Imagine running a company with hundreds of inventory and equipment across various locations. It’s impossible to keep track of all information in real-time without a cloud-based inventory management solution.
Poor inventory management leads to a huge waste of time. The average cost of downtime ranges anywhere between $140,000 to $5 million every hour.
That is enough to cripple even the most well-prepared of enterprises, let alone mom-and-pop shops down the street.
This is why your business needs to invest in industry-standard, high-quality programs that will streamline managing assets in the most simple and efficient way.
In this article...
What Is an Inventory Management System?
An inventory management system encompasses features like:
- Order management
- Inventory tracking and locating
- Supplier communications
- Automated repair requests
- Cost optimizations
- Loss and theft prevention
Features may vary depending on your needs but the basics remain the same for all companies.
An inventory management system gives companies more control beyond simple tracking and reordering.
This translates to better demand forecasting, production, and quality, all of which contribute to increased business growth and happier clients.
Your company needs to keep track of asset levels in today’s competitive landscape where assets move quickly.
There will be a centralized record of every asset in your organization. Determining where assets are stored and whether they are in stock is only a few clicks away.
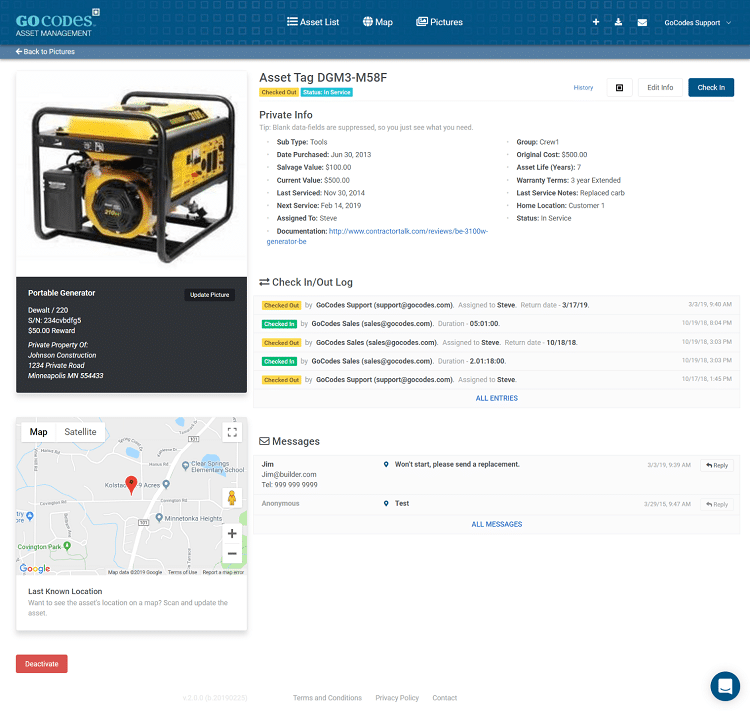
Suppliers will automatically receive delivery requests when you run low on critical equipment. This, along with a plethora of equally useful features, make inventory management systems a must-have for your business.
Manual vs. Automated Inventory Management
Small businesses often rely on manual software like Excel to manage their inventory.
46% of small to medium-sized businesses still use pen and paper for stock tracking-some don’t even bother to track at all!
Manual tracking is fine when you’re just starting. However, as your business and inventory grow, it becomes a major time barrier.
These challenges can ruin your budget if you fail to address them.
Companies in the U.S. hold $1.43 in inventory for every $1 they make due to poor inventory management. In today’s competitive markets, you cannot afford to throw money away with such tight margins.
Your company must invest in an inventory management system to overcome these problems. The hours lost on manual work in the past can now be spent on productive work thanks to automation.
You can deliver products and services faster too as a result of streamlining tasks.
Cloud-Based Inventory Management Systems
Almost every business tool today works on the cloud-inventory management systems are not any different.
For starters, cloud providers guarantee total uptime (99.9% uptime is the industry-standard) which prevents the downtime issue we covered earlier.
Cost saving is another benefit of cloud-based tools since you only pay for what you use i.e. the software-as-a-service (SaaS) model.
You can manage your inventory with enterprise-grade features while having extra funds to invest in other important departments like sales and marketing, for example.
Since cloud tools are device-agnostic, your employees can access inventory data anywhere, anytime.
Staff working in the field could scan and track equipment with a smartphone and have the data updated instantly for a manager working from home.
Not only do you boost productivity, but your clients will also appreciate your efficiency as your offering is delivered on the dot.
These technologies will be even more crucial for businesses as Industry 4.0 looms and aims to drive profitability and growth through smart solutions. Warehousing is a big part of the Industry 4.0 roadmap since many of its practices can be revamped with technology.
