Construction professionals spend so much time on worksites that it’s easy to feel complacent in them. However, ignoring basic safety precautions can quickly lead to catastrophic injury or expensive, time-consuming delays.
In fact, on average, two construction workers a day die in the United States, which results in disastrous repercussions for the employee’s family, loved ones, and co-workers.
The most common fatal incidents include falls, object strikes, electrocution, and becoming caught between objects.
However, it is possible to mitigate these risks with some simple precautions.
By paying attention to occupational hazards, taking care of equipment, wearing proper gear, and moving with caution in potentially dangerous situations, contractors and their employees can remain safe on the job.
In this article, we’ll share some valuable tips that help you set a positive example for your team, while simultaneously indicating to clients that safety is paramount in your operation.
In this article...
Get In and Out of Machinery Carefully
Getting into heavy equipment and then leaving the machine seems so simple. However, these transitional moments contribute to many workplace insurance claims, particularly those resulting in repetitive, ergonomic injuries.
While entering or exiting the cab of heavy equipment, the employee might become distracted, thinking of the job ahead or focusing on going home after a long day at work.
Yet, a single moment of inattention can spell disaster, leading to missteps or falls, among other things.
Since it’s often difficult to maintain focus during these in-between activities, consider taking the following steps to minimize injury during entry and exit:
- Ensure handholds and steps are in good repair.
- Park the vehicle on level ground.
- Face the cab when coming and going.
- Clear the zone of trip hazards.
- Always maintain three points of hand/foot contact when entering or exiting the vehicle.
- Clean mud, oil, ice, or other slip hazards from the steps and the general area.
- Avoid jumping into or out of the machine.
For instance, joint damage is difficult to avoid when entry and exit take place quickly. These injuries can also befall those who carry objects while climbing into and out of vehicles or heavy equipment.
According to OSHA Safety Manuals, jumping from a distance as small as that of a delivery van creates an impact of up to 3.5 times greater than the employee’s body weight—and that doesn’t include the weight of the object the person is carrying.

Worse injuries than ergonomic ones can occur if employees neglect to wear appropriate footwear or attempt to enter or exit a vehicle while it is in motion.
It’s also important to emphasize the importance of avoiding the use of tires, wheel hubs, or door frames as handholds.
Finally, employees who enter and exit heavy equipment cabs often should either avoid bulky clothes or take extra care to ensure that their safety vests or thermal clothes do not catch on equipment edges.
Make sure your employees take these simple precautions to minimize the risk of injuries while entering or exiting vehicles.
Wear Protective Gear
Everyone’s idea of protective gear has changed since the COVID-19 pandemic.
However, no matter what precautions a company might take regarding the coronavirus or other evolving dangers, these should never replace traditional protective gear.
Wearing personal protective equipment (PPE) is a major aspect of preventing injuries on the job. Some of these injuries accumulate and worsen over time, while others happen suddenly and without warning. In either case, proper protective gear helps minimize harm.
Keep in mind that the distribution of appropriate PPE that is in good repair is the responsibility of the employer. In some cases, the use of PPE is regulated by national standards; in others, it is governed by unions or the rules of the industry itself.
It’s impossible to know what kind of PPE to provide to employees without understanding the extent of the danger a tool or vehicle that they rely on can pose.
For example, the chart below shows the decibel level of tools typically used on a construction site. Information like this can help guide construction professionals in the acquisition of appropriate PPE.
