks.
Let’s briefly review the steps you can take to prepare a risk management plan.
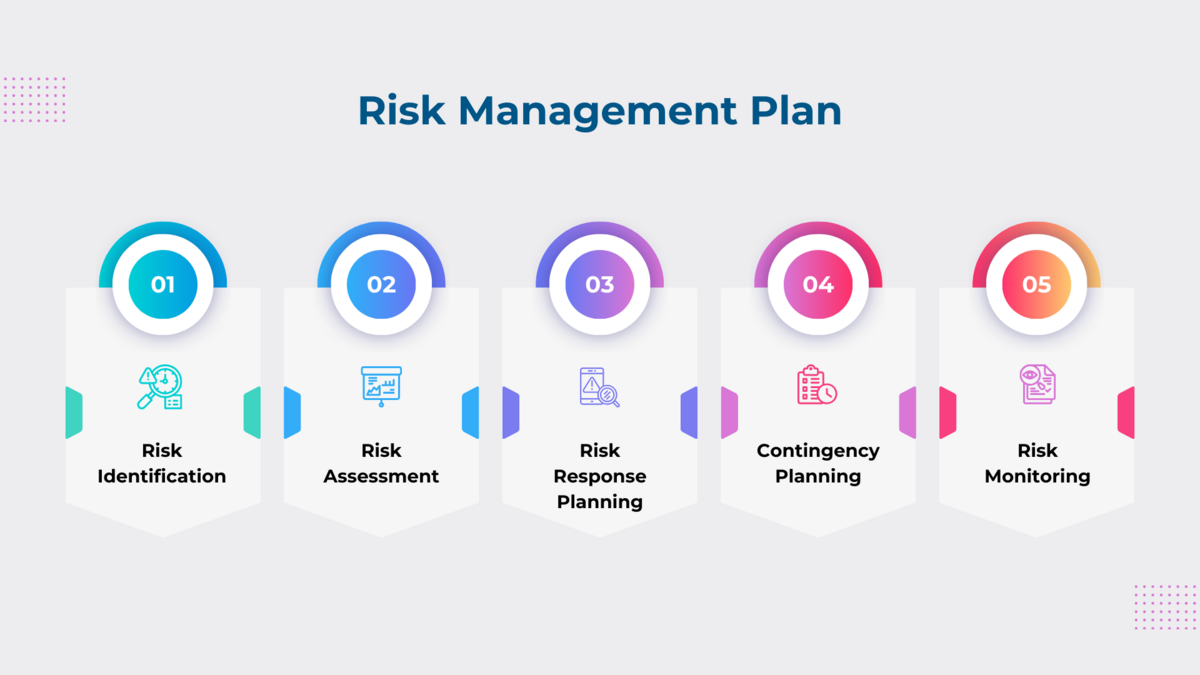
Start with a thorough risk analysis to identify potential risks. The risks can range from external factors like weather conditions to internal challenges like resource availability.
Then, assess each risk based on severity and probability and implement strategies to mitigate or eliminate high-priority risks.
Also, make sure to regularly update the risk management plan as the project evolves.
As you can see, risk management planning in construction is a dynamic process that anticipates and addresses potential challenges that could disrupt your project’s lifecycle.
So, make sure to invest time into this planning process. It will only enhance your project’s success.
Quality Planning
Another crucial planning for a construction project is quality planning.
This planning ensures the final project meets specified standards, ultimately enhancing client satisfaction and minimizing the need for rework.
Quality planning encompasses the development of comprehensive quality standards, inspection protocols, and testing procedures, all designed to maintain construction output at predefined levels of excellence.