The Internet of Things (IoT) is a prime example as it transforms how businesses track products through the use of interconnected smart devices.
The evolution to Industry 4.0
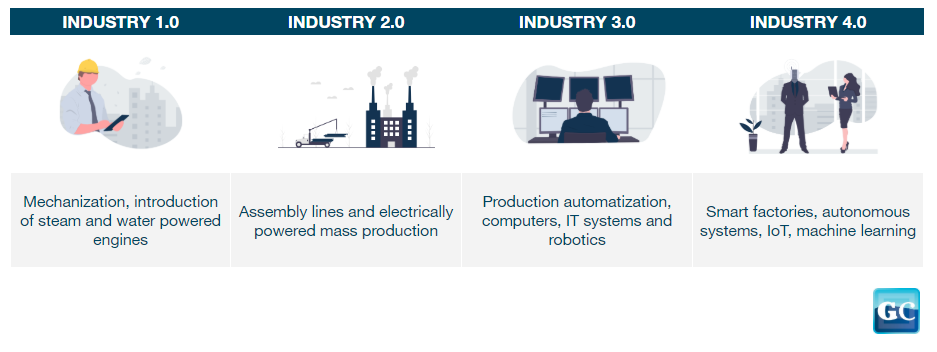
There will also be a greater push for automation in inventory management. Routine employee tasks like scanning barcodes or updating SKUs will soon be automated and accelerated by robots.
This does not mean warehouse workers are out of jobs. Instead, their efforts will shift towards strategic tasks rather than menial work.
Employees will drive more value in their organizations which results in increased salaries and work satisfaction since they no longer need to push buttons all day.
Ultimately, businesses that pursue smart solutions to bolster their inventory management system will gain a huge advantage over less proactive rivals. 81% of executives already agree that technology is the most important contributor to business growth.
Expect the gap to grow as we enter a new decade of change and disruption.
The Benefits of Cloud-Based Inventory Management
1. Eliminate Errors
Algorithms are better than humans at making complex calculations and turning data into valuable insights. They are also immune to mistakes which are inevitable when employees work round the clock.
Equipment checking in and checkout, for instance, becomes error-free as data is updated every time an item is scanned without employees having to enter serial numbers in the system by hand.
This cuts down errors to a minimum. If an error does happen, it’s easy to look into product logs and identify where the mistake happened.
Common mistakes like duplicate entries or misplaced items can also be avoided with cloud-based inventory management.
Most cloud-based providers integrate with popular business tools. You can funnel inventory data from one tool to another for every business department to work seamlessly. That increases your operational efficiency.
If a data mismatch happens, you can pin down the source of the error with a few clicks-something you cannot do with traditional inventory tracking.
2. Data Security and Reliability
What happens if your work computer breaks down tomorrow?
If you don’t have a backup, then your inventory data is likely gone forever. If you do have a backup, how would you import the data back to your computer? Are they the latest backups?
These headaches won’t be a problem if your inventory data is on the cloud since backups are created automatically whenever there’s a data change. These real-time updates make your inventory data reliable and create data integrity.
Cloud providers invest a sizable amount of money into best-in-class servers to store data. If a server goes down, you can still access your inventory since cloud data is hosted across multiple servers in different regions.
If your device is lost or damaged, you can simply get a new one and resync all your inventory data from the cloud as if nothing happened.
Downtime can happen but the chances are slim since most providers guarantee high uptime levels in their service-level agreements.
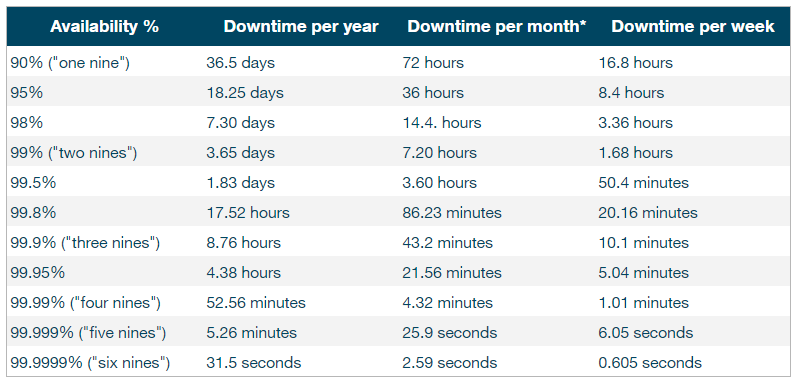
Cloud providers are among the best in terms of data security.
You no longer need to spend money on security teams to protect sensitive data-your cloud partner does that for you behind the scenes. This bolsters physical security as well since your office has no risk of servers being stolen.
3. Scalability and Flexibility
When your business grows, new staff needs to be equipped with existing tools to be productive at work. It would take forever to do this without a cloud-based system.