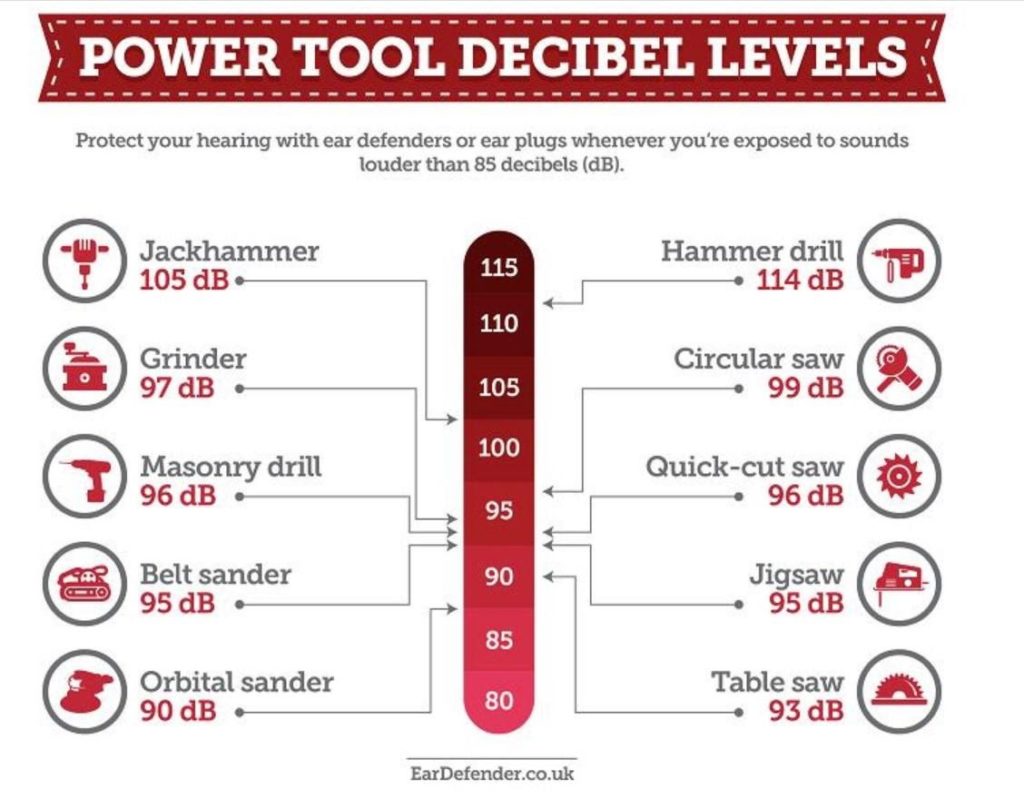
In this situation, a simple set of earplugs or noise cancellation headphones can provide vital protection.
However, there are many other types of protective gear you can use, depending on the conditions your workers are exposed to.
All of these should constantly undergo review to ensure compliance and good quality:
- Eye protection (goggles, glasses, face shields)
- Lung and respiratory protection
- Gloves for rough work or sanitization
- Coveralls, heavy aprons, and chemical suits
- Head protection (hard hats, hats shielding from the sun)
- Hearing protection (earplugs, headset)
Nevertheless, effective management of PPE encompasses more than just providing the necessary equipment.
You should also organize regular training on the proper use of PPE to make sure your team members are getting the most out of it.
Additionally, you should make updating worn or out-of-date equipment your priority.
In short, when employees wear proper protection, health and safety risks are minimized, so make sure they have access to it.
Be Careful While Loading and Unloading
Loading and unloading hazards are a constant issue in the construction industry and instituting consistent best practices for employees is crucial during these operations.
Workers can avoid danger by ensuring load security before the process begins.
For example, the vehicle intended for loading and unloading must stand in a stable, level area with the parking brake on and chocks in place.
As is the case with PPE, employers are responsible for providing the appropriate vehicles for each task, as well as all the materials employees require for loading and unloading. This includes hooks and ropes for securing cargo.
Additionally, clear instructions for each part of the job are essential.
Since safe loading and unloading begins before any cargo moves, it’s helpful for employees to have a checklist to remind them of important steps.
Here’s an example:
As you can see, the checklist covers everything from rigging the load to creating the right conditions for the job in the immediate environment.
It is usually best to perform loading and unloading tasks in a designated area and to ensure that employees are aware of the typical loading and unloading hazards.
