There’s nothing worse than when you’re working on a construction site and an essential piece of equipment breaks down, causing unexpected downtime and costly repairs.
And, of course, even costlier delays.
This is all too common if you don’t diligently keep track of your equipment maintenance.
And what better solution to track equipment maintenance than using software designed specifically for this purpose?
Today, we will give you six reasons why you should invest in such software and prevent your equipment from failing you when you need it the most.
Let’s dive in.
In this article...
Enables Centralized Data Management
When you’re juggling multiple pieces of equipment on numerous construction sites, keeping track of maintenance records can be a headache, leading to disorganization, inefficiency, and potential oversight of crucial maintenance tasks.
Cloud-based software offers a solution by consolidating all your equipment maintenance information into one centralized database.
Can you imagine having all your maintenance records, work orders, and inspection reports neatly organized in a single platform, accessible with just a few clicks?
With software, that’s precisely what you get—no more sifting through piles of paperwork or hunting down scattered files.
Furthermore, the software doesn’t just organize your data. It also tracks the service history of your equipment.
Need to know when a particular machine was last serviced or repaired?
The answer is right there at your fingertips, helping you make informed decisions about current maintenance needs.
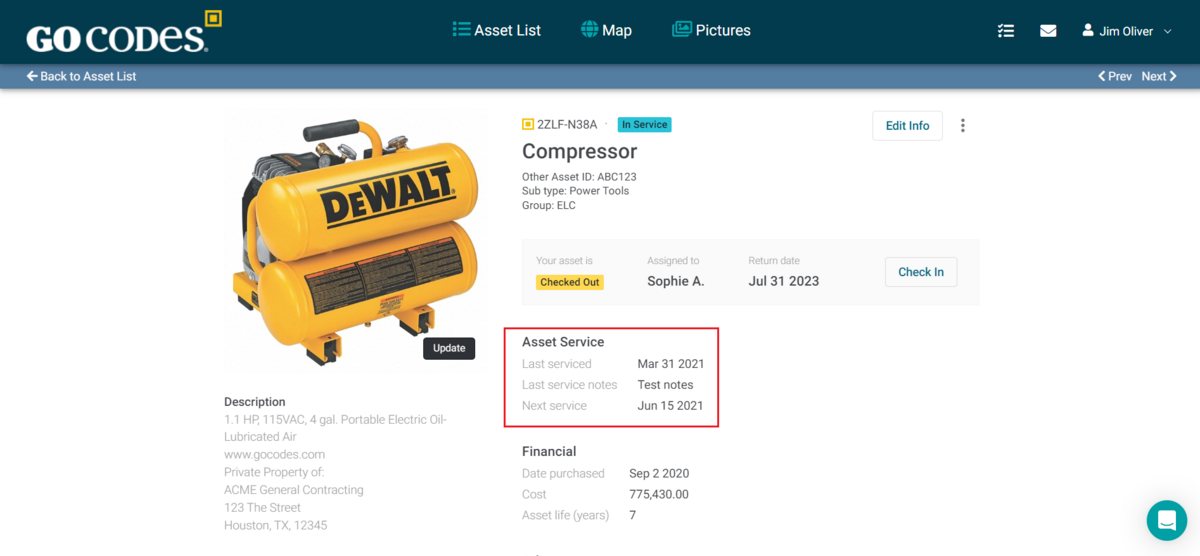
A software solution that exemplifies centralized asset data management is our GoCodes.
Essentially an asset tracking software, GoCodes is an all-in-one hub that also helps you manage asset data and maintenance records.
With GoCodes, you can keep all your maintenance information in one central database, including data on previous repairs, inspections, and services.