Let’s say your company brings in twenty employees to cope with rising demand.
Each employee needs to be authorized to access inventory data as well as install required software on their devices, all of which takes around two hours. Doing so for all twenty will eat up forty hours of valuable business time!
It’s easier to scale across new locations and staff with cloud-based inventory management. You only need to bump your subscription fee to accommodate new employees and meet your usage requirements.
Most tools also come with simple one-click installations and data syncing, allowing new hires to start working with minimal distractions.
Cloud-based tools can be customized according to your needs. You can upgrade or downgrade your subscription depending on your usage anytime without restrictions.
Additionally, you can modify your inventory workflow to include custom data specific to your company. You can even integrate your inventory data with internal business tools through the use of third-party APIs.
This will streamline collaboration between employees and departments to further ease business growth.
4. Save Time and Money
Thanks to the SaaS model, you only pay for what you use on a monthly or annual basis.
Since data is hosted on the cloud, you don’t need to invest in expensive physical servers to manage your inventory while all software updates are managed by cloud providers.
Most cloud management systems are easy to implement and don’t require significant technical expertise to get started, further eliminating the need for additional IT personnel.
A subscription-based service seems expensive but in the long run, it’s far more affordable than having in-house servers.
The time you save with automation translates to your bottom line as well. Think about how much time is spent on manual work in your business right now. Not only are you wasting time, but employees may key in incorrect data which hampers operations.
Cloud-based inventory tools prevent this by tracking everything in real-time and generating valuable insights from your data, leading to fewer inventory management challenges.
5. Transparency and Real-Time Insights
With a cloud-based system in place, you can track every asset whenever it’s moved, updated, or in repair in real-time.
Most tools forecast demand or predict maintenance based on historical data so you act on time. This prevents idle time and keeps your operations efficient.
The insights you gain also benefits your company beyond demand forecasting. Knowing what is mostly used and what tools just sit in the warehouse is useful for process optimization.
Consequently, these real-time insights make everything transparent. If someone checked out equipment and hasn’t returned it on time-you will know and be able to act on it immediately.
Transparent operations are key to identifying problems and inefficiencies. Quality decision making rests on quality data.
6. Convenience and Easy Access
The best thing about cloud-based tools is that you can access them from anywhere-all you need is a laptop (or smartphone) and an Internet connection.
Sales teams love working with cloud software since they can check stock on the road which helps them immensely in closing deals.
Likewise, any company doing fieldwork finds cloud-based solutions indispensable as they allow incredible mobility. We suggest using specialized rugged laptops for such work, so your equipment stays protected at all times.
With smartphones being so prevalent in our daily lives, it’s a no-brainer to invest in cloud-based inventory management so you (and your team) can work anywhere, anytime.
Common Capabilities in Cloud-Based Inventory Management Tools
1. Software Functionalities
Most cloud inventory management tools offer the following options:
-
Inventory optimization: Having too much of the same tools or not having critical equipment when needed is a real problem. You can identify the optimal quantity of each item with the aid of inventory optimization. With data from your software, you can calculate asset depreciation for better equipment life-cycle management.
-
Alerts and notifications: Staying alert is the best precautionary measure. With this feature, you will receive notifications for important things you set triggers for. For example, you can be updated when inventory items are low, when an asset is overdue and hasn’t been returned on time, or when an asset reaches its next service date.
-
Instant reports: Reports are essential for performance reviews, or when you need to send some information to the government, like IRS, for example. A lot of software solutions lets you generate various types of reports whether you need to calculate maintenance summaries or fixed-asset depreciation
-
Historical data and analytics: Apart from custom monthly reporting, you can look back at inventory data from any point in time to compare your performance. Most systems use data analytics to generate actionable insights for your business. As with having real-time, current data, having historical data is important for a better perspective of your asset management.
-
Multi-location management: If you have multiple warehouses or work locations, you can sync all inventory data into one management system to ease cross-location management. Anyone working on-site can see the up to date situation in the warehouse, for example.
-
Integrations: We mentioned APIs before. They can connect various business tools with your inventory management system. You no longer have to waste time moving data from one platform to another with the aid of integrations.
These are some of the common features of inventory management software. Since we are talking about cloud-based solutions, keep in mind that you will get automatic software upgrades and security patches so your business is always using the latest features and capabilities.
2. Hardware Options
Aside from software features, most providers offer hardware solutions to complement your inventory management system.
These include:
-
RFID-based tags: Some companies provide RFID tracking tags that integrate natively with inventory management systems. This is helpful for real-time asset tracking which streamlines operations, eliminates theft, and improves data collection all at once.
