Construction projects employ a broad range of resources like labor, equipment, and materials.
Naturally, construction companies want to use those and other construction resources as efficiently as possible.
That’s where construction resource management steps in.
In this article, we’ll take a closer look at the five benefits of construction resource management you should know about.
In this article...
Improved Budget Forecasting
Effective construction resource management will improve budget forecasting for your current and future projects by providing information crucial for more accurate estimates of the required resources and their costs that need to be included in the budget.
But before we dive in, let’s set the stage and define what we’re talking about.
In short, construction resources refer to everything a construction firm would need to complete a construction project.
Although such resources can range from, for example, credit line funds for financing a project to on-site storage facilities, the most common resources involved in construction projects are people, equipment, and materials.
Those and other resources can be broken down by function and type in various ways, depending on each project’s specific construction resource management requirements.
For example, here’s a breakdown of resources needed for constructing a bridge:
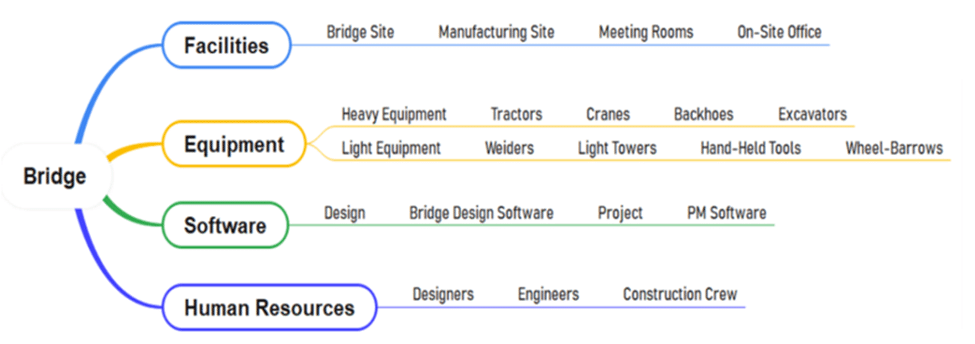
Each of these resource types can be broken down further or structured differently.
Still, all of them have the same purpose—to classify, organize and display construction resources, which can then be used for successful construction budgeting.
It follows that construction resource management refers to how a construction manager or general contractor tracks and utilizes (i.e., manages) all of the resources required to complete a construction project, preferably on time and within budget.
This brings us back to how construction resource management improves budget forecasting.
Simply put, when you’re able to track the productivity of labor and the utilization of materials and equipment throughout the construction project lifecycle, the insights gained from the collected data will make your budget forecasts for current and future projects much more precise.
Of course, the market offers a vast selection of construction management software that can streamline all or specific aspects of resource management, as this one does.
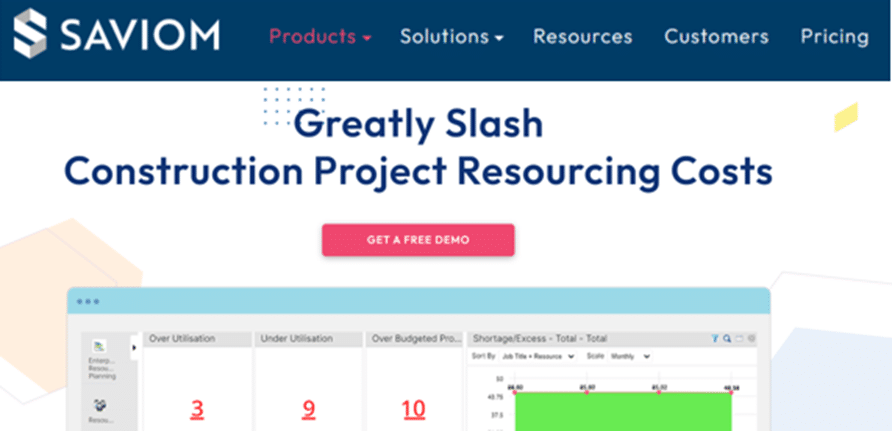
This and other similar software will allow you to track project financials and productive utilization of your workforce, equipment, materials, etc., thus improving your budget forecasting when, for example, you need to integrate change orders into the budget of your ongoing construction project.
