An equipment inventory list is a mechanism that gives you more control over your business’ assets.
It includes all the information related to the equipment, such as purchase date, dimensions, serial numbers, and much more.
A completed and finished equipment inventory list is one of the company’s best assets. It serves as a buffer between department requirements and order fulfillment.
In this article...
Why It’s Essential To Keep An Inventory List
It’s hard to commit to doing something that is time-consuming if you don’t perceive its value. However, keeping your equipment in check is similar to controlling your expenses and financial management.
You know how the old saying goes: if you don’t control your money it will control you.
Keeping an inventory list will not only point out some unnecessary expenditures, but it will overall contribute to your business operations.
Here’s how:
Sense Of Knowledge
The best decisions are based on data.
If you keep an updated equipment list, you get enough knowledge about your inventory to decide whether, for example, you can take on new projects or not. You can also predict what else you need in next month or next quarter to keep your business run smoothly.
Let’s assume you’re a school manager. With insights from your inventory list, you’ll know what school supplies are running low so that you can order them on time.
If you’re an office manager, you get to know what stationery and other items are required for the fluid functioning of your office.
Better Customer Satisfaction
If you’re in a business where you have to accept and decline a project based on your inventory status, you must keep track of it at all times.
A correct inventory list means a better response time for your customers. It also means that there is less cancellation of orders and better customer service.
Cost Factors
The list helps to understand all the cost factors related to your equipment. It also helps you to identify the resale value of the equipment based on the date of buying.
A maintained inventory list can also save you upfront costs as you’ll know precisely when to repair/upgrade or replace equipment. If you are selling your equipment, you get to fetch a higher price for it based on the knowledge you have.
Also, sometimes companies order more equipment to fulfill the project, only to find out that the equipment was there all that time and that they made a wrong decision. Last-minute delivery can have extra expenses such as fast delivery and downtime.
Timely Maintenance
Another benefit of good equipment management is that you can schedule maintenance on your equipment based on usage. Regular maintenance will reduce your downtime and save you some money, as out of commission, or insufficient equipment can hinder your workflow.
Additionally, you might have to pay your employees for idle time if you are having an unexpected equipment problem.
Understanding Equipment Usage Trends
It’s useful to identify which tools your business uses more, which equipment breaks down the most, which one has the lowest cost per hour, and which one has high maintenance costs.
All this data can also predict which equipment requires maintenance next month so you can budget accordingly. Safe equipment is a must-have for your business.
Increasing Personal Responsibility Among Staff
You can identify who is doing more work and who’s doing less. Inventory lists can detect who is regularly losing tools and not returning them on time, as they are transparent and thus improve accountability among team members.
Whoever is irresponsible toward company property needs to be reprimanded and informed that the cost of the instrument affects the bottom line and possibly their salary.
People that take and return tools every day are honest and responsible, and those that are not can motivate you to make changes to your current company policy and equipment handling procedures.
Now that you know that your business needs to have an equipment inventory list, the question is—how do you make one?
How To Create and Manage an Equipment Inventory List?
The office/equipment manager in charge creates this list, which other responsible staff members should update daily.
There should be a fixed structure in the final placement of the item in the list.
Start with a regular spreadsheet. You can use a ready-made template, edit your business name and logo, and categorize your tools. Then you just have to populate the fields based on your inventory.
Prepare columns on different tabs with information about your tools and equipment.
The following are the elements of a standard equipment inventory list that you might want to include.
Tool Information Tab
This part will have all the information about a particular tool/equipment in your total inventory.
Components of this are:
- Serial number
- Equipment description
- Location
- Condition
- Years of service left
- Vendor/company
- No of tools for a particular type
- Date of purchase
- Cost
Serial number: This can be an equipment number, a tracking number, or PIN (product identification number) as defined by NER, depending on the type of equipment. This information is critical to keep at hand, as it’s required in case of theft.
Equipment description: Here, list the make, or the model of your tool. Equipment description incorporates all the information about color, specific markings, and others. This is another crucial piece of information in an unfortunate case of theft. You can use it to file an insurance claim.
