Key Takeaways:
- 75% of professionals already follow proactive equipment maintenance.
- Daily inspection templates should adjust for seasonal conditions.
- Manual maintenance logs and spreadsheets can’t keep up with assets across job sites.
- High-quality parts safeguard both equipment and your bottom line.
Construction equipment sets the pace for every project, which means that proper maintenance is what separates seamless progress from costly delays.
By adopting best practices such as smart scheduling, operator training, and using high-quality parts, you’re safeguarding both assets and workers while keeping projects profitable.
The following sections break down exactly why these practices matter and how to put them into action.
In this article...
Schedule Maintenance Strategically
Maximizing equipment uptime requires you to anticipate problems and plan maintenance strategically, not wait for things to break.
When your company relies on excavators, cranes, and other essential equipment to keep projects moving, smart scheduling is one of the most effective ways to prevent costly downtime and keep your job sites productive.
Limble CMMS found that 75% of maintenance professionals in manufacturing already practice proactive maintenance.
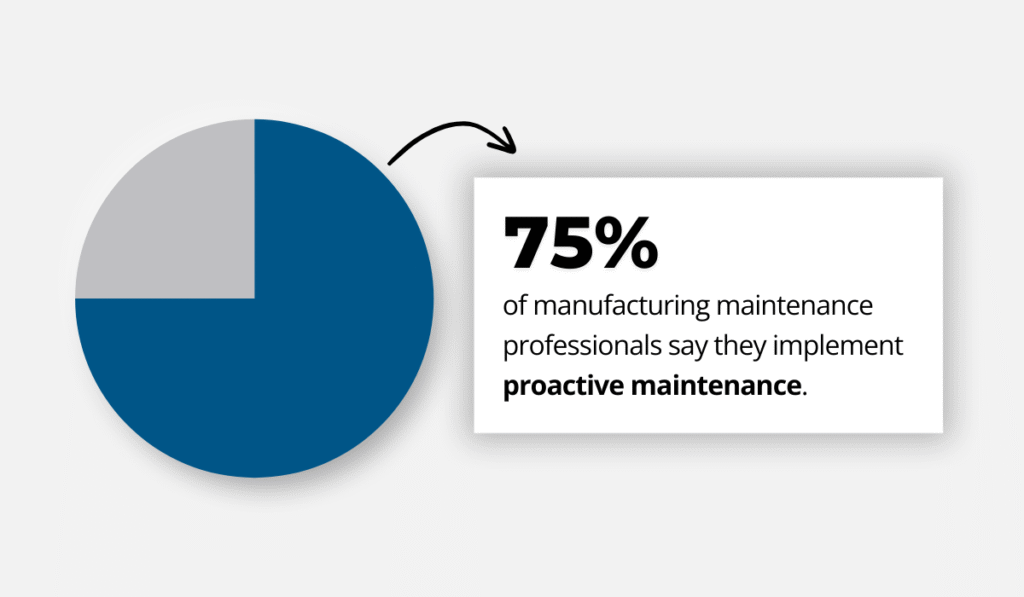
Illustration: GoCodes Asset Tracking / Data: Limble
While manufacturing may look different from construction, the principle is the same: waiting until critical equipment failure is a gamble with massive financial and safety risks.
But with strategic maintenance scheduling, you’re ensuring these efforts become a key performance driver instead.
At its core, proactive maintenance comes in three flavors:
- Periodic, following OEM intervals
- Condition-based, using real-time indicators to decide when action is due
- Planned corrective, delaying minor fixes until resources align
You don’t need to master every type. What matters is using scheduling to prioritize assets, coordinate resources, ensure parts availability, and avoid being caught off-guard in general.
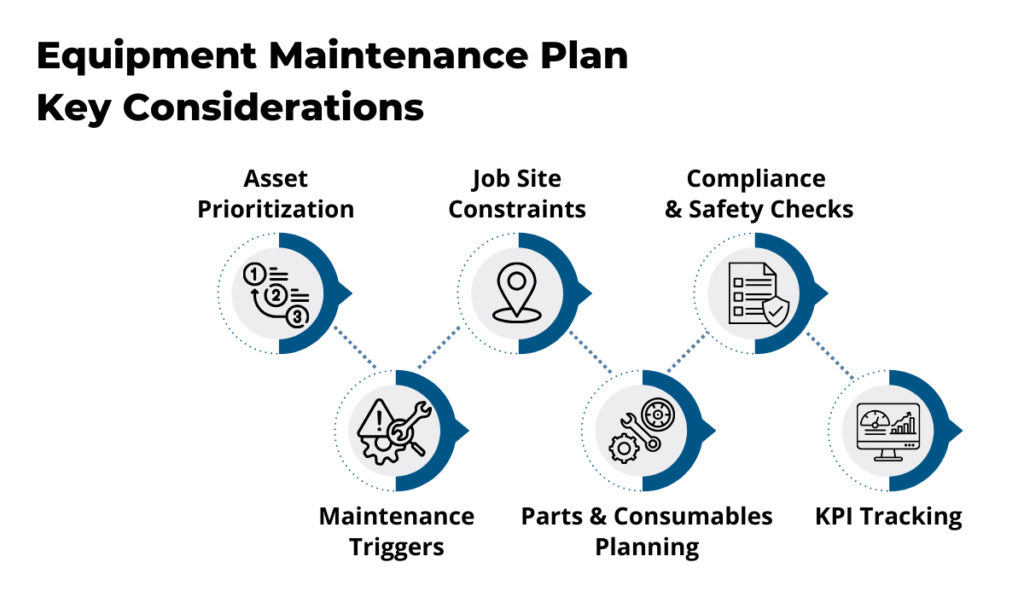
Source: GoCodes Asset Tracking
For construction, proper timing is crucial.
If you know that your graders and pavers will be running nonstop from May through September, doesn’t it make sense to schedule heavy maintenance in March or April?
By factoring in seasonal demands, your equipment enters peak season in top shape, instead of breaking down when you can least afford it.
Bret Kasubke, Director of Customer Equipment Solutions at United Rentals, reinforces this point:
“Contractors need to adapt equipment maintenance to the seasons. Tailoring actions to the specialized needs of equipment during the summer can help contractors protect workers and maximize productivity.”
This is why scheduling can’t be an improvised activity.