It will also allow you to compare cost estimates with actual project costs after project completion, so you can use the lessons learned to produce better budget forecasts for future construction projects.
To sum up, effective construction resource management gives you the tools to analyze and understand how construction resources are used, and that knowledge leads to more accurate budget forecasts.
Enabled Tracking of All Construction Resources
Proper construction resource management aims to achieve optimal utilization of all construction resources.
To do that, efficient resource management will necessarily involve tracking different construction resources throughout the project lifecycle, which then produces a host of other benefits.
First, it’s clear that the times when, for instance, the quantities of construction materials used on-site every day were manually tracked on paper are long gone.
Nowadays, all construction resource management processes can and should be automated and streamlined with the help of technology.
Naturally, construction companies recognized this and started integrating different technological solutions into their operations.
Construction management software was among the first solutions to be widely adopted, with 54% of construction managers already using them in 2018.
Furthermore, recent global developments provided plenty more reasons to improve construction resource management, and that’s why the global construction management software market is predicted to grow by 8.04% in 2022, with even higher growth rates in subsequent years.
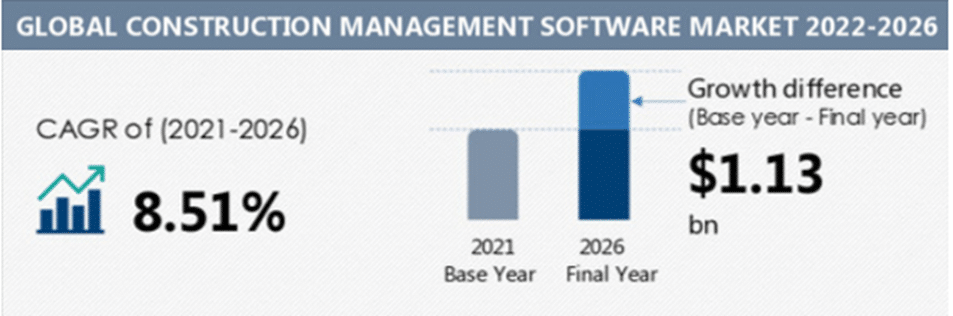
One of the primary benefits of such software is that they enable the tracking of all construction resources.
For example, you can track the availability of construction materials, plan their procurement, and adjust to potential constraints like supply chain breakdowns or rising material prices.
As expected, the market offers solutions that enable tracking of all or specific types of construction resources.
For instance, 4castplus lets you track and manage labor, equipment, and materials and provides centralized control of those and other construction resources.
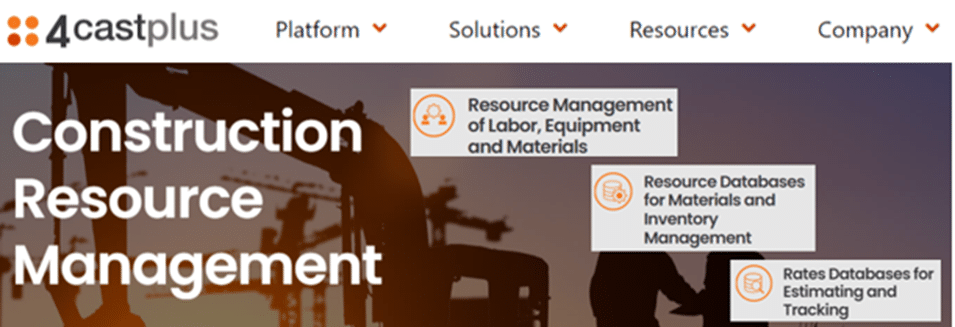
Such solutions can, for example, allow you to efficiently reallocate workers, machinery, and materials when an inevitable change order appears.
However, with construction projects having so many moving parts, it is often necessary to deploy specialized tools for tracking different resources, such as equipment.
As construction tools and equipment often change hands and locations, neglecting to physically track them can jeopardize efficient equipment management.
In other words, a piece of equipment can be misplaced, lost, or stolen, or it can break down due to poor maintenance.