For instance, the following situations should be avoided:
- Incorrectly distributed weight that can lead to the cargo falling off
- A cluttered workspace
- Slippery loads or walking areas
- Improperly fastened objects
- Poor visibility
- Parking the vehicle on uneven ground
- Letting the vehicle depart before loading is completed and the load is secured
When employees fail to take the appropriate precautions, injuries such as sprains, bruises, and even spinal damage can follow.
Good training, proper technique, and ensuring a clean worksite can help to prevent them.
Use Ladders Safely
Ladders are among the most basic pieces of construction equipment. They require no electricity, aren’t designed to move, and contain no sharp or rotating objects.
However, the United States is the world leader in ladder-related deaths, and, according to research conducted by the NMSU, ladders are responsible for 6,000 deaths in residences.
In total, the report shows, over 30,000 people suffer injuries due to accidents involving ladders.
Using the right ladder for the job is a critical aspect of worksite safety.
Height matters, as does the kind of terrain on which the ladder will rest.
This chart offers a quick glance at the various classes of extension ladders and how much weight they are supposed to hold, as well as the type of environment in which they are designed to work:
Type IAA: Rugged | Special Duty | 375 lbs. |
Type IA: Industrial | Extra Duty | 300 lbs. |
Type I: Industrial | Heavy Duty | 250 lbs. |
Type II: Commercial | Medium Duty | 225 lbs. |
Type III: Household | Light Duty | 200 lbs. |
Supervisors should ensure that employees and site visitors are familiar with the basic rules of ladder safety once the correct type is in place.
Here are a few tips that can help ensure a safe day on the job when ladder use is necessary.
First, do not use aluminum ladders if energized electrical lines are nearby.
Next, always place the ladder so that all four feet of it are on level ground and ensure the legs of the ladder are locked before climbing.
Also, maintain one worker at a time, unless a two-person stepladder is in use.
When using extension ladders, raise them to the desired height before leaning them, and use a 4:1 ratio for the leaning angle of the ladder.
Finally, avoid standing above the fourth-highest step while working to prevent toppling, and never store tools or other materials on the steps of the ladder.
Also, overreaching for work areas or objects is an easy temptation when it comes to ladder use, and should be avoided.
Remember, emphasizing the importance of safety while using this construction industry staple can pay off immensely in terms of avoiding accidents.
Be Aware of Potential Occupational Hazards
Staying alert to occupational hazards isn’t just the job of a supervisor or inspector. Certain tools, such as circular saws or welding equipment, tend to command caution in a worksite.
Working with materials such as asbestos or biohazards usually encourages workers to think carefully about safety.
However, other dangers might lurk in the field that your employees might tend to overlook. Encouraging your team to recognize them contributes to a healthy work environment.
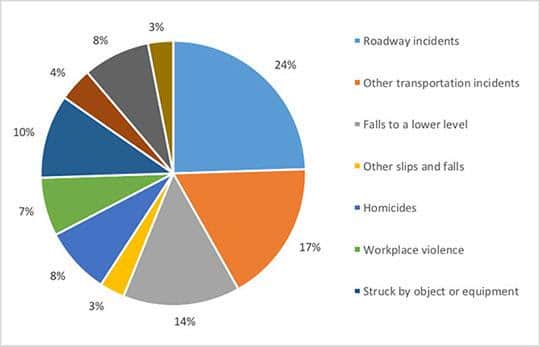
As this chart shows, there are many different incidents that occur in the workplace. Roadway incidents, especially transportation accidents, are among the most significant categories.
The simple act of transferring personnel and materials to the site is responsible for over 40 percent of workplace-related deaths.
These include incidents of workers struck by vehicles.
High-visibility PPE, then, is a must for roadwork and especially for jobs undertaken in adverse weather or at night. Providing sufficient lighting in the work area is also a top priority.
Furthermore, construction professionals are also frequently exposed to other types of worksite hazards, such as electrical injuries or environmental risks like dust, chemicals, and even inclement weather.