A formal maintenance plan or calendar, even if it’s a simple spreadsheet, should integrate OEM recommendations, seasonal workloads, and your company’s operational priorities.
And remember, the plan shouldn’t just cover mechanical assets.
As Jim Whittaker of JLL notes, HVAC units and other “background systems” often fall victim to deferred maintenance, but their failure can be just as disruptive and expensive.
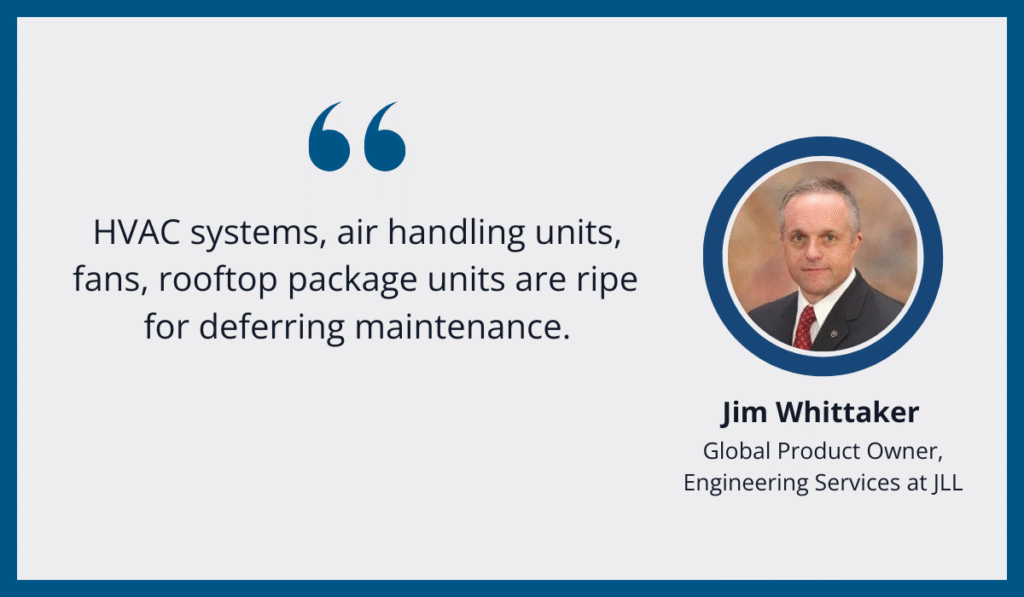
Illustration: GoCodes Asset Tracking / Quote: Buildings
If unexpected breakdowns occur, you’re left to scramble for replacements.
Conversely, when you take scheduling seriously, you reduce the risk of emergency breakdowns while aligning your entire company around a clear, proactive maintenance culture.
Ultimately, this saves you money, boosts uptime, and supports safer, more efficient projects in the long run.
Conduct Daily Inspections
Daily inspections are your company’s first line of defense against costly failures.
No matter how carefully you’ve scheduled maintenance, if your operators skip daily checks, small problems will eventually slip through the cracks.
And as business owners and construction managers well know, a minor leak or loose belt today can quickly escalate into a repair that sidelines your entire project tomorrow.
Overlooking daily inspections doesn’t just risk downtime—it can put a huge dent in your budget and compromise safety.
Buildern estimates that equipment costs hover around 5–10% of total construction project costs.
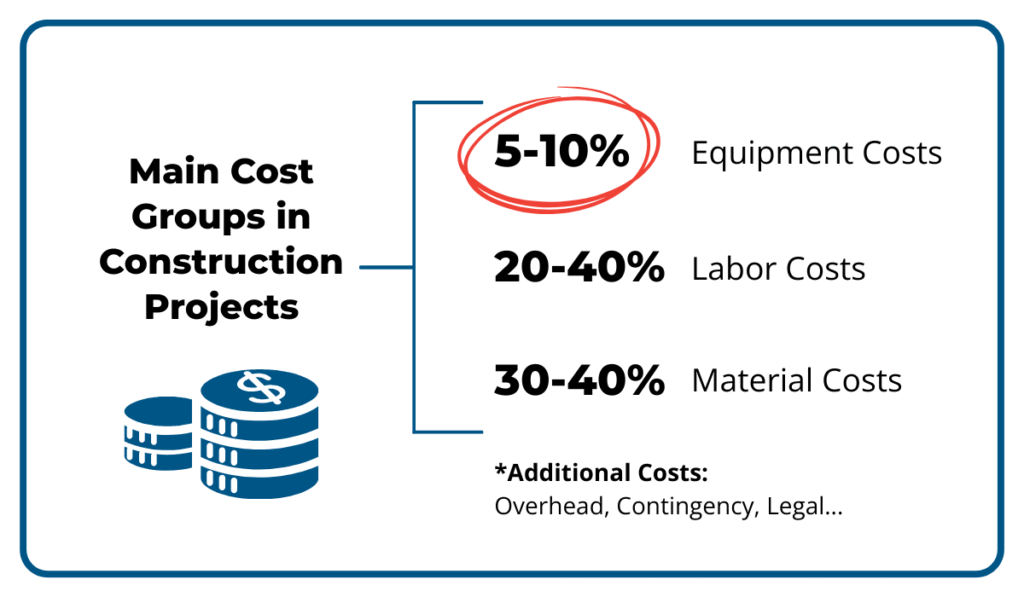
Illustration: GoCodes Asset Tracking / Data: Buildern
However, once you factor in both ownership and operating expenses, EquipmentWatch estimates that figure to be anywhere from 10% to over 50%.
That’s why daily checks need to be clearly defined and executed flawlessly and consistently.
Start by outlining which tasks must be done every day, compared to those that are part of weekly or monthly routines.
For instance, checking fluid levels and doing a quick walkaround are daily items, while lubrication or filter replacement may follow a longer cycle.