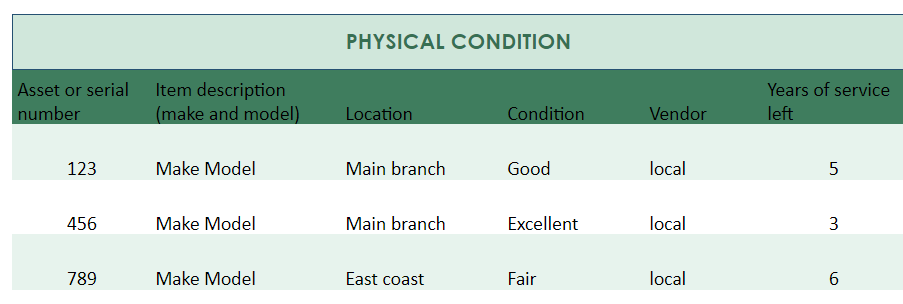
Location: Location represents either the facility where you are keeping the equipment or its last known location. As most stolen tools are found in a 100-mile radius in case of theft, it becomes important to know from where to start the investigation.
Condition: What’s the status of an item? It can be new, good, needs to be repaired, broken, decommissioned, etc. This information needs to be known so that you can order new stuff to replace decommissioned equipment. Also, if a project requires more tools, the order can be placed accordingly.
Years of service left: Number of years that your workers can use the appliance safely.
Vendor/company: The place from where you bought that equipment from. Why do you need to list that info? In case you need to replace your equipment with the same model.
No of tools for a particular type: You can bunch the same kind of tools of the same type together so that if something’s missing, everyone knows about it
Date of purchase: The date of purchase is related to years of service left, as you can use this to predict and calculate the life cycle of that tool. This info is also often required while filing a claim and in police reports.
Cost: You should always list the cost of your equipment. More expensive equipment might need more security. Tip: you can batch the less costly ones together.
Issued Tools Tab
This tab will have information about who issued a tool, which tool they issued etc. This list will increase personal responsibility.
Elements to this list are
1. Device serial number: same as one in the tool information sheet
2. Device description. same as one in the tool information sheet
3. Issued to: name of the person who took the tool
4. Check-in /check out status: The status of a particular tool, whether checked in or out.
5. Time for check-in /check-out: the time of checking in and out. This can calculate the time when the tool was in use.
6. Reason (if not returned at the end of the day): if the tool is not returned, you should know about it. Sometimes there’s a valid reason why someone did not return the tool at the end of the day, but the managing person needs to track this data to make sure that the workers are not misusing tools. Reasons commonly include statuses like: sent for repair, overnight use, and others.
7. Floor manager: Here, put the name of the person-in-charge of tools. They are the responsible ones for all tools check-ins and checkouts. They are also a point of contact for all issues related to equipment.
Financial Information Tab
As the name says, this tab will include all the information related to the cost of your equipment. Here, you will pull some data from the main tab (tool information tab) and then you will add additional financial information for every piece of equipment.
We will show you a few formulas to calculate some of the financial costs.
Date purchased and serial number: those will be the same as one in the tool information sheet.
Current value: The value at which the equipment you can sell in today’s market. It helps determine a company’s financial condition better as it takes into consideration assets rather than just cash inflow.
It also takes into consideration changing costs, as opposed to the historical value that only takes into account the price at which equipment you bought the equipment.
Operating cost: This is a summary of a few factors. Acquisition cost (cost for owning/renting equipment) + Maintaining cost (maintenance cost per hour) + Running cost (fuel consumption, electricity)
Acquisition cost =total price paid for the tool / number of lifetime hours
Maintenance cost =Lifetime maintenance cost (oil change,repair,parts) / no of lifetime hours Running cost = Price per gallon/ number of hours used per day
Annual Straight-line depreciation: It is a method to identify the carrying amount for equipment over its life usage. The underlying idea is that the equipment’s value depreciates uniformly (a fixed amount) over a certain period until it reaches its salvage point (scrap value).
