Key Takeaways:
- A construction risk management plan isn’t a static document.
- A risk matrix helps prioritize risks based on their likelihood and impact.
- By documenting risks and responses over multiple projects, companies can create a knowledge base that improves future risk management.
In construction, there’s certainly no shortage of risks—for both investors and contractors.
Many of these risks have the potential to derail an entire project or cause serious delays and budget overruns.
That’s why effective risk management is crucial, and a well-crafted construction risk management plan is key to that effort.
In this guide, we’ll cover everything you need to know about these plans—from their purpose and core components to the practical benefits they bring.
So, if you’re looking to strengthen your approach to risk management or simply refresh your knowledge, read on.
In this article...
Construction Risk Management Plan Defined
Before defining a construction risk management plan, there are a few essential caveats to consider.
First, while creating this plan might sound like a one-time task resulting in a finalized document, it’s actually an ongoing process.
Although a risk management plan should be initially drafted before construction begins, it needs to be regularly updated.
Why?
Because new, previously unidentified risks are likely to arise throughout the project lifecycle.
Second, it’s important to recognize that not all construction risks can be predicted or avoided.
A well-crafted plan, however, should include broad measures and contingencies that can help mitigate even these unforeseen challenges.
With these considerations in mind, below is the definition of both construction risk management as a process and as a plan:

While straightforward, these definitions could easily be misunderstood without the caveats we just discussed.
With all that in mind, let’s look at who is typically involved in creating this plan.
The answer will largely depend on the type, size, and complexity of the construction project, but one thing is certain: it’s not a one-person job.
Given the vast number of construction risks that must be considered, producing a comprehensive plan requires close collaboration between all key stakeholders, primarily the project owner and the contractor.
More specifically, crafting a construction risk management plan typically involves a range of professionals from both teams, each contributing their expertise.
Furthermore, it’s usually the construction project manager who oversees the process, ensuring that input from all relevant parties is integrated into the plan.
Here are some key participants who are typically involved:
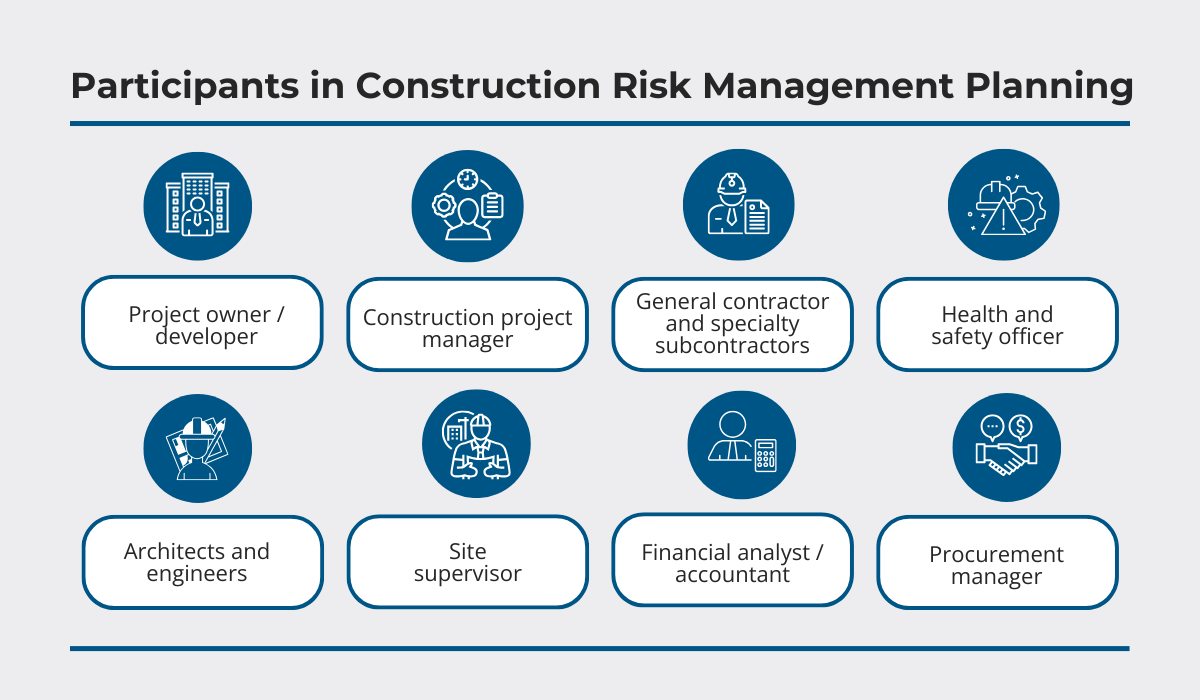
Each one of these participants brings valuable insights into a range of off-site and on-site construction risks.
