If you care about your business and revenue, equipment tracking is a must.
Why? It’s simple! Without it, you wouldn’t know where your equipment is, how much you use it or how often it requires repairs. You wouldn’t have an overview of insurance, depreciation, or ownership costs either.
Since you cannot run your business effectively without this information, we’ll explain how spreadsheets can help you track your equipment.
In this article...
What Does an Equipment Tracking Spreadsheet Include?
What information can you even get from a spreadsheet?
The good thing about spreadsheets is that you can customize them and add any information you find necessary.
If you don’t know where to start, here’s what most businesses track.
First, there is the baseline data, which includes identifying information such as the item ID or code, model, name, and quantity.
Of course, you should always know the purchase date and current condition of an item.

The asset details category should provide more information about the piece of equipment, like links to pictures and manuals. You can always list the price and seller to know where you got the tool and how much you paid.
Don’t forget to include maintenance details—you should know who’s in charge of equipment upkeep and how often it breaks down. On top of that, list the warranty and insurance details here.
The equipment usage section is essential for cost calculations. In this area, you’ll track how often a particular item is in use, who is using it, and how long they need the equipment.
You can always add a column for scheduling future use or maintenance.
Spreadsheets allow you to keep track of all relevant data about your equipment.
Why Companies Use Spreadsheets to Track Equipment
You might be wondering how you would even benefit from tracking your equipment through spreadsheets.
Let’s look at the four most common reasons why companies opt for this mode of equipment tracking.
Minimal Training Required
Many equipment tracking methods are complicated enough that employees have to be taught how to use them. This is why companies that can’t afford to spend time and money on additional training prefer spreadsheets.
After all, most people have already used spreadsheets at one point or another, making them the perfect tool for beginners.
Because spreadsheets are very intuitive, you don’t need to invest in detailed training. Instead, showing your team the essential functions and explaining what to put into each column will suffice.
A solution that requires little to no training saves you a lot of resources, which might be essential for your company, especially if you’re just starting out.
In short, spreadsheets are popular because they’re straightforward and easy to use.
Digitized Data
If you want to finally move on from pen and paper, you need to use spreadsheets.
Not only is the manual tracking of assets outdated, but it is also risky and inefficient.
Besides, when you rely on this form of tracking, your team can’t fill out the paperwork at the worksite or from home.
Instead, they need to wait until they get to the office to do it, so that someone can store the data.
Get rid of these obstacles by digitizing your data. That way, you also eliminate errors that arise from clumsiness or illegible handwriting.
Today, companies strive to make all their data digital.
Quick Access
Ease of access is a major advantage of spreadsheets.
When using a paper database, you have to go through many pages until you get to the asset page of the piece of equipment at hand.
Sometimes the data is not even filed correctly, costing you extra time and energy to locate it. Besides, you can only get to this data if you’re in the office.
However, you can access spreadsheets wherever you have an internet connection. There’s no shuffling through papers—a simple Ctrl+F will locate the data you need.
Since easy access saves time, spreadsheets are an excellent option for equipment tracking.
Information Filtering
When you track your equipment using paper, you can’t filter the data you need. Instead, you have to look through each document to locate it.
Let’s say you want to find all laptops that cost over $1,000. If you’re using a paper database, you’ll have to find all laptop-related entries and manually inspect them to see which ones fit the criteria.
Sounds exhausting? That’s because it is. With spreadsheets, you can simply look up two columns (asset category and price) to find all the equipment that fits the bill.
The choice between manual searching and making two clicks to get to the data you need is pretty easy, don’t you think?
The Downsides of Using Spreadsheets for Equipment Tracking
Nothing is perfect, and neither are spreadsheets, especially when it comes to equipment tracking.
Let’s take a look at the most critical drawbacks of relying only on spreadsheets as your go-to tracking tool.
They Require a Lot of Manual Input
Why would you do something manually if you can automate it?
One of the most significant flaws of spreadsheets is the fact that they’re labor-intensive.
When you first buy an asset, you have to enter all its relevant data into the spreadsheet and fill out every column. Of course, this doesn’t seem like much of a sacrifice if you get to reap the benefits of equipment tracking.
Nevertheless, if you consider that you’ll have to enter each future change by hand, it becomes a lot of work. Besides, it’s not just you who’s using the file—employees who use your equipment will have to access it and input new data, too.
Life is much simpler when you can just scan the piece of equipment to conduct those tasks automatically.
Spreadsheets Are Prone to Errors
Due to all the manual activity, spreadsheets are highly susceptible to errors.
Their greatest weakness lies in the fact that you can’t control who makes changes and how well they do it. When employees enter information manually, inaccuracies can easily occur.