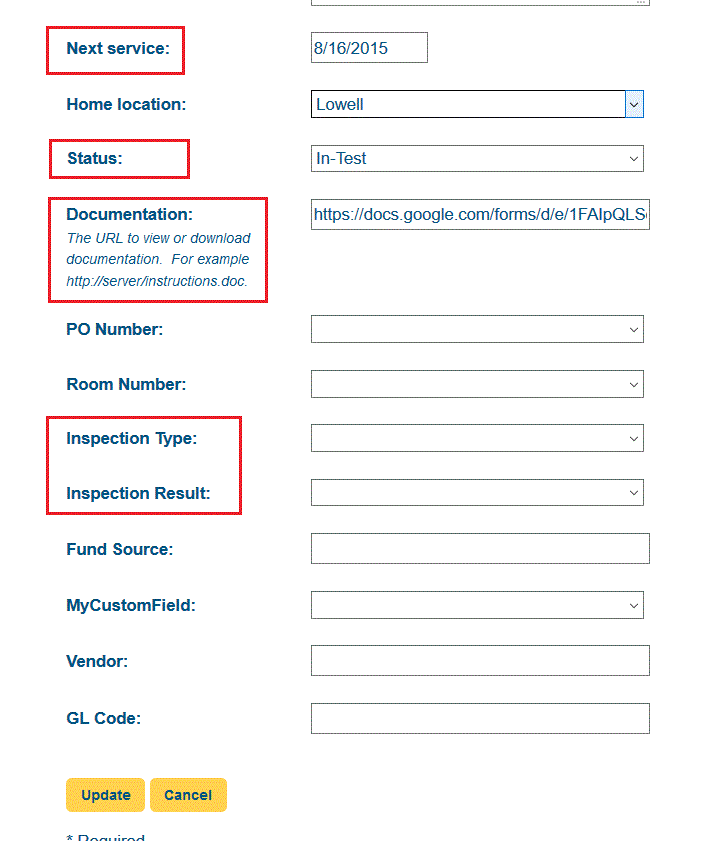
Since GoCodes is primarily a tracking tool, it comes equipped with QR code labels that you attach to your equipment.
These labels, paired with the user-friendly app, allow for easy scanning.
When someone scans a QR code, they can instantly access asset information, including status (such as in-service or in need of repair).
On the other hand, you can manage all your asset data from one centralized location, ensuring that all maintenance records are easily accessible whenever needed.
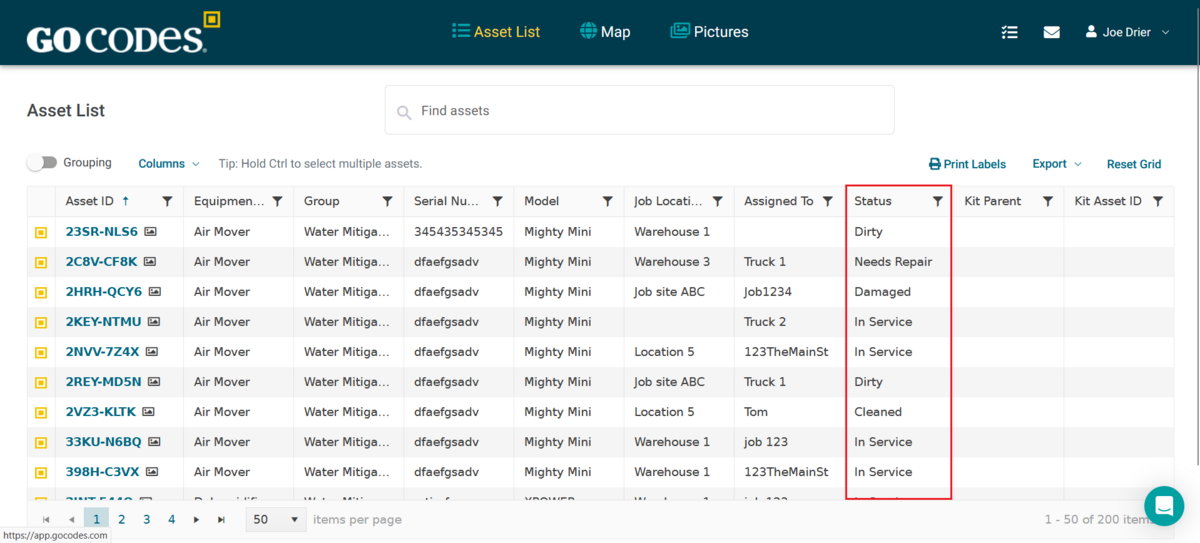
Rex Sherburn, a Heavy Equipment Mechanic at Hanford Mission Integration Solutions, stresses the importance of having such detailed insights into each piece of equipment:
“Having accurate information for individual equipment provides valuable information regarding its value, repair costs, depreciation, and maintenance program efficiency.”