For instance, architects and engineers can identify risks related to design feasibility, structural integrity, and engineering challenges.
Financial analysts or accountants, on the other hand, assess financial risks, including potential budget overruns and cost allocations.
Jeff Mains, CEO of the software company Intelligent Contacts, believes that the importance of assessing and identifying risks early to ensure more effective budget management cannot be overstated.
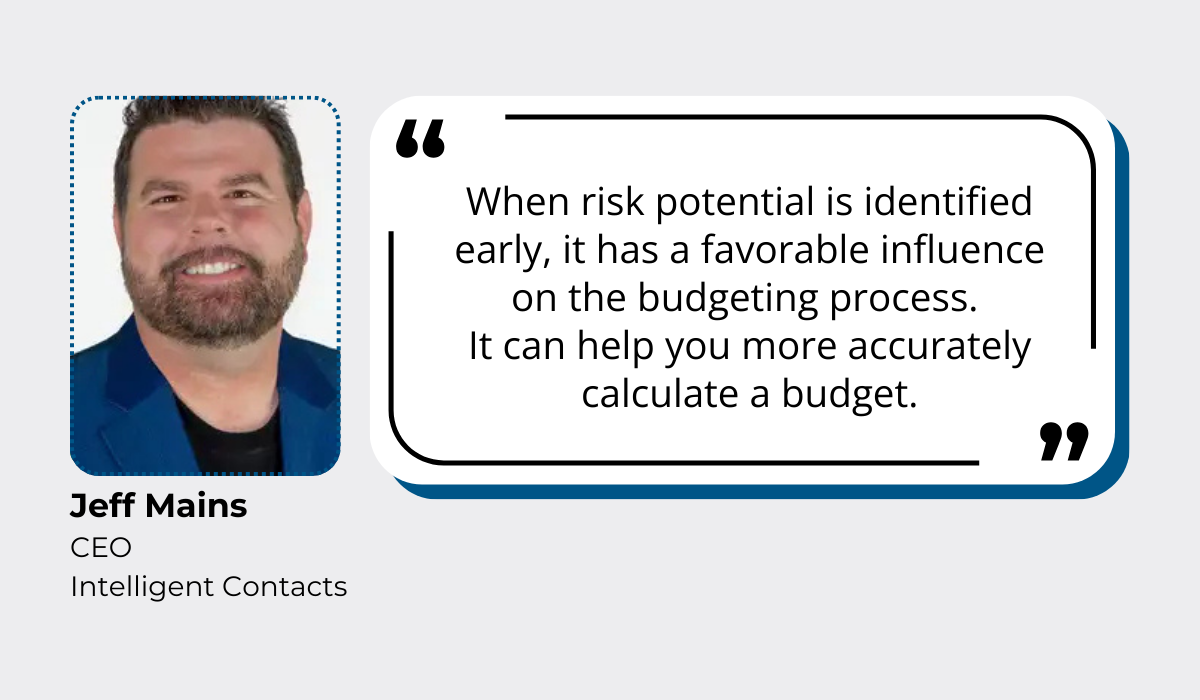
Health and safety officers focus on compliance with safety regulations, while site supervisors contribute knowledge of daily on-site risks.
Other relevant participants in this process may include environmental consultants, legal advisors, and quality assurance specialists, to name a few.
Once the plan is drafted, many of these same participants will reference and apply it throughout the project lifecycle.
Additionally, the plan may be inspected by external regulators, auditors, or safety inspectors to ensure compliance with industry standards and legal requirements.
Now that we’ve explored what a construction risk management plan is and who contributes to its preparation and implementation, let’s take a closer look at its key components.
Components of a Risk Management Plan
A well-structured construction risk management plan is built on several core components, each essential for identifying, assessing, and managing risks throughout the project.