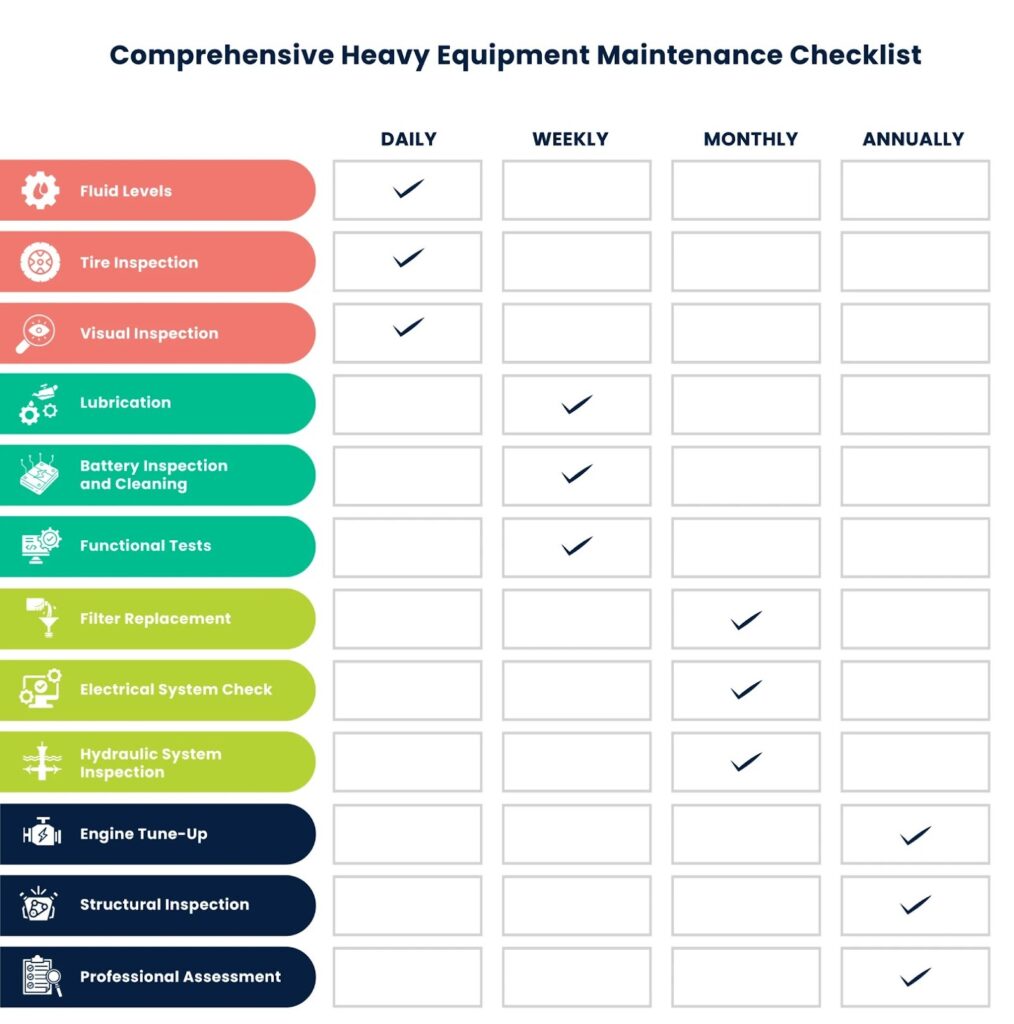
Source: Click Maint
Once you’ve defined the basics, it helps to see how they play out in practice.
The video below shows a daily inspection of a wheel loader, demonstrating how simple steps, when followed every day, keep equipment in working order.
Source: CAHill Tech on YouTube
Of course, the needs of your construction business won’t stop at one piece of machinery.
You’ll need a standardized checklist that applies across assets but can be adapted per machine.
A solid daily inspection template should cover coolant and oil, grease points, belts and hoses, hydraulics and air filters, tires, brakes, and the cooling system.
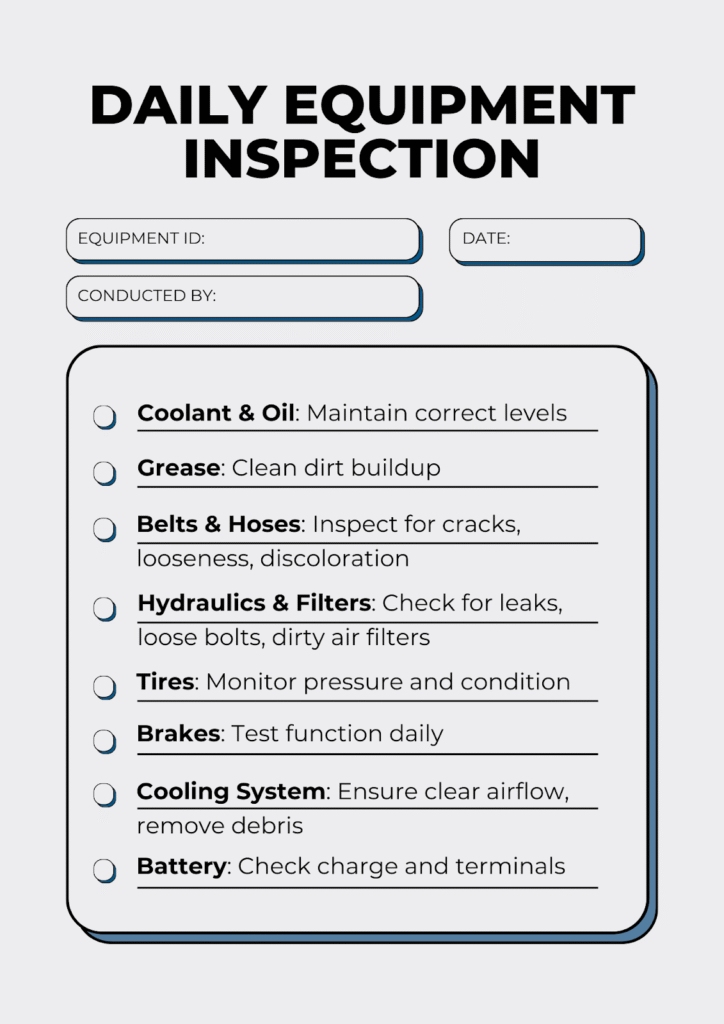
Source: GoCodes Asset Tracking
You’ll also want to consider season-specific risks.
In summer, heat accelerates wear through overheating, grease thinning, tire blowouts, and brake fade. Meanwhile, the winter season causes the fluids to thicken, hoses to crack more easily, and batteries to drain faster.
Adjusting your checklist for these realities makes inspections far more effective.