This calls for specialized tracking software like GoCodes Asset Tracking. This affordable and simple solution combines the power of cloud software, smartphones, and patented QR code tags.
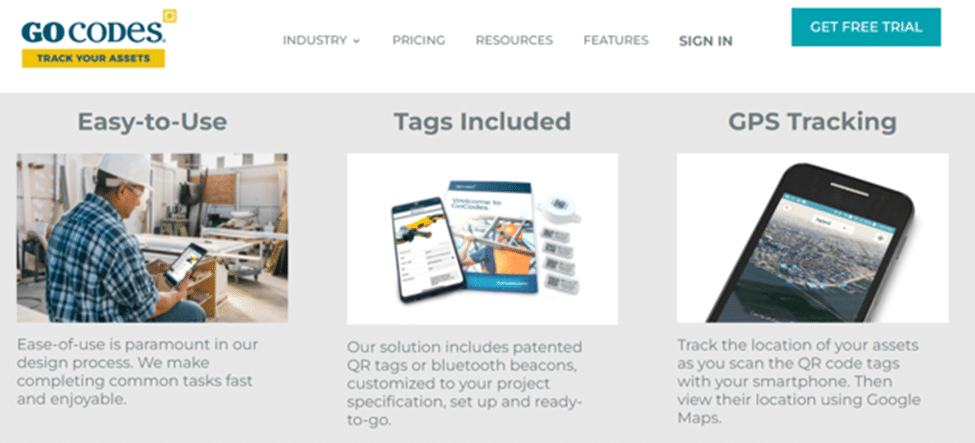
All in all, effective construction resource management can’t be imagined without the ability to track how different resources are utilized.
And when tracking is automatized with the help of software, this can vastly improve resource management, increase productivity, and maximize profitability.
Minimized Construction Project Costs
Another all-encompassing benefit of proficient construction resource management is that it minimizes costs from start to finish of the project.
Costs can be cut in the resource planning process or during project delivery, where efficient resource management allows construction managers to avoid many pitfalls of construction projects.
With so many factors at play that can negatively affect the project outcome, it’s no surprise that construction projects are vulnerable to time and cost overruns.
In fact, 86% of construction projects exceed their budget.
For example, bad weather can stop the works, short-circuit some equipment, and ruin certain materials.
When this happens, it results in higher labor, equipment, and material costs, thus blowing up your project budget.
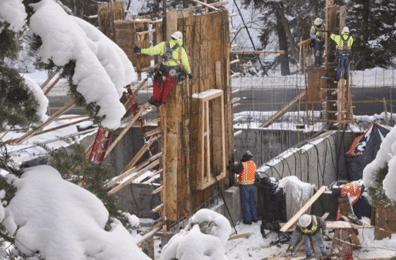
Naturally, establishing a robust resource management system that can adjust to such events without causing extensive delays or excessive costs requires good planning and preparation, which start with prudent resource allocation.
This is a crucial step in the resource planning process as it helps minimize the costs ensuing from mistakes like delays due to late delivery of materials or not having the right equipment and people available.
Naturally, that process can be streamlined by software like this.
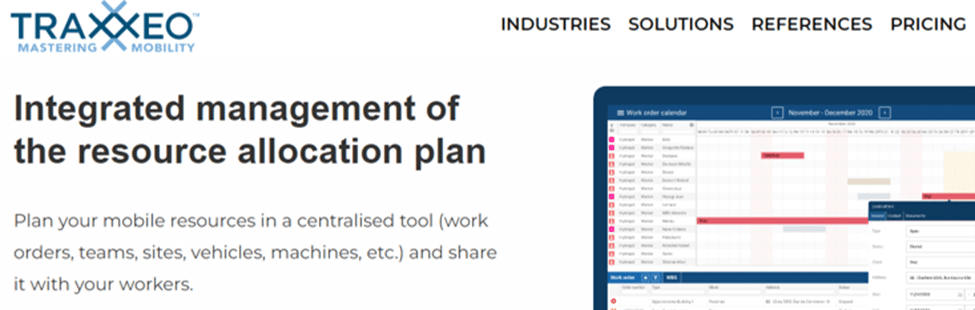
For instance, efficient workforce allocation could involve you deciding to pair a seasoned worker with a less experienced one to perform a specific construction task, thus preventing the extra cost of potential rework resulting from inexperience.