Together, these components provide a clear framework that guides risk management from start to finish.
The process begins with risk identification—typically during the project planning phase—though additional risks are identified as they emerge during construction.
Initially identified risks are then grouped into categories—such as financial, legal, safety, and environmental—to facilitate risk assessment.
However, to do this effectively, it’s important to first define the risk management methodology.
For more clarity, here’s a breakdown of a plan’s key components:
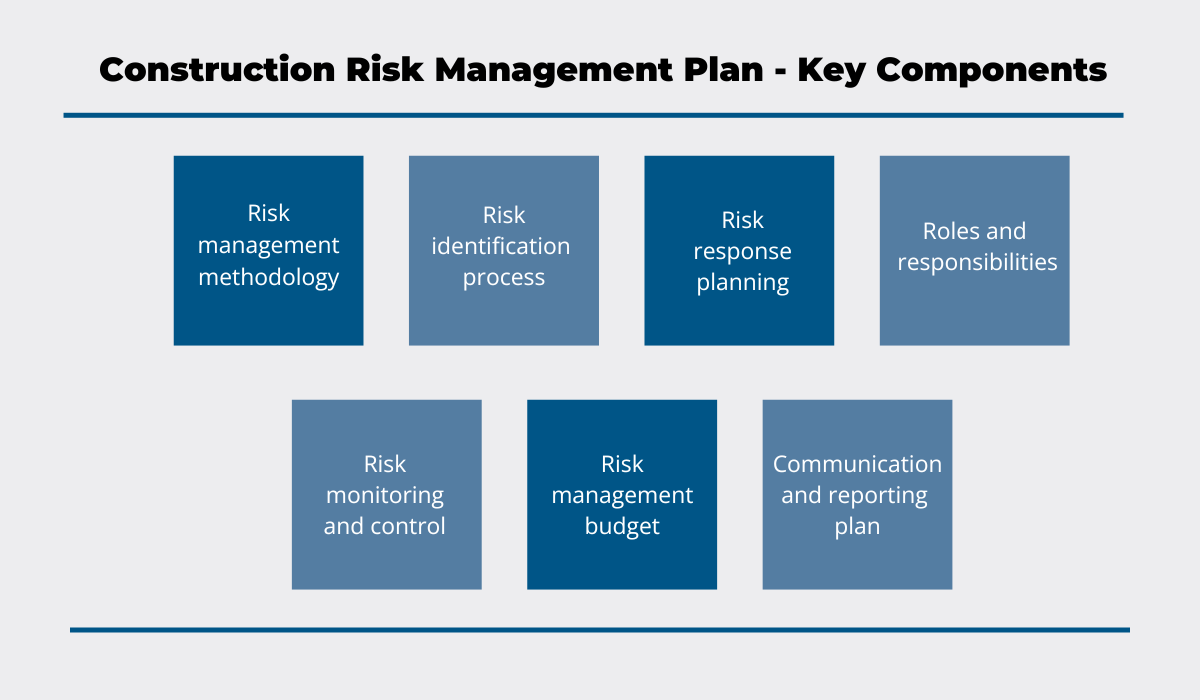
As mentioned, the risk management methodology is where the tools and approaches for other activities in the plan, such as risk assessment and analysis, are defined.
These methods can be either quantitative or qualitative and may include techniques like brainstorming, interviews, SWOT analysis, and risk probability and impact assessments.
One of the most well-known methods is the risk matrix, which can be used to organize identified risks based on their likelihood and potential impact.