Your team members might make a mistake because they are tired, or in a hurry or tired, leading to corrupt files that can hinder your future operations.
Don’t forget that spreadsheets don’t offer automated updates, so you have to edit each field by hand. Every update can lead to a mistake and compromise the reliability of the data.
Can you vouch for the validity of your spreadsheet data?
There Is a Lack of Data Protection
One of the downsides of spreadsheets is that protecting your data can be difficult.
If sensitive information about your equipment and assets falls into the wrong hands, you could be in big trouble. The main issue? It can easily happen.
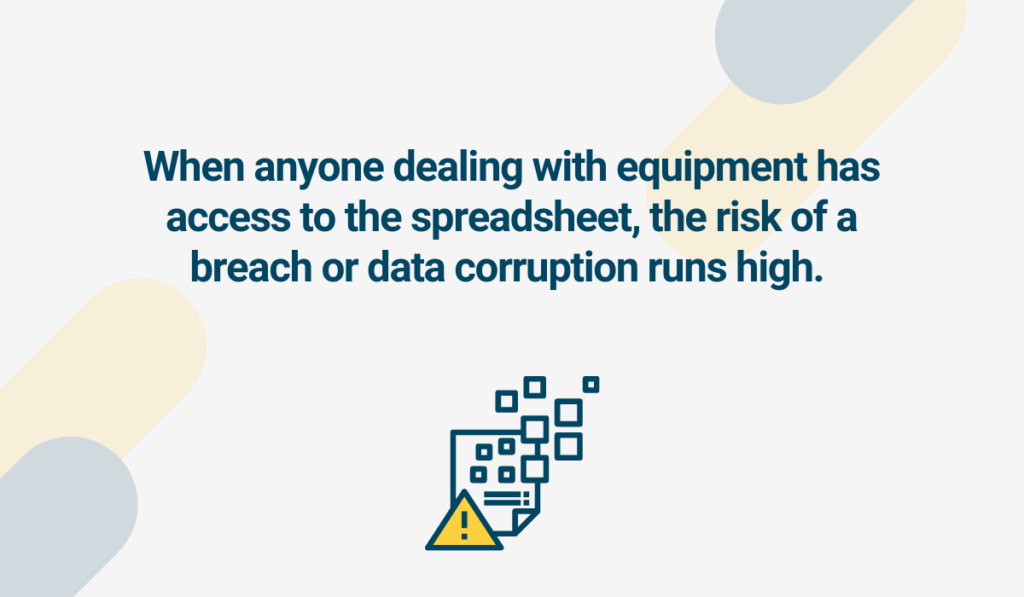
Think about it—anyone dealing with equipment has access to the file, including the operators, maintenance team, and your accountant. With so many people using the file, the risk of a breach runs high.
On top of that, anyone can copy and move spreadsheets, increasing the safety risks. Besides, people can transfer the spreadsheet to a USB and share it with others.
Therefore, if information safety is crucial for you, spreadsheets aren’t the best option for you.
Minimal Features Are Available
When tracking your equipment, you should be able to choose between different features.
Companies deal with different assets and find various uses for them. An equipment tracking tool should take all this into account.
Unfortunately, spreadsheets don’t, mainly because tracking is not their primary purpose.
What does this mean for you? You will only get the most basic options of adding rows, columns, and data filtering.
If you want to automate check-in and check-out procedures, have a detailed audit history, or add attachments, you have to look elsewhere.
Spreadsheets won’t support all the options you’d like to have, and you’ll outgrow them soon.
The extent of your tracking needs will help you determine the necessary features.
Spreadsheets Don’t Increase Accountability
Do you know who entered which information into your spreadsheet?
The answer is almost always no.
The tool doesn’t allow you to see who has accessed and edited the document. Therefore, you don’t know who to hold accountable for incorrect data.
However, you can access detailed equipment history with good asset tracking software.
With this option, you always know who has used an asset and when, how often the tool is in use, and how frequently it needs maintenance.
Such data can save you time and resources as well as make you more efficient.
Using specialized software for equipment tracking lets you assign responsibility for the data.
One Person Access
Multiple user access is the last thing an equipment tracking tool should limit.
Look at it like this: the more assets you own, the more you will use them. So, you’ll need to use your spreadsheets more often, meaning that quick access will be essential.
Spreadsheets aren’t exactly quick—they allow only one user at a time. While one employee is editing the file by hand, others have to wait for their turn.
This means you have to waste a lot of time and energy on making preparations instead of doing actual work.
Spreadsheets are therefore not the best option for companies with a large amount of equipment.
No Actual Location Tracking
Spreadsheets cannot pinpoint the location of your equipment.
The current user should write their name, the check-out, and the expected check-in date. However, that’s all you can see from your spreadsheet.