All in all, daily inspections may feel routine, but they’re the simplest, most cost-effective way to protect uptime, extend equipment life, and keep your projects running safely without surprises.
Maintain Accurate Records
Accurate maintenance records guide equipment upkeep, ensuring operational efficiency, safety, and compliance.
When you track every service, inspection, and repair done on your equipment, it’s easier to spot early warning signs, identify repeat issues, and understand when a machine is starting to cost more to maintain than it’s worth.
More importantly, incomplete histories contribute to unsafe conditions.
Eurostat data shows that 27.4% of fatal workplace accidents in the EU stem from losing control of a machine, tool, or handling equipment.
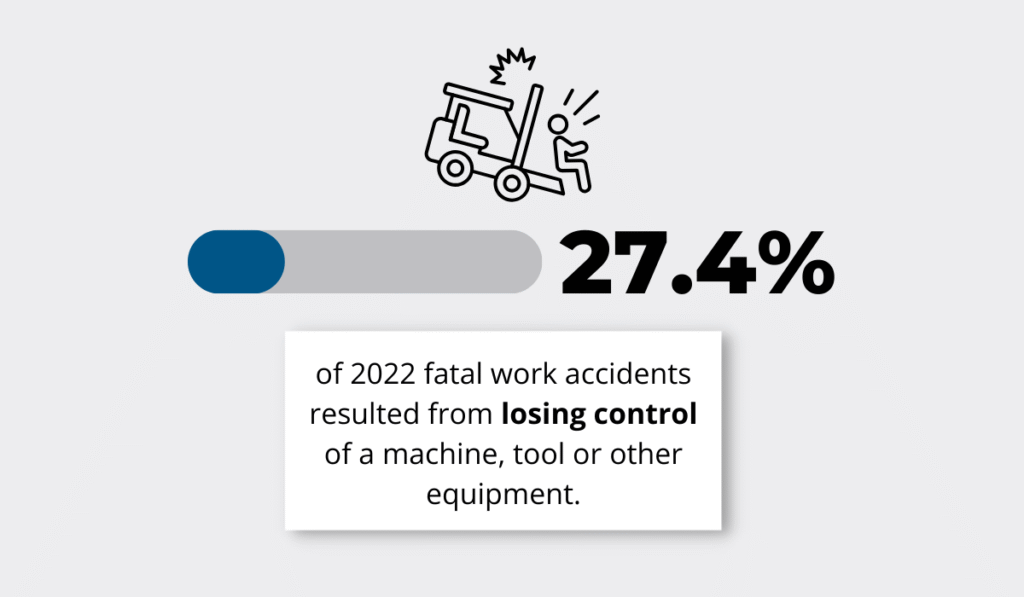
Illustration: GoCodes Asset Tracking / Data: Eurostat
While not all these incidents can be traced back to poor maintenance, the failure to keep track of your assets’ conditions and service history increases safety risks.
Industry experts agree.
As Andrew Noel, Project & Construction Management Specialist at DHN & Company, puts it, many machinery-related incidents are preventable when you practice proper maintenance.
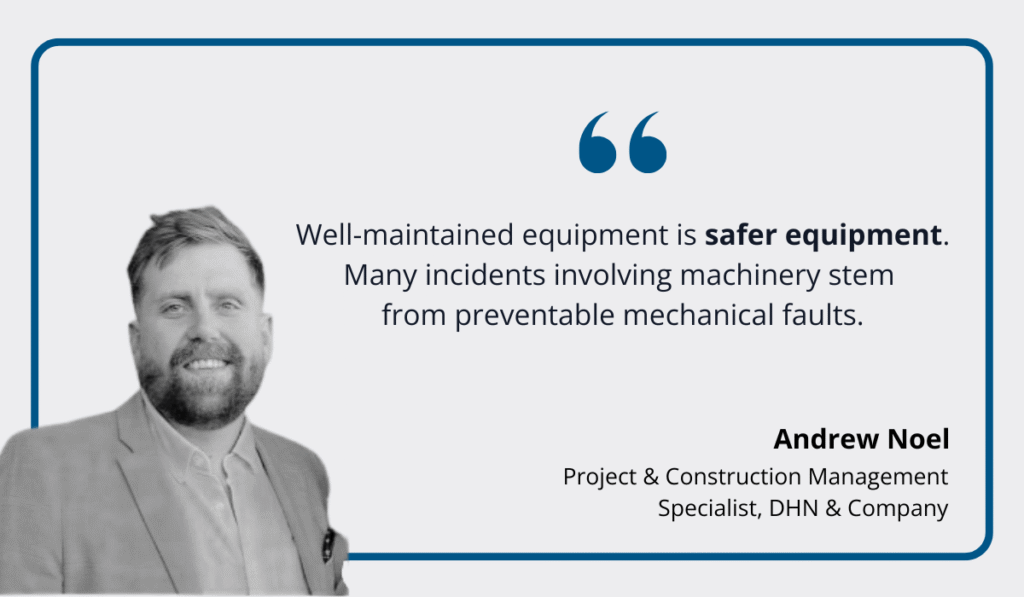
Illustration: GoCodes Asset Tracking / Quote: LinkedIn
A recent study also confirms that improving maintenance practices, such as keeping maintenance logs, is a key factor in accident prevention.
So, how do you keep track of maintenance efforts?
Besides manual logs, there are plenty of Excel templates for simplified asset tracking and creating service schedules that can be archived for future reference.
Source: Ashley N. Cameron on YouTube
However, these systems quickly fall apart once you’re managing multiple assets across multiple job sites, as they make it hard to track historical data and keep documentation organized.
In other words, for companies that are serious about safety and efficiency, software is the only viable solution.
Field-first platforms like GoCodes Asset Tracking make things easy by centralizing your asset list and giving you real-time access to each machine’s service status from any device.