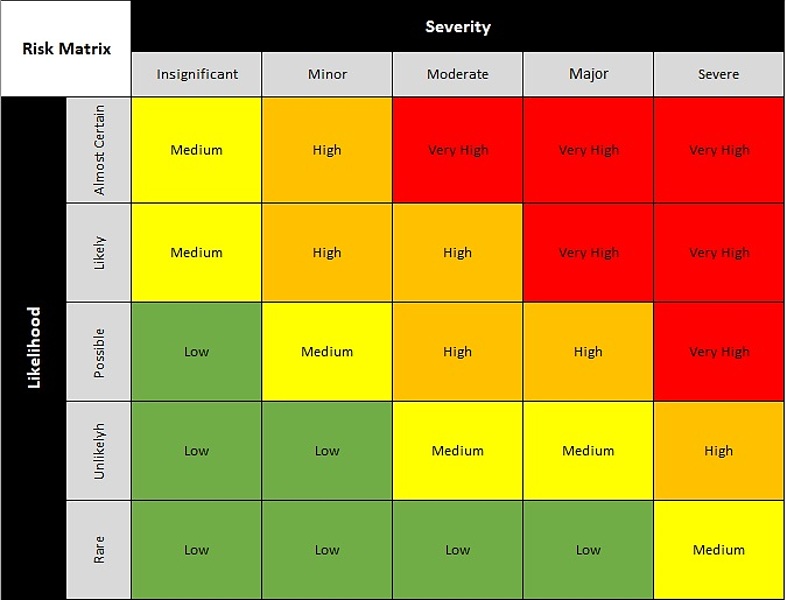
This visual tool helps the project team prioritize risks, allocate resources efficiently, and focus on addressing high-priority risks first.
Once risks are identified, assessed, and prioritized, the next step is risk response planning.
At this point, all project stakeholders collaborate to determine the best strategies for managing the identified risks.
Below, you can see the four typical risk response strategies and how each can be applied to an example of managing potential delays caused by severe weather.
Risk Response Strategy | Application for Severe Weather |
---|---|
Avoidance | Adjust the project schedule to avoid peak weather risks. |
Mitigation | Prepare additional buffer time and use weather-resistant materials. |
Transfer | Include weather-related clauses or delay insurance in project contracts. |
Acceptance | Accept minor delays, have a recovery plan, and monitor weather forecasts. |
As this example illustrates, some risks, such as bad weather, can’t be entirely avoided.
So, while scheduling works outside the hurricane season in some regions may be prudent, there’s not much more you can do to avoid severe weather conditions.
That’s why you can mitigate these risks by adding buffer time into your schedule and ensuring that the jobsite is prepared for such events.
Additionally, you can transfer weather-related risks to the project owner (by including appropriate contract clauses) or the insurance company (by securing delay insurance).
Lastly, you can choose to accept the risk.
As Mike Wills, an assistant professor at Embry-Riddle Aeronautical University’s College of Business, puts it:
“You’re not ignoring the risks, but you’re saying, ‘I can’t do anything practical about them. So they’re there. But I’m not going to spend gray matter driving myself crazy thinking about them.’”
In our example, that involves accepting minor delays, having a quick recovery plan, and closely monitoring forecasts.
Just like in many other areas of risk management, technology—such as the weather application you can see below—can provide crucial assistance in avoiding and minimizing weather-related risks.
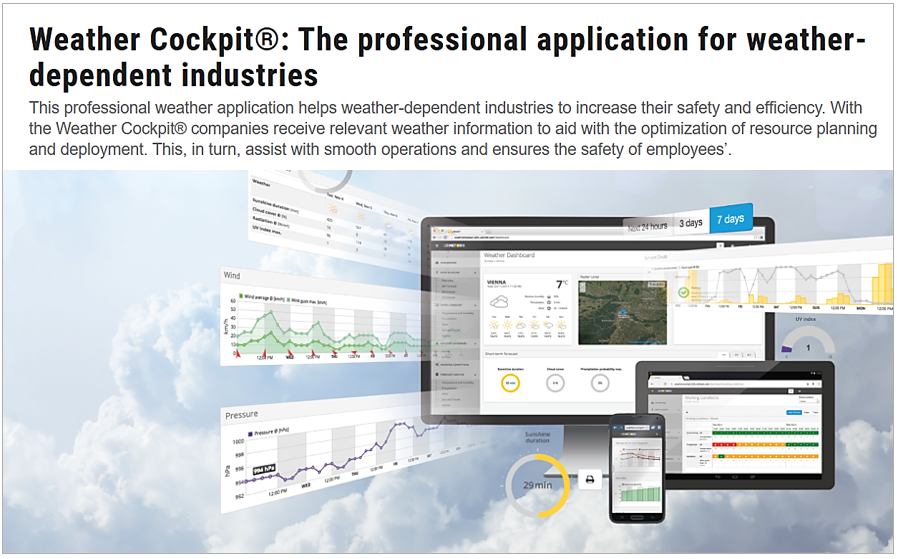
The above example also indicates that, when planning risk response, it’s often a combination of strategies that provides the most optimal risk management approach.