-
Wireless barcode scanners: Some solutions are not mobile, and they come with handheld wireless barcode scanners. Otherwise, people can use cameras on their smartphones to eliminate the need for any barcode scanners.
-
Printers and labels: Inventory management and tracking require some item labeling. Depending on the types of labels you need, you might continue using your regular office printer, or order custom labels (metal labels, for example) if you cannot make them on-premise.
Using complementary hardware with cloud-based systems is a small price to pay given the end result, which is total management control and efficiency, among others.
What Should You Look Out For in a Cloud-based Inventory Management Software?
Inventory management systems share the same basic features but you should consider their nuances before buying. Here are three factors to help you make a decision:
Industry Applications
Are you a retailer, school, or manufacturer?
Do you need to manage inventory in real-time and manage a huge number of products? Or, do you have multiple warehouses and are looking to track the stock of your raw material, work-in-progress, and finished goods across all locations?
Some platforms work better for retail businesses while others are geared specifically towards companies with fixed assets.
Buyer vs. Vendor
Buyers need to keep a track of what they have so they can manage their expenses and reorder items when needed. As a result, buyers focus more on expense management and reporting-platforms with strong analytics features will work best here.
On the other hand, vendors need to manage their inventory according to customer demand and supplier requests so they’ll want to work with providers that specialize in supply chain and multi-site support.
Perpetual vs. Periodic Inventory Management
Businesses with low sales volumes (e.g. car dealerships) should work with periodic inventory management systems.
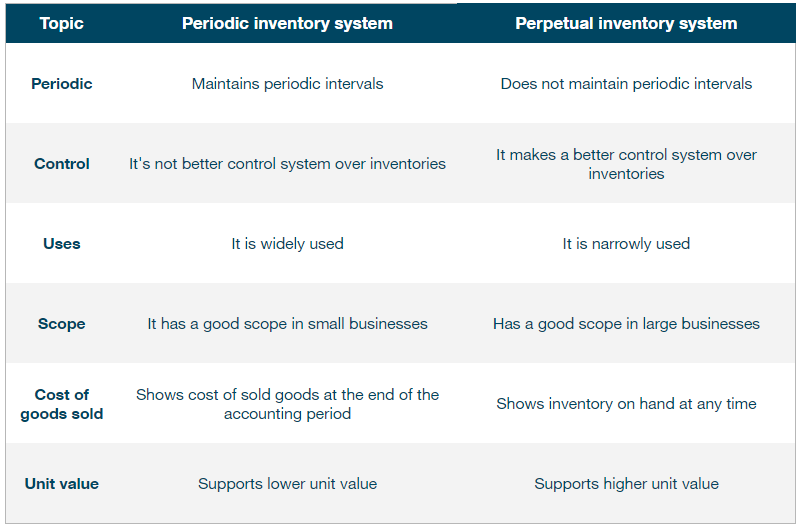
If you have multiple outlets and maintain a high sales volume (e.g. FMCG companies), a perpetual inventory management system is better suited for your needs.
Must-Have Features
An inventory management system can be the best in the world, yet it won’t help if it doesn’t offer features suited for your business needs.
Consider the following must-haves when deciding between providers:
-
Ease of migration and integration: Can your existing data be migrated into the system without error? Can inventory data be integrated with other popular tools? Is integration simple or does it require significant technical expertise?
-
Customization: Can you customize the platform to fit requirements specific to your business? Do you have custom fields for item descriptions?
-
Multi-asset management: Can it manage assets of different types and categories (e.g. fixed assets, retail products, food and beverage) and retain rich metadata for each item?
-
Multi-platform support: Can you access inventory data from different devices like smartphones and tablets?
-
Performance: Can the platform maintain optimal performance for large inventories or high-volume operations? Is it fast to work with?
-
User interface: Is the system easy to use? Is the user interface clean and intuitive even for non-technical users?
-
Notifications: Can you configure automated alerts and notifications for specific events?
-
Scalability: Does your subscription fee scale reasonably based on usage and the number of users?
-
Security: Is the system secure enough to protect sensitive inventory data? Are there role-based access features for user authorization?
Start With Cloud-Based Inventory Management Today
Your business must be efficient in today’s competitive markets or you risk losing out to more proactive rivals.
Cloud-based inventory management helps you achieve this goal since it improves performance and reduces operational costs-at a fraction of the price of manual accounting.
With cloud-based inventory management, you can automate tasks to allow employees to work on strategic, higher-value work. You can also work on any device no matter where you are since data is hosted on the cloud, further improving your company’s productivity.
The subscription-based model of inventory management tools means every business is capable of deploying one.
Even if you are a one-man show, you can greatly streamline your work by choosing a SaaS inventory management solution without burning a hole in your pocket.
If you are looking to take your inventory management to the next level, now is the perfect time to start.