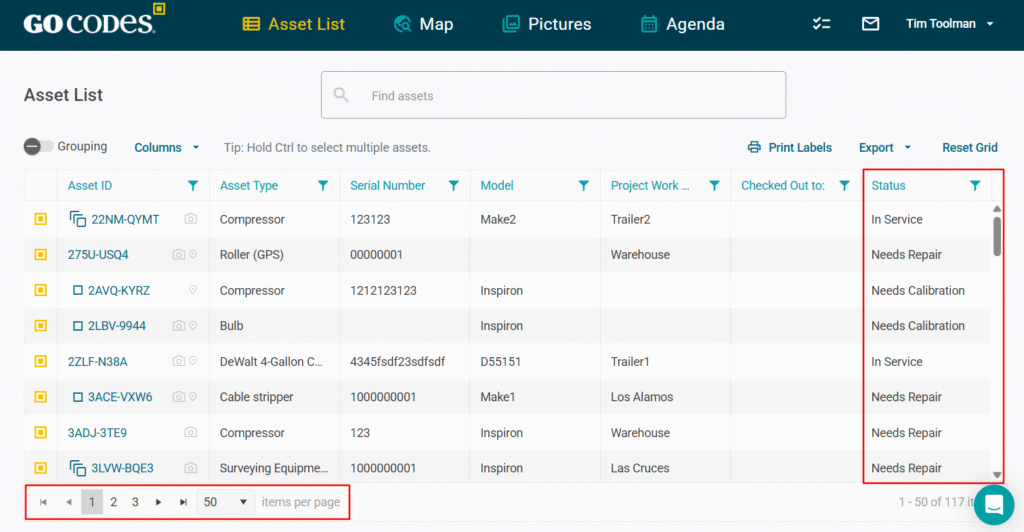
Source: GoCodes Asset Tracking
And when you enter individual records, you can access each asset’s check-in/check-out histories, manuals, and full maintenance histories.
The service log also lists key information about upcoming tasks, from the assigned technician and due date to estimated costs of the intervention.
Source: GoCodes Asset Tracking
On top of all that, GoCodes Asset Tracking comes with powerful built-in reporting.
You can easily prepare key documentation for inspections, use utilization insights to maximize asset lifecycle, or track depreciation to strike the best resale value.
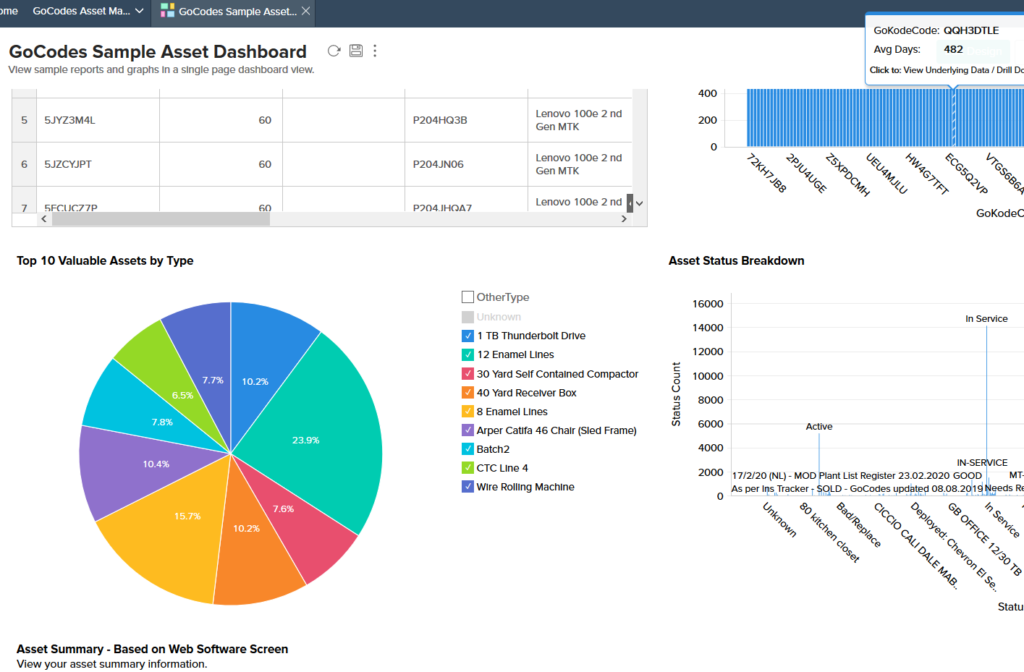
Source: GoCodes Asset Tracking
Whether you choose GoCodes Asset Tracking or another asset management solution, the benefits of accurate, accessible records are palpable.
Instead of putting your company at risk, you’re creating safer job sites and a more efficient, cost-effective operation.
Thoroughly Train Your Operators
Thorough operator training is another essential prerequisite of effective equipment maintenance.
This is in large part due to operator misuse being one of the most common causes of premature wear or outright damage to equipment.
As this Reddit thread illustrates, mechanics frequently complain about operators lacking even basic knowledge.
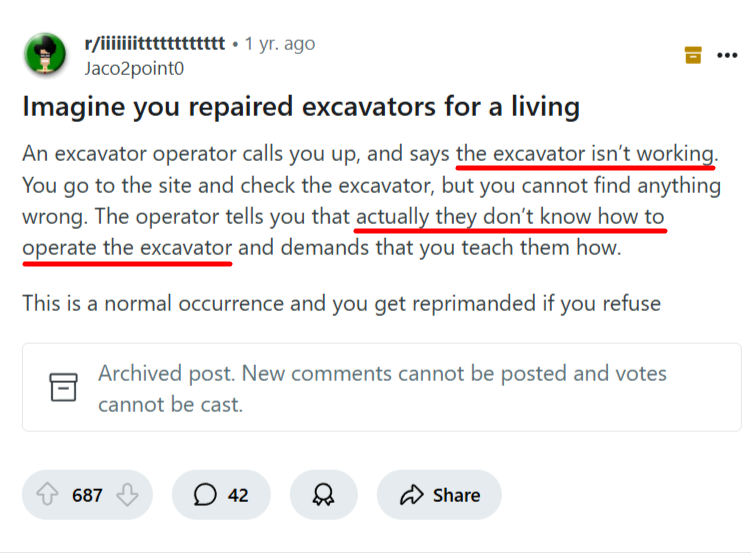
Source: Reddit
While the example exaggerates for effect, the central idea is true: many costly issues stem from operators ignoring warning signs or simply never learning how to handle equipment properly.
Well-trained operators, on the other hand, not only use assets more efficiently but also detect and report issues before they escalate.
A survey of 3,215 plant maintenance leaders revealed that technical expertise and response speed are the most valued qualities in a service partner.