Next, it’s time to clearly define roles and responsibilities, i.e., stakeholders (risk owners) who will be responsible for monitoring specific risks and overseeing the planned risk response actions.
This ties closely to risk monitoring and control, which is the plan’s section that outlines how:
- the status of risks will be tracked,
- the effectiveness of risk response measures will be evaluated, and
- necessary adjustments to the plan will be made.
You can see some of the described components summarized in a table format with examples below.
Risk Response Plan | Monitoring and Control | ||||
---|---|---|---|---|---|
Risk Event | Response Strategy | Response Actions | Responsible Entity | Interval or Milestone Check | Status: Date and Review Comments |
Inaccurate cost estimate | Mitigate | Increased unit price for excavation to match rock excavation price | Geotechnical Manager | At completion of subsurface exploration | xx/xx/2024 |
Unidentified utility impacts | Transfer | Contingency plan. Contractor is responsible for coordination | Utility Engineer | Monthly | xx/xx/2024 |
Permit delays | Transfer | Consultant responsible for coordinating permits and identifying permit requirements. | Environmental Engineer | Monthly | xx/xx/2024 |
As for the risk management budget, this section of the document is going to detail the costs associated with implementing risk response strategies, such as setting aside contingency funds or purchasing materials for mitigation.
The final component is the communication and reporting plan, which outlines how risk-related information should be shared among stakeholders.
It includes details on the frequency of updates, communication channels, and the reporting obligations of risk owners.
When all the activities involved in preparing the plan are finalized, the components we outlined create a comprehensive framework for navigating construction risks effectively.
By ensuring continuous risk monitoring, regular plan updates, and clear communication, this plan enables project stakeholders to achieve significant operational benefits.
So, let’s explore them in more detail.
Benefits of Having a Construction Risk Management Plan
The process of assessing risks and identifying appropriate responses brings numerous benefits.
These benefits are primarily operational—and therefore also financial—as they enable the project team to maintain set timelines, control costs, and enhance safety measures.
In this section, we’ll examine these key advantages, starting with the essence of effective construction risk management—proactive risk mitigation.
Supports Proactive Risk Mitigation
The process of crafting a construction risk management plan allows for identifying and addressing risks before they become critical issues.
We’ve already provided an example of proactive risk mitigation for weather-related risks.
Whether it’s building schedule buffers or using protective covers for on-site materials and equipment, these actions help the project team stay ahead of potential disruptions.
Another proactive strategy is to identify critical equipment and tools needed for the project, check their availability and condition, and see what backups are available in case of failure.
This kind of risk mitigation measure is easy to apply if you have an asset tracking system like our GoCodes Asset Tracking.
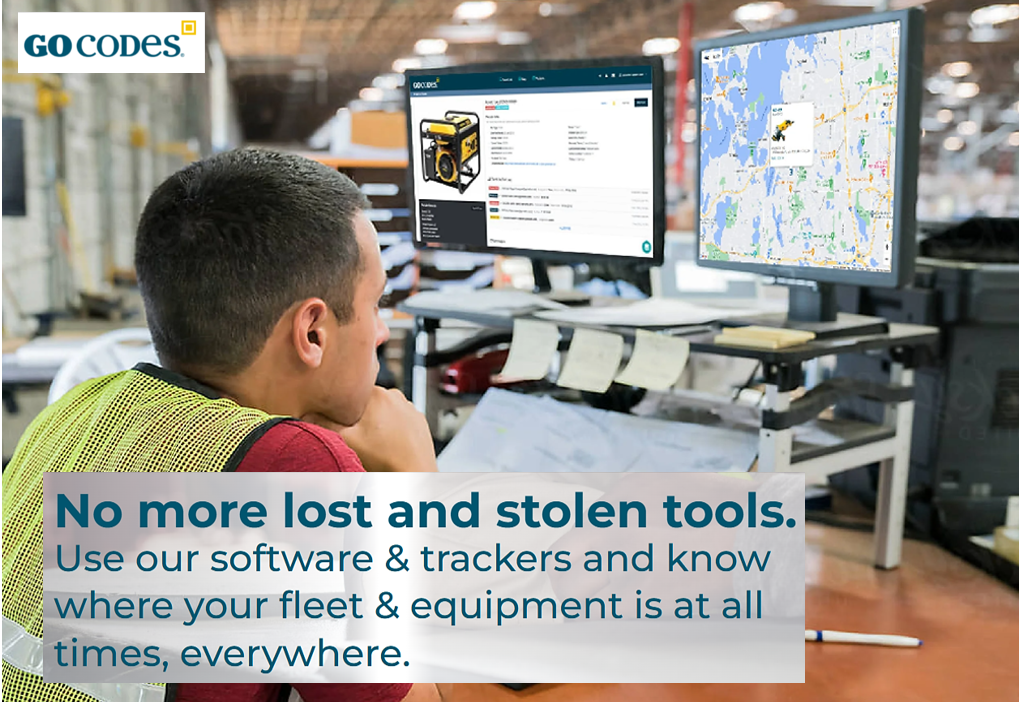
GoCodes Asset Tracking integrates QR code scanning via smartphones or tablets and real-time GPS tracking with an easy-to-use mobile app.