With easy access to comprehensive asset data, including maintenance records, from one central database, you can make informed decisions that will help you keep all your assets at peak performance.
Improves Organization
With software, you can become much more organized, and that’s a fact.
Various software solutions will help you automate maintenance scheduling and even enable you to assign maintenance tasks to employees.
Take our GoCodes, for instance.
In addition to having maintenance data for each piece of equipment in one place, with GoCodes, you can assign maintenance tasks, such as changing oil or checking filters, to your employees.
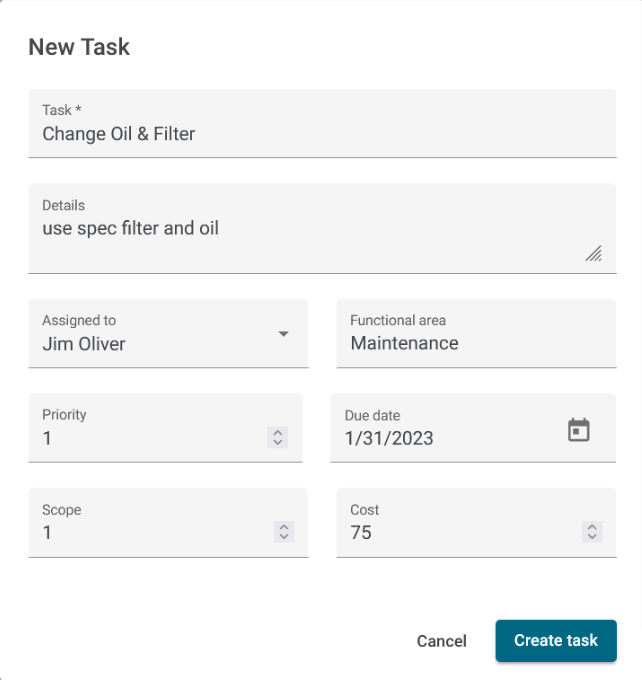
Of course, this is much easier to do when you have an equipment maintenance history in front of you and know what has to be done next.
Such a way of organizing work brings you significant benefits.
From making you more organized and saving you time in the first place, as now you can assign maintenance tasks in just a few clicks and have all information in one place, to reducing manual paperwork and juggling phone calls.
Not to mention reducing mistakes that come with manually organizing all this maintenance work.
On top of that, when work is organized through cloud-based software, everyone responsible can see what they have been assigned to.
This also minimizes the risk of overlooking maintenance tasks or not completing them on time.
In other words, better task organization means maintenance is more likely to be completed on time.
This, in turn, reduces the risk of equipment failures and unplanned downtime and creates a safe environment for workers.
Offers Real-Time Visibility
When it comes to managing equipment and maintenance activities on construction sites, having real-time visibility is crucial for ensuring smooth operations and minimizing equipment downtime.
Fortunately, many software solutions are designed to offer real-time visibility into equipment status, maintenance activities, and performance metrics.
This is crucial for making informed decisions on time.
Imagine this scenario: you’re overseeing a construction project, and suddenly, one of your critical pieces of equipment experiences a breakdown.
Although this is less likely to happen with software to track equipment maintenance, in the event it does, that same reliable software will help you.
Take, for example, the power of field service requests.
When workers encounter an issue with an asset, they can simply whip out their mobile phone, scan the piece of equipment, and send a direct message detailing the problem.