Insufficient scaffolding or opening support and inadequate fall protection (missing safety harnesses, floor covers, guardrails, etc.) can also prove fatal.
In short, any failure to keep pace with rules, equipment, and best practices for safety will put your workers at considerable risk.
Ignoring risks doesn’t merely invite tragedy; it can prove costly to a company as well.
For example, in 2020, a construction company in Georgia received a $170,000 fine when a worker fell from an interstate bridge at a site with inadequate fall prevention measures.
The Occupational Safety and Health Administration (OSHA) also found that the contractor failed to conduct site inspections, deliver proper fall prevention training, or use a lifeline system.
Simple measures like daily safety checks and courses for hazard awareness help prevent incidents like these.
Make Sure the Equipment is Functioning Properly
Training and conducting inspections help create a safe workspace, but it’s just as vital to provide employees and contractors with properly functioning equipment.
When workers climb ladders with broken hinges, run machinery with leaning fluid or faulty valves, or drive on tires with dangerously low treads, they face increased danger of an accident.
To supply your team with safe and dependable equipment, encourage immediate reporting in the event of accidents or rough use, and attend to minor damages immediately to avoid more serious problems.
Remember, devoting time and resources to preventive maintenance and minor repairs not only contributes to worker safety but also helps avoid expensive downtime.
So, check for danger signs such as odd smoke, smells, or vibrations at the end of each shift, and pay special attention to the structural integrity of weight-bearing tools and material.
When it comes to keeping the equipment in top condition, rapid access to real-time information is key.
Using a service such as GoCodes Asset Tracking can help your company easily track maintenance records and service needs.
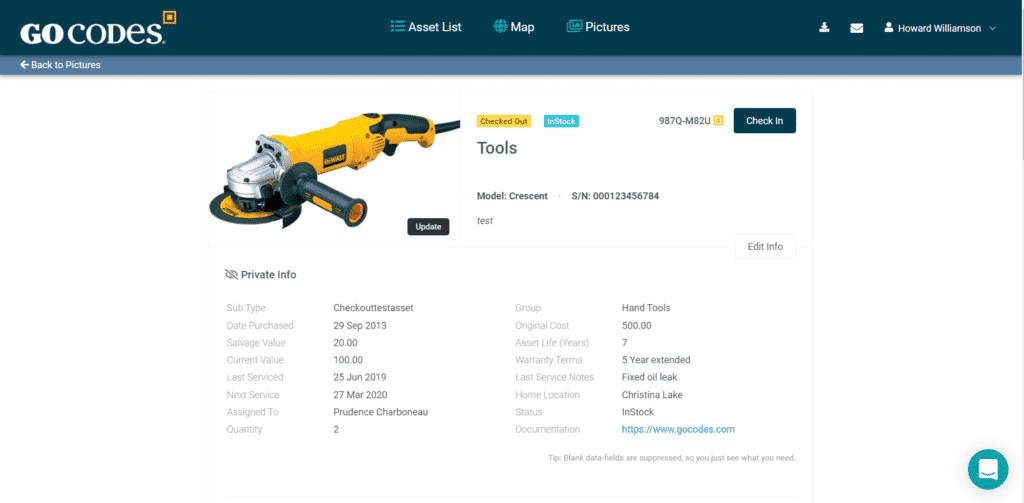
As shown in the example above, the GoCodes Asset Tracking app allows employees to quickly check on service notes and pending management needs, offering them relevant information concerning the condition of their tools. This is a great way to encourage a positive safety culture.
Also, invest in a systemized and thorough safety training program for new employees to make sure they’re aware of the best practices they should implement in their own work.
Finally, lead by example and make sure you adhere to these practices yourself.
Conclusion
Construction work is inherently dangerous, since it involves the use of powerful tools, loading and unloading heavy materials and machinery, as well as occasionally working at great heights.
However, employers can mitigate these risks with current information, training, proper equipment, and good maintenance.
Make sure you implement these tips on your construction site to ensure the safety of your employees.