This enables your team to easily view and update all the data on your equipment and tools in one place, along with their availability, maintenance status, current location, and more.
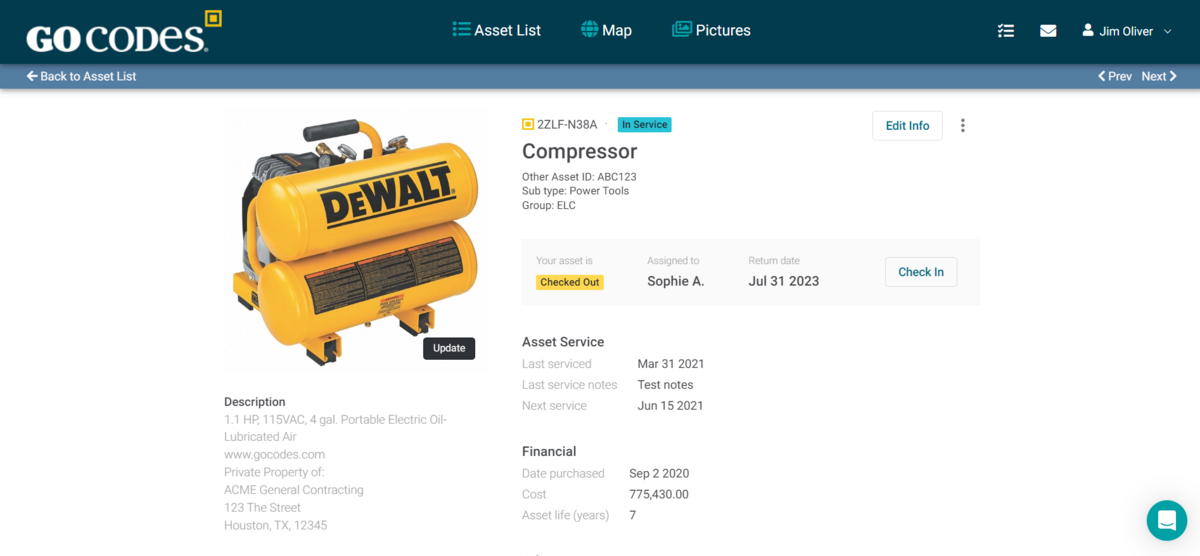
This way, the equipment manager can easily schedule equipment and plan for backups or tentatively pre-arrange rentals, ensuring that unexpected breakdowns of critical equipment won’t disrupt project timelines.
There are many other examples of proactive risk mitigation enabled by the plan, such as:
- vetting material suppliers and subcontractors to ensure quality and reliability,
- conducting detailed site surveys and inspections to identify potential issues early on, and
- providing safety workshops and training sessions to prevent job site accidents.
By acting on these and other potential risks early, your construction team can prevent disruptions, minimize damage, and avoid crisis-driven responses.
In the event that risks do occur, though, having a risk management plan in place ensures a structured response to issues and helps resolve them quickly.
Improves Safety on the Construction Site
Construction sites are inherently hazardous environments, that much is for certain.