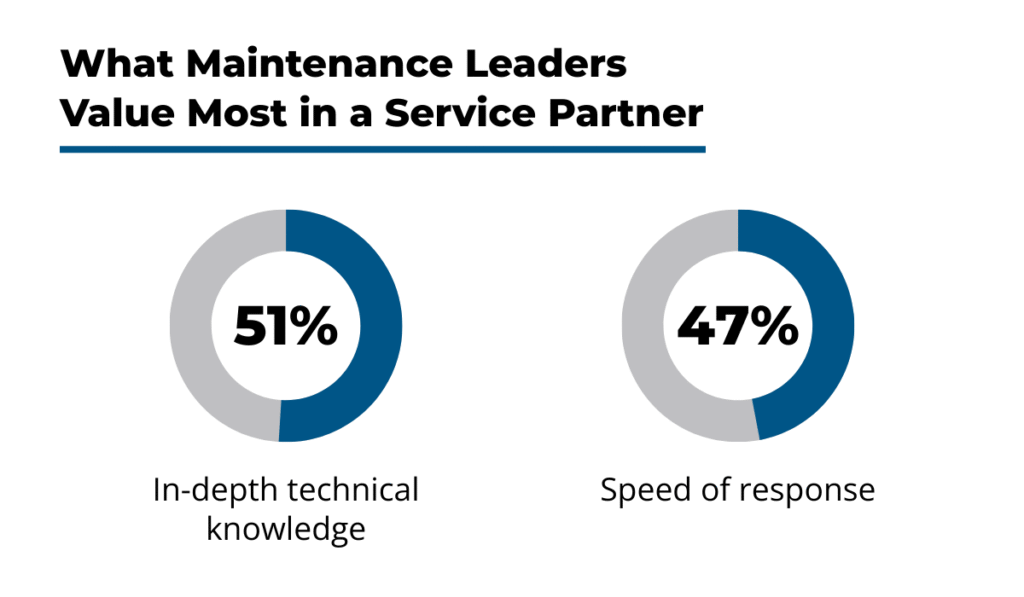
Illustration: GoCodes Asset Tracking / Data: ABB
Your operators don’t need to reach the level of outside specialists, but the better trained they are, the more value they bring to your projects.
A good example comes from Simmons Feed Ingredients (SFI), a facility that faced repeated equipment failures due to inadequate lubrication practices, poor oil storage, and no oil analysis program.
To fix this, SFI enlisted Noria to establish clear lubrication standards and train staff on which oil to use under specific conditions.
The results of implementing Noria’s Lubrication Program Development and training were dramatic: cleaner oil, fewer failures, uninterrupted production, and annual savings of up to $1 million.
As explained by Kyle Rubeck, the company’s Lead Reliability Technician, these results wouldn’t have been possible without formal training.
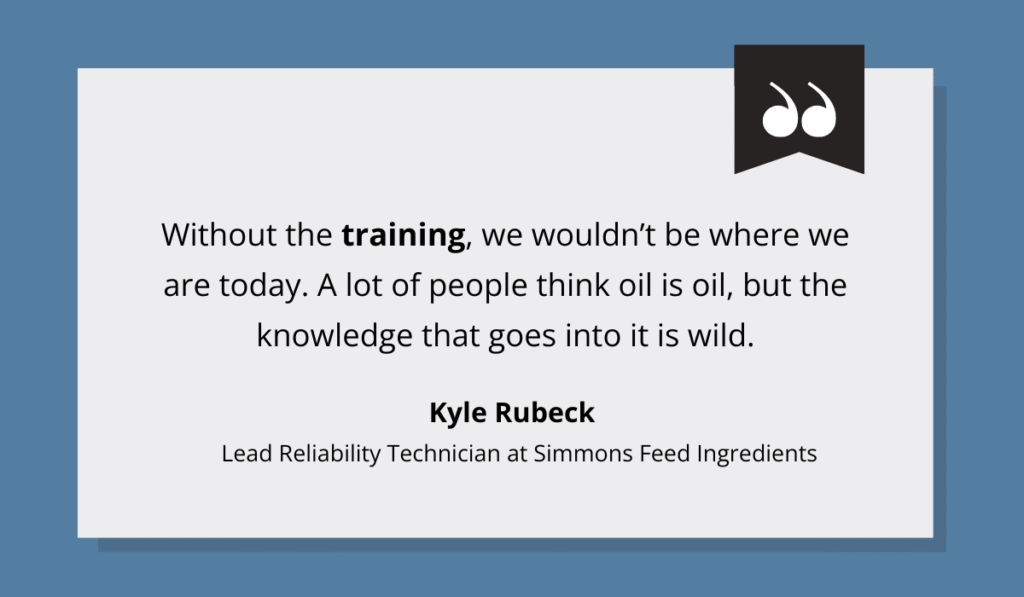
Illustration: GoCodes Asset Tracking / Quote: Noria on YouTube
The same principle applies in construction.
Beyond lubrication and fluid management, operators should be trained in daily inspections, efficient operation, and general job site awareness.
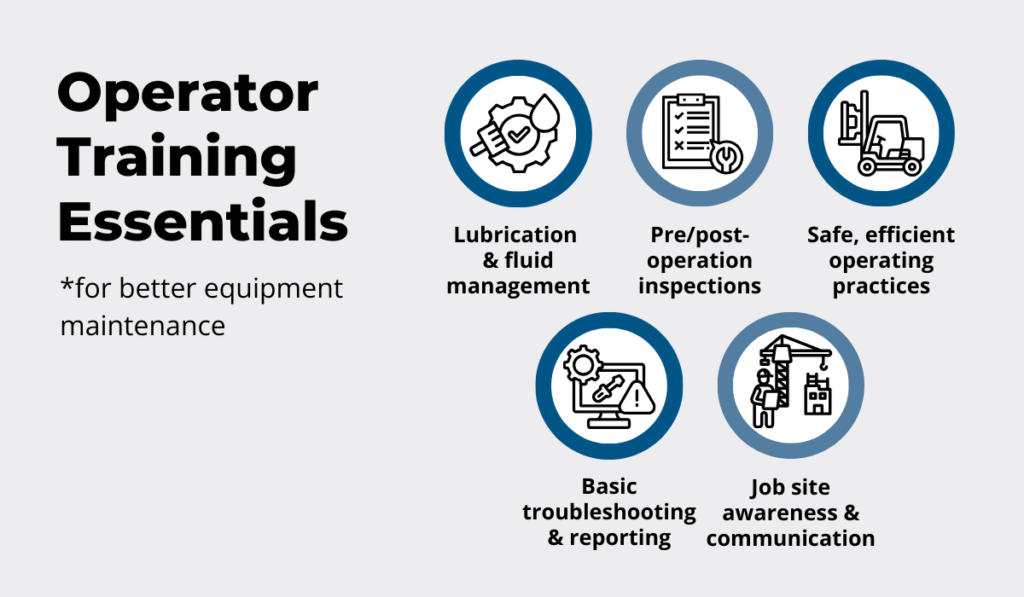
Source: GoCodes Asset Tracking
All of these skills tie directly back to maintenance.