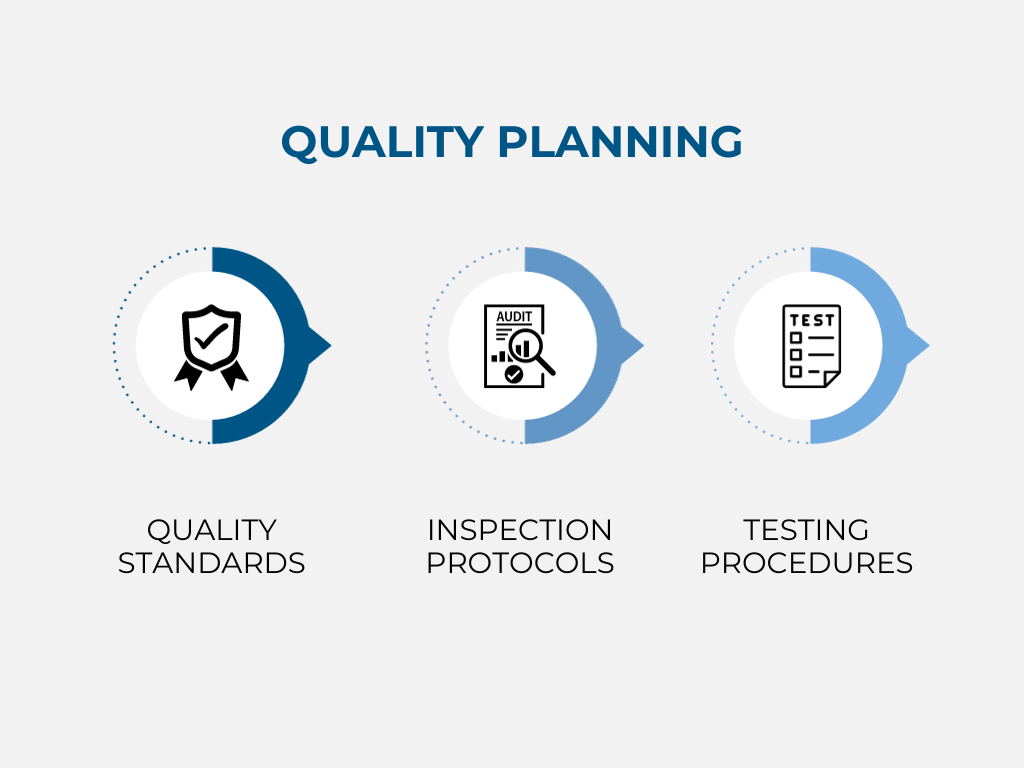
It should begin with setting clear and measurable quality goals aligned with the project’s overall goals.
This includes defining the criteria that will be used to assess the quality of materials, workmanship, and the final constructed product.
Of course, quality standards must be discussed with stakeholders and clients and be in line with industry standards.
Then, you can develop inspection protocols that outline the methods and frequency of inspections at various stages of the construction process.
Here, you also have to plan tests and checks across all phases to make sure that materials and components meet the specified standards.
For example, you must plan tests on materials such as concrete, steel, or other construction elements to verify their strength, durability, and compliance with industry regulations.
However, as Syed Gaiser Imam, consulting engineer at Integrated Engineering Services, points out:
“Testings are costly affairs for medium-sized projects, especially in developing countries and have to be managed with due consideration.”
So, during quality planning, you have to make sure that the tests you plan are indeed at the stage when they will show proper results.
What’s more, an essential part of quality planning is assigning roles and responsibilities.
That means you have to find a designated quality manager who will be responsible for the overall quality of the project.
It is also important to define the responsibilities that superintendents of your day-to-day operations on the site have in terms of quality assurance.
As you can see, quality planning is indispensable in the construction industry, laying the groundwork for delivering projects that meet and exceed expectations.
So, it is crucial to write a thorough quality plan that will indeed result in high-quality projects.
Safety Planning
And last but not least, the type of construction planning we will mention today is safety planning.
In essence, safety planning prioritizes the well-being of workers, minimizing accidents and ensuring strict compliance with safety regulations, including local and national standards.
It involves the identification of potential safety hazards, implementation of robust safety protocols, and continuous monitoring to create a secure working environment during all construction phases.