So, having a well-crafted risk management plan plays a key role in enhancing safety practices and preventing accidents.
Given that many construction risks are tied directly to on-site operations, one part of preparing the plan focuses on identifying potential safety hazards and establishing protocols to mitigate them.
For instance, the plan may include requirements for equipment operators to conduct daily pre-use inspections to reduce the risk of failure and accidents.
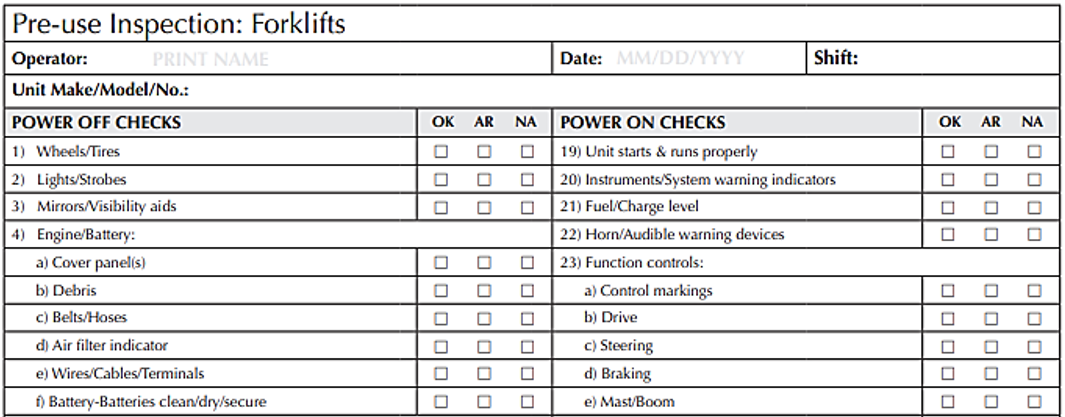
Such inspections help ensure that any worn or defective parts are promptly replaced to prevent malfunctions that could endanger workers and cause delays.
Similarly, the plan may mandate that all workers wear personal protective equipment (PPE) and establish clear procedures for monitoring compliance.
In addition to routine safety training for all workers, the plan may also include specialized training for high-risk activities, such as working at heights.
After all, falls to a lower level are one of the most common causes of fatal injuries among construction workers.
Overall, a well-crafted plan will encompass a range of measures designed to minimize on-site accidents, thereby promoting a safer work environment, reducing injuries, and helping companies avoid costly legal and medical claims.
Builds Stakeholder Trust
A well-thought-out risk management plan builds trust between the contractor, client, and other project stakeholders by demonstrating that potential risks are actively controlled.
When a contractor does their part in proactively identifying and addressing risks, they instill confidence in their client and other stakeholders.
Ultimately, this leads to stronger working relationships.
For instance, take a contractor who regularly sends project progress reports updated with the latest risk assessments and response strategies, like in the example below.
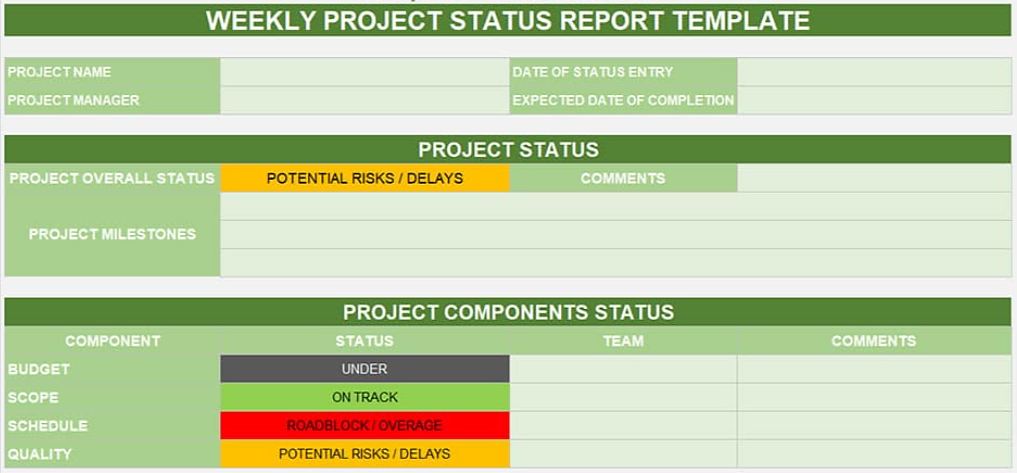
This transparency is reassuring to stakeholders, often resulting in fewer disputes and greater support throughout the project lifecycle.