Operators prevent premature wear, catch problems early, and provide the frontline feedback that informs maintenance planning.
As Tim Newman, Maintenance Manager at SFI, explains, operator insights are often what guide service schedules and troubleshooting efforts.
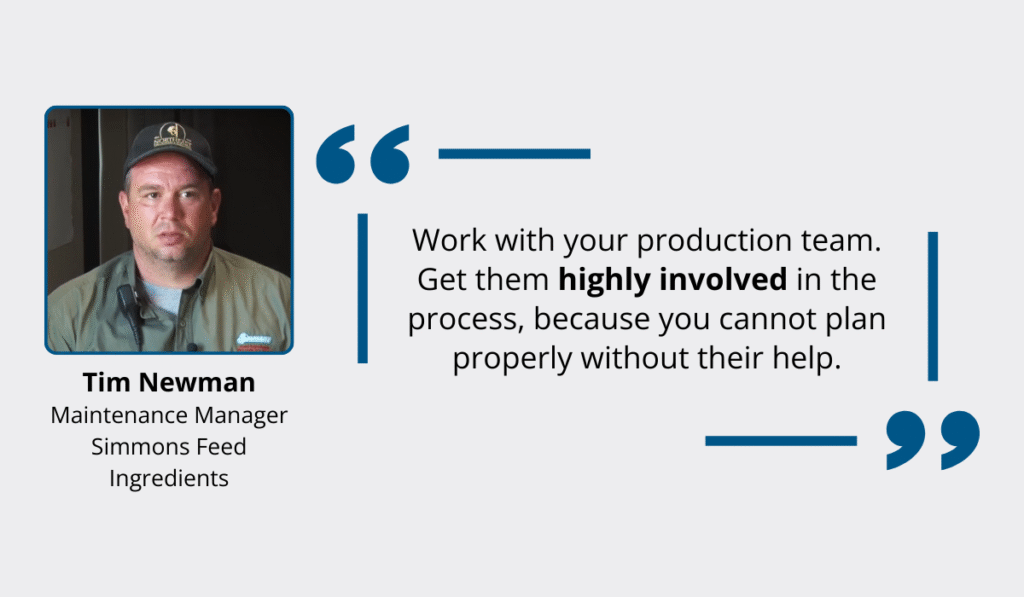
Illustration: GoCodes Asset Tracking / Quote: Reliable Plant
And this strategic scheduling is exactly what we highlighted earlier in this guide.
The bottom line is that when you invest in operator training, you’re doing more than reducing mistakes.
You’re equipping your frontline staff to actively extend equipment life, prevent downtime, and strengthen your company’s entire maintenance program.
Use High-Quality Replacement Parts
High-quality replacement parts protect your equipment, your workers, and ultimately your investment.
They’re the building blocks of your entire maintenance program, which is why it pays to think long term.
If you choose the cheapest available component, you may save upfront, but you’re also inviting premature wear, unexpected breakdowns, and higher lifecycle costs.
Quality, in this context, means:
- Durable materials that withstand heavy-duty use
- Reliable manufacturing processes tested for consistency
- Warranties that signal confidence in performance.
To illustrate, Volvo highlights how its OEM engine filters extend asset life, reduce wear, and minimize downtime.
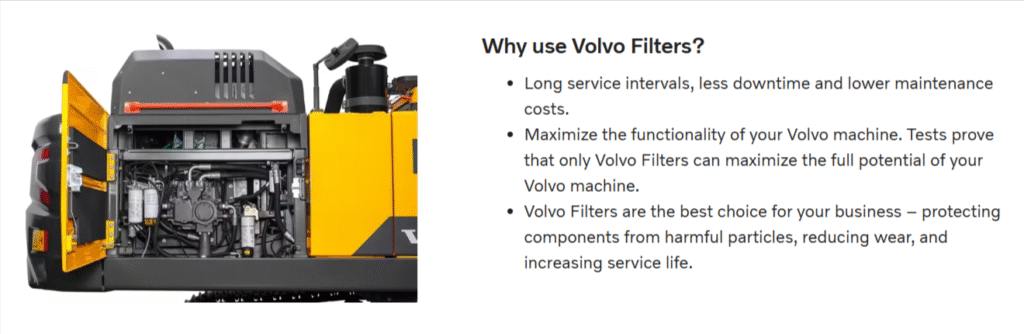
Source: Volvo
Getting replacement parts from the original equipment manufacturer ensures maximum compatibility and performance.
Still, OEM parts are not the only option—the aftermarket parts are just as popular.
While the market was valued at $40.10 billion in 2024, it’s projected to reach over $73.6 billion by 2033, growing at a CAGR of 7.41%.