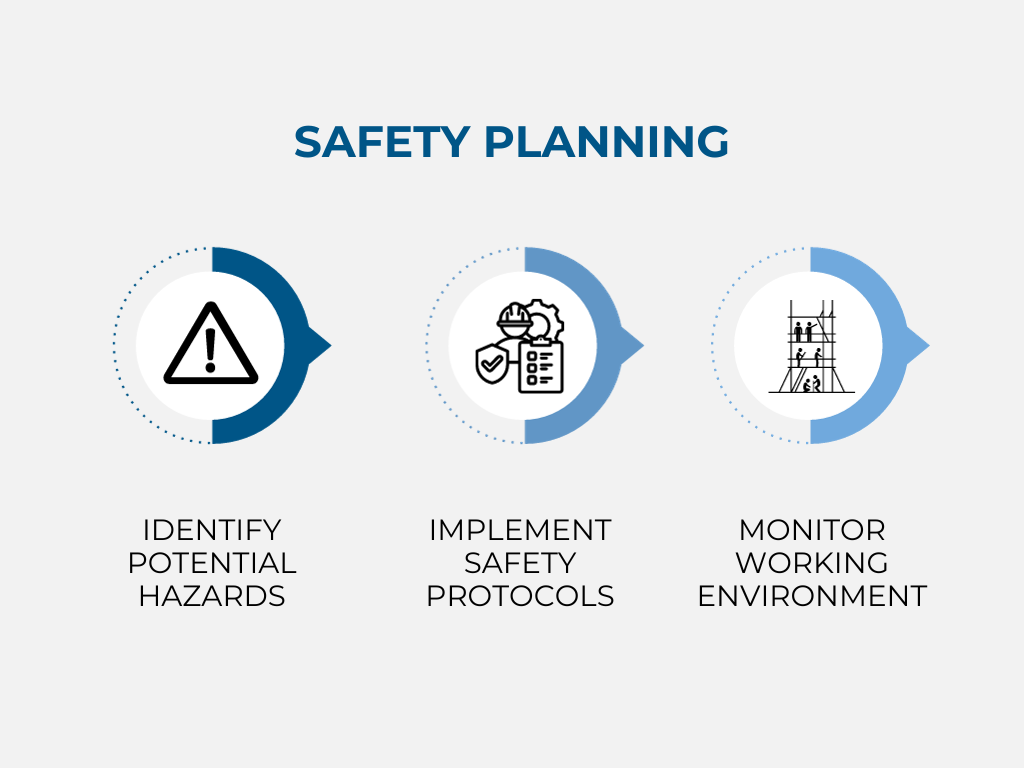
The first step in safety planning is identifying potential hazards that pose risks to employees, visitors, or even the surrounding environment.
Potential hazards may include anything from handling heavy machinery to working at heights or exposure to hazardous materials.
When you identify the hazards you deal with, you have to plan safety protocols.
This involves clearly defining step-by-step procedures for all aspects of the construction process, from equipment operation to emergency response protocols.
For example, hazardous material handling protocol would include:
- the use of appropriate personal protective equipment (PPE), such as gloves and goggles
- a clear and effective emergency response plan for accidental spills, leaks, or exposure incidents, including evacuation procedures
- procedures for the disposal of hazardous waste, including compliance with local regulations and guidelines
Your safety plan should also include regular training sessions and a plan to communicate safety guidelines to all your workers.
After all, only if every team member is well-versed in the protocols, your safety planning will yield results, and your company will foster a collective commitment to a safe working environment.
Continuous monitoring, which involves regular site inspections, safety audits, and the integration of feedback from your workers, should also be planned thoroughly at this phase.
In summary, safety planning is a cornerstone of responsible construction management, safeguarding the well-being of all involved parties.
Through hazard identification, implementation of safety protocols, and ongoing monitoring, you will successfully foster a culture of safety for your workers.
Conclusion
And that concludes our exploration of construction planning.
Understanding and implementing the six types of construction planning outlined here are crucial for every construction project manager and company owner.
It’s not merely about knowing them but about integrating these planning phases into your project management approach.
By carefully planning through each of these phases, your projects will align seamlessly with your company’s long-term goals.
What’s more, your projects will be executed on time, adhere to budget constraints and deliver the highest quality, all while committing to the safety of your workers.
Therefore, make sure to incorporate all these types of planning into your construction projects!