The enhanced trust extends to regulatory bodies that may conduct job site inspections or documentation reviews, too.
Ultimately, having a risk management plan signals that construction risks are anticipated and addressed proactively, thus building stakeholder trust and enhancing collaboration.
Improves Future Risk Management
Lastly, documenting risks and risk responses from project to project helps create a repository of lessons learned.
This can then be used to enhance future risk management.
For example, risks that frequently materialized in past projects, such as unexpected site conditions or recurring safety violations, can be analyzed to develop more effective mitigation strategies next time around.
As Kris Reynolds, Founder and CEO of Arrowhead Consulting, explains:
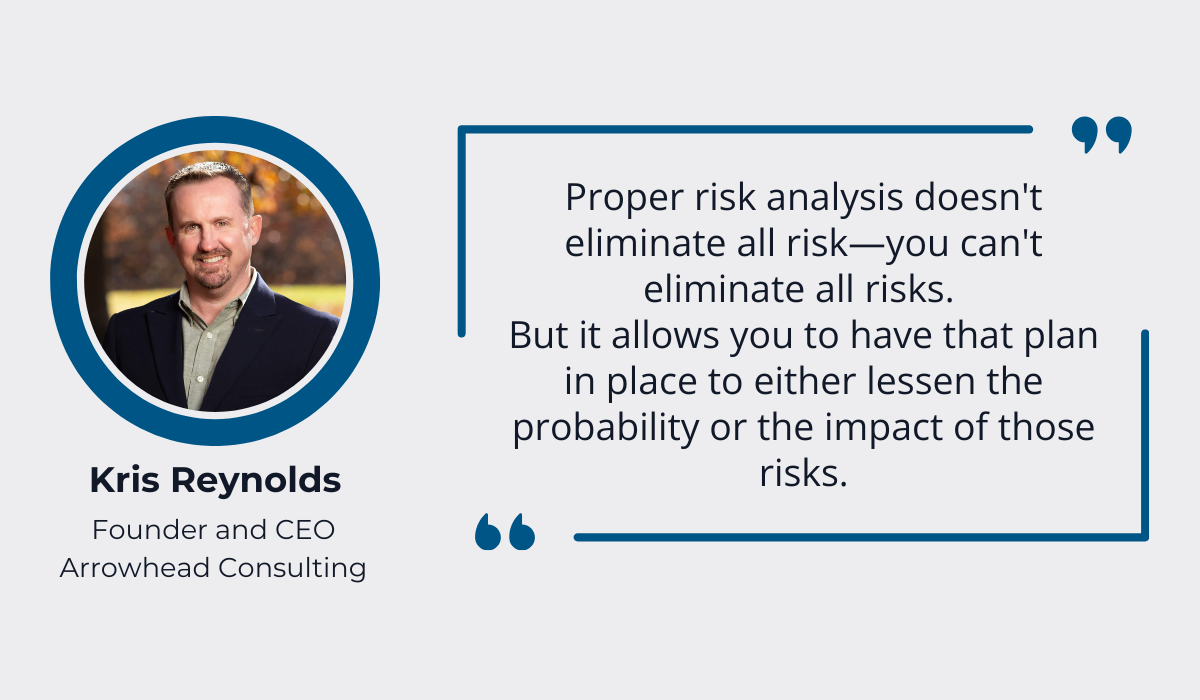
Overall, creating a construction risk management plan and using it as a sort of knowledge base can do your company a world of good.
Among other things, it will allow you to improve risk planning for future projects, ultimately helping you continuously refine your approach to risk management.
Conclusion
We hope this guide has served its purpose in offering new insights to enhance your company’s risk management planning practices.
Yes, developing a robust construction risk management plan is going to require time, resources, and commitment.
But it is also essential to delivering successful projects—on time, on budget, and with minimized risk.
So, don’t underestimate its importance, and you should soon be reaping the benefits.