It’s a more straightforward method of depreciation. You can use this in situations where there’s no fixed pattern to use the equipment over time.
Annual Straight Line depreciation can be calculated by :
Annual Straight Line Depreciation =(Cost of Asset – Salvage or Scrap value) / Useful life of equipment
Monthly depreciation: The declining value of equipment can be calculated over its useful time
Monthly depreciation is simply calculated by dividing annual depreciation by 12.
If you don’t have capital, you can ask for a bank loan to get the necessary stuff. If you will need that tool for more than three years, taking a loan will pay off.
Loan term: In this column, enter the number of years you have fixed with your bank to repay the loan.
Extra tip: If your equipment will become obsolete, you should take the lease instead.
Loan rate: This is the interest rate applied to a loan. The equipment serves as collateral, so there is no need for an additional one. Interests range between 8 and 30%.
Monthly payment: The expense that you have to pay every month for a single piece of equipment. A lease normally has less monthly payment than a loan.
Expected value at the end of the loan term: Some equipment loses its value over time. Cars are a great example of this. Therefore, you should calculate an expected value (EV) for the time when you stop paying the loan.
This is the value you’ll get if you would try to sell your equipment after you have repaid your loan. You might know this by heart in your industry, or you can use a following mathematical formula:
EV = ∑ probability of event * event
If you wonder what the “event” stands for — it is the income from the tool.
Normally, you should consider equipment a long time asset, not a current asset, as they are used for more than one year. It is part of a fixed asset table in the balance sheet.
But, if a business sells and buys equipment routinely, that is considered inventory, and inventory is considered part of current assets.
The components of this list can vary depending on the type of industry. Inventory list is a versatile tool that can be used by many industries, but the underlying idea is the same—to put all your equipment records into one table so that you can look into it if required.
Industries That Benefit From Keeping Inventory Equipment Lists
As mentioned, many industries benefit from keeping track of their inventory, as this is a universal strategy, beneficial for every business having physical assets that can be easily lost, misplaced, or even forgotten about.
Here are some industries that greatly benefit from keeping their equipment in check.
Manufacturing
Technological advancement in the last 15 years has caused significant advancement in the manufacturing industry. But where there’s growth, there is also a fear of loss, be it a loss of money or a loss of tools.
There are many tools issued each day to workers and employees in factories. Losing equipment can cause considerable operational and financial problems, both in the field and in the warehouse. Aside from that, losing tools causes downtime and creates problems for management.
Healthcare
Most hospital equipment is costly. Expensive healthcare equipment like specialized beds, defribrilators, and cheap ones small ones like stethoscopes, stools/chairs all go missing.
Not having the necessary equipment can create operational and compliance issues. Even small things like cotton swabs, IV bags, or tongue depressors, can negatively affect day to day operations if they are not present.
Healthcare institutions need to keep their equipment in the control even more than others. In any emergency situation, supplies can quickly disappear, leaving patients without proper care.
Schools
Schools also face the problems of missing inventory because there are many people involved in equipment handling, and students also have access to certain things.
School supplies such as chalk or pens are so easy to get lost. Even though they are small, their costs can add up to a significant amount.
Schools have a lot of equipment for different activities. Think lab equipment and locker stuff—those are items that frequently go missing. There is a desperate need for efficient inventory tracking in schools.
Construction
Construction is one of the industries that is most affected by equipment management problems.
Every year, around $1 billion worth of construction equipment/tools go missing in the US alone.
Out of this, companies recover only 10% of lost items. There are other problems when it comes to construction companies and their equipment tracking, such as the absence of a global database, organized crime, loose fences on work sites, and no theft prevention strategies.
Office-based Companies
Did you know that more than half of the employees admitted to misplacing office supplies or taking something home from the office?
Usually, office managers order around 20% more than the required amount for office supplies, probably due to the fact stated above. Besides typical office supplies such as stationary, people even steal things like food and tissue papers.