At the same time, you’re minimizing risks associated with ever-present skilled labor shortages, which is an issue that 89% of construction companies have to deal with.
This is a good example of how competent allocation of human resources in the project initiation phase can minimize construction project costs.
One way to keep construction project costs under control is through constant monitoring of resource-related financial elements of the project.
In other words, when a project milestone is reached, actual and planned costs can be compared, and any overruns can be timely managed, thus minimizing their effect of increasing construction project costs.
Overall, effective construction resource management will ensure both budget and schedule contingencies that will help minimize delays and costs associated with many risks and constraints inherent to construction projects.
Improved Jobsite Productivity
Perhaps the biggest advantage of construction resource management is seen in the improved productivity on your construction site and across your construction operations.
Like in the case of project costs, efficient planning, allocation, and management of construction resources can enhance the overall jobsite productivity.
Productivity is another long-standing problem in the construction industry.
According to McKinsey, despite being the biggest industry in the world (13% of global GDP), its productivity has been “growing” at a steady rate of just 1% over the last twenty years.
When the efficiency of individual jobsites is concerned, it rests upon optimal management of construction resources required for successful project completion.
To achieve this, they first need to be planned and allocated, possibly with the help of software like this.
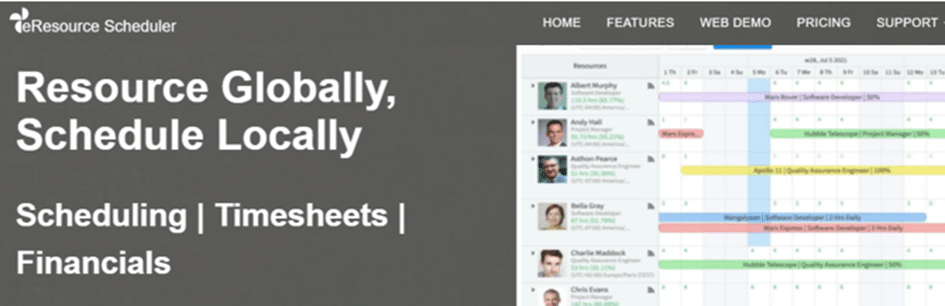
Using such software to, let’s say, plan the time and cost of operator training and allocate the necessary resources will improve the productivity of your machine operators by empowering them to do their job and preventing breakdowns and injuries due to improper operation.
It will also facilitate the management of operator working hours and equipment utilization during construction.
The risks, constraints, dependencies, and interrelationships related to different construction project resources can be best captured by one of many available construction management software solutions that allow for scheduling all those factors.
For instance, the ones shown below are among the best-reviewed management software for small-to-medium-sized construction businesses.
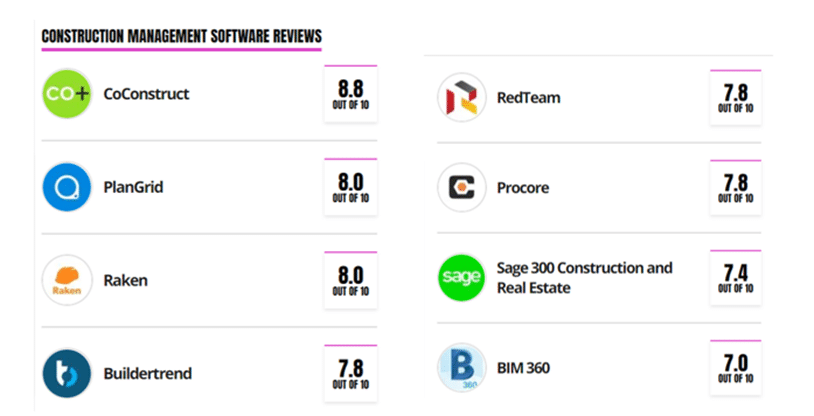
Any of these and other similar software solutions will allow you to plan and allocate different construction resources and manage their interdependencies across one or more construction sites, thus boosting the efficiency of your construction operations.