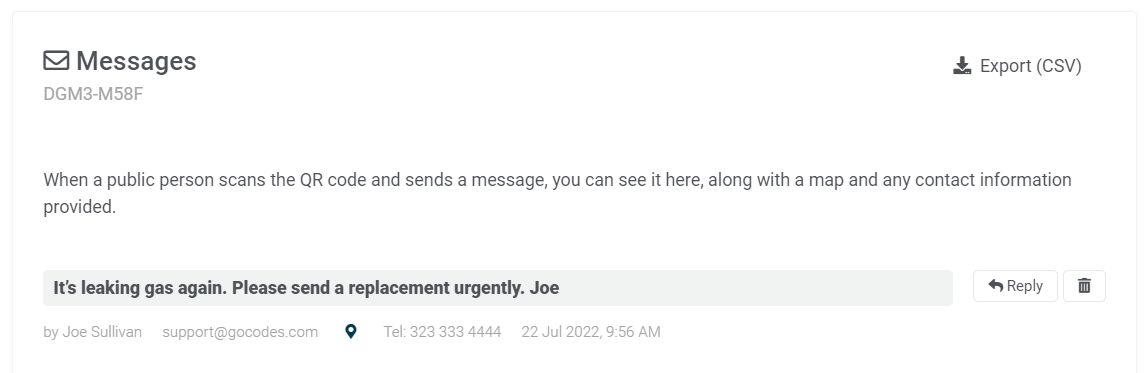
Instantly, you’re notified and armed with crucial information like GPS location and details of the issue.
This allows you to quickly arrange for a technician to address the issue or send a replacement piece of equipment to avoid delays.
This level of real-time visibility is a necessity on busy construction sites, as it translates to less downtime, fewer delays, and smoother operations.
So, the next time you encounter a construction challenge, rest assured that software for tracking equipment maintenance has your back.
It provides the clarity and agility needed to keep your projects moving forward.
Facilitates Proactive Maintenance
In addition to providing real-time visibility, software solutions are invaluable tools for facilitating proactive maintenance.
When managing a large number of assets and equipment, it’s all too easy to overlook maintenance tasks for some of them, with potentially dire consequences.
First and foremost, neglecting regular maintenance poses a significant risk to the health and safety of your employees.
Machinery and tools must undergo regular maintenance to ensure they function safely.
If that’s not the case, the consequences can be severe, as Howard Raphaelson, a lawyer representing workers who have suffered injuries due to such malfunctions, emphasizes:
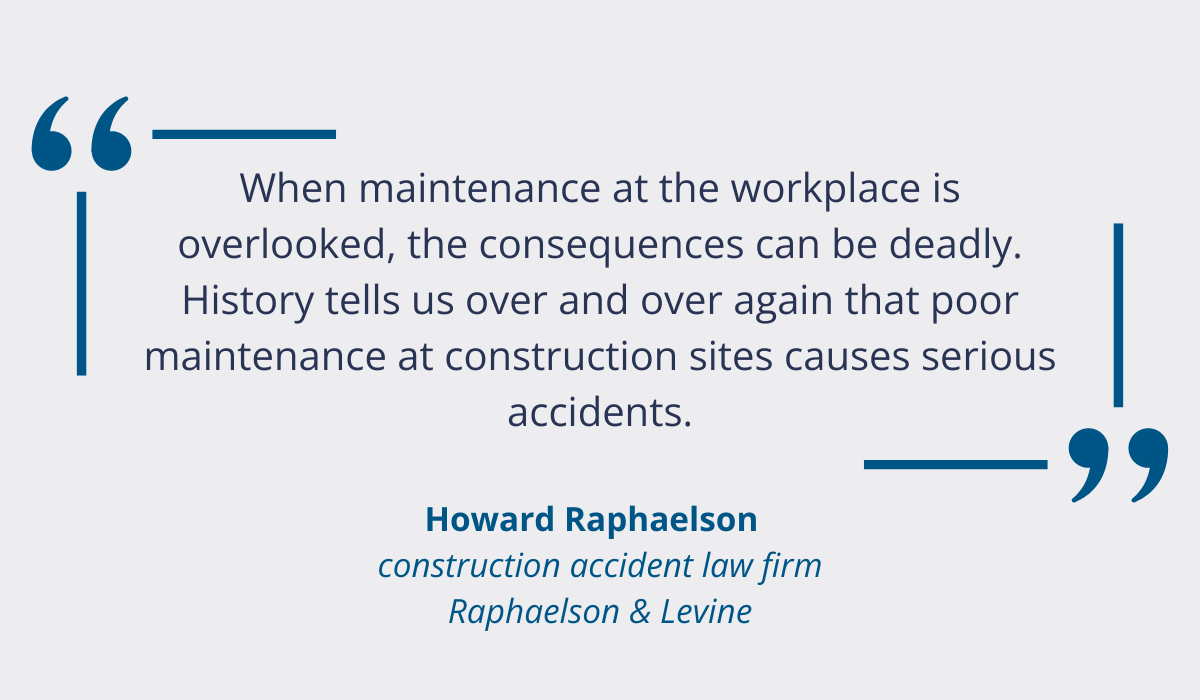
This sobering reminder underscores how important it is for every construction company to prioritize proper equipment maintenance, with the safety of workers taking precedence above all else.