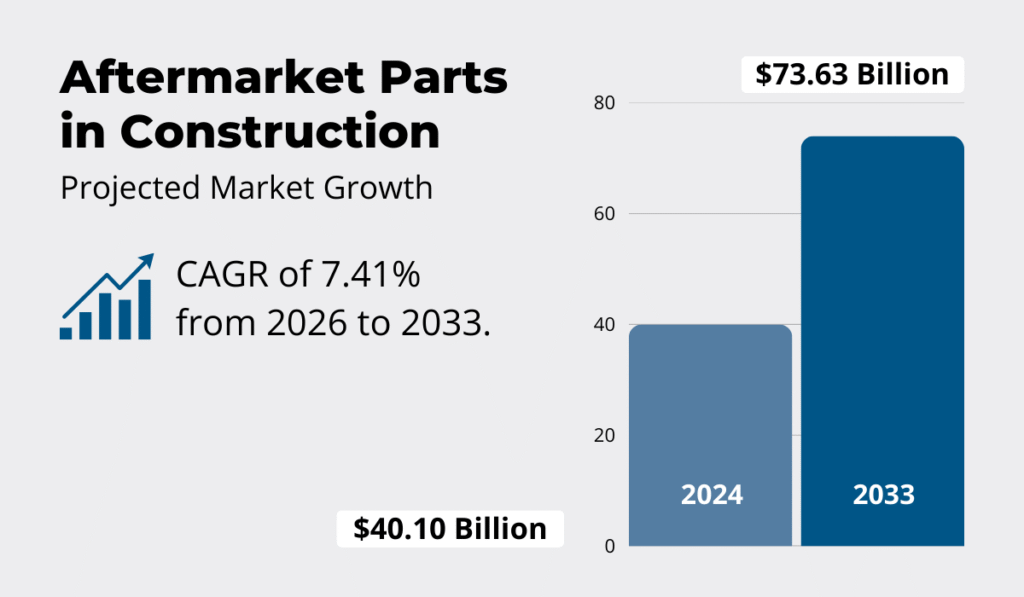
Illustration: GoCodes Asset Tracking / Data: Verified Market Reports
This growth underscores the reality that strategically sourced aftermarket parts offer solid value at a more affordable price.
For instance, putting a used replacement part in a newly purchased excavator would be risky and shortsighted, but it’s a different story for a non-essential forklift nearing the end of its useful life.
Here are some examples of what you can find on sites like Equipment Share.
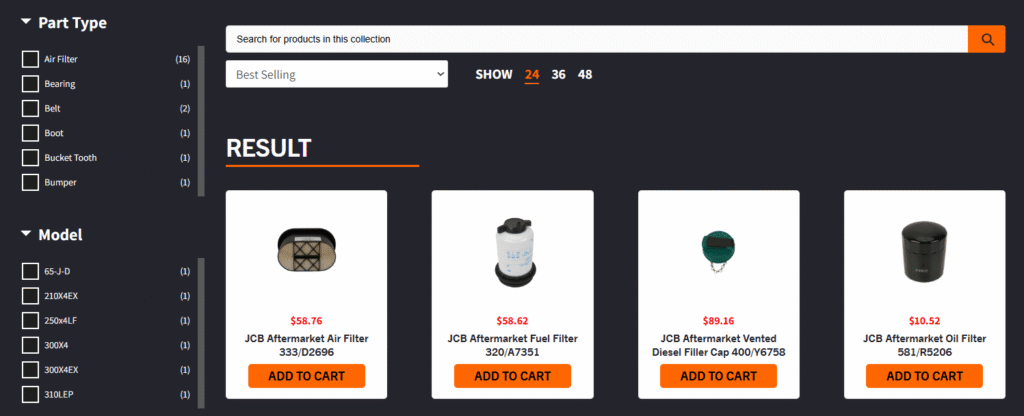
Source: Equipment Share
When it comes to sourcing replacement parts, your choices typically fall into four categories:
- New OEM parts
- New aftermarket parts
- Rebuilt or remanufactured parts
- Used parts.
Each comes with its trade-offs in terms of cost, reliability, warranty, and availability.
For example, getting new OEM parts guarantees reliability, but the lead times are longer. Meanwhile, used parts are the easiest to source and cheapest to buy, but their lifespan is largely unpredictable.
The comparison below highlights these differences at a glance.
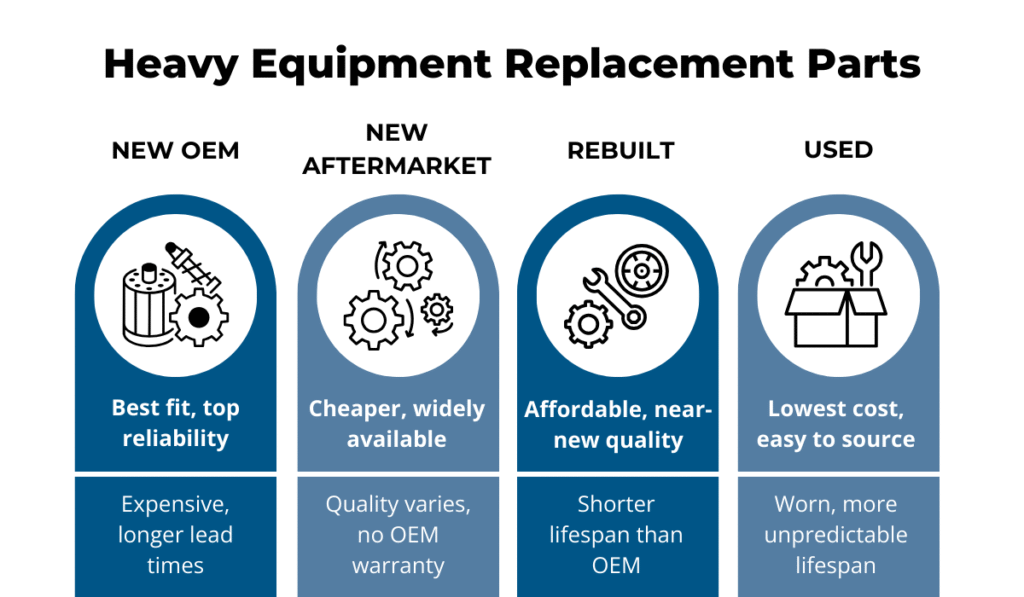
Source: GoCodes Asset Tracking
Ultimately, the right choice will depend on the equipment, its age, and the role it plays in your projects.
But one thing is certain: Prioritizing quality and weighing trade-offs carefully reduces long-term costs while extending the working life of your fleet.
Conclusion
Now that we’ve reached the end of the article, let’s repeat the key message: Maintenance is less about fixing breakdowns and more about preventing them.
Scheduling, inspections, records, and training all serve the same purpose—maximizing uptime, protecting workers, and keeping costs in check.
With margins as tight as they are in construction, companies that take equipment maintenance seriously gain a decisive edge.
Now is the moment to evaluate your practices and consider which tools you can adopt to streamline processes and ensure reliable results.