If you would make an equipment inventory list for an IT company, your list would include your hardware assets as well, and you would calculate the depreciation rate for equipment, and you would include all software licenses on your list.
How Technology Streamlines Equipment Inventory Lists
If you think that spreadsheets are too much work and the above-mentioned formulas seem too complicated, consider using software for making your equipment inventory instead.
There are quite a few advantages that the software inventory system has over spreadsheet-based tracking.
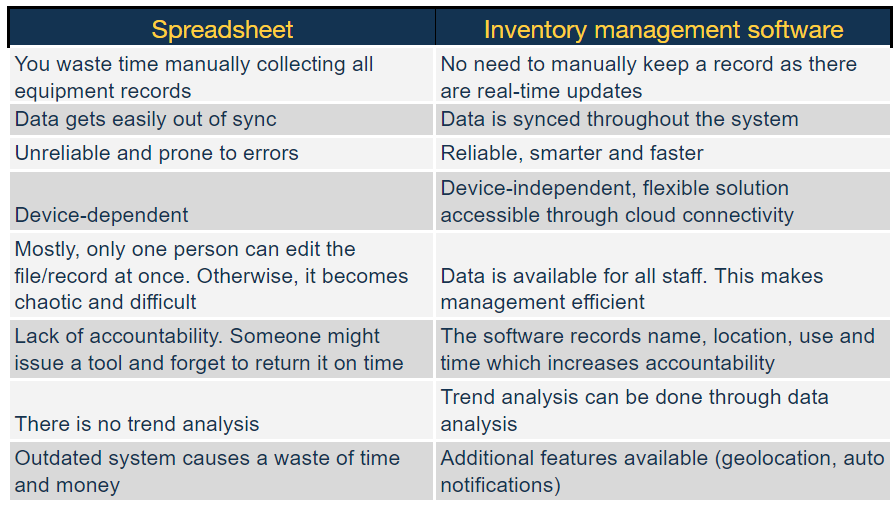
Software solutions for equipment management are dedicated to keeping track of your inventory on a day to day basis.
It tracks your tools through their whole use cycle—from the day you buy a new piece of equipment, to its last working day. It logs all the information about the asset, such as the issuer name, and time and date of the last usage.
Before you choose an equipment inventory system, consider the factors related to your business. Here are some of them.
Hardware
If you want to use a dedicated scanning device for scanning your equipment in or out, you’ll have to buy a handheld scanner.
Alternatively, you can use a smartphone scanner as these provide more flexibility and can quickly scan your equipment.
It’s cheaper as you don’t have to buy any additional product for scanning your equipment, and also you don’t have to maintain/repair the scanners. Everyone having a smartphone can do it.
Tagging Solutions
Think about which tagging solution you’re going to use. There are different options on the market, such as RFID, QR codes. They come in different materials, so you can use the option that will endure the environment you operate in.
Besides tagging, you can also use GPS tagging for large size, expensive equipment. All these solutions can work with or without Bluetooth or 3G networks. We provide patented solutions for asset tracking and tagging.
Software Upgrades
Once you decide on a software solution, you could probably upgrade it with a host of other features. Cloud-based software provides you with connectivity so that you can have real-time tracking of the tools in your record 24 hours a day. Some of them can create a tool roster to show which tool is issued right now and who has it.
The software has the ability to integrate IoT enable devices so that you can use cameras and motion detectors in your warehouse. So that if there’s a theft, you’ll receive automatic alerts, and you will be able to automatically inform local authorities about it.
Conclusion
Creating an equipment Inventory list is one of the most essential steps in managing your business.
Doing so makes you financially knowledgeable about your company’s asset situation. It may seem like too much effort, but it will help you run your business efficiently and maintain a better flow of inventory.
A software solution is the future of inventory lists. Real-time forecasting, advanced tool management techniques and IoT integration is the future. As an equipment manager, you should employ a solution that boosts productivity, maximizes profits and provides the best outcome.