Second, sudden equipment failures can result in costly downtime and repairs.
But it’s not just about the repair costs, points out Dan Corbett, equipment manager at Lancaster Development.
“It’s the collateral damage that really costs you money. Not so much the repair of a downed piece of equipment, but how that impacts the job.”
So, it’s also about lowered productivity, idle operators, and rental costs.
The key to avoiding both safety risks and unplanned equipment downtime is proactive maintenance.
Fortunately, equipment maintenance software offers a solution by automating alerts and reminders for scheduled maintenance tasks, inspections, and preventive maintenance activities, ensuring you never miss a maintenance task.
Below is one such reminder.
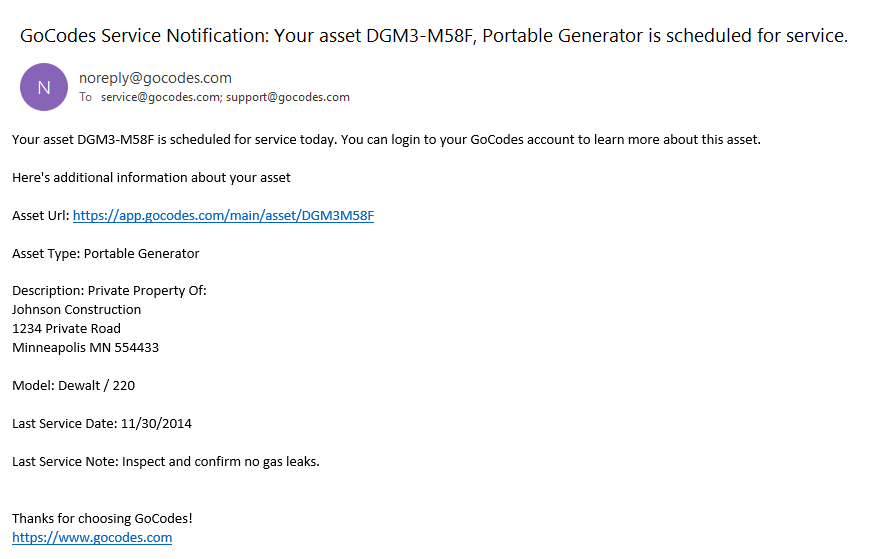
Such alerts help you stay on top of your maintenance schedules, mitigate the risk of equipment failures, and ensure that your workers always use safe and reliable equipment.
And—it makes you proactive rather than reactive!
Helps Identify Cost Saving Opportunities
Besides creating a safe environment and safeguarding you from collateral cost damage, using software to track your equipment maintenance will also help you identify cost-saving opportunities.
Let’s unveil what we have in mind.
For starters, staying on top of your equipment maintenance will prolong the equipment’s lifespan, ensuring that it retains its worth for a longer period.
By implementing regular inspections, lubrication, and part replacements, you can extend the operational life of your machinery, delaying the need for costly replacements or upgrades and saving you money in the long run.
But there’s more to it.
Through data analysis and performance monitoring facilitated by the software, you may identify opportunities to optimize maintenance practices.