An example of a more specific resource management strategy that optimizes the utilization of materials on construction sites is known as “kitting.”
This process refers to collecting, packaging, and delivering otherwise unrelated construction materials together in one “kit” prepared according to the place of their installation.
This improves the overall jobsite productivity (e.g., by saving the time needed to find and get the right materials) and minimizes material waste, as you’ll see below.
Thus, efficient resource management will mirror how you, probably by using software, initially planned and allocated construction resources and how you’re optimizing their utilization during the project lifecycle, all of which improves jobsite productivity.
Reduced Material Waste
The benefit of reduced material waste has long been overlooked, but it’s quickly becoming an essential element of any efficient construction resource management strategy due to environmental and economic concerns.
Whether it’s demolition waste, packaging materials, leftover wood, metal, glass or plastic waste, expired paints, varnishes, or adhesives, etc., construction sites usually generate sizable quantities of material waste.
In fact, around a third of all construction materials on-site can end up disposed of as waste, with immense negative environmental and financial effects.
Thus, any miscalculations in estimating and scheduling construction materials needed during a project can result in more material waste.
Here’s what a typical composition of waste materials generated on a construction site looks like.
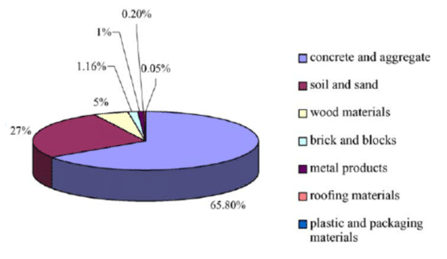
For example, extra waste can arise when the quantity of construction materials is misestimated, thus resulting in overordering.
If the excess material can’t be reallocated and used somewhere else, it will most likely be discarded as waste after project completion.
The same applies if the wrong type of material was ordered or the right material was delivered to the wrong construction site.
Mind you, cost-effective reallocation of such materials to avoid them becoming waste can be demanding as it requires additional resources like people and equipment needed for their transport or facilities required for their temporary storage.
Conversely, proper waste disposal also comes with a price tag, which many try to avoid, as this image shows.
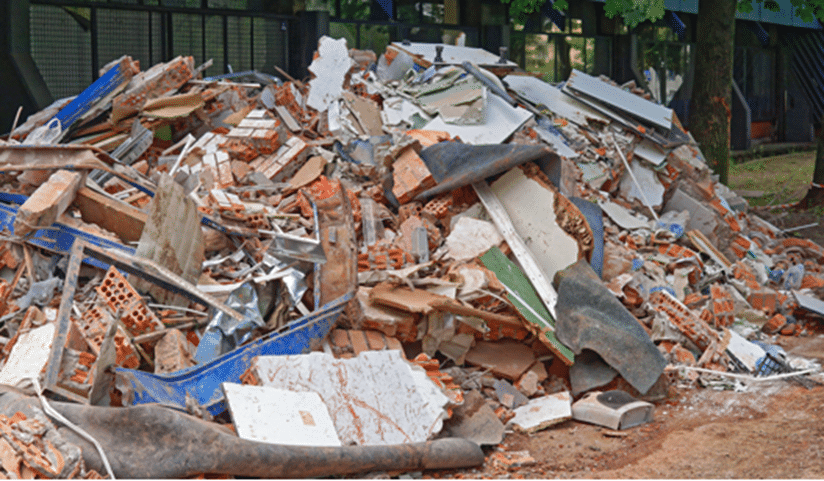
Many of those wasted resources can be prevented by efficient construction material management, which is an integral part of construction resource management.
A successful material management strategy will ensure more accurate estimating, planning, and scheduling of materials, thus reducing the likelihood of the above-described events generating excess waste.
Naturally, appropriate quality control of materials and their suitable storage will also reduce the generation of waste.
To sum up, effective construction resource management uses all its different components to optimize waste-generating processes, thus reducing material waste, lowering costs, and alleviating the environmental burden of waste.
Conclusion
In closure, it’s safe to say that construction resource management, especially when supported by relevant software solutions, brings immense benefits throughout the project lifecycle.
In this article, we covered only five you should know about and, naturally, there are many more.