You won’t have insight into how often your employees use a particular item or where.
Why?
Spreadsheets don’t allow you to see the field’s history so you won’t know who has used the item before—you’ll only see the current user’s name.
Then, spreadsheets don’t give you the option to track your asset in real-time or know its last known GPS location.
If you want to know who is using your assets and where, replace spreadsheets with specialized software.
Spreadsheets Are Limited to Desktop Use
How can your employees access the tool-tracking spreadsheet?
Spreadsheets limit your options to desktops or laptops, wasting the potential of smartphones. Nowadays, most people own one, and businesses often give them out to contact field staff.
If that’s the case in your company, why not make the most out of that technology?
Your employees can only access a tool-tracking spreadsheet if they’re on a PC or laptop.
This is limiting their productivity. If there is an urgent update, they have to drop everything to get to the nearest acceptable device.
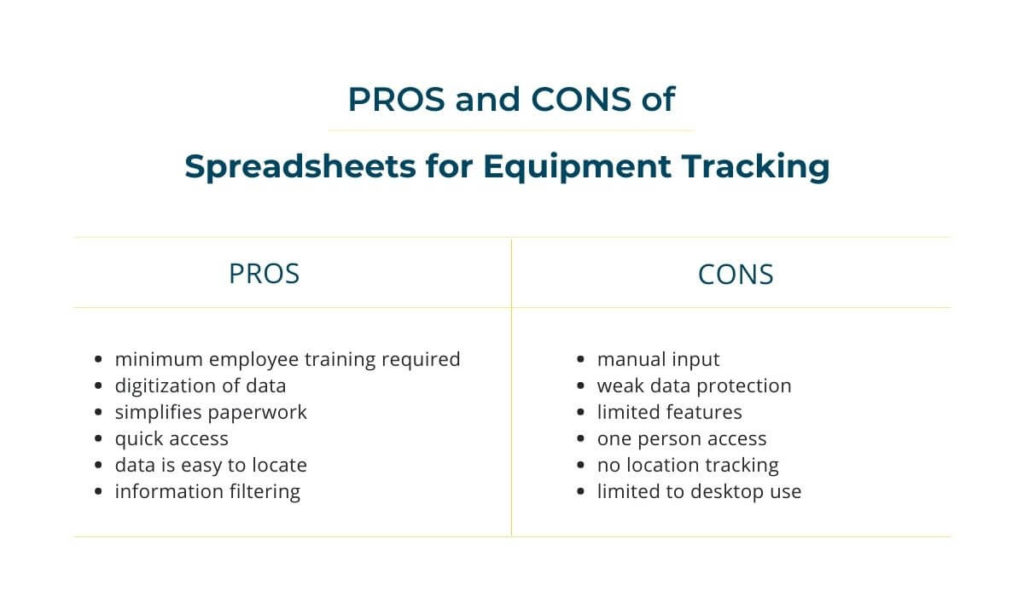
But if you use mobile-friendly software, your staff can access it whenever they have an internet connection. This option allows you to have real-time equipment updates without any hassle.
If easy access from the worksite is crucial for your team, you should strive to find an alternative to spreadsheets.
Why Is a Specialized Equipment Tracking App a Time Saver?
Ask yourself if spreadsheets offer all the time-and-effort-saving features you need.
If the answer is no, it’s time to switch to specialized equipment tracking software. Not only does such software have a lot more to offer, but it is also made with the purpose of asset monitoring.
What are some of its benefits?
- a single centralized system: an overview of all equipment data gathered in the same place
- data backup: automatic information storage in the cloud, accessible at any time
- easy integration: the ability to connect the software to other tools or apps you use
- 24/7 access: anyone with granted access can use the software whenever they’re using the internet
- real-time tracking: equipment status is updated on the spot, promoting transparency
- fewer manual entries: everything except the after-purchase data and extra comments is automatic
Monitoring applications allow you to track your equipment using QR codes, simplifying the whole process.
A simple scan leads you to the item’s page. There, you can see all the relevant data such as attachments, maintenance statistics, and pictures.
If necessary, you can update the information on the go.
Everything you have to know about a piece of equipment is available through a scan or manual search in the software.
Equipment tracking software offers all the features you need to monitor your equipment efficiently.
Conclusion
While spreadsheets may be helpful if you’re just starting and have a limited amount of equipment, you can’t use them for that purpose long-term.
Why? Because they weren’t made for it.
When you want to be as effective as possible at monitoring your equipment, choose tracking software that allows you to protect your data while offering 24/7 access from mobile devices for multiple users.
On top of that, it promotes accountability while letting you know where your equipment is.
If you prefer extensive and detailed tracking, specialized software is the way to go.