This could include adjusting maintenance intervals, implementing more efficient maintenance procedures, or identifying cost-effective alternatives for parts or services.
For example, software may reveal that certain equipment requires less frequent maintenance than originally scheduled, allowing you to reallocate resources and reduce unnecessary expenses.
And last but not least, when you are on top of your maintenance tasks, which software allows you to be through one centralized platform, this can lead to labor cost savings.
For example, just scheduling maintenance repairs will save you hours of time, as you can now do it in just a couple of clicks.
Let’s round this off with a real-life example from Zefiro, a pile-driving corporation based in Southern California.
Their General Superintendent, Mike Buntich, highlights the financial benefits of preventive maintenance facilitated by such software:
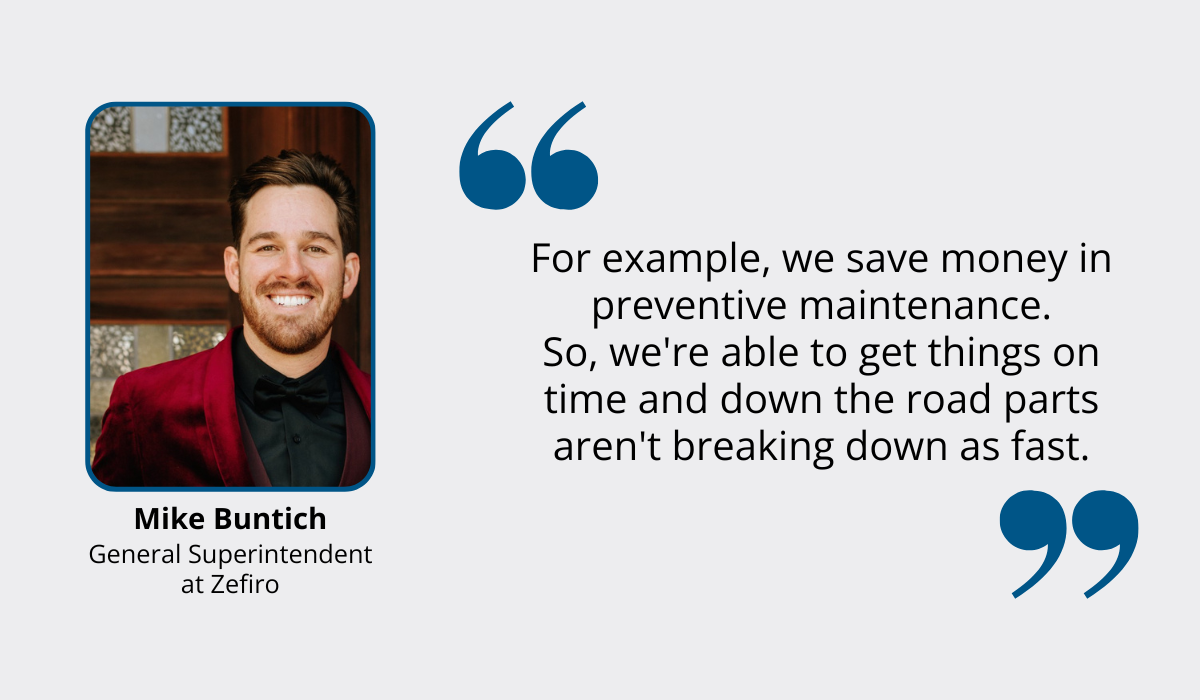
Finally, McKinsey’s statistics confirm the benefits we listed, stating that companies that have embraced digitalization and automation in their maintenance processes experience notable improvements.
Specifically, they report a substantial boost in labor productivity and a significant reduction of 20 to 30% in maintenance costs.
This fact alone might inspire you to adopt software for tracking equipment maintenance at your own construction company.
Enhances Collaboration
When it comes to managing equipment maintenance, effective collaboration is key.
Software solutions designed to track equipment maintenance have an important role in improving collaboration among various stakeholders, including equipment operators, maintenance technicians, supervisors, and management.
Why, you wonder?
Well, by now, it is clear that cloud-based software provides one centralized platform with data on your equipment—including maintenance data such as:
- previous maintenance records,
- equipment manuals, and
- safety guidelines.
So, whoever needs information on this can access it easily.
This is especially valuable for field technicians, who can now quickly access the information they need to perform maintenance tasks efficiently and in compliance with regulations.
Take a look at the firsthand experience of a GoCodes client that highlights precisely this benefit, enhancing how their technicians carry out their work:
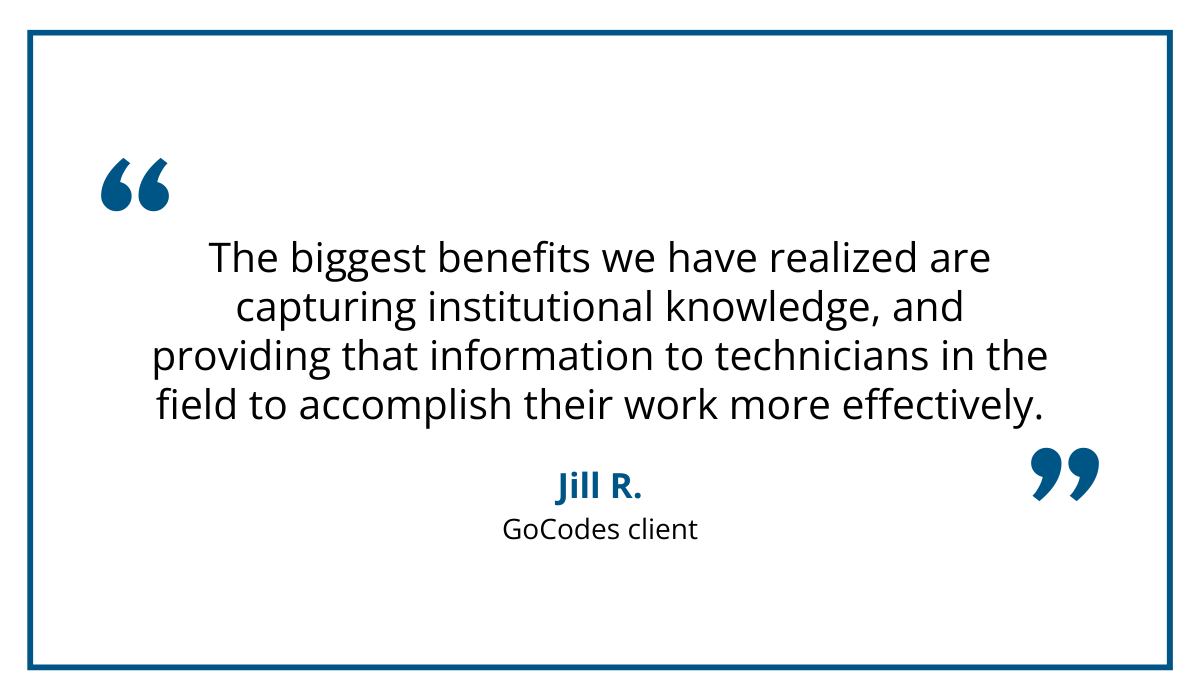
Naturally, it’s essential to ensure that your staff is well-trained in maintenance procedures to maximize the benefits of collaboration.
We’ve prepared a comprehensive guide on maintenance training, which we encourage you to explore for further insights.
All in all, by leveraging cloud-based software, you can streamline maintenance processes, improve communication among team members, and ultimately achieve greater efficiency and productivity across your organization.
Conclusion
As we saw today, using software to track equipment maintenance would be smart for many great reasons.
From enabling centralized data management to facilitating proactive maintenance and enhancing collaboration, these solutions offer numerous benefits for construction companies.
By leveraging technology, you can streamline your maintenance processes, improve operational efficiency, and, ultimately, save time and money.
It’s more than clear that, with access to real-time data, as well as the ability to identify cost-saving opportunities and ensure compliance with regulations, maintenance tracking software has become indispensable in today’s construction industry.
So, embrace this software and reap